
Product Design Technology for Die Casting
The die-casting process is a very good way to manufacture large amounts of non-ferrous metal parts. This manufacturing process produces parts by injecting molten metal into the die at high pressure and high speed. This process makes very complex parts cost-effective and effective. This process can create parts that vary greatly in size and weight. You can also choose a variety of alloys depending on the purpose of the product and the working environment.
Designing products for die-casting can require a variety of skills. This is especially true when designing a housing with good shapes and mechanical requirements; thin wall enclosures can be particularly challenging and often require rib and boss inside to increase strength.
Other external and internal functions, such as gradient angles, are required to easily eject parts after the die casting process. You can also use the sliding core of the die to frequently see enclosures with connectors and buttons on the side of casting these features on the part.
The design of die cast parts can have a significant impact on manufacturing costs. However, if you refine your design and optimize it for mass production, the results can be very significant.
Production Capabilities
CASTMAN has the technology to make high-quality die cast parts affordable and fast.
Contact our sales team to learn more about the powerful production capability that drives the CASTMAN products and find out if it can be used to solve your particular problem.
CASTMAN’s Technical Keyword
- Sand casting
- Permanent mold casting
- Aluminum casting
- Die casting
- Copper(Cu) die casting
- Copper(Cu) casting
- Copper(Cu) machining parts
- Heat sink
- Bus bar
- Connecter
- copper(Cu) rotor
- salt core
- under-cut die casting
The die casting process uses high pressure and high speed to inject molten metal into the die to create parts. At the end of the solidification process, two parts of the die are opened and the part is ejected from the moving surface of the platen. It is usually important that there is no undercut area in the direction of the die opening.
This is why die cast components should be oriented before tooling or die fabrication to ensure that these areas are free from undercuts. However, as die cast components become increasingly complex, many features are added to the edges of the components to incorporate additional features.
These features are very common with undercuts, so sliding cores are added to the tooling design. The sliding core slides into place during the casting process, creating an undercut feature on the die cast part and sliding outward for the draining process.
It is important to note that there should be no undercuts in the direction of the sliding core.
While these undercut products are difficult to compete in terms of production and cost, Castman's Salt Core technology can easily address these challenges.
Under-cut die casting Products
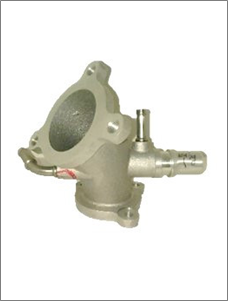