settingsOpen AccessReview
Current Trends in Automotive Lightweighting Strategies and Materials
by Frank Czerwinski
CanmetMATERIALS, Natural Resources Canada, Hamilton, ON L8P 0A5, Canada
Academic Editor: Carola Esposito Corcione
Materials2021, 14(21), 6631; https://doi.org/10.3390/ma14216631
Received: 17 September 2021 / Revised: 26 October 2021 / Accepted: 29 October 2021 / Published: 3 November 2021
(This article belongs to the Special Issue Lightweight Structural Materials for Automotive and Aerospace)
Abstract
The automotive lightweighting trends, being driven by sustainability, cost, and performance, that create the enormous demand for lightweight materials and design concepts, are assessed as a part of the circular economy solutions in modern mobility and transportation. The current strategies that aim beyond the basic weight reduction and cover also the structural efficiency as well as the economic and environmental impact are explained with an essence of guidelines for materials selection with an eco-friendly approach, substitution rules, and a paradigm of the multi-material design. Particular attention is paid to the metallic alloys sector and progress in global R&D activities that cover the “lightweight steel”, conventional aluminum, and magnesium alloys, together with well-established technologies of components manufacturing and future-oriented solutions, and with both adjusting to a transition from internal combustion engines to electric vehicles. Moreover, opportunities and challenges that the lightweighting creates are discussed with strategies of achieving its goals through structural engineering, including the metal-matrix composites, laminates, sandwich structures, and bionic-inspired archetypes. The profound role of the aerospace and car-racing industries is emphasized as the key drivers of lightweighting in mainstream automotive vehicles.
Korea Abstract
경량 소재 및 디자인 개념에 대한 엄청난 수요를 창출하는 지속 가능성, 비용 및 성능에 의해 주도되는 자동차 경량화 추세는 현대 이동성 및 운송 분야의 순환 경제 솔루션의 일부로 평가됩니다.
기본적인 경량화를 넘어 구조적 효율성과 경제적, 환경적 영향을 포괄하는 현재의 전략을 친환경적 접근을 통한 자재 선택 가이드라인, 대체 규칙, 멀티 머티리얼 디자인의 패러다임을 핵심으로 설명합니다.
금속 합금 부문과 "경량 강철", 기존 알루미늄 및 마그네슘 합금을 포괄하는 글로벌 R&D 활동의 진행과 부품 제조 및 미래 지향적인 솔루션에 대한 잘 정립된 기술과 함께 내연기관에서 전기차로의 전환이 리루어지고 있습니다
또한 경량화가 창출하는 기회와 과제는 금속 매트릭스 복합 재료, 라미네이트, 샌드위치 구조 및 생체 공학에서 영감을 받은 원형을 포함한 구조 엔지니어링을 통해 목표를 달성하는 전략과 함께 논의됩니다.
항공 우주 및 자동차 경주 산업의 중요한 역할은 주류 자동차에서 경량화의 핵심 동인으로 강조됩니다.
Keywords
automotive lightweighting; circular economy; sustainability; lightweight alloys
1. Introduction
Lightweighting is becoming the major trend, reaching many industrial sectors associated not only with all forms of transportation but more broadly with civil infrastructure, manufacturing, and clean energy technologies [1]. In contrast to common perception, the lightweighting objectives are not exclusively focused on the reduction of weight but cover also other aspects involving the structural efficiency as well as the economic and environmental impact. In industry, reducing the weight of a product not only consumes fewer resources for its manufacturing but also requires less energy for its transportation, thus preserving natural resources and reducing the harmful pollution. Although lightweighting is not a new concept and aerospace has been on the lightweight path since its origin, while other sectors have also pursued it for decades, it is re-emerging as the mature, enormous growth course that is driven by sustainability, cost, and performance.The core lightweighting objectives can be achieved through a number of individual strategies or their combinations that balance the design and material factors. The aim of lightweight design is to build structures with a minimal use of materials and an optimized utilization of the material strength, with numerical methods being developed to model the complex geometries of lightweight structures, e.g., in a parametric isogeometric environment [2]. The material selection has many aspects and just increasing its strength alone leads to a design weight reduction without changing its specific density. Through exploring this factor and using the high strength, Nb-containing weathering steel for, currently, the tallest bridge in the world, Viaduct de Millau, France, allowed for the reduction of its overall weight by 60% and for the related carbon footprint through fabrication, welding, construction, and transportation [3].The ultimate lightweighting goal can be accomplished, however, through an application of lightweight materials and by combining their unique features with other strategies [4]. An increasing demand for lightweight materials led to an expansion of research towards novel solutions with strategies for achieving lightweighting goals through structural engineering, including metal-matrix composites, laminates, sandwich structures, and bionic-inspired archetypes. This report provides an overview of the current lightweighting strategies and materials, with a major focus on structural metallic alloys and their present and possible future applications in automotive transportation. It is a general statement, expressed by global automakers, that the vehicle weight reduction is a core part of the overall technology strategy that the industry will utilize to achieve the future targets of energy consumption, emissions, safety, and affordability.
2. Lightweighting as a Part of the Circular Economy
In contrast to the linear economy, with its predisposition towards wasting valuable resources, the concept of the circular economy offers opportunities for a more productive use of materials through recirculating their larger share through reuse and recycling, thus reducing waste in production and extending the lifetimes of products, and through associated policies (Figure 1). The purpose of moving towards a circular economy is to slow down the depletion of scarce natural resources, reduce environmental damage from an extraction of raw materials, and reduce pollution caused by their processing, use, and end-of-life (EOL) recycling of materials [5].
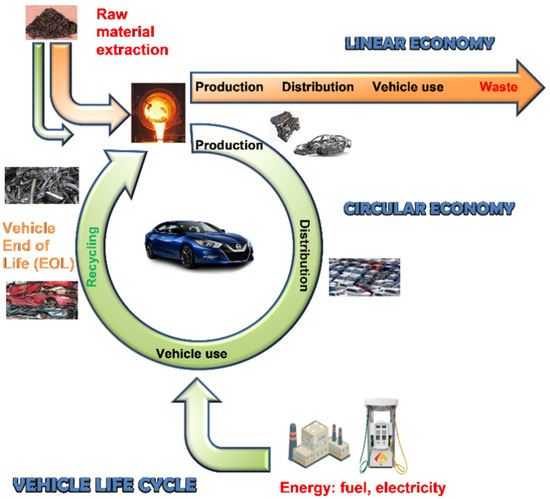
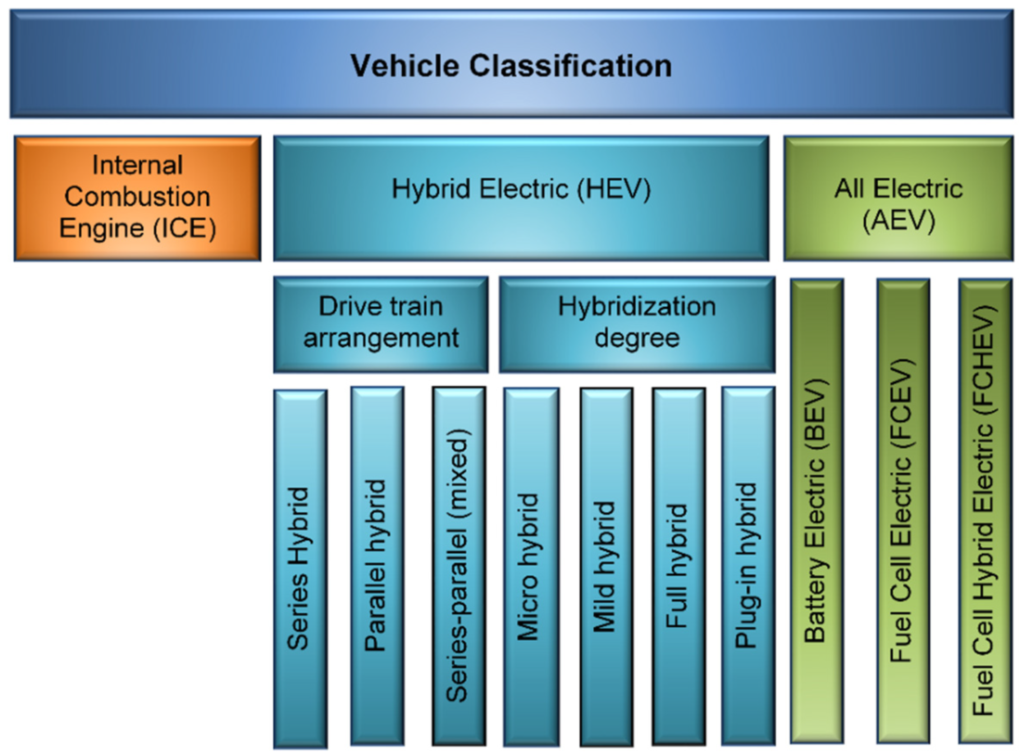
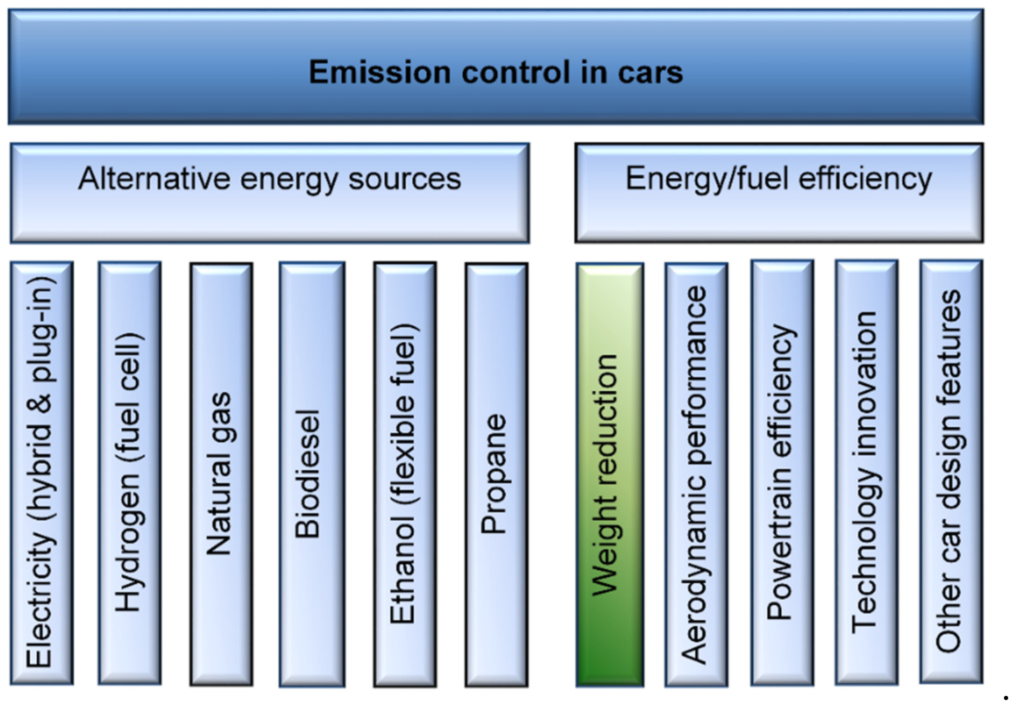
![Figure 4. Architecture difference between internal combustion engine vehicles and battery electric vehicles: (a) ICE, Toyota Crown redesigned platform, 2018 [18], and (b) BEV, Hyundai/Kia/Genesis E-GMP platform, 2021 [19].](https://castman.co.kr/wp-content/uploads/Genesis-E-GMP-platform-2021-19.-1024x265.png)
![Figure 5. A concept of lightweight design through topology optimization: (a) topology optimization work-flow, with the example of a 75% mass reduction for a cube under a compressive load on the top face; (b) post-optimization result, showing element pseudo-densities of >0.25; and (c) structural member of the vehicle suspension assembly after EBM manufacturing and CNC machining [25].](https://castman.co.kr/wp-content/uploads/Figure-5.-A-concept-of-lightweight-design-through-topology-optimization-1024x307.png)
![Figure 6. Examples of manufacturing processes that can be used for the lightweight components of electric vehicles [26].](https://castman.co.kr/wp-content/uploads/Figure-6.-Examples-of-manufacturing-processes-that-can-be-used-for-the-lightweight-components-of-electric-vehicles-26.-1024x442.png)
![Figure 7. An example of the multi-material selection algorithm for lightweight design, taking into account product recyclability [29].](https://castman.co.kr/wp-content/uploads/Figure-7.-An-example-of-the-multi-material-selection-algorithm-for-lightweight-design-taking-into-account-product-recyclability-29.-1024x849.png)
![Figure 8. Multi-material designs of ICE and EV (body-in-white): (a) ICE, multi-material lightweight vehicle (MMLV), Magna, 2015 [33], and (b) EV, Porsche 800 V Taycan electric sports car, 2019 [35].](https://castman.co.kr/wp-content/uploads/Figure-8.-Multi-material-designs-of-ICE-and-EV-body-in-white-1024x265.png)
![Figure 9. Reducing density of steels for automotive applications: (a) density as a function of aluminum content for binary Fe-Al18 and for quaternary 0.2C−8.5Mn (wt.%) alloys, wherein the continuous line corresponds to the density calculation for the quaternary system using Thermo-Calc [39]; (b) elongation (TE) as a function of ultimate tensile strength (UTS) in Fe–Mn–Al–C alloys (solution-treated and water-quenched strips) [40].](https://castman.co.kr/wp-content/uploads/Figure-9.-Reducing-density-of-steels-for-automotive-applications-1024x431.png)
![Figure 10. AHSS steels in electric vehicles: (a) schematics of formability–strength relationships in AHSS and (b,c) contribution of various steel grades to battery electric vehicles developed within the Future Steel Vehicle (FSV) program with 95% HSLA and AHSS, and with 48% having a strength over 1000 MPa, according to the World Steel Association [46].](https://castman.co.kr/wp-content/uploads/Figure-10.-AHSS-steels-in-electric-vehicles-1024x270.png)
![Figure 11. Current and predicted contribution of major automotive materials: (a) aluminum content growth in North American vehicles based on data from [47] and (b) average vehicle structure (body-in-white and closures) material percentage by curb weight per vehicle based on data from [49].](https://castman.co.kr/wp-content/uploads/Figure-11.-Current-and-predicted-contribution-of-major-automotive-materials-1024x363.png)
![Figure 12. Considered application of aluminum in electric cars: (a,b) aluminum sheet battery enclosures of 1st and 2nd generation by Novelis [54] and (c,d) concept of lightweight drum brake and bionic-inspired caliper by Continental [55].](https://castman.co.kr/wp-content/uploads/Figure-12.-Considered-application-of-aluminum-in-electric-cars-1024x435.png)
![Figure 13. Example of Life Cycle Assessments of AHSS steel and aluminum in electric cars: (a) savings by stage and (b) savings by use phase. Details of the model, developed by the European Aluminum, are available from [66].](https://castman.co.kr/wp-content/uploads/Figure-13.-Example-of-Life-Cycle-Assessments-of-AHSS-steel-and-aluminum-in-electric-cars-1024x329.png)
![Figure 14. Schematics of semisolid processing and examples of automotive components manufactured from magnesium alloy using injection molding: (a) car seat backrest AM50, 1970 g; (b) car dashboard member AZ91D, 138 g; (c) car navigator member AZ91D, 280 g; (d) car dashboard member AZ91D, 710 g; and (e) car navigator member AZ91D, 278 g. Parts manufactured by SSD Magnesium, China [76].](https://castman.co.kr/wp-content/uploads/Figure-14.-Schematics-of-semisolid-processing-and-examples-of-automotive-components-manufactured-from-magnesium-alloy-using-injection-molding-1024x348.png)
![Figure 15. Aluminum matrix composite use in automotive parts: (a,b) MMC rotor of an axial flux electric motor and a hydrogen fuel cell compressor developed by Alvant, UK [86] and (c,d) composite manufactured by a reinforcement of the aluminum matrix through a steel mesh [87].](https://castman.co.kr/wp-content/uploads/Figure-15.-Aluminum-matrix-composite-use-in-automotive-parts-1024x427.png)
![Figure 16. Application of fiber metal laminates in automotive parts: (a) general concept of FML [90]; (b) elastic and plastic regions of the steel–FRP composite under three-point bending [94]; and (c) 2016 BMW 7 Series (G12) CFRP B-pillar inner reinforcement [95].](https://castman.co.kr/wp-content/uploads/Figure-16.-Application-of-fiber-metal-laminates-in-automotive-parts-1024x306.png)
![Figure 17. Sandwich-structured composites: (a) schematics showing elements of the sandwich structure [105]; (b) aluminum foam sandwich [105]; and (c,d) concept of applying the lightweight aluminum and ARPRO propylene-based foam sandwich material in a car (Inrekor, UK) [110].](https://castman.co.kr/wp-content/uploads/Figure-17.-Sandwich-structured-composites-1024x561.png)
![Figure 18. Bionic-inspired cellular structure design: (a) bee honeycomb pattern; (b) geometry of the cellular structure designed for numerical modelling [112]; (c) fractal texture of the wings of dragonflies; and (d) finite element model of the novel fractal structures [114]](https://castman.co.kr/wp-content/uploads/Figure-18.-Bionic-inspired-cellular-structure-design-1024x578.png)
![Figure 19. Additive manufacturing of ultralight components: (a) octahedron cell lattice of the structure; (b,c) detailed image of the structure manufactured by laser powder bed fusion using Inconel 718; and (d) deformation map during the vertical compression [118].](https://castman.co.kr/wp-content/uploads/Figure-19.-Additive-manufacturing-of-ultralight-components-1024x442.png)
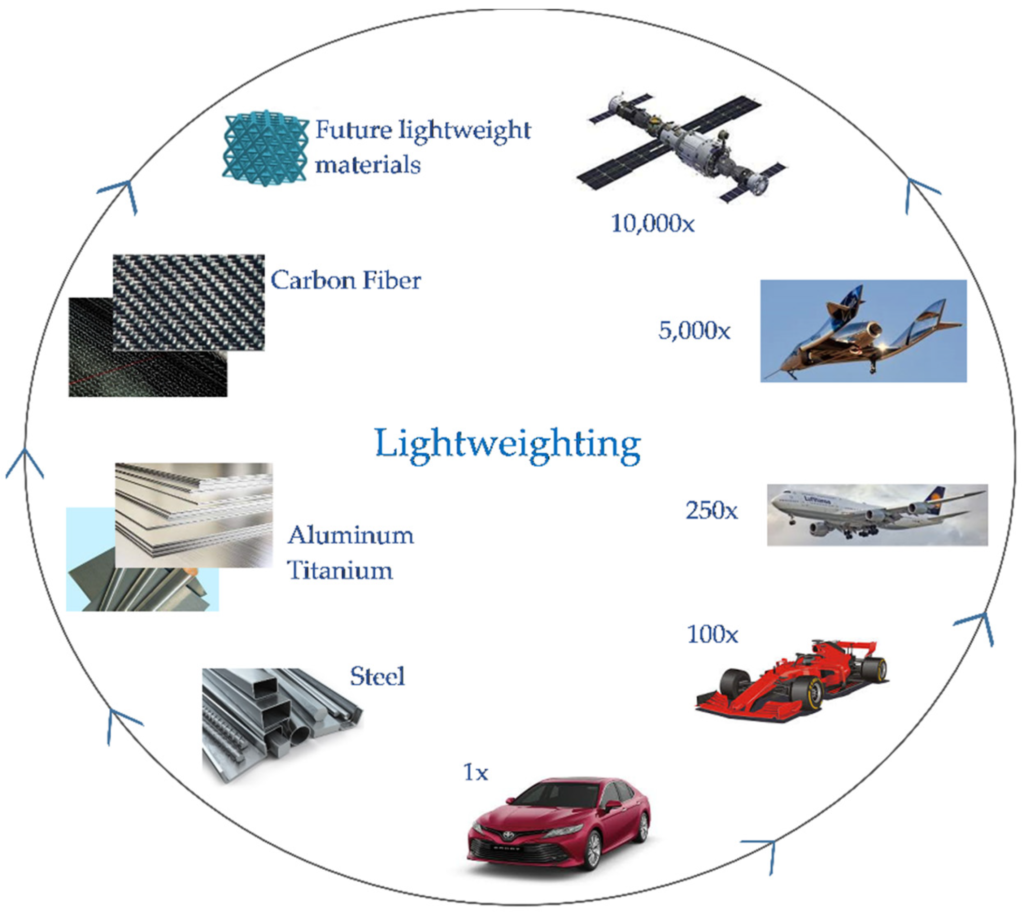
10. Conclusions
The automotive lightweighting strategy is becoming the mature growth trend, driven by sustainability, cost, and performance, and creating an enormous demand for modern lightweight materials and design concepts. The lightweighting strategy is growing as a part of the circular economy and is the solution for both modern mobility and transportation; its objectives are not exclusively focused on the reduction of weight but also cover other aspects such as structural efficiency as well as economic and environmental impacts. It appears that the emergence of electric vehicles creates even more pressure on lightweighting.In current lightweighting strategies, in addition to design, the materials represent the key part of the trend. A quest for lightweight materials creates many challenges and opportunities not only for existing conventional metallic alloys but also for novel strategies of achieving lightweighting goals through structural engineering, including metal-matrix composites, laminates, sandwich structures, and bionic-inspired archetypes.Lightweighting design combined with the use of advanced lightweight materials leads to structural optimization, maximum weight reduction, and fulfilled required performance and safety standards. Manufacturability is still an important limitation to the design of lightweight structures but with progress in additive manufacturing, this constraint will gradually be eliminated.
This research study was funded by the Program of Energy Research and Development (PERD) of Natural Resources Canada.
References
- Lutsey, N. Review of Technical Literature and Trends Related to Automobile Mass-Reduction Technology; Research Report UCD-ITS-RR-10-10; Institute of Transportation Studies, University of California: Davis, CA, USA, 2010. [Google Scholar]
- Goldbach, A.-K.; Bauer, A.; Wüchner, R.; Bletzinger, K.-U. CAD-Integrated Parametric Lightweight Design with Isogeometric B-Rep Analysis. Front. Built Environ. 2020, 6, 44. [Google Scholar] [CrossRef]
- Jansto, S. Steel Producers Respond to Demand for High Performance Bridge Steels with Niobium; CBMM North America, Inc.: Pittsburgh, PA, USA, 2020; Available online: www.cbmm.com (accessed on 15 August 2021).
- Campbell, F. (Ed.) Lightweight Materials: Understanding the Basics; ASM International: Novelty, OH, USA, 2012. [Google Scholar]
- Ekins, P.; Domenech, T.; Drummond, P.; Bleischwitz, R.; Hughes, N.; Lotti, L. The Circular Economy: What, Why, How and Where. In Managing Environmental and Energy Transitions for Regions and Cities, Proceedings of the OECD/EC Workshop, Paris, France, 5 July 2019; OECD: Paris, France, 2019. [Google Scholar]
- Nuss, P.; Eckelman, M.J. Life Cycle Assessment of Metals: A Scientific Synthesis. PLoS ONE 2014, 9, e101298. [Google Scholar] [CrossRef]
- Hottle, T.; Caffery, C.; McDonnald, J.; Dodder, R. Critical factors affecting life cycle assessments of material choice for vehicle mass reduction. Transp. Res. D Transp. Environ. 2017, 56, 241–257. [Google Scholar] [CrossRef] [PubMed]
- Relland, J.; Bax, L.; Ierdes, M. A Vision on the Future of Automotive Lightweighting; Alliance: Surrey, UK, 2019. [Google Scholar]
- Feloy, M.; Souza, R.D.; Jones, R.; Bayliss, M. Technology and Skills in the Aerospace and Automotive Industries; Evidence Report 76; UK Commission for Employment and Skills: London, UK, 2013. [Google Scholar]
- Albatayneh, A.; Assaf, M.N.; Alterman, D.; Jaradat, M. Comparison of the Overall Energy Efficiency for Internal Combustion Engine Vehicles and Electric Vehicles. Environ. Clim. Technol. 2020, 24, 669–680. [Google Scholar] [CrossRef]
- Sanguesa, J.; Torres-Sanz, V.; Garrido, P.; Martinez, F.; Marquez-Barja, J. A Review on Electric Vehicles: Technologies and Challenges. Smart Cities 2021, 4, 372–404. [Google Scholar] [CrossRef]
- Lidoy, J.B.; Moreno, J.M. Eficiencia energética en la automoción, el vehículo eléctrico, un reto del presente. Econ. Ind. 2010, 377, 76–85. [Google Scholar]
- Kumar, D.; Nema, R.K.; Gupta, S. A comparative review on power conversion topologies and energy storage system for electric vehicles. Int. J. Energy Res. 2020, 44, 7863–7885. [Google Scholar] [CrossRef]
- Automotive Lightweight Material Market—Global Forecast to 2025. Markets and Markets. 2021. Available online: www.marketsandmarkets.com (accessed on 24 May 2021).
- Alonso, E.; Lee, T.M.; Bjelkengren, C.; Roth, R.; Kirchain, R. Evaluating the Potential for Secondary Mass Savings in Vehicle Lightweighting. Environ. Sci. Technol. 2012, 46, 2893–2901. [Google Scholar] [CrossRef]
- Electric Vehicles to Transform Aluminum Demand by 2035. Eccomelt LLC. Available online: https://eccomelt.com/electric-vehicles-transform-aluminum-demand-2035/ (accessed on 3 September 2021).
- Kumanan, A.; Varadarajan, S.; Narayanan, K. Lightweighting in Electric Vehicles: Review of the Design Strategies Based on Patents and Publications. In Design for Tomorrow—Volume 3. Smart Innovation, Systems and Technologies; Chakrabarti, A., Poovaiah, R., Bokil, P., Kant, V., Eds.; Springer: Singapore, 2021; Volume 223. [Google Scholar] [CrossRef]
- Toyota Rolls Out Completely Redesigned Crown. Toyota. 28 June 2018. Available online: https://global.toyota/en/newsroom/toyota/23102775.html (accessed on 28 August 2021).
- Halvorson, B. Electric Car Platform for Hyundai, Kia, and Genesis. Green Car Reports. 2 December 2020. Available online: https://www.greencarreports.com/news/1130487_ev-platform-hyundai-kia-genesis-bi-directional-charging-robotaxi-ready (accessed on 28 August 2021).
- Osborne, J. FEATURE: Light Speed—How Electric Cars are Driving a New Wave of Lightweighting. Institution of Mechanical Engineers. 2019. Available online: https://www.imeche.org/news/news-article/feature-light-speed-how-electric-cars-are-driving-a-new-wave-of-lightweighting (accessed on 2 September 2021).
- Moen, L. How Lightweight Design Saves Costs in Battery-Electric Vehicles. Shapes—The Aluminium Knowledge Hub. 2020. Available online: https://www.shapesbyhydro.com/en/sustainable-design/how-lightweight-design-saves-costs-in-battery-electric-vehicles/ (accessed on 1 September 2021).
- Jackson, N. Lightweight Vehicle and Powertrain Structures Roadmap 2020; UK Automotive Council: London, UK, 2021. [Google Scholar]
- By 2030 Battery Electric Vehicles Will Be Less Reliant on Lightweighting. Available online: http://connectedenergysolutions.co.uk/by-2030-battery-electric-vehicles-will-be-less-reliant-on-lightweighting/ (accessed on 10 August 2021).
- Kaluza, A.; Frohlich, T.; Kleeman, S.; Walk, W.; Herrmann, C.; Krinke, S. Conceptual Development of Hybrid Structures Towards Eco-Efficient Vehicle Lightweighting. In Designing Sustainable Technologies, Products and Policies; Benetto, E., Gericke, K., Guiton, M., Eds.; Springer: Cham, Switzerland, 2018; pp. 181–191. [Google Scholar]
- Walton, D.; Moztarzadeh, H. Design and Development of an Additive Manufactured Component by Topology Optimization. Procedia CIRP 2017, 60, 205–210. [Google Scholar] [CrossRef]
- Rosenthal, S.; Maaß, F.; Kamaliev, M.; Hahn, M.; Gies, S.; Tekkaya, A.E. Lightweight in automotive components by forming technology. Automot. Innov. 2020, 3, 195–209. [Google Scholar] [CrossRef]
- Kopp, G.; Geeh, E. New multi-material design concepts and high integration of light metals application for lightweight body structure. Mater. Sci. Forum 2010, 638–642, 437–442. [Google Scholar] [CrossRef]
- Kleeman, S.; Frohlich, T.; Turck, E.; Vietor, T. A methodological approach towards multi-material design of automotive components. Procedia CIRP 2017, 60, 68–73. [Google Scholar] [CrossRef]
- Kromm, F.; Quenisset, J.; Lorriot, T.; Harry, R.; Wargnier, H. Definition of a multi-materials design method. Mater. Des. 2007, 28, 2641–2646. [Google Scholar] [CrossRef]
- Sakudarini, N.; Taha, Z.; Abdul-Rashid, Z.; Ghazila, R. Optimal multi-material selection for lightweight design of automotive body assembly incorporating recyclability. Mater. Des. 2013, 50, 846–857. [Google Scholar] [CrossRef]
- Li, C.; Kim, I.Y. Multi-material topology optimization for automotive design problems. Proc. Inst. Mech. Eng. Part D J. Automob. Eng. 2017, 232, 1950–1969. [Google Scholar] [CrossRef]
- Bushi, L.; Skszek, T.; Wagner, D. MMLV: Life Cycle Assessment; SAE Technical Paper 2015-01-1616; SAE: Warrendale, PA, USA, 2015. [Google Scholar] [CrossRef]
- Multi Material Lightweight Vehicle (MMLV). Magna, Cosma International. Available online: https://www.magna.com/docs/default-source/Body-Chassis-Systmes/mmlv_one_pager.pdf?sfvrsn=4 (accessed on 31 August 2021).
- Skszek, T.; Conklin, J.; Wagner, D.; Zaluzec, M. Multi-Material Lightweight Vehicles; Vema International, Ford Motor Co.: Dearborn, MI, USA, 2015. Available online: www.energy.gov (accessed on 15 August 2021).
- Porsche’s 800V Electric Sports Car Taycan Makes World Debut. Green Car Congress. 5 September 2019. Available online: https://www.greencarcongress.com/2019/09/20190905-taycan.html (accessed on 10 September 2021).
- Yellishetty, M.; Mudd, G.; Ranjith, P.; Tharumarajah, A. Environmental life-cycle comparisons of steel production and recycling: Sustainability issues, problems and prospects. Environ. Sci. Policy 2011, 14, 650–663. [Google Scholar] [CrossRef]
- Korter, W.; Ton, W. Die Eisenecke des Systems Eisen-Mangan-Aluminium. Arch. Eisenhuettenw. 1933, 7, 365–366. [Google Scholar]
- Rana, R.; Lahaye, C.; Ray, R.K. Overview of Lightweight Ferrous Materials: Strategies and Promises. JOM 2014, 66, 1734–1746. [Google Scholar] [CrossRef]
- Zuazo, I.; Hallstedt, B.; Lindahl, B.; Selleby, M.; Soler, M.; Etienne, A.; Perlade, A.; Hasenpouth, D.; Massardierjourdan, V.; Cazottes, S.; et al. Low-Density Steels: Complex Metallurgy for Automotive Applications. JOM 2014, 66, 1747–1758. [Google Scholar] [CrossRef]
- Chen, S.; Rana, R.; Haldar, A.; Ray, R.K. Current state of Fe-Mn-Al-C low density steels. Prog. Mater. Sci. 2017, 89, 345–391. [Google Scholar] [CrossRef]
- Wu, Z.; Ding, H.; An, X.X.; Han, D.; Liao, X. Influence of Al content on the strain-hardening behavior of aged low density Fe–Mn–Al–C steels with high Al content. Mater. Sci. Eng. A 2015, 639, 187–191. [Google Scholar] [CrossRef]
- Kim, S.-H.; Kim, H.; Kim, N.J. Brittle intermetallic compound makes ultra strong low-density steel with large ductility. Nature 2015, 518, 77–79. [Google Scholar] [CrossRef]
- Kuziak, R.; Kawalla, R.; Waengler, S. Advanced high strength steels for automotive industry. Arch. Civ. Mech. Eng. 2008, 8, 103–117. [Google Scholar] [CrossRef]
- Bleck, W.; Brühl, F.; Ma, Y.; Sasse, C. Materials and processes for the third-generation advanced high-strength steels. Berg Huettenmaenn Mon. 2019, 164, 466–474. [Google Scholar] [CrossRef]
- Tisza, M. Development of Lightweight Steels for Automotive Applications. In Engineering Steels and High Entropy-Alloys; Sharma, A., Duriagina, Z., Kumar, S., Eds.; IntechOpen: London, UK, 2020. [Google Scholar]
- 20 Years of Automotive Steel Contributions. WorldAutoSteel. 18 April 2016. Available online: https://www.worldautosteel.org/20-years-of-automotive-steel-contributions/ (accessed on 10 September 2021).
- Swensen, A. Aluminum Continues Unprecedented Growth in Automotive Applications. Light Metal Age. October 2020. Available online: www.lightmetalage.com (accessed on 29 October 2021).
- Automotive Life-Cycle Assessment Model. European Aluminium. 16 June 2015. (Update December 2018). Available online: https://www.european-aluminium.eu/resource-hub/automotive-lca-model (accessed on 2 August 2021).
- Modi, S.; Vadhavkar, A. Technology Roadmap: Intelligent Mobility Technologies; Center for Automotive Research: Ann Arbor, MI, USA, 2019. [Google Scholar]
- Sakurai, T. The latest trends in aluminum alloy sheets for automotive body panels. Kobelco Technol. Rev. 2008, 28, 2–28. [Google Scholar]
- Ota, Y.; Masuda, T.; Kimura, S. Technical trends in aluminum alloy sheets for automotive body panels. Kobelco Technol. Rev. 2020, 16–20. Available online: www.kobelco.co.jp (accessed on 27 October 2021).
- Hirsch, J. Recent development in aluminium for automotive applications. Trans. Nonferrous Met. Soc. China 2014, 24, 1995–2002. [Google Scholar] [CrossRef]
- Long, R.S.; Boettcher, E.; Crawford, D. Current and future uses of aluminum in the automotive industry. JOM 2017, 69, 2635–2639. [Google Scholar] [CrossRef]
- Novelis Develops World’s First Aluminum Sheet Battery Enclosure—30 April 2019; Novelis Introduces Second-Generation Aluminum Intensive Battery Enclosure Solution for Electric Vehicles—26 October 2021. Available online: https://www.novelis.com/NewsReleases (accessed on 27 October 2021).
- Carney, D. Lightweight Aluminum Might Seem Like an Obvious Choice for EV Brakes, but it Brings Numerous Challenges. Design News. 30 April 2020. Available online: https://www.designnews.com/automotive/lightweight-aluminum-brakes-evs-are-continentals-aim (accessed on 12 September 2021).
- Czerwinski, F. Thermomechanical processing of metal feedstock for semisolid forming: A Review. Met. Mater. Trans. A 2018, 49, 3220–3257. [Google Scholar] [CrossRef]
- Jarfors, A. A comparison between semisolid casting methods for aluminium alloys. Metals 2020, 10, 1368. [Google Scholar] [CrossRef]
- Côté, P.; Vlastimil, B.; Stunová, B.B. Case Study: Engine bracket made by rheocasting using the seed process. Solid State Phenom. 2019, 285, 441–445. [Google Scholar] [CrossRef]
- Czerwinski, F. Thermal stability of aluminum alloys. Materials 2020, 13, 3441. [Google Scholar] [CrossRef] [PubMed]
- Czerwinski, F.; Kasprzak, W.; Sediako, D.; Emadi, D.; Shaha, S.; Friedman, J.; Chen, D. High-temperature aluminum alloys for automotive powertrains. Adv. Mater. Process. 2016, 174, 16–20. [Google Scholar]
- Czerwinski, F. Cerium in aluminum alloys. J. Mater. Sci. 2019, 55, 24–72. [Google Scholar] [CrossRef]
- Czerwinski, F.; Amirkhiz, B.S. On the Al-Al11Ce3 eutectic transformation in aluminum-cerium binary alloys. Materials 2020, 13, 4549. [Google Scholar] [CrossRef]
- Czerwinski, F. Assessing differences between the use of cerium and scandium in aluminum alloying. Mater. Sci. Technol. 2020, 36, 255–263. [Google Scholar] [CrossRef]
- Czerwinski, F. Thermal stability of aluminum-cerium binary alloys containing the Al11Ce3 eutectic. Mater. Sci. Eng. A 2021, 809, 140973. [Google Scholar] [CrossRef]
- Czerwinski, F. Thermal stability of aluminum-nickel binary alloys containing the Al-Al3Ni eutectic. Met. Mater. Trans. A 2021, 52, 4342–4356. [Google Scholar] [CrossRef]
- Automotive Life Cycle Assessment Model. European Aluminum Association. 2019. Available online: https://www.european-aluminium.eu/resource-hub/automotive-lca-model/ (accessed on 3 September 2021).
- Bertram, M.; Bayliss, C. Updated automotive lifecycle assessment model launched. Light Met. Age 2019, 77, 10–14. [Google Scholar]
- Battery Electric Vehicle Life Cycle Energy Aluminium vs. AHSS: A Case Study. WorldAutoSteel. Available online: https://www.worldautosteel.org/life-cycle-thinking/case-studies/battery-electric-vehicle-life-cycle-energy-aluminium-vs-ahss/ (accessed on 3 September 2021).
- Kulekci, M.K. Magnesium and its alloys applications in automotive industry. Int. J. Adv. Manuf. Technol. 2007, 39, 851–865. [Google Scholar] [CrossRef]
- Czerwinski, F. Magnesium Injection Molding; Springer: New York, NY, USA, 2008. [Google Scholar]
- Hirsch, J.; Al-Samman, T. Superior light metals by texture engineering: Optimized aluminum and magnesium alloys for automotive applications. Acta Mater. 2013, 61, 818–843. [Google Scholar] [CrossRef]
- Javaid, A.; Hadadzadeh, A.; Czerwinski, F. Solidification behavior of dilute Mg-Zn-Nd alloys. J. Alloys Compd. 2019, 782, 132–148. [Google Scholar] [CrossRef]
- Javaid, A.; Czerwinski, F. Effect of hot rolling on microstructure and properties of the ZEK100 alloy. J. Magnes. Alloys 2019, 7, 27–37. [Google Scholar] [CrossRef]
- Javaid, A.; Czerwinski, F. Progress in twin roll casting of magnesium alloys: A review. J. Magnes. Alloys 2020, 9, 362–391. [Google Scholar] [CrossRef]
- Czerwinski, F. Exploring thixoforming for net shape manufacturing. Adv. Mater. Process. 2019, 177, 14–19. [Google Scholar]
- Magnesium Semisolid Forming Equipment. SSD-Magnesium. Available online: http://www.ssd-magnesium.com/product/I8rC1o.html (accessed on 10 September 2021).
- Kim, J.; Han, S. Recent development and applications of magnesium alloys in the Hyundai and Kia Motors Corporation. Mater. Trans. 2008, 49, 894–897. [Google Scholar] [CrossRef]
- Joost, W.J.; Krajewski, P.E. Towards magnesium alloys for high-volume automotive applications. Scr. Mater. 2017, 128, 107–112. [Google Scholar] [CrossRef]
- Luo, A.A. Magnesium: Current and potential automotive applications. JOM 2002, 54, 42–48. [Google Scholar] [CrossRef]
- Kareta, N. IMA Report Vehicle Construction—Life Cycle Assessment of MAGNESIUM components. Spot Light Metal. 2021. Available online: https://www.spotlightmetal.com/vehicle-construction--life-cycle-assessment-of-magnesium-components-a-1027791/ (accessed on 1 September 2021).
- Xu, T.; Yang, Y.; Peng, X.; Song, J.; Pan, F. Overview of advancement and development trend on magnesium alloy. J. Magnes. Alloys 2019, 7, 536–544. [Google Scholar] [CrossRef]
- Ehrenberger, S. Carbon Footprint of Magnesium Production and its Use in Transport Applications; Update of the IMA Report Life Cycle Assessment of Magnesium Components in Vehicle Construction (2013); DLR German Aerospace Center e.V., Institute of Vehicle Concepts: Stuttgart, Germany, 2020. [Google Scholar]
- Mussatto, A.; Ahad, I.U.; Mousavian, R.T.; Delaure, Y.; Brabazon, D. Advanced production routes for metal matrix composites. Eng. Rep. 2021, 3, e12330. [Google Scholar] [CrossRef]
- Prasad, S.; Asthana, R. Aluminum metal-matrix composites for automotive applications: Tribological considerations. Tribol. Lett. 2004, 17, 445–453. [Google Scholar] [CrossRef]
- Vellingiri, S. The future in metal matrix composites for automotive Industry: A Review. Int. Res. J. Automot. Technol. 2018, 1, 88–100. [Google Scholar]
- Metal Matrix Composites Deliver 40 per cent Weight Saving for Electric Motor Rotors. Alvant Ltd., 29 January 2019. Available online: https://www.alvant.com/news/mmc-electric-motors/ (accessed on 15 September 2021).
- Frolov, Y.; Nosko, M.; Samsonenko, A.; Bobukh, O.; Remez, O. Roll Bonding of Al-Based Composite Reinforced with C10 Steel Expanded Mesh Inlay. Metals 2021, 11, 1044. [Google Scholar] [CrossRef]
- Huang, H.; Wang, J.; Liu, W. Mechanical properties and reinforced mechanism of the stainless steel wire mesh–reinforced Al-matrix composite plate fabricated by twin-roll casting. Adv. Mech. Eng. 2017, 9, 1687814017716639. [Google Scholar] [CrossRef]
- Szczepanik, S. Composites of aluminum alloy matrix reinforced by a steel mesh. Mater. Today Proc. 2015, 25, S9–S18. [Google Scholar] [CrossRef]
- Rodi, R.; Alderliesten, R.; Benedictus, R. Experimental characterization of the crack-tip-opening angle in fiber metal laminates. Eng. Fract. Mech. 2010, 77, 1012–1024. [Google Scholar] [CrossRef]
- Sinmazçelik, T.; Avcu, E.; Bora, M.Ö.; Çoban, O. A review: Fiber metal laminates, background, bonding types and applied test methods. Mater. Des. 2011, 32, 3671–3685. [Google Scholar] [CrossRef]
- Ding, Z.; Wang, H.; Luo, J.; Li, N. A review on forming technologies of fiber metal laminates. Int. J. Lightweight Mater. Manuf. 2021, 4, 110–126. [Google Scholar] [CrossRef]
- Heggemann, T.; Homberg, W. Deep drawing of fiber metal laminates for automotive lightweight structures. Compos. Struct. 2019, 216, 53–57. [Google Scholar] [CrossRef]
- Lin, Y.; Min, J.; Teng, H.; Lin, J.; Hu, J.; Xu, N. Flexural performance of steel–FRP composites for automotive applications. Automot. Innov. 2020, 3, 1–16. [Google Scholar] [CrossRef]
- A guide to Carbon Fiber Reinforced Polymer Repairs. Vehicle Service Pros. 1 December 2016. Available online: https://www.vehicleservicepros.com/collision-repair/body-shop-and-repair/article/21191679/a-guide-to-carbon-fiber-reinforced-polymer-repairs (accessed on 10 September 2021).
- Ishak, N.M.; Malingam, S.D.; Mansor, M.R.; Razali, N.; Mustafa, Z.; Ab Ghani, A.F. Investigation of natural fiber metal laminate as car front hood. Mater. Res. Express 2021, 8, 025303. [Google Scholar] [CrossRef]
- Santhosh, M.; Sasikumar, R.; Thangavel, T.; Pradeep, A.; Poovarasan, K.; Periyasamy, S.; Premkumar, T. Fabrication and characterization of Basalt/Kevlar/Aluminum fiber metal laminates for automobile applications. Int. J. Mater. Sci. 2019, 14, 1–9. [Google Scholar]
- Bachman, K. Steel, aluminum laminate an alternative material for vehicle light weighting. Stamp. J. Available online: www.thefabricator.com/stampingjournal (accessed on 3 February 2020).
- Feng, Y.; Qiu, H.; Gao, Y.; Zheng, H.; Tan, J. Creative design for sandwich structures: A review. Int. J. Adv. Robot. Syst. 2020, 17, 1729881420921327. [Google Scholar] [CrossRef]
- Brückmann, S.M.; Friedrich, H.E.; Kriescher, M.; Kopp, G.; Gätzi, R. Lightweight sandwich structures in innovative vehicle design under crash load cases. Mater. Sci. Forum 2016, 879, 2419–2427. [Google Scholar] [CrossRef]
- Ferrari, F. Lightweight Metal/Polymer/Metal Sandwich Composites for Automotive Applications. Master’s Thesis, University of Windsor, Windsor, ON, Canada, 2017. [Google Scholar]
- Hagnell, M.; Kumaraswamy, S.; Nyman, T.; Åkermo, M. From aviation to automotive—A study on material selection and its implication on cost and weight efficient structural composite and sandwich designs. Heliyon 2020, 6, e03716. [Google Scholar] [CrossRef] [PubMed]
- Zaharia, S.; Enescu, L.; Pop, M. Mechanical Performances of Lightweight Sandwich Structures Produced by Material Extrusion-Based Additive Manufacturing. Polymers 2020, 12, 1740. [Google Scholar] [CrossRef]
- Banhart, J.; García-Moreno, F.; Heim, K.; Seeliger, H.-W. Light-weighting in transportation and defense using aluminum foam sandwich structures. In Proceedings of the International Symposium on Light Weighting for Defense, Aerospace and Transportation, Indian Institute of Metals, Goa, India, 11 November 2017. [Google Scholar]
- Sandwich Structures. Tasuns Composite Technology Co., Ltd., 12 November 2017. Available online: https://www.china-composites.net/info/sandwich-structures-22060296.html (accessed on 12 September 2021).
- Banhart, J. Aluminium foams for lighter vehicles. Int. J. Veh. Des. 2005, 37, 114. [Google Scholar] [CrossRef]
- Yao, C.; Hu, Z.; Mo, F.; Wang, Y. Fabrication and Fatigue Behavior of Aluminum Foam Sandwich Panel via Liquid Diffusion Welding Method. Metals 2019, 9, 582. [Google Scholar] [CrossRef]
- Hommel, P.; Roth, D.; Binz, H. Derivation of motivators for the use of aluminum foam sandwich and advantageous applications. In Proceedings of the International Conference on Engineering Design (ICED21), Chalmers University of Technology, Gothenburg, Sweden, 16–20 August 2021. [Google Scholar]
- Quagliato, L.; Jang, C.; Murugesan, M.; Kim, N. Steel skin—SMC laminate structures for lightweight automotive manufacturing. J. Phys. Conf. Ser. 2019, 896, 012086. [Google Scholar] [CrossRef]
- Ireson, N. Lightweight Aluminum-Foam Sandwich Material May Solve Porky Car Problem. Motor Authority. 15 September 2010. Available online: https://www.motorauthority.com/news/1049388_lightweight-aluminum-foam-sandwich-material-may-solve-porky-car-problem (accessed on 12 September 2021).
- Zhang, Q.; Yang, X.; Li, P.; Huang, G.; Feng, S.; Shen, C.; Han, B.; Zhang, X.; Jin, F.; Xu, F.; et al. Bioinspired engineering of honeycomb structure—Using nature to inspire human innovation. Prog. Mater. Sci. 2015, 74, 332–400. [Google Scholar] [CrossRef]
- Mudassir, M.; Tarlochan, F.; Mansour, M. Nature-Inspired Cellular Structure Design for Electric Vehicle Battery Compartment: Application to Crashworthiness. Appl. Sci. 2020, 10, 4532. [Google Scholar] [CrossRef]
- Wu, Y.-Q.; Guo, C.; Li, L.-H.; Dai, Z.-D.; Tao, C.W. Design of Bio-Inspired Lightweight Sandwich Structure and Its Mechanical Performance. Mech. Mater. Sci. 2017, 404–411. [Google Scholar] [CrossRef]
- Li, K.; Feng, Y.; Gao, Y.; Zheng, H.; Qiu, H. Crashworthiness optimization design of aluminum alloy thin-walled triangle column based on bioinspired strategy. Materials 2020, 13, 666. [Google Scholar] [CrossRef] [PubMed]
- Baroutaji, A.; Arjunan, A.; Niknejad, A.; Tran, T.; Olabi, A. Application of cellular material in crashworthiness applications: An Overview. In Reference Module in Materials Science and Materials Engineering; Elsevier: Amsterdam, The Netherlands, 2019. [Google Scholar] [CrossRef]
- Lippert, R.; Laymayer, R. Bionic inspired infill structures for a light-weight design by using slm. In Proceedings of the International Design Conference—DESIGN 2016, Dubrovnik, Croatia, 16–19 May 2016. [Google Scholar]
- Liu, G.; Zhang, X.; Chen, X.; He, Y.; Cheng, L.; Huo, M.; Yin, J.; Hao, F.; Chen, S.; Wang, P.; et al. Additive manufacturing of structural materials. Mater. Sci. Eng. R Rep. 2021, 145, 100596. [Google Scholar] [CrossRef]
- Calleja-Ochoa, A.; Gonzalez-Barrio, H.; de Lacalle, N.L.; Martínez, S.; Albizuri, J.; Lamikiz, A.A. A new approach in the design of microstructured ultralight components to achieve maximum functional performance. Materials 2021, 14, 1588. [Google Scholar] [CrossRef]
- Benedetti, M.; du Plessis, A.; Ritchie, R.; Dallago, M.; Razavi, S.; Berto, F. Architected cellular materials: A review on their mechanical properties towards fatigue-tolerant design and fabrication. Mater. Sci. Eng. R Rep. 2021, 144, 100606. [Google Scholar] [CrossRef]
- Ashby, M. Materials Selection in Mechanical Design, 5th ed.; Butterworth-Heinemann: London, UK, 2016. [Google Scholar]
- Kumar, A.; Gupta, M. An Insight into evolution of lightweight high entropy alloys: A Review. Metals 2016, 6, 199. [Google Scholar] [CrossRef]
- Flores-Leonard, M.; Meija-Mendoza, L. Materials Acceleration Platforms: On the way to autonomous experimentation. Curr. Opin. Green Sustain. Chem. 2020, 25, 100370. [Google Scholar] [CrossRef]