This article introduces the paper "SYSTEM UNDERSTANDING OF HIGH PRESSURE DIE CASTING PROCESS AND DATA WITH MACHINE LEARNING APPLICATIONS".
Overview:
- Title: SYSTEM UNDERSTANDING OF HIGH PRESSURE DIE CASTING PROCESS AND DATA WITH MACHINE LEARNING APPLICATIONS
- Author: David J. Blondheim, Jr.
- Publication Year: Fall 2021
- Publishing Journal/Academic Society: Colorado State University (Dissertation)
- Keywords: Die casting, machine learning, systems engineering, Industry 4.0, data framework, unsupervised machine learning, anomaly detection, process control.
Research Background:
- Social/Academic Context of the Research Topic: Die casting is a complex manufacturing system widely used for producing near net shape castings. Despite its long history, a comprehensive systems engineering approach to define the process and utilize the data generated in each cycle is lacking. Existing research often focuses on a narrow scope of critical parameters within die castings.
- Limitations of Existing Research: Narrow focus on limited data parameters in die casting research has led to limited success and applicability of machine learning in production foundries. Process optimization literature often uses poorly chosen experimental design inputs and ranges, and lacks complexity of real-world die casting applications for quality prediction.
- Necessity of the Research: There is a need for a systems engineering perspective to understand the die casting process and data comprehensively. A data framework is necessary to manage the large volume of data generated and identify meaningful applications of machine learning to improve process control and quality in die casting.
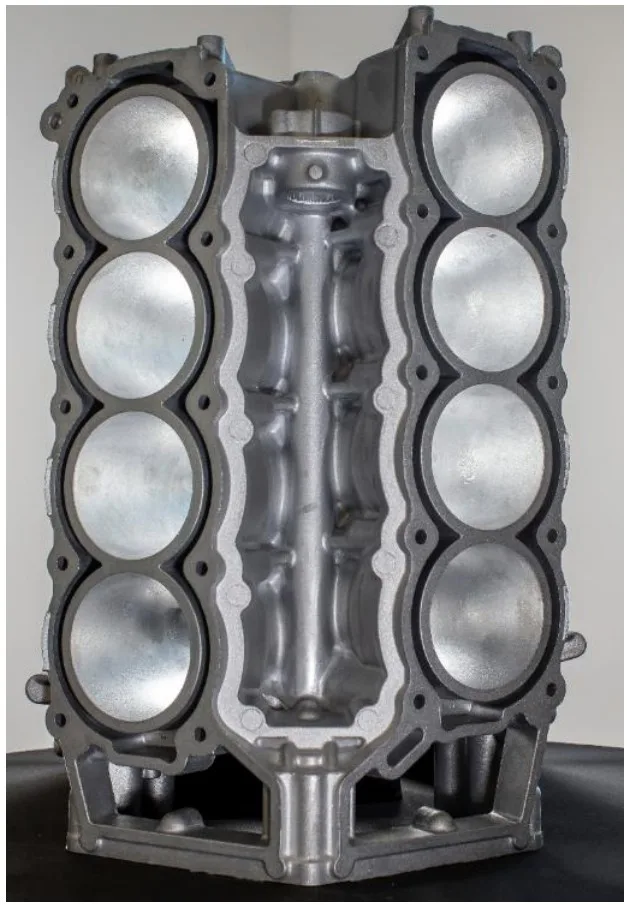
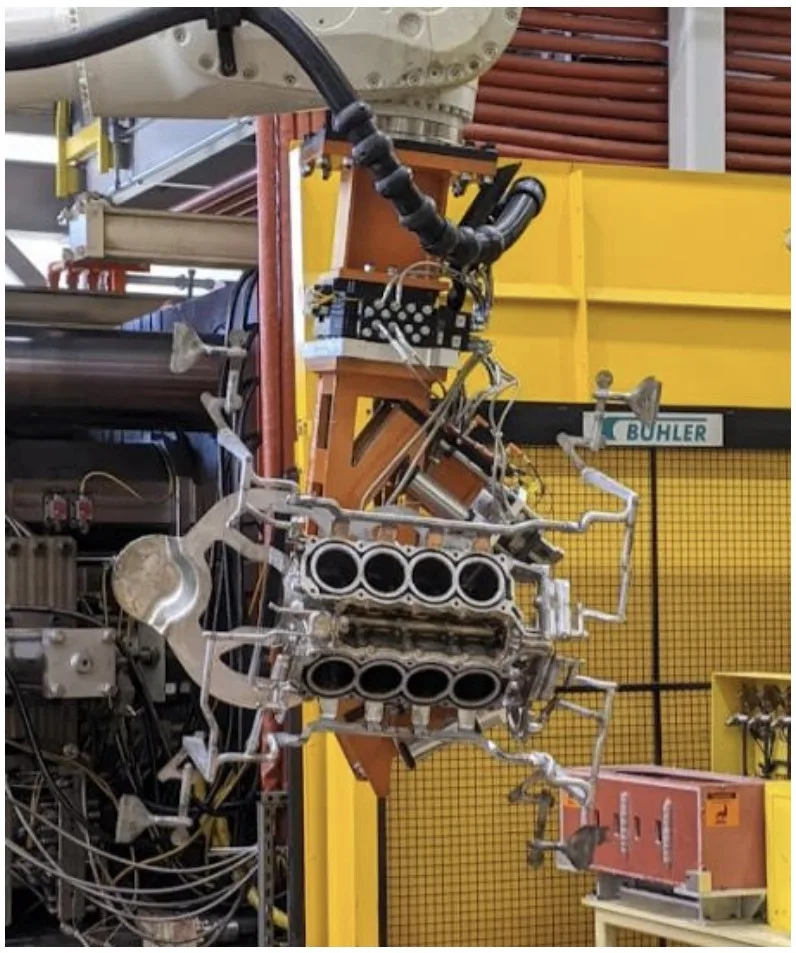
Research Purpose and Research Questions:
- Research Purpose: To investigate the die casting process from a systems engineering perspective and demonstrate meaningful ways to apply machine learning to enhance system understanding, process control, and data utilization in the die casting industry.
- Key Research Questions:
- How can a systems engineering approach define the critical processes and data framework in die casting?
- How can machine learning be meaningfully applied to the complex die casting system to improve process control and quality?
- Can unsupervised machine learning provide value by automatically monitoring data and identifying anomalies in die casting?
- Research Hypotheses: Unsupervised machine learning, applied within a systems engineering framework for die casting, can provide value by automatically monitoring data and identifying anomalies, leading to process control improvement and better utilization of data generated by the die casting process.
Research Methodology
- Research Design: Dissertation research involving literature review, systems engineering analysis, case studies, and experimental studies.
- Data Collection Method: Data collected from production die casting processes, including equipment settings, time-series data from injection and other systems, thermal images, and casting quality data.
- Analysis Method: Systems engineering approach to define the die casting system and data framework. Statistical analysis (Wilcoxon Signed Rank Test) for experimental data. Machine learning algorithms including k-means clustering and autoencoders for case studies.
- Research Subjects and Scope: High pressure die casting process, data generated from die casting operations, case studies conducted at Mercury Marine.
Main Research Results:
- Key Research Results:
- Die casting process is defined as a complex system with network structure, adaptive, self-organizing, and nonlinear characteristics.
- A comprehensive data framework for die casting is developed, categorizing data into Design Parameter Data, Input Settings Data, Output – Discrete Data, Output – Time-Series Data, and Cycle Time Analysis Data.
- Data volume in die casting is several orders of magnitude larger than what is currently used in the industry.
- Unsupervised machine learning, particularly anomaly detection using autoencoders, provides value in monitoring die casting processes and identifying anomalies.
- Case studies demonstrate the application of unsupervised machine learning for process monitoring, anomaly detection in thermal images and time-series data, and process optimization.
- Stochastic nature of porosity formation is confirmed, and limitations of traditional supervised machine learning approaches for quality prediction in die casting are highlighted.
- Statistical/Qualitative Analysis Results: Wilcoxon Signed Rank Test showed no statistically significant difference in critical injection parameters between best and worst samples, indicating stochastic nature of porosity. Case studies demonstrated the effectiveness of unsupervised machine learning in anomaly detection and process understanding.
- Data Interpretation: The complexity of die casting and the stochastic nature of defect formation necessitate a shift from traditional supervised machine learning for quality prediction to unsupervised methods for process monitoring and anomaly detection. A systems engineering approach and comprehensive data utilization are crucial for effective application of machine learning in die casting.
- Figure Name List:
- Figure 1: Example die cast cell layout
- Figure 2: Example V8 engine block die casting
- Figure 3: Metal delivery: dosing furnace (left), 2-axis ladle (center), and 7-axis robot ladle (right)
- Figure 4: Die and chamber diagram
- Figure 5: Waves entrap air when slow shot speed is too slow
- Figure 6: Turbulent waves form when slow shot speed is too fast
- Figure 7: Correct wave formation allows all air to escape from the chamber
- Figure 8: Example shot injection velocity and pressure graph
- Figure 9: Die shown with hydraulic cylinders and slides in (left) and out (right) positions
- Figure 10: Die example with ejection pins in the out position
- Figure 11: Hot water unit (left) and jet cool unit (right) in production
- Figure 12: Spray systems: 2-axis manifold (left) and 6-axis robot (right)
- Figure 13: Key nomenclature of features within the die
- Figure 14: Biscuity, runner, gating, and venting system on casting
- Figure 15: Simulated metal fluid flow during injection
- Figure 16: Complex thermal cooling lines in die design
- Figure 17: Example of hot water and jet cool lines on a moving half of a large die
- Figure 18: Complexity in Die Casting
- Figure 19: Systems engineering “V” Diagram based on [60]
- Figure 20: Decomposition of hierarchical systems
- Figure 21: Die casting context diagram
- Figure 22: Tooling Management system diagram
- Figure 23: Generic closed-loop feedback system
- Figure 24: Example programmed set points for shot profile
- Figure 25: Example shot profile output
- Figure 26: Thermal imaging camera in production die cast environment
- Figure 27: Example thermal image on stationary half (left) and moving half (right)
- Figure 28: Example extraction cell with multiple robots and post-die cast processing
- Figure 29: Sawed sample casting for X-ray
- Figure 30: Example X-ray gradings 1 through 3
- Figure 31: 9 best samples (Grade 1)
- Figure 32: 9 worst samples (Grade 3)
- Figure 33: Simulated results of predicted porosity zone
- Figure 34: Volume of liquid in the sample area as predicted by MAGMA
- Figure 35: Example of overlapping data space
- Figure 36: Examples of HPDC porosity
- Figure 37: Sample X-Ray images of porosity
- Figure 38: Classification issue due to binary acceptance specifications example
- Figure 39: Example of simulated predicted porosity zone
- Figure 40: Sequential castings showing stochastic porosity formation
- Figure 41: Classification issue due to stochastic defect formation example
- Figure 42: Classification issue due to secondary process variation example
- Figure 43: Combination of elements example
- Figure 44: Bias-Variance tradeoff graph
- Figure 45: Traditional confusion matrix based on counts
- Figure 46: Normalized confusion matrix based on percentage
- Figure 47: Example calculations on traditional and normalized confusion matrices
- Figure 48: Example of different accuracy calculations
- Figure 49: Bias-Variance tradeoff graph with Critical Error Threshold
- Figure 50: Increased inherent error
- Figure 51: Increased bias
- Figure 52: Artificial intelligence, machine learning, and deep learning hierarchy
- Figure 53: Example 2-class confusion matrix
- Figure 54: Six challenges of machine learning in die casting
- Figure 55: Example 2D laser barcode on a die casting
- Figure 56: Hughes Phenomenon visually depicted
- Figure 57: Generic IT architecture for machine learning implementation
- Figure 58: Reducing scrap rates drives a need for increased accuracy and a lower CET target
- Figure 59: Porosity defect uncovered after machining
- Figure 60: Gate break-in defect
- Figure 61: Thermal imaging system installed on die cast machine
- Figure 62: Thermal image example with data conversion
- Figure 63: 2D barcode and serial number example
- Figure 64: Intensification Pressure data over experimental run
- Figure 65: Example of a linear regression model
- Figure 66: Example of an overfitted model
- Figure 67: Example of a neural network structure
- Figure 68: Example of a SVM classification in two dimensions
- Figure 69: Elbow Method for determining number of clusters
- Figure 70: Cluster Assignment with 7 Clusters
- Figure 71: Boxplot and Individual Plots of Average Slow Shot Velocity and Intensification Pressure
- Figure 72: Matrix scatter plot of key parameters by clusters
- Figure 73: Matrix scatter plot of key parameters by result (Good v. Bad)
- Figure 74: Scatter plots of intensified pressure versus average slow shot velocity
- Figure 75: Boxplot and Individual Plots of Average Slow Shot Velocity and Intensification Pressure comparing clusters with historical scrap data
- Figure 76: Three-step algorithm for anomaly detection
- Figure 77: Visualization of steady state image stack with mean and standard deviation matrices
- Figure 78: Mathematical code for different anomaly identification per color layer
- Figure 79: Thermal image camera system install on die cast machine [45]
- Figure 80: Thermal image temperature matrix and grayscale image
- Figure 81: Pre-crop versus post-crop thermal image (stationary half)
- Figure 82: Comparison of scaled pixel thermal images (moving half)
- Figure 83: F-Scores per cluster size
- Figure 84: Sequence of cluster assignments
- Figure 85: Time-based sequence of cluster assignments
- Figure 86: Mean and standard deviation images for cluster #1
- Figure 87: Histogram of mean image of cluster #1 versus cluster #3
- Figure 88: Anomaly detection on warmup shot
- Figure 89: Anomaly detection on die with water turned off
- Figure 90: Mean and stand deviation images of two process settings
- Figure 91: Typical range point settings for slow and fast shot velocities
- Figure 92: Four example profiles with the same average
- Figure 93: Anomaly detection using Standard Cosine Similarity
- Figure 94: Anomaly detection using Modified Cosine Similarity
- Figure 95: Distribution of Cosine Similarity calculation values
- Figure 96: Home screen of Azure web page showing multiple machines running
- Figure 97: Detailed shot screen with anomalous shot detected
- Figure 98: Set points for shot profiles
- Figure 99: Changing setpoints on a ramped slow shot velocity profile
- Figure 100: Examples of identical slow shot velocity averages with different profiles
- Figure 101: Simple neural network
- Figure 102: Deep learning example
- Figure 103: Autoencoder components
- Figure 104: Example MNIST handwritten digits
- Figure 105: Plot raster example
- Figure 106: Data preparation
- Figure 107: Digit predictions per example
- Figure 108: Example 5s from training data set
- Figure 109: Mean absolute error (MAE) based on autoencoder trained on 5s only
- Figure 110: Visual and error examples from test data
- Figure 111: 5s identified as anomalies by autoencoder
- Figure 112: Example spray flow rate profile
- Figure 113: Raw SQL data storage examples
- Figure 114: Training data clusters
- Figure 115: Original input and recreated profile
- Figure 116: MAE of test samples
- Figure 117: Illustrations of anomalies
- Figure 118: Theoretical anomaly detection profile graphs
- Figure 119: Specific gravity measurements and X-ray images on select BoB and WoW castings
- Figure 120: Example furnace temperature data
- Figure 121: Slides author presented at November 2019 NADCA Chapter 12 meeting
- Figure 122: CT scan of porosity in casting from Chapter 3 study
Conclusion and Discussion:
- Summary of Main Results: This dissertation establishes die casting as a complex system requiring a systems engineering approach and highlights the limitations of traditional machine learning applications focused solely on quality prediction. It demonstrates the value of unsupervised machine learning for anomaly detection and process control, utilizing a comprehensive data framework. The research emphasizes the stochastic nature of porosity and the challenges of defect classification due to human factors and process variations.
- Academic Significance of the Research: This work bridges the gap between theoretical machine learning solutions and practical applications in complex manufacturing environments like die casting. It contributes to the understanding of complexity theory in manufacturing systems and provides a novel data framework for die casting. The research also introduces the concept of Critical Error Threshold (CET) for evaluating the financial viability of machine learning applications.
- Practical Implications: The findings suggest a shift in focus from supervised quality prediction to unsupervised anomaly detection for immediate value in die casting. The developed data framework and anomaly detection algorithms offer practical tools for foundries to improve process control, reduce downtime, and better utilize the vast amounts of data generated. The case studies provide concrete examples of successful machine learning implementation in a production setting.
- Limitations of the Research: The research primarily focuses on unsupervised machine learning and anomaly detection. Further research is needed to explore the full potential of supervised machine learning with improved data quality and comprehensive data sets. The case studies are limited to a specific die casting process and foundry, and further validation across different processes and foundries is needed. The complexity of die casting and the stochastic nature of porosity formation pose inherent limitations to achieving perfect predictability.
Future Follow-up Research:
- Directions for Follow-up Research:
- Industrialization and implementation of the developed anomaly detection algorithm on the shop floor.
- Further research into feature importance to identify critical process parameters influencing casting quality.
- Investigation of density in predicted porosity zones and its correlation with casting quality.
- Exploration of recurrent neural networks and other advanced machine learning techniques to capture time-dependent data characteristics.
- Development of improved methods for data collection, traceability, and ground truth data acquisition, particularly for porosity detection using CT scanning.
- Further investigation into the concept of Critical Error Threshold and its application in various manufacturing settings.
- Areas Requiring Further Exploration:
- Reducing inherent error by incorporating more comprehensive data and process understanding into machine learning models.
- Mitigating bias by improving defect classification accuracy through enhanced inspection methods and operator training.
- Addressing the challenges of data imbalance and limited data sets in die casting.
- Overcoming non-technical barriers to machine learning adoption in manufacturing, such as cultural resistance and skillset gaps.
References:
- [1] B. Andresen, Die Casting Engineering: A Hydraulic, Thermal, and Mechanical Process. New York: Marcel Dekker, 2005.
- [2] D. Blondheim, Jr., “Artificial Intelligence, Machine Learning, and Data Analytics: Understanding the Concepts to Find Value in Die Casting Data,” presented at the NADCA Executive Conference, Clearwater, Florida, Feb. 25, 2020.
- [3] J. Folk, “U.S. Aluminum Casting Industry - 2019,” Die Casting Engineer, vol. July 2019, pp. 16– 19, 2019.
- [Online]. Available: https://www.diecasting.org/archive/dce/71916.pdf
- [4] S. Midson, “Report on the 2014 Die Casting Benchmarking Survey Part 2 of 3: Operations,” in Report on the 2014 Die Casting Benchmarking Survey, North American Die Casting Association, 2014.
- [5] T. Wuest, D. Weimer, C. Irgens, and K.-D. Thoben, “Machine learning in manufacturing: advantages, challenges, and applications,” Production & Manufacturing Research, vol. 4, no. 1, pp. 23–45, Jan. 2016, doi: 10.1080/21693277.2016.1192517.
- [6] L. Baier, F. Johren, and S. Seebacher, “CHALLENGES IN THE DEPLOYMENT AND OPERATION OF MACHINE LEARNING IN PRACTICE,” in In Proceedings of the 27th European Conference on Information Systems (ECIS), Stockholm & Uppsala, Sweden, Jun. 2019, p. 16.
- [Online]. Available: https://aisel.aisnet.org/ecis2019_rp/163
- [7] N. Sun, A. Kopper, R. Karkare, R. C. Paffenroth, and D. Apelian, “Machine Learning Pathway for Harnessing Knowledge and Data in Material Processing,” Inter Metalcast, Sep. 2020, doi: 10.1007/s40962-020-00506-2.
- [8] J. Landry, J. Maltais, J.-M. Deschênes, M. Petro, X. Godmaire, and A. Fraser, “Inline Integration of Shotblast Resistant Laser Marking in a Die Cast Cell,” Indianapolis, IN, 2018, vol. T18-123.
- [Online]. Available: https://www.diecasting.org/archive/transactions/T18-123.pdf
- [9] D. Blondheim, Jr., “Unsupervised Machine Learning and Statistical Anomaly Detection Applied to Thermal Images,” Indianapolis, IN, Oct. 2018, vol. T18-071.
- [Online]. Available: http://www.diecasting.org/archive/transactions/T18-071.pdf
- [10] “2018: Die Casting Award Winners,” Die Casting Engineer, p. 61, Sep. 2018.
- [Online]. Available: https://www.diecasting.org/docs/dce/issues/2018DCESep.pdf
- [11] S. Alvarez, “Tesla Model Y single-piece rear casts spotted in Fremont factory,” Sep. 10, 2020. https://www.teslarati.com/tesla-model-y-unibody-casts-sighting-video/ (accessed Sep. 28, 2020).
- [12] Product Design for Die Casting E-606, Sixth Edition., vol. E-606. North American Die Casting Association, 2009.
- [13] H. H. Doehler, Die Casting. New York: McGraw-Hill Book Company, 1951.
- [14] NADCA Product Specification Standards for Die Casting, 10th Edition. Arlington Heights, IL: North American Die Casting Association, 2018.
- [15] E. A. Herman and J. S. Kirkman, Designing Die Casting Dies Series - E-506. Arlington Heights, IL: North American Die Casting Association, 2011.
- [16] “Aluminum Alloys 101,” Oct. 13, 2020. https://www.mercalloy.com/aluminum-alloys-101/ (accessed Oct. 13, 2020).
- [17] K. Ch. Apparao and A. K. Birru, “Optimization of Die casting process based on Taguchi approach,” Materials Today: Proceedings, vol. 4, no. 2, pp. 1852–1859, 2017, doi: 10.1016/j.matpr.2017.02.029.
- [18] Q.-C. Hsu and A. T. Do, “Minimum Porosity Formation in Pressure Die Casting by Taguchi Method,” Mathematical Problems in Engineering, vol. 2013, pp. 1–9, 2013, doi: 10.1155/2013/920865.
- [19] S. Balasubramaniam, S. Kannan, and R. Shivpuri, “Improving the Quality in Die Casting Production Using Statistical Analysis Procedures,” presented at the 1999 NADCA World of Die Casting, Cleveland, OH, 1999.
- [Online]. Available: http://www.diecasting.org/archive/transactions/T99-071.pdf
- [20] Q. Han, D. McClure, D. Wood, and D. Yang, “Statistical Analysis of the Effect of Operational Parameters on the Scrap Rates of Crossmember Casting,” Die Casting Engineer, no. November 2017, pp. 38–43, 2017.
- [Online]. Available: http://www.diecasting.org/archive/dce/111738.pdf
- [21] V. D. Tsoukalas, “Optimization of porosity formation in AlSi9Cu3 pressure die castings using genetic algorithm analysis,” Materials & Design, vol. 29, no. 10, pp. 2027–2033, Dec. 2008, doi: 10.1016/j.matdes.2008.04.016.
- [22] J. Zheng, Q. Wang, P. Zhao, and C. Wu, “Optimization of high-pressure die-casting process parameters using artificial neural network,” Int J Adv Manuf Technol, vol. 44, no. 7–8, pp. 667–674, Oct. 2009, doi: 10.1007/s00170-008-1886-6.
- [23] E. A. Herman, Die Casting Process Control E-410. North American Die Casting Association, 2012.
- [24] I. Vuksanović Herceg, V. Kuč, V. M. Mijušković, and T. Herceg, “Challenges and Driving Forces for Industry 4.0 Implementation,” Sustainability, vol. 12, no. 10, p. 4208, May 2020, doi: 10.3390/su12104208.
- [25] A. Raj, G. Dwivedi, A. Sharma, A. B. Lopes de Sousa Jabbour, and S. Rajak, “Barriers to the adoption of industry 4.0 technologies in the manufacturing sector: An inter-country comparative perspective,” International Journal of Production Economics, vol. 224, p. 107546, Jun. 2020, doi: 10.1016/j.ijpe.2019.107546.
- [26] L. S. Dalenogare, G. B. Benitez, N. F. Ayala, and A. G. Frank, “The expected contribution of Industry 4.0 technologies for industrial performance,” International Journal of Production Economics, vol. 204, pp. 383–394, Oct. 2018, doi: 10.1016/j.ijpe.2018.08.019.
- [27] A. Mayr et al., “Machine Learning in Production – Potentials, Challenges and Exemplary Applications,” Procedia CIRP, vol. 86, pp. 49–54, 2019, doi: 10.1016/j.procir.2020.01.035.
- [28] M. Bertolini, D. Mezzogori, M. Neroni, and F. Zammori, “Machine Learning for industrial applications: A comprehensive literature review,” Expert Systems with Applications, vol. 175, p. 114820, Aug. 2021, doi: 10.1016/j.eswa.2021.114820.
- [29] R. Kenett, I. Yahav, and A. Zonnenshain, “Chapter 13: Analytics as an Enabler of Advanced Manufacturing,” in Systems Engineering in the Fourth Industrial Revolution: Big Data, Novel Technologies, and Modern Systems Engineering, First., John Wiley & Sons Inc, 2020, pp. 321–344.
- [30] C. Hoyer, I. Gunawan, and C. H. Reaiche, “The Implementation of Industry 4.0 - A Systematic Literature Review of the Key Factors,” Syst Res Behav Sci, vol. 37, no. 4, pp. 557–578, Jul. 2020, doi: 10.1002/sres.2701.
- [31] S. Pfeiffer, “The Vision of ‘Industrie 4.0’ in the Making—a Case of Future Told, Tamed, and Traded,” Nanoethics, vol. 11, no. 1, pp. 107–121, Apr. 2017, doi: 10.1007/s11569-016-0280-3.
- [32] S. Wang, J. Wan, D. Zhang, D. Li, and C. Zhang, “Towards smart factory for industry 4.0: a selforganized multi-agent system with big data based feedback and coordination,” Computer Networks, vol. 101, pp. 158–168, Jun. 2016, doi: 10.1016/j.comnet.2015.12.017.
- [33] V. Roblek, M. Meško, and A. Krapež, “A Complex View of Industry 4.0,” SAGE Open, vol. 6, no. 2, p. 215824401665398, Apr. 2016, doi: 10.1177/2158244016653987.
- [34] “Industry 4.0 after the initial hype. Where manufacturers are finding value and how they can best capture it.” McKinsey Digital, 2016.
- [Online]. Available: https://www.mckinsey.com/~/media/mckinsey/business%20functions/mckinsey%20digital/our%20i nsights/getting%20the%20most%20out%20of%20industry%204%200/mckinsey_industry_40_2016 .ashx
- [35] “German Industry 4.0 Index 2018.” Staufen AG, 2018. Accessed: Aug. 21, 2021.
- [Online]. Available: https://www.staufen.ag/fileadmin/HQ/02-Company/05-Media/2-Studies/STAUFEN.- Study-Industry-4.0-Index-2018-Web-DE-en.pdf
- [36] “German Industry 4.0 Index 2019.” Staufen AG, 2019. Accessed: Aug. 21, 2021.
- [Online]. Available: https://www.staufen.ag/fileadmin/HQ/02-Company/05-Media/2-Studies/STAUFEN.- Study-Industry-4-0-index-2019-en_.pdf
- [37] L. Bonekamp and M. Sure, “Consequences of Industry 4.0 on Human Labour and Work Organisation,” Journal of Business and Media Psychology, vol. 6, no. 1, pp. 33–40, 2015.
- [38] A. G. Frank, L. S. Dalenogare, and N. F. Ayala, “Industry 4.0 technologies: Implementation patterns in manufacturing companies,” International Journal of Production Economics, vol. 210, pp. 15–26, Apr. 2019, doi: 10.1016/j.ijpe.2019.01.004.
- [39] S. B. Gershwin, “The future of manufacturing systems engineering,” International Journal of Production Research, vol. 56, no. 1–2, pp. 224–237, Jan. 2018, doi: 10.1080/00207543.2017.1395491.
- [40] R. A. Miller, “Gate Speed, Fraction Solid, and the Effect on Mechanical Properties,” Indianapolis, IN, Oct. 2018, vol. T18-042.
- [Online]. Available: https://www.diecasting.org/archive/transactions/T18-042.pdf
- [41] H. Bramann, L. Leineweber, and J. C. Sturm, “Innovative Product Design and Robust Process Layout in Die Casting with Autonomous Engineering,” Indianapolis, IN, Oct. 2018, vol. T18-093.
- [Online]. Available: https://www.diecasting.org/archive/transactions/T18-093.pdf
- [42] M. Hartlieb and C. Raone, “Optimization of the Die Thermal Monitoring and Die Lubrication Process,” Indianapolis, IN, Oct. 2018, vol. T18-023.
- [Online]. Available: https://www.diecasting.org/archive/transactions/T18-023.pdf
- [43] M. Ognianov, “Influence of the Cooling Rate on the Microstructure and Mechanical Properties in 5wt.% Cr Martensitic Steels,” Indianapolis, IN, Oct. 2018, vol. T18-013.
- [Online]. Available: https://www.diecasting.org/archive/transactions/T18-013.pdf
- [44] R. A. Miller, “Multi-time Scale Systems and Quasi Equilibrium,” 2016, vol. T16-082.
- [Online]. Available: https://www.diecasting.org/archive/transactions/T16-082.pdf
- [45] D. Blondheim, Jr., “Initial Development of Machine Learning Algorithms to Predict Casting Defects in High-Pressure Die Casting,” Atlanta, GA, Sep. 2017, vol. T17-073.
- [Online]. Available: http://www.diecasting.org/archive/transactions/T17-073.pdf
- [46] E. Herman, “The Net Shape Paradox (Why Die Casting Sometimes Seems Mysterious),” Die Casting Engineer, vol. November 2018, pp. 20–22, Nov. 2018.
- [Online]. Available: https://www.diecasting.org/archive/dce/111820.pdf
- [47] M. Mitchell, Complexity: a guided tour, 1. iss. as an paperback. New York, NY: Oxford University Press, 2011.
- [48] N. F. Johnson, Simply complexity: a clear guide to complexity theory. Oneworld Publications, 2009. Accessed: Aug. 22, 2021.
- [Online]. Available: http://public.ebookcentral.proquest.com/choice/publicfullrecord.aspx?p=1792154
- [49] H. G. Sillitto, “On Systems Architects and Systems Architecting: some thoughts on explaining and improving the art and science of systems architecting,” INCOSE International Symposium, vol. 19, no. 1, pp. 970–985, Jul. 2009, doi: 10.1002/j.2334-5837.2009.tb00995.x.
- [50] V. R. Vemuri, Modeling of complex systems: an introduction. New York: Academic Press, 1978.
- [51] K. Warren, “Chaos Theory and Complexity Theory,” in Encyclopedia of Social Work, NASW Press and Oxford University Press, 2013. doi: 10.1093/acrefore/9780199975839.013.45.
- [52] F. Heylighen, “Complexity and Self-organization,” in Encyclopedia of Library and Informatoin Sciences, Bates&Maack., Taylor & Francis, 2018.
- [53] L. M. Jiji, Heat Conduction. Berlin, Heidelberg: Springer Berlin Heidelberg, 2009. doi: 10.1007/978-3-642-01267-9.
- [54] A. Kossiakoff, Ed., Systems engineering: principles and practice, 2nd ed. Hoboken, N.J: WileyInterscience, 2011.
- [55] C. S. Wasson, System engineering analysis, design, and development: concepts, principles, and practices, Second edition. Hoboken, New Jersey: John Wiley & Sons Inc, 2016.
- [56] D. D. Walden, G. J. Roedler, K. Forsberg, R. D. Hamelin, T. M. Shortell, and International Council on Systems Engineering, Eds., Systems engineering handbook: a guide for system life cycle processes and activities, 4th edition. Hoboken, New Jersey: Wiley, 2015.
- [57] USA, Ed., Systems engineering handbook. Washington, D.C: National Aeronautics and Space Administration, 2007.
- [58] A. Schneider, C. Wickert, and E. Marti, “Reducing Complexity by Creating Complexity: A Systems Theory Perspective on How Organizations Respond to Their Environments: Reducing Complexity by Creating Complexity,” Jour. of Manage. Stud., vol. 54, no. 2, pp. 182–208, Mar. 2017, doi: 10.1111/joms.12206.
- [59] “Systems Engineering Definition,” Default. https://www.incose.org/about-systemsengineering/system-and-se-definition/systems-engineering-definition (accessed Aug. 29, 2021).
- [60] National ITS Architecture Team, “Systems Engineering for Intelligent Transportation Systems: An Introduction for Transportation Professionals,” Department of Transportation, Office of Operations, FHWA-HOP-07-069, Jan. 2007. Accessed: Aug. 30, 2021.
- [Online]. Available: https://ops.fhwa.dot.gov/publications/seitsguide/
- [61] M. Mennenga, F. Cerdas, S. Thiede, and C. Herrmann, “Exploring the Opportunities of System of Systems Engineering to Complement Sustainable Manufacturing and Life Cycle Engineering,” Procedia CIRP, vol. 80, pp. 637–642, 2019, doi: 10.1016/j.procir.2019.01.026.
- [62] R. Sturdivant, “Application of Systems Engineering to Complex Systems and System of Systems,” Colorado State University, 2017.
- [63] K. E. Boulding, “General Systems Theory - The Skeleton of Science,” Management Science, vol. 2, no. 3, pp. 197–208, Apr. 1956.
- [64] R. L. Ackoff, “Towards a System of Systems Concepts,” Management Science, vol. 17, no. 11, pp. 661–671, Jul. 1971, doi: 10.1287/mnsc.17.11.661.
- [65] Control of complex systems: theory and applications, 1st edition. Cambridge, MA: Elsevier, 2016.
- [66] K. Åström, P. Albertos, M. Blanke, A. Isidori, W. Schaufelberger, and R. Sanz, Eds., Control of Complex Systems. London: Springer London, 2001. doi: 10.1007/978-1-4471-0349-3.
- [67] “Mercury Marine’s new high-pressure die casting machine is now the largest in North America,” Mercury Marine. http://www.mercurymarine.com/en/us/news/mercury-marines-new-high-pressuredie-casting-machine-is-now-the-largest-in-north-america/ (accessed Aug. 31, 2021).
- [68] “Tesla Giga Press Die Casting Machine - World’s Largest Die Cast Machine,” Sunrise Metal - Aluminium Die Casting Expert. https://www.sunrise-metal.com/tesla-giga-press-die-castingmachine/ (accessed Aug. 31, 2021).
- [69] Idra Group, IDRA GROUP | Flash News - Giga Press (Riccardo Ferrario), (Mar. 18, 2021). Accessed: Aug. 31, 2021.
- [Online Video]. Available: https://www.youtube.com/watch?v=o2Mi84wCRg8
- [70] M. L. Cox, R. R. Fish, and J. P. Wronowicz, PQ2 - Machine Power and Die Compatibility. Arlington Heights, IL: North American Die Casting Association.
- [71] J. Scott. Kirkman, Thermal Design & Control of DIe Casting Dies, Publication #415. Arlington Heights, IL: North American Die Casting Association, 2010.
- [72] D. J. Armentrout, J. Brevick, and T. Altan, “Investigation and Reduction of Air Entrapment in the Shot Sleeve of a Cold Chamber Die Casting Machine (A Progress Report),” The Ohio State University, NSF Engineering Research Center for Net Shape Manufacturing, ERC/NSM-C-92-61, Oct. 1992.
- [Online]. Available: https://www.diecasting.org/archive/erc/ERC-92-61.pdf
- [73] D. J. Armentrout, J. Brevick, and T. Altan, “Investigation of the Slow Shot Phase to Minimize Entrapped Air in Cold Chamber Die Casting,” The Ohio State University, NSF Engineering Research Center for Net Shape Manufacturing, ERC/NSM-C-93-19, Jun. 1993.
- [Online]. Available: https://www.diecasting.org/archive/erc/ERC-93-19.pdf
- [74] M. C. Thome and J. Brevick, “Optimal Slow Shot Profiles in Cold Chamber Die Casting,” The Ohio State University, NSF Engineering Research Center for Net Shape Manufacturing, ERC/NSM-C95-14, Dec. 1993.
- [Online]. Available: https://www.diecasting.org/archive/erc/ERC-95-14.pdf
- [75] M. C. Thome, J. Brevick, and Y.-L. Chu, “Modeling the Effect of Shot Plunger Acceleration on Wave Formation and Air Entrapment in Cold Chamber DIe Casting (A Progress Report),” The Ohio State University, NSF Engineering Research Center for Net Shape Manufacturing, ERC/NSM-C94-04, Dec. 1993.
- [Online]. Available: https://www.diecasting.org/archive/erc/ERC-94-04.pdf
- [76] M. Thome and J. R. Brevick, “Optimal Slow Shot Velocity Profiles For Cold Chamber Die Casting,” Indianapolis, IN, Oct. 1995, pp. 53–59.
- [Online]. Available: http://www.diecasting.org/archive/transactions/T95-024.pdf
- [77] A. V. Deshpande, “Evaluation of Slow Shot Acceleration on Gas Porosity in Medium Sized Diecast Components,” Master of Science, The Ohio State University, 1999.
- [Online]. Available: https://www.diecasting.org/archive/erc/ERC-99-01.pdf
- [78] G. V. Sheffer, “Direct Recording In The Die Casting Industry,” North American Die Casting Association Archive, 64–040d, 1964.
- [Online]. Available: http://www.diecasting.org/archive/reports/64-040d.pdf
- [79] L. A. Bartling, “Recording instrumentation a valuable die casting tool,” North American Die Casting Association Archive, 66–201, 1966.
- [Online]. Available: https://www.diecasting.org/archive/reports/66-201.pdf
- [80] R. Moore, “Monitoring the Die-Casting Process,” North American Die Casting Association Archive, 69–011, 1969.
- [Online]. Available: https://www.diecasting.org/archive/reports/69-011.pdf
- [81] J. R. Vann, “A Building Block Approach to Shot End Monitoring and Control,” Die Casting Engineer, no. September-October 1981, pp. 15–26, 1981.
- [Online]. Available: https://www.diecasting.org/archive/dce/98116.pdf
- [82] J. R. Vann, “Automatic Shot Control with Computer Monitoring and Programming for Increased Productivity in Die Casting,” Die Casting Engineer, no. March/April 1985, pp. 28–40, 1985.
- [Online]. Available: https://www.diecasting.org/archive/dce/38528.pdf
- [83] L. X. Kong, F. H. She, W. M. Gao, S. Nahavandi, and P. D. Hodgson, “Integrated optimization system for high pressure die casting processes,” Journal of Materials Processing Technology, vol. 201, no. 1–3, pp. 629–634, May 2008, doi: 10.1016/j.jmatprotec.2007.11.250.
- [84] I. Pastor-Lopez, I. Santos, A. Santamaria-Ibirika, M. Salazar, J. de-la-Pena-Sordo, and P. G. Bringas, “Machine-learning-based surface defect detection and categorisation in high-precision foundry,” in 2012 7th IEEE Conference on Industrial Electronics and Applications (ICIEA), Singapore, Singapore, Jul. 2012, pp. 1359–1364. doi: 10.1109/ICIEA.2012.6360934.
- [85] A. E. Kopper and D. Apelian, “Predicting Quality of Castings via Supervised Learning Method,” Inter Metalcast, Apr. 2021, doi: 10.1007/s40962-021-00606-7.
- [86] N. Gramegna and F. Bonollo, Smart Control and Cognitive System applied to the HPDC Foundry 4.0. MUSIC Consortium, 2016.
- [87] K. J. Rogers, G. Savage, and B. Cooper, “Experiments With a New Generation Shot Monitoring System in High-Pressure Die Casting,” Die Casting Engineer, no. January/February 2000, pp. 54– 62, 2000.
- [Online]. Available: https://www.diecasting.org/archive/dce/10054.pdf
- [88] G. Savage, M. Gershenzon, and K. J. Rogers, “The Role of Pressure in High Pressure Die Casting,” in NADCA Congress, Cincinnati, OH, Oct. 2001, vol. T01-053, pp. 151–156.
- [Online]. Available: https://www.diecasting.org/archive/transactions/T01-053.pdf
- [89] W. R. McAlister, “Continuous Process Monitoring Leads to Reduced Scrap and Shorter Cycle Times,” Die Casting Engineer, vol. July/August 1998, pp. 14–20, 1998.
- [Online]. Available: https://www.diecasting.org/archive/dce/79814.pdf
- [90] R. A. Miller and A. K. Monroe, “Benefits and Limitations of Time-varying Fast Shot Profiles,” Atlanta, GA, Sep. 2017, vol. T17-092.
- [Online]. Available: https://www.diecasting.org/archive/transactions/T17-092.pdf
- [91] M. Winkler, L. Kallien, and T. Feyertag, “Correlation between Process Parameters and Quality Characteristics in Aluminum High Pressure Die Casting,” vol. T15-022.
- [Online]. Available: http://www.diecasting.org/archive/transactions/T15-022.pdf
- [92] A. E. Kopper, “Knowledge Creation via Data Analytics in a High Pressure Die Casting Operation,” Worcester Polytechnic Institute, 2020.
- [Online]. Available: https://digital.wpi.edu/concern/etds/3484zk755
- [93] D. Blondheim, Jr. and A. Monroe, “Macro Porosity Formation - A Study in High Pressure Die Casting,” International Journal of Metalcasting, 2021, doi: https://doi.org/10.1007/s40962-021- 00602-x.
- [94] J. Brevick, Die Casting Porosity Guidebook. North American Die Casting Association, 2008.
- [95] W. G. Walkington, Die Casting Defects: Causes and Solutions. Rosemont, IL: North American Die Casting Association, 1997.
- [96] D. Twarog, “State of the Industry 2012.” North American Die Casting Association, Feb. 2012.
- [Online]. Available: https://www.diecasting.org/archive/dce/212online2.pdf
- [97] S. Viswanathan et al., Eds., “Shrinkage Porosity and Gas Porosity,” in Casting, ASM International, 2008, pp. 370–374. doi: 10.31399/asm.hb.v15.a0005222.
- [98] P. D. Lee, A. Chirazi, and D. See, “Modeling microporosity in aluminum–silicon alloys: a review,” Journal of Light Metals, vol. 1, no. 1, pp. 15–30, Feb. 2001, doi: 10.1016/S1471-5317(00)00003-1.
- [99] J. Campbell, Castings, 2. ed. Oxford: Butterworth-Heinemann, 2003.
- [100] E. Fiorese, F. Bonollo, G. Timelli, L. Arnberg, and E. Gariboldi, “New Classification of Defects and Imperfections for Aluminum Alloy Castings,” Inter Metalcast, vol. 9, no. 1, pp. 55–66, Jan. 2015, doi: 10.1007/BF03355602.
- [101] R. Atwood, “A Combined Cellular Automata and Diffusion Model for the Prediction of Porosity Formation During Solidification,” University of London, 2001.
- [102] I. Brill, B. Kappes, and S. Midson, “An Initial Evaluation of CT Scanning for Measuring and Characterizing Porosity in Aluminum Die Castings,” Indianapolis, IN, Oct. 2018, vol. T18-083.
- [Online]. Available: http://www.diecasting.org/archive/transactions/T18-083.pdf
- [103] M. Weidt, R. A. Hardin, C. Garb, J. Rosc, R. Brunner, and C. Beckermann, “Prediction of porosity characteristics of aluminium castings based on X-ray CT measurements,” International Journal of Cast Metals Research, pp. 1–19, May 2018, doi: 10.1080/13640461.2018.1467105.
- [104] C. Gu, Y. Lu, and A. A. Luo, “Three-dimensional visualization and quantification of microporosity in aluminum castings by X-ray micro-computed tomography,” Journal of Materials Science & Technology, vol. 65, pp. 99–107, Feb. 2021, doi: 10.1016/j.jmst.2020.03.088.
- [105] H. Cao, M. Hao, C. Shen, and P. Liang, “The influence of different vacuum degree on the porosity and mechanical properties of aluminum die casting,” Vacuum, vol. 146, pp. 278–281, Dec. 2017, doi: 10.1016/j.vacuum.2017.09.048.
- [106] X. P. Niu, B. H. Hu, I. Pinwill, and H. Li, “Vacuum assisted high pressure die casting of aluminium alloys,” Journal of Materials Processing Technology, vol. 105, no. 1–2, pp. 119–127, Sep. 2000, doi: 10.1016/S0924-0136(00)00545-8.
- [107] Y. Zhang, E. Lordan, K. Dou, S. Wang, and Z. Fan, “Influence of porosity characteristics on the variability in mechanical properties of high pressure die casting (HPDC) AlSi7MgMn alloys,” Journal of Manufacturing Processes, vol. 56, pp. 500–509, Aug. 2020, doi: 10.1016/j.jmapro.2020.04.071.
- [108] J. A. Dantzig and M. Rappaz, Solidification, 1 st. EPFL Press, 2009.
- [109] J. Huang and J. G. Conley, “Modeling of Microporosity Evolution During Solidification Processes,” in Review of Progress in Quantitative Nondestructive Evaluation, D. O. Thompson and D. E. Chimenti, Eds. Boston, MA: Springer US, 1998, pp. 1839–1846. doi: 10.1007/978-1-4615-5339- 7_238.
- [110] T. Liang, C. Mobley, and N. Tsumagari, “The Effects of Shot Delay Time on the Microstructures and Mechanical Properties of a Die Cast Aluminum Alloy,” presented at the Die Casting Toward The Future, Rosemont, IL, Oct. 2002.
- [Online]. Available: https://www.diecasting.org/archive/transactions/T02-053.pdf
- [111] B. Zhang, S. L. Cockcroft, D. M. Maijer, J. D. Zhu, and A. B. Phillion, “Casting defects in lowpressure die-cast aluminum alloy wheels,” JOM, vol. 57, no. 11, pp. 36–43, Nov. 2005, doi: 10.1007/s11837-005-0025-1.
- [112] K. D. Carlson and C. Beckermann, “Prediction of Shrinkage Pore Volume Fraction Using a Dimensionless Niyama Criterion,” Metall and Mat Trans A, vol. 40, no. 1, pp. 163–175, Jan. 2009, doi: 10.1007/s11661-008-9715-y.
- [113] G. K. Sigworth, “Shrinkage, Feeding and Riser Design,” AFS Transactoins 2014, vol. 14–002, pp. 25–36, 2014.
- [114] M. Shabani and A. Mazahery, “Prediction of Mechanical Properties of Cast A356 Alloy as a Function of Microstructure and Cooling Rate,” Archives of Metallurgy and Materials, vol. 56, no. 3, Jan. 2011, doi: 10.2478/v10172-011-0073-1.
- [115] M. Easton, C. Davidson, and D. St John, “Effect of Alloy Composition on the Dendrite Arm Spacing of Multicomponent Aluminum Alloys,” Metall and Mat Trans A, vol. 41, no. 6, pp. 1528– 1538, Jun. 2010, doi: 10.1007/s11661-010-0183-9.
- [116] J. Cho and C. Kim, “THE RELATIONSHIP BETWEEN DENDRITE ARM SPACING AND COOLING RATE OF Al-Si CASTING ALLOYS IN HIGH PRESSURE DIE CASTING,” InternationalJournal ofMetalcasting, vol. 8, no. 1, pp. 49–55, 2014, doi: https://doi.org/10.1007/BF03355571.
- [117] “SRE MAX,” Bosello High Technology , a ZEISS company. https://bosello.eu/products/sre-max/ (accessed Dec. 29, 2020).
- [118] “Phoenix Vtomex C | 3D CT Scanner (Mini Focus),” Waygate Technologies. https://www.bakerhughesds.com/industrial-x-ray-ct-scanners/phoenix-vtomex-c-ct (accessed Dec. 29, 2020).
- [119] “Xradia 610 & 620 Versa.” https://www.zeiss.com/microscopy/us/products/x-ray-microscopy/zeissxradia-610-and-620-versa.html (accessed Dec. 29, 2020).
- [120] T. J. Schorn, Improving the Effectiveness of Visual Inspection. Schaumburg, IL USA: American Foundry Society, 2018.
- [121] J. F. Koretz and G. H. Handelman, “How the Human Eye Focuses,” Sci Am, vol. 259, no. 1, pp. 92– 99, Jul. 1988, doi: 10.1038/scientificamerican0788-92.
- [122] J. Schindelin et al., “Fiji: an open-source platform for biological-image analysis,” Nat Methods, vol. 9, no. 7, pp. 676–682, Jul. 2012, doi: 10.1038/nmeth.2019.
- [123] S. Preibisch, S. Saalfeld, J. Schindelin, and P. Tomancak, “Software for bead-based registration of selective plane illumination microscopy data,” Nat Methods, vol. 7, no. 6, pp. 418–419, Jun. 2010, doi: 10.1038/nmeth0610-418.
- [124] “Standard Reference Radiographs for Inspection of Aluminum and Magnesium Die Castings E505- 15.” ASTM International, 2015. doi: 10.1520/E0505-15.
- [125] S. S. Shapiro and M. B. Wilk, “An Analysis of Variance Test for Normality (Complete Samples),” Biometrika, vol. Vol. 52, pp. 591–611, Dec. 1965,
- [Online]. Available: https://www.jstor.org/stable/2333709
- [126] F. Wilcoxon, “Individual Comparisons by Ranking Methods,” Biometrics Bulletin, vol. 1, no. No. 6, pp. 80–83, Dec. 1945.
- [127] MAGMAsoft. Kackerstrasse 11, 52072 Aachen, Germany: MAGMA Gmbh, 2019.
- [128] M. R. Brand, “An examination of certain Bayesian methods used in reliability analysis,” Reliability Engineering, vol. 1, no. 2, pp. 115–125, Oct. 1980, doi: 10.1016/0143-8174(80)90003-7.
- [129] S. G. Lee and A. M. Gokhale, “Formation of gas induced shrinkage porosity in Mg-alloy highpressure die-castings,” Scripta Materialia, vol. 55, no. 4, pp. 387–390, Aug. 2006, doi: 10.1016/j.scriptamat.2006.04.040.
- [130] F. Bonollo, N. Gramegna, and G. Timelli, “High-Pressure Die-Casting: Contradictions and Challenges,” JOM, vol. 67, no. 5, pp. 901–908, May 2015, doi: 10.1007/s11837-015-1333-8.
- [131] C. H. Cáceres and B. I. Selling, “Casting defects and the tensile properties of an AlSiMg alloy,” Materials Science and Engineering: A, vol. 220, no. 1–2, pp. 109–116, Dec. 1996, doi: 10.1016/S0921-5093(96)10433-0.
- [132] R. Lumley, N. Deeva, and M. Gershenzon, “An Evaluation of Quality Parameters for High Pressure Die Castings,” Inter Metalcast, vol. 5, no. 3, pp. 37–56, Jul. 2011, doi: 10.1007/BF03355517.
- [133] D. Blondheim, Jr., “Improving Manufacturing Applications of Machine Learning by Understanding Defect Classification and the Critical Error Threshold,” Inter Metalcast, Jun. 2021, doi: 10.1007/s40962-021-00637-0.
- [134] Y. LeCun et al., “Handwritten Digit Recognition with a Back-Propagation Network,” 1990, pp. 396–404.
- [135] S. Lalmuanawma, J. Hussain, and L. Chhakchhuak, “Applications of machine learning and artificial intelligence for Covid-19 (SARS-CoV-2) pandemic: A review,” Chaos, Solitons & Fractals, vol. 139, p. 110059, Oct. 2020, doi: 10.1016/j.chaos.2020.110059.
- [136] “The transformative potential of AI in the manufacturing industry - Microsoft Industry Blogs.” https://cloudblogs.microsoft.com/industry-blog/manufacturing/2017/09/25/the-transformativepotential-of-ai-in-the-manufacturing-industry/ (accessed Nov. 27, 2020).
- [137] “Bringing Intelligence to Industrial Manufacturing Through AWS IoT and Machine Learning | AWS Partner Network (APN) Blog.” https://aws.amazon.com/blogs/apn/bringing-intelligence-toindustrial-manufacturing-through-aws-iot-and-machine-learning/ (accessed Nov. 27, 2020).
- [138] P. K. Tseng, “Smart Manufacturing Becomes Key to Enterprise Survival in Post-Pandemic Era with Forecasted Revenue of US$400 Billion in 2024, Says TrendForce,” Aug. 17, 2020. https://www.trendforce.com/presscenter/news/20200817-10437.html (accessed Nov. 27, 2020).
- [139] “Thriving in an AI World.” KPMG, Apr. 15, 2021.
- [Online]. Available: https://info.kpmg.us/content/dam/info/en/newsperspectives/pdf/2021/Updated%204.15.21%20-%20Thriving%20in%20an%20AI%20world.pdf
- [140] G. Rebala, A. Ravi, and S. Churiwala, An Introduction to Machine Learning. Cham: Springer International Publishing, 2019. doi: 10.1007/978-3-030-15729-6.
- [141] R. Fernandes de Mello and M. Antonelli Ponti, Machine Learning: A Practical Approach on the Statistical Learning Theory. Cham: Springer International Publishing, 2018. doi: 10.1007/978-3- 319-94989-5.
- [142] J. M. Juran, Ed., Juran’s quality handbook, 5. ed. New York, NY: McGraw-Hill, 1999.
- [143] J. J. Sheehan and C. G. Drury, “The analysis of industrial inspection,” Applied Ergonomics, vol. 2, no. 2, pp. 74–78, Jun. 1971, doi: 10.1016/0003-6870(71)90073-1.
- [144] C. G. Drury, “The effect of speed of working on industrial inspection accuracy,” Applied Ergonomics, vol. 4, no. 1, pp. 2–7, Mar. 1973, doi: 10.1016/0003-6870(73)90002-1.
- [145] C. G. Drury and M.-J. Wang, “Are Research Results in Inspection Task Specific?,” Proceedings of the Human Factors Society Annual Meeting, vol. 30, no. 5, pp. 476–480, Sep. 1986, doi: 10.1177/154193128603000515.
- [146] C.-F. Chi, “The human as an optimizer in inspection,” State University of New York, Buffalo, NY, 1990.
- [147] A. Fernández, S. García, and F. Herrera, “Addressing the Classification with Imbalanced Data: Open Problems and New Challenges on Class Distribution,” in Hybrid Artificial Intelligent Systems, vol. 6678, E. Corchado, M. Kurzyński, and M. Woźniak, Eds. Berlin, Heidelberg: Springer Berlin Heidelberg, 2011, pp. 1–10. doi: 10.1007/978-3-642-21219-2_1.
- [148] S. Viswanathan et al., Eds., “High-Pressure Die Casting,” in Casting, ASM International, 2008, pp. 715–718. doi: 10.31399/asm.hb.v15.a0005266.
- [149] J. Folk, “The U.S. Aluminum Casting Industry,” Die Casting Engineer, vol. May 2015, pp. 24–33, May 2015.
- [Online]. Available: https://www.diecasting.org/archive/dce/51524.pdf
- [150] V. Khalajzadeh, K. D. Carlson, D. G. Backman, and C. Beckermann, “A Pore-Centric Model for Combined Shrinkage and Gas Porosity in Alloy Solidification,” Metall and Mat Trans A, vol. 48, no. 4, pp. 1797–1816, Apr. 2017, doi: 10.1007/s11661-016-3940-6.
- [151] P. F. Ostwald and J. Huang, “A Method for Optimal Tolerance Selection,” Journal of Engineering for Industry, vol. 99, no. 3, pp. 558–565, Aug. 1977, doi: 10.1115/1.3439279.
- [152] C. Zhang, H. P. Wang, and J. K. Li, “Simultaneous Optimization of Design and Manufacturing — Tolerances with Process (Machine) Selection,” CIRP Annals, vol. 41, no. 1, pp. 569–572, 1992, doi: 10.1016/S0007-8506(07)61270-0.
- [153] A. Jeang, “Tolerance chart optimization for quality and cost,” International Journal of Production Research, vol. 36, no. 11, pp. 2969–2983, Nov. 1998, doi: 10.1080/002075498192238.
- [154] M. D. Al-Ansary and I. M. Deiab, “Concurrent optimization of design and machining tolerances using the genetic algorithms method,” International Journal of Machine Tools and Manufacture, vol. 37, no. 12, pp. 1721–1731, Dec. 1997, doi: 10.1016/S0890-6955(97)00033-3.
- [155] S. A. Irani, R. O. Mittal, and E. A. Lehtihet, “Tolerance chart optimization,” International Journal of Production Research, vol. 27, no. 9, pp. 1531–1552, Sep. 1989, doi: 10.1080/00207548908942638.
- [156] A. N. Haq, K. Sivakumar, R. Saravanan, and V. Muthiah, “Tolerance design optimization of machine elements using genetic algorithm,” Int J Adv Manuf Technol, vol. 25, no. 3–4, pp. 385– 391, Feb. 2005, doi: 10.1007/s00170-003-1855-z.
- [157] American Society of Mechanical Engineers and American National Standards Institute, Dimensioning and tolerancing: engineering drawing and related documentation practices. New York: American Society of Mechanical Engineers, 2019.
- [158] J. D. Meadows, Geometric Dimensioning and Tolerancing: Applications, Analysis & Measurement
- [per ASME Y14.5-2009]. James D. Meadows & Associated, Inc., 2009.
- [159] D. Steiner and R. Katz, “Measurement Techniques for the Inspection of Porosity Flaws on Machined Surfaces,” Journal of Computing and Information Science in Engineering, vol. 7, no. 1, pp. 85–94, Mar. 2007, doi: 10.1115/1.2424244.
- [160] S. J. Świłło and M. Perzyk, “Automatic inspection of surface defects in die castings after machining,” Archives of Foundry Engineering, vol. Volume 11, no. Special Issue 3/2011, pp. 231– 236, 2011.
- [161] F. Peters, R. Stone, K. Watts, P. Zhon, and A. Clemons, “Visual Inspection of Casting Surfaces,” Transactions of the American Foundry Society, pp. 45–52, 2013.
- [162] D. H. Harris and F. B. Chaney, Human Factors in Quality Assurance. New York: John Wiley & Sons Inc, 1969.
- [163] S. B. Kotsiantis, “Supervised Machine Learning: A Review of Classification Techniques,” Informatica, vol. 31, no. 3, pp. 249–269, Oct. 2007.
- [164] T. Hastie, R. Tibshirani, and J. Friedman, The Elements of Statistical Learning. New York, NY: Springer New York, 2009. doi: 10.1007/978-0-387-84858-7.
- [165] Y. Wang, D. Zou, J. Yi, J. Bailey, X. Ma, and Q. Gu, “IMPROVING ADVERSARIAL ROBUSTNESS REQUIRES REVISITING MISCLASSIFIED EXAMPLES,” Virtual Conference, 2020, p. 14. Accessed: Mar. 01, 2021.
- [Online]. Available: https://openreview.net/forum?id=rklOg6EFwS
- [166] M. R. Smith and T. Martinez, “Improving classification accuracy by identifying and removing instances that should be misclassified,” in The 2011 International Joint Conference on Neural Networks, San Jose, CA, USA, Jul. 2011, pp. 2690–2697. doi: 10.1109/IJCNN.2011.6033571.
- [167] D. Chicco and G. Jurman, “The advantages of the Matthews correlation coefficient (MCC) over F1 score and accuracy in binary classification evaluation,” BMC Genomics, vol. 21, no. 1, p. 6, Dec. 2020, doi: 10.1186/s12864-019-6413-7.
- [168] D. Powers, “Evaluation: From Precision, Recall and F-Factor to ROC, Informedness, Markedness & Correlation,” Mach. Learn. Technol., vol. 2, p. 25, 2008,
- [Online]. Available: https://arxiv.org/abs/1504.00854
- [169] D. Blondheim, Jr. and S. Bhowmik, “Time-Series Analysis and Anomaly Detection of HighPressure Die Casting Shot Profiles,” Die Casting Engineer, pp. 14–18, Nov. 2019.
- [Online]. Available: http://www.diecasting.org/archive/dce/111914.pdf
- [170] P. Patel, M. I. Ali, and A. Sheth, “From Raw Data to Smart Manufacturing: AI and Semantic Web of Things for Industry 4.0,” IEEE Intell. Syst., vol. 33, no. 4, pp. 79–86, Jul. 2018, doi: 10.1109/MIS.2018.043741325.
- [171] R. S. Peres, X. Jia, J. Lee, K. Sun, A. W. Colombo, and J. Barata, “Industrial Artificial Intelligence in Industry 4.0 - Systematic Review, Challenges and Outlook,” IEEE Access, vol. 8, pp. 220121– 220139, 2020, doi: 10.1109/ACCESS.2020.3042874.
- [172] A. Bécue, I. Praça, and J. Gama, “Artificial intelligence, cyber-threats and Industry 4.0: challenges and opportunities,” Artif Intell Rev, vol. 54, no. 5, pp. 3849–3886, Jun. 2021, doi: 10.1007/s10462- 020-09942-2.
- [173] A. B. Simmons and S. G. Chappell, “Artificial intelligence-definition and practice,” IEEE J. Oceanic Eng., vol. 13, no. 2, pp. 14–42, Apr. 1988, doi: 10.1109/48.551.
- [174] S. J. Russell, P. Norvig, and E. Davis, Artificial intelligence: a modern approach, 3rd ed. Upper Saddle River: Prentice Hall, 2010.
- [175] I. Goodfellow, Y. Bengio, and A. Courville, Deep learning. Cambridge, Massachusetts: The MIT Press, 2016.
- [176] T. Sasakawa, J. Hu, and K. Hirasawa, “A brainlike learning system with supervised, unsupervised, and reinforcement learning,” Elect. Eng. Jpn., vol. 162, no. 1, pp. 32–39, Jan. 2008, doi: 10.1002/eej.20600.
- [177] H. Oliff, Y. Liu, M. Kumar, M. Williams, and M. Ryan, “Reinforcement learning for facilitating human-robot-interaction in manufacturing,” Journal of Manufacturing Systems, vol. 56, pp. 326– 340, Jul. 2020, doi: 10.1016/j.jmsy.2020.06.018.
- [178] L. Wang et al., “Dynamic job-shop scheduling in smart manufacturing using deep reinforcement learning,” Computer Networks, vol. 190, p. 107969, May 2021, doi: 10.1016/j.comnet.2021.107969.
- [179] D. Blondheim, Jr., “Utilizing Machine Learning Autoencoders to Detect Anomalies in Time-Series Data,” presented at the 2021 NADCA Congress and Exposition, Indianapolis, IN, Oct. 2021.
- [180] S. Žapčević and P. Butala, “Adaptive process control based on a self-learning mechanism in autonomous manufacturing systems,” Int J Adv Manuf Technol, vol. 66, no. 9–12, pp. 1725–1743, Jun. 2013, doi: 10.1007/s00170-012-4453-0.
- [181] S. Profanter, A. Tekat, K. Dorofeev, M. Rickert, and A. Knoll, “OPC UA versus ROS, DDS, and MQTT: Performance Evaluation of Industry 4.0 Protocols,” in 2019 IEEE International Conference on Industrial Technology (ICIT), Melbourne, Australia, Feb. 2019, pp. 955–962. doi: 10.1109/ICIT.2019.8755050.
- [182] M. Silveira Rocha, G. Serpa Sestito, A. Luis Dias, A. Celso Turcato, and D. Brandao, “Performance Comparison Between OPC UA and MQTT for Data Exchange,” in 2018 Workshop on Metrology for Industry 4.0 and IoT, Brescia, Apr. 2018, pp. 175–179. doi: 10.1109/METROI4.2018.8428342.
- [183] G. Büchi, M. Cugno, and R. Castagnoli, “Smart factory performance and Industry 4.0,” Technological Forecasting and Social Change, vol. 150, p. 119790, Jan. 2020, doi: 10.1016/j.techfore.2019.119790.
- [184] Y.-H. Choi and S.-H. Choi, “A Study of Crossing the Chasm in applying Smart Factory System for SMEs,” International Journal of Pure and Applied Mathematics, vol. 118, no. No 19, pp. 469–487, Jan. 2018,
- [Online]. Available: http://www.ijpam.eu
- [185] M. Khan, X. Wu, X. Xu, and W. Dou, “Big data challenges and opportunities in the hype of Industry 4.0,” in 2017 IEEE International Conference on Communications (ICC), Paris, France, May 2017, pp. 1–6. doi: 10.1109/ICC.2017.7996801.
- [186] A. Khan and K. Turowski, “A Survey of Current Challenges in Manufacturing Industry and Preparation for Industry 4.0,” in Proceedings of the First International Scientific Conference “Intelligent Information Technologies for Industry” (IITI’16), vol. 450, A. Abraham, S. Kovalev, V. Tarassov, and V. Snášel, Eds. Cham: Springer International Publishing, 2016, pp. 15–26. doi: 10.1007/978-3-319-33609-1_2.
- [187] T. Wuest, C. Irgens, and K.-D. Thoben, “An approach to monitoring quality in manufacturing using supervised machine learning on product state data,” J Intell Manuf, vol. 25, pp. 1167–1180, 2014, doi: 10.1007/s10845-013-0761-y.
- [188] S. Sun, X. Zheng, J. Villalba-Díez, and J. Ordieres-Meré, “Data Handling in Industry 4.0: Interoperability Based on Distributed Ledger Technology,” Sensors, vol. 20, no. 11, p. 3046, May 2020, doi: 10.3390/s20113046.
- [189] R. Sahal, J. G. Breslin, and M. I. Ali, “Big data and stream processing platforms for Industry 4.0 requirements mapping for a predictive maintenance use case,” Journal of Manufacturing Systems, vol. 54, pp. 138–151, Jan. 2020, doi: 10.1016/j.jmsy.2019.11.004.
- [190] K. Villalobos, V. J. Ramírez-Durán, B. Diez, J. M. Blanco, A. Goñi, and A. Illarramendi, “A three level hierarchical architecture for an efficient storage of industry 4.0 data,” Computers in Industry, vol. 121, p. 103257, Oct. 2020, doi: 10.1016/j.compind.2020.103257.
- [191] F. Y. Kuo and I. H. Sloan, “Lifting the Curse of Dimensionality,” Notices of the AMS, vol. 52, no. 11, pp. 1320–1329, 2005.
- [192] G. Hughes, “On the mean accuracy of statistical pattern recognizers,” IEEE Trans. Inform. Theory, vol. 14, no. 1, pp. 55–63, Jan. 1968, doi: 10.1109/TIT.1968.1054102.
- [193] P. Domingos, “A few useful things to know about machine learning,” Commun. ACM, vol. 55, no. 10, pp. 78–87, Oct. 2012, doi: 10.1145/2347736.2347755.
- [194] F. Provost, “Machine Learning from Imbalanced Data Sets 101,” in AAAI Technical Report WS-00- 05, 2000, p. 3.
- [Online]. Available: https://www.aaai.org/Papers/Workshops/2000/WS-00- 05/WS00-05-001.pdf
- [195] M. Kuhn and K. Johnson, Applied Predictive Modeling. New York, NY: Springer New York, 2013. doi: 10.1007/978-1-4614-6849-3.
- [196] A. Paleyes, R.-G. Urma, and N. D. Lawrence, “Challenges in Deploying Machine Learning: a Survey of Case Studies,” arXiv:2011.09926
- [cs], Jan. 2021, Accessed: Feb. 07, 2021.
- [Online]. Available: http://arxiv.org/abs/2011.09926
- [197] L. Breiman, “Random Forests,” Machine Learning, vol. 45, no. 1, pp. 5–32, 2001, doi: 10.1023/A:1010933404324.
- [198] S. Kuutti, R. Bowden, Y. Jin, P. Barber, and S. Fallah, “A Survey of Deep Learning Applications to Autonomous Vehicle Control,” IEEE Trans. Intell. Transport. Syst., vol. 22, no. 2, pp. 712–733, Feb. 2021, doi: 10.1109/TITS.2019.2962338.
- [199] A. Kuusk and J. Gao, “Factors for successfully integrating operational and information technologies,” in 2015 Portland International Conference on Management of Engineering and Technology (PICMET), Portland, OR, USA, Aug. 2015, pp. 1513–1523. doi: 10.1109/PICMET.2015.7273136.
- [200] E. J. M. Colbert and A. Kott, Eds., Cyber-security of SCADA and Other Industrial Control Systems, vol. 66. Cham: Springer International Publishing, 2016. doi: 10.1007/978-3-319-32125-7.
- [201] L. Thames and D. Schaefer, Eds., Cybersecurity for Industry 4.0: Analysis for Design and Manufacturing. Cham: Springer International Publishing, 2017. doi: 10.1007/978-3-319-50660-9.
- [202] G. Culot, F. Fattori, M. Podrecca, and M. Sartor, “Addressing Industry 4.0 Cybersecurity Challenges,” IEEE Eng. Manag. Rev., vol. 47, no. 3, pp. 79–86, Sep. 2019, doi: 10.1109/EMR.2019.2927559.
- [203] M. Lezzi, M. Lazoi, and A. Corallo, “Cybersecurity for Industry 4.0 in the current literature: A reference framework,” Computers in Industry, vol. 103, pp. 97–110, Dec. 2018, doi: 10.1016/j.compind.2018.09.004.
- [204] P. O’Donovan, K. Leahy, K. Bruton, and D. T. J. O’Sullivan, “Big data in manufacturing: a systematic mapping study,” Journal of Big Data, vol. 2, no. 1, p. 20, Dec. 2015, doi: 10.1186/s40537-015-0028-x.
- [205] M. Fahmideh and G. Beydoun, “Big data analytics architecture design—An application in manufacturing systems,” Computers & Industrial Engineering, vol. 128, pp. 948–963, Feb. 2019, doi: 10.1016/j.cie.2018.08.004.
- [206] I. Nunes and D. Jannach, “A systematic review and taxonomy of explanations in decision support and recommender systems,” User Model User-Adap Inter, vol. 27, no. 3–5, pp. 393–444, Dec. 2017, doi: 10.1007/s11257-017-9195-0.
- [207] C. Rudin and K. L. Wagstaff, “Machine learning for science and society,” Mach Learn, vol. 95, no. 1, pp. 1–9, Apr. 2014, doi: 10.1007/s10994-013-5425-9.
- [208] N. Werts and M. Adya, “Data Mining in Healthcare: Issues and a Research Agenda,” in AMCIS 2000 Proceedings, 2000, pp. 94–97.
- [209] R. Boutaba et al., “A comprehensive survey on machine learning for networking: evolution, applications and research opportunities,” J Internet Serv Appl, vol. 9, no. 1, p. 16, Dec. 2018, doi: 10.1186/s13174-018-0087-2.
- [210] “NADCA - Schedule of Events.” https://www.diecasting.org/wcm/Meetings/Congress_and_Exposition/Schedule_of_Events/wcm/Me etings/Schedule_of_Events.aspx?hkey=03f18550-584d-4f4f-9e69-df3668429226 (accessed Sep. 22, 2021).
- [211] “AIM 2022: Home.” https://www.tms.org/portal/MEETINGS___EVENTS/TMS_Meetings___Events/Upcoming_TMS_ Meetings/AIM2022/portal/Meetings___Events/2022/AIM2022/default.aspx?hkey=7050d00c-58bb4f5c-854b-84486f96c37b (accessed Sep. 22, 2021).
- [212] “AI Course: Home.” https://www.tms.org/portal/Meetings___Events/2021/AIcourse/default.aspx (accessed Sep. 22, 2021).
- [213] F. von Hayek, “Friedrich von Hayek Prize Lecture,” NobelPrize.org, Dec. 11, 1974. https://www.nobelprize.org/prizes/economic-sciences/1974/hayek/lecture/ (accessed Aug. 22, 2021).
- [214] B. Marr, “A Short History of Machine Learning -- Every Manager Should Read,” Forbes, Feb. 19, 2016. https://www.forbes.com/sites/bernardmarr/2016/02/19/a-short-history-of-machine-learningevery-manager-should-read/
- [215] R Core Team, R: A language and environment for statistical computing. Vienna, Austria: R Foundation for Statistical Computing, 2016.
- [Online]. Available: https://www.R-project.org
- [216] B. Lantz, Machine Learning with R, 2nd edition. Packt Publishing Ltd., 2015.
- [217] E. Siegel, Predictive Analytic: the power to predict who will click, buy, lie or die. John Wiley & Sons Inc, 2013.
- [218] M. Kuhn, caret: Classification and Regression Training. 2017.
- [Online]. Available: https://CRAN.R-project.org/package=caret
- [219] W. N. Venables and B. D. Ripley, Modern Applied Statistics with S. New York, NY: Springer New York, 2002. doi: 10.1007/978-0-387-21706-2.
- [220] S. Fritsch and F. Guenther, neuralnet: Training of Neural Networks. 2017.
- [Online]. Available: https://CRAN.R-project.org/package=neuralnet
- [221] D. Meyer, E. Dimitriadou, K. Hornik, A. Weingessel, and F. Leisch, e1071: Misc Functions of the Department of Statistics, Probability Theory Group (Formerly: E1071), TU Wien. 2017.
- [Online]. Available: https://CRAN.R-project.org/package=e1071
- [222] J. Macqueen, “SOME METHODS FOR CLASSIFICATION AND ANALYSIS OF MULTIVARIATE OBSERVATIONS,” in Proceedings of 5th Berkeley Symposium on Mathematical Statistics and Probability, 1967, pp. 281–297.
- [223] P. Catterina and C. Raone, “Towards the ‘Total’ certification in diecasting process Thermographic monitoring and traceability with TOTAL THERMAL VISION (TTV),” 2013, vol. T13-041.
- [Online]. Available: https://www.diecasting.org/archive/transactions/T13-041.pdf
- [224] L. X. Kong, F. H. She, S. Nahavandi, and L. H. Wang, “Thermal control with image processing and fuzzy controllers,” in Proceedings Joint 9th IFSA World Congress and 20th NAFIPS International Conference (Cat. No. 01TH8569), Vancouver, BC, Canada, 2001, vol. 3, pp. 1443–1449. doi: 10.1109/NAFIPS.2001.943761.
- [225] S. Simske, Meta-Algorithmics: Patterns for Robust, Low Cost, High Quality Systems. Wiley-IEEE Press, 2013.
- [226] W. A. Shewhart, Economic Control of Quality of Manufactured Products. New York, NY: D. Van Nostrand Company, Inc., 1931.
- [227] D. L. Simon and J. C. Lafeber, “Optimization of Die Casting Processes Using Infrared Thermography,” 2011, vol. T11-071.
- [Online]. Available: https://www.diecasting.org/archive/transactions/T11-071.pdf
- [228] A. Reikher, H. Gerber, and A. Starobin, “Multi-Stage Plunger Deceleration System,” Atlanta, GA, May 2008, vol. T08-011.
- [Online]. Available: https://www.diecasting.org/archive/transactions/T08- 011.pdf
- [229] J. Liang and S. Parthasarathy, “Robust Contextual Outlier Detection: Where Context Meets Sparsity,” in Proceedings of the 25th ACM International on Conference on Information and Knowledge Management, Indianapolis Indiana USA, Oct. 2016, pp. 2167–2172. doi: 10.1145/2983323.2983660.
- [230] S. Tartaglia and J. Vandertouw, “Benchmarking Study Comparison of North American and Japanese Companies,” Die Casting Engineer, no. March/April 2000, pp. 104–109, 2000.
- [Online]. Available: https://www.diecasting.org/archive/dce/200104.pdf
- [231] K.-D. Thoben, S. Wiesner, and T. Wuest, “‘Industrie 4.0’ and Smart Manufacturing – A Review of Research Issues and Application Examples,” Int. J. Automation Technol., vol. 11, no. 1, pp. 4–16, Jan. 2017, doi: 10.20965/ijat.2017.p0004.
- [232] S. P. Udvardy, “2019 State of the Die Casting Industry,” Die Casting Engineer, no. January 2020, pp. 10–15, 2020.
- [Online]. Available: https://www.diecasting.org/archive/dce/12010.pdf
- [233] S. P. Udvardy, “2020 State of the Die Casting Industry,” Die Casting Engineer, vol. January 2021, pp. 8–13, 2021.
- [Online]. Available: https://www.diecasting.org/docs/information/stateoftheindustry-dcejan2021.pdf
- [234] A. Heidarian and M. J. Dinneen, “A Hybrid Geometric Approach for Measuring Similarity Level Among Documents and Document Clustering,” in 2016 IEEE Second International Conference on Big Data Computing Service and Applications (BigDataService), Oxford, United Kingdom, Mar. 2016, pp. 142–151. doi: 10.1109/BigDataService.2016.14.
- [235] S. Samarasinghe, Neural networks for applied sciences and engineering: from fundamentals to complex pattern recognition. Auerbach Publications, 2007.
- [236] D. Forsyth, Applied Machine Learning. Cham: Springer International Publishing, 2019. doi: 10.1007/978-3-030-18114-7.
- [237] W. Liu, Z. Wang, X. Liu, N. Zeng, Y. Liu, and F. E. Alsaadi, “A survey of deep neural network architectures and their applications,” Neurocomputing, vol. 234, pp. 11–26, Apr. 2017, doi: 10.1016/j.neucom.2016.12.038.
- [238] G. E. Hinton, “Reducing the Dimensionality of Data with Neural Networks,” Science, vol. 313, no. 5786, pp. 504–507, Jul. 2006, doi: 10.1126/science.1127647.
- [239] Y. LeCun, C. Cortes, and C. J. C. Burges, “The MNIST Database of handwritten digits.” http://yann.lecun.com/exdb/mnist/ (accessed Jun. 25, 2021).
- [240] “2.1 Million Manufacturing Jobs Could Go Unfilled by 2030,” NAM, May 04, 2021. https://www.nam.org/2-1-million-manufacturing-jobs-could-go-unfilled-by-2030-13743/ (accessed Sep. 04, 2021).
- [241] P. Wellener, V. Reyes, H. Ashton, and C. Moutray, “Creating pathways for tomorrow’s workforce today,” Deloitte Insights. https://www2.deloitte.com/us/en/insights/industry/manufacturing/manufacturing-industrydiversity.html (accessed Sep. 04, 2021).
List of Abbreviations
- AFS – American Foundry Society
- AI – Artificial Intelligence
- BoB – Best of Best
- CET – Critical Error Threshold
- CT Scanning – Computed Tomography Scanning
- HPDC – High Pressure Die Casting
- IIoT – Industrial Internet of Things
- IT – Information Technology
- INCOSE – International Council on Systems Engineering
- ML – Machine Learning
- MQTT – Message Queuing Telemetry Transport
- NADCA – North American Die Casting Association
- NN – Neural Network
- OPC UA – Open Platform Communications Unified Architecture
- OT – Operational Technology
- PLC – Programmable Logic Controller
- PSI – Pounds per Square Inch
- RPM – Revolutions per Minute
- SE – Systems Engineering
- SoS – Systems-of-Systems
- SVM – Support Vector Machine
- WoW – Worst of worst
Copyright:
- This material is David J. Blondheim, Jr.'s paper: Based on SYSTEM UNDERSTANDING OF HIGH PRESSURE DIE CASTING PROCESS AND DATA WITH MACHINE LEARNING APPLICATIONS.
- This material was summarized based on the above paper, and unauthorized use for commercial purposes is prohibited.
- Copyright © 2025 CASTMAN. All rights reserved.