Summary of "Automobile Parts Casting-Methods and Materials Used: A Review"
This material is based on the paper "Automobile Parts Casting-Methods and Materials Used: A Review" by Madhav Goenka, Chico Nihal, Rahul Ramanathan, Pratyaksh Gupta, Aman Parashar, and Joel Jb.
Paper Source: https://doi.org/10.1016/j.matpr.2020.03.518
1. Overview:
- Title: Automobile Parts Casting-Methods and Materials Used: A Review
- Authors: Madhav Goenka, Chico Nihal, Rahul Ramanathan, Pratyaksh Gupta, Aman Parashar, Joel Jb
- Publication Year: 2020
- Published Journal/Conference: Materials Today: Proceedings 22 (2020) 2525-2531, ICMMM 2019
- Keywords: Centrifugal Casting; Die Casting; Engine Block; Piston; Al-Si Alloys; CGI
2. Research Background:
- Social/Academic Context of Research Topic: Automobiles are becoming more sophisticated each year, and manufacturers are striving to reduce the kerb weight of automobiles by using various materials with high strength-to-weight ratios. To comply with high standards like NCAP, automobile parts are being made much stronger than before, pushing manufacturers to develop new and innovative methods for manufacturing automobile parts.
- Limitations of Existing Research: The paper does not explicitly mention limitations of existing research. However, considering the continuous emphasis on lightweighting and high-strength requirements for automotive parts, it can be implicitly inferred that conventional casting methods and materials faced challenges in meeting these demands.
- Necessity of Research: A comprehensive review of various casting processes and materials used in automobile part manufacturing is needed. Especially with the advancement of the automotive industry and increasing demands for lightweight and high-performance parts, providing information on suitable casting methods and material selection is crucial.
3. Research Objectives and Research Questions:
- Research Objective: This paper aims to investigate various casting processes used in manufacturing automobile parts, discuss the most suitable materials for each component, and briefly review the pros and cons of each process.
- Core Research Questions:
- What are the main casting processes used in automobile part manufacturing?
- What are the appropriate materials for each casting process, and what are the reasons?
- What are the advantages and disadvantages of each casting process?
- Research Hypothesis: No explicit research hypothesis is presented in the paper.
4. Research Methodology
- Research Design: This paper is a review paper on casting methods and materials for automobile parts. It comprehensively reviews casting processes and materials used in the automotive industry by analyzing existing research literature and data.
- Data Collection Methods: It is presumed that data was collected by referencing various academic literature, research reports, and industry materials, but the paper does not specify the data collection methods in detail.
- Analysis Methods: Based on the collected data, the paper analyzes the main casting processes (Green sand casting, Centrifugal casting, Lost-foam casting, Die casting, Squeeze casting) and materials (Grey cast iron, CGI, Aluminum alloy, Al-Si alloys, Magnesium alloy, Titanium casts) used in automobile part casting. It compares and analyzes the characteristics, advantages, disadvantages, and application examples of each process and material.
- Research Subjects and Scope: This paper comprehensively covers casting processes and materials used in automobile part manufacturing, focusing particularly on major automobile components such as engine blocks, pistons, cylinder heads, and wheels.
5. Key Research Findings:
- Core Findings:
- Various casting processes (Green sand casting, Centrifugal casting, Lost-foam casting, Die casting, Squeeze casting) are used in automobile part manufacturing.
- Each casting process has specific advantages and disadvantages, and the appropriate process is selected based on the required part characteristics and production volume.
- Die casting is widely used in automobile part casting, but it is costly.
- Green sand casting is a low-cost alternative, but it has low dimensional accuracy and surface finish.
- CGI exhibits superior strength-to-weight ratio and mechanical properties compared to Grey cast iron, making it preferred for engine block manufacturing (Table 1).
- Centrifugal casting is mainly used for manufacturing cylindrical parts and provides high metallurgical cleanliness and homogeneous microstructures.
- Lost foam casting is suitable for manufacturing complex shapes and is described as a reliable technique for engine block manufacturing.
- Squeeze casting is advantageous for reducing porosity and improving mechanical properties, making it suitable for automobile part manufacturing.
- Al-Si alloys are used more frequently than cast iron, offering high strength-to-weight ratio and thermal conductivity.
- Low-pressure die casting (LPDC) is mainly used for wheel production, providing high quality and low porosity.
- Statistical/Qualitative Analysis Results:
- Table 1: Comparison of mechanical properties of CGI and Grey cast iron
- Modulus of Elasticity (GPa): Grey cast iron (98-110), Compacted Graphite Cast Iron (170-190)
- Tensile Strength (MPa): Grey cast iron (160-320), Compacted Graphite Cast Iron (300-600)
- Comparison of Centrifugal casting piston and gravity permanent mold casting piston:
- Coefficient of linear expansion: Centrifugal casting piston is approximately 23% lower (15.3*10^-6 K-1)
- Wear analysis improvement rate: Centrifugal casting piston is 70.4% higher
- Reduction rate of fluidity when Sb is added to AlSi6Cu2Mg alloy: 25% when added with strontium, 15% when added with antimony
- Die casting part wall thickness: 0.75 mm possible
- Die casting part surface roughness: approximately 2.2 micrometres
- Mechanical properties of Squeeze casting parts: 20-30% improvement compared to die casting
- Table 1: Comparison of mechanical properties of CGI and Grey cast iron
- Data Interpretation: By comparing and analyzing the characteristics of each casting process and material, the paper provides guidelines for selecting the optimal casting method and material that meet the functional requirements of automobile parts. It particularly emphasizes the importance of casting technologies and materials that meet the demands for lightweighting, high strength, and high quality.
- Figure Name List:
- Fig. 1. Aluminium Die Cast Parts.
- Fig. 2. Flow chart of manufacturing of MMC pistons using squeeze casting.
- Fig. 3. The process of squeeze casting.


6. Conclusion and Discussion:
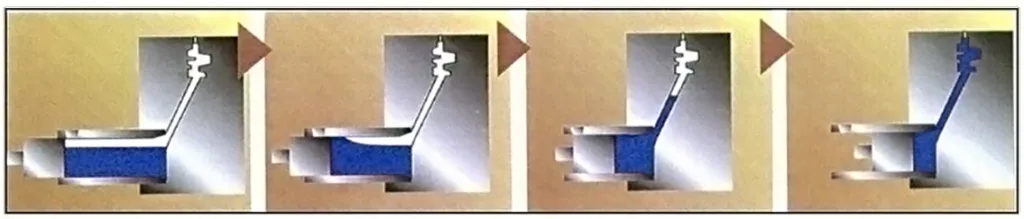
- Summary of Main Results: This paper reviewed the main casting processes and materials used in the automotive industry and analyzed the characteristics and application fields of each process. Die casting is widely used but costly, and Green sand casting is inexpensive but has low precision. Special processes (Centrifugal casting, Lost-foam casting, Squeeze casting) can be utilized for specific parts and requirements.
- Academic Significance of Research: Provides comprehensive information on casting processes and materials for automobile parts, serving as foundational data for related research and industrial fields. Clearly presents the advantages and disadvantages of each casting process through comparative analysis and provides insights into material selection.
- Practical Implications: Provides useful information for automobile part design and manufacturing engineers to select the optimal casting process and material considering the functional requirements, production volume, and cost of parts. Contributes to the development and application of casting technologies for lightweight and high-performance part manufacturing.
- Limitations of Research: This paper is a review paper and does not include in-depth experimental analysis or performance evaluation of specific casting processes or materials. Additionally, a review of the scope and recency of the references cited in the paper is needed.
7. Future Follow-up Research:
- Directions for Future Research:
- In-depth research on optimal process variables and material combinations for each casting process.
- Research on the development of new casting technologies and materials.
- Research to improve the performance and reliability of cast parts.
- Research on the development of eco-friendly casting processes.
- Areas Requiring Further Exploration: Although the paper does not explicitly suggest future research directions, the above future research directions can be inferred based on the conclusion and discussion.
[Full Text View]
Automobile Parts Casting-Methods and Materials Used: A Review
Madhav Goenkaa, Chico Nihala, Rahul Ramanathana, Pratyaksh Guptaa, Aman Parashara, Joel Jb*
aB.Tech Mechanical Engineering,Vellore Institute of Technology, Katpadi,Vellore, TamilNadu, India
b*Assistant Professor (senior),Vellore Institute of Technology, Katpadi,Vellore, TamilNadu, India
Abstract
Automobiles are becoming more and more sophisticated with every passing year. Manufacturers have been trying their best to bring down the kerb weight of their automobiles by using various materials with high strength to weight ratio. The different parts of the automobile are being made much stronger than before in order to comply with the high standards set by NCAP.
Hence, this pushes automobile makers to come up with new and innovative methods to manufacture the parts of their automobiles. Our paper addresses the various casting processes used to make automobile parts and also touches on the various materials used to make the components.
The casting methods discussed are- Green sand casting, Centrifugal casting, Lost- foam casting, Die casting and Squeeze casting. In the paper we discuss about the most suited materials used for each component and briefly discuss about the pros and cons of each process.
Keywords : Centrifugal Casting, Die Casting, Engine BlockPiston, Al-Si Alloys, CGI
1. Introduction
Casting is the process of pouring a liquid metal into a mold of specific dimensions in order to obtain a desired shape. Casting is preferred in industries as it is cost effective and produces dimensionally accurate components. Casting can be carried out using most metals, however the metals most predominantly used are iron, aluminum, steel and copper based alloys.
According to Sacred records the use of casting to shape metals can be traced back to 5000 BC. It was established that metal casting was first discovered in the Middle East and later on moved to China and India. During the initial years, the progress of casting was relatively slow. The first metals to be cast were gold and silver, followed by copper and bronze.
The next era of foundry started to develop towards the culmination of the 15th century. The start of the 16th century saw the use of the blast furnace for the first time and pig iron was introduced, paving the way for iron and steel molding. As the casting process developed, the latest technologies were incorporated and different casting techniques like squeeze casting, centrifugal casting, lost wax casting, shell molding, stir casting etc. were introduced.
As the number of applications of castings increased, the materials used also got more and more sophisticated. Starting with gold and silver, materials used in the present day and age are MMCs, Al-Si alloys, Zinc etc. One major application of metal casting is in the automobile industry.
Metal casting is a huge market for cast products using ferrous, non-ferrous metals and their alloys. There are many a processes to produce automobile parts and accessories efficiently that are light in weight, inexpensive to make and have a good life. Zinc die casting and aluminum die casting are the most popular casting processes to produce automobile parts.
The weights of these parts are generally around one third the weight of the steel parts with the parts having good thermal properties. The major automobile components made using casting are pistons, engine blocks, valve covers, wheels, transmission housing, carburetors, fan clutches etc.
With the constant need to make the automobiles lighter and stronger, Magnesium alloy and Titanium casts have grown due to their superior corrosion performance. Al-Si alloys are popularly used for casting internal combustion engine components owing to their excellent thermal conductivity preventing thermomechanical damage and lower density providing light weight components.
The automobile industry offers a myriad of applications of casting processes which are constantly being worked on and improved in order to fall in line with the established standards of the industry.
2. Casting Methods and Materials Used
2.1. Green Sand Casting
Hieu Nguyen[1] discussed about cast irons and aluminium alloy used to manufacture engine blocks using green sand moulding . Green sand is usually a mixture of 5-11% bentonite, 1% anthracite, 3% water, silica and chromite sand. Grey cast iron alloys was preferred owing to its low cost, good mechanical properties and availability. These alloys contain 2.5-4 weight % carbon 0.2-1.0 weight % manganese and about 1-3 weight % silicone. These alloys have great wear resistance, and a very good damping capacity making it ideal for engine blocks. However, a major trade off is that Grey cast irons are weak and prone to deformation. Aluminium alloys were used as it provided a
high strength to weight ratio required to manufacture the engine block. The Aluminium alloy 319 is normally used to make engine blocks and comprises of 85.8-91.5 weight % aluminium, 3-4 weight % copper and 5.5-6.5 weight % silicone. Now days CGI is preferred due to its better strength to weight ratio and mechanical properties as shown on table 1.

Adeleke Victor Adedayo [2] spoke about the influence the chemical composition of cast iron has on the
mechanical properties of sand cast components. He discussed how the cooling rate of molten cast iron during solidification influences the microstructure of the component. An accelerated cooling rate promoted the formation of cementite due to the suppression of the graphitization process. A mixed microstructure consisting of cementite and graphite was formed during slow cooling.
Hieu Nguyen [1] discussed about the use of green sand moulding in order to cast the engine block. The process of green sand moulding was described in detail and the key aspects were highlighted. Firstly, a mix of silica, clay and water was poured into the pattern. Mould compaction was carried out by jolting and squeezing. The core which consists of hardened sand is then used for support. The molten metal is then poured into the mould and it is allowed to solidify. After solidification the moulds were removed and the cylinder block was cleaned and inspected. Heat treatment was done on the block to improve its properties.
One of the main advantages of green sand casting is that it gives a good design flexibility thus stating that casting can be done for any size and weight of component. Using this casting process, even complex shapes can be cast very easily with very minimal expenditure on tooling and equipment. Also, a wide range of materials can be used with a very short lead time in comparison to the other casting processes. On the other hand green sand casting process does not provide with adequate strength due to its high porosity. Also, there is low dimensional accuracy and a very poor surface finish. A secondary machining operation is often required to give the component the adequate tolerance.
Also, defects such as shrinkage, porosity and surface defects are unavoidable.
2.2. Centrifugal Casting
D. Anantha Padmanaban [3] stated that Al-Si alloys exhibit a considerable amount of precipitation hardening, thus allowing for the improvement of its mechanical properties on heat treatment. These enhanced mechanical properties give this alloy a distinct advantage over other alloys when it comes to manufacturing automotive parts using centrifugal casting.
The process of centrifugal casting has been mainly used for cylindrical parts. There are two basic types of
centrifugal castings: horizontal and vertical. As their name suggests, the horizontal types rotate about the horizontal axis and the vertical about the vertical axis. Horizontal types are used to make pipes, tubes, sleeves and tubular castings that are simple in shape. Vertical types are used to make a huge variety of things like gear blanks, wheels, yokes, brackets, valve bodies. These types can even make castings that are not cylindrical or symmetrical.
The centrifugal casting process provides with a high degree of metallurgical cleanliness and homogenous
microstructures. A test was done by the mechanical engineering department at the Minho University, Portugal where the material used for castings was an aluminium alloy AS12UN with the following composition: Fe-0.75%, Si-(11.50–13.00)%, Zn-0.20%, Mg(0.75–1.30)%, Ni-(0.80–1.30)%, Pb-0.10, Sn-0.05%, Ti-0.20% [4]. Three tensile specimens were cut out from the casting to compare the mechanical properties of the different places of the casting with each other. Cylindrical components of up to 8m in diameter and 17 m in length with a wall thickness in the range of 2.5-125mm can be cast by centrifugal casting.
K.Venatesvaran [5] discussed about the use of Silumin (Al-Si alloys) in centrifugal castings. The silicone content in this alloy ranges between 3-50%. This material is preferred due to its light weight, high castibility, high corrosion resistance and high machinability. The reason why Silumin is preferred over cast iron for centrifugal casting of pistons is because of its weight (3 times lighter than CI). It also possesses a higher thermal conductivity, allowing it to dissipate heat very easily as compared to cast iron.
Aqeel Ahmed, M. S. Wahab [6] stated that out of the numerous casting methods used to manufacture pistons, each process has its pros and cons and each process has its own impact on the mechanical and physical properties as well as on the microstructure of the piston. They analysed pistons manufactured by centrifugal casting and observed that the hardness from the piston skirt to the piston head increased by 23.7HRB. They compared the properties of a piston made by centrifugal casting to a piston made from gravity permanent mould casting It was observed that the piston made by centrifugal casting had a coefficient of linear expansion as 15.3*10-6 K-1 which is about 23% lower than gravity permanent mould casting. The improvement in wear analysis of the piston made from centrifugal casting was found to be 70.4% more than the piston made from gravity permanent mould casting.
Most of the casting processes solidify both from the inside as well as the outside thus risking the formation of mid-wall shrinkage, whereas in centrifugal casting it solidifies from outside to inside thus resulting in a part free of shrinkage and porosities. Because of the centrifugal force the high density metal gets pushed outside and at the same time the lower density components float towards the inside, because these lower density materials float inside such as the oxides, sulphides and gases there are no inclusions in the casting. Another major advantage of this casting is that it reduces micro-porosity. One of the limitations of this casting is the limited length to diameter ratio which is 2:1. Another challenge that one can face is the irregular shape of the cast and the cost to make its die. Also casting of very small inside diameters using this process is also difficult.
2.3. Lost Foam Process
P.Scarber, H.Littleton [7] elaborated on the use of aluminium and iron alloys in the lost foam casting process. Compacted Grey cast iron is the only iron alloy used, owing to the lack of lustrous carbon defects and undesirable carbon pick-ups in the final casting. They also state that due to the high elastic modulus and tensile strength of CGI, it is used in the lost foam process. According to them, these superior properties of CGI were achieved by modifying the morphology of graphite. Mousa Javidani [9] briefly explained that Mg has an advantage over Al as it is 33% lighter and have a specific strength which is 14.075% more than Al. However the specific stiffness of Al was found to be 0.7% more than that of Mg.Magnesium alloys are another type of preferred materials used in lost foam casting owing to their high strength to weight ratio. These alloys exhibit good workability at high temperatures and are thus widely used in the lost foam process. It is also widely used due to its ability to be moulded into thin- walled intricate castings which are predominantly made using the lost foam process. The weight of castings that can be cast in this process range from 0.5 kg to 1 tonne, with a minimum wall thickness of 2.5mm.
Hieu Nguyen [1] discussed about the different casting processes used to make the engine block. He described lost foam casting as the most reliable technique to manufacture engine blocks. He subsequently describes the lost foam process and stated the important factors in order to achieve a good dimensional accuracy and surface finish. Some of the factors discussed were the heating of the tool before the polystyrene beads were injected into it. Over-fusion of the beads takes place if they are heated for an extended period or not cooled to a desired temperature, thus resulting in surface variations in the moulding. They stated that the mould assembly can be stiffened by placing it in a vat along with a water based ceramic liquid. This helps to prevent the molten metal from destroying the mould. Once the casting is complete, it undergoes heat treatment to enhance the mechanical properties.
2.4. Die Casting
Acknowledgements and Reference heading should be left justified, bold, with the first letter capitalized but have no numbers. Text below continues as normal. The European Aluminium Association discuss how cylinder heads are made using gravity die casting. They use this process as it allows the engineers to achieve a high solidification rate in the flame deck region, thus resulting in a very fine microstructure with low porosity. Sand cores were used to realise a sophisticated water jacket cooling system of complex geometry. They also discuss how the Rotacast process which is a type of gravity die casting provides higher productivity due to a considerably lesser amount of runners and feeders. We also know about the use low pressure die casting to manufacture the cylinder head. The major advantages of this process being almost no process scrap. However, this process decreases the productivity of the manufacturing as the cycle time is relatively high. Usually, die cast components can have walls of 0.75 mm with a smooth surface finish of about 2.2 micrometres, making it useful for thin walled automotive components. Table 2 shows typical die temperatures and life of Al & Mg
![Table 2. Typical die temperatures and life of Al and Mg [16]](https://castman.co.kr/wp-content/uploads/Table-2.-Typical-die-temperatures-and-life-of-Al-and-Mg-16.png)
In place of cast iron, Al-Si alloys are more frequently used because these alloys have high strength-weight ratio and high thermal conductivity. Another advantage of using alloys is that the composition can be varied depending on the demand of the operating conditions on the material properties. However, hypoeutectic Al-Si alloys may soften (hampering the surface characteristics) at very high temperatures even though performance of the engine increases at said temperature [8]. Thus, this challenge calls for strengthening of the alloy. In a start-stop cycle an engine might be warmed up to 243-523 K in a cold winter. Thus, in case of cylinder head, if we consider three different loads- the assembly load, combustion load (combustion pressures as high as 200 bar), and thermal loadthermal load [9] will be the maximum due to non-uniform thermal expansion and contraction. Automobile parts require uniformity and high surface finish which can be accomplished by using casting methods that work in a controlled environment- pressure die casting. In fact, die casting was originally developed specifically for automotive applications. The idea is to produce parts that are light, easy to handle and cheap. Thus, die casting is widely applied to zinc and aluminium which are lighter than cast iron. Figure 1 shows the aluminium die cast parts of an automobile.

Die casting is mostly used because a large number of parts need to be manufactured in a short amount of time (hundreds to thousands per day) with high accuracy. Parts like valve covers, wheels, transmission housings, engine block, wheel spacer, carburettor, impellers and fan clutch, alternator housing, airbag gas generator housing, etc. are all mode through aluminium die casting method. Aluminium or Al-Si alloys are used for Die casting. During this process, molten metal is injected at a high pressure into a die (made of metal) which is a permanent mould comprising of two parts of the desired shape attached together. Once the metal cools, these segments are detached and the cast part is obtained. Since the die is a permanent mould, it can be used multiple times for casting the same component with the same dimensional accuracy and surface finish, thus producing a uniformity in the cast parts. However, since the component is cast in a metal in contrast to sand in sand casting, certain factors like cooling and solidification time, dissolved gas removal, etc. also come into play. Appropriate modifications must be done to the die to alleviate these challenges which makes the designing of the die difficult. An appropriate draft angle ensures that the cast part is removed easily.
Alloys used for making the cylinder heads and blocks must have good fluidity, density, machinability, etc. It has been observed that addition of sodium or strontium in nugatory quantities increases the fluidity of the metal. The Al-Si alloy is being used extensively nowadays for the production of complex wheel geometries that weigh less. This composition of alloy is not only used in the automotive industry but also in the aeronautic and aerospace industries because of their high strength-to-weight ratio and also because of the improvement in their mechanical properties upon heat treatment. Other than this grain refinement can be done which promotes the formation of finer grains thus improving the mechanical properties. These are generally used in the forms of bars which are directly added to the molten metal. This effect is based on Ti and B. Therefore, the refiner used is Al-5Ti-B or ATB [10]. The process which is predominantly used for the production of wheels is the low-pressure die casting (LPDC)because of the higher quality products that it delivers along with the reduction in porosity. Also the large scale production for this process is easier than that of gravity die casting (GDC). Some of the defects that are found in the aluminium alloy are macro-porosity, micro-porosity and exogenous oxide inclusions [11]. These defects affect a lot on the wheel cosmetics, air-tightness and wheel mechanical performance.
2.5. Squeeze Casting
Reinforcements are often added to metal alloys to improve certain properties of the alloy-specific stiffness, strength, wear resistance, high- temperature properties and thermal expansion. M. Dudyk [10] found that the best way to reduce shrinkage of cast parts was by using AlSi6Cu2Mg alloy with Sb. AlSi6Cu2Mg along with strontium and antimony lowers fluidity of the alloy by 25% and 15% respectively as compared to unmodified alloys. Ceramic particulates [12] are normally composed of silicon carbide or aluminium oxide with volume fraction in the range of 5-70%. Other ceramic- fibre materials like carbon fibre are also used which find a popular application in automobile bodies. The purpose of addition of the said reinforcements is centred at reducing the weight for the brake and engine components and increased length for the driveshaft. MMCs result in reduction of reciprocating weight, noise, fuel consumption, and emissions and increase in engine power. For instance, components like connecting rods are fabricated from either fibre or particulate reinforced aluminium alloys. The components of squeeze casting were found to have 20-30% better mechanical properties than die casting.
Wu Shenqing and Li Jun [15] gave an elaborate discussion on the material and the type of casting used to make pistons. In the paper they describe how Aluminium Pistons are manufactured using a eutectic aluminium and silicone alloy. The process flow of MMC partially reinforced pistons starts with the pre-treatment of the ceramic fibres. The fibres were kept to a length to diameter ratio of 50 – 150. A bonding agent was added to the short fibres in a suitable ratio, so that the fibres can take the shape of the die sets. The preform was dried and sintered to a temperature of 800o C, thus making them porous. The composite piston was then manufactured by squeeze casting. The mother preform is injected with the molten aluminium alloy. The liquid alloy penetrates into the 3-D spaces in the fibres and solidifies. Figure 2 shows flow chart of manufacturing of MMC pistons using squeeze casting process.

The horizontal squeeze casting process can be used for the production of engine bracket mounts. [3] The process followed for the production starts by the controlled flow of molten metal into a heated sleeve. This is followed by the plunger slowly moving until the sleeve and runner are completely filled as to avoid the seepage of air inside the die. Figure 3 shows the four process of squeeze casting.
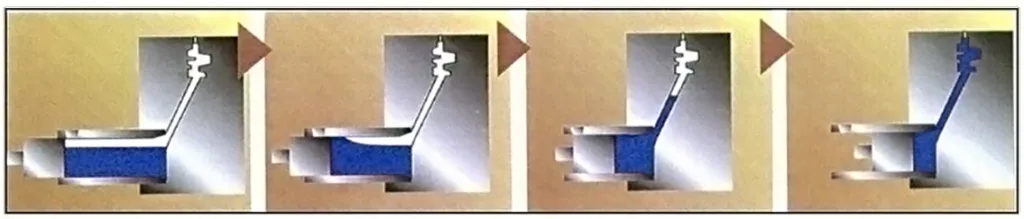
The squeeze casting has many advantages with porosity reduction being the most important one. Also using this process a near net shape can be achieved and also the mechanical properties can be enhanced. This process is extremely suitable for mass production. The squeeze casting process is being used in the fabrication of automobile parts which satisfies the high strength [13] requirement and the desired elongation. It has been seen that the squeeze casting process can be used in a very limited manner when it comes to the vertical type process.
3. Conclusion
In this paper the casting processes which are most specifically used in the automobile industry have been discussed and attempts have been made to give a comprehensive evaluation of the processes which would be most suited for casting a particular part. During the course of this evaluation it was found that Die casting finds a ubiquitous application in casting most of the automobile parts, despite its high cost. Other processes like green sand casting can be used as an inexpensive alternative for casting parts which are less demanding on dimensional accuracy and surface finish. Based on the requirement of the part to be cast, specialised processes can be used the material and process parameters of which have been elucidated in this paper.
References
[1] H. Nguyen, “Manufacturing Processes and Engineering Materials Used in Automotive Engine Block,” Mater. Sci. Eng. Sect. B, EGR250, pp.
11–23, 2005.
[2] A. V. Adedayo, “Effects of addition of iron (Fe) filings to green moulding sand on the microstructure of grey cast iron,” J. Brazilian Soc.
Mech. Sci. Eng., vol. 32, no. 2, pp. 171–175, 2010.
[3] D. Anantha Padmanaban and G. Kurien, “Silumins: The automotive alloys,” Adv. Mater. Process., vol. 170, no. 3, pp. 28–30, 2012.
[4] G. Chirita, D. Soares, and F. S. Silva, “Advantages of the centrifugal casting technique for the production of structural components with Al-Si
alloys,” Mater. Des., vol. 29, no. 1, pp. 20–27, 2008.
[5] N. Periyasamy, “Thermal Analysys and Material Optimization of Piston in IC Engine,” no. 3, pp. 1132–1144, 2018.
[6] Q. Bakhsh, D. Ali, A. Ahmed, M. S. Wahab, K. Kamarudin, and A. A. Raus, “Mechanical Properties, Material and Design of the Automobile
Piston: An Ample Review,” Indian J. Sci. Technol., vol. 9, no. 36, pp. 5–11, 2016.
[7] P. Scarber, H. Littleton, and A. Druschitz, “Preliminary Study of Compacted Graphite Iron Engine Blocks Produced by the Lost Foam
Casting Process,” AFS Trans, pp. 881–890, 2009.
[8] R. Colás, J. Talamantes-Silva, S. Valtierra, F. Morales, and A. J. Pérez-Unzueta, “Cast-In Hypereutectic Aluminum Liners for EngineBlocks,” J. Manuf. Sci. Eng., vol. 131, no. 1, p. 014502, 2009.
[9] M. Javidani and D. Larouche, “Application of cast Al–Si alloys in internal combustion engine components,” Int. Mater. Rev., vol. 59, no. 3,
pp. 132–158, 2014.
[10] E. Aguirre-De La Torre, U. Afeltra, C. D. Gómez-Esparza, J. Camarillo-Cisneros, R. Pérez-Bustamante, and R. Martínez-Sánchez, “Grain
refiner effect on the microstructure and mechanical properties of the A356 automotive wheels,” J. Mater. Eng. Perform., vol. 23, no. 2, pp.
581–587, 2014.
[11] B. Zhang, S. L. Cockcroft, D. M. Maijer, J. D. Zhu, and A. B. Phillion, “Casting defects in low-pressure die-cast aluminum alloy wheels,”
Jom, vol. 57, no. 11, pp. 36–43, 2005.
[12] M. V. Kevorkijan, “MMCs for automotive applications,” Am. Ceram. Soc. Bull., vol. 77, no. 12, pp. 53–59, 1998.
[13] S. W. Youn, C. G. Kang, and P. K. Seo, “Thermal fluid/solidification analysis of automobile part by horizontal squeeze casting process and
experimental evaluation,” J. Mater. Process. Technol., vol. 146, no. 3, pp. 294–302, 2004.
[15] Wu Shenqing and Li Jun, “Application of ceramic short fiber reinforced Al alloy matrix composites on piston for internal combustion
engines.”
[16] Schrader, George F, Elshennawy, Ahmad K, Doyle, Lawrence E, “Manufacturing processes and materials”, SME, p.186, ISBN .978-0-
87263-517-3.