This article introduces the paper 'Advances in Metal Casting Technology: A Review of State of the Art, Challenges and Trends—Part II: Technologies New and Revived' published by MDPI.
1. Overview:
- Title: Advances in Metal Casting Technology: A Review of State of the Art, Challenges and Trends—Part II: Technologies New and Revived
- Author: Dirk Lehmhus
- Publication Year: 2024
- Publishing Journal/Academic Society: Metals, MDPI
- Keywords: Metal Casting Technology, Review, State of the Art, Challenges, Trends, Technologies, New, Revived
![Figure 1. An overview of topics covered in the present text. The graphic shows the areas of interest discussed in the previously published first part of this editorial (PART I in the diagram, see [1]) as well as those focused on in this second part. While Part I concentrated on boundary conditions, Part II is technology oriented. (a) Figure 1. An overview of topics covered in the present text. The graphic shows the areas of interest discussed in the previously published first part of this editorial (PART I in the diagram, see [1]) as well as those focused on in this second part. While Part I concentrated on boundary conditions, Part II is technology oriented.](https://castman.co.kr/wp-content/uploads/image-1130-1024x509.webp)
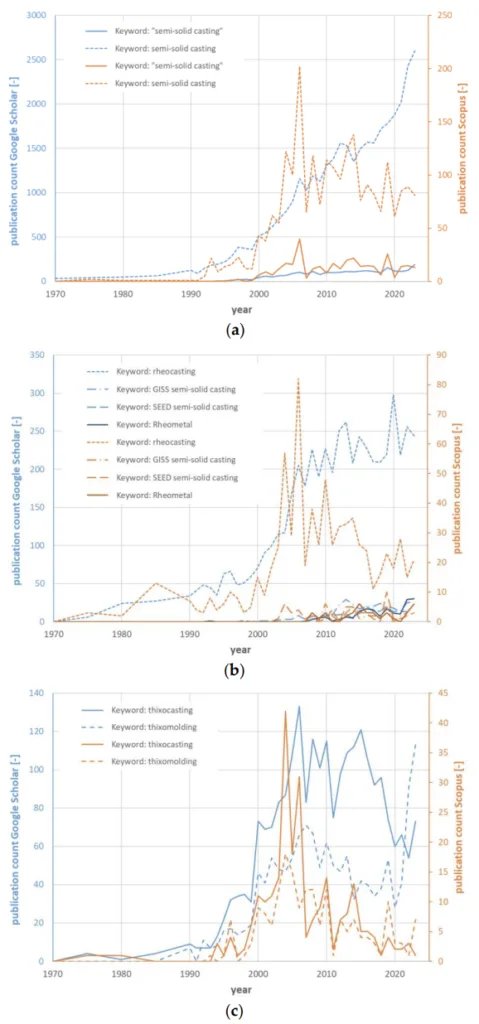
2. Abstracts or Introduction
The present text, as the second part of an editorial for the Special Issue "Advances in Metal Casting Technology," builds upon Part I published in November 2022. Part I provided an overview of the global metal casting industry, emphasizing market and product changes driven by factors like e-mobility and environmental pressures. This Part II shifts perspective to examine technological developments within the industry, categorizing them as general trends or responses to preceding challenges, encompassing both "technologies both new and revived." While acknowledging the impossibility of complete coverage, this review aims to offer "points of attack for further study." The final section will contextualize contributions to the Special Issue within the discussed technological fields. Consistent with Part I, a bias towards "high-pressure die casting (HPDC) of aluminum alloys" is acknowledged due to the author's expertise.
3. Research Background:
Background of the Research Topic:
The metal casting industry is in a state of flux, driven by "changes in markets and products, such as e-mobility, the associated advent of Gigacasting technology, or the increasing pressure on the casting industry to justify and minimize the environmental impact of its processes [1]." These evolving demands necessitate a review of technological advancements within the field. The cyclical nature of technological evolution, influenced by factors like "technology-centered models, such as the famed Gartner hype cycle [2-4], or more generally by economy-level observations, such as Kondratiev waves and all their relatives [5]," underscores the importance of periodically reassessing technologies, both new and those experiencing resurgence.
Status of Existing Research:
Part I of this editorial, published previously, has already "discussed in the preceding Part I of the text" the "changing markets and boundary conditions" affecting the casting industry. Existing research includes overviews of global metal casting trends and analyses of specific technologies like Gigacasting. Academic and industrial interest in specific technologies, such as "Semi-solid metal processing," is evidenced by publication trends in databases like Google Scholar and Scopus, as illustrated in "Figure 2." However, a comprehensive review focusing on both new and revived technologies, particularly in the context of current industry challenges, is warranted.
Necessity of the Research:
The "increasing pressure on the casting industry to justify and minimize the environmental impact of its processes [1]" and adapt to new market demands like e-mobility creates a "necessity" for foundries to explore and adopt advanced technologies. This review addresses this need by providing an overview of "technologies both new and revived," offering "readers with points of attack for further study" and aiding in strategic technology adoption decisions. Furthermore, understanding the cyclical nature of technology and the potential for "reemergence of technologies" due to "new ideas, new market needs, or the expiration of limiting patents" is crucial for long-term industry competitiveness.
4. Research Purpose and Research Questions:
Research Purpose:
The primary "purpose" of this review is to examine and summarize "technological developments within the industry that can either be seen as general trends or as responses to the preceding challenges; in other words, this text discusses technologies both new and revived." It aims to provide an expert-level handbook overview of these technologies, contextualizing them within the current state of the art in metal casting. A secondary purpose is to contextualize the contributions within the Special Issue "Advances in Metal Casting Technology" within the broader technological landscape discussed.
Key Research:
The "key research" areas explored in this review are:
- Technologies New and Revived: Specifically focusing on "Semi-solid Processing," "Compound & Hybrid Casting," "Complexity," and "Smart Castings" as depicted in "Figure 1."
- Semi-Solid Processing: Examining the renewed interest in rheocasting and thixomolding, highlighting the "slurry on demand" principle of rheocasting and its advantages over thixocasting. Detailed review of specific rheocasting methods like "Gas-Induced Semi-Solid (GISS)," "New Rheocasting (NRC)," "Rapid Slurry Formation (RSF, also known as RheoMetalTM)," "Swirled Enthalpy Equilibration Device (SEED)," and "Semi-Solid Rheocasting (SSRTM)."
- Compound and Hybrid Casting: Exploring the motivations and methods for joining materials by casting, including material joints, form fit, and force fit, with a focus on applications in lightweight design, design freedom, smart products, production efficiency, heat transfer, and electrical conductivity. Review of various material pairings and bonding techniques.
- Complexity: Analyzing the concept of complexity in castings, methods for achieving increased complexity through core technologies and additive manufacturing, and new core technologies like collapsible cores and additive manufacturing of cores, molds, and patterns.
- Smart Castings: Reviewing approaches to integrate sensors and electronic systems into castings, categorized by "simplify, distribute, harden and protect" principles, and examining various sensor types and applications.
- Virtual Worlds: Modelling, Simulation and Optimization: Discussing the state of the art in casting simulation, focusing on usability improvements, prediction of defects, and boundary condition understanding. Exploring data analytics, digital twins, and metamodels as key aspects of Industry 4.0 in casting.
Research Hypotheses:
As a review paper, there are no explicit research hypotheses. However, the implicit hypothesis is that these "technologies new and revived" offer viable solutions to the challenges and trends facing the metal casting industry, and that a structured review will provide valuable insights for experts in the field.
5. Research Methodology
Research Design:
This paper employs a descriptive review design. It is structured as an editorial review, drawing upon existing literature and the author's expert knowledge to provide a state-of-the-art overview of selected metal casting technologies. The "graphic shows the areas of interest discussed in the previously published first part of this editorial (PART I in the diagram, see [1]) as well as those focused on in this second part. While Part I concentrated on boundary conditions, Part II is technology oriented" as shown in "Figure 1."
Data Collection Method:
The data collection method is based on a comprehensive review of existing publications, patents, and industry resources related to metal casting technologies. The author utilizes databases like "Google Scholar or Scopus" to assess publication trends, as shown in "Figure 2," indicating academic activity in areas like semi-solid casting. The review also incorporates information from industry websites and technical literature, as evidenced by references to company websites like "Comptech" and "Rheinfelden Alloys."
Analysis Method:
The analysis method is qualitative and descriptive. The author categorizes and synthesizes information from the reviewed literature to identify key trends, challenges, and advancements in each technology area. The analysis is structured around the technology categories outlined in "Figure 1," providing a systematic overview of "Semi-solid Processing," "Compound & Hybrid Casting," "Complexity," and "Smart Castings." The author also uses comparative analysis to highlight the advantages and disadvantages of different technologies, such as rheocasting versus thixocasting, and various rheocasting methods.
Research Subjects and Scope:
The "research subjects" are primarily metal casting technologies, specifically focusing on "technologies both new and revived" relevant to current industry challenges and trends. The "scope" is limited to selected technologies, acknowledging that "it cannot possibly be complete." The review emphasizes "high-pressure die casting (HPDC) of aluminum alloys" due to the author's expertise, but also includes discussions of other casting processes like "gravity die casting," "low-pressure die casting (LPDC)," "sand casting," and "investment casting" where relevant to the technology being discussed. The geographical scope is global, considering research and industrial activities from various regions, including China and Europe.
6. Main Research Results:
Key Research Results:
- Semi-Solid Processing: Rheocasting is highlighted as a revived technology with advantages over thixocasting due to its "slurry on demand" principle, enabling the use of conventional alloys and material re-use. Various rheocasting methods (GISS, NRC, RSF/RheoMetalTM, SEED, SSRTM) are detailed, emphasizing their mechanisms for achieving semi-solid state and their respective benefits and drawbacks. Rheocasting offers advantages over HPDC including "Lower solidification shrinkage," "Laminar flow during mold filling," "Improved feeding efficiency," and "Lower thermal energy levels."
- Compound & Hybrid Casting: Compound and hybrid casting are presented as viable alternatives to Gigacasting for large structural components, offering lightweight design, design freedom, and integration of functionalities. Key principles for achieving stable bonds (material joints, form fit, force fit) are discussed, along with examples of material pairings and applications in e-mobility and structural components. "Figure 5" illustrates principles controlling strength in compound casting.
- Complexity: Additive manufacturing, particularly 3D sand printing, is identified as a key enabler for increased casting complexity, especially in core production. Collapsible cores are introduced as a novel approach for decoring. "Table 3" provides examples of approaches toward increasing complexity in different casting processes.
- Smart Castings: Integration of sensors and electronics into castings is reviewed as an emerging trend, categorized by "simplify, distribute, harden and protect" strategies. Various sensor types (wire-type, fiber-optic, piezoresistive, RFID) and applications in structural health monitoring and process control are discussed. "Figure 9" illustrates principles to enable sensor integration.
- Virtual Worlds: Modelling, Simulation and Optimization: Casting simulation is recognized as a mature technology, with ongoing advancements focused on usability, defect prediction, and boundary condition accuracy. Data analytics, digital twins, and metamodels are highlighted as key components of Industry 4.0 in casting, enabling process optimization and quality control. "Figure 12" illustrates the Lambda Architecture for data analytics.
Analysis of presented data:
- Publication Trends (Figure 2): Analysis of publication data from Google Scholar and Scopus ("Figure 2") reveals fluctuating but generally sustained academic interest in semi-solid casting technologies, with rheocasting showing a recent rise in Scopus data. Thixocasting publication counts show a decline after peaking in the 2000s and 2010s.
- Rheocasting Advantages (List): The listed advantages of rheocasting over HPDC highlight its potential for improved casting quality, reduced material waste, and enhanced process efficiency.
- Material Joints in Compound Casting (Figure 5): "Figure 5" visually categorizes different approaches to achieving strong bonds in compound casting, emphasizing the importance of infiltration and material interaction.
- Complexity Approaches (Table 3): "Table 3" provides a structured overview of various techniques for enhancing casting complexity, categorized by casting process and approach, showcasing the diverse strategies available.
- Sensor Integration Principles (Figure 9): "Figure 9" visually summarizes the four key principles for successful sensor integration in castings, providing a conceptual framework for smart casting design.
- Lambda Architecture (Figure 12): "Figure 12" illustrates the Lambda Architecture as a solution for balancing speed and accuracy in data analytics for casting processes, highlighting its layered approach to data processing and information delivery.
- Digital Twin Concept (Figure 14): "Figure 14" presents a conceptual workflow for implementing a digital twin in casting, integrating simulation, metamodeling, and real-time process data for quality management and process control.
Figure Name List:
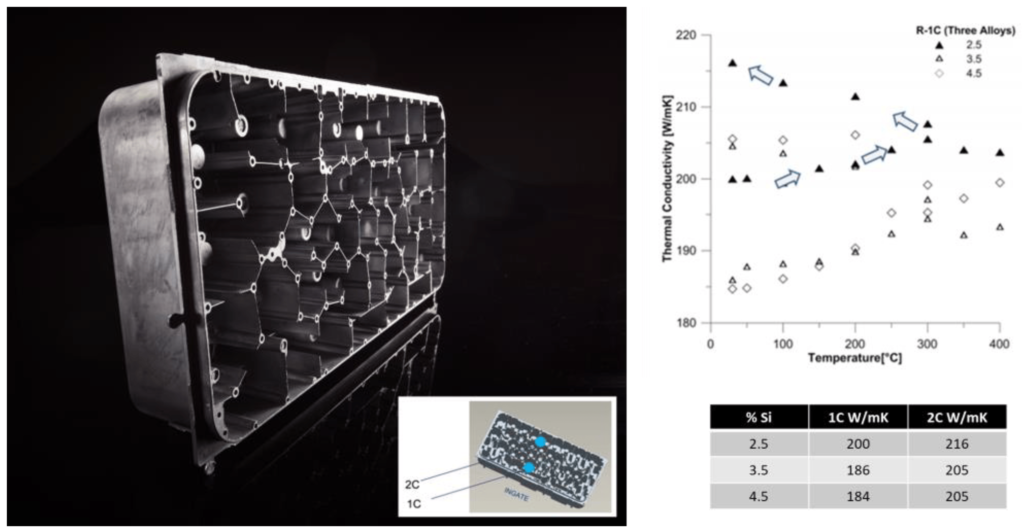
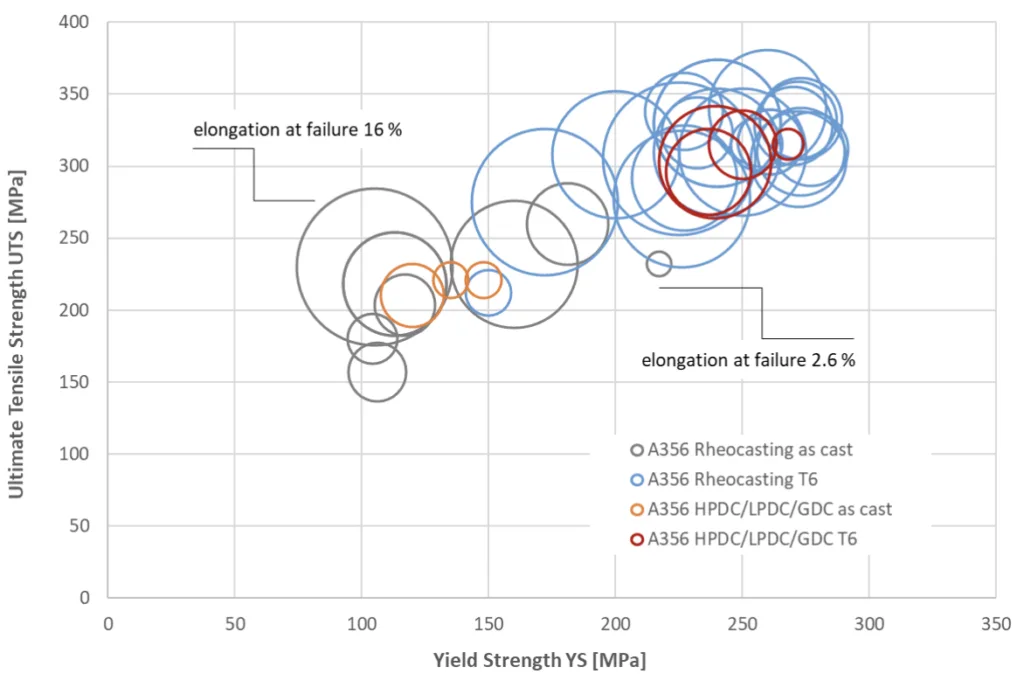
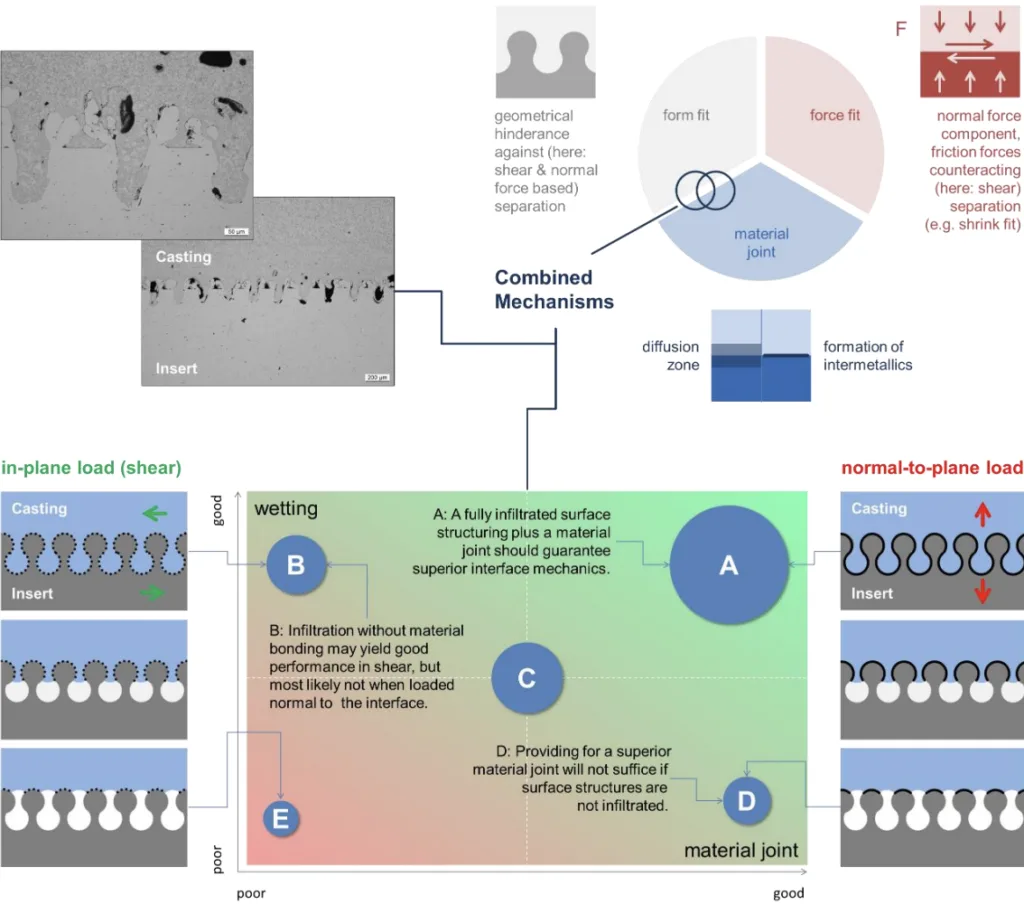
![Figure 6. Sample images of parts produced by compound (a–c) and hybrid casting (d); (a,b) AlSi7Mg0.3 LPDC subsize front axle carrier frame demonstrator with integrated EN AW6060 extrusion, general (a) and detail view (b); (c) AlSi9Cu3 HPDC e-motor housing demonstrator with integrated aluminum tubes as cooling channels, cast by ae group AG, Gerstungen, Germany; (d) aerospace secondary structure hybrid bracket combining a CFRP and an aluminum HPDC component [131] (all images by Fraunhofer IFAM)](https://castman.co.kr/wp-content/uploads/image-1134-1024x772.webp)
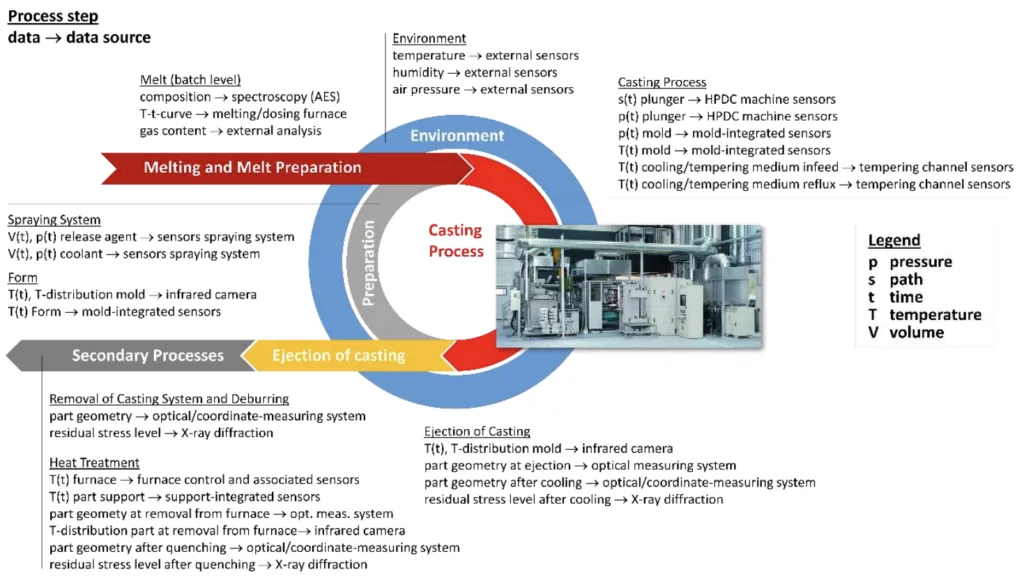
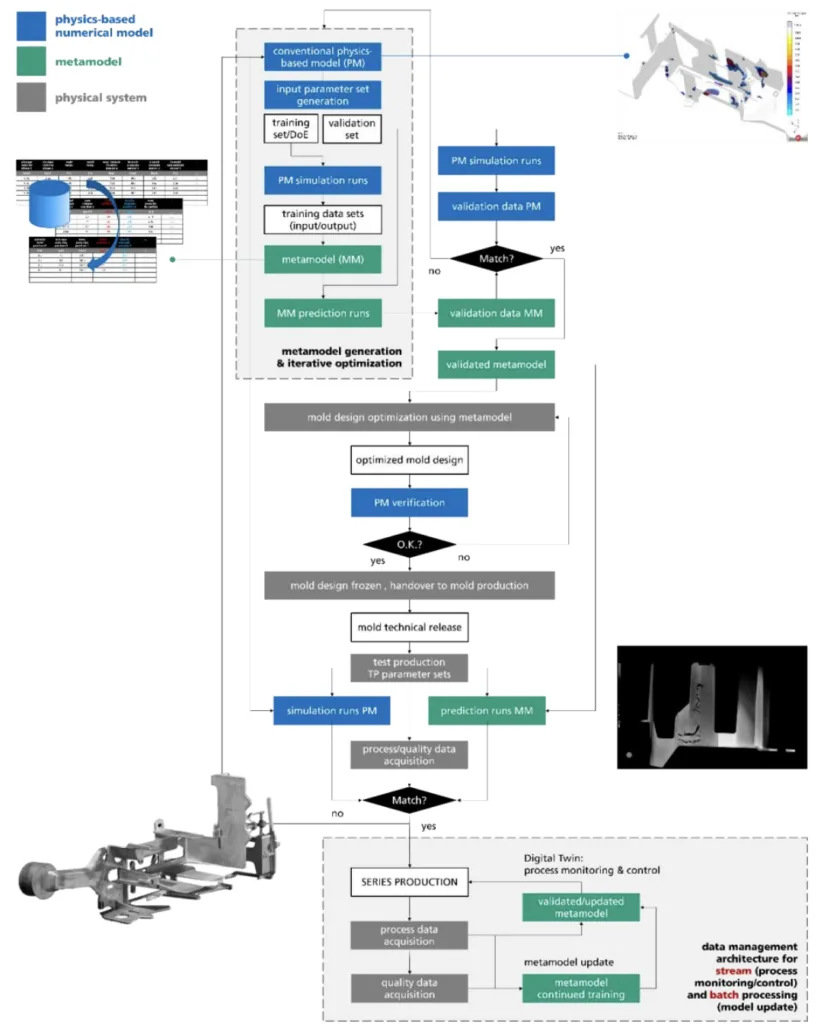
- Figure 1. An overview of topics covered in the present text.
- Figure 2. Publication numbers sourced from Google Scholar and Scopus on semi-solid casting technologies: (a) semi-solid casting in general, (b) rheocasting and (c) thixocasting process family examples.
- Figure 3. Radio filter produced by means of the RSF/RheoMetalTM process.
- Figure 4. Overview of rheocast and high-pressure die-cast aluminum and magnesium alloys in as-cast and T6 states in terms of yield strength, ultimate tensile strength and elongation at failure.
- Figure 5. An overview of principles controlling strength in compound casting.
- Figure 6. Sample images of parts produced by compound (a-c) and hybrid casting (d).
- Figure 7. The fundamental principle behind the concept of collapsible cores.
- Figure 8. (a) S-Max Pro sand printer as offered by ExOne, (b) examples of a printed core package.
- Figure 9. How to enable sensors and electronic systems to survive integration in metal castings—general principles.
- Figure 10. Schematic diagram describing a concept for constant product evolution relying on monitoring of in-service loads and conditions.
- Figure 11. Digitalization meets the HPDC challenge.
- Figure 12. The Lambda Architecture, an example of a compromise between securing accuracy and speed in data analytics.
- Figure 13. Ways of making use of data analytics—a general scheme.
- Figure 14. Combining advanced simulation and modelling and AI or MOR techniques to realize a digital twin in casting technology.
7. Conclusion:
Summary of Key Findings:
This review highlights the dynamic evolution of metal casting technology, driven by market demands and environmental concerns. "Semi-solid casting" is re-emerging as a viable alternative to conventional HPDC, with rheocasting offering distinct advantages. "Compound and hybrid casting" present solutions for large, multi-material components, while additive manufacturing is revolutionizing casting complexity, particularly in core production. "Smart castings" are emerging as a functional extension, integrating sensing and communication capabilities. "Virtual Worlds," encompassing advanced simulation, data analytics, and digital twins, are crucial for process optimization and quality control in the context of Industry 4.0.
Academic Significance of the Study:
This review provides a comprehensive and structured overview of key technological advancements in metal casting, offering a valuable resource for researchers and academics in the field. It synthesizes information from diverse sources, highlighting trends, challenges, and future research directions. The categorization of technologies and the analysis of their respective strengths and weaknesses contribute to a deeper understanding of the current state of metal casting technology.
Practical Implications:
For industry experts and foundry practitioners, this review offers strategic insights into technology adoption and development. It highlights the potential of revived technologies like rheocasting, provides guidance on implementing compound and hybrid casting, showcases the capabilities of additive manufacturing for complexity, and explores the opportunities presented by smart castings and Industry 4.0 concepts. The review emphasizes the importance of simulation and data analytics for optimizing casting processes and improving quality, providing a roadmap for foundries seeking to enhance their competitiveness and sustainability.
Limitations of the Study and Areas for Future Research:
The review acknowledges its limited scope, stating "it cannot possibly be complete." The inherent bias towards "high-pressure die casting (HPDC) of aluminum alloys" is also a limitation. Future research areas identified include:
- Further development and industrial implementation of rheocasting technologies.
- Addressing challenges in interface characterization and prediction for compound and hybrid casting.
- Expanding the application of additive manufacturing in core and mold production, and exploring new core materials like collapsible cores.
- Overcoming economic and technical barriers to widespread adoption of smart casting technologies.
- Advancing simulation techniques for defect prediction and material property forecasting, particularly for complex defect populations.
- Developing robust and user-friendly digital twin solutions for casting processes, integrating data analytics and metamodeling for real-time process control and optimization.
- Further research into physics-informed machine learning to enhance the efficiency and accuracy of data-driven models in casting.
8. References:
- [1] Lehmhus, D. Advances in Metal Casting Technology: A Review of State of the Art, Challenges and Trends—Part I: Changing Markets, Changing Products. Metals 2022, 12, 1959.
- [2] Steinert, M.; Leifer, L. Scrutinizing Gartner's Hype Cycle Approach. In PICMET 2010 Proceedings: Technology Management for Global Economic Growth; Kocaoglu, D.F., Anderson, T.R., Daim, T.U., Eds.; IEEE: Phuket, Thailand, 2010; pp. 1–13.
- [3] Campani, M.; Vaglio, A. A simple interpretation of scientific/technological research impact leading to hype-type evolution curves. Scientometrics 2015, 103, 75-83.
- [4] Gartner Hype Cycle. Available online: https://www.gartner.com/en/research/methodologies/gartner-hype-cycle (accessed on 4 January 2023).
- [5] Kondratjew, N.D. Die langen Wellen der Konjunktur. Arch. Für Sozialwissenschaft Und Sozialpolitik 1926, 56, 573–609.
- [6] Flemings, M.C.; Riek, R.C.; Young, K.P. Rheocasting. Mater. Sci. Eng. A 1976, 25, 103-117.
- [7] Young, R.M.K. The Processing of Metals as Semi-Solid Slurries. Ph.D. Thesis, University of Surrey, Guildford, UK, 1986.
- [8] Jorstad, J.L. Semi-Solid Metal Processing from an Industrial Perspective: The Best is Yet to Come! Solid State Phenom. 2016, 256, 9-14.
- [9] Czerwinski, F. Semisolid Processing-Origin of Magnesium Molding. In Magnesium Injection Molding; Springer: New York, NY, USA, 2008; pp. 81–147.
- [10] Decker, R.; LeBeau, S. Thixomolding. Adv. Mater. Process. 2008, 166, 28–29.
- [11] Huang, J.; Arbel, T.; Ligeski, L.; McCaffrey, J.; Kulkarni, S.; Jones, J.; Pollock, T.; Decker, R.; LeBeau, S. On Mechanical Properties & Microstructure of TTMP Wrought Mg Alloys. In Magnesium Technology 2010; Agnew, S., Ed.; The Minerals, Metals and Materials Society (TMS): Warrendale, PA, USA, 2010; pp. 489-493.
- [12] Zhu, Y.; Midson, S. The Status of Magnesium Injection Molding in China. Solid State Phenom. 2019, 285, 436-440.
- [13] Decker, R.; LeBeau, S.; Wilson, B.; Reagan, J.; Moskovich, N.; Bronfin, B. Thixomolding® at 25 years. Solid State Phenom. 2016, 256, 3-8.
- [14] Mohammed, N.N.; Omar, M.Z.; Salleh, M.S.; Alhawari, K.S.; Kapranos, P. Semisolid Metal Processing Techniques for Nondendritic Feedstock Production. Sci. World J. 2013, 2013, 752175.
- [15] Kapranos, P. Current State of Semi-Solid Net-Shape Die Casting. Metals 2019, 9, 1301.
- [16] Midson, S.P. Rheocasting processes for semi-solid casting of aluminum alloys. Die Cast. Eng. 2006, 50, 48-51.
- [17] Midson, S.P.; Jackson, A. A Comparison of Thixocasting and Rheocasting. In Proceedings of the 67th World Foundry Congress, Harrogate, UK, 5–7 June 2006; Institute of Cast Metals Engineers (ICME): Tipton, UK, 2006; pp. 22/1-22/10, ISBN 9781604236767.
- [18] Bakhtiyarov, S.; Siginer, D.A. Rheoprocessing of Semisolid Aluminum Alloys. In Encyclopedia of Aluminum and Its Alloys, 1st ed.; Totten, G.E., Tiryakioğlu, M., Kessler, O., Eds.; Taylor & Francis Group: London, UK, 2018.
- [19] Jarfors, A.E.W. A Comparison Between Semisolid Casting Methods for Aluminium Alloys. Metals 2020, 10, 1368.
- [20] Li, G.; Qu, W.-Y.; Cheng, L.; Guo, C.; Li, X.-G.; Xu, Z.; Hu, X.-G.; Li, D.-Q.; Lu, H.-X.; Zhu, Q. Semi-solid processing of aluminum and magnesium alloys: Status, opportunity and challenge in China. Trans. Nonferrous Met. Soc. China 2021, 31, 3255-3280.
- [21] Wannasin, J. Applications of Semi-solid Slurry Casting using the Gas Induced Semi-Solid Technique. Solid State Phenom. 2013, 192-193, 28-35.
- [22] Kaufmann, H.; Uggowitzer, P.J. Fundamentals of the New Rheocasting Process for Magnesium Alloys. Adv. Eng. Mater. 2001, 3, 963-967.
- [23] Wabusseg, H.; Kaufmann, H.; Wahlen, A.; Uggowitzer, P.J. Theoretische Grundlagen und praktische Umsetzung von New Rheocasting von Al-Legierungen. Druckguss-Praxis 2002, 1, 16–19.
- [24] Uggowitzer, P.J.; Kaufmann, H. Evolution of Globular Microstructure in New Rheocasting and Super Rheocasting Semi-Solid Slurries. Steel Res. Int. 2004, 75, 525-530.
- [25] Wessén, M.; Cao, H. The RSF Technology: A Possible Breakthrough for Semi-Solid Casting Processes. In Proceedings of the International Conference of High Tech Die Casting, Vicenza, Italy, 21-22 September 2006.
- [26] Ratke, L.; Sharma, A.; Kohli, D. The RSF Technology for Semi-Solid Casting Processes. Indian Foundry J. 2011, 57, 33–36.
- [27] Doutre, D.; Hay, G.; Wales, P.; Gabathuler, J.-P. SEED: A new process for semi-solid forming. Can. Metall. Q. 2004, 43, 265–272.
- [28] Yurko, J.A.; Martinez, R.A.; Flemings, M.C. The Use of Semi-Solid Rheocasting (SSR) for Aluminum Automotive Castings. SAE Trans. J. Mater. Manuf. 2003, 112, 119–123.
- [29] Serving the Platform of Tomorrow! Available online: https://comptech.se/ (accessed on 11 March 2023).
- [30] Li, M.; Du, W.; Elwany, A.; Pei, Z.; Ma, C. Metal binder jetting additive manufacturing: A literature review. J. Manuf. Sci. Eng. 2020, 142, 090810.
- [31] Zetterström, S.; Comptech AB, Skillingaryd, Sweden. Private communication, 2022.
- [32] Chauke, L.; Möller, H.; Curle, U.A.; Govender, G. Industrial heat treatment of R-HPDC A356 automotive brake callipers. Solid State Phenom. 2013, 192–193, 533-538.
- [33] Dey, A.K.; Poddar, P.; Singh, K.K.; Sahoo, K.L. Mechanical and wear properties of rheocast and conventional gravity die cast A356 alloy. Mater. Sci. Eng. A 2006, 435–436, 521–529.
- [34] Govender, G.; Ivanchev, L.; Jahajeeah, N.; Bëan, R. Application of CSIR Rheocasting Technology for the Production of an Automotive Component. Solid State Phenom. 2006, 116–117, 501-504.
- [35] Guo, H.M.; Yang, X.J.; Wang, J.X. Microstructure and mechanical properties of Al alloys by semi-solid processing with LSPSF technology. Mater. Sci. Forum 2009, 628–629, 477-482.
- [36] Gupta, R.; Sharma, A.; Pandel, U.; Ratke, L. Effect of heat treatment on microstructures and mechanical properties of A356 alloy cast through rapid slurry formation (RSF) process. Int. J. Cast Met. Res. 2017, 30, 283–292.
- [37] Möller, H.; Govender, G.; Stumpf, W.E.; Knutsen, R.D. Influence of temper condition on microstructure and mechanical properties of semisolid metal processed Al-Si-Mg alloy 356. Int. J. Cast Met. Res. 2009, 22, 417-421.
- [38] Möller, H.; Govender, G.; Stumpf, W.E. Comparison of the heat treatment response of SSM-HPDC 6082 and 6004 wrought alloys with A356 and F357 casting alloys. Mater. Sci. Forum 2011, 690, 53-56.
- [39] Anticorodal®—Unendlich Anpassungs Fähig. Available online: https://rheinfelden-alloys.eu/legierungen/anticorodal/ (accessed on 21 February 2022).
- [40] Rosso, M.; Peter, I.; Villa, R. Effect of T5 anfd T6 Heat Treatments Applied to Rheocast A356 Parts for Automotive Applications. Solid State Phenom. 2008, 141-143, 237-242.
- [41] Rosso, M. Thixocasting and rheocasting technologies, improvements going on. J. Achiev. Mater. Manuf. Eng. 2012, 54, 110–119.
- [42] Tahamtan, S.; Fadavi Boostani, A.; Nazemi, H. Mechanical properties and fracture behavior of thixoformed, rheocast and gravity-cast A356 alloy. J. Alloys Compd. 2009, 468, 107-114.
- [43] Zhang, L. Technology Innovation & Green Development—Chinese Foundry Industry Status and Outlook. Chinese Foundry Association. 2015. Available online: https://www.foundry-planet.com/fileadmin/redakteur/pdf-dateien/18.09.2015BRICS_2015_China.pdf (accessed on 13 May 2020).
- [44] Atkinson, H.V. Alloys for Semi-Solid Processing. Solid State Phenom. 2012, 192–193, 16-27.
- [45] Curle, U.A. Semi-solid near-net shape rheocasting of heat treatable wrought aluminum alloys. Trans. Nonferrous Met. Soc. China 2010, 20, 1719-1724.
- [46] Li, G.; Lu, H.; Hu, X.; Lin, F.; Li, X.; Zhu, Q. Current Progress in Rheoforming of Wrought Aluminum Alloys: A Review. Metals 2020, 10, 238.
- [47] Sauermann, R.; Friedrich, B.; Bünck, M.; Bührig-Polaczek, A.; Uggowitzer, P.J. Semi-Solid Processing of Tailored Aluminium-Lithium Alloys for Automotive Applications. Adv. Eng. Mater. 2007, 9, 253-258.
- [48] Bünck, M.; Küthe, F.; Bührig-Polaczek, A.; Arnold, A.; Friedrich, B.; Sauermann, R. Semi-solid Casting of High-reactive Wrought Alloys by Means of the Alloy AlLi2.1Mg5.5ScZr (AA1420*). Solid State Phenom. 2008, 141–143, 145-150.
- [49] Langlais, J.; Lemieux, A. The SEED Technology for Semi-solid Processing of Aluminum Alloys: A Metallurgical and Process Overview. Solid State Phenom. 2006, 116–117, 472-477.
- [50] Langlais, J.; Andrade, N.; Lemieux, A.; Chen, X.G.; Bucher, L. The Semi-Solid Forming of an Improved AA6061 Wrought Aluminum Alloy Composition. Solid State Phenom. 2008, 141-143, 511-516.
9. Copyright:
- This material is "Dirk Lehmhus"'s paper: Based on "Advances in Metal Casting Technology: A Review of State of the Art, Challenges and Trends—Part II: Technologies New and Revived".
- Paper Source: https://doi.org/10.3390/met14030334
This material was summarized based on the above paper, and unauthorized use for commercial purposes is prohibited.
Copyright © 2025 CASTMAN. All rights reserved.