This article introduces the paper ['Fatigue behavior of A356-T6 aluminum cast alloys. Part I. Effect of casting defects'] presented at the ['Journal of Light Metals']
1. Overview:
- Title: Fatigue behavior of A356-T6 aluminum cast alloys. Part I. Effect of casting defects
- Author: Q.G. Wang, D. Apelian, D.A. Lados
- Publication Year: 2001
- Publishing Journal/Academic Society: Journal of Light Metals
- Keywords: Aluminum castings; Fatigue life; Casting defects; Fracture mechanics; Weibull statistics
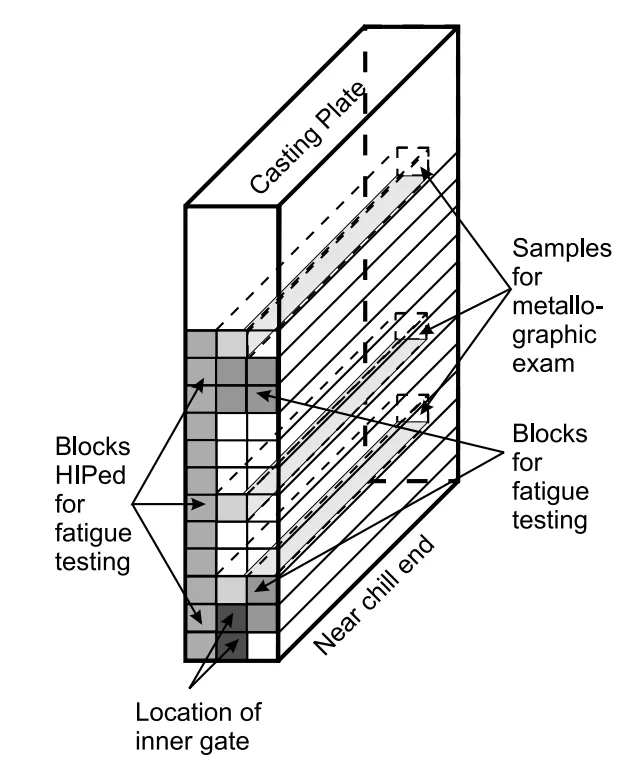
2. Research Background:
Background of the Research Topic:
Cast aluminum alloys are increasingly utilized in the automotive sector owing to their superior castability, corrosion resistance, and notably their high strength-to-weight ratio. The heightened application of high integrity shaped cast aluminum components under repeated cyclic loading has significantly focused attention on the fatigue properties of cast Al-Si alloys. Fatigue properties of cast aluminum components are critically influenced by casting defects and microstructural characteristics.
Status of Existing Research:
While some research indicates that fatigue resistance, akin to tensile ductility, is enhanced by refining the dendrite arm spacing and the size of eutectic silicon particles [1,2], the detrimental impact of casting defects is also acknowledged [3]. Liquid aluminum's susceptibility to hydrogen adsorption and oxidation leads to the inevitable presence of gas porosity and oxide inclusions in aluminum castings. Furthermore, inadequate casting feeding results in shrinkage porosity, which is also detrimental to fatigue properties. A quantitative method for predicting the relationship between fatigue life and defect size has been recently developed [4–8]. However, a comprehensive understanding that fully accounts for the effects of pore shape and defect type on fatigue life, based on experimental data, remains elusive.
Necessity of the Research:
In practical applications, a certain level of porosity is tolerated in castings, varying with the specific application. Identifying the specific roles of defects and other microstructural parameters on fatigue life is crucial. Moreover, a quantitative understanding of the role of defects is essential for establishing defect acceptance standards for both design specifications and quality control [9].
3. Research Purpose and Research Questions:
Research Purpose:
This study aims to experimentally investigate the influence of casting defects (porosity and oxide films) and secondary dendrite arm spacing (SDAS) on the fatigue performance of A356 aluminum casting alloy under various stress conditions. The research also seeks to examine the existence of a critical defect (pore/oxide) size for fatigue crack initiation.
Key Research:
- To quantify the detrimental effects of casting defects, specifically porosity and oxide films, on the fatigue life of A356-T6 aluminum alloy.
- To determine the relationship between casting defect size and fatigue life.
- To investigate the role of Secondary Dendrite Arm Spacing (SDAS) in fatigue performance in conjunction with casting defects.
- To explore the applicability of fracture mechanics and Weibull statistics in predicting the fatigue life of castings with defects.
- To identify and characterize the types of defects that initiate fatigue cracks in A356-T6 alloy.
Research Hypotheses:
- Casting defects significantly reduce the fatigue life of A356-T6 aluminum alloy.
- Fatigue life decreases with increasing casting defect size.
- A critical defect size exists for fatigue crack initiation, below which other microstructural features become dominant initiators.
- Fracture mechanics principles can be used to quantitatively predict the fatigue life of castings based on defect size.
- Weibull statistics can effectively describe the fatigue fracture behavior of aluminum castings with defects.
4. Research Methodology
Research Design:
An experimental investigation was conducted using A356 aluminum casting alloy. Cylindrical specimens were prepared from test castings produced with varying degrees of porosity and oxide films, achieved by controlling hydrogen levels and mold filling. Some samples were subjected to HIP-ed and Densal™ treatments to produce pore-free conditions for comparison. Fatigue tests were performed under different stress amplitudes and stress ratios (R = 0.1, 0.2, -1).
Data Collection Method:
Fatigue tests were conducted using a servo-hydraulic Instron machine under load control with pull-pull and pull-push sinusoidal loading at 55 Hz. Cylindrical specimens were tested at room temperature. The number of cycles to failure (Nf) was recorded for each specimen. Fracture surfaces were examined using Scanning Electron Microscopy (SEM) to identify fatigue crack initiators and measure defect sizes. Quantitative metallographic analysis was performed to measure SDAS.
Analysis Method:
- Fatigue crack growth analysis: The Paris-Erdogon equation was employed to model fatigue crack propagation from casting defects. The effective stress intensity factor range (ΔKeff) was considered, incorporating crack closure effects.
- Weibull statistical analysis: A two-parameter Weibull distribution was used to statistically analyze the fatigue life data and characterize the scatter in fatigue performance. Linear regression was applied to estimate Weibull modulus (b) and characteristic fatigue life (N₀).
- Fracture mechanics approach: The size of casting defects on fracture surfaces was measured and used as the initial crack size (aᵢ) in the fracture mechanics model to predict fatigue life.
- Microfractographic examination: SEM and EDS were used to identify fatigue crack initiation sites (porosity, oxide films) and characterize fracture features.
Research Subjects and Scope:
The research focused on Sr-modified A356-T6 aluminum casting alloy. Specimens were prepared with varying secondary dendrite arm spacings (SDAS) and levels of casting defects (porosity and oxide films). The study investigated the effect of defect size (up to 400-500 µm) and stress ratio (R = 0.1, -1) on room temperature fatigue performance. HIP-ed and Densal™ treated samples were included to represent defect-free conditions.
5. Main Research Results:
Key Research Results:
- Casting defects significantly reduced fatigue life, by at least an order of magnitude compared to defect-free (HIP-ed) samples.
- Fatigue life decreased as casting defect size increased.
- HIP-ed samples exhibited significantly longer fatigue lives than non-HIP-ed samples.
- A critical defect size appeared to exist for fatigue crack initiation; below this size, fatigue cracks initiated from other sources like eutectic particles and slip bands.
- Fatigue cracks predominantly initiated from porosity and oxide films located at or near the specimen surface.
- Porosity was found to be more detrimental to fatigue life than oxide films.
- Fatigue life data was well described by a two-parameter Weibull distribution.
- Fatigue life of castings with defects could be quantitatively predicted using fracture mechanics, based on defect size.
Data Interpretation:
- The presence of casting defects, particularly porosity and oxide films, is the primary factor controlling fatigue life in A356-T6 alloy.
- Larger defects lead to earlier fatigue failure due to increased stress concentration and accelerated crack propagation.
- Eliminating or reducing casting defects through processes like HIP significantly improves fatigue performance.
- The Weibull distribution effectively captures the statistical nature of fatigue failure in cast aluminum alloys, considering the variability in defect characteristics.
- Fracture mechanics provides a viable approach for predicting fatigue life based on defect size, suggesting that crack propagation from defects is the dominant stage of fatigue failure in these materials.
- The difference in Weibull modulus and characteristic fatigue life for cracks originating from porosity and oxide films indicates distinct fatigue behaviors associated with different defect types.
Figure Name List:
- Fig. 5. S-N data of a Sr-modified A356 alloy with various defect sizes, tested at two different stress ratios (a) R = 0.1 and (b) R = −1. " → " indicates run out – sample did not fail up to 10⁷ cycles.
- Fig. 6. SEM micrographs showing different defects originating fatigue cracks in the Sr-modified A356 castings: (a) pores; (b) oxide films.
- Fig. 7. Two-parameter Weibull plot for fatigue life data of the Sr-modified A356 casting alloy containing a variety of defects.
- Fig. 8. Fatigue life of a Sr-modified A356-T6 alloy as a function of pore size; (a) SDAS: 20-25 µm, (b) SDAS: 70-75 µm.
- Fig. 9. Fatigue life of a Sr-modified A356-T6 alloy as a function of oxide film size for various SDAS values.
- Fig. 10. Modified fatigue life plots which include the effect of defect size, √A, for tests at (a) R = 0.1, and (b) R = -1.
- Fig. 11. Comparison of actual fatigue life (Nf) with the calculated crack propagation life (Np) for tests at (a) R = 0.1, and (b) R = −1.
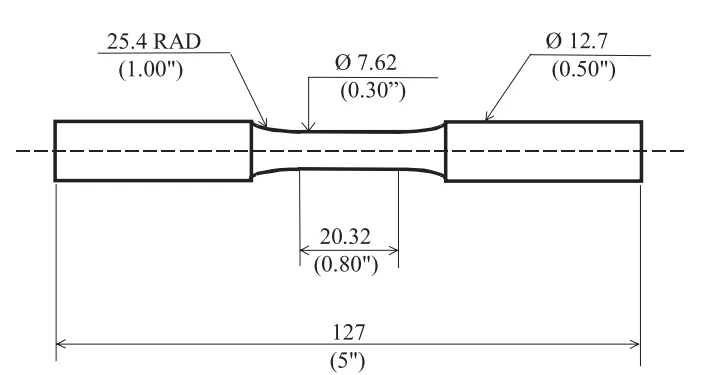
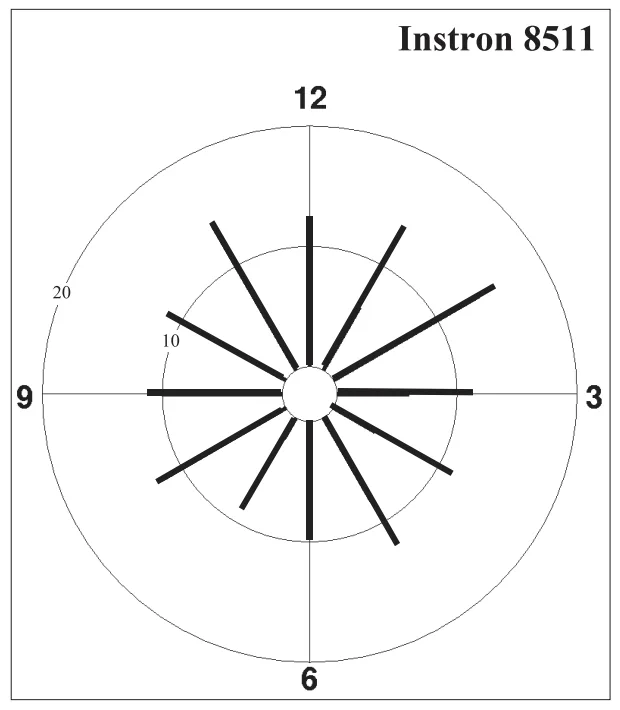
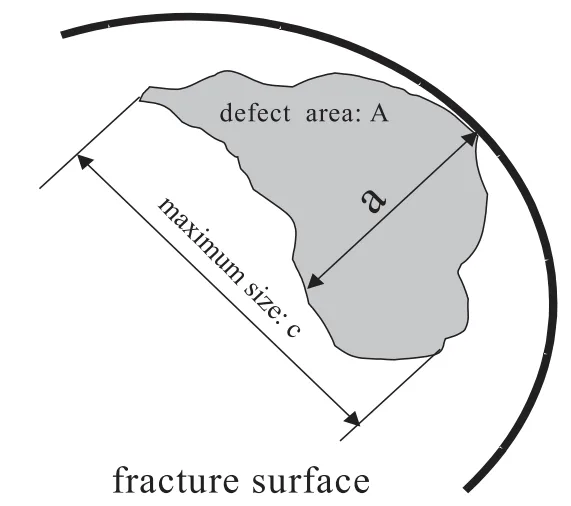
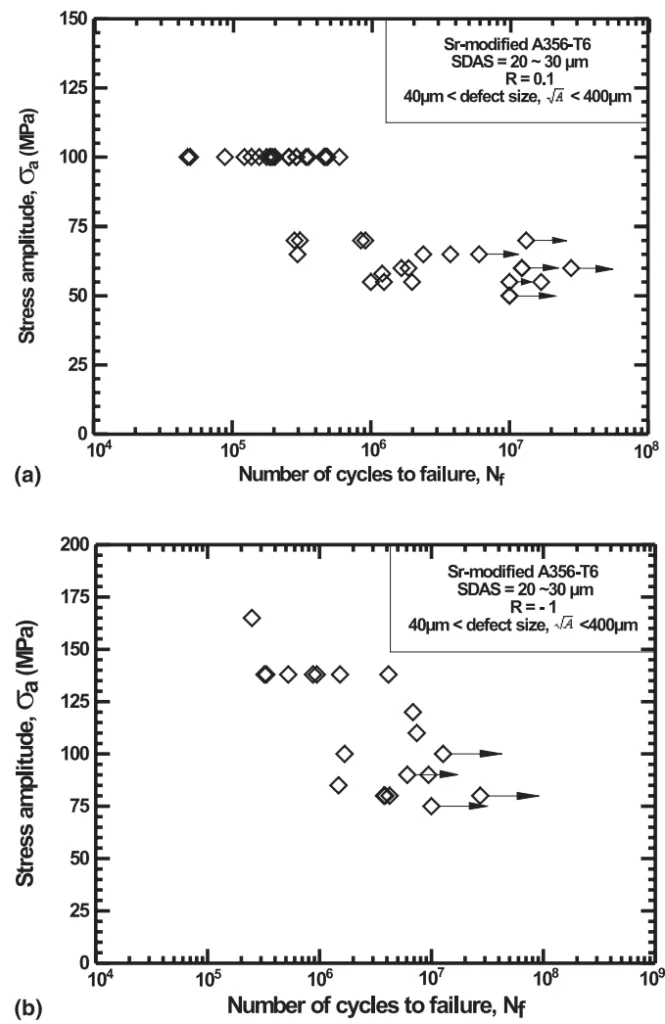
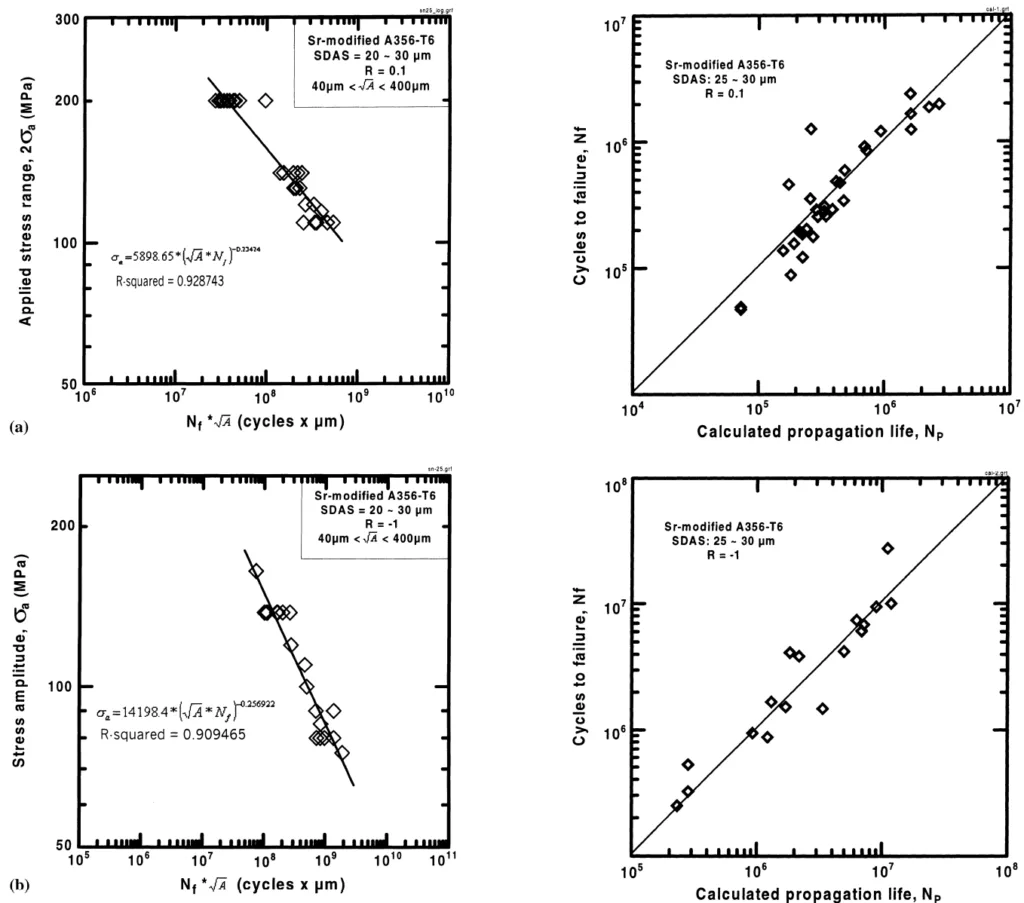
6. Conclusion:
Summary of Main Results:
This research conclusively demonstrates that casting defects, specifically porosity and oxide films, exert a significant detrimental influence on the fatigue behavior of A356-T6 aluminum cast alloy. These defects not only shorten the crack propagation phase but also the crack initiation phase of fatigue life. The size of casting defects is directly correlated with the reduction in fatigue life. Below a critical defect size, fatigue cracks initiate from other microstructural features. Fracture mechanics and Weibull statistics are effective tools for analyzing and predicting fatigue life in these materials. Porosity is identified as a more critical defect type compared to oxide films in terms of fatigue performance.
Academic Significance of the Research:
This study provides valuable quantitative data on the impact of casting defects on the fatigue performance of A356-T6 alloy, a widely used material in the automotive industry. It validates the application of fracture mechanics and Weibull statistics for fatigue life prediction in cast aluminum alloys with defects. The research contributes to a deeper understanding of the mechanisms of fatigue crack initiation and propagation in the presence of casting defects, differentiating the roles of porosity and oxide films.
Practical Implications:
The findings have significant practical implications for the die casting industry. The established correlation between defect size and fatigue life can inform the development of defect acceptance criteria and quality control standards for cast aluminum components. The identification of a critical defect size provides a target for minimizing defect levels to achieve desired fatigue performance. The study highlights the importance of reducing porosity, in particular, during casting processes. The predictive models can be utilized for component design and life assessment, enhancing the reliability of cast aluminum parts in fatigue-critical applications.
Limitations of the Research
The study focused on room temperature fatigue behavior of A356-T6 alloy under specific loading conditions (sinusoidal loading, R=0.1, -1). The findings may be specific to this alloy and these test conditions. The research primarily considered porosity and oxide films as casting defects, and further investigation into other types of defects and their interactions is warranted. The crack closure assumption (Kopening = 0) in the fracture mechanics model is a simplification and may introduce some level of approximation in life predictions, particularly at negative stress ratios.
7. Future Follow-up Research:
- Directions for Follow-up Research
Future research should explore the influence of pore shape and morphology, and different types of oxide films (young vs. old) on fatigue life. Investigating the fatigue behavior under variable amplitude loading and at elevated temperatures would broaden the applicability of the findings. Further studies are needed to refine the fracture mechanics models to account for crack closure effects more accurately, especially at negative stress ratios, and to incorporate the statistical distribution of defect sizes and types for more robust fatigue life predictions. - Areas Requiring Further Exploration
Further exploration is needed to fully understand the interaction between casting defects and other microstructural features, such as eutectic silicon particles and intermetallic phases, on fatigue crack initiation. Developing advanced non-destructive evaluation (NDE) techniques for accurate characterization of casting defects, including size, shape, and distribution, is crucial for implementing defect-based fatigue life prediction models in industrial practice. Investigating the effectiveness of different defect reduction strategies and post-casting treatments on improving fatigue performance remains an important area for future research.
8. References:
- [1] A.Wickberg, G. Gustafsson, L.E. Larsson, Microstructural effects on the fatigue properties of a cast Al7SiMg alloy, SAE Technical Publication #840121, 1984.
- [2] T.L. Reinhart, ASM Handbook, vol. 19, ASM International, Materials Park, OH, 1996, pp. 813-822.
- [3] N.E. Promisel, Evaluation of non-ferrous materials, 1956 (cited by H.E. Boyer, Atlas of fatigue curves, American Society of Metals, 1986).
- [4] M.J. Couper, A.E. Neeson, J.R. Griffiths, Casting defects and the fatigue life of an aluminum casting alloy, Fatigue Fract. Eng. Mater. Struct. 13 (1990) 213-227.
- [5] B. Skallerud, T. Iveland, G. Härkegård, Fatigue life assessment of aluminum alloys with casting defects, Eng. Fracture Mech. 44 (1993) 857-874.
- [6] J.A. Odegard, K. Pedersen, Fatigue properties of an A356 (AlSi7Mg) aluminium alloy for automotive applications - fatigue life prediction, SAE technical paper SAE-940811, 1994, pp. 25-32.
- [7] Chih-Hsien Ting, A model for the long-life fatigue behaviour of small notches, Ph.D. Dissertation, University of Illinois at Urbana-Champaign, 1991.
- [8] D.L McLellan, M.M. McLellan, An approach to fatigue design for aluminum castings, AFS Trans. 104 (1996) 445-449.
- [9] J.F. Major, Porosity control and fatigue behaviour in A356T61 aluminum alloy, AFS Trans. 105 (1997) 901-906.
- [10] W. Elber, Fatigue crack closure under cyclic tension, Eng. Fracture Mech. 2 (1970) 37-45.
- [11] N.E. Dowling, ASTM STP 637 (1977) 97–121.
- [12] D. Wilhem, J. FitzGerald, J. Carter, D. Dittmer, An empirical approach to determining K for surface cracks, in: Proceedings of the Fifth International Conference on Fracture, vol. 1, Cannes, 1981, pp. 11-21.
- [13] W. Weibull, A statistical distribution function of wide applicability, J. App. Mech. 18 (1951) 293-297.
- [14] A. Khalili, K. Kromp, Statistical properties of weibull estimators, J. Mater. Sci. 26 (1991) 6741-6752.
- [15] J. Campbell, The origin of porosity in castings, in: Proceedings of the fourth Asia Foundry Congress incorporated in 32nd Annual Convention of Australian Foundry Institute, 1996, pp. 33-50.
- [16] Q.G. Wang, Microstructure and tensile fracture behavior of Al-Si-Mg casting alloys, Ph.D. Thesis, The University of Queensland, Brisbane, Australia, 1997.
- [17] C.H. Cáceres, C.J. Davidson, J.R. Griffiths, The deformation and fracture behaviour of an Al-Si-Mg casting alloy, Mater. Sci. Eng. A A197 (1995) 171-179.
- [18] Q.G. Wang, C.H. Cáceres, The fracture mode in Al-Si-Mg casting alloys, Mater. Sci. Eng. A A241 (1998) 72-82.
- [19] Q.G. Wang, C.H. Cáceres, On the strain hardening behavior of Al-Si-Mg casting alloys, Mater. Sci. Eng. A 234-236A (1997) 106-109.
- [20] C.H. Cáceres, Q.G. Wang, J.R. Griffiths, C.J. Davidson, The effect of Mg on the microstructure and mechanical behavior of two commercial Al-Si-Mg casting alloys, Metall. Trans. A 30A (1999) 2611-2618.
- [21] Q.G. Wang, C.H. Cáceres, J.R. Griffiths, The cracking of Fe-rich and eutectic Si particles in an Al-7Si-0.7Mg casting alloy, AFS Trans. 106 (1998) 131-136.
- [22] D.S. Saunders, J.R. Griffiths, B.A. Parker, The fracture toughness of an aluminum casting alloy, J. Aust. Inst. Metals 20 (1975) 33-38.
- [23] D.A. Gerard, D.A. Koss, The dependence of crack initiation on porosity during low cycle fatigue, Mater. Sci. Eng. A 129 (1990) 77-85.
- [24] D.A. Gerard, The influence of porosity on low cycle fatigue, Ph.D. Dissertation, Michigan Technological University, Houghton, MI, 1989, pp. 1–167.
- [25] J.C. Ting, The long-life regime fatigue analysis for lost foam cast Al-Si Alloy 319, Ph.D. Dissertation, University of Illinois-Champaign, IL, 1991, pp. 1–186.
- [26] J. Campbell, C. Nyahumwa, N.R. Green, The concept of the fatigue potential of cast alloys, in: Proceedings of Materials Solution Conference '98 on Advances in Aluminum Casting Technology, 12-15 October 1998, pp. 225-233.
- [27] C. Nyahumwa, N.R. Green, J. Campbell, Effect of mold filling turbulence on fatigue properties of cast aluminum alloys, AFS Trans. 106 (1998) 215-223.
- [28] J.C. Newman Jr., A crack opening stress equation for fatigue crack growth, Int. J. Fracture 24 (1984) 131-135.
- [29] J.C. Newman Jr., A crack closure model for prediction of fatigue crack growth under aircraft spectrum loading, ASTM STP 748 (1982) 53-84.
- [30] N.E. Dowling, N.S. Iyyer, Fatigue crack growth and closure at high cyclic strains, Mater. Sci. Eng. 96 (1987) 99-107.
- [31] I. Gustavson, A. Melander, A finite element study of the early growth of fatigue cracks emanating from a spherical pore, in: Proceedings of the Fifth International Conference on Numerical Methods in Fracture Mechanics, Germany, 1990, pp. 225-236.
- [32] Y. Verremen, J.P. Ballon, J. Masounave, Fatigue short crack propagation and plasticity-induced crack closure at the toe of a fillet welded joint, in: The Behavior of Short Fatigue Cracks, EGF publication 1, 1986, pp. 387-404 (Mechanical Engineering Publication, London).
9. Copyright:
- This material is "[Q.G. Wang, D. Apelian, D.A. Lados]"'s paper: Based on "[Fatigue behavior of A356-T6 aluminum cast alloys. Part I. Effect of casting defects]".
- Paper Source: https://doi.org/10.1016/S1471-5317(00)00008-0
This material was summarized based on the above paper, and unauthorized use for commercial purposes is prohibited.
Copyright © 2025 CASTMAN. All rights reserved.