EwanLordanaYijieZhangaKunDouabAlainJacotacChrysoulaTzileroglouaPaulBlakedZhongyunFanaa
Brunel Centre for Advanced Solidification Technology, Brunel University London, Uxbridge, Middlesex, UB83PH, UK
bSchool of Metallurgy and Environment, Central South University, Changsha, 410083, Hunan, China
cCalcom ESI SA, SwitzerlanddJaguar Land Rover Ltd, Coventry, CV3 4LF, UK
Abstract
This article unmasks the probabilistic nature of high-pressure die casting; specifically, the cause of scatter in the tensile ductility of die-cast Al8Si0·4Mn0·3Mg (wt.%) alloy. Scatter in tensile ductility is related to the size of large pores and non-metallic inclusions. We propose that these non-metallic inclusions form during the pyrolysis of commercial plunger lubricants, and that these large pores derive from dilatational strains introduced during semi-solid deformation. The apparent randomness of pore formation is thus ascribed to the heterogeneous nature of the semi-solid network. Reducing heat loss in the shot chamber is shown to promote a more homogeneous grain structure, leading to a decrease in the maximum pore size from 1.32 mm to 0.37 mm, and an increase in the minimum tensile ductility from 6.8% to 9.4%.
이 기사는 고압 다이캐스팅의 확률론적 특성에 대해 설명합니다. 특히, 다이 캐스트 Al8Si0 · 4Mn0 · 3Mg (wt. %) 합금의 인장 연성에서 산란의 원인이 됩니다. 인장 연성의 산란은 큰 기공 및 비금속 개재물의 크기와 관련이 있습니다. 우리는 이러한 비금속 개재물이 상업용 플런저 윤활유의 열분해 과정에서 형성되는 것을 제안합니다.
그리고 이러한 큰 기공은 반고체 변형 중에 도입된 팽창 변형에서 파생됩니다. 따라서 기공 형성의 명백한 무작위성은 반고체 네트워크의 이질적인 특성에 기인합니다. 쇼트 챔버에서 열 손실을 줄이면보다 균일 한 입자 구조를 촉진하여 최대 기공 크기가 1.32mm에서 0.37mm로 감소하고 최소 인장 연성이 6.8 %에서 9.4 %로 증가하는 것으로 나타났습니다.
Keywords
High pressure die casting (HPDC)Al-Si alloyMicrostructureComputational fluid dynamics (CFD)Mechanical Property
1. Introduction
High-pressure die casting (HPDC) is widely used in the manufacture of light alloy structures intended for use in automobiles and aeroplanes, due in part to its high dimensional accuracy and suitability for robotic automation. HPDC is characterised by the high-speed injection of molten metal into a sealed mould cavity, followed by solidification under an applied pressure of 30 ~100 MPa [1]. The process thus elicits an array of rich and complex phenomena including fluid turbulence, solidification, and semi-solid deformation. Combined, these phenomena make HPDC somewhat probabilistic in nature: the tensile ductility of die-castings is notoriously inconsistent [[2], [3], [4]]. This inconsistency leads to high scrap rates, and increased safety factors for component design. Although the tensile ductility of die-castings has been linked to various casting defects—porosity [[5], [6], [7], [8]], oxides [8,9], and sludge intermetallic particles [[9], [10], [11]] to name a few—the underlying cause of variability remains enigmatic.
Previous investigations into the reliability of die-castings have generally pursued one of three lines of inquiry. The first derives empirical correlations between the tensile ductility and various measures of microstructural uniformity (e.g. bulk porosity content [3,4,12,13], maximum pore size [[5], [6], [7]], grain size [[13], [14], [15]], eutectic fraction [3,4,10]). The second relates the scatter in tensile ductility to statistical variations in melt quality (e.g. chemical composition [11,16], gas content [8], number of inclusions in the melt [9]). The third considers the stochastic nature of fluid flow, and the subsequent encapsulation of air and oxides [[17], [18], [19], [20]]. Although porosity is a recurrent theme in these studies, its formation mechanism is widely disputed [4,9,13]. Tian et al. [9] relate the amount of porosity to the number of inclusions in the melt. Li et al. [13] observe a linear correlation between the volume fraction of porosity and the fraction of primary α-Al1 grains solidified in the shot chamber. Dong et al. [4] found that the use of vacuum can lead to fewer pores and improved tensile properties. However, these studies assume that porosity is the main source of scatter in tensile ductility. In light of such findings, it would be interesting to determine whether or not this assumption is valid.
Previously [21,22] we simulated the HPDC process using the finite element method (FEM) under the ProCAST (ESI Group) software platform; an optimum plunger speed profile was derived in Ref. [22] based on predictions from the model. Here, we perform HPDC experiments under both Baseline and Optimized conditions to identify the primary source of scatter in tensile ductility. Based on our findings, we explain the seemingly random nature of pore formation in the HPDC process.
![Fig. 1. Die geometry used to produce ASTM standard E8/E8M tensile specimens [24]. (a) Front view. (b) Side view of runner-orifice system. (c) Schematic of tensile specimens (all dimensions in mm).](https://castman.co.kr/wp-content/uploads/E8M-tensile-specimens-24.-a-Front-view.-b-Side-view-of-runner-orifice-system.-c-Schematic-of-tensile-specimens-all-dimensions-in-mm..png)
2.2. Casting parameters
Fig. 2 shows the plunger speed profiles considered in this work. Notable differences lie in the speeds attained at displacements of 50 mm and 375 mm (Baseline {0.2 ms−1, 0.3 ms−1} and Optimized {0.4 ms−1, 0.6 ms−1}, respectively). The Baseline profile was defined according to recommendations from the supplier of the HPDC machine (FRECH). Previously [21,22], we simulated the HPDC process using a FEM model developed under the ProCAST software platform. An optimal plunger speed profile (Fig. 2) was derived in Ref. [22] based on the amount and distribution of oxides, entrapped air, and shrinkage porosity predicted by the model. A fast shot speed of 3.6 ms−1 was used for both plunger speed profiles based on preliminary trials. A pressure of 32 MPa was selected for the intensification stage, corresponding to the maximum attainable pressure of the hydraulic actuator.
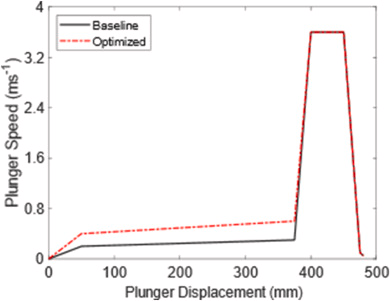
....
5. Conclusions
- Scatter in tensile ductility is related to the size of large pores and non-metallic inclusions, for specimens produced under the observed conditions. A power-law relationship is established between the tensile ductility and the size of the largest defect on the fracture surface, which is irrespective of defect type.
2. We propose that these non-metallic inclusions form during the pyrolysis of commercial plunger lubricants in the shot chamber. This hypothesis is based on the chemical constituents of the inclusions, and is substantiated by shot chamber filling tests.
3. Scatter in tensile ductility is greatly reduced under Optimized conditions, due to a decrease in the maximum pore size from 1.32 mm to 0.37 mm. Our findings suggest that these large pores derive from dilatational strains introduced during semi-solid deformation. The apparent randomness of pore formation is thus attributed to the heterogeneous nature of the semi-solid network. Indeed, a more uniform grain structure is produced under Optimized conditions, which is expected to result in a more homogeneous strain field, reducing scatter in pore size.
References
[1]X.P. Niu, K.K. Tong, B.H. Hu, I. PinwillCavity pressure sensor study of the gate freezing behaviour in aluminium high pressure die castingInt. J. Cast. Met. Res., 11 (1998), pp. 105-112, 10.1080/13640461.1998.11819264CrossRefView Record in ScopusGoogle Scholar
[2]Y. Zhang, J.B. Patel, J. Lazaro-Nebreda, Z. FanImproved defect control and mechanical property variation in high-pressure die casting of A380 alloy by high shear melt conditioningJ. Occup. Med., 70 (2018), pp. 2726-2730, 10.1007/s11837-018-3005-yCrossRefView Record in ScopusGoogle Scholar
[3]S. Ji, H. Yang, D. Watson, Z. FanWeibull analysis for the repeatability of die castings made by an Al-Mg-Si-Mn alloyLight Met. (2016), pp. 681-685, 10.1007/978-3-319-48251-4_114CrossRefView Record in ScopusGoogle Scholar
[4]X. Dong, X. Zhu, S. JiEffect of super vacuum assisted high pressure die casting on the repeatability of mechanical properties of Al-Si-Mg-Mn die-cast alloysJ. Mater. Process. Technol., 266 (2019), pp. 105-113, 10.1016/j.jmatprotec.2018.10.030ArticleDownload PDFView Record in ScopusGoogle Scholar
[5]J.P. Weiler, J.T. Wood, R.J. Klassen, E. Maire, R. Berkmortel, G. WangRelationship between internal porosity and fracture strength of die-cast magnesium AM60B alloyMater. Sci. Eng., A, 395 (2005), pp. 315-322, 10.1016/j.msea.2004.12.042ArticleDownload PDFView Record in ScopusGoogle Scholar
[6]J.P. Weiler, J.T. WoodModeling fracture properties in a die-cast AM60B magnesium alloy I—analytical failure modelMater. Sci. Eng., A, 527 (2009), pp. 25-31, 10.1016/j.msea.2009.08.060ArticleDownload PDFView Record in ScopusGoogle Scholar
[7]E. Lordan, J. Lazaro-Nebreda, Y. Zhang, K. Dou, P. Blake, Z. FanOn the relationship between internal porosity and the tensile ductility of aluminium alloy die-castingsMater. Sci. Eng., 778 (2020), p. 139107, 10.1016/j.msea.2020.139107ArticleDownload PDFView Record in ScopusGoogle Scholar
[8]E. Lordan, J. Lazaro-Nebreda, Y. Zhang, Z. FanEffective degassing for reduced variability in high-pressure die casting performanceJ. Occup. Med., 71 (2019), pp. 824-830, 10.1007/s11837-018-3186-4CrossRefView Record in ScopusGoogle Scholar
[9]C. Tian, J. Law, J. van der Touw, M. Murray, J.-Y. Yao, D. Graham, D. St JohnEffect of melt cleanliness on the formation of porosity defects in automotive aluminium high pressure die castingsJ. Mater. Process. Technol., 122 (2002), pp. 82-93, 10.1016/S0924-0136(01)01229-8ArticleDownload PDFView Record in ScopusGoogle Scholar
[10]G. Timelli, A. FabriziThe effects of microstructure heterogeneities and casting defects on the mechanical properties of high-pressure die-cast AlSi9Cu3(Fe) alloysMetall. Mater. Trans., 45 (2014), pp. 5486-5498, 10.1007/s11661-014-2515-7CrossRefView Record in ScopusGoogle Scholar
[11]S. Ferraro, G. TimelliInfluence of sludge particles on the tensile properties of die-cast secondary aluminum alloysMetall. Mater. Trans. B, 46 (2015), pp. 1022-1034, 10.1007/s11663-014-0260-3CrossRefView Record in ScopusGoogle Scholar
[12]H. Yang, S. Ji, D. Watson, Z. FanRepeatability of tensile properties in high pressure die-castings of an Al-Mg-Si-Mn alloyMet. Mater. Int., 21 (2015), pp. 936-943, 10.1007/s12540-015-5108-0CrossRefView Record in ScopusGoogle Scholar
[13]X. Li, S.M. Xiong, Z. GuoImproved mechanical properties in vacuum-assist high-pressure die casting of AZ91D alloyJ. Mater. Process. Technol., 231 (2016), pp. 1-7, 10.1016/j.jmatprotec.2015.12.005ArticleDownload PDFCrossRefView Record in ScopusGoogle Scholar
[14]H. Gjestland, S. Sannes, J. Svalestuen, H. WestengenOptimizing the magnesium die casting process to achieve reliability in automotive applicationsSAE Trans., 114 (2005), pp. 67-73https://www.jstor.org/stable/44718874?seq=1Google Scholar
[15]X. Li, S.M. Xiong, Z. GuoOn the porosity induced by externally solidified crystals in high-pressure die-cast of AM60B alloy and its effect on crack initiation and propagationMater. Sci. Eng., A, 633 (2015), pp. 35-41, 10.1016/j.msea.2015.02.078ArticleDownload PDFCrossRefView Record in ScopusGoogle Scholar
[16]S. Ji, W. Yang, F. Gao, D. Watson, Z. FanEffect of iron on the microstructure and mechanical property of Al–Mg–Si–Mn and Al–Mg–Si diecast alloysMater. Sci. Eng., A, 564 (2013), pp. 130-139, 10.1016/j.msea.2012.11.095ArticleDownload PDFView Record in ScopusGoogle Scholar
[17]K. Dou, E. Lordan, Y.J. Zhang, A. Jacot, Z.Y. FanNumerical simulation of fluid flow, solidification and defects in high pressure die casting (HPDC) processIOP Conf. Ser. Mater. Sci. Eng., 529 (2019), Article 012058, 10.1088/1757-899X/529/1/012058CrossRefView Record in ScopusGoogle Scholar
[18]M. Saeedipour, S. Schneiderbauer, S. Pirker, S. BozorgiA numerical and experimental study of flow behaviour in high pressure die castingMagnesium Technol (2014), pp. 185-190, 10.1007/978-3-319-48231-6_37View Record in ScopusGoogle Scholar
[19]D.R. Gunasegaram, M. Givord, R.G. O'Donnell, B.R. FinninImprovements engineered in UTS and elongation of aluminum alloy high pressure die castings through the alteration of runner geometry and plunger velocityMater. Sci. Eng., A, 559 (2013), pp. 276-286, 10.1016/j.msea.2012.08.098ArticleDownload PDFView Record in ScopusGoogle Scholar
[20]X. Li, W. Yu, J. Wang, S. XiongInfluence of melt flow in the gating system on microstructure and mechanical properties of high pressure die casting AZ91D magnesium alloyMater. Sci. Eng., A, 736 (2018), pp. 219-227, 10.1016/j.msea.2018.08.090ArticleDownload PDFView Record in ScopusGoogle Scholar
[21]K. Dou, E. Lordan, Y.J. Zhang, A. Jacot, Z.Y. FanA complete computer aided engineering (CAE) modelling and optimization of high pressure die casting (HPDC) processJ. Manuf. Process., 60 (2020), pp. 435-446, 10.1016/j.jmapro.2020.10.062ArticleDownload PDFView Record in ScopusGoogle Scholar
[22]K. Dou, E. Lordan, Y. Zhang, A. Jacot, Z. FanImprovement of Mechanical Properties for Aluminium Alloy in High Pressure Die Casting (HPDC) Process Combining Experimental and Modelling Approach(2020)manuscript submitted for publicationGoogle Scholar
[23]D.G. Eskin, I. Tzanakis, F. Wang, G.S.B. Lebon, T. Subroto, K. Pericleous, J. MiFundamental studies of ultrasonic melt processingUltrason. Sonochem., 52 (2019), pp. 455-467, 10.1016/j.ultsonch.2018.12.028ArticleDownload PDFView Record in ScopusGoogle Scholar
[24]ASTM Committee, Test methods for tension testing of metallic materials, ASTM international. http://www.astm.org/cgi-bin/resolver.cgi?E8E8M-16AE1 (accessed September 10, 2020).Google Scholar
[25]J. CampbellCastings(second ed.), Butterworth-Heinemann (2002)Google Scholar
[26]R.B. Bergmann, A. BillOn the origin of logarithmic-normal distributions: an analytical derivation, and its application to nucleation and growth processesJ. Cryst. Growth, 310 (2008), pp. 3135-3138, 10.1016/j.jcrysgro.2008.03.034ArticleDownload PDFView Record in ScopusGoogle Scholar
[27]S. Otarawanna, C.M. Gourlay, H.I. Laukli, A.K. DahleMicrostructure formation in AlSi4MgMn and AlMg5Si2Mn high-pressure die castingsMetall. Mater. Trans., 40 (2009), pp. 1645-1659, 10.1007/s11661-009-9841-1CrossRefView Record in ScopusGoogle Scholar
[28]S. Otarawanna, C.M. Gourlay, H.I. Laukli, A.K. DahleAgglomeration and bending of equiaxed crystals during solidification of hypoeutectic Al and Mg alloysActa Mater., 58 (2010), pp. 261-271, 10.1016/j.actamat.2009.09.002ArticleDownload PDFView Record in ScopusGoogle Scholar
[29]S. ColesAn Introduction to Statistical Modeling of Extreme ValuesSpringer (2001), 10.1007/978-1-4471-3675-0Google Scholar
[30]A. Borbély, H. Mughrabi, G. Eisenmeier, H.W. HöppelA finite element modelling study of strain localization in the vicinity of near-surface cavities as a cause of subsurface fatigue crack initiationInt. J. Fract., 115 (2002), pp. 227-232, 10.1023/A:1016350528652View Record in ScopusGoogle Scholar
[31]L. Wang, P. Turnley, G. SavageGas content in high pressure die castingsJ. Mater. Process. Technol., 211 (2011), pp. 1510-1515, 10.1016/j.jmatprotec.2011.03.024ArticleDownload PDFView Record in ScopusGoogle Scholar
[32]Tribo-chemie GmbH, The thermal reaction of different plunger lubricants and its influence on casting quality. https://tribochemie.de/images/media/downloads/EN/plungerlubricant.pdf (accessed August 20, 2020)..Google Scholar
[33]T. Mang, W. DreselLubricants and LubricationJohn Wiley & Sons (2007)Google Scholar
[34]ATC EuropeLubricant Additives: use and Benefits(2016)https://www.atc-europe.org/public/Document%20118%20-%20Lubricant%20Additives%20Use%20and%20Benefits.pdf, Accessed 20th Aug 2020Google Scholar
[35]K.M. Kareh, P.D. Lee, R.C. Atwood, T. Connolley, C.M. GourlayRevealing the micromechanisms behind semi-solid metal deformation with time-resolved X-ray tomographyNat. Commun., 5 (2014), p. 4464, 10.1038/ncomms5464View Record in ScopusGoogle Scholar
[36]K.M. Kareh, P.D. Lee, R.C. Atwood, T. Connolley, C.M. GourlayPore behaviour during semi-solid alloy compression: insights into defect creation under pressureScripta Mater., 89 (2014), pp. 73-76, 10.1016/j.scriptamat.2014.06.033ArticleDownload PDFView Record in ScopusGoogle Scholar
[37]C.M. Gourlay, A.K. DahleDilatant shear bands in solidifying metalsNature (Paris), 445 (2007), pp. 70-73, 10.1038/nature05426CrossRefView Record in ScopusGoogle Scholar
[38]T.C. Su, C. O'Sullivan, T. Nagira, H. Yasuda, C.M. GourlaySemi-solid deformation of Al-Cu alloys: a quantitative comparison between real-time imaging and coupled LBM-DEM simulationsActa Mater., 163 (2019), pp. 208-225, 10.1016/j.actamat.2018.10.006ArticleDownload PDFView Record in ScopusGoogle Scholar