This article introduces the paper "Materials for Automotive Lightweighting".
1. Overview:
- Title: Materials for Automotive Lightweighting
- Authors: Alan Taub, Emmanuel De Moor, Alan Luo, David K. Matlock, John G. Speer, and Uday Vaidya
- Publication Year: 2019
- Journal/Conference: Annual Review of Materials Research
- Keywords:
- advanced high-strength steel
- aluminum
- magnesium
- polymer composites
- lightweighting
- multimaterial joining
2. Research Background:
- Social/Academic Context of the Research Topic:
- Reducing vehicle weight is a major contributor to increased fuel economy.
- Baseline materials like low-carbon steel and cast iron are being replaced by materials with higher specific strength and stiffness.
- Key challenge is reducing the cost of manufacturing structures with new lightweight materials.
- Maximizing weight reduction requires optimized designs using multimaterials.
- Use of mixed materials presents challenges in joining and preventing galvanic corrosion.
- Limitations of Existing Research:
- Existing manufacturing processes for lighter-weight materials need to meet cost requirements for particular applications.
- Joining and preventing galvanic corrosion in mixed material structures are additional challenges.
- Necessity of Research:
- To review advances in material systems like advanced high-strength steels, aluminum, magnesium, and polymer composites for automotive lightweighting.
- To discuss manufacturing technologies that enable increased use of aluminum and magnesium.
- To explore improvements in material properties and cost reduction for wider adoption of lightweight materials.
3. Research Objectives and Research Questions:
- Research Objective:
- To review the current state-of-the-art in materials and manufacturing technologies for automotive lightweighting, focusing on advanced high-strength steels, aluminum, magnesium, and polymer composites.
- Core Research Questions:
- What are the recent advancements in ferrous alloys, specifically advanced high-strength steels and ductile cast iron, for automotive lightweighting?
- What are the manufacturing technologies enabling increased use of aluminum and magnesium in automotive structures, and what are the recent alloy developments?
- What are the current applications and advancements in polymer composites for automotive lightweighting, including material developments and processing technologies?
- What are the challenges and advancements in multimaterial joining for automotive lightweight structures?
- Research Hypothesis: (Not explicitly stated as a hypothesis in the paper, but implied)
- Advances in materials science, manufacturing processes, and design optimization are crucial for achieving significant automotive lightweighting and improving fuel economy while maintaining performance and safety, and cost-effectiveness.
4. Research Methodology:
- Research Design: Review paper summarizing existing literature and research findings in the field of automotive lightweighting materials and manufacturing.
- Data Collection Method: Literature review of published research articles, industry reports, and technical publications related to automotive materials, manufacturing, and lightweighting technologies.
- Analysis Method: Qualitative synthesis and summarization of information from the reviewed literature, focusing on identifying key trends, advancements, challenges, and future directions in the field.
- Research Scope and Subject: Focus on materials for body, chassis, and interior components of automobiles. Primarily reviews advanced high-strength steels, aluminum, magnesium, and polymer composites. Scope excludes powertrain electrification aspects beyond material considerations for lightweighting.
5. Main Research Findings:
- Core Research Findings:
- Advanced High-Strength Steels (AHSS) and Ductile Cast Iron:
- Development of third-generation AHSS with complex microstructures (martensite, bainite, ultrafine-grained ferrite, retained austenite) for improved strength and formability.
- Quenching and Partitioning (Q&P) and TRIP-aided bainitic ferrite (TBF) steels as novel processing routes for third-generation AHSS.
- Thin-wall Austempered Ductile Iron (ADI) castings offering high strength-to-density ratios and cost-effectiveness.
- Aluminum and Magnesium:
- Increased use of aluminum and magnesium driven by fuel economy demands and manufacturing innovations.
- Sheet forming technologies like warm forming to enhance formability of aluminum and magnesium alloys.
- High-vacuum die casting processes (SVDC) for aluminum and magnesium to produce components with minimal porosity and improved ductility.
- Alloy development for high-temperature magnesium alloys (e.g., AE44) using CALPHAD approach.
- Polymer Composites:
- Fiber-reinforced polymer composites as key enablers for lightweighting due to high strength-to-weight ratios and design flexibility.
- Various applications in body exterior, interior, safety, chassis, powertrain, fuel systems, and engine components.
- Advances in carbon fiber technologies and processing methods (HP-RTM, wet compression, IOM, prepreg stamping, extrusion-compression) for cost-effective composite manufacturing.
- Recycling technologies for polymer composites gaining importance for cost reduction and sustainability.
- Multimaterial Joining:
- Multimaterial joining becoming crucial for integrating different lightweight materials in automotive designs.
- Need for robust design tools, reliable test methods, and cost-effective joining techniques.
- Research focused on scaling up joining approaches, developing accelerated aging tests, and third-party data evaluation.
- Advanced High-Strength Steels (AHSS) and Ductile Cast Iron:
- Statistical/Qualitative Analysis Results:
- Weight Reduction Benefits: Light vehicles: "$4.50/kg" weight reduction value. Heavy trucks: "$5-11/kg dry van dedicated routes" and "$13-24/kg bulk carriers" weight reduction value (Table 1).
- Material Substitution Impact: Mass reduction and relative cost per part for various lightweight materials compared to mild steel/cast iron (Table 2). For example, Magnesium: "60-75%" mass reduction, "1.5 to 2.5" relative cost per part. Carbon fiber composites: "50-60%" mass reduction, "2 to 10+" relative cost per part.
- AHSS Elongation: Figure 5 shows property map of tensile strength and total elongation for conventional and AHSS grades. Third-generation AHSS aims for properties within specific bands in this map.
- Q&P Steel Stress-Strain Curves: Figure 6 and Figure 8 illustrate stress-strain curves for Q&P steels under different processing conditions, showing variations in tensile properties.
- Austenite Transformation in Medium-Mn Steel: Figure 10 shows the evolution of austenite transformation to martensite with strain and corresponding stress-strain curves for medium-Mn steel at different annealing temperatures.
- Fatigue Life and Inclusion Content: Figure 11 shows the relationship between inclusion content and fatigue stress/life in steels. Improved steelmaking practices led to a "two-order-of-magnitude increase in fatigue life" since 1980.
- Nodule Density in Ductile Iron: Figure 12 compares nodule density in thin-wall vs. thick-wall ductile iron castings.
- Carbon Fiber Composite Properties: Table 3 shows representative properties of textile carbon fiber (TCF) epoxy composites, e.g., Tensile strength: "548 MPa (79.48 ksi)", Tensile modulus: "84 GPa (12.18 Msi)".
- Load Bearing Capacity of Overmolded Composites: Figure 24 shows a "275% enhancement of load bearing and strain capacity" for overmolded PA6-C LFT compared to PA6-C LFT.
- Data Interpretation:
- Material substitution and optimized design are key strategies for automotive lightweighting.
- Advanced materials and manufacturing processes are continuously evolving to meet the demands for lighter, stronger, and more cost-effective automotive structures.
- Polymer composites and multimaterial designs are increasingly important for future lightweighting efforts.
- Figure Name List:
- Figure 1: Changes in adjusted fuel economy, weight, and horsepower for model years 1975–2016.
- Figure 2: (a) Incremental forming and cost-effectiveness at low volume production relative to traditional forming technologies. (b) Balance of part complexity and production volume for different forming processes.
- Figure 3: Mixed-material lightweight vehicle Mach-II body-in-white material distribution.
- Figure 4: US automotive metal market history and projection.
- Figure 5: A property map of tensile strength and total elongation combinations for various classes of conventional and AHSS grades.
- Figure 6: Engineering stress-strain curves of a 0.2 wt% C–1.5 wt% Mn–1.0 wt% Si-0.5 wt% Al steel austempered at varying temperatures ranging between 300°C and 500°C for 200 s.
- Figure 7: Schematic diagram showing the two-step quenching and partitioning heat treatment process starting with a fully austenitic microstructure.
- Figure 8: Engineering stress-strain curves obtained in x wt% C-1.5 wt% Mn–1.6 wt% Si steels with varying carbon contents from 0.2 to 0.4 wt% after quenching and partitioning processing.
- Figure 9: Electron back-scattered diffraction image quality map for 7 wt% Mn steel annealed at 620°C for 24 h to produce 40 vol% austenite.
- Figure 10: (a) Evolution of the fraction of austenite transformed to martensite with tensile deformation for different annealing temperatures. (b) Corresponding tensile stress-strain curves for 0.1 wt% C–7.1 wt% Mn–0.1 wt% Si samples.
- Figure 11: Effects of inclusion contents on (a) allowable fatigue stress and (b) bearing fatigue life.
- Figure 12: Light optical micrographs of unetched specimens that show the influence of section thickness on nodule count.
- Figure 13: Timeline of key aluminum and magnesium automobile applications.
- Figure 14: Hydroformed aluminum rail for the Corvette Z06 shown immediately after forming.
- Figure 15: (a) Calculated isopleth for Al-8 wt% Si-0.35 wt% Mg-0.6 wt% Fe-x% Mn. (b) The effect of Fe and Mn content on the formation of the β-Al5FeSi intermetallic phase in the Al-Si-Mg-Fe-Mn alloy system.
- Figure 16: Achieving thin-wall aluminum and magnesium die casting through alloy optimization and process simulation.
- Figure 17: (a) Calculated Mg-Al phase diagram. (b) Calculated Mg-Al-Ce liquidus projection and solidification paths of experimental Mg-Al-Ce alloys.
- Figure 18: Comprehensive opportunities for polymers and polymer composites with associated manufacturing processes for lightweighting in vehicles.
- Figure 19: Historical average material usage of various plastics and composites in US and Canadian light vehicles.
- Figure 20: Average plastics and polymer composites use in US/Canadian light vehicles.
- Figure 21: Wide-tow textile-grade carbon fiber produced at the Carbon Fiber Technology Facility at Oak Ridge National Laboratory.
- Figure 22: (a) High-pressure resin transfer molding (RTM). (b) Wet compression processing.
- Figure 23: Overmolding steps of automotive components.
- Figure 24: Comparison of carbon PA6 versus overmolded carbon PA6.
- Figure 25: Material stages in the long-fiber thermoplastic-extrusion-compression molding process.
- Figure 26: (a) Molded sheet molding compound (SMC) seat backrest at a cycle time of 45 s. (b) SMC molded plaque and overmolded SMC plaque.
- Figure 27: Example of a recycled carbon fiber polyamide 6 (PA6) mat that can be stamped/compression molded to near net shape.
- Figure 28: Hexagonal geometry section of a Strati car produced on the BAAM (big-area additive manufacturing) printer at the Manufacturing Demonstration Facility at Oak Ridge National Laboratory.
- Figure 29: (a) Modeling and simulation hub at IACMI Purdue University. (b) Model of local thermal stresses developed in layer-by-layer extrusion deposition of acrylonitrile butadiene styrene material.
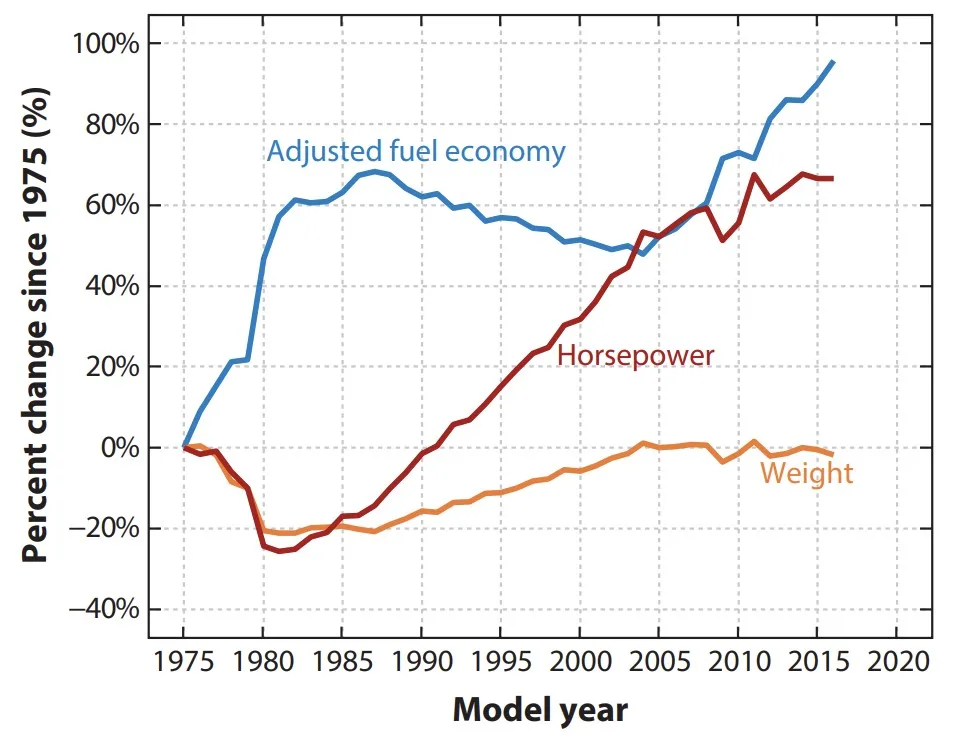
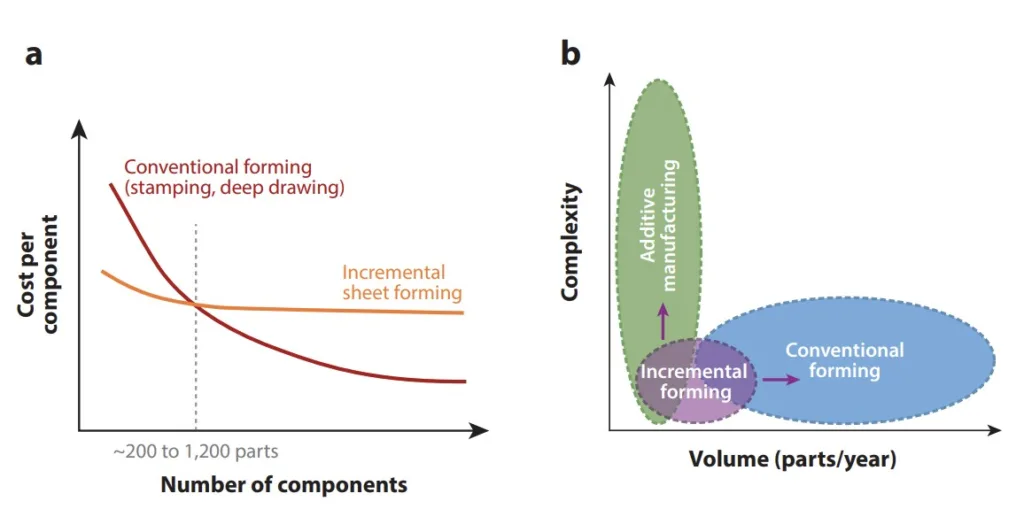
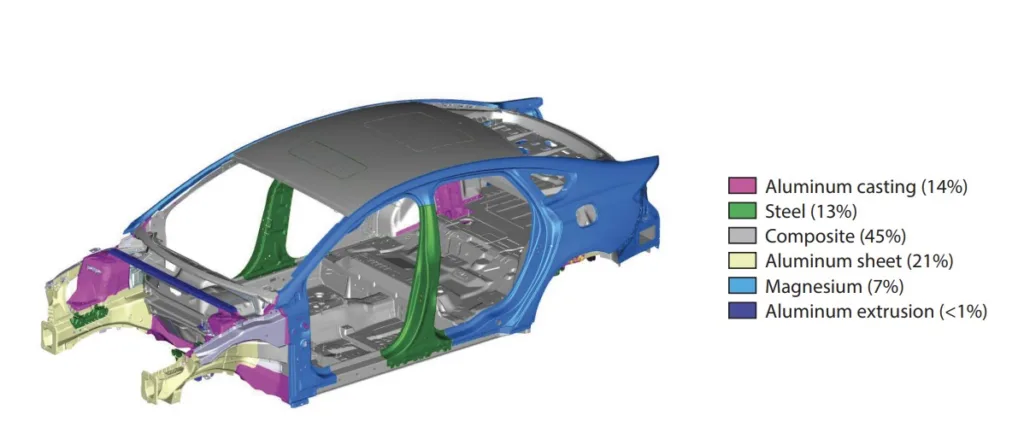
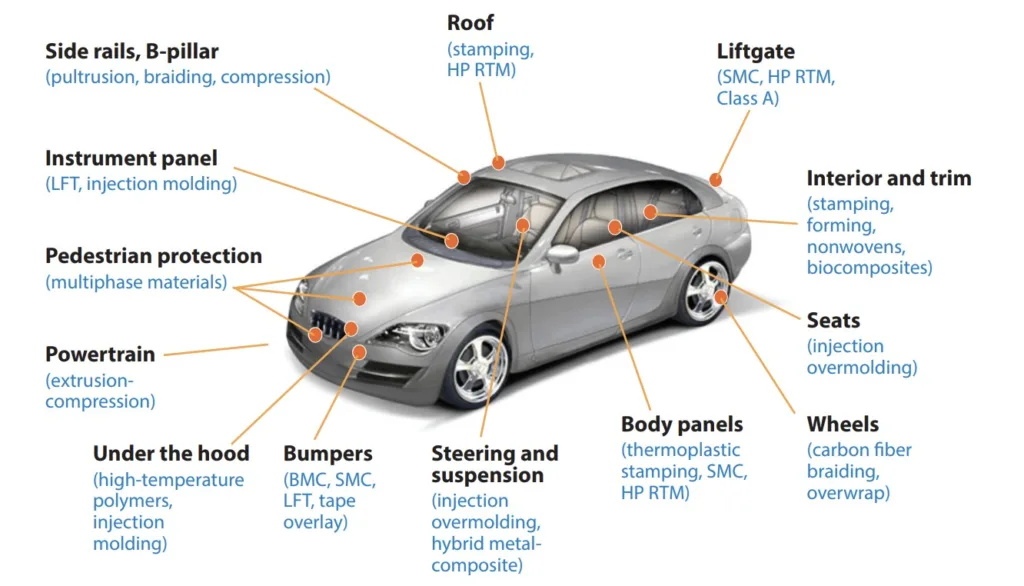
6. Conclusion and Discussion:
- Summary of Main Results:
- The automotive industry is actively transitioning to lightweighting by adopting advanced materials like AHSS, aluminum, magnesium, and polymer composites.
- Optimized designs and advanced manufacturing technologies are crucial for cost-effective implementation of lightweight materials.
- Significant progress has been made in developing new alloys and processing routes for each material category to enhance performance and reduce weight.
- Multimaterial designs and joining technologies are essential for maximizing weight reduction and achieving desired performance characteristics.
- Academic Significance of Research:
- Provides a comprehensive overview of the latest advancements in materials and manufacturing for automotive lightweighting.
- Highlights the importance of integrated computational materials engineering (ICME) for design optimization and material selection.
- Emphasizes the shift towards multimaterial designs and the associated challenges and opportunities.
- Practical Implications:
- Offers valuable insights for automotive engineers and material scientists in selecting and implementing lightweight materials and manufacturing processes.
- Identifies key research areas and technological advancements needed for further progress in automotive lightweighting.
- Underscores the importance of cost-effectiveness and recyclability in the adoption of new lightweighting technologies.
- Limitations of Research:
- The review primarily focuses on material aspects and manufacturing technologies, with limited discussion on broader system-level implications like full lifecycle analysis or detailed cost modeling.
- Scope is limited to body, chassis, and interior components, excluding deeper analysis of powertrain electrification impacts on lightweighting beyond material considerations.
7. Future Follow-up Research:
- Directions for Future Research:
- Further development of low-cost carbon fibers and efficient composite manufacturing processes.
- Advancements in multimaterial joining technologies and galvanic corrosion prevention methods.
- Development and refinement of ICME tools for accelerated material design and process optimization.
- Research into recycling technologies for composite materials to enhance sustainability.
- Exploration of novel alloy designs and processing techniques for AHSS, aluminum, and magnesium with improved properties and reduced cost.
- Areas Requiring Further Exploration:
- Techno-economic analysis of different lightweighting strategies and material choices.
- Validation of composite crash simulation models and development of robust design guidelines.
- Development of standardized testing methods and databases for multimaterial joints.
- Integration of lightweighting strategies with vehicle electrification and autonomous driving technologies.
8. References:
- US Natl. Res. Counc. 2003. Materials Research to Meet 21st Century Defense Needs.Washington, DC: Natl. Acad. Press
- Roeth M. 2015. Confidence report: lightweighting. Rep., North American Council for Freight Efficiency.
https://nacfe.org/technology/lightweighting-2/. Accessed Nov. 20, 2017 - Taub AI, Krajewski PE, Luo AA, Owens JN. 2007. The evolution of technology for materials processing
over the last 50 years: the automotive example. JOM 59(2):48–57 - Schutte C, Joost WJ. 2014. Lightweight materials for cars and trucks. https://www.energy.gov/eere/
vehicles/lightweight-materials-cars-and-trucks - Joost W. 2015.Energy, materials and vehicle weight reduction. Rep., US Dep. Energy. http://www.nist.gov/
mml/acmd/structural_materials/upload/Joost-W-DOE-VTP-NIST-ASP-AHSS-WorkshopR03.pdf - Picker L. 2017. Vehicle weight and automotive fatalities. Digest, NBER. http://www.nber.org/digest/
nov11/w17170.html. Accessed Dec. 3, 2017 - Plumer B. 2014. Cars in the US are more fuel-efficient than ever. Here are 5 reasons why. Vox,
Sept. 4. https://www.vox.com/2014/9/4/6107203/cars-in-the-us-are-more-fuel-efficient-thanever-here-are-5-reasons. Accessed Dec. 3, 2017 - US Envir. Prot. Agency (EPA). 2015. Light-duty automotive technology, carbon dioxide emissions, and fuel economy trends: 1975 through 2015. Rep., US EPA
- Baron JS, Modi S. 2016. Assessing the fleet-wide material technology and costs to lightweight vehicles. Rep.,
Cent. Automot. Res. - Isenstadt A, German J, Bubna P, Wiseman M, Venkatakrishnan U, et al. 2016. Lightweighting technology development and trends in U.S. passenger vehicles. Work. Pap., Int. Counc. Clean Transp.
- US EPA. 2016. Light-duty vehicle CO2 and fuel economy trends. Rep. EPA-420-S-16-001, US EPA
- Bullis K. 2013. Automakers shed the pounds to meet fuel efficiency standards. MIT Technol. Rev., Feb. 20
- Kunkel GA, Hovanski Y. 2016. From the lab to your driveway: aluminum tailor-welded blanks. Weld. J.
95(8):36–39 - Joost WJ, Krajewski PE. 2017. Towards magnesium alloys for high-volume automotive applications. Scr. Mater. 128:107–12
- Winters J. 2014. Light vehicles’ lightweight future. Mech. Eng. CIME, Aug. 1. Accessed Nov. 28, 2017
- Hartfield-Wünsch SE, Hall JN. 2012. Manufacturing challenges for aluminum sheet in the automotive
industry. In ICAA13, ed. H Weiland, AD Rollett, WA Cassada, pp. 885–90. Cham, Switz.: Springer - Xia L. 2016. Multiscale Structural Topology Optimization. London: Elsevier
- Fiedler K, Rolfe BF, De Souza T. 2017. Integrated shape and topology optimization: applications in
automotive design and manufacturing. SAE Int. J. Mater. Manuf. 10(3):385–94 - Keough JR, Hayrynen KL. 2000. Automotive applications of austempered ductile iron (ADI): a critical
review. SAE Trans. 109:344–54 - Horstemeyer MF. 2012. Integrated Computational Materials Engineering (ICME) for Metals: Using Multiscale Modeling to Invigorate Engineering Design with Science. Hoboken, NJ: Wiley
- Pollock DGB, Tresa M, Allison JE. 2008. Integrated Computational Materials Engineering: A Transformational Discipline for Improved Competitiveness and National Security. Washington, DC: Natl. Acad. Press
- Allison J, Li M, Wolverton C, Su XM. 2006. Virtual aluminum castings: an industrial application of
ICME. JOM 58(11):28–35 - Sames WJ, List FA, Pannala S, Dehoff RR, Babu SS. 2016. The metallurgy and processing science of
metal additive manufacturing. Int. Mater. Rev. 61(5):315–60 - Daehn G. 2017. Metamorphic manufacturing. Abstract, LIFT. https://lift.technology/pillar/novelagile-processing/. Accessed Nov. 30, 2017
- Allwood JM, Utsunomiya H. 2006. A survey of flexible forming processes in Japan. Int. J. Mach. Tools
Manuf. 46(15):1939–60 - Allwood J, Houghton N, Jackson K. 2005. The design of an incremental sheet forming machine. Adv.
Mater. Res. 6–8:471–78 - Cao J, Huang Y, Reddy NV, Malhotra R, Wang Y. 2008. Incremental sheet metal forming: advances
and challenges. In Proceedings of International Conference on Technology of Plasticity (ICTP 2008). Gyeongju,
Korea: Korean Soc. Technol. Plastic. - Taub AI, Babu SS. 2018. Opportunities and challenges for introducing new lightweight metals in transportation. Int. J. Powder Metall. 54(2):27–33
- Taub AI, Luo AA. 2015. Advanced lightweight materials and manufacturing processes for automotive
applications. MRS Bull. 40(12):1045–54 - Skszek T, Conklin J, Zaluzec M,Wagner D. 2014. Multi-material lightweight vehicles: Mach-II design. Rep. for US Dep. Energy. https://energy.gov/sites/prod/files/2014/07/f17/lm088_skszek_2014_o.pdf.
Accessed Dec. 1, 2017 - Skszek T. 2015. Demonstration project for a multi-material lightweight prototype vehicle as part of the clean energy dialogue with Canada. Final Rep. for US Dep. Energy (award DE-EE0005574)
- Henriksson F. 2016. An outlook on multi material body solutions in the automotive industry: possibilities and
manufacturing challenges. Tech. Pap. 2016-01-1332, SAE - US Dep. Energy. 2010. 2010 annual progress report: lightweight material. Rep., US Dep.
Energy. https://www.energy.gov/sites/prod/files/2014/03/f8/2010_lightweighting_materials.pdf.
Accessed Sept. 1, 2015 - US EPA. 2012. Light-duty vehicle mass reduction and cost analysis—midsize crossover utility vehicle. Rep. EPA-420-R-12-026, US EPA. https://nepis.epa.gov/Exe/ZyPDF.cgi/P100EWVL.PDF?Dockey=
P100EWVL.PDF - Gehm R. 2016. Multi-material structures move mpg upward. Automot. Eng. 2016(3):18–21
- Singh H. 2012. Mass reduction for light-duty vehicles for model years 2017–2025. Rep. DOT HS 811 666,US Dep. Transp.
- US EPA. 2015. Mass reduction and cost analysis: light duty pickup model years 2020–2025. Rep. EPA-420-R15-006, US EPA
- Vasalash GS. 2017. Light vehicles and how they got that way. Automotive Design and Production, Oct. 11.
https://www.adandp.media/articles/light-vehicles-and-how-they-got-that-way - Monaghan M. 2012. Light and mighty. Automot. Eng. 2012(7):20–24
- Steven A. 2015. Mixing metals. Automot. Eng. 2015:27–29
- Wagner DA, Zaluzec MJ. 2015. Mixed materials drive lightweight vehicle design. Adv. Mater. Process.
2015(3):18–23 - Meschut G, Janzen V, Olfermann T. 2014. Innovative and highly productive joining technologies for
multi-material lightweight car body structures. J. Mater. Eng. Perform. 23(5):1515–23 - Ghosh D, Pancholi L, Sathaye A. 2014. Forming a strong bond. Automot. Eng. 2014:24–29
- Gould JE. 2012. Joining aluminum sheet in the automotive industry—a 30 year history. Weld. J. 91:23–34
- WorldAutoSteel. 2017. Advanced high-strength steels application guidelines version 6.0. https://www.
worldautosteel.org/projects/advanced-high-strength-steel-application-guidelines/. Accessed
Oct. 2018 - De Moor E, Gibbs PJ, Speer JG, Matlock DK, Schroth JG. 2010. Strategies for third-generation advanced high-strength steel development. AIST Trans. 7(3):133–44
- Matlock DK, Speer JG. 2009. Third generation of AHSS: microstructure design concepts. In Microstructure and Texture in Steels and Other Materials, ed. A Haldar, S Suwas, D Bhattacharjee, pp. 185–205. New York: Springer
- Matlock DK, Speer JG. 2006. Design considerations for the next generation of advanced high strength steels. In Proceedings of the Third International Conference on Advanced Structural Steels, ed. HC Lee, pp. 774–81. Seoul, Korea: Korean Institute of Metals and Materials
- Olson GB. 1984. Transformation plasticity and the stability of plastic flow. In Deformation, Processing and Structure, ed. G Krauss, pp. 391–424. Materials Park, OH: ASM
- Matlock DK, Speer JG, De Moor E, Gibbs PJ. 2011. TRIP steels—historical perspectives and recent
developments. In Proceedings of the 1st International Conference on High Manganese Steels, HMnS2011.
Seoul, Korea: Yonsei Univ. Press - De Cooman BC. 2004. Structure-properties relationship in TRIP steels containing carbide-free bainite.
Curr. Opin. Solid State Mater. Sci. 8(3–4):285–303 - Sugimoto K, Murata M, Song SM. 2010. Formability of A1-Nb bearing ultra high-strength TRIP-aided
sheet steels with bainite ferrite and/or martensite matrix. ISIJ Int. 50(1):162–68 - Rana R, De Moor E, Speer JG, Matlock DK. 2018. On the importance of adiabatic heating on deformation behavior of medium-manganese sheet steels. JOM 70(5):706–13
- Lee S, De Cooman BC. 2014. Tensile behavior of intercritically annealed 10 pct Mn multi-phase steel.
Metall. Mater. Trans. A 45(2):709–16 - Merwin MJ. 2007. Low-carbon manganese TRIP steels. Mater. Sci. Forum 539–543:4327–32
- Merwin MJ. 2007. Hot- and cold-rolled low-carbon manganese TRIPS steels. Tech. Pap. 2007-01-0336, SAE
- Bhadeshia HKDH. 2010. Nanostructured bainite. Proc. R. Soc. A 466(2113):3–18
- Speer JG, De Moor E, Findley KO, Matlock DK, De Cooman BC, Edmonds DV. 2011. Analysis of
microstructure evolution in quenching and partitioning automotive sheet steel. Metall. Mater. Trans. A 42(12):3591–601 - Wang L, Speer JG. 2013. Quenching and partitioning steel heat treatment. In ASM Handbook, Volume 4A: Steel Heat Treating Fundamentals and Processes, ed. GE Dossett, J Totten, pp. 317–26. Materials Park, OH:ASM Int.
- Sugimoto K, Iida T, Sakaguchi J, Kashima T. 2000. Retained austenite characteristics and tensile properties in a TRIP type bainitic sheet steel. ISIJ Int. 40(9):902–8
- Sugimoto K, Tsunezawa M, Hojo T, Ikeda S. 2004. Ductility of 0.1-0.6C-1.5Si-1.5Mn ultra highstrength TRIP-aided sheet steels with bainitic ferrite matrix. ISIJ Int. 44(9):1608–14
- Speer JG, Matlock DK, De Cooman BC, Schroth JG. 2003. Carbon partitioning into austenite after
martensite transformation. Acta Mater. 51(9):2611–22 - Matlock DK, Bräutigam VE, Speer JG. 2003. Application of the quenching and partitioning (Q&P)
process to a medium-carbon, high-Si microalloyed bar steel. Mater. Sci. Forum 426–432(1):1089–94 - Pierce DT, Coughlin DR, Williamson DL, Clarke KD, Clarke AJ, et al. 2015. Characterization of transition carbides in quench and partitioned steel microstructures by Mössbauer spectroscopy and complementary techniques. Acta Mater. 90:417–30
- Speer JG, Striecher AM, Matlock DK, Rizzo F, Krauss G. 2003. Quenching and partitioning a fundamentally new process to create high strength TRIP sheet microstructures. In Austenite Deformation and
Decomposition, ed. EB Damm, MJ Merwin, pp. 502–22. Warrendale, PA: ISS/TMS - Kahkonen MJ, De Moor E, Speer JG, Thomas GA. 2015. Carbon and manganese effects on quenching
and partitioning response of CMnSi-steels. SAE Int. J. Mater. Manuf. 8(2):419–24 - Wang L, Zhong Y, Feng W, Jin X, Speer JG. 2013. Industrial application of Q&P sheet steels. In Proceedings of the International Symposium on New Developments in Advanced High-Strength Steels, ed. E De Moor, HJ Jun, JG Speer, MJ Merwin, pp. 141–51. Warrendale, PA: AIST
- Gibbs PJ, De Moor E, Merwin MJ, Clausen N, Speer JG, Matlock DK. 2011. Austenite stability
effects on tensile behavior of manganese-enriched-austenite transformation-induced plasticity steel.
Metall. Mater. Trans. A 42(12):3691–702 - De Moor E, Matlock DK, Speer JG, Merwin MJ. 2011. Austenite stabilization through manganese enrichment. Scr. Mater. 64:185–88
- Zhang Y, Wang L, Findley KO, Speer JG. 2017. Influence of temperature and grain size on austenite
stability in medium manganese steels. Metall. Mater. Trans. A 48:2140–49 - Rana R, Lahaye C, Ray RK. 2014. Overview of lightweight ferrous materials: strategies and promises.
JOM 66(9):1734–46 - Ghanbari ZN, Speer JG. 2016. Elevated- and room-temperature mechanical behaviour of Zn-coated
steel sheet for hot stamping. AST Trans. 13(4):170–77 - Matlock DK, Speer JG. 2009. Microalloying concepts and application in long products. Mater. Sci. Technol. 25:1118–25
- Thompson RE, Matlock DK, Speer JG. 2007. The fatigue performance of high temperature vacuum
carburized Nb modified 8620 steel. SAE Trans. J. Mater. Manuf. 116(5):392–407 - Darragh CV. 2002. Engineered gear steels: a review. Gear Technol. Nov.–Dec.:33–40
- Gynther D. 2018. UltrapremiumTM and endurance steels. Presented at Great Designs in Steel, Livonia, MI. https://www.autosteel.org/-/media/files/autosteel/great-designs-in-steel/gdis-2018/track2- - -gynther- - -timkensteel.ashx. Accessed July 2018
- Findley KO, Cryderman RL, Nissan AB, Matlock DK. 2013. The effects of inclusions on fatigue performance of steel alloys. AIST Trans. 10(6):234–44
- Jhaveri K, Lewis GM, Sullivan JL, Keoleian GA. 2018. Life cycle assessment of thin-wall ductile cast
iron for automotive lightweighting applications. Sustain. Mater. Technol. 15:1–8 - Labrecque C, Gagné M, Javaid A, Sahoo M. 2003. Production and properties of thin-wall ductile iron
castings. Int. J. Cast Met. Res. 16:313–17 - Borrajo JM, Martínez RA, Boeri RE, Sikora JA. 2002. Shape and count of free graphite particles in thin
wall ductile iron castings. ISIJ Int. 42(3):257–63 - Fras E, Górny M, Lopez H. 2014. Thin wall ductile iron castings as substitutes for aluminum alloy ´
castings. Arch. Metall. Mater. 59(2):459–65 - Stefanescu DM, Dix LP, Ruxanda RE, Corbitt-Coburn C, Piwonka TS. 2002. Tensile properties of
thin-wall ductile iron. AFS Trans. 2(178):1149–61 - Górny M, Tyrała E. 2013. Effect of cooling rate on microstructure and mechanical properties of thinwalled ductile iron castings. J. Mater. Eng. Perform. 22(1):300–5
- Krajewski P, Sachdev A, Luo A, Carsley J, Schroth J. 2009. Automotive aluminum and magnesium:
innovation and opportunities. Light Met. Age 67(5):6–13 - Healey JR. 2014. 2015 Ford F-150 makes radical jump to aluminum body. USA Today, Jan. 13. https://
www.usatoday.com/story/money/cars/2014/01/13/redesigned-2015-ford-f-series-pickup-f150-aluminum/4421041/ - Ducker Worldwide. 2017.Aluminum content in North American light vehicles 2016 to 2028: summary report. Rep. for DriveAluminum
- Krajewski PE, Schroth JG. 2007. Overview of quick plastic forming technology. Mater. Sci. Forum 3:551–52
- Carter JT, Krajewski PE, Verma R. 2008. The hot blow forming of AZ31 Mg sheet: formability assessment and application development. JOM 60:77
- Shehata F, Painter MJ, Pearce R. 1978. Warm forming of aluminium/magnesium alloy sheet. J. Mech.
Work. Technol. 2:279–90 - Ayres RA. 1977. Enhanced ductility in an aluminum–4 Pct magnesium alloy at elevated temperature.
Metall. Trans. A 8:487–92- Warmed-up aluminum could beat steel to the draw. Mater. Eng. 88:52–54
- Luo AK, Sachdev AA. 2007. Development of light metals automotive structural subsystems. In Proceedings of the Light Metals Technology Conference. Ottawa, Can.: Nat. Resour. Can.
- Luo AA, Fu PH, Yu YD, Jiang HY, Peng LM, et al. 2008. Vacuum-assisted high pressure die casting of
AZ91 magnesium alloy. North Am. Die Cast. Assoc. Trans. 2008:T08–83 - Brown Z, Szymanowski B, Musser M, Saha D, Seaver S. 2009. Development of super-vacuum die casting
process for magnesium alloys. North Am. Die Cast. Assoc. Trans. - Brown Z, Szymanowski B, Musser M, Saha D, Seaver S. 2007. Manufacturing of thin wall structural automotive components through high vacuum die casting technology. Presented at International Die Casting
Congress and Exposition, Houston, TX, May 15–18 - Casarotto F, Franke AJ, Franke R. 2012.High-pressure die cast (HPDC) aluminum alloys for automotive
applications. In Advanced Materials in Automotive Engineering, ed. J Rowe, pp. 109–49. Sawston, UK:
Woodhead - Apelian D. 2009. Aluminum Cast Alloys: Enabling Tools for Improved Performance. Wheeling, IL: N. Am.Die Cast. Assoc.
- Taylor JA. 2012. Iron-containing intermetallic phases in Al-Si based casting alloys. Proc. Mater. Sci. 1:19–33
- Dinnis CM, Taylor JA, Dahle AK. 2006. Interactions between iron, manganese, and the Al-Si eutectic
in hypoeutectic Al-Si alloys. Metall. Mater. Trans. A 37:3283–91 - Ceschini L, Boromei I, Morri A, Seifeddine S, Svensson IJ. 2009. Microstructure, tensile and fatigue
properties of the Al–10% Si–2% Cu alloy with different Fe and Mn content cast under controlled conditions. J. Mater. Proc. Technol. 209:5669–79 - Cinkilic E, Sun W, Klarner AD, Luo AA. 2015. Use of CALPHAD modeling in controlling microstructure of cast aluminum alloys. Pap. 15-044, Am. Foundry Soc.
- Klarner AD, et al. 2017. A new fluidity die for castability evaluation of high pressure die cast alloys.Trans.
North Am. Die Cast. Assoc. T17–101 - Luo AA. 2013. Application of computational thermodynamics and CALPHAD in magnesium alloy development. In Proc. 2nd World Congr. Integr. Comput. Mater. Eng., ed. M Li, C Campbell, K Thornton, E Holm, P Gumbsch, pp. 3–8. Warrendale, PA: TMS
- Am. Chem. Counc. 2018. Plastics and polymer composites in light vehicles. Rep., Am. Chem. Counc.
- Institute for Advanced Composites Manufacturing Innovation (IACMI). 2017. Phase two roadmap. Feb. http://www.iacmi.org
- Vaidya U. 2017. Advanced composite materials and manufacturing in vehicles, wind and compressed gas storage. Text. World, Mar. 21
- Cedric B. 2016. New developments for mass production of epoxy automotive composites. Presented at Global Automotive Lightweight Materials Conference, Detroit. Accessed Aug. 2018
- Gardiner G. 2015. HP-RTM on the rise. Compos. World, Apr. 14
- Gardiner G. 2016. Wet compression molding. Compos. World, Jan. 2
- Rocky Mt. Inst. 2013. Kickstarting the widespread adoption of automotive carbon fiber composites: key findings and next steps. Rep., Rocky Mt. Inst.
- Thattaiparthasarathy K, Pillay S, Bansal D, Ning H, Vaidya U. 2013. Processing and characterization
of continuous fibre tapes co-moulded with long fibre reinforced thermoplastics. Polym. Polym. Compos. 21(8):483–94 - Emerson D, Grauer D, Hang B, Reif M, Henning F, et al. 2012. Using unidirectional glass tapes to improve impact performance of thermoplastic composites in automotive applications. Presented at Soc. Plast. Eng.
Automot. Compos. Conf. Exhib., Troy, MI, Sept. 11–13 - LayStitch Technology. 2018. Print technology. http://www.laystitch.com/Technology.html. Accessed
Aug. 2018 - Behrens BA, Raatz A, Hubner S, Bonk C, Bohne F, et al. 2017. Automated stamp forming of continuous
fiber reinforced thermoplastics for complex shell geometries. Proc. CIRP 66:113–18 - Vaidya UK. 2010. Composites for Automotive, Truck and Mass Transit. Lancaster, PA: DEStech
- Thattaiparthasarathy KB. 2008. Process simulation, design and manufacturing of a long fiber thermoplastic composite for mass transit application. Composites A Appl. Sci. Manuf. 39(9):1512–21
- Thomason JL, Vlug MA. 1996. Influence of fiber length and concentration on the properties of glass
fibre–reinforced polypropylene. 1. Tensile and flexural modulus.Composites A Appl. Sci.Manuf. 27(6):477–84 - IDI Compos. 2018. Structural thermoset composites. http://www.idicomposites.com/technology-stc.
php - Cabrera-Rios M, Castro JM. 2006. An economical way of using carbon fibers in sheet molding compound
compression molding for automotive applications. Polym. Compos. 27(6):718–22 - Carberry W. 2008. Airplane recycling efforts benefit Boeing operators. AERO, Quart. 4. http://www.
boeing.com/commercial/aeromagazine/articles/qtr_4_08/pdfs/AERO_Q408_article02.pdf - IACMI. 2016. Pioneering partnerships announced for composite recycling. News Release, IACMI. http://iacmi.org/2016/07/01/pioneering-partnerships-announced-composite-recycling/. Accessed Aug. 1
- Janney M, Ledger J, Vaidya U. 2012. Long fiber thermoplastic composites from recycled carbon fiber. Presented at ISTC, 44th, Charleston, SC, Oct. 22–25
- Janney M, Vaidya U, Sutton R, Ning H. 2014.Re-grind study of PPS-based long fiber thermoplastic composites. Presented at SAMPE, Seattle
- Okine RK, Edison DH, Little NK. 1990. Properties and formability of an aligned discontinuous fiber
thermoplastic composite sheet. J. Reinf. Plast. Compos. 9(1):70–90 - Sloan J, ed. 2016. Composites recycling becomes a necessity. Compos. World, May 16. https://www.
compositesworld.com/articles/composites-recycling-becomes-a-necessity - Blackman B, Kinloch A, Watts J. 1994. The plasma treatment of thermoplastic fibre composites for
adhesive bonding. Composites 25(5):332–41 - Brosius D, Armstrong K. 2017. IACMI baseline cost and energy metrics. Presentation, Mar.
- Das S, Armstrong K. 2018. FRPC energy use estimation tool. https://ornlenergyestimatortools.
shinyapps.io/frpc-energy-estimator2/ - USDRIVE. 2015. Materials technical team roadmap. Rep. https://www.energy.gov/…/MTT%
20Roadmap%20UPDATE%20Apprvd%2003-11-1 - Baldan A. 2004. Adhesively-bonded joints and repairs in metallic alloys, polymers and composite materials: adhesives, adhesion theories and surface pretreatment. J. Mater. Sci. 39(1):1–49
9. Copyright:
This material is based on the paper by [Alan Taub et al.] titled: [Materials for Automotive Lightweighting].
Paper Source: [https://doi.org/10.1146/annurev-matsci-070218-010134]
This material is a summary based on the above paper and is for informational purposes only. Unauthorized commercial use is prohibited.
Copyright © 2025 CASTMAN. All rights reserved.