This article introduces the paper ['Ultra-large aluminum shape casting: Opportunities and challenges'] presented at the ['CHINA FOUNDRY']
1. Overview:
- Title: Ultra-large aluminum shape casting: Opportunities and challenges
- Author: Qi-gui Wang, Andy Wang, and Jason Coryell
- Publication Year: 2024
- Publishing Journal/Academic Society: CHINA FOUNDRY
- Keywords: ultra-large castings; aluminum; light-weighting; quality; microstructure; materials properties
![Fig. 1: Growth of aluminum in North American light vehicle [2]](https://castman.co.kr/wp-content/uploads/image-609-png.webp)
2. Research Background:
Background of the Research Topic:
The increasing demand for light-weighting in automotive vehicles, especially electric vehicles, has led to a surge in the use of lightweight aluminum shape castings. These castings are crucial for reducing vehicle weight, improving fuel efficiency in internal combustion engines, and enhancing battery energy usage in electric vehicles. Aluminum shape castings offer a combination of near-net-shape capability, high strength-to-weight ratio, design flexibility, and cost-effectiveness, making them attractive for automotive applications.
Status of Existing Research:
Historically, aluminum shape castings were primarily used in powertrain components like engine blocks and transmission housings, utilizing secondary alloys such as 319 and A380. However, the application has expanded to vehicle body and chassis components, particularly for battery electric vehicles (BEVs), where primary aluminum alloys are favored for their high ductility. Both High Pressure Die Casting (HPDC) and Low Pressure Sand Casting (LPSC) are employed for producing ultra-large aluminum shape castings. Recent advancements in aluminum shape casting are documented in Refs. [1, 3-4]. Al-Si-Mg alloys and their variants are widely used due to their castability, corrosion resistance, and strength-to-weight ratio.
Necessity of the Research:
The trend towards simpler vehicle body designs using ultra-large single-piece castings, also known as mega-castings or giga-castings, presents new challenges. These large castings, while reducing parts and assembly complexity, introduce complexities in quality control and performance prediction. Factors such as varying wall thicknesses, increased "hot spots," longer metal flow distances, and potential for shrinkage porosity, trapped air, oxides, cold shuts, and misrun necessitate a deeper understanding of the factors affecting quality, microstructure, and material properties of ultra-large aluminum castings.
3. Research Purpose and Research Questions:
Research Purpose:
This paper aims to critically examine the key factors influencing the quality, microstructure, and material properties of ultra-large aluminum shape castings. It also intends to present advanced technologies for enhancing casting quality and performance and to demonstrate the robust design and development of high-integrity castings using virtual casting tools.
Key Research:
- Evaluation of factors affecting quality, microstructure, and mechanical properties of ultra-large aluminum castings.
- Discussion of advanced technologies to improve casting quality and performance.
- Demonstration of robust design and development using virtual casting tools.
- Metallurgical analysis and mechanical property assessment of an ultra-large aluminum shape casting.
- Highlighting challenges and suggesting improvements for robust design and manufacturing.
Research Hypotheses:
The paper does not explicitly state research hypotheses but implies that:
- Quality and performance of ultra-large aluminum shape castings are significantly influenced by factors related to casting process, alloy selection, and design.
- Advanced technologies and virtual casting tools can effectively address the challenges associated with producing high-integrity ultra-large aluminum castings.
- Understanding and controlling factors like melt cleanliness, gating system design, mold surface treatment, and casting process parameters are crucial for achieving desired quality and properties.
4. Research Methodology
Research Design:
This paper is a review paper, focusing on summarizing existing knowledge and recent developments in ultra-large aluminum shape casting. It uses application examples, metallurgical analysis, and mechanical property assessments from existing literature and industry practices to illustrate the opportunities and challenges.
Data Collection Method:
The paper primarily relies on literature review, industry reports, and case studies. Data is collected from published articles, patents, conference proceedings, and industry publications related to aluminum casting, particularly ultra-large castings in automotive applications.
Analysis Method:
The analysis is descriptive and qualitative, focusing on identifying and discussing the key factors, challenges, and opportunities related to ultra-large aluminum shape castings. It involves summarizing and synthesizing information from various sources to provide a comprehensive overview of the topic. The paper also uses examples of tensile property variations and porosity observations to support its arguments.
Research Subjects and Scope:
The scope of the paper is focused on ultra-large aluminum shape castings used in automotive applications, particularly for structural components in electric vehicles. The paper discusses various aspects from alloy selection and casting processes to design considerations and sustainability.
5. Main Research Results:
Key Research Results:
- Opportunities of Ultra-large Aluminum Castings: Ultra-large aluminum castings offer benefits such as reduced part count (60+ parts replaced), tooling cost savings (40%), energy savings (30%), mass reduction (30%), and reduced lead time. They also enable broader applications like integrated battery cases. (Table 1)
- Challenges in Manufacturing: Producing quality ultra-large aluminum castings is difficult due to size, die complexity, thermal management, and defect susceptibility (shrinkage porosity, oxides, cold shuts, misrun). Material properties within a large casting can be non-uniform (Fig. 5). Dimensional stability and repairability are also significant challenges.
- Factors Affecting Casting Quality:
- Cast Aluminum Alloys: Alloys with ~7% Si (e.g., C611, Aural 5) are used for HPDC mega-castings for balanced castability and tensile elongation. Cu content in Al-Si-Mg alloys can detrimentally increase porosity and reduce corrosion resistance (Fig. 9, Fig. 11).
- Melt Cleanliness: Clean liquid metal is crucial. Preheating and flux coating scrap charges can reduce oxides and contamination. (Fig. 12, Fig. 13)
- Gating System Design: Optimal gating system design is critical to minimize turbulent flow and air entrapment. (Fig. 14, Fig. 15)
- Mold Surface Treatment: Proper mold surface treatment affects surface finish and casting skin layer quality.
- Casting Process: Optimal casting process control, including mold temperature (ideally ~1/3 of melt pouring temperature), pouring temperature (50-100 °C above liquidus), pouring velocity, and shot profile (Fig. 17, Fig. 18), are essential for quality.
Data Interpretation:
- Figure 1: Illustrates the growth of aluminum usage in North American light vehicles, highlighting castings as a major application.
- Figure 2 & 3: Show examples of ultra-large aluminum castings in Tesla Model Y and Cadillac Celestiq, demonstrating industry adoption.
- Figure 4: Depicts macro shrinkage porosity observed in a giga aluminum casting, highlighting a challenge.
- Figure 5: Shows tensile property variations within a giga casting, indicating non-uniformity.
- Figure 6 & 7: Illustrate the aluminum paradox in sustainability and the CO2 emission reduction potential of recycled aluminum.
- Figure 8: Presents calculated solidification sequences of alloys used in ultra-large castings, showing phase transformations.
- Figure 9: Shows the relationship between Cu content and porosity in Al-Si-Mg alloys, demonstrating Cu's negative impact.
- Figure 10: Predicts cracking susceptibility coefficient (CSC) as a function of Cu and Si content.
- Figure 11: Illustrates the effect of Cu, Mg, Fe, and Sr on corrosion resistance, highlighting Cu's detrimental effect.
- Figure 12 & 13: Schematically explain the aluminum oxide detachment process using molten salt and interfacial tension forces.
- Figure 14 & 15: Show gating system designs and their impact on trapped air, emphasizing design importance.
- Figure 16: Demonstrates surface defect elimination through proper die surface treatment.
- Figure 17 & 18: Illustrate shot profiles and their effect on trapped air, highlighting process parameter optimization.
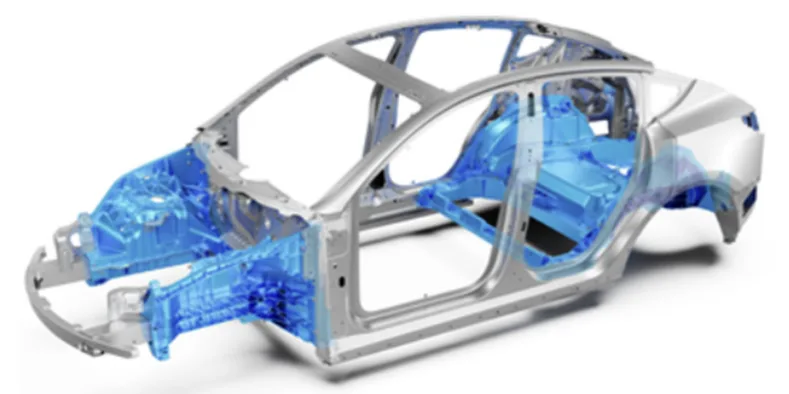
![Fig. 3: Six mega aluminum shape castings forming the entire lower body structure for Cadillac Celestiq vehicles [13]](https://castman.co.kr/wp-content/uploads/Six-mega-aluminum-shape-castings-forming-the-entire-lower-body-structure-for-Cadillac-Celestiq-vehicles.png)
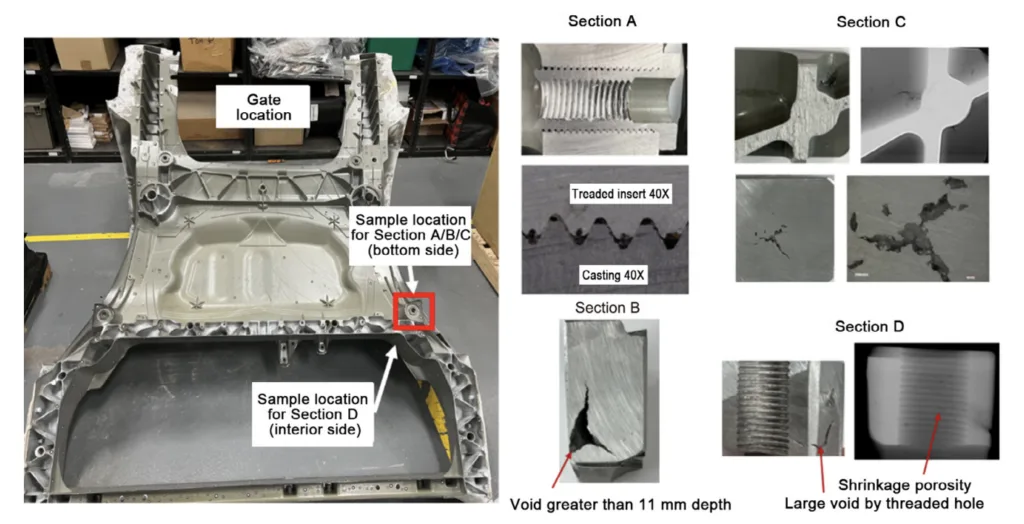
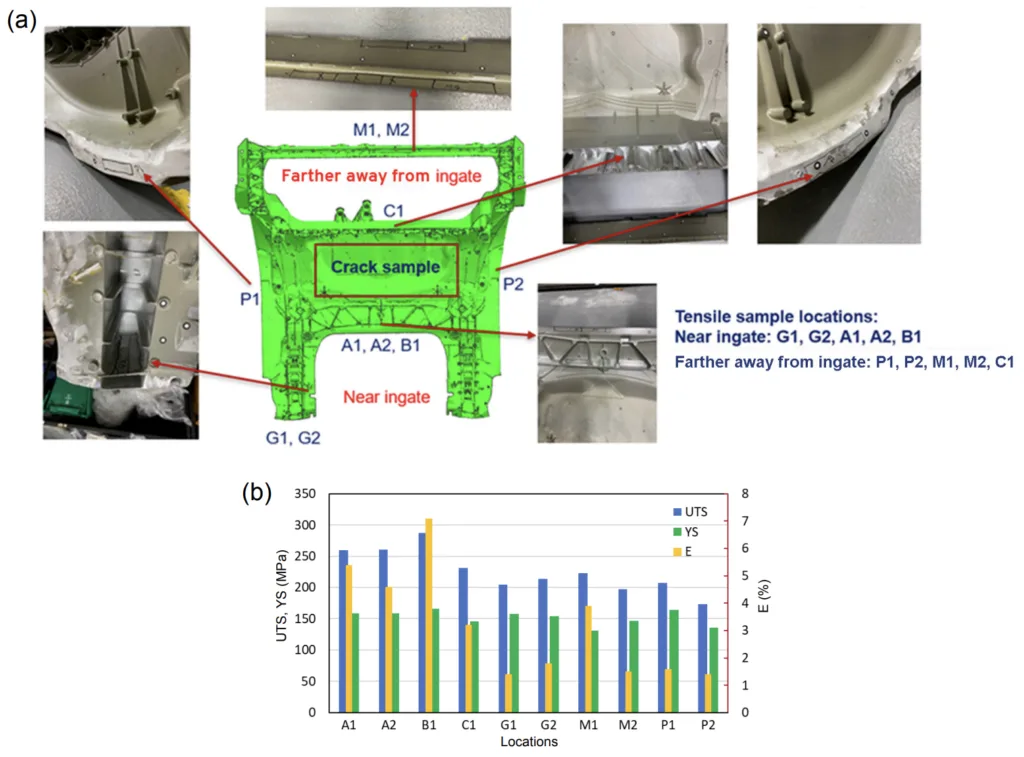
![Fig. 6: Aluminum paradox from sustainability aspect [19]](https://castman.co.kr/wp-content/uploads/image-613-1024x381.webp)
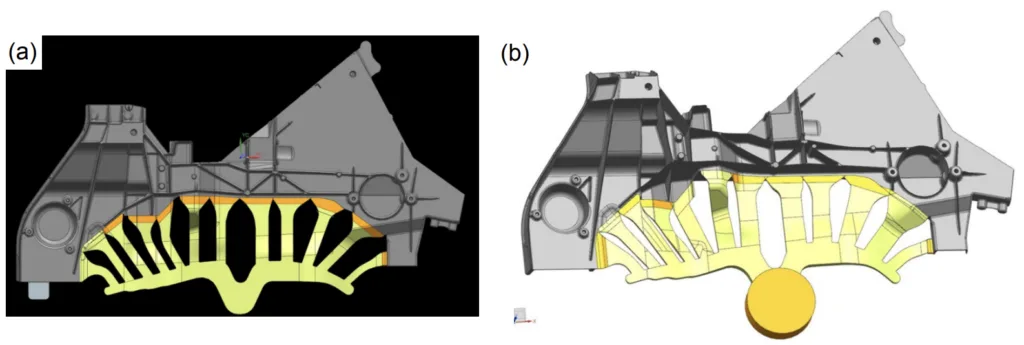
Figure Name List:
- Fig. 1: Growth of aluminum in North American light vehicle [2]
- Fig. 2: A Tesla Model Y giga-casting [10]
- Fig. 3: Six mega aluminum shape castings forming the entire lower body structure for Cadillac Celestiq vehicles [13]
- Fig. 4: Large macro shrinkage porosity observed in a giga aluminum casting
- Fig. 5: Sampling locations (a) and tensile properties (b) of an aluminum giga casting in various locations
- Fig. 6: Aluminum paradox from sustainability aspect [19]
- Fig. 7: Comparison of CO2 production during various aluminum manufacturing processes [19]
- Fig. 8: Calculated friction of solid and solidification sequences of alloys currently used in ultra-large aluminum castings
- Fig. 9: Volume fraction of porosity as a function of Cu content in a cast Al-Si-Mg alloy [24]
- Fig. 10: Predicted cracking susceptibility coefficient (CSC) as a function of Cu and Si contents [25]
- Fig. 11: Effect of Cu, Mg, Fe, and Sr contents on corrosion resistance of Al-Si-Mg alloy
- Fig. 12: A schematic illustrating aluminum oxide detachment process [29]
- Fig. 13: Interfacial tension forces acting on the aluminum liquid droplet and aluminum oxide substrate [29]
- Fig. 14: Two gating designs for a large HPDC structural part: (a) Design 1; (b) Design 2
- Fig. 15: Trapped air integral comparison between two gating designs (in casting only)
- Fig. 16: An example showing cast surface defects eliminated with the proper die surface treatment [32]: (a) casting surface defects; (b) surface defect eliminated with die surface treatment
- Fig. 17: Two shot profiles for a large HPDC structure casting
- Fig. 18: Accumulation of the trapped air calculated for the four combinations of two gating designs and two shot profiles
6. Conclusion:
Summary of Main Results:
Ultra-large aluminum mega/giga castings are revolutionizing automotive manufacturing by simplifying designs, reducing weight and cost, and shortening lead times. However, challenges exist in achieving casting quality, dimensional accuracy, repairability, and sustainability. The paper highlights critical factors for producing high-quality ultra-large castings, including alloy selection (low Cu content Al-Si-Mg alloys), melt cleanliness (flux treatment), optimized gating system design, precise mold surface treatment, and controlled casting processes (mold temperature, pouring temperature, shot profile). Virtual casting tools are essential for robust design and process optimization.
Academic Significance of the Research:
This review paper consolidates and summarizes the current state of knowledge regarding ultra-large aluminum shape castings. It provides a handbook-level overview of the opportunities, challenges, and critical factors influencing their production and performance. The paper emphasizes the multi-physics nature of the casting process and the importance of a holistic approach encompassing material science, casting engineering, and virtual simulation.
Practical Implications:
The findings offer practical guidance for automotive manufacturers and casting engineers involved in the design and production of ultra-large aluminum castings. By understanding and addressing the identified challenges and implementing the recommended best practices in alloy selection, melt treatment, gating design, and process control, manufacturers can improve casting quality, reduce defects, enhance mechanical properties, and ensure dimensional stability. The paper also points towards sustainable practices like using recycled aluminum and designing for repairability.
Limitations of the Research
As a review paper, it relies on existing literature and does not present new experimental data. The paper acknowledges the complexity and uncertainties inherent in ultra-large aluminum shape casting but does not delve into specific quantitative analyses or detailed modeling aspects. The discussion on repairability and sustainability is introductory and suggests areas for further research rather than providing definitive solutions.
7. Future Follow-up Research:
- Directions for Follow-up Research
- Further research is needed to develop robust and cost-effective repair strategies for ultra-large castings, potentially focusing on advanced joining techniques and modular design approaches.
- Investigating and optimizing the use of high-recycled content aluminum alloys for structural castings to enhance sustainability without compromising performance is crucial.
- Advanced process monitoring and control systems, incorporating real-time feedback and AI-driven optimization, are needed to ensure consistent casting quality in large-scale production.
- Areas Requiring Further Exploration
- Detailed investigation into the long-term performance and durability of ultra-large aluminum castings under various service conditions, including fatigue, corrosion, and crashworthiness.
- Development of advanced simulation tools that can accurately predict microstructure evolution, defect formation, and mechanical property variations within ultra-large castings.
- Exploration of novel casting processes and die materials to improve die life and reduce manufacturing costs for ultra-large castings.
8. References:
- [1] Luo A A, Sachdev A, Apelian D. Alloy development and process innovations for light metals casting. Journal of Materials Processing Technology, 2022, 306: 117606.
- [2] Ducker Frontier, 2020. 2020 North America light vehicle aluminum content and outlook. Final Report Summary: July 2020.
- [3] Wang Q G, Apelian D and Griffiths J R. Microstructural effects on the fatigue properties of aluminum castings, in advances in aluminum casting technology. Eds.: M. Tiryakioglu and J. Campbell, ASM International, Materials Park, OH, 1998: 217-224.
- [4] Wang Q G. Latest advances and developments in aluminum shape casting. China Foundry, 2013, 10(1): 43-49.
- [5] Wang L, Makhlouf M and Apelian D. Aluminum die casting alloys-Alloy composition, microstructure, and properties/performance relationships. Int. Materials Reviews, 1995, 40: 221-238.
- [6] Cáceres C H, Davidson C J, Griffiths J R, et al. Hypoeutectic Al-Si-Mg foundry alloys. Materials Forum, 1997, 21: 27-43.
- [7] Taylor J. Metal related castability effects in aluminium foundry alloys. Cast Metals, 1996, 8: 225-252.
- [8] Wang Q G. Fatigue fracture mechanism and fatigue life assessment of aluminum castings. In: Proceedings of Materials Lifetime Science & Engineering, edited by P. K. Liaw, R. A. Buchanan, D. L. Klarstrom, R. P. Wei, D. G. Harlow, and P. F. Tortorelli, TMS (The Minerals, Metals & Materials Society), 2003, Warrendale, PA: 211-222.
- [9] Hartlieb A and Hartlieb M. The impact of giga-castings on car manufacturing and aluminum content. https://www.lightmetalage.com/news/industry-news/automotive/the-impact-of-giga-castings-on-car-manufacturing-and-aluminum-content, July 10, 2023.
- [10] Hardigree M. How Tesla made 'gigacasting', the most important word in the car industry. https://www.theautopian.com/how-tesla-made-gigacasting-the-most-important-word-in-the-car-industry, Sept. 14, 2023.
- [11] Hart C, Afseth A, and Zuidema B. Aluminum value in battery electric vehicles. The Aluminum Association, 2022.
- [12] Abraham A K. Automotive materials in an evolving landscape. Ducker Carlisle, January 24, 2023.
- [13] Mihalascu D. Cadillac takes a page from Tesla's book, uses mega castings on Celestiq. https://insideevs.com/news/617108/cadillac-takes-page-from-tesla-book-uses-mega-castings-on-celestiq, October 18, 2022.
- [14] Phelan K. Casting of the year: Planets aligned for clean-sheet cadillac casting design. Modern Casting, May 2023: 24-31.
- [15] Panday A. What do Toyota's announcements on battery technologies, giga castings mean? Aug. 2, 2023. https://www.linkedin.com/pulse/what-do-toyotas-announcements-battery-technologies-giga-castings/
- [16] Schuh G, Bergweiler G, Dworog L, et al. Opportunities and risks of mega-casting in automotive production - The aluminum die-cast body in white. Düsseldorf: VDI Fachmedien, www.researchgate.net/publication/363880399, September 2022.
- [17] Wärmefjord K, Hansen J, and Söderberg R. Challenges in geometry assurance of megacasting in the automotive industry. ASME, Journal Computing and Information Science in Engineering, 2023, 23(6). https://doi.org/10.1115/1.4062269.
- [18] Giga Presses. The giant die casts that are reshaping car manufacturing. Reuters/Automotive News Europe, February 10, 2023.
- [19] Zhan H, Zeng G, Wang Q, et al. Unified cast (UniCast) aluminum alloy - Resolving sustainability paradox material solution for vehicle lightweighting. Journal of Materials Science & Technology, 2023, 154: 251-268.
- [20] Wilson D J, Wang L, Wang Q, et al. Repair ultra-large casting. US Patent Application No.: 20230356293.
- [21] Wilson D J, Wang L, Wang Q, et al. Method of in-situ repair of an ultra-large single-piece casting. US Patent Application No.: 20230339052.
- [22] Ravi K R. Fluidity of aluminum alloys and composites: A review. Journal of Alloys & Compounds, 2008, 456(1-2): 201-210.
- [23] Gao Y, Liao H, Suo X, et al. Prediction of fluidity of casting aluminum alloys using artificial neural network. In: Proceedings of Materials Science & Technology (MS&T2019), Sept. 29-Oct. 3, 2019, Portland USA.
- [24] Cáceres C H, Djurdjevic M B, Stockwell T J, et al. The effect of Cu content on the level of microporosity in Al-Si-Cu-Mg casting alloys. Scripta Materialia, 1999, 40(5): 631-637.
- [25] Edwards G A, Sigworth GK, Cáceres C H, et al. Microporosity formation in Al-Si-Cu-Mg casting alloys. AFS Transaction, 1997: 809-818.
- [26] Liao H, Wang Q, Suo X, et al. Modeling of solute-dependent fluidity and hot tearing sensitivity of conductive aluminum alloys. TMS 2018, 147th Annual Meeting & Exhibition Supplemental Proceedings, Feb. 2018, https://doi.org/10.1007/978-3-319-72526-0_34.
- [27] Lei Z, Liao H, Wang Q, et al. In-situ observation of porosity formation during directional solidification of Al-Si casting alloys. China Foundry, 2011, 8(1): 14-18.
- [28] Liao H, Wu Y, Fan R, et al. Effect of Sr content on porosity formation in directionally solidified Al-12.3wt.%Si alloy. China Foundry, 2014, 11(5): 435-439.
- [29] Liao H, Zhao L, Wu Y, et al. Investigation on formation mechanism of irregular shape porosity in hypoeutectic aluminum alloy by X-ray real time observation. Metall. Mater. Trans., 2012, 43A: 2587-2590.
- [30] Wang Q, Gerard D. Methods of reducing old oxides in aluminum castings. US Patent No. 9574252 (Feb 21, 2017).
- [31] Lee B D, Baek U H, Han J W. Optimization of gating system design for die casting of thin magnesium alloy-based multi-cavity LCD housings. Journal of Materials Engineering and Performance, 2012, 21: 1893-1903.
- [32] Campbell J. Castings, 2nd edition. Butterworth-Heinemann, June 12, 2003.
- [33] Wang Q, Xu Y, Rubin A, et al. Methods to improve surface appearance and quality of high pressure die castings and permanent mold castings. Research Disclosure, 2023.
9. Copyright:
- This material is "Qi-gui Wang, Andy Wang, and Jason Coryell"'s paper: Based on "Ultra-large aluminum shape casting: Opportunities and challenges".
- Paper Source: https://doi.org/10.1007/s41230-024-4111-9
This material was summarized based on the above paper, and unauthorized use for commercial purposes is prohibited.
Copyright © 2025 CASTMAN. All rights reserved.
Qi-gui Wang, Andy Wang & Jason Coryell
Abstract
Ultra-large aluminum shape castings have been increasingly used in automotive vehicles, particularly in electric vehicles for light-weighting and vehicle manufacturing cost reduction. As most of them are structural components subject to both quasi-static, dynamic and cyclic loading, the quality and quantifiable performance of the ultra-large aluminum shape castings is critical to their success in both design and manufacturing. This paper briefly reviews some application examples of ultra-large aluminum castings in automotive industry and outlines their advantages and benefits. Factors affecting quality, microstructure and mechanical properties of ultra-large aluminum castings are evaluated and discussed as aluminum shape casting processing is very complex and often involves many competing mechanisms, multi-physics phenomena, and potentially large uncertainties that significantly influence the casting quality and performance. Metallurgical analysis and mechanical property assessment of an ultra-large aluminum shape casting are presented. Challenges are highlighted and suggestions are made for robust design and manufacturing of ultra-large aluminum castings.