Naveen Singhal
Research Scholar
Dept of Mechanical Engineering Arni University-H.P.
Dr. Sangeeth Gupta
Professor
Arni University-H.P
Dr.Krishnamachary P C
Professor & Principal
J.B.Institute of Engineering & Technology-Hyderabad.
Abstract
In order to provide ecological balance, new technologies are being developed to reduce fuel consumption. Within these new technologies, usage of light alloys such as aluminum and magnesium has gained great importance in the automotive applications. The advantages of aluminum alloys in terms of light weight, recycling, machinability and corrosion resistance led to increase application area of these alloys. Due to these characteristics of aluminum alloys, fuel-saving light-weight material selection plays an important role for automotive parts. Aluminum applications increase not only in automotive, but also in aerospace, space shuttle, marine, and defense applications. According to the production methods, aluminum alloys are generally classified as casting, sheet, forging and extrusion. Aluminum die casting alloys are generally used the production of suspension systems, engines and gears parts. However, with the developing aluminum casting technologies, the aluminum die casting method makes it possible to manufacture multiple body parts in one piece. It is predicted that number of aluminum die casting parts will increase, especially in electric vehicles. In this study, the importance of the use of aluminum die casting alloys in the automotive industry is emphasized. Research and trends so far of the development of aluminum die casting alloys are also summarized. Keywords: Light weighting, Aluminum casting alloys, Fuel consumption.
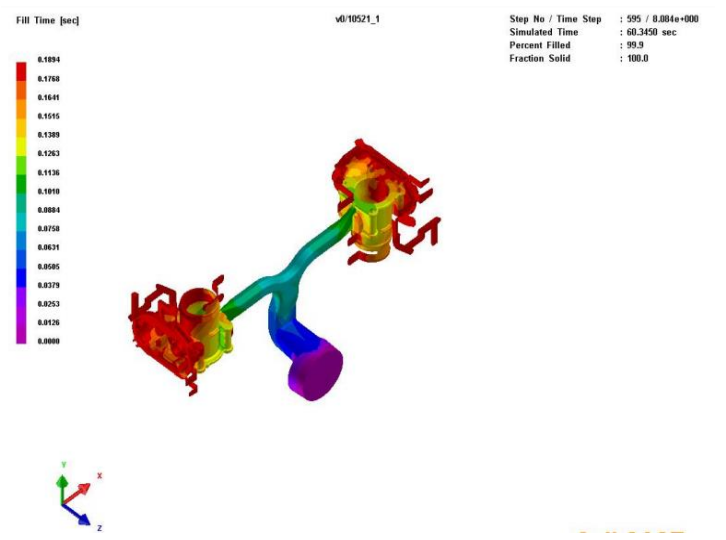
Reference
- Fiorese, E.; Richiedei, D.; Bonollo, F. Improved metamodels for the optimization
of high-pressure die casting process.
Metall. Ital. 2016, 108, 21–24. - G.F.Mi, C.Y.Li and K.F.Wang. Numerical Simulation and Application of Low
Pressure Die-casting Aluminum Alloy Wheel. Hot Working Technology 2013,
Vol.42, No.7, pp: 60-62. - Gerrit Dumstorffa, Christoph Pille b, Rico Tiedemanna, Matthias Busseb, Walter
Langa, Smart aluminum components: Printed sensors for integration into
aluminum during high-pressure casting, The Society of Manufacturing Engineers.
Published by Elsevier Ltd.,166–172, (2017). - Guharaja S., Noorul Haq A., Karuppannan K.,M., 2006, “Optimization
of green sand casting process parameters by using Taguchi's method”. International
Journal of Advanced Manufacturing Technology, Vol.30, pp.1040–1048. - Gunasegaram, D.R.; Givord, M.; O’Donnell, R.G.; Finnin, B.R. Improvements engineered in UTS and
elongation of aluminum alloy high pressure die castings through the alteration of runner geometry and plunger velocity. Mat. Sci. Eng. A 2013, 559, 276–286 - H. B. R. Bhatt, "A design optimization of feeding sys- tem and solidification simulation for cast iron," in Proceeding on 2nd International Conference on Innovations in Automation and Mechatronics Engineering, 2014.
- H. Mayer, M. Papakyriacou, B. Zettl, S.E. Stanzl-Tschegg,“ Influence of porosity on the fatigue limit of die cast magnesium and aluminium alloys”, International Journal of Fatigue 25 (2003) 245–256 ,
2003 - Hsu, Q.C.; Do, A.T. Minimum porosity formation in pressure die casting by Taguchi method. Math. Prob. Eng. 2013, 2013, 1–9.
- J. Madan, P. V. M. Rao, and T. K. Kundra, “Optimal-parting direction selection for die-casting,” Int. J. Manuf. Technol. Manag., vol. 18, no. 2, pp. 167–182, 2009.
- Jer-Haur Kuo, Feng-Lin Hsu, Weng-Sing Hwang, Development of an interactive simulation system for the determination of the pressure-time relationship during the filling of a low-pressure casting process, Science and technology of advanced materials 2 (2001) 131- 145