by Dirk Lehmhus
Fraunhofer Institute for Manufacturing Technology and Advanced Materials IFAM, Wiener Straße 12, 28359 Bremen, Germany
Metals 2024, 14(3), 334; https://doi.org/10.3390/met14030334
Submission received: 25 February 2024 / Accepted: 8 March 2024 / Published: 14 March 2024
(This article belongs to the Special Issue Advances in Metal Casting Technology)
1. Introduction
It is a platitude that science and technology do not necessarily evolve along straight paths. Instead, cycles may occur which can sometimes, but not always, be explained by technology-centered models, such as the famed Gartner hype cycle [2,3,4], or more generally by economy-level observations, such as Kondratiev waves and all their relatives [5]. In other cases, new ideas, new market needs, or the expiration of limiting patents may support the reemergence of technologies. The casting industry has experienced its share of such effects, and in as far as they concern changing markets and boundary conditions, these have already been discussed in the preceding Part I of this text. The delimitation between both these parts is illustrated in Figure 1, which has also been included in a similar form in Part I [1].
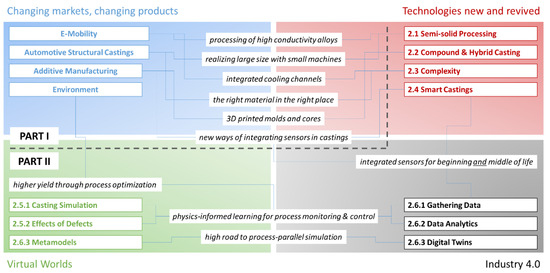
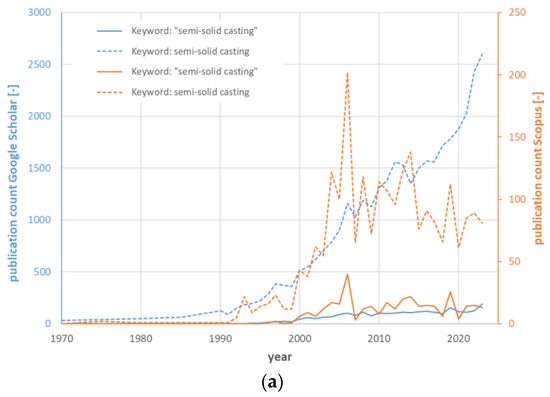
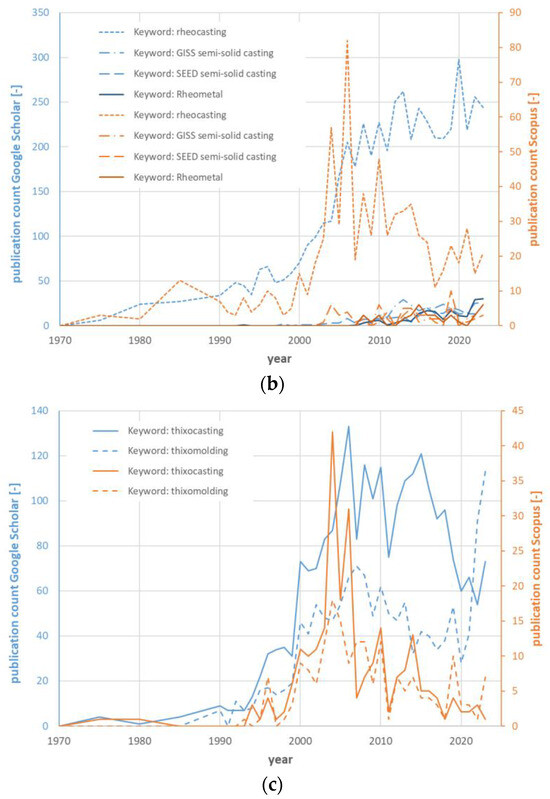
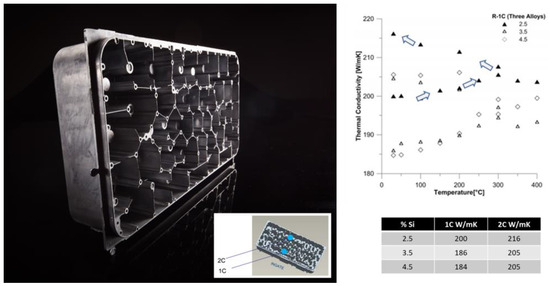
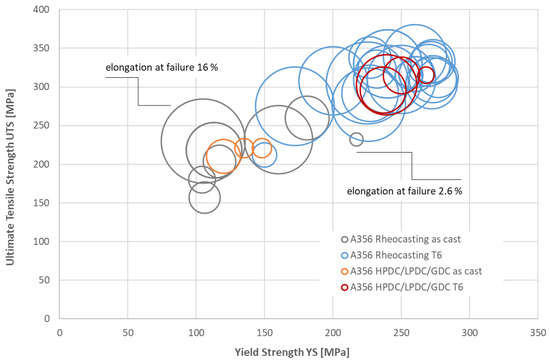
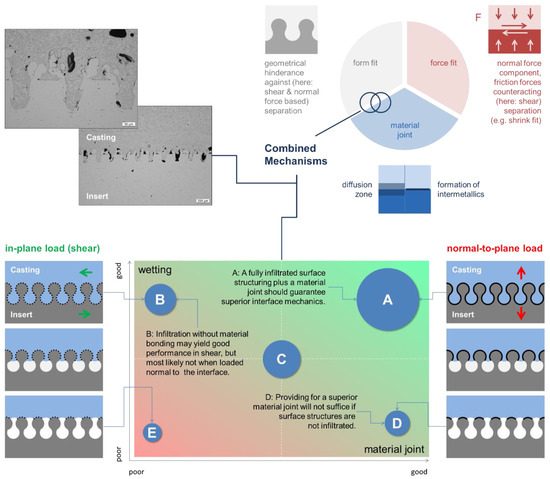
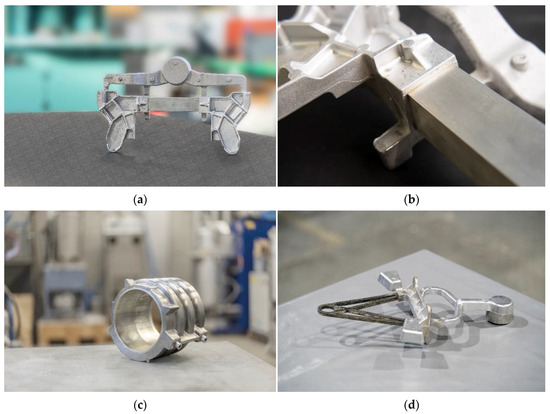
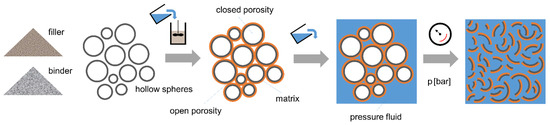
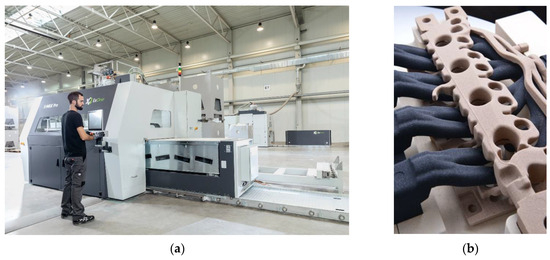
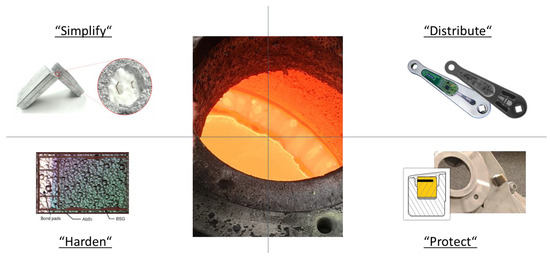

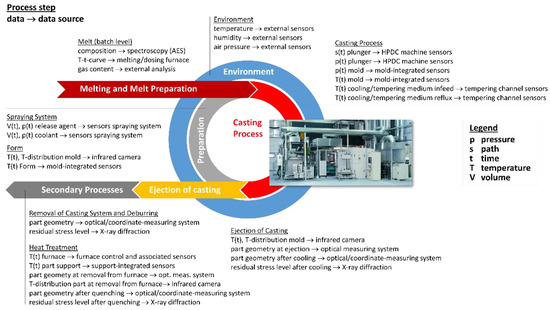
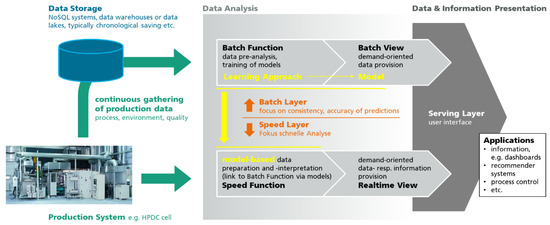
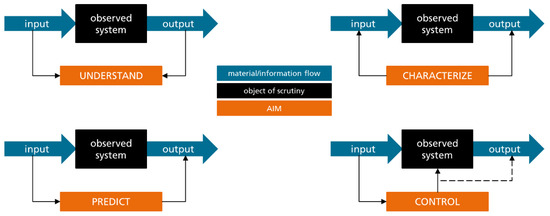
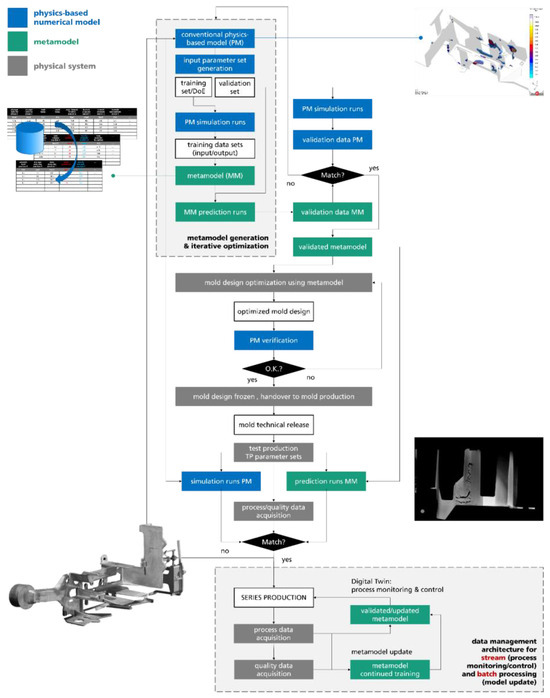
References
- Lehmhus, D. Advances in Metal Casting Technology: A Review of State of the Art, Challenges and Trends—Part I: Changing Markets, Changing Products. Metals 2022, 12, 1959. [Google Scholar] [CrossRef]
- Steinert, M.; Leifer, L. Scrutinizing Gartner’s Hype Cycle Approach. In PICMET 2010 Proceedings: Technology Management for Global Economic Growth; Kocaoglu, D.F., Anderson, T.R., Daim, T.U., Eds.; IEEE: Phuket, Thailand, 2010; pp. 1–13. [Google Scholar]
- Campani, M.; Vaglio, A. A simple interpretation of scientific/technological research impact leading to hype-type evolution curves. Scientometrics 2015, 103, 75–83. [Google Scholar] [CrossRef]
- Gartner Hype Cycle. Available online: https://www.gartner.com/en/research/methodologies/gartner-hype-cycle (accessed on 4 January 2023).
- Kondratjew, N.D. Die langen Wellen der Konjunktur. Arch. Für Sozialwissenschaft Und Sozialpolitik 1926, 56, 573–609. [Google Scholar]
- Flemings, M.C.; Riek, R.C.; Young, K.P. Rheocasting. Mater. Sci. Eng. A 1976, 25, 103–117. [Google Scholar] [CrossRef]
- Young, R.M.K. The Processing of Metals as Semi-Solid Slurries. Ph.D. Thesis, University of Surrey, Guildford, UK, 1986. [Google Scholar]
- Jorstad, J.L. Semi-Solid Metal Processing from an Industrial Perspective: The Best is Yet to Come! Solid State Phenom. 2016, 256, 9–14. [Google Scholar] [CrossRef]
- Czerwinski, F. Semisolid Processing—Origin of Magnesium Molding. In Magnesium Injection Molding; Springer: New York, NY, USA, 2008; pp. 81–147. [Google Scholar]
- Decker, R.; LeBeau, S. Thixomolding. Adv. Mater. Process. 2008, 166, 28–29. [Google Scholar]
- Huang, J.; Arbel, T.; Ligeski, L.; McCaffrey, J.; Kulkarni, S.; Jones, J.; Pollock, T.; Decker, R.; LeBeau, S. On Mechanical Properties & Microstructure of TTMP Wrought Mg Alloys. In Magnesium Technology 2010; Agnew, S., Ed.; The Minerals, Metals and Materials Society (TMS): Warrendale, PA, USA, 2010; pp. 489–493. [Google Scholar]
- Zhu, Y.; Midson, S. The Status of Magnesium Injection Molding in China. Solid State Phenom. 2019, 285, 436–440. [Google Scholar] [CrossRef]
- Decker, R.; LeBeau, S.; Wilson, B.; Reagan, J.; Moskovich, N.; Bronfin, B. Thixomolding® at 25 years. Solid State Phenom. 2016, 256, 3–8. [Google Scholar] [CrossRef]
- Mohammed, N.N.; Omar, M.Z.; Salleh, M.S.; Alhawari, K.S.; Kapranos, P. Semisolid Metal Processing Techniques for Nondendritic Feedstock Production. Sci. World J. 2013, 2013, 752175. [Google Scholar] [CrossRef]
- Kapranos, P. Current State of Semi-Solid Net-Shape Die Casting. Metals 2019, 9, 1301. [Google Scholar] [CrossRef]
- Midson, S.P. Rheocasting processes for semi-solid casting of aluminum alloys. Die Cast. Eng. 2006, 50, 48–51. [Google Scholar]
- Midson, S.P.; Jackson, A. A Comparison of Thixocasting and Rheocasting. In Proceedings of the 67th World Foundry Congress, Harrogate, UK, 5–7 June 2006; Institute of Cast Metals Engineers (ICME): Tipton, UK, 2006; pp. 22/1–22/10, ISBN 9781604236767. [Google Scholar]
- Bakhtiyarov, S.; Siginer, D.A. Rheoprocessing of Semisolid Aluminum Alloys. In Encyclopedia of Aluminum and Its Alloys, 1st ed.; Totten, G.E., Tiryakioğlu, M., Kessler, O., Eds.; Taylor & Francis Group: London, UK, 2018. [Google Scholar] [CrossRef]
- Jarfors, A.E.W. A Comparison Between Semisolid Casting Methods for Aluminium Alloys. Metals 2020, 10, 1368. [Google Scholar] [CrossRef]
- Li, G.; Qu, W.-Y.; Cheng, L.; Guo, C.; Li, X.-G.; Xu, Z.; Hu, X.-G.; Li, D.-Q.; Lu, H.-X.; Zhu, Q. Semi-solid processing of aluminum and magnesium alloys: Status, opportunity and challenge in China. Trans. Nonferrous Met. Soc. China 2021, 31, 3255–3280. [Google Scholar] [CrossRef]
- Wannasin, J. Applications of Semi-solid Slurry Casting using the Gas Induced Semi-Solid Technique. Solid State Phenom. 2013, 192–193, 28–35. [Google Scholar] [CrossRef]
- Kaufmann, H.; Uggowitzer, P.J. Fundamentals of the New Rheocasting Process for Magnesium Alloys. Adv. Eng. Mater. 2001, 3, 963–967. [Google Scholar] [CrossRef]
- Wabusseg, H.; Kaufmann, H.; Wahlen, A.; Uggowitzer, P.J. Theoretische Grundlagen und praktische Umsetzung von New Rheocasting von Al-Legierungen. Druckguss-Praxis 2002, 1, 16–19. [Google Scholar]
- Uggowitzer, P.J.; Kaufmann, H. Evolution of Globular Microstructure in New Rheocasting and Super Rheocasting Semi-Solid Slurries. Steel Res. Int. 2004, 75, 525–530. [Google Scholar] [CrossRef]
- Wessén, M.; Cao, H. The RSF Technology: A Possible Breakthrough for Semi-Solid Casting Processes. In Proceedings of the International Conference of High Tech Die Casting, Vicenza, Italy, 21–22 September 2006. [Google Scholar]
- Ratke, L.; Sharma, A.; Kohli, D. The RSF Technology for Semi-Solid Casting Processes. Indian Foundry J. 2011, 57, 33–36. [Google Scholar]
- Doutre, D.; Hay, G.; Wales, P.; Gabathuler, J.-P. SEED: A new process for semi-solid forming. Can. Metall. Q. 2004, 43, 265–272. [Google Scholar] [CrossRef]
- Yurko, J.A.; Martinez, R.A.; Flemings, M.C. The Use of Semi-Solid Rheocasting (SSR) for Aluminum Automotive Castings. SAE Trans. J. Mater. Manuf. 2003, 112, 119–123. [Google Scholar]
- Serving the Platform of Tomorrow! Available online: https://comptech.se/ (accessed on 11 March 2023).
- Li, M.; Du, W.; Elwany, A.; Pei, Z.; Ma, C. Metal binder jetting additive manufacturing: A literature review. J. Manuf. Sci. Eng. 2020, 142, 090810. [Google Scholar] [CrossRef]
- Zetterström, S.; Comptech AB, Skillingaryd, Sweden. Private communication, 2022.
- Chauke, L.; Möller, H.; Curle, U.A.; Govender, G. Industrial heat treatment of R-HPDC A356 automotive brake callipers. Solid State Phenom. 2013, 192–193, 533–538. [Google Scholar] [CrossRef]
- Dey, A.K.; Poddar, P.; Singh, K.K.; Sahoo, K.L. Mechanical and wear properties of rheocast and conventional gravity die cast A356 alloy. Mater. Sci. Eng. A 2006, 435–436, 521–529. [Google Scholar] [CrossRef]
- Govender, G.; Ivanchev, L.; Jahajeeah, N.; Bëan, R. Application of CSIR Rheocasting Technology for the Production of an Automotive Component. Solid State Phenom. 2006, 116–117, 501–504. [Google Scholar] [CrossRef]
- Guo, H.M.; Yang, X.J.; Wang, J.X. Microstructure and mechanical properties of Al alloys by semi-solid processing with LSPSF technology. Mater. Sci. Forum 2009, 628–629, 477–482. [Google Scholar] [CrossRef]
- Gupta, R.; Sharma, A.; Pandel, U.; Ratke, L. Effect of heat treatment on microstructures and mechanical properties of A356 alloy cast through rapid slurry formation (RSF) process. Int. J. Cast Met. Res. 2017, 30, 283–292. [Google Scholar] [CrossRef]
- Möller, H.; Govender, G.; Stumpf, W.E.; Knutsen, R.D. Influence of temper condition on microstructure and mechanical properties of semisolid metal processed Al-Si-Mg alloy 356. Int. J. Cast Met. Res. 2009, 22, 417–421. [Google Scholar] [CrossRef]
- Möller, H.; Govender, G.; Stumpf, W.E. Comparison of the heat treatment response of SSM-HPDC 6082 and 6004 wrought alloys with A356 and F357 casting alloys. Mater. Sci. Forum 2011, 690, 53–56. [Google Scholar] [CrossRef]
- Anticorodal®—Unendlich Anpassungs Fähig. Available online: https://rheinfelden-alloys.eu/legierungen/anticorodal/ (accessed on 21 February 2022).
- Rosso, M.; Peter, I.; Villa, R. Effect of T5 anfd T6 Heat Treatments Applied to Rheocast A356 Parts for Automotive Applications. Solid State Phenom. 2008, 141–143, 237–242. [Google Scholar] [CrossRef]
- Rosso, M. Thixocasting and rheocasting technologies, improvements going on. J. Achiev. Mater. Manuf. Eng. 2012, 54, 110–119. [Google Scholar]
- Tahamtan, S.; Fadavi Boostani, A.; Nazemi, H. Mechanical properties and fracture behavior of thixoformed, rheocast and gravity-cast A356 alloy. J. Alloys Compd. 2009, 468, 107–114. [Google Scholar] [CrossRef]
- Zhang, L. Technology Innovation & Green Development—Chinese Foundry Industry Status and Outlook. Chinese Foundry Association. 2015. Available online: https://www.foundry-planet.com/fileadmin/redakteur/pdf-dateien/18.09.2015BRICS_2015_China.pdf (accessed on 13 May 2020).
- Atkinson, H.V. Alloys for Semi-Solid Processing. Solid State Phenom. 2012, 192–193, 16–27. [Google Scholar] [CrossRef]
- Curle, U.A. Semi-solid near-net shape rheocasting of heat treatable wrought aluminum alloys. Trans. Nonferrous Met. Soc. China 2010, 20, 1719–1724. [Google Scholar] [CrossRef]
- Li, G.; Lu, H.; Hu, X.; Lin, F.; Li, X.; Zhu, Q. Current Progress in Rheoforming of Wrought Aluminum Alloys: A Review. Metals 2020, 10, 238. [Google Scholar] [CrossRef]
- Sauermann, R.; Friedrich, B.; Bünck, M.; Bührig-Polaczek, A.; Uggowitzer, P.J. Semi-Solid Processing of Tailored Aluminium-Lithium Alloys for Automotive Applications. Adv. Eng. Mater. 2007, 9, 253–258. [Google Scholar] [CrossRef]
- Bünck, M.; Küthe, F.; Bührig-Polaczek, A.; Arnold, A.; Friedrich, B.; Sauermann, R. Semi-solid Casting of High-reactive Wrought Alloys by Means of the Alloy AlLi2.1Mg5.5ScZr (AA1420*). Solid State Phenom. 2008, 141–143, 145–150. [Google Scholar] [CrossRef]
- Langlais, J.; Lemieux, A. The SEED Technology for Semi-solid Processing of Aluminum Alloys: A Metallurgical and Process Overview. Solid State Phenom. 2006, 116–117, 472–477. [Google Scholar] [CrossRef]
- Langlais, J.; Andrade, N.; Lemieux, A.; Chen, X.G.; Bucher, L. The Semi-Solid Forming of an Improved AA6061 Wrought Aluminum Alloy Composition. Solid State Phenom. 2008, 141–143, 511–516. [Google Scholar] [CrossRef]
- Curle, U.A.; Govender, G. Semi-solid rheocasting of grain-refined aluminum alloy 7075. Trans. Nonferrous Met. Soc. China 2010, 20, s832–s836. [Google Scholar] [CrossRef]
- Qi, M.F.; Kang, Y.L.; Zhou, B.; Liao, W.N.; Zhu, G.M.; Yan, D.L.; Li, W.R. A forced convection stirring process for Rheo-HPDC aluminum and magnesium alloys. J. Mater. Process. Technol. 2016, 234, 353–367. [Google Scholar] [CrossRef]
- Kang, Y.; Li, J.; Li, G.; Wang, J.; Liu, A.; Chen, J.; Qi, M. Preparation and rheological die-casting of 7075 aluminum alloy semisolid slurry. J. Netshape Form. Eng. 2020, 12, 74–80. [Google Scholar]
- Kongiang, S.; Plookphol, T.; Wannasin, J.; Wisutmethangoon, S. Effect of Two-Step Solution Heat Treatment on the Microstructure Of Semisolid Cast 075 Aluminum Alloy. Adv. Mater. Res. 2012, 488–489, 243–247. [Google Scholar] [CrossRef]
- Payakkapol, S.; Chayopitak, N.; Kunsuwan, P.; Ohtake, N.; Srimanosaowapak, S. Production of low impurity aluminum rotor for motor efficiency enhancement. MATEC Web Conf. 2018, 192, 01043. [Google Scholar] [CrossRef]
- Aluman®—Widerstand Auch bei Höchsten Temperaturen. Available online: https://rheinfelden-alloys.eu/legierungen/aluman/ (accessed on 10 February 2022).
- Palanivel, S.; Kuehmann, C.; Edwards, P.; Filip, E. Casting Aluminum Alloys for High-Performance Applications. U.S. Patent Application US2019/0127824A1, 2 May 2019. [Google Scholar]
- Evans, J.M.; Hagan, R.J.; Routh, W.C.; Gibbs, R.N. Aluminum Alloys for Die Casting. Patent Application WO2020/028730A1, 6 February 2020. [Google Scholar]
- Schweigert, D.; Mileti, M.; Morhard, B.; Fromberger, M.; Sedlmair, M.; Lohner, T.; Otto, M.; Stahl, K. Innovative transmission concepts for hyper-high-speed electromechanical powertrains. In Proceedings of the EDrive 2019 International Conference, Bonn, Germany, 10–11 July 2019. [Google Scholar]
- Schweigert, D.; Gerlach, M.E.; Hoffmann, A.; Morhard, B.; Tripps, A.; Lohner, T.; Otto, M.; Ponick, B.; Stahl, K. On the Impact of Maximum Speed on the Power Density of Electromechanical Powertrains. Vehicles 2020, 2, 365–397. [Google Scholar] [CrossRef]
- Ley, M.; Al-Zuhairi, A.; Teutsch, R. Classification approach for hybrid components in mechanical engineering with a focus on additive manufacturing. Procedia CIRP 2021, 100, 738–743. [Google Scholar] [CrossRef]
- Schuh, G.; Bergweiler, G.; Dworog, L.; Fiedler, F. Die Karosserie aus dem Aluminium-Druckguss. WT Werkstattstech. 2022, 112, 580–585. [Google Scholar]
- Volk, W. Giga-Casting Ist Geeignet, den Karosseriebau neu zu Denken. Available online: https://www.automobil-produktion.de/produktion/gigacasting-ist-geeignet-den-karosseriebau-neu-zu-denken-501.html (accessed on 7 March 2024).
- Bork, H. Teslas Konstruktionsmethode Verbreitet Sich in China. Available online: https://www.konstruktionspraxis.vogel.de/teslas-konstruktionsmethode-verbreitet-sich-in-china-a-1081294/ (accessed on 5 January 2023).
- HiPhi and Tuopu Jointly Announces the Production of Ultra-large Die-Casting Integrated Rear Body Structure. Available online: https://www.human-horizons.com/main/en/news_detail?id=78 (accessed on 22 September 2022).
- Yuan, L. In China, Tesla Is a Catfish and Turns Auto Companies into Sharks. Available online: https://www.nytimes.com/2021/11/30/business/china-tesla-electric-cars.html (accessed on 5 January 2023).
- Zhang, P. HiPhi Becomes Latest Chinese EV Startup to Use Large Die-Casting Technology. Available online: https://cnevpost.com/2022/03/01/hiphi-becomes-latest-chinese-ev-startup-to-use-large-die-casting-technology/ (accessed on 5 January 2023).
- Loveday, S. VW’s Project Trinity to Use Giga-Casting & Automation to Compete with Tesla. Available online: https://insideevs.com/news/577128/volkwagen-compete-tesla-gigapress-robots/ (accessed on 5 January 2023).
- Waldersee, V.; Schwartz, J.; Schimroszik, N. Gigacasting and Robots: How Volkswagen’s Trinity Aims to Catch up with Tesla. Available online: https://www.reuters.com/business/autos-transportation/giga-casting-robots-how-volkswagens-trinity-aims-catch-up-with-tesla-2022-03-31/ (accessed on 5 January 2023).
- Ludwig, C.; Holt, N. The Die Is Cast for Volvo’s Future EV Production. Available online: https://automotivemanufacturingsolutions.h5mag.com/ams_january-march_2022/oem_volvo_mega-casting (accessed on 5 January 2023).
- Die Casting Machine Carat. Available online: https://www.buhlergroup.com/content/buhlergroup/global/en/products/carat_die-castingmachine.html (accessed on 4 January 2022).
- Bühler Adds Volvo Cars to Its Megacasting Customers. Available online: https://www.buhlergroup.com/content/buhlergroup/global/en/media/media-releases/buehler_adds_volvocarstoitsmegacastingcustomers.html (accessed on 5 January 2023).
- Blala, H.; Pengzhi, C.; Gang, C.; Shenglun, Z.; Shangwen, R.; Zhang, M. Innovative Hybrid High-Pressure Die-Casting Process for Load-Bearing Body-in-White Structural Components. Int. J. Met. 2024. [Google Scholar] [CrossRef]
- Lehmhus, D.; Pille, C.; Rahn, T.; Struss, A.; Gromzig, P.; Seibel, A.; Wischeropp, T.; Becker, H.; Diefenthal, F. Druckgießen und Additive Fertigung: Durch strategische Kombination das Beste aus zwei Welten nutzen. Giesserei 2021, 108, 36–43. [Google Scholar]
- Jiang, W.; Fan, Z.; Li, C. Improved steel/aluminum bonding in bimetallic castings by a compound casting process. J. Mater. Process. Technol. 2015, 226, 25–31. [Google Scholar] [CrossRef]
- Fang, X. Evaluation of Coating Systems for Steel Aluminum Hybrid Casting. J. Mater. Sci. Eng. A 2017, 7, 51–67. [Google Scholar]
- Schittenhelm, D.; Burblies, A.; Busse, M. Stahlverstärkter Aluminiumguss—Bauraumreduzierung durch lastfallgerechte Auslegung eines Verbund-Längsträgers mittels Mehrphasen-Topologieoptimierung. Forsch. Ingenieurwesen 2018, 82, 131–147. [Google Scholar] [CrossRef]
- Papis, K.J.M.; Hallstedt, B.; Löffler, J.F.; Uggowitzer, P.J. Interface formation in aluminum-aluminum compound casting. Acta Mater. 2008, 56, 3036–3043. [Google Scholar] [CrossRef]
- Papis, K.J.M.; Löffler, J.F.; Uggowitzer, P.J. Light metal compound casting. Sci. China Ser. E Technol. Sci. 2009, 52, 46–51. [Google Scholar] [CrossRef]
- Rübner, M.; Günzl, M.; Körner, C.; Singer, R.F. Aluminum-aluminum compound fabrication by high pressure die casting. Mater. Sci. Eng. A 2011, 528, 7024–7029. [Google Scholar] [CrossRef]
- Schwankl, M.; Kellner, R.; Singer, R.F.; Körner, C. The influence of sandblasting on the morphology of electrolessdeposited zinclayers on aluminum sheets. Appl. Surf. Sci. 2013, 283, 202–208. [Google Scholar] [CrossRef]
- Koerner, C.; Schwankl, M.; Himmler, D. Aluminum-aluminum compound castings by electroless deposited zinc layers. J. Mater. Process. Technol. 2014, 214, 1094–1101. [Google Scholar] [CrossRef]
- Schwankl, N.; Wedler, J.; Körner, C. Wrought Al-Cast Al compound casting based in zincate treatment for aluminum alloy inserts. J. Mater. Process. Technol. 2016, 238, 160–168. [Google Scholar] [CrossRef]
- Feng, J.; Ye, B.; Zuo, L.; Wang, Q.; Wang, Q.; Jiang, H.; Ding, W. Bonding of Aluminum Alloys in Compound Casting. Metall. Mater. Trans. A 2017, 48A, 4632–4644. [Google Scholar] [CrossRef]
- Liu, G.; Wang, Q.; Liu, T.; Ye, B.; Jiang, H.; Ding, W. Effect of T6 heat treatment on microstructure and mechanical property of 6101/A356 bimetal fabricated by squeeze casting. Mater. Sci. Eng. A 2017, 696, 208–215. [Google Scholar] [CrossRef]
- Liu, J.C.; Hu, J.; Nie, X.Y.; Li, H.X.; Du, Q.; Zhang, J.S.; Zhuang, L.Z. The interface bonding mechanism and related mechanical properties of Mg/Al compound materials fabricated by insert molding. Mater. Sci. Eng. A 2015, 635, 70–76. [Google Scholar] [CrossRef]
- Vicario, I.; Crespo, I.; Plaza, L.M.; Caballero, P.; Idoiaga, I.K. Aluminum foam and magnesium compound casting produced by high-pressure die casting. Metals 2016, 6, 24. [Google Scholar] [CrossRef]
- Cheng, J.; Zhao, J.-H.; Zhang, J.-Y.; Guo, Y.; He, K.; Shang-guan, J.-J.; Wen, F.-L. Microstructure and Mechanical Properties of Galvanized-45 Steel/AZ91D Bimetallic Material by Liquid-Solid Compound Casting. Materials 2019, 12, 1651. [Google Scholar] [CrossRef] [PubMed]
- Liu, T.; Wang, Q.; Sui, Y.; Wang, Q.; Ding, W. An investigation into interface formation and mechanical properties of aluminum-copper bi-metal by squeeze casting. Mater. Des. 2016, 89, 1137–1146. [Google Scholar] [CrossRef]
- Hu, Y.; Chen, Y.; Li, L.; Hu, H.; Zhu, Z. Microstructure and properties of Al/Cu bi-metal in liquid–solid compound casting process. Trans. Nonferrous Met. Soc. China 2016, 26, 1555–1563. [Google Scholar] [CrossRef]
- Liu, H.; Fu, D.; Dong, Z.; Huang, S.; Zhang, H. Bonding interfacial characterization of SiCp/8009Al composite and A356 aluminum alloy using compound casting. J. Mater. Process. Technol. 2019, 263, 42–49. [Google Scholar] [CrossRef]
- Nie, X.Y.; Liu, J.C.; Li, H.X.; Du, Q.; Zhang, J.S.; Zhuang, L.Z. An investigation on bonding mechanisms and mechanical properties of Al/Ti compound materials prepared by insert moulding. Mater. Des. 2014, 63, 142–150. [Google Scholar] [CrossRef]
- Pawlowski, A.E.; Splitter, D.A.; Muth, T.R.; Shyam, A.; Carver, J.K.; Dinwiddie, R.B.; Elliot, A.M.; Cordero, Z.C.; French, M.R. Producing hybrid metal composites by combining additive manufacturing and casting. Adv. Mater. Process. 2017, 175, 16–21. [Google Scholar]
- Lao, B. Druckgegossene Metallhybridstrukturen für den Leichtbau-Prozess, Werkstoffe und Gefüge der Metallhybriden. Ph.D. Thesis, Gießerei-Institut, RWTH Aachen, Aachen, Germany, 2013. [Google Scholar]
- Burblies, A.; Busse, M. Computer-based porosity design by multi-phase topology optimization. In Proceedings of the Multiscale & Functionally Graded Materials Conference (FGM), Honolulu, HI, USA, 15–18 October 2006. [Google Scholar]
- Mounchili, A.P.; Bosse, S.; Lehmhus, D.; Struss, A. Putting stiffness where it’s needed: Optimizing the mechanical response of multi-material structures. MATEC Web Conf. 2021, 349, 03001. [Google Scholar] [CrossRef]
- Chen, B.; Moon, S.K.; Yao, X.; Bi, G.; Shen, J.; Umeda, J.; Kondoh, K. Comparison Study on Additive Manufacturing (AM) and Powder Metallurgy (PM) AlSi10Mg Alloys. JOM 2018, 70, 644–649. [Google Scholar] [CrossRef]
- Potesser, M.; Schoeberl, T.; Antrekowitsch, H.; Bruckner, J. The characterization of the intermetallic Fe-Al layer of steel-aluminum weldings. In Proceedings of the EPD Congress 2006; The Minerals, Metals and Materials Society: Pittsburgh, PA, USA, 2006. [Google Scholar]
- Borrisutthekul, R.; Yachi, T.; Miyashita, Y.; Mutoh, Y. Suppression of intermetallic reaction layer formation by controlling heat flow in dissimilar joining of steel and aluminum alloy. Mater. Sci. Eng. A 2007, 467, 108–113. [Google Scholar] [CrossRef]
- Yin, F.-C.; Zhao, M.; Liu, Y.; Han, W.; Li, Z. Effect of Si on growth kinetics of intermetallic compounds during reaction between solid iron and molten aluminium. Trans. Nonferrous Met. Soc. China 2013, 23, 556–561. [Google Scholar] [CrossRef]
- Bobzin, K.; Öte, M.; Wiesner, S.; Gerdt, L.; Senge, S.; Hirt, G.; Bührig-Polaczek, A.; Brachmann, J. Effect of Alloying Elements on Growth Behavior of Intemetallic Compounds at the Cold-Sprayed Coating/Steel-Interface during Immersion in Aluminum Melt. Int. J. Met. 2018, 12, 712–721. [Google Scholar]
- Jiang, W.; Fan, Z.; Li, G.; Li, C. Effects of zinc coating on interfacial microstructures and mechanical properties of aluminum/steel bi-metallic composites. J. Alloys Compd. 2016, 678, 249–257. [Google Scholar] [CrossRef]
- Bobzin, K.; Öte, M.; Wiesner, S.; Gerdt, L.; Senge, S.; Hirt, G. Investigation on the cold rolling and structuring of cold sprayed copper-coated steel sheets. IOP Conf. Ser. Mater. Sci. Eng. 2017, 181, 012028. [Google Scholar] [CrossRef]
- Senge, S.; Brachmann, J.; Hirt, G.; Bührig-Polaczek, A. Evaluation of interlocking bond strength between structured 1.0338 steel sheets and high pressure die cast AlMg5Si2. AIP Conf. Proc. 2018, 1960, 040019. [Google Scholar]
- Ukar, E.; Liébana, F.; Andrés, M.; Marcos, I.; Lamikiz, A. Laser texturing and dissimilar material joining. Procedia Manuf. 2017, 13, 671–678. [Google Scholar] [CrossRef]
- Bizi-Bandoki, P.; Benayoun, S.; Valette, S.; Beaugiraud, B.; Audouard, E. Modifications of roughness and wettability properties of metals induced by femtosecond laser treatment. Appl. Surf. Sci. 2011, 257, 5213–5218. [Google Scholar] [CrossRef]
- Cunha, A.P.; Serro, V.; Oliveira, A.; Almeida, A.; Vilar, R.; Durrieu, M. Wetting behaviour of femtosecond laser textured Ti–6Al–4V surfaces. Appl. Surf. Sci. 2013, 265, 688–696. [Google Scholar] [CrossRef]
- Lao, B.; Bührig-Polaczek, A. Funktionsintegrierte Leichtbaustrukturen in gussintensiver Metall-Hybridbauweise. In Proceedings of the 18th Symposium Verbundwerkstoffe und Werkstoffverbunde, Chemnitz, Germany, 30 March–1 April 2011; pp. 413–421. [Google Scholar]
- Nayak, B.K.; Gupta, M.C.; Kolasinski, K.W. Formation of nano-textured conical microstructures in titanium metal surface by femtosecond laser irradiation. Appl. Phys. A 2008, 90, 399–402. [Google Scholar] [CrossRef]
- Bo, W.; Ming, Z.; Jian, L.; Xia, Y.; Gang, L.; Lan, C. Superhydrophobic surfaces fabricated by microstructuring of stainless steel using a femtosecond laser. Appl. Surf. Sci. 2009, 256, 61–66. [Google Scholar]
- Nolte, N.; Specht, U.; Fischer, M.; Lukasczyk, T.; Lehmhus, D.; Wilken, R. Laser Surface Pretreatment for Aluminium-Aluminium Compound Casting: Effect of Surface Topography and Wetting Behavior. In Proceedings of the Euromat 2019 Conference, Stockholm, Sweden, 1–5 September 2019. [Google Scholar]
- Nolte, N. Untersuchungen Lasermikrostrukturierter Metalloberflächen zur Her-Stellung Formschlüssiger Aluminium-Aluminium Verbindungen im Druckgussverfahren. Master’s Thesis, University of Bremen, Bremen, Germany, 2019. [Google Scholar]
- Voss, F. Herstellung Eines Stoffschlüssigen Aluminium-Aluminium-Verbundes im Niederdruckgießverfahren—Ermittlung von Übergangsparametern Durch Gießsimulationen und Deren Validierung. Master’s Thesis, University of Bremen, Bremen, Germany, 2020. [Google Scholar]
- Technisches Datenblatt. Available online: https://multimedia.3m.com/mws/media/1853182O/3m-impact-resistant-structural-adhesive-07333-german-tds.pdf (accessed on 4 January 2023).
- Lehmhus, D.; Clausen, J.; Woestmann, F.-J.; Gärtner, F.; List, A.; Klassen, T. Verfahren zur Erzeugung Einer Stoffschlüssigen Verbindung im Verbundguss. German Patent Application DE 10 2020 206 009 A1, 18 November 2021. [Google Scholar]
- Pintore, M.; Mittler, T.; Volk, W.; Starykov, O.; Tonn, B. Experimental investigation on the influence of thermal conditions during composite casting on the microstructure of Cu-Al bilayer compounds. Int. J. Met. 2018, 12, 79–88. [Google Scholar] [CrossRef]
- Pintore, M.; Wölck, J.; Mittler, T.; Greß, T.; Volk, W.; Tonn, B. Composite Casting and Characterization of Cu-Al Bilayer Compounds. Int. J. Met. 2020, 14, 155–166. [Google Scholar] [CrossRef]
- Liu, G.; Wang, Q.; Zhang, L.; Ye, B.; Jiang, H.; Ding, W. Effect of Cooling Rate on the Microstructure and Mechanical Properties of Cu/Al Bimetal Fabricated by Compound Casting. Metall. Mater. Trans. A 2018, 49A, 661–672. [Google Scholar] [CrossRef]
- Klose, C.; Freytag, P.; Otten, M.; Thürer, S.E.; Naier, H.J. Thermal Properties of Intermetallic Phases at the Interface of Aluminum-Copper Compound Castings. Adv. Eng. Mater. 2018, 20, 1701027. [Google Scholar] [CrossRef]
- Stein, S.; Wedler, J.; Rhein, S.; Schmidt, M.; Koerner, C.; Michaelis, A.; Gebhardt, S. A process chain for integrating piezoelectric transducers into aluminum die castings to generate smart lightweight structures. Results Phys. 2017, 7, 2534–2539. [Google Scholar] [CrossRef]
- Schwankl, M.; Himmler, D.; Urban, M.; Körner, C. Optimization of Mechanical Properties of Al–Al-Compound Castings by Adapted Heat Treatment. Adv. Eng. Mater. 2018, 20, 1800400. [Google Scholar] [CrossRef]
- Lehmhus, D.; List, A.; Gärtner, F.; Klassen, T. Aluminum-Aluminum Compound Casting Approaches Supported by Cold Sprayed Interlayers. 2024; unpublished work. [Google Scholar]
- Jiang, W.; Jiang, Z.; Li, G.; Wu, Y.; Fan, Z. Microstructure of Al/Al bimetallic composites by lost foam casting with Zn interlayer. Mater. Sci. Technol. 2018, 34, 487–492. [Google Scholar] [CrossRef]
- Guler, K.A.; Kisasoz, A.; Karaaslan, A. Fabrication of Al/Mg Bimetal Compound Casting by Lost Foam Technique and Liquid-Solid Process. Mater. Test. 2014, 56, 700–702. [Google Scholar] [CrossRef]
- Bakke, A.O.; Arnberg, L.; Løland, J.-O.; Jørgensen, S.; Kvinge, J.; Li, Y. Formation and evolution of the interfacial structure in al/steel compound castings during solidification and heat treatment. J. Alloys Compd. 2020, 849, 156685. [Google Scholar] [CrossRef]
- Fadaeinia, M.; Raiszadeh, R. Bonding of compound casted Ti/Al bimetal by heat treatment. Int. J. Miner. Metall. Mater. 2021, 28, 1515–1524. [Google Scholar] [CrossRef]
- Ho, J.-S.; Lin, C.B.; Liu, C.H. The Effect of Heat Treatment on Interface Properties of S45C Steel/Copper Compound Casting. Tamkang J. Sci. Eng. 2003, 6, 49–56. [Google Scholar]
- Mola, R.; Bucki, T.; Dziadon, A. Microstructure of the Bonding Zone Between AZ91 and AlSi17 Formed by Compound Casting. Arch. Foundry Eng. 2017, 17, 202–206. [Google Scholar] [CrossRef]
- Tayal, R.K.; Singh, V.; Gupta, A.; Kumar, S.; Ujjawal, D. Experimental investigation and evaluation of joint strength of A356/Mg bimetallic fabricated using compound casting. Int. J. Met. 2019, 13, 686–699. [Google Scholar] [CrossRef]
- Zhao, K.N.; Li, H.X.; Luo, J.R.; Liu, Y.J.; Du, Q.; Zhang, J.S. Interfacial bonding mechanism and mechanical properties of novel AZ31/WE43 bimetal composites fabricated by insert molding method. J. Alloys Compd. 2017, 729, 344–353. [Google Scholar] [CrossRef]
- Schmid, A.; Arnaut, K.; Clausen, J.; Koerdt, M.; Struss, A.; Woestmann, F.-J.; Busse, M. Process Concepts for the Manufacturing of Hybrid Composites from Aluminum and CFRP with a Polymer-based Decoupling Layer. In Proceedings of the Hybrid Materials and Structures Conference, Bremen, Germany, 18–19 April 2018. [Google Scholar]
- Schmid, A.; Arnaut, K.; Clausen, J.; Koerdt, M.; Struss, A.; Wöstmann, F.-J.; Busse, M. Intrinsic Aluminum CFRP Hybrid Composites Produced in High Pressure Die Casting with Polymer Based Decoupling Layer. Key Eng. Mater. 2017, 742, 197–204. [Google Scholar] [CrossRef]
- Clausen, J.; Kelch, M.; Wöstmann, F.-J.; Busse, M. Development of a high pressure die casting tool for partial integration of glass fiber structures. Key Eng. Mater. 2017, 742, 520–526. [Google Scholar] [CrossRef]
- Clausen, J.; Kelch, M.; Wöstmann, F.-J.; Busse, M. Mechanical characterization of integral aluminum-FRP-structures produced by high pressure die-casting. Prod. Eng. 2018, 12, 269–278. [Google Scholar] [CrossRef]
- Struss, A.; Schmid, A.; Ebrahimi, A.; Jablonski, F.; Busse, M. Description of the Boundary Layer Behavior of an Aluminum–Carbon-Fiber-Reinforced Polymer Hybrid Compound Using a Cohesive Zone Model. J. Fail. Anal. Prev. 2020, 20, 930–935. [Google Scholar] [CrossRef]
- Schmid, A.; Haubold, T.; Koschek, K.; Marx, A.; Pursche, L.; Struss, A.; Thiel, K.; Wiesing, M.; Busse, M. Hybrid casting—An investigation into the interface of high pressure die-cast intrinsic aluminum-PEEK-CFRP hybrid composites. IOP Conf. Ser. Mater. Sci. Eng. 2021, 1147, 012022. [Google Scholar] [CrossRef]
- Bitsche, R.D. Design and Computational Analysis of Compound Castings and other Multi-Material Structures. Ph.D. Thesis, Technical University of Vienna, Vienna, Austria, 2009. [Google Scholar]
- Leinenbach, F.; Sukowski, F.; Clausen, J.; Straß, B.; Wolter, B. Detection of quality features in hybrid cast components using NDT. In Proceedings of the 1st Congress for intelligent Combining of Design, Casting, Computer Simulation, Checking and Cyclic Behaviour for efficient Cast Components (InCeight Casting C8), Darmstadt, Germany, 2–3 March 2021; pp. 171–180. [Google Scholar]
- Holub, W.; Haßler, U.; Schorr, C.; Maisl, M.; Janello, P.; Jahnke, P. XXL-Micro-CT—Comparative Evaluation of Microscopic Computed Tomography for Macroscopic Objects. In Proceedings of the Digital Industrial Radiology and Computed Tomography (DIR 2015), Ghent, Belgium, 22–25 June 2015. [Google Scholar]
- Holub, W.; Brunner, F.; Schön, T. RoboCT—Application for in-situ inspection of join technologies of large scale objects. Int. Symp. Digit. Ind. Radiol. Comput. Tomogr. 2019, 11, 1–9. [Google Scholar]
- Nagai, Y.; Holub, W. Overview of Robot guided Computed Tomography—Production Monitoring in Automotive Industry 4.0. J. Jpn. Soc. Precis. Eng. 2020, 86, 316–322. [Google Scholar] [CrossRef]
- Glück Nardi, V.; Greß, T.; Tonn, B.; Volk, W. Modelling of intermetallic layers formation during solid-liquid joining of dissimilar metallic materials. IOP Conf. Ser. Mater. Sci. Eng. 2020, 861, 012058. [Google Scholar] [CrossRef]
- Joshi, D.; Ravi, B. Quantifying the shape complexity of cast parts. Comput.-Aided Des. Appl. 2010, 7, 685–700. [Google Scholar] [CrossRef]
- Johnson, M.D.; Valverde, L.M.; Thomison, W.D. An investigation and evaluation of computer-aided design model complexitiy metrics. Comput.-Aided Des. Appl. 2018, 15, 61–75. [Google Scholar] [CrossRef]
- Camba, J.D.; Contero, M.; Company, P.; Perez-Lopez, D.; Otey, J. Identifying high-value CAD models: An exploratory study on dimensional variability as complexity indicator. In Proceedings of the ASME 2018 13th International Manufacturing Science and Engineering Conference (MSEC 2018), College Station, TX, USA, 18–22 June 2018. [Google Scholar]
- Almaghariz, E.S. Determining when to Use 3D Sand Printing: Quantifying the Role of Complexity. Master’s Thesis, Youngstown State University, Youngstown, OH, USA, 2015. [Google Scholar]
- Almaghariz, E.S.; Conner, B.P.; Lenner, L.; Gullapalli, R.; Manogharan, G.; Lamoncha, B.; Fang, M. Quantifying the role of part design complexity in using 3D sand printing for molds and cores. Int. J. Met. 2016, 10, 240–252. [Google Scholar] [CrossRef]
- Martof, A.; Gullapalli, R.; Kelly, J.; Rea, A.; Lamoncha, B.; Walker, J.M.; Conner, B.; MacDonald, E. Economies of complexity of 3D printed sand molds for casting. In Proceedings of the Solid Freeform Fabrication 2018: Proceedings of the 29th Annual International Solid Freeform Fabrication Symposium, Austin, TX, USA, 13–15 August 2018; p. 117. [Google Scholar]
- Wang, J.; Sama, S.R.; Manogharan, G. Re-thinking design methodology for castings: 3D sand-printing and topology optimization. Int. J. Met. 2019, 13, 2–17. [Google Scholar] [CrossRef]
- Mukhtarkhanov, M.; Perveen, A.; Talamona, D. Application of Stereolithography Based 3D Printing Technology in Investment Casting. Micromachines 2020, 11, 946. [Google Scholar] [CrossRef]
- Hafsa, M.N.; Kassim, N.; Ismail, S.; Kamaruddin, S.A.; Hafeez, T.M. Study on surface roughness quality of FDM and MJM additive manufacturing model for implementation as investment casting sacrificial pattern. J. Mech. Eng. 2018, 5, 25–34. [Google Scholar]
- Kumar, R.; Kapil, S.; Negi, S.; Gehlot, N.; Gopalakrishna, S.H.; Karunakaran, K.P. Rapid Prototyping of EPS Pattern for Complicated Casting. In Proceedings of the Solid Freeform Fabrication 2017: Proceedings of the 28th Annual International Solid Freeform Fabrication Symposium—An Additive Manufacturing Conference, Austin, TX, USA, 7–9 August 2017. [Google Scholar]
- Gote, G.; Kamble, P.; Kori, S.; Karunakaran, K.P. Process Optimization of Segmented Object Manufacturing for Expandable Polystyrene Foam. In Advances in Lightweight Materials and Structures: Select Proceedings of ICALMS 2020; Praveen Kumar, A., Dirgantara, T., Krishna, P.V., Eds.; Springer Proceedings in Materials Book Series; Springer: Berlin/Heidelberg, Germany, 2020; Volume 8, pp. 695–704. [Google Scholar]
- Upadhyay, T.; Sivarupan, I.; El Mansori, M. 3D printing for rapid sand casting—A review. J. Manuf. Process. 2017, 29, 211–220. [Google Scholar] [CrossRef]
- Sivarupan, T.; Balasubramanian, N.; Saxena, P.; Nagarajan, D.; El Mansori, M.; Salonitis, K.; Jolly, M.; Dargusch, M.S. A review on the progress and challenges of binder jet 3D printing of sand moulds for advanced casting. Addit. Manuf. 2021, 40, 101889. [Google Scholar] [CrossRef]
- Tu, S.; Liu, F.; Li, G.; Jiang, W.; Liu, X.; Fan, Z. Fabrication and characterization of high-strength water-soluble composite salt core for zinc alloy die casting. Int. J. Adv. Manuf. Technol. 2018, 95, 505–512. [Google Scholar] [CrossRef]
- Findeisen, S.; Van der Auwera, R.; Heuser, M.; Woestmann, F. Gießtechnische Fertigung von E-Motorengehäusen mit interner Kühlung. Giesserei 2019, 106, 72–78. [Google Scholar]
- Gong, X.; Jiang, W.; Liu, F.; Yang, Z.; Guan, F.; Fan, Z. Effects of glass fiber size and content on microstructures and properties of KNO3-based water-soluble salt core for high pressure die casting. Int. J. Met. 2021, 15, 520–529. [Google Scholar] [CrossRef]
- Gong, X.; Liu, X.; Chen, Z.; Yang, Z.; Jiang, W.; Fan, Z. 3D printing of high-strength water-soluble salt cores via material extrusion. Int. J. Adv. Manuf. Technol. 2022, 118, 2993–3003. [Google Scholar] [CrossRef]
- Cornacchia, G.; Dioni, D.; Fccoli, M.; Gislon, C.; Solazzi, L.; Panvini, A.; Cecchel, S. Experimental and Numerical Study of an Automotive Component Produced with Innovative Ceramic Core in High Pressure Die Casting (HPDC). Metals 2019, 9, 217. [Google Scholar] [CrossRef]
- Koya, E.; Fukuda, Y.; Kitagawa, S. Manufacturing Technology for Hollow Structure Large Aluminum Parts Production by HPDC. SAE Int. J. Passeng. Cars Mech. Syst. 2015, 8, 65–72. [Google Scholar] [CrossRef]
- The Platform for the Entire Casting Industry. Available online: https://www.foundry-planet.com/d/innovative-sand-cores-with-watersoluble-binder-systems-for-the-non-ferrous-sector/ (accessed on 16 March 2023).
- Ams. Available online: https://www.automotivemanufacturingsolutions.com/bmw/bmw-landshut-is-now-using-new-multi-plate-die-casting-technology/42923.article (accessed on 16 March 2023).
- Winklhofer, J. Semi-Solid Casting of Aluminum from an Industrial Point of View. Solid State Phenom. 2019, 285, 24–30. [Google Scholar] [CrossRef]
- Imran, M.K.; Masood, S.H.; Brandt, M. Bimetallic dies with direct metal-deposited steel on Moldmax for high-pressure die casting application. Int. J. Adv. Manuf. Technol. 2011, 52, 855–863. [Google Scholar] [CrossRef]
- Armillotta, A.; Baraggi, R.; Fasoli, S. SLM tooling for die casting with conformal cooling channels. Int. J. Adv. Manuf. Technol. 2014, 71, 573–583. [Google Scholar] [CrossRef]
- Anand, A.; Nagarajan, D.; El Mansori, M.; Sivarupan, T. Integration of Additive Fabrication with High-Pressure Die Casting for Quality Structural Castings of Aluminium Alloys; Optimising Energy Consumption. Trans. Indian Inst. Met. 2023, 76, 347–379. [Google Scholar] [CrossRef]
- Lehmhus, D.; von Hehl, A.; Hausmann, J.; Kayvantash, K.; Alderliesten, R.; Hohe, J. New Materials and Processes for Transport Applications: Going Hybrid and Beyond. Adv. Eng. Mater. 2019, 21, 1900056. [Google Scholar] [CrossRef]
- Weise, J.; Hilbers, J.; Handels, F.; Lehmhus, D.; Busse, M.; Heuser, M. New core technology for light metal casting. Adv. Eng. Mater. 2019, 21, 1800608. [Google Scholar] [CrossRef]
- Kohlstädt, S. On Determining Lost Core Viability in High-Pressure Die Casting Using Computational Continuum Mechanics. Ph.D. Thesis, KTH Royal Institute of Technology, Stockholm, Sweden, 2019. [Google Scholar]
- Kohlstädt, S.; Vynnycky, M.; Jäckel, J. Towards the modelling of fluid-structure interactive lost core deformation in high-pressure die casting. Appl. Math. Model. 2020, 80, 319–333. [Google Scholar] [CrossRef]
- Kohlstädt, S.; Vynnycky, M.; Goeke, S. On the CFD Modelling of Slamming of the Metal Melt in High-Pressure Die Casting Involving Lost Cores. Metals 2021, 11, 78. [Google Scholar] [CrossRef]
- Fuchs, B.; Eibisch, H.; Körner, C. Core Viability Simulation for Salt Core Technology in High-Pressure Die Casting. Int. J. Met. 2013, 7, 39–45. [Google Scholar] [CrossRef]
- Jelínek, P.; Adámková, E. Lost Cores for High Pressure Die Casting. Arch. Foundry Eng. 2014, 14, 101–104. [Google Scholar] [CrossRef]
- Kallien, L. Salzkerne im Druckguss. Available online: https://www.hs-aalen.de/uploads/publication/file/9730/2016-Salzkerne_im_Druckguss.pdf (accessed on 26 April 2023).
- Pierri, D.; Roos, H.J.; Padovan, S. Verfahren zur Herstellung von Salzkernen. European Patent Application EP 2647451 A1, 4 April 2012. [Google Scholar]
- Fabbroni, M. Lost Core—Industrieller Prozesspfad für Hochwertige Salzkerne: Das Salz in der Suppe. Available online: https://automobilkonstruktion.industrie.de/allgemein/das-salz-in-der-suppe/ (accessed on 26 April 2023).
- Becker, M. Hohle Aluminiumstrukturbauteile Durch Salzkerne im Druckguss. Ph.D. Thesis, TU Clausthal, Clausthal, Germany, 2021. [Google Scholar]
- Gong, X.; Xiao, X.; Liu, X.; Fan, Z. Fabrication of high-strength salt cores for manufacturing hollow aluminum alloy die castings. Mater. Manuf. Process. 2023, 38, 188–196. [Google Scholar] [CrossRef]
- Serghini, A. Konzept zum Einsatz von verlorenen Kernen im HPDC. In Proceedings of the 3. VDI-Fachkonferenz Gießtechnik und E-Mobilität, Bremen, Germany, 18–19 October 2022. [Google Scholar]
- Reberger, E. Entwicklung von mehrschichtigen Sandkernen für den Druckguss. Giesserei 2023, 110, 68. [Google Scholar]
- Michels, H.; Bünck, M.; Bührig-Polaczek, A. Suitability of lost cores in rheocasting process. Trans. Nonferrous Met. Soc. China 2010, 20, s948–s953. [Google Scholar] [CrossRef]
- Lehmhus, D.; Weise, J.; Baumeister, J.; Peroni, L.; Scapin, M.; Fichera, C.; Avalle, M.; Busse, M. Quasi-static and Dynamic Mechanical Performance of Glass Microsphere- and Cenosphere-based 316L Syntactic Foams. Procedia Mater. Sci. 2014, 4, 383–387. [Google Scholar] [CrossRef]
- Szlancsik, A.; Katona, B.; Kemény, A.; Károly, D. On the Filler Materials of Metal Matrix Syntactic Foams. Materials 2019, 12, 2023. [Google Scholar] [CrossRef] [PubMed]
- Hobaica, E.C.; Cook, S.D. The Characteristics of Syntactic Foams Used for Buoyancy. J. Cell. Plast. 1968, 4, 143–148. [Google Scholar] [CrossRef]
- Gupta, N.; Zeltmann, S.; Schunmugasamy, V.C.; Pinisetty, D. Applications of Polymer Matrix Syntactic Foams. JOM 2014, 66, 245–254. [Google Scholar] [CrossRef]
- Gupta, N.; Rohatgi, P.K. (Eds.) Metal Matrix Syntactic Foams, 1st ed.; DEStech Publications, Inc.: Lancaster, PA, USA, 2015. [Google Scholar]
- Pille, D.; Soltmann, C.; Lehmhus, D.; Heuser, M.; Horeis, R.; Peters, M. Kollabierbare Kerne: Ein neuer Ansatz für den Aluminium-Feinguss? Giesserei 2023, 110, 89–94. [Google Scholar]
- Ziaee, M.; Crane, N.B. Binder jetting: A review of process, materials, and methods. Addit. Manuf. 2019, 28, 781–801. [Google Scholar] [CrossRef]
- Chowdhury, S.; Yadaiah, N.; Prakash, C.; Ramakrishna, S.; Dixit, S.; Gupta, L.R.; Buddhi, D. Laser powder bed fusion: A state-of-the-art review of the technology, materials, properties & defects, and numerical modelling. J. Mater. Res. Technol. 2022, 20, 2109–2172. [Google Scholar]
- Azar, A.S.; Diplas, S. Fundamental aspects of processing multi-metallic components using additive manufacturing technologies. Eur. J. Mater. 2022, 2, 234–364. [Google Scholar] [CrossRef]
- Hasanov, S.; Alkunte, S.; Rajeshirke, M.; Gupta, A.; Hseynov, O.; Fidan, I.; Alifui-Segbaya, F.; Rennie, A. Review on Additive Manufacturing of Multi-Material Parts: Progress and Challenges. J. Manuf. Process. Mater. Process. 2021, 6, 4. [Google Scholar] [CrossRef]
- Mussatto, A. Research progress in multi-material laser-powder bed fusion additive manufacturing: A review of the state-of-the-art techniques for depositing multiple powders with spatial selectivity in a single layer. Results Eng. 2022, 16, 100769. [Google Scholar] [CrossRef]
- Gibson, I.; Rosen, D.; Stucker, B. (Eds.) Directed Energy Deposition Processes. In Additive Manufacturing Technologies; Springer: New York, NY, USA, 2015. [Google Scholar] [CrossRef]
- Mudge, R.P.; Wald, N.R. Laser engineered net shaping advances additive manufacturing and repair. Weld. J. 2007, 86, 44–48. [Google Scholar]
- Deirmina, F.; Peghini, N.; AlMangour, B.; Grzesiak, D.; Pellizzari, M. Heat treatment and properties if a hot work tool steel fabricated by additive manufacturing. Mater. Sci. Eng. A 2019, 753, 109–121. [Google Scholar] [CrossRef]
- Nandwana, P.; Kannan, R.; Siddel, D. Microstructural evolution during binder jet additive manufacturing of H13 tool steel. Addit. Manuf. 2020, 36, 101534. [Google Scholar]
- Klocke, F.; Arntz, K.; Teli, M.; Winands, K.; Wegener, M.; Oliari, S. State-of-the-art Laser Additive Manufacturing for Hot-work Tool Steels. Procedia CIRP 2017, 63, 58–63. [Google Scholar] [CrossRef]
- Bohlen, A.; Freiße, H.; Hunkel, M.; Vollertsen, F. Additive manufacturing of tool steel by laser metal deposition. Procedia CIRP 2018, 74, 192–195. [Google Scholar] [CrossRef]
- Popovich, A.; Sufiiarov, V.; Polozov, I.; Borisov, E.; Masaylo, D.; Orlov, A. Microstructure and mechanical properties of additive manufactured copper alloy. Mater. Lett. 2016, 179, 38–41. [Google Scholar] [CrossRef]
- Kumar, A.Y.; Wang, J.; Bai, Y.; Huxtable, S.T.; Williams, C.B. Impacts of process-induced porosity on material properties of copper made by binder jetting additive manufacturing. Mater. Des. 2019, 182, 108001. [Google Scholar] [CrossRef]
- Jadhav, S.D.; Goossens, L.; Kinds, Y.; Van Hooreweder, B.; Vanmeensel, K. Laser-based powder bed fusion additive manufacturing of pure copper. Addit. Manuf. 2021, 42, 101990. [Google Scholar] [CrossRef]
- Gobran, H. Herstellungsverfahren und Verwendung für ein Wolframlegierungsprodukt—Method of Preparation and Use for a Tungsten Alloy Product. European Patent EP 3 643 429 B1, 13 January 2021. [Google Scholar]
- Adams, T.-E.; Mayr, P. The Path from Arc Welding to Additive Manufacturing of Multi-material Parts Using Directed Energy Deposition. Berg. Huettenmann. Monatsh. 2022, 167, 318–324. [Google Scholar] [CrossRef]
- Treutler, K.; Wesling, V. The Current State of Research ofWire Arc Additive Manufacturing (WAAM): A Review. Appl. Sci. 2021, 11, 8619. [Google Scholar] [CrossRef]
- Shah, M.; Patel, D.R.; Pande, S. Additive manufacturing integrated Casting—A review. Mater. Proc. 2022, 62, 7199–7203. [Google Scholar] [CrossRef]
- Wen, S.; Shen, Q.; Wei, Q.; Yan, C.; Zhu, W.; Shi, Y.; Yang, J.; Shi, Y. Material optimization and post-processing of sand moulds manufactured by the selective laser sintering of binder-coated Al2O3 sands. J. Mater. Process. Technol. 2015, 225, 93–102. [Google Scholar] [CrossRef]
- Yang, L.; Tang, S.-Y.; Fan, Z.-T.; Jiang, W.-M.; Liu, X.-W. Rapid Casting Technology based on Selective Laser Sintering. China Foundry 2021, 18, 296–306. [Google Scholar] [CrossRef]
- Sama, S.R.; Wang, J.; Manogharan, G. Non-conventional mold design for metal casting using 3D sand-printing. J. Manuf. Process. 2018, 34, 765–775. [Google Scholar] [CrossRef]
- Sama, S.R.; Badamo, T.; Lynch, P.; Manogharan, G. Novel sprue designs in metal casting via 3D sand-printing. Addit. Manuf. 2019, 25, 563–578. [Google Scholar] [CrossRef]
- Walker, J.; Harris, E.; Lynagh, C.; Beck, A.; Vuksanovich, B.; Conner, B.; MacDonald, E.; Lonardo, R.; Thiel, J.; Rogers, K. 3D printed smart molds for sand casting. Int. J. Met. 2018, 12, 785–796. [Google Scholar] [CrossRef]
- Walker, J.; Prokop, A.; Lynagh, C.; Vuksanovich, B.; Conner, B.; Rogers, K.; Thiel, J.; MacDonald, E. Real-time process monitoring of core shifts during metal casting with wireless sensing and 3D sand printing. Addit. Manuf. 2019, 27, 54–60. [Google Scholar] [CrossRef]
- Vuksanovich, B.; Herberger, C.; Daugherty, T.; Waker, J.; Cortes, P.; MacDonald, E.; Jaric, D.; Gaffney, S.; Lonardo, R.; Clancy, M.; et al. Wireless ventilation measurement in 3D printed sand molds. Int. J. Met. 2022, 16, 80–92. [Google Scholar] [CrossRef]
- Thiel, J.; Ravi, S.; Bryant, N. Advancements in materials for three-dimensional printing of molds and cores. Int. J. Met. 2017, 11, 3–13. [Google Scholar] [CrossRef]
- Kaiser, M. Binder jetting additive manufacturing of sand moulds/cores and its newest developments—Machine and material. In Proceedings of the 1st Congress for intelligent Combining of Design, Casting, Computer Simulation, Checking and Cyclic Behaviour for efficient Cast Components (InCeight Casting C8), Darmstadt, Germany, 2–3 March 2021; pp. 89–97. [Google Scholar]
- Zaretskiy, L. Modified silicate binders new developments and applications. Int. J. Met. 2016, 10, 88–99. [Google Scholar] [CrossRef]
- Vykoukal, M.; Burian, A.; Prerovska, M. GEOPOL. The Innovated Environment Friendly Inorganic Binder System. Arch. Foundry Eng. 2019, 19, 109–116. [Google Scholar] [CrossRef]
- Danko, R.; Kmita, A.; Holtzer, M.; Danko, J.; Lehmhus, D.; Tapola, S. Development of inorganic binder systems to minimise emissions in ferrous foundries. Sustain. Mater. Technol. 2023, 37, e00666. [Google Scholar]
- Ramakrishnan, R.; Griebel, B.; Volk, W.; Günther, D.; Günther, J. 3D Printing of Inorganic Sand Moulds for Casting Applications. Adv. Mater. Res. 2014, 1018, 441–449. [Google Scholar] [CrossRef]
- Pacurar, R.; Berce, P.; Nemes, O.; Baila, D.-I.; Stan, D.S.; Oarcea, A.; Popister, F.; Borzan, C.M.; Maricic, S.; Legutko, S.; et al. Cast Iron Parts Obtained in Ceramic Molds Produced by Binder Jetting 3D Printing—Morphological and Mechanical Characterization. Materials 2021, 14, 4502. [Google Scholar] [CrossRef] [PubMed]
- Lynch, P.; Hasbrouck, C.R.; Wilck, J.; Kay, M.; Manogharan, G. Challenges and Opportuinties to integrate the oldest and newest manufacturing processes; metal casting and additive manufacturing. Rapid Prototyp. J. 2020, 26, 1145–1154. [Google Scholar] [CrossRef]
- Lee, C.W.; Chua, C.K.; Cheah, C.M.; Tan, L.H.; Feng, C. Rapid investment casting: Direct and indirect approaches via fused deposition modelling. Int. J. Adv. Manuf. Technol. 2004, 23, 93–101. [Google Scholar]
- Cheah, C.M.; Chua, C.K.; Lee, C.W.; Feng, C.; Totong, K. Rapid prototyping and tooling techniques: A review of applications for rapid investment casting. Int. J. Adv. Manuf. Technol. 2005, 25, 308–320. [Google Scholar] [CrossRef]
- Zocca, A.; Colombo, P.; Gomes, C.M.; Günster, J. Additive Manufacturing of Ceramics: Issues, Potentialities, and Opportunities. J. Am. Cer. Soc. 2015, 98, 1983–2001. [Google Scholar] [CrossRef]
- Lakhdar, Y.; Tuck, C.; Binner, J.; Terry, A.; Goodridge, R. Additive manufacturing of advanced ceramic materials. Prog. Mater. Sci. 2021, 116, 100736. [Google Scholar] [CrossRef]
- Kumar, P.; Ahuja, I.P.S.; Singh, R. Application of fusion deposition modelling for rapid investment casting—A review. Int. J. Mater. Eng. Innov. 2012, 3, 204–227. [Google Scholar] [CrossRef]
- Hafsa, M.N.; Ibrahim, M.; Wahab, M.S.; Zahid, M.S. Evaluation of FDM pattern with ABS and PLA material. Appl. Mech. Mater. 2014, 465–466, 55–59. [Google Scholar] [CrossRef]
- Andrew, K.; Weaver, J.M. Using Wax Filament Additive Manufacturing for Low-Volume Investment Casting. In Proceedings of the Solid Freeform Fabrication 2019: Proceedings of the 30th Annual International Solid Freeform Fabrication Symposium—An Additive Manufacturing Conference, Austin, TX, USA, 12–14 August 2019. [Google Scholar]
- Votava, F.; Bricin, D. Options for Implementing Additive Manufacturing Technologies into a Foundry for Small Castings. IOP Conf. Ser. Mater. Sci. Eng. 2022, 1243, 012007. [Google Scholar] [CrossRef]
- Badanova, N.; Perveen, A.; Talamona, D. Study of SLA Printing Parameters Affecting the Dimensional Accuracy of the Pattern and Casting in Rapid Investment Casting. J. Manuf. Mater. Process. 2022, 6, 109. [Google Scholar] [CrossRef]
- Nguyen, T.T.; Tran, V.T.; Pham, T.H.N.; Nguyen, V.-T.; Thanh, N.C.; Thi, H.M.N.; Duy, N.V.A.; Thanh, D.N.; Nguyen, V.T.T. Influences of Material Selection, Infill Ratio, and Layer Height in the 3D Printing Cavity Process on the Surface Roughness of Printed Patterns and Casted Products in Investment Casting. Micromachines 2023, 14, 395. [Google Scholar] [CrossRef] [PubMed]
- Frost, M.; Hong, I. Utilization of Resin-Based Additive Manufacturing for Investment Casting. Available online: https://digitalcommons.calpoly.edu/mesp/637/ (accessed on 6 May 2023).
- Nkhasi, N.P.; Preez, W.B.D.; van der Walt, J.G. Investment casting of Aluminium alloy A356 using Primecast® and PMMA additive manufacturing materials for sacrificial patterns. In Proceedings of the 19th Annual International RAPDASA Conference, Johannesburg, South Africa, 7–9 November 2018; pp. 22–31. [Google Scholar]
- Bae, C.-J.; Kim, D.; Halloran, J.W. Mechanical and kinetic studies on the refractory fused silica of integrally cored ceramic mold fabricated by additive manufacturing. J. Eur. Ceram. Soc. 2019, 39, 618–623. [Google Scholar] [CrossRef]
- Klocke, F.; Ader, C. Direct Laser Sintering of Ceramics. In Proceedings of the Solid Freeform Fabrication 2003: Proceedings of the 30th Annual International Solid Freeform Fabrication Symposium—An Additive Manufacturing Conference, Austin, TX, USA, 4–6 August 2003. [Google Scholar]
- Liu, H.; Su, G.; Li, Y. Effect of wall structure on the dimensional accuracy of shell mould prepared by slurry extrusion-based additive manufacturing process. Int. J. Cast Met. Res. 2022, 35, 102–110. [Google Scholar] [CrossRef]
- Bosse, S.; Lehmhus, D. On Concepts and Challenges of Realizing Material-Integrated Intelligent Systems. In Material-Integrated Intelligent Systems—Technology and Applications; Bosse, S., Lehmhus, D., Lang, W., Busse, M., Eds.; Wiley-VCH Verlag: Weinheim, Germany, 2018; pp. 1–28. [Google Scholar]
- Hribernik, K.A.; Pille, C.; Jeken, O.; Thoben, K.-D.; Windt, K.; Busse, M. Autonomous control of intelligent products in beginning of life processes. In Proceedings of the 7th International Conference on Product Lifecycle Management, Bremen, Germany, 12–14 July 2010. [Google Scholar]
- Lehmhus, D.; Busse, M. Structural Health Monitoring. In Material-Integrated Intelligent Systems—Technology and Applications; Bosse, S., Lehmhus, D., Lang, W., Busse, M., Eds.; Wiley-VCH Verlag: Weinheim, Germany, 2018; pp. 531–594. [Google Scholar]
- Wuest, T.; Hribernik, K.; Thoben, K.-D. New Marktes/Opportunities through Availability of Product Life Cycle Data. In Material-Integrated Intelligent Systems—Technology and Applications; Bosse, S., Lehmhus, D., Lang, W., Busse, M., Eds.; Wiley-VCH Verlag: Weinheim, Germany, 2018; pp. 613–628. [Google Scholar]
- Lehmhus, D.; Wuest, T.; Wellsandt, S.; Bosse, S.; Kaihara, T.; Thoben, K.-D.; Busse, M. Cloud-based automated design and additive manufacturing: A usage data-enabled paradigm shift. Sensors 2015, 15, 32079–32122. [Google Scholar] [CrossRef]
- Carvalho, T.P.; Soares, F.A.A.M.N.; Vita, R.; Francisco, R.d.P.; Basto, J.P.; Alcala, S.G.S. A systematic literature review of machine learning methods applied to predictive maintenance. Comput. Ind. Eng. 2019, 137, 106024. [Google Scholar] [CrossRef]
- Zonta, T.; da Costa, C.A.; da Rosa Righi, R.; de Lima, M.J.; da Trindade, E.S.; Li, G.P. Predictive maintenance in the Industry 4.0: A systematic literature review. Comput. Ind. Eng. 2020, 150, 106889. [Google Scholar] [CrossRef]
- Amafabia, D.M.; Montalvao, D.; David-West, O.; Haritos, G. A Review of Structural Health Monitoring Techniques as Applied to Composite Structures. Struct. Damage Health Monit. 2017, 11, 91–147. [Google Scholar]
- Moghaddam, M.K.; Salas, M.; Koerdt, M.; Brauner, C.; Hübner, M.; Lehmhus, D.; Lang, W. Sensor Integration in Fiber-REinforced Polymers. In Material-Integrated Intelligent Systems—Technology and Applications; Bosse, S., Lehmhus, D., Lang, W., Busse, M., Eds.; Wiley-VCH Verlag: Weinheim, Germany, 2018; pp. 161–200. [Google Scholar]
- Güemes, A.; Fernandez-Lopez, A.; Pozo, A.R.; Sierra-Perez, J. Structural Health Monitoring for Advanced Composite Structures: A Review. J. Compos. Sci. 2020, 4, 13. [Google Scholar] [CrossRef]
- Lehmhus, D.; Rahn, T.; Pille, C.; Busse, M. Integrating Electronic Components, Sensors and Actuators in Cast Metal Components: An Overview of the State of the Art. Springer Lect. Notes Netw. Syst. 2023, 556, 350–361. [Google Scholar]
- Busse, M.; Woestmann, F.-J.; Müller, T.; Melz, T.; Spies, P. Intelligente Gussteile—Einsatz adaptronischer Komponenten in Kombination mit Gussteilen. Giesserei 2006, 93, 48–53. [Google Scholar]
- Lang, W.; Jakobs, F.; Tolstosheeva, E.; Sturm, H.; Ibragimov, A.; Kesel, A.; Lehmhus, D.; Dicke, U. From embedded sensors to sensorial materials—The road to function scale integration. Sens. Actuators A Phys. 2011, 171, 3–11. [Google Scholar] [CrossRef]
- Bonollo, F.; Gramegna, N. The MUSIC Guide to the Key-Parameters in High Pressure Die Casting; Enginsoft, SpA; Assomet Servizi srl: Milano, Italy, 2014; ISBN 978-8887786-10-1. [Google Scholar]
- Carlsson, R.; Elmquist, L.; Johansson, C. Cast metal with intelligence—From passive to intelligent cast components. In Proceedings of the 8th ECCOMAS Thematic Conference on Smart Structures and Materials (SMART 2017), Madrid, Spain, 5–8 June 2017. [Google Scholar]
- Carlsson, R.; Elmquist, L.; Thore, A.; Ahrentorp, F.; Johansson, C.; Israelsson, B. Connecting sensors inside smart castings. In Proceedings of the 7th International Symposium on Aircraft Materials (ACMA2018), Compiègne, France, 24–26 April 2018. [Google Scholar]
- Elmquist, L.; Carlsson, R.; Johansson, C. Cast Iron Components with Intelligence. Mater. Sci. Forum 2018, 925, 512–519. [Google Scholar] [CrossRef]
- Carlsson, R.; Elmquist, L.; Thore, A.; Johansson, C.; Ahrentorp, F.; Schaller, V.; Johannisson, P.; Israelsson, B.; Törnvall, M.; Zander, P. Sensors integrated inside metal castings verified to respond to force. In Proceedings of the 9th ECCOMAS Thematic Conference on Smart Structuresand Materials (SMART 2019), Paris, France, 8–11 July 2019. [Google Scholar]
- Weraneck, K.; Heilmeier, F.; Lindner, M.; Graf, M.; Jakobi, M.; Volk, W.; Roths, J.; Koch, A.W. Strain Measurement in Aluminium Alloy during the Solidification Process using Embedded Fibre Bragg Gratings. Sensors 2016, 16, 1853. [Google Scholar] [CrossRef] [PubMed]
- Lindner, M.; Tunc, E.; Weraneck, K.; Heilmeier, F.; Volk, W.; Jakobi, M.; Koch, A.W.; Roths, J. Regenerated Bragg Grating Sensor Array for Temperature Measurements During an Aluminum Casting Process. IEEE Sens. J. 2018, 18, 5352–5360. [Google Scholar] [CrossRef]
- Heilmeier, F.; Koos, R.; Weraneck, K.; Lindner, M.; Jakobi, M.; Roths, J.; Koch, A.W.; Volk, W. In-situ strain measurements in the plastic deformation regime inside casted parts using fibre-optical strain sensors. Prod. Eng. 2019, 13, 351–360. [Google Scholar] [CrossRef]
- Lindner, M.; Stadler, A.; Hamann, G.; Fischer, B.; Jakobi, M.; Heilmeier, F.; Bauer, C.; Volk, W.; Koch, A.W.; Roths, J. Fiber Bragg Sensors Embedded in Cast Aluminum Parts: Axial Strain and Temperature Response. Sensors 2021, 21, 1680. [Google Scholar] [CrossRef]
- Bian, Q.; Bauer, C.; Stadler, A.; Jakobi, A.; Koch, A.W.; Roths, J. Multipoint Temperature Monitoring Based on a Regenerated Fiber Bragg Grating Temperature Sensor Array in Copper Casting. In Proceedings of the SPIE 11591, Sensors and Smart Structures Technologies for Civil, Mechanical, and Aerospace Systems 2021, Online, 22–26 March 2021; Volume 11591. [Google Scholar] [CrossRef]
- Lehmhus, D.; Klatt, A.; Struss, A.; Cen, M.; Pille, C.; Hepp, E.; Middelmann, O.; Lang, W.; Busse, M. Metal casting meets smart systems—Integrating sensors and electronics as contribution to the digitalization of the foundry industry. In Proceedings of the 2nd Congress for Intelligent Combining of Design, Casting, Computer Simulation, Checking and Cyclic Behaviour for Efficient Cast Components (InCeight Casting C8), Darmstadt, Germany, 6–8 March 2023. [Google Scholar]
- Lehmhus, D.; Cen, M.; Struss, A.; de Rijk, T.; Pille, C.; Lang, W. Thick Film Sensor Manufacturing Techniques for Realization of Smart Components via Low Pressure Die Casting. J. Phys. Conf. Ser. 2024, 2692, 012007. [Google Scholar] [CrossRef]
- Pille, C.; Biehl, S.; Busse, M. Encapsulating piezoresistive thin film sensors based on amorphous diamond-like carbon in aluminum castings. In Proceedings of the 1st Intern. Symposium on System-Integrated Intelligence (SysInt 2012), Hanover, Germany, 27–29 June 2012. [Google Scholar]
- Dumstorff, G.; Pille, C.; Tiedemann, R.; Busse, M.; Lang, W. Smart aluminum components: Printed sensors for integration into aluminum during high-pressure casting. J. Manuf. Process. 2017, 26, 166–172. [Google Scholar] [CrossRef]
- Ibragimov, A.; Pleteit, H.; Pille, C.; Lang, W. Micromachined Thermogenerator Directly Integrated into Metal Parts: Technological Aspects of the Embedding Process. In Proceedings of the 1st Joint International Symposium on System-Integrated Intelligence, Hanover, Germany, 27–29 June 2012; pp. 192–194. [Google Scholar]
- Ibragimov, A.; Pleteit, H.; Pille, C.; Lang, W. A Thermoelectric Energy Harvester Directly Embedded into Casted Aluminum. Electron Device Lett. IEEE 2012, 33, 233–235. [Google Scholar] [CrossRef]
- Schwankl, M.; Rübner, M.; Singer, R.F.; Körner, C. Integration of PZT-ceramic modules using hybrid structures in high pressure die casting. Procedia Mater. Sci. 2013, 2, 166–172. [Google Scholar] [CrossRef]
- Schwankl, M.; Rübner, M.; Flössel, M.; Gebhardt, S.; Michaelis, A.; Singer, R.F.; Koerner, C. Active functionality of piezoceramic modules integrated in aluminum high pressure die castings. Sens. Actuators A Phys. 2014, 207, 84–90. [Google Scholar] [CrossRef]
- Schwankl, M.; Kimme, S.; Pohle, C.; Drossel, W.-G.; Körner, C. Active vibration damping in structural aluminum die castings via piezoelectricity—Technology and characterization. Adv. Eng. Mater. 2015, 17, 969–975. [Google Scholar] [CrossRef]
- Altimus, J.C.; Johnson, V.D. Remote Identification of Metal Castings. Trans. Am. Foundrymens Soc. 1998, 106, 605–608. [Google Scholar]
- Pille, C. In-process embedding of piezo sensors and RFID transponders into cast parts for autonomous manufacturing logistics. In Proceedings of the Smart Systems Integration (SSI) 2010, Como, Italy, 23–24 March 2010. [Google Scholar]
- Campbell, J. Review of computer simulation versus casting reality. In Proceedings of Modeling of Casting, Welding and Advanced Solidication Processes VII; Cross, M., Campbell, S., Eds.; The Minerals, Metals and Materials Society: London, UK, 1995; pp. 907–913. [Google Scholar]
- Flender, E.; Sturm, J. Thirty years of casting process simulation. Int. J. Met. 2010, 4, 7–23. [Google Scholar] [CrossRef]
- Jolly, M.; Katgerman, L. Modelling of defects in aluminium cast products. Prog. Mater. Sci. 2022, 123, 100824. [Google Scholar] [CrossRef]
- Cleary, P.W.; Ha, J.; Alguine, V.; Nguyen, T. Flow modelling in casting processes. Appl. Math. Model. 2002, 26, 171–190. [Google Scholar] [CrossRef]
- Cleary, P.W.; Ha, J. Three-dimensional smoothed particle hydrodynamics simulation of high pressure die casting of light metal components. J. Light Met. 2002, 2, 169–183. [Google Scholar] [CrossRef]
- Cleary, P.W.; Ha, J.; Prakash, M.; Nguyen, T. 3D SPH flow predictions and validation for high pressure die casting of automotive components. Appl. Math. Model. 2006, 30, 1406–1427. [Google Scholar] [CrossRef]
- Khan, M.A.A.; Sheikh, A.K. Simulation tools enhancing metal casting productivity and quality: A review. J. Eng. Manuf. 2016, 230, 1799–1817. [Google Scholar] [CrossRef]
- Khan, M.A.A.; Sheikh, A.K. A comparative study of simulation software for modelling metal casting processes. Int. J. Simul. Model 2018, 17, 197–209. [Google Scholar] [CrossRef] [PubMed]
- Khan, M.A.A.; Sheikh, A.K. Virtual Casting: State of the Art in Metal Casting Simulation Tools. J. Eng. Res. 2018, 15, 142–154. [Google Scholar]
- Danylchenko, L. Comparative Analysis of Computer Systems for Casting Processes Simulation. In Proceedings of the International Conference on Advanced Applied Energy and Information Technologies, Ternopil, Ukraine, 15–17 December 2021; pp. 105–113. [Google Scholar]
- Dhodare, A.S.; Ravanan, P.M.; Dodiya, N. A Review on Interfacial Heat Transfer Coefficient during Solidification in Casting. Int. J. Eng. Res. Technol. 2017, 6, 464–467. [Google Scholar]
- Kouki, Y.; Müller, S.; Schuchardt, T.; Dilger, K. Development of an instrumented test tool for the determination of heat transfer coefficients for die casting applications. Metals 2020, 10, 1206. [Google Scholar] [CrossRef]
- Wollf, N.; Zimmermann, G.; Vroomen, U.; Bührig-Polaczek, A. A statistical evaluation of the influence of different material and process parameters on the heat transfer coefficient in gravity die casting. Metals 2020, 10, 1367. [Google Scholar] [CrossRef]
- Cao, L.; Liaon, D.; Sun, F.; Chen, T.; Teng, Z.; Tang, Y. Prediction of gas entrapment defects during zinc alloy high-pressure die casting based on a gas-liquid multiphase flow model. Int. J. Adv. Manuf. Technol. 2018, 94, 807–815. [Google Scholar] [CrossRef]
- Jolly, M. Casting simulation: How well do reality and virtual casting match? State of the art review. Int. J. Cast Met. Res. 2002, 14, 303–313. [Google Scholar] [CrossRef]
- Liu, Z.-K. Computational thermodynamics and its applications. Acta Mater. 2020, 200, 745–792. [Google Scholar] [CrossRef]
- Liu, Z.K. Thermodynamics and its prediction and CALPHAD modeling: Review, state of the art, and perspectives. Calphad 2023, 82, 102580. [Google Scholar] [CrossRef]
- The Microstructure Evolution Simulation Software. Available online: https://micress.rwth-aachen.de/ (accessed on 16 February 2024).
- Chen, R.; Xu, Q.; Liu, B. Cellular automaton simulation of three-dimensional dendrite growth in Al-7Si-Mg ternary aluminum alloys. Comput. Mater. Sci. 2015, 105, 90–100. [Google Scholar] [CrossRef]
- Gu, C.; Lu, Y.; Cinkilic, E.; Miao, J.; Klarner, A.; Yan, X.; Luo, A.A. Predicting grain structure in high pressure die casting of aluminum alloys: A coupled cellular automaton and process model. Comput. Mater. Sci. 2019, 161, 64–75. [Google Scholar] [CrossRef]
- Jakumeit, J.; Behnken, H.; Laqua, R.; Eiken, J.; Brachmann, J. Multi-scale simulation of hybrid light metal structures produced by high pressure die casting. IOP Conf. Ser. Mater. Sci. Eng. 2020, 861, 012035. [Google Scholar] [CrossRef]
- Wang, Y.; Zhang, Y.; Liu, X.; Wang, J.; Xie, X.; Jiang, J.; Liu, J.; Liu, H.; Wu, Y.; Dong, S.; et al. Simulation of Microstructure Evolution in Mg Alloys by Phase-Field Methods: A Review. Crystals 2022, 12, 1305. [Google Scholar] [CrossRef]
- Kovacevic, L.; Oliveira, R.; Terek, P.; Terek, V.; Pristavec, J.; Skoric, B. The Direction of Foundry Industry: Toward the Foundry 4.0. J. Mechatron. Autom. Identif. Technol. 2020, 5, 23–28. [Google Scholar]
- Sikorski, S.; Dieckhues, G.W.; Sturm, J.C. Systematic Optimization of Aluminum Sand Casting Gating Systems. Am Foundry Society. 2012. Available online: https://www.magmasoft.de/export/shared/MAGMA/common/_galleries/_downloads/2012_Systematic-optimization-aluminum-gating-system.pdf (accessed on 13 February 2022).
- Dojka, R.; Jezierski, J.; Campbell, J. Optimized Gating System for Steel Castings. J. Mater. Eng. Perform. 2018, 27, 5152–5163. [Google Scholar] [CrossRef]
- Dojka, R.; Jezierski, J.; Tiedje, N.S. Geometric Form of Gating System Elements and Its Influence on the Initial Filling Phase. J. Mater. Eng. Perform. 2019, 28, 3922–3928. [Google Scholar] [CrossRef]
- Yun, J.; Lee, S.B. Influence of Aluminum Die-Cast Rotor Porosity on the Efficiency of Induction Machines. IEEE Trans. Magn. 2018, 54, 8104905. [Google Scholar] [CrossRef]
- Pille, C.; Mäurer, G. A Look into the hidden—The First Complete CT of Cast Rotors in Electric Asynchronous Motors. Insp. Int. 2020, 2, 12–13. [Google Scholar]
- Blair, M.; Monroe, R.; Beckermann, C.; Hardin, R.; Carlson, K.; Monroe, C. Predicting the Occurrence and Effects of Defects in Castings. JOM 2005, 57, 29–34. [Google Scholar] [CrossRef]
- Blondheim, D., Jr. Systems Understanding of High Pressure Die Casting Process and Data with Machine Learning Applications. Ph.D. Thesis, Colorado State University, Fort Collins, CO, USA, 2021. [Google Scholar]
- Blondheim, D., Jr.; Monroe, A. Macro porosity formation: A study in high pressure die casting. Int. J. Met. 2022, 16, 330–341. [Google Scholar] [CrossRef]
- Lauterbach, B.; Nigge, K.-M. Beurteilung von Volumendefekten—Struktursimulation auf Basis der Computertomografie. Giesserei 2021, 108, 48–53. [Google Scholar]
- Zhang, Y.; Lordan, E.; Dou, K.; Wang, S.; Fan, Z. Influence of porosity characteristics on the variability in mechanical properties of high pressure die casting (HPDC) AlSi7MgMn alloys. J. Manuf. Process. 2019, 56, 500–509. [Google Scholar] [CrossRef]
- Nourian-Avval, A.; Fatemi, A. Characterization and Analysis of Porosities in High Pressure Die Cast Aluminum by Using Metallography, X-Ray Radiography, and Micro-Computed Tomography. Materials 2020, 13, 3068. [Google Scholar] [CrossRef]
- Andrieux, F.; Sun, D.; Burblies, A. Multiscale Approach for the Damage Modeling of an Aluminum Casting Alloy with Stochastic Character. Mater. Sci. Forum 2017, 877, 680–685. [Google Scholar] [CrossRef]
- Goodfellow, I.J.; Pouget-Abadiey, J.; Mirza, M.; Xu, B.; Warde-Farley, D.; Ozairz, S.; Courville, A.; Bengiox, Y. Generative Adversarial Nets. In Proceedings of the 27th International Conference on Neural Information Processing Systems (ACM), Montreal, QC, Canada, 8–13 December 2014; pp. 2672–2680. [Google Scholar]
- Gui, J.; Sun, Z.; Wen, Y.; Tao, D.; Ye, J. A Review on Generative Adversarial Networks: Algorithms, Theory and Applications. IEEE Trans. Knowl. Data Eng. 2023, 35, 3313–3332. [Google Scholar] [CrossRef]
- Raghavendra, A.K.M.; Lacourt, L.; Marcin, L.; Maurel, V.; Proudhon, V. Generation of synthetic microstructures containing casting defects: A machine learning approach. Nat. Sci. Rep. 2023, 13, 11852. [Google Scholar] [CrossRef]
- Andrieux, F.; Fehrenbach, C.; Oeser, S.; Sun, D.-Z.; Ebrahimi, A.; Heuser, M.; Lehmhus, D.; Struss, A. Modellierung der Einflüsse von Mikrodefekten auf das Versa-Gensverhalten von Al-Druckgusskomponenten mit Stochastischem Aspekt für die Crashsimulation; FAT-Schriftenreihe Band 338; Forschungsvereinigung Automobiltechnik e. V. (FAT): Berlin, Germany, 2020. [Google Scholar]
- Kong, D.; Sun, D.-Z.; Yang, B.; Qiao, H.; Wie, C.; Lang, Y.; Song, H.; Gao, J. Characterization and modeling of damage behavior of a casting aluminum wheel considering inhomogeneity of microstructure and microdefects. Eng. Fail. Anal. 2023, 145, 107018. [Google Scholar] [CrossRef]
- Campbell, J. An Overview of the Effects of Bifilms on the Structure and Properties of Cast Alloys. Metall. Mater. Trans. B 2006, 37B, 857–863. [Google Scholar] [CrossRef]
- Gopalan, R.; Prabhu, N.K. Oxide bifilms in aluminium alloy castings—A review. Mater. Sci. Technol. 2011, 27, 1757–1769. [Google Scholar] [CrossRef]
- El-Sayed, M.A.; Griffiths, W.D. Hydrogen, biofilms and mechanical properties of Al castings. Int. J. Cast Met. Res. 2014, 27, 282–287. [Google Scholar] [CrossRef]
- Gyarmati, G.; Fegyverneki, G.; Mende, T.; Tokar, M. Characterization of the double oxide film content of liquid aluminum alloys by computed tomography. Mater. Charact. 2019, 157, 109925. [Google Scholar] [CrossRef]
- Garcia-Perez, A.; Gomez Silva, M.J.; de la Escalera Huesco, A. Automated Defect Recognition of Casting Defects Using Neural Networks. J. Nondestruct. Eval. 2022, 41, 11. [Google Scholar] [CrossRef]
- Bosse, S.; Lehmhus, D. Automated Detection of Hidden Damages and Impurities in Aluminum Die Casting Materials and Fibre-Metal Laminates Using Low-Quality X-ray Radiography, Synthetic X-ray Data Augmentation by Simulation, and Machine Learning. arXiv 2023, arXiv:2311.12041. [Google Scholar]
- Hen, B.; Wei, Z.; Perron, L.; Ibarra Castanedo, C.; Maldague, X. Towards Enhancing Automated Defect Recognition (ADR) in Digital X-ray Radiography Applications: Synthesizing Training Data through X-ray Intensity Distribution Modeling for Deep Learning Algorithms. Information 2024, 15, 16. [Google Scholar] [CrossRef]
- Fuchs, P.; Kröger, T.; Garbe, S. Defect detection in CT scans of cast aluminum parts: A machine vision perspective. Neurocomputing 2021, 453, 85–96. [Google Scholar] [CrossRef]
- Mery, D. Aluminum Casting Inspection Using Deep Learning: A Method Based on Convolutional Neural Networks. J. Nondestruct. Eval. 2020, 39, 12. [Google Scholar] [CrossRef]
- Mery, D. Aluminum Casting Inspection using Deep Object Detection Methods and Simulated Ellipsoidal Defects. Mach. Vis. Appl. 2021, 32, 72. [Google Scholar] [CrossRef]
- Ghansiyal, S.; Yi, L.; Simon, P.M.; Klar, M.; Müller, M.M.; Glatt, M.; Aurich, J.C. Anomaly detection towards zero defect manufacturing using generative adversarial networks. Procedia CIRP 2023, 120, 1457–1462. [Google Scholar] [CrossRef]
- Lee, J.H.; Noh, S.D.; Kim, H.-J.; Kang, Y.-S. Implementation of Cyber-Physical Production Systems for Quality Prediction and Operation Control in Metal Casting. Sensors 2018, 18, 1428. [Google Scholar] [CrossRef]
- Wang, X.; Yew, A.W.W.; Ong, S.K.; Nee, A.Y.C. Enhancing smart shop floor management with ubiquitous augmented reality. Int. J. Prod. Res. 2020, 58, 2352–2367. [Google Scholar] [CrossRef]
- Mourtzis, D.; Siatras, V.; Angelopoulos, J. Real-time remote maintenance support based on augmented reality (AR). Appl. Sci. 2020, 10, 1855. [Google Scholar] [CrossRef]
- Mourtzis, D.; Angelopoulos, J.; Panopoulos, N. Challenges and Opportunities for Integrating Augmented Reality and Computational Fluid Dynamics Modeling under the Framework of Industry 4.0. Procedia CIRP 2022, 106, 215–220. [Google Scholar] [CrossRef]
- Ravi, B. Metal Casting 4.0: Closing the loop between design and manufacturing. Trans. Indian Inst. Met. 2021, 74, 1017–1028. [Google Scholar] [CrossRef]
- Lipp, J.; Rudack, M.; Vroomen, U.; Bührig-Polaczek, A. When to Collect What? Optimizing Data Load via Process-driven Data Collection. In Proceedings of the 22nd International Conference on Enterprise Information Systems (ICEIS 2020), Prague, Czech Republic, 5–7 May 2020; Volume 1, pp. 220–225. [Google Scholar] [CrossRef]
- Kopper, A.E. Knowledge Creation via Data Analytics in a High Pressure Die Casting Operation. Ph.D. Thesis, Worcester Polytechnic Institute, Worcester, MA, USA, 2020. [Google Scholar]
- Rudack, M.; Rath, M.; Vroomen, U.; Bührig-Polaczek, A. Towards a Data Lake for High Pressure Die Casting. Metals 2022, 12, 349. [Google Scholar] [CrossRef]
- OPC. Unified Architecture—Part 1: Overview and Concepts. IEC TR 62541-1:2022. 2022. Available online: https://reference.opcfoundation.org/Core/Part1/v105/docs/ (accessed on 7 March 2024).
- Profanter, S.; Tekat, A.; Dorofeev, K.; Rickert, M.; Knoll, A. OPC UA versus ROS, DDS, and MQTT: Performance Evaluation of Industry 4.0 Protocols. In Proceedings of the 2019 IEEE International Conference on Industrial Technology (ICIT), Melbourne, VIC, Australia, 13–15 February 2019; pp. 955–962. [Google Scholar] [CrossRef]
- Riedel, E. MQTT protocol for SME foundries: Potential as an entry point into industry 4.0, process transparency and sustainability. Procedia CIRP 2022, 105, 601–606. [Google Scholar] [CrossRef]
- Yang, C.; Zheng, Y.; Tu, X.; Ala-Laurinaho, R.; Autiosalo, J.; Seppänen, O.; Tammi, K. Ontology-based knowledge representation of industrial production workflow. Adv. Eng. Inform. 2023, 58, 102185. [Google Scholar] [CrossRef]
- Sanfilippo, E.M.; Kitamura, Y.; Young, R.I.M. Formal Ontologies in Manufacturing. Appl. Ontol. 2019, 14, 1. [Google Scholar] [CrossRef]
- Nilsson, J.; Sandin, F. Semantic Interoperability in Industry 4.0: Survey of Recent Developments and Outlook. In Proceedings of the 2018 IEEE 16th International Conference on Industrial Informatics (INDIN), Porto, Portugal, 18–20 July 2018; pp. 127–132. [Google Scholar] [CrossRef]
- Kluska-Nawarecka, S.; Smolarek-Grzyb, A.; Wilk-Kołodziejczyk, D.; Adrian, A. Knowledge Representation of Casting Metal Defects by Means of Ontology. Arch. Foundry Eng. 2007, 7, 75–78. [Google Scholar]
- Kluska-Nawarecka, S.; Nawarecki, E.; Dobrowolski, G.; Haratym, A.; Regulski, K. The Platform for Semantic Integration and Sharing Technological Knowledge on Metal Processing. Comput. Methods Mater. Sci. 2013, 13, 304–312. [Google Scholar]
- Ameri, F.; Urbanovsky, C.; McArthur, C. A systematic approach to developing ontologies for manufacturing service modeling. In Proceedings of the 2nd International Workshop on Ontology and Semantic web for Manufacturing (OSEMA 2012), Graz, Austria, 24–25 July 2012. [Google Scholar]
- Singh, K.N.; Behera, R.K.; Mantri, J.K. Big Data Ecosystem: Review on Architectural Evolution. In Emerging Technologies in Data Mining and Information Security; Abraham, A., Dutta, P., Mandal, J., Bhattacharya, A., Dutta, S., Eds.; Book Series Advances in Intelligent Systems and Computing; Springer: Singapore, 2019; Volume 813. [Google Scholar] [CrossRef]
- Pennekamp, J.; Glebke, R.; Henze, M.; Meisen, T.; Quix, C.; Hai, R.; Gleim, L.; Niemietzky, P.; Rudack, M.; Knape, S.; et al. Towards an infrastructure enabling the internet of production. In Proceedings of the 2019 IEEE International Conference on Industrial Cyber Physical Systems (ICPS), Taipei, Taiwan, 6–9 May 2019; pp. 31–37. [Google Scholar]
- Lin, J. The Lambda and the Kappa. IEEE Internet Comput. 2017, 17, 60–66. [Google Scholar] [CrossRef]
- Cerezo, F.; Cuesta, C.E.; Moreno-Herranz, J.C.; Vela, B. Deconstructing the Lambda Architecture: An Experience Report. In Proceedings of the 2019 IEEE International Conference on Software Architecture Companion (ICSA-C), Hamburg, Germany, 25–26 March 2019; pp. 196–201. [Google Scholar] [CrossRef]
- Mathis, C. Data Lakes. Datenbank Spektrum 2017, 17, 289–293. [Google Scholar] [CrossRef]
- Rix, M.; Kujat, B.; Meisen, T.; Jeschke, S. An agile information processing framework for high pressure die casting applications in modern manufacturing systems. Procedia CIRP 2016, 41, 1084–1089. [Google Scholar] [CrossRef]
- Lipp, J.; Rath, M.; Rudack, M.; Vroomen, U.; Bührig-Polaczek, A. Flexible OPC UA Data Load Optimizations on the Edge of Production. In Enterprise Information Systems, Proceedings of the 22nd International Conference (ICEIS 2020), Virtual Event, 5–7 May 2020; Revised Selected Papers; Springer: Cham, Switzerland, 2020; pp. 43–61. [Google Scholar]
- Gramegna, N.; Greggio, F.; Bonollo, F. Smart Factory Competitiveness Based on Real Time Monitoring and Quality Predictive Model Applied to Multi-stages Production Lines. In Proceedings of the IFIP International Conference on Advances in Production Management Systems (APMS), Novi Sad, Serbia, 30 August 2020; pp. 185–196. [Google Scholar]
- Kim, J.; Lee, J.Y. Data-analytics-based factory operation strategies for die-casting quality enhancement. Int. J. Adv. Manuf. Technol. 2022, 119, 3865–3890. [Google Scholar] [CrossRef]
- Fernandez, A.; Garcia, S.; Herrera, F.; Chawla, N.V. SMOTE for Learning from Imbalanced Data: Progress and Challenges, Marking the 15-year Anniversary. J. Artif. Intell. Res. 2018, 61, 863–905. [Google Scholar] [CrossRef]
- Kim, J.S.; Kim, J.; Lee, J.Y. Die-Casting Defect Prediction and Diagnosis System using Process Condition Data. Procedia Manuf. 2020, 51, 359–364. [Google Scholar] [CrossRef]
- Karniadakis, G.E.; Kevrekidis, I.G.; Lu, L.; Perdikaris, P.; Wang, S.; Yang, L. Physics-informed machine learning. Nat. Rev. Phys. 2021, 3, 422–440. [Google Scholar] [CrossRef]
- Ebrahimi, A.; Fritsching, U.; Heuser, M.; Lehmhus, D.; Struß, A.; Toenjes, A.; von Hehl, A. A digital twin approach to predict and compensate distortion in a High Pressure Die Casting (HPDC) process chain. Procedia Manuf. 2020, 52, 144–149. [Google Scholar] [CrossRef]
- Jones, D.; Snider, C.; Nassehi, A.; Yon, J.; Hicks, B. Characterising the Digital Twin: A systematic literature review. CIRP J. Manuf. Sci. Technol. 2020, 29, 36–52. [Google Scholar] [CrossRef]
- Al-Sehrawy, R.; Kumar, B.; Watson, R. A mulit-dimensional digital twin use cases classification framework. In Proceedings of the 2021 European Conference on Computing in Construction, Online, 26–28 July 2021. [Google Scholar] [CrossRef]
- Moiceanu, G.; Paraschiv, G. Digital Twin and Smart Manufacturing in Industries: A Bibliometric Analysis with a Focus on Industry 4.0. Sensors 2022, 22, 1388. [Google Scholar] [CrossRef]
- Kritzinger, W.; Karner, M.; Traar, G.; Henjes, J.; Sihn, W. Digital Twin in manufacturing: A categorical literature review and classification. IFAC PapersOnLine 2018, 51, 1016–1022. [Google Scholar] [CrossRef]
- He, B.; Bai, K.-J. Digital twin-based sustainable intelligent manufacturing: A review. Adv. Manuf. 2021, 9, 1–21. [Google Scholar] [CrossRef]
- Shen, Z.J.M.; Wang, L.; Deng, T. Digital Twin: What It Is, Why Do It, Related Challenges, and Research Opportunities for Operations Research. 2021. Available online: https://papers.ssrn.com/sol3/papers.cfm?abstract_id=3777695 (accessed on 19 February 2024).
- Kendrik, L.Y.H.; Zheng, P.; Chen, C.-H. A state-of-the-art survey of Digital Twin: Techniques, engineering product lifecycle management and business innovation perspectives. J. Intell. Manuf. 2020, 31, 1313–1337. [Google Scholar] [CrossRef]
- Melesse, T.Y.; Di Pasquale, V.; Riemma, S. Digital Twin Models in Industrial Operations: A Systematic Literature Review. Procedia Manuf. 2020, 42, 267–272. [Google Scholar] [CrossRef]
- Huang, Z.; Shen, Y.; Li, J.; Fey, M.; Brecher, C. A survey on AI-driven Digital Twins in Industry 4.0: Smart manufacturing and advanced robotics. Sensors 2021, 21, 6340. [Google Scholar] [CrossRef] [PubMed]
- Benner, P.; Faßbender, H. Model order reduction: Techniques and tools. In Encyclopedia of Systems and Control; Springer: London, UK, 2013; pp. 1–10. [Google Scholar]
- Baur, U.; Benner, P.; Feng, L. Model Order Reduction for Linear and Nonlinear Systems: A System-Theoretic Perspective. Arch. Comput. Methods Eng. 2014, 21, 331–358. [Google Scholar] [CrossRef]
- Simpson, T.W.; Peplinski, J.D.; Koch, P.N.; Allen, J.K. Metamodels for computer-based engineering design: Survey and recommendations. Eng. Comput. 2001, 17, 129–150. [Google Scholar] [CrossRef]
- Anglada, E.; Boto, F.; Garcia de Cortazar, M.; Garmendia, I. Metamodels Development for High Pressure Die Casting of Aluminum Alloy. Metals 2021, 11, 1747. [Google Scholar] [CrossRef]
- Lucia, D.J.; Beran, P.S.; Silva, W.A. Reduced-order modeling: New approaches for computational physics. Prog. Aerosp. Sci. 2004, 40, 51–117. [Google Scholar] [CrossRef]
- Lu, K.; Jin, Y.; Chen, Y.; Yang, Y.; Hu, L.; Zhang, Z.; Li, Z.; Fu, C. Review for order reduction based on proper orthogonal decomposition and outlooks of applications in mechanical systems. Mech. Syst. Signal Process. 2019, 123, 264–297. [Google Scholar] [CrossRef]
- Chakrabarti, A.; Sukumar, R.P.; Jarke, M.; Rudack, M.; Buske, P.; Holly, C. Efficient Modeling of Digital Shadows for Production Processes: A Case Study for Quality Prediction in High Pressure Die Casting. In Proceedings of the 8th International Conference on Data Science and Analytics (DSAA), Porto, Portugal, 6–9 October 2021. [Google Scholar] [CrossRef]
- Liu, D.; Du, Y.; Chai, W.; Lu, C.Q.; Cong, M. Digital Twin and Data-Driven Quality Prediction of Complex Die-Casting Manufacturing. IEEE Trans. Ind. Inform. 2022, 18, 8119–8128. [Google Scholar] [CrossRef]
- Ktari, A.; El Mansori, M. Digital twin of functional gating system in 3D printed molds for sand casting using a neural network. J. Intell. Manuf. 2020, 33, 897–909. [Google Scholar] [CrossRef]
- Zhang, H.; Liu, X.; Ma, D.; Song, M.; Ludwig, A.; Kharicha, A.; Wu, M. Digital twin for directional solidification of a single-crystal turbine blade. Acta Mater. 2023, 244, 118579. [Google Scholar] [CrossRef]
- Doroshenko, V.S.; Kravchenko, V.P.; Tokova, O.V. Development of a digital twin of the technological process of consumable pattern casting using production data. Control Syst. Comput. 2020, 3, 41–49. [Google Scholar] [CrossRef]
- Fiedler, T.; Movahedi, N.; York, L.; Broxtermann, S. Functionally-graded metallic syntactic foams produced via particle pre-compaction. Metals 2020, 10, 314. [Google Scholar] [CrossRef]
- Gimmler, S.; Apel, M.; Bührig-Polaczek, A. Selection of dedicated as-cast microstructures in Zn-Al-Cu alloys for bearing applications supported by phase-field simulations. Metals 2020, 10, 1659. [Google Scholar] [CrossRef]
- Sama, S.R.; MacDonald, E.; Voigt, R.; Manogharan, G. Measurement of Metal Velocity in Sand Casting during Mold Filling. Metals 2019, 9, 1079. [Google Scholar] [CrossRef]
- Niu, R.; Li, B.; Liu, Z.; Bu, L.; Li, X.; Yang, X.; Tsukihashi, F. Experimental investigation of solidification in the cast mold with a consumable cooler introduced inside. Metals 2019, 9, 55. [Google Scholar] [CrossRef]
- Avila-Salgado, D.A.; Juarez-Hernandez, A.; Medina-Ortiz, F.; Banda, M.L.; Hernandez-Rodriguez, M.A.L. Influence of B and Nb additions and heat treatments on the mechanical properties of Cu-Ni-Co-Cr-Si alloy for high pressure die casting application. Metals 2020, 10, 602. [Google Scholar] [CrossRef]
- Avila-Salgado, D.A.; Juarez-Hernandez, A.; Cabral-Miramontes, J.; Camacho-Martinez, J.L. Strengthening Properties and Wear Resistance of the Cu-xNi-yCo-Cr-Si Alloy by Varying Ni/Co and Zr Addition. Lubricants 2021, 9, 96. [Google Scholar] [CrossRef]
- Wan, Y.; Li, M.; Chen, L.; Wu, Y.; Li, J.; Pan, H.; Zhong, W. Effect of final electromagnetic stirring parameters on central cross-sectional carbon concentration distribution of high-carbon square billet. Metals 2019, 9, 665. [Google Scholar] [CrossRef]
- Yan, W.; Zhang, Y.; Chen, W.; Li, J. Characteristics and formation tendency of freckle segregation in electroslag remelting of bearing steel. Metals 2020, 10, 246. [Google Scholar] [CrossRef]