This introduction paper is based on the paper "Minimizing the casting defects in high-pressure die casting using Taguchi analysis" published by "Scientia Iranica, Transactions B: Mechanical Engineering".
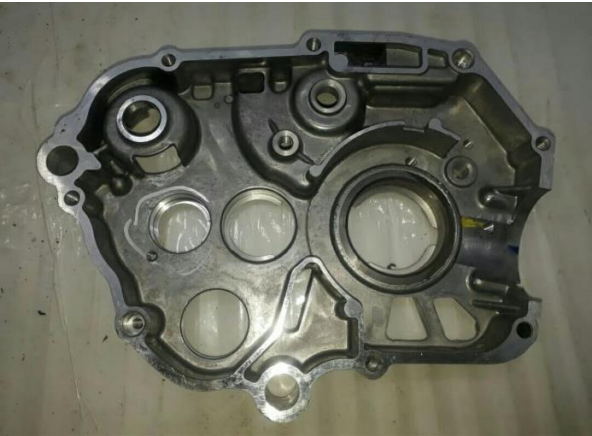
1. Overview:
- Title: Minimizing the casting defects in high-pressure die casting using Taguchi analysis
- Author: S. Tariq, A. Tariq, M. Masud, and Z. Rehman
- Year of publication: 2022 (Online publication May 2021, Issue publication 2022)
- Journal/academic society of publication: Scientia Iranica, Transactions B: Mechanical Engineering (Published by Sharif University of Technology)
- Keywords: High pressure die casting; Porosity; Design of experiment; Optimization; Casting defects.
2. Abstract:
Abstract. High-Pressure Die Casting (HPDC) is one of the major production processes of the automotive industry, widely used to manufacture geometrically complex nonferrous castings. The mechanical strength and microstructure of HPDC-manufactured products change with variation in several process parameters such as injection pressure, molten temperature, 1st and 2nd stage plunger velocities, cooling temperature, etc. Since these process parameters directly affect casting quality, their optimum combination is needed to maximize productivity of the process and minimize casting defects such as porosity, pinholes, blowholes, etc. Hence, to tackle this problem, an approach is presented in this paper that minimizes the major casting defect, i.e., porosity, in the HPDC process by optimizing parameters through Design Of Experiments (DOE) in combination with Taguchi Analysis. The obtained results showed that cooling time, injection pressure, and 2nd stage plunger velocity had a major influence on the response factor (density of the cast part). It was further concluded that by using a 178-bar injection pressure, 665°C molten temperature, 5 seconds of cooling time, 210°C mold temperature, 0.20 m.s⁻¹ 1st stage plunger velocity, and 6.0 m.s⁻¹ 2nd stage plunger velocity, the rejection rate of the selected part due to porosity was reduced by 61%.
3. Introduction:
High-Pressure Die Casting (HPDC) is a prominent manufacturing process used to produce economical, complex-shaped, and dimensionally precise non-ferrous metal parts, particularly aluminum alloys for industries like automotive, telecommunication, and agriculture. In HPDC, molten metal is forced under high pressure into a die cavity and held until solidification. While HPDC offers advantages like high production rates and dimensional accuracy, the final castings can still suffer from defects such as porosity, pinholes, blowholes, shrinkage, inclusions, and cracks. These defects negatively impact mechanical properties (tensile, fatigue strength) and surface finish. The quality of HPDC parts depends on optimizing numerous process parameters, including injection pressure, molten temperature, plunger velocities (1st and 2nd stage), cooling temperature, and die cooling time. Porosity, often linked to injection pressure and cooling uniformity, is a major concern. Variations in parameters like plunger velocity, cooling temperature (especially with A380 alloy), and die temperature significantly affect part quality and defect formation. Optimizing the combination of these parameters is crucial for producing high-quality castings with minimal defects.
4. Summary of the study:
Background of the research topic:
HPDC is a vital process for mass-producing complex non-ferrous parts, but it is prone to various casting defects like porosity, which compromise product quality and performance. Controlling the numerous interacting process parameters is essential but challenging.
Status of previous research:
Previous research has investigated the effects of individual HPDC parameters using simulations and experiments. Methods like fuzzy systems, neural networks, and software simulations (e.g., Anycasting) have been used to predict or minimize defects like porosity. The Taguchi method combined with Design of Experiments (DOE) has been applied to optimize various manufacturing processes, including squeeze casting and sand casting. However, a comprehensive experimental approach using DOE and Taguchi analysis specifically focused on optimizing multiple key HPDC parameters simultaneously to minimize porosity defects in a real industrial application was identified as less explored. The conventional trial-and-error method used in foundries is often inefficient and costly.
Purpose of the study:
The study aimed to minimize the major casting defect, porosity, in an industrial HPDC process for a specific automotive part (motorbike Crankcase LH). This was achieved by optimizing six key controllable process parameters (injection pressure, molten metal temperature, die cooling time, mold temperature, 1st stage plunger velocity, and 2nd stage plunger velocity) using a combination of Design of Experiments (DOE) and Taguchi analysis. The goal was to find the optimal parameter combination to maximize the density of the cast part, thereby reducing porosity and improving overall product quality and production yield.
Core study:
The research was conducted at a motorbike manufacturing company. The Crankcase Left Hand (LH) part, made of Aluminum ADC 12 alloy, was selected due to high production volume and rejection rates. Porosity/pinholes were identified as the primary cause of rejection through production data analysis and Pareto charts. Six controllable HPDC process parameters were chosen as factors. A Taguchi L27 Orthogonal Array (OA) was used to design the experiments with three levels for each factor. Experiments were conducted on an 800-ton HPDC machine. The density of the resulting castings was measured (using Archimedes' principle) as the response factor, with higher density indicating lower porosity ("Larger the better" S/N ratio analysis). Taguchi analysis (Mean response and S/N ratio) was performed using Minitab software to identify the influence of each parameter and predict optimal settings. Further validation experiments were conducted by varying individual parameters around the suggested optimal levels to confirm the best combination. Finally, the optimized parameters were implemented for a week, and production data was collected to verify the reduction in rejection rate due to porosity.
5. Research Methodology
Research Design:
The study employed a structured experimental design based on DOE and Taguchi robust experimentation principles. The methodology involved:
- Analyzing the existing die casting procedure to identify the most frequently cast part and its major defects.
- Selecting input variables (factors) and the response factor (density).
- Setting parameter ranges and levels based on initial trials and foundry practice.
- Choosing an appropriate Orthogonal Array (L27) based on Degrees Of Freedom (DOF).
- Conducting experiments according to the OA design.
- Acquiring and analyzing the response factor data using Taguchi methods (Mean and S/N ratio analysis).
- Performing validation experiments to refine and confirm the optimal parameter settings.
- Comparing production defect data before and after implementing the optimized parameters.
Data Collection and Analysis Methods:
- Part/Defect Identification: Production data (Table 1) and defect records (Table 3) were collected for one month. Pareto analysis (Figure 3) was used to identify porosity/pinholes as the major defect.
- Material Analysis: Material composition of the ADC 12 aluminum alloy was determined using a Spectromax metal analyzer (Table 2).
- Parameter Selection: A cause-and-effect (fishbone) diagram (Figure 4) helped identify potential factors influencing porosity. Six controllable factors were selected.
- Experimental Setup: An 800-ton Yizumi SM-800T HPDC machine with auxiliary equipment was used. Factor levels were set (Table 4). 27 experimental runs (Table 5) based on the L27 OA were performed, with three samples ('shots') per run.
- Response Measurement: The mass of each cast part was measured using an electronic weighing scale. Density was calculated using Archimedes' principle (Table 6).
- Data Analysis: Taguchi analysis was performed using Minitab 18 software. Analysis included calculating mean response (Table 7, Figure 5) and Signal-to-Noise (S/N) ratios (Table 8, Figure 6) using the "Larger the better" criterion for density.
- Validation: Targeted experiments were conducted by varying one factor at a time around the predicted optimum (Tables 10-15) to find the final optimized settings (Table 16). Post-optimization production data was collected (Table 17) and analyzed (Figure 7).
Research Topics and Scope:
The research focused on the optimization of the High-Pressure Die Casting (HPDC) process for a specific component, the Crankcase Left Hand (LH) part, made from Aluminum ADC 12 alloy. The scope was limited to minimizing porosity defects by optimizing six specific process parameters:
- Injection pressure (bar)
- Molten temperature (°C)
- Die cooling time (s)
- Mold temperature (°C)
- 1st stage plunger velocity (m.s⁻¹)
- 2nd stage plunger velocity (m.s⁻¹)
The study used density as the primary measurable response variable, assuming higher density corresponds to lower porosity. The experiments were conducted within an industrial setting at a motorbike manufacturing facility.
6. Key Results:
Key Results:
- Analysis of production data revealed that "Pin hole/blow hole" (porosity) was the most significant defect for the Crankcase LH part, accounting for 32.17% of total rejections (435 out of 1352 rejected parts over one month).
- Taguchi analysis (Mean and S/N ratio) identified the most influential parameters affecting the density (and thus porosity) in descending order of significance: Die cooling time (Rank 1), Injection pressure (Rank 2), and 2nd stage plunger velocity (Rank 3). Molten temperature (Rank 4), Mold temperature (Rank 5), and 1st stage plunger velocity (Rank 6) had less significant effects.
- Through Taguchi analysis and subsequent validation experiments, the optimal combination of parameters to maximize density (minimize porosity) was determined as:
- Injection pressure: 178 bar
- Molten temperature: 665°C
- Die cooling time: 5 s
- Mold temperature: 210°C
- 1st stage plunger velocity: 0.20 m.s⁻¹
- 2nd stage plunger velocity: 6.0 m.s⁻¹
- Implementing these optimized parameters in production for one week resulted in a significant reduction in the rejection rate due to porosity/pinholes. The rejection quantity dropped from 435 (0.9% of total production, 32.17% of defects) to 140 (0.29% of total production, 11.47% of defects), representing an approximate 61% reduction in porosity-related rejections.
- Reductions in rejection rates due to cracks (approx. 16%) and inclusions (approx. 10%) were also observed after implementing the optimized parameters. Other defects like shrinkage, dents, ring crack/mismatch, and shade did not show significant changes.
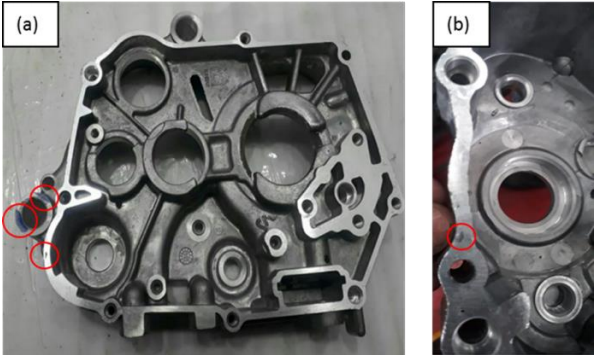
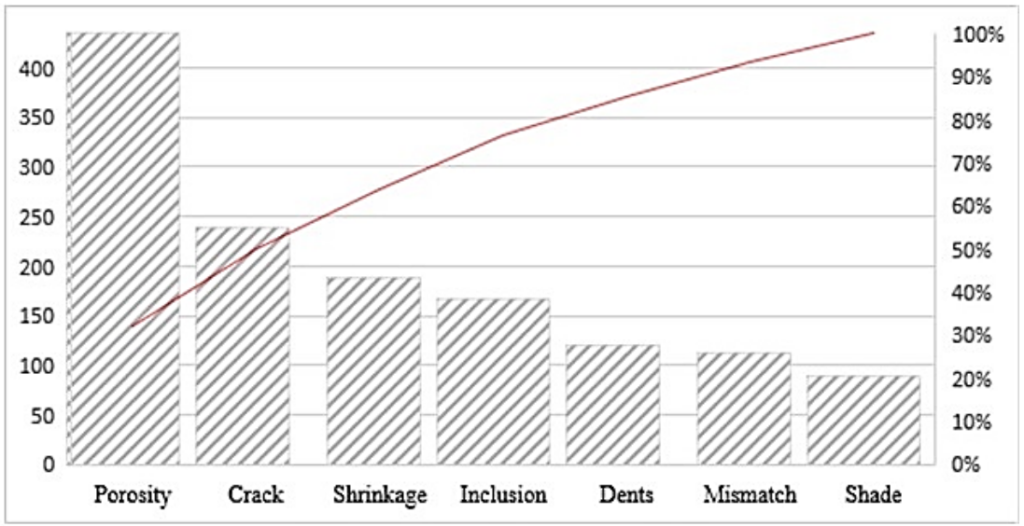
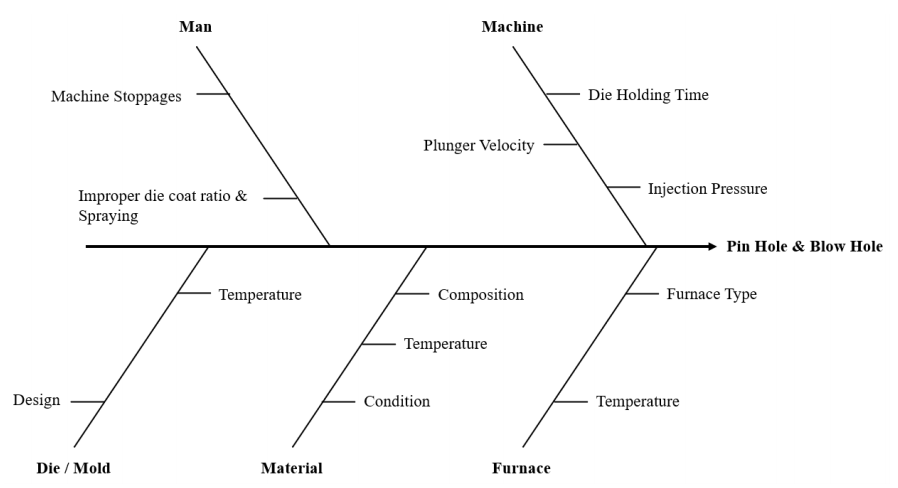
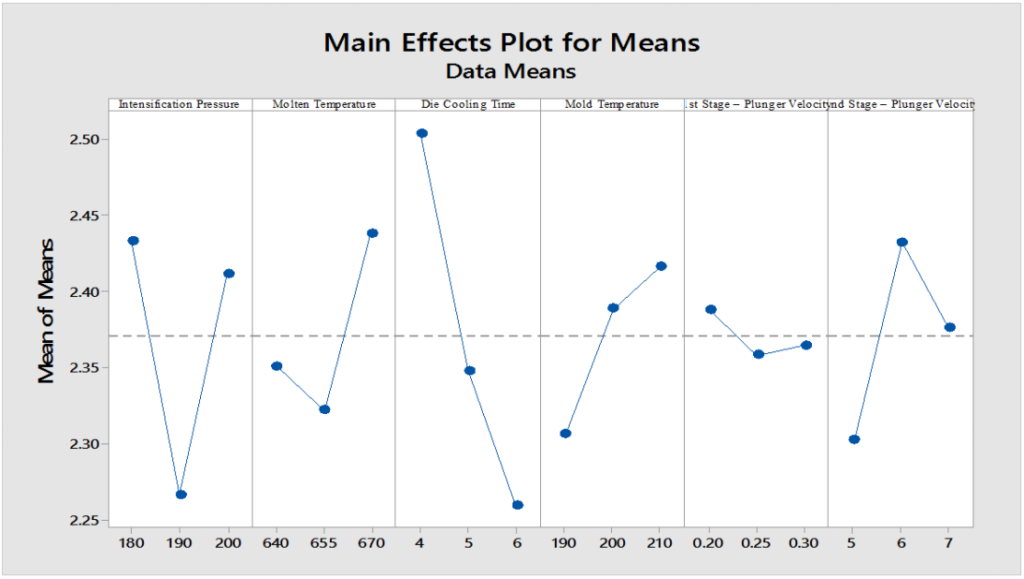
Figure Name List:
- Figure 1. Crankcase specimen produced with the High-Pressure Die Casting (HPDC) process.
- Figure 2. Casting defects found in the Crankcase: (a) pinhole and (b) porosity.
- Figure 3. Pareto chart of the defects.
- Figure 4. Cause and effect diagram.
- Figure 5. Response graph of means against the selected input parameters.
- Figure 6. Response graph of the S/N ratio against the selected input parameters.
- Figure 7. Pareto chart of the defects after optimization.
7. Conclusion:
High-Pressure Die Casting (HPDC) is a critical process for producing large quantities of complex parts cost-effectively, but it is susceptible to defects like porosity, pinholes, and cracks. This study successfully developed and applied an approach using Design Of Experiment (DOE) combined with Taguchi analysis to optimize HPDC process parameters and minimize casting defects, specifically porosity, for a motorbike Crankcase LH part in an industrial setting. The analysis revealed that die cooling time, injection pressure, and 2nd stage plunger velocity were the most significant factors affecting the density of the cast part. By implementing the experimentally validated optimized parameters (178-bar injection pressure, 665°C molten temperature, 5 s cooling time, 210°C mold temperature, 0.20 m.s⁻¹ 1st stage plunger velocity, and 6.0 m.s⁻¹ 2nd stage plunger velocity), the overall rejection rate of the selected part due to porosity was reduced by approximately 61%. This demonstrates the effectiveness of the DOE-Taguchi methodology for improving quality and reducing defects in HPDC processes.
8. References:
- [1] Teng, X., Mae, H., Bai, Y., et al. "Pore size and fracture ductility of aluminum low pressure die casting", Eng. Fract. Mech., 76(8), pp. 983-996 (2009).
- [2] Fracchia, E., Lombardo, S., and Rosso, M. "Case study of a functionally graded aluminum part", Appl. Sci., 8(7), p. 1113 (2018).
- [3] Makhlouf, M.M., Apelian, D., and Wang, L., Microstructures and Properties of Aluminum Die Casting Alloys, USDOE Idaho Operations Office, Idaho Falls, ID (US); North American Die … (1998).
- [4] Dargusch, M.S., Dour, G., Schauer, N., et al. "The influence of pressure during solidification of high pressure die cast aluminium telecommunications components", J. Mater. Process. Technol., 180(1-3), pp. 37-43 (2006).
- [5] Bonollo, F., Gramegna, N., and Timelli, G. "High-pressure die-casting: contradictions and challenges", Jom, 67(5), pp. 901-908 (2015).
- [6] Hamasaiid, A., Dargusch, M.S., Davidson, C., et al. "Effect of mold coating materials and thickness on heat transfer in permanent mold casting of aluminum alloys", Metall. Mater. Trans. A, 38, pp. 1303-1316 (2007).
- [7] Adamane, A.R., Arnberg, L., Fiorese, E., et al. "Influence of injection parameters on the poorosity and tensile properties of high-pressure die cast Al-Si alloys: A review", Int. J. Met., 9(1), pp. 43-53 (2015).
- [8] Hidalgo, R., Esnaola, J., Larrañaga, M., et al. “Influence of surface finish and porosity on the fatigue behaviour of A356 Aluminium casting alloy", MATEC Web Conf., 165, p. 14007 (2018).
- [9] Anilchandra, A.R., Arnberg, L., Bonollo, F., et al. "Evaluating the tensile properties of aluminum foundry alloys through reference castings-A review", Materials (Basel)., 10(9), p. 1011 (2017).
- [10] Yang, H., Yu, W., LI, X., et al. "Effect of different processing parameters on interfacial heat-transfer behavior in high-pressure die-casting process", Trans. Nonferrous Met. Soc. China, 28, pp. 2599-2606 (2018).
- [11] Kong, L.X., She, F.H., Nahavandi, S., et al. "Die temperature monitoring of high pressure die casting", Smc 2000 Conference Proceedings, 2000 Ieee International Conference on Systems, Man and Cybernetics, Cybernetics Evolving to Systems, Humans, Organizations, and Their Complex Interactions, 3, pp. 1756-1761 (2000).
- [12] Syrkos, G. "Die casting process optimization using Taguchi methods", J. Mater. Process. Technol., 135, pp. 68-74 (2003).
- [13] Ingle, V. and Sorte, M.B. "Defects, root causes in casting process and their remedies: Review", Int. J. Eng. Res. Appl., 07, pp. 47-54 (2017).
- [14] Zyska, A., Konopka, Z., Lagiewka, M., et al. "Porosity of castings produced by the vacuum assisted pressure die casting method", Archives of Foundry Engineering, 15(1), pp. 125-130 (2015).
- [15] Apparao, K.C. and Birru, A.K. "QFD-Taguchi based hybrid approach in die casting process optimization", Trans. Nonferrous Met. Soc. China, 27(11), pp. 2345-2356 (2017).
- [16] Wang, Y., Shiping, W., Lianjie, N., et al. "Optimization of low-pressure die casting process parameters for reduction of shrinkage porosity in ZL205 A alloy casting using Taguchi method", Proc. Inst. Mech. Eng. Part B J. Eng. Manuf., 228, pp. 1508-1514 (2014).
- [17] Kwon, H.-J. and Kwon, H.-K. "Computer aided engineering (CAE) simulation for the design optimization of gate system on high pressure die casting (HPDC) process", Robot. Comput. Integr. Manuf., 55, pp. 147-153 (2019).
- [18] Yalçın, B., Koru, M., Ipek, O., et al. "Effect of injection parameters and vacuum on the strength and porosity amount of die-casted A380 alloy", International Journal of Metalcasting, 11(2), pp. 195-206 (2017).
- [19] Fiorese, E., Bonollo, F., and Battaglia, E. "A tool for predicting the effect of the plunger motion profile on the static properties of aluminium high pressure die cast components", Metals (Basel)., 8(10), p. 798 (2018).
- [20] Cao, H., Wang, C., Che, J., et al. "Effect of flow state of pure aluminum and A380 alloy on porosity of high pressure die castings", Materials (Basel), 12(24), p. 4219 (2019).
- [21] Iwata, Y., Dong, S., Sugiyama, Y., et al. "Effects of solidification behavior during filling on surface defects of aluminum alloy die casting", Mater. Trans., 54, pp. 1944-1950 (2013).
- [22] Sadeghi, M. and Mahmoudi, J. "Experimental and theoretical studies on the effect of die temperature on the quality of the products in high-pressure die-casting process", Adv. Mater. Sci. Eng., 2012, p. 434605 (2012).
- [23] Liu, C., Jiao, X., Nishat, H., et al. "Characteristics of Fe-rich intermetallics compounds and their influence on the cracking behavior of a newly developed high-pressure die cast Al-4Mg-2Fe alloy", J. Alloys Compd., 854, p. 157121 (2021).
- [24] Kumar, S., Satsangi, P., and Prajapati, D.R. "Optimization of green sand casting process parameters of a foundry by using Taguchi's method", The International Journal of Advanced Manufacturing Technology, 55, pp. 23-34 (2010).
- [25] Fajkiel, A., Dudek, P., Walczak, W., et al. "Improvement of quality of a gravity die casting made from aluminum bronze be application of numerical simulation", Arch. Foundry Eng., 7, pp. 11-14 (2007).
- [26] Świłło, S. and Myszka, D. “Archives of 39/3 advanced metrology of surface defects measurement for aluminum die casting", Archives of Foundry Engineering, 11(3), pp. 227-230 (2011).
- [27] Cica, D. and Kramar, D. "Intelligent process modeling and optimization of porosity formation in high-pressure die casting", International Journal of Metalcasting, 12, pp. 814-824 (2018).
- [28] Cao, H., Shen, C., Wang, C., et al. "Direct observation of filling process and porosity prediction in high pressure die casting", Mater. (Basel, Switzerland), 12(7), p. 1099 (2019).
- [29] Aamir, M., Tu, S., Tolouei-Rad, M., et al. "Optimization and modeling of process parameters in multi-hole simultaneous drilling using Taguchi method and fuzzy logic approach", Materials (Basel), 13(3), p. 680 (2020).
- [30] Do, T.-V. and Hsu, Q.-C. "Optimization of minimum quantity lubricant conditions and cutting parameters in hard milling of AISI H13 steel", Appl. Sci., 6(3), p. 83 (2016).
- [31] Vu, N.-P., Nguyen, Q.-T., Tran, T.-H., et al. "Optimization of grinding parameters for minimum grinding time when grinding tablet punches by CBN wheel on CNC milling machine", Applied Sciences, 9(5) (2019).
- [32] Lan, T.-S., Chuang, K.-C., and Chen, Y.-M. "Optimization of machining parameters using fuzzy Taguchi method for reducing tool wear", Appl. Sci., 8(7), p. 1011 (2018).
- [33] Kolahan, F. and Azadi Moghaddam, M. "The use of Taguchi method with grey relational analysis to optimize the EDM process parameters with multiple quality characteristics", Sci. Iran., 22(2), pp. 530-538 (2015).
- [34] Azadi Moghaddam, M. and Kolahan, F. "Modeling and optimization of the electrical discharge machining process based on a combined artificial neural network and particle swarm optimization algorithm", Sci. Iran., 27(3), pp. 1206-1217 (2020).
- [35] Karthik, A., Karunanithi, R., Srinivasan, S.A., et al. "The optimization of squeeze casting process parameter for AA2219 alloy by using the Taguchi method", Materials Today: Proceedings, 27, pp. 2556-2561 (2020).
- [36] Hassasi, S.A., Abbasi, M., and Hosseinipour, S.J. "Parametric investigation of squeeze casting process on the microstructure characteristics and mechanical properties of A390 aluminum alloy", Int. J. Met., 14(1), pp. 69-83 (2020).
- [37] Souissi, N., Souissi, S., Niniven, C., et al. "Optimization of squeeze casting parameters for 2017 a wrought Al alloy using Taguchi method", Metals (Basel), 4(2), pp. 141-154 (2014).
- [38] Prabhakar, A., Papanikolaou, M., Salonitis, K., et al. "Minimising defect formation in sand casting of sheet lead: A DoE approach", Metals (Basel), 10(2), p. 252 (2020).
- [39] Mohsin, I., He, K., Li, Z., et al. "Optimization of the polishing efficiency and torque by using Taguchi method and ANOVA in robotic polishing", Appl. Sci., 10(3), p. 824 (2020).
- [40] Balikai, V.G., Siddlingeshwar, I.G., and Gorwar, M. "Optimization of process parameters of High Pressure Die Casting process for ADC12 Aluminium alloy using Taguchi method", Int. J. Pure Appl. Math., 120(6), pp. 959-969 (2018).
- [41] Sarin, S. "Teaching Taguchi's approach to parameter design", Quality Progress, 30(5), p. 102 (1997). 30 (1997).
- [42] Wu, C.C. and Su, T.S. "Application of the Taguchi method for the optimization of visual inspection parameters for multi-layer ceramic capacitors", Sci. Iran., 21(6), pp. 2379-2386 (2014).
- [43] Chang, M.S. "Use of Taguchi method to develop a robust design for the magnesium alloy die casting process", Mater. Sci. Eng. A, 379(1-2), pp. 366-371 (2004).
- [44] Kamaruddin, S., Khan, Z., and Foong, S. "Application of Taguchi method in the optimization of injection moulding parameters for manufacturing products from plastic blend", Int. J. Web Eng. Technol., 2, pp. 574-580 (2010).
- [45] Asim, M., Khan, M., Khan, L., and Umer, M. "An integrated approach of quality for polymer composite manufacturing validated and optimized through Taguchi method", Sci. Iran., 24, pp. 1985-1995 (2017).
- [46] Banik, K. "Effect of mold temperature on short and long-term mechanical properties of PBT", Express Polym. Lett.-Express Polym Lett., 2, pp. 111-117 (2008).
9. Copyright:
- This material is a paper by "S. Tariq, A. Tariq, M. Masud, and Z. Rehman". Based on "Minimizing the casting defects in high-pressure die casting using Taguchi analysis".
- Source of the paper: https://doi.org/10.24200/sci.2021.56545.4779
This material is summarized based on the above paper, and unauthorized use for commercial purposes is prohibited.
Copyright © 2025 CASTMAN. All rights reserved.