"FSW: The high-strength joining technology that needs no bolts or rivets."
FSW (Friction Stir Welding) is a solid-state joining method developed in 1991 at The Welding Institute (TWI) in the UK. Unlike conventional fusion welding, FSW joins materials without melting them. The process involves inserting a rotating tool into the joint line. The frictional heat generated softens the material, and the tool's rotation and traverse movement then plastically deform and forge the materials together, creating a high-integrity solid-state weld.
Advantages of FSW
- Excellent Mechanical Properties: The weld zone has a fine and uniform microstructure, resulting in superior mechanical strength compared to the base material.
- High-Quality Joints: Produces high-quality welds with almost no defects such as porosity or cracks, which are common in fusion welding.
- No Consumables: It does not require filler materials or shielding gas, leading to cost savings.
- Joins Dissimilar Materials: Enables the joining of dissimilar materials, such as aluminum and copper, which is difficult with conventional welding methods.
- Low Distortion & High Precision: The low heat input minimizes thermal deformation, ensuring excellent dimensional accuracy of the final product.
- Eco-Friendly Process: It is an environmentally friendly process as it does not generate harmful fumes, spatter, or arc flash.
Characteristics of FSW
- Solid-State Joining: The process is performed below the material's melting point, preventing issues associated with solidification, such as cracking and porosity.
- Superior Weld Quality: The weld zone, which undergoes plastic deformation and recrystallization, has a finer and more uniform grain structure than the base material, resulting in excellent mechanical properties.
- Low Distortion: Compared to fusion welding, the heat input is significantly lower, which drastically reduces thermal shrinkage and distortion.
- Eco-Friendly: With no fumes, spatter, or harmful radiation, it provides a clean and safe working environment.
- Ease of Automation: The process is easily automated using CNC machines or robots, making it ideal for mass production and ensuring consistent quality.
Applications of FSW
FSW is widely used in various industries requiring high-strength, lightweight, and high-quality joints.
- Aerospace: Fuselage panels, wing structures, fuel tanks.
- Automotive: EV battery trays and enclosures, chassis frames, wheels, suspension components.
- Railway / Rolling Stock: Body panels for high-speed trains, structural components.
- Shipbuilding / Marine: Aluminum deck panels, hulls, offshore structures.
- Electrical / Electronics: Heatsinks for power electronics, enclosures for electronic devices, busbars.
- Defense Industry: Armor plates, structural components for military vehicles.
Castman's FSW Technology
Castman operates FSW equipment, enabling us to perform precise welding on complex 3D-shaped products. We provide comprehensive solutions tailored to our clients' needs, from prototyping and small-batch production to mass production.
We specialize in the high-quality welding of non-ferrous metals like aluminum and copper, and our expertise covers a wide range of applications, including EV battery cases, cooling plates (cold plates), and various electronic components.
If you have any inquiries about FSW, please do not hesitate to contact Castman.
Contact Us
Tel : +82-31-351-5022
Fax: +82-31-351-5033
E-mail : sales@castman.co.kr
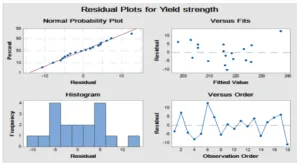
Maximizing Friction Stir Welding (FSW) Strength: A Statistical Optimization for Joining Dissimilar Aluminum Alloys
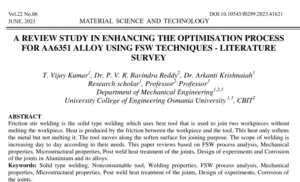
A REVIEW STUDY IN ENHANCING THE OPTIMISATION PROCESS FOR AA6351 ALLOY USING FSW TECHNIQUES – LITERATURE SURVEY
![Figure 1.8 View of FSW [100]](https://castman.co.kr/wp-content/uploads/image-2665-300x191.webp)
Development of FSW and LFW Joints with High Ductility and Fatigue Strength for Weathering Steels
![Figure 1 FSW process scheme (a), FSSW process stages (b) [8]](https://castman.co.kr/wp-content/uploads/Figure-1-FSW-process-scheme-a-FSSW-process-stages-b-8-272x300.webp)
ADVANCED WELDING TECHNOLOGIES: FSW IN AUTOMOTIVE MANUFACTURING
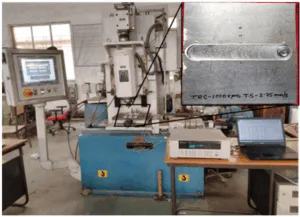
A comprehensive investigation on various welding facets for FSW of advanced structural AMC
![Fig. 1: Representation of the main parameters and nomenclature of FSW joints [2]](https://castman.co.kr/wp-content/uploads/image-2647-300x158.webp)
A Review of Bobbin Tool Friction Stir Welding (FSW) Process
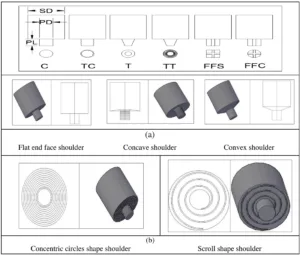
A Critical Review of Friction Stir Welding Process
