High-Pressure Aluminum Die Casting and Copper Die Casting Heatsinks
CASTMAN's high-pressure die casting is a manufacturing process that injects liquid metal into a mold under high pressure. This method offers advantages such as high production speed and the ability to create complex shapes. Aluminum is a lightweight material with high thermal conductivity, making it suitable for heatsinks. Copper, with its even higher thermal conductivity than aluminum, is preferred for high-heat generating components.
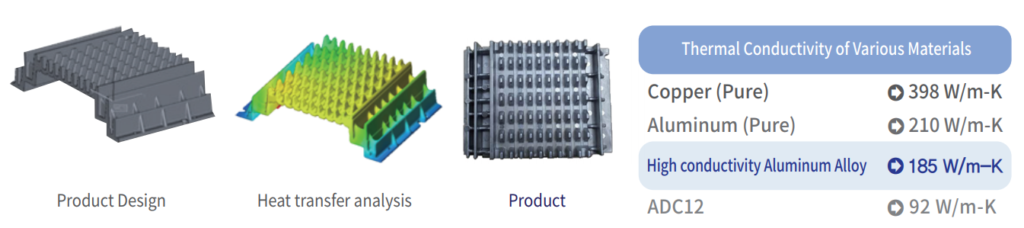
I. High-Pressure Aluminum Die Casting Heatsinks
High-pressure aluminum die casting is a widely used heatsink manufacturing process due to its high productivity and cost-effectiveness. It efficiently produces heatsinks with thin wall thicknesses and complex internal structures, offering advantages in miniaturization and lightweight design. However, quality control is crucial to address surface roughness and internal porosity inherent in the die casting process.
A. Computer, Power Electronics Industry:
- Products: CPU coolers, GPU coolers, power supply heatsinks, inverter heatsinks, power module heatsinks, server heatsinks, network equipment heatsinks, etc.
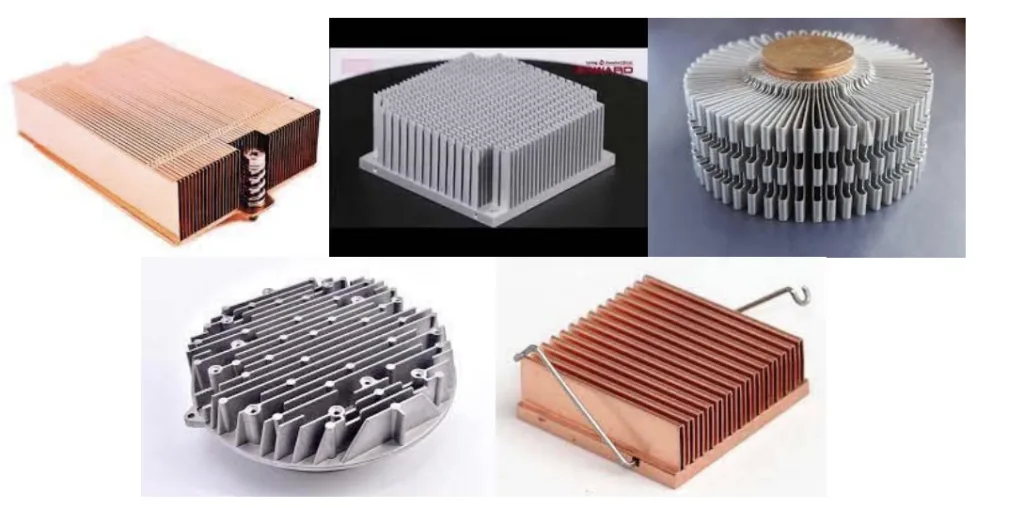
Source: "An Overview of Heat Sink Technology" presented at the IJME
- Characteristics:
- High thermal conductivity and heat dissipation efficiency are required.
- Complex shapes and high precision are necessary, and designs are optimized for miniaturization and lightweight design.
- Some products incorporate electromagnetic shielding. Recent research focuses on optimizing fin shapes, arrangements, and sizes to enhance heat transfer performance.
- Efforts are also underway to improve durability and heat dissipation performance through the combination of various materials.
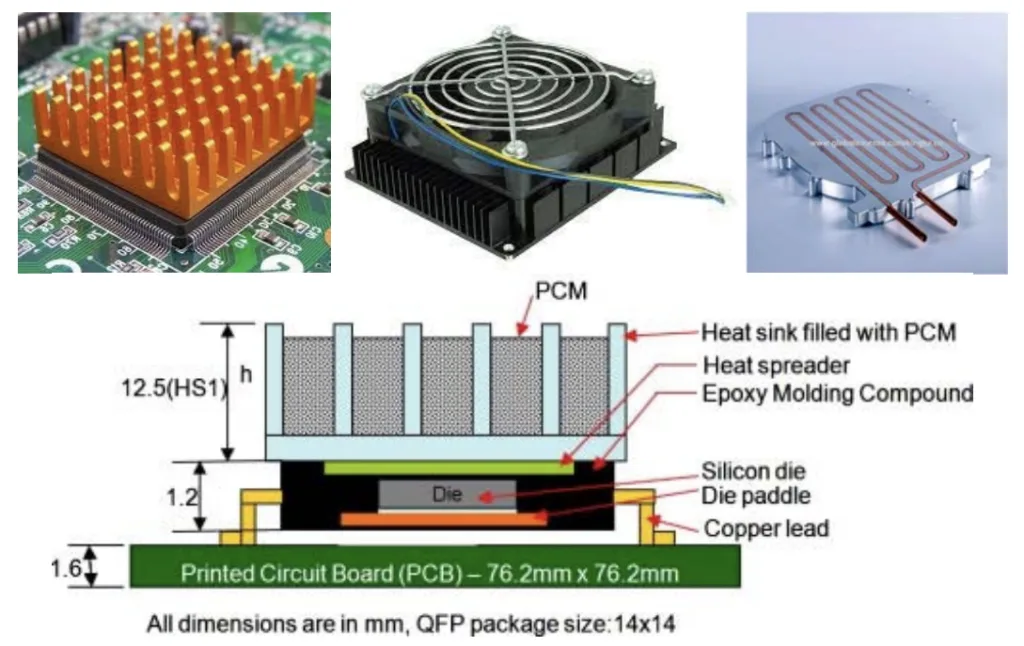
Source: "An Overview of Heat Sink Technology" presented at the IJME
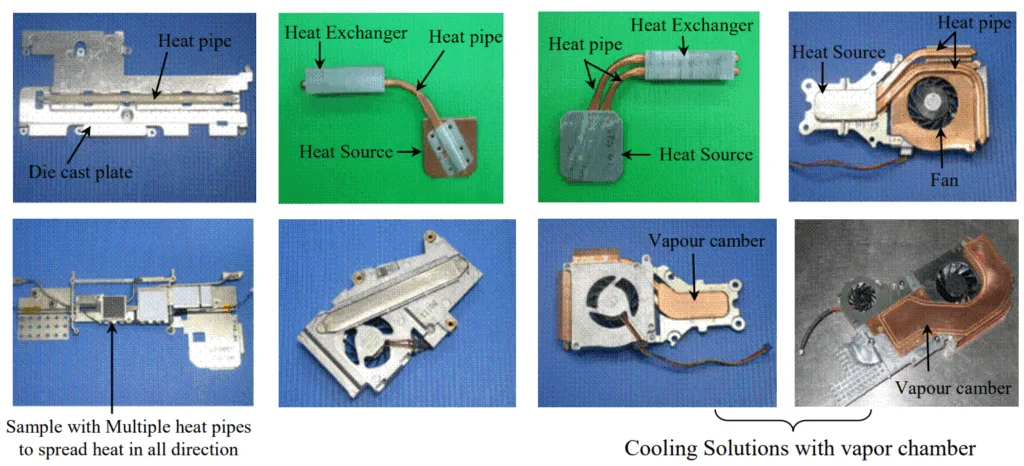
B. Automotive Industry:
- Products: Engine coolers, transmission coolers, power electronics device heatsinks (ECUs, motor drivers, etc.), LED headlight heatsinks, battery coolers, etc.
- Characteristics:
- Heat resistance, durability, and vibration resistance are crucial.
- Designs must ensure stable operation in extreme environments and prevent performance degradation during long-term use.
- The trend towards lightweight vehicles emphasizes the advantages of aluminum, and research is actively pursuing various fin structures and integrated designs with cooling systems.
C. Industrial Automation Industry:
- Products: Servo motor heatsinks, PLC heatsinks, inverter heatsinks, robot coolers, industrial equipment heatsinks, etc.
- Characteristics:
- Durability and environmental durability are essential, maintaining stable heat dissipation performance even during long-term continuous operation.
- Ease of installation and maintenance is also considered.
- Products with enhanced corrosion and abrasion resistance may be required considering the specific characteristics of industrial environments.
D. LED Lighting Industry:
- Products: LED lighting heatsinks, LED strip heatsinks, etc.
- Characteristics:
- High-efficiency heat dissipation and durability are crucial, and aesthetic design also affects product competitiveness.
- Optimized design considering the heat generation characteristics of LEDs is essential, and research is underway to enhance design freedom through miniaturization and lightweight design.
II. Copper Die Casting Heatsinks
Copper, with its significantly higher thermal conductivity than aluminum, is suitable for high-heat generating components. However, its high cost and difficult processing limit its usage compared to aluminum. It is primarily used in applications requiring high performance and reliability.
A. High-Power Power Devices:
- Products: High-power semiconductor heatsinks, laser diode heatsinks, high-power power supply heatsinks, etc.
- Characteristics:
- Extremely high thermal conductivity is essential, ensuring stable operation even at high temperatures.
- Durability is crucial, maintaining performance without degradation during long-term use.
- The demand for miniaturization and lightweight design is also increasing.
B. Medical Equipment:
- Products: Medical laser equipment heatsinks, high-power ultrasound equipment heatsinks, etc.
- Characteristics: High-temperature stability and corrosion resistance are important, and biocompatibility may be required for some products. Strict quality control and safety standards must be adhered to.
C. Aerospace Industry:
- Products: High-power electronic equipment heatsinks, aircraft engine component heatsinks, etc.
- Characteristics:
- Lightweight design and high strength are crucial, ensuring stable operation in extreme environments.
- Maintaining high thermal conductivity while ensuring durability is essential.
High-pressure aluminum die casting and copper die casting each have their advantages and disadvantages. Selecting the appropriate material and process based on the requirements of the industrial sector is critical.
Custom Extruded Heat Sink Fabrication |
We can make custom extruded heat sinks. It offers a variety of features to obtain the required alloy, surface finish, and secondary work. There are two commonly used materials to make heat sinks. Heat sinks are usually made of aluminum or copper. Each has its own advantages.
Heat Sink by High conductivity Aluminum Alloy
Integrated Heat Sink with Cooling Capability
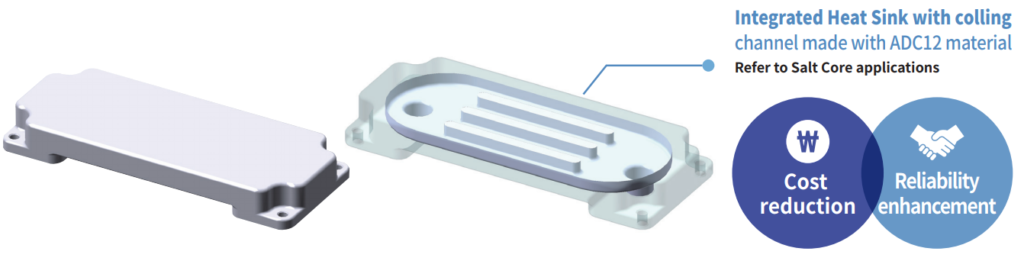
Aluminum heat sink
Aluminum is the most common material for heat sinks. Especially extruded aluminum heat sink is suitable for most projects. Metals are light and have a relatively good thermal conductivity.
Copper heat sink
Copper has a much better thermal conductivity than aluminum. But the downside is weight and cost. Metals are sometimes used when the importance of thermal conductivity is more important than reducing weight.
Each heat sink manufacturing process has its own advantages and disadvantages. There are several ways to make a heat sink.
Heat Sink Types
- Extruded heat sink
Most heat sinks are made of extruded aluminum. This process is useful for most applications. Extruded heat sinks are available at low cost and can be easily manufactured to custom specifications. For Castman, heat flow analysis (CFD) allows you to maximize the performance of your extruded heat sink.
- Skid heat sink
This method is usually produced from hard molds using copper. These heat sinks can provide high design flexibility and achieve high fin density. Copper heat sinks offer higher performance by creating more surface area and opportunities for heat dissipation, but weight is generally a drawback.
- CNC machined heat sink
CNC machined heat sinks provide high thermal conductivity and can achieve the most complex shapes. However, it is expensive and may not be suitable for mass production due to the production time of each piece.
Choose the type of heat sink that fits your needs
Heat sinks help absorb and dissipate heat generated by electronic devices. You should choose the appropriate type according to your design requirements and volume requirements.
When it comes to materials, aluminum saves weight and costs, while copper offers the highest level of thermal conductivity. A variety of manufacturing options are available, from extrusion and splicing to forging and machining. Each has its own advantages and disadvantages.
It also offers a variety of finishing options. One of the most common surface finishes for heat sinks is anodized. This electrochemical process increases the surface emissivity, corrosion resistance, wear resistance and electrical insulation. Coatings such as paint or powder are not recommended as they act as insulators.
When produced by CASTMAN, high quality products can be produced with significant cost savings while maintaining excellent quality.
Technical Resource For Heat Sinks
Development_of_High_Performance_Copper_Alloy_Chill_Vent_for_High_Pressure_Die_Casting
Review on nano particle reinforced aluminum metal matrix composites
Beyond Heat Sinks: A Deep Dive into Advanced Loop Cooling for High-Powered Electronics
A High Performance Active Antenna for the High Frequency Band
3W SFP Interface Development
New Optimal Heat Sink Design with Concave Fins for Cooling System in Light Emitting Diode Lamp
Model Characterization of High-Voltage Layer Heater for Electric Vehicles through Electro-Thermo-Fluidic Simulations
A New Hybrid Approach to Cooling High-Power Electronics with HPDC
LIQUID COOLING OF BRIGHT LEDS FOR AUTOMOTIVE APPLICATIONS
Contact Us
Please feel free to contact us for product production. We can help.
Tel : +82-31-351-5022
Fax: +82-31-351-5033
E-mail : sales@castman.co.kr