Salt core technology used for high pressure die casting
With the development of the manufacturing industry, aluminum die casting parts are increasingly used in many fields, and hollow die casting parts can increase the strength of the structure and reduce the weight. Vacuum die casting is mainly used for automotive parts and can make thin walls. Complex hollow parts can be made using salt cores that are removed by water during die casting.
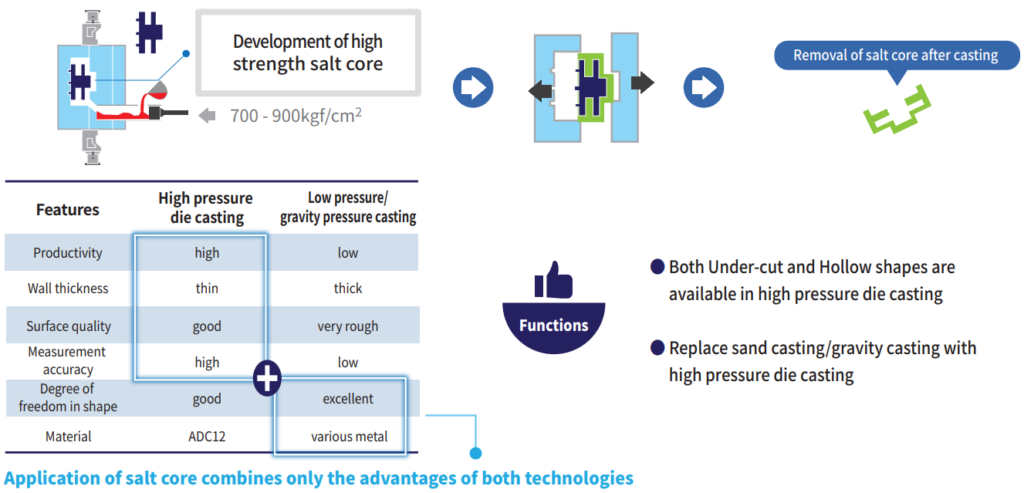
Competitive Cost Reduction
- Mass production enabled by short cycle time of high pressure die casting increases productivity
- Also reduces weight by 10-20% vs sand casting
- Cheaper materials compared to sand casting (AC4C ▶ ADC12)
Products Made by Replacing Sand Core with Salt Core Technology
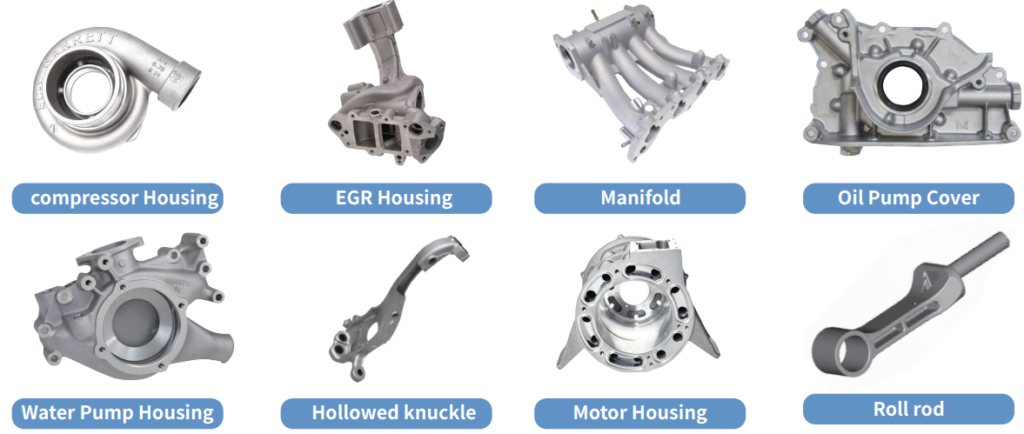
Salt core
Salt core dissolved by water means a core made of salt dissolved in water and can be removed by high pressure water after die casting compared to sand core used for low pressure or sand casting.
The salt core is of high strength, clean cast surface finish, less air bubbles, easy removal, minimal damage to parts and environmentally friendly. You can also recycle salt. Therefore, more and more salt cores will be used in the automotive industry.
In high pressure die casting, the tooling core must be able to withstand the impact of the molten alloy at a temperature of 680 ~ 720 ℃ and a speed of 20 ~ 50m / s. Therefore, salts soluble in water must be of high strength and meet the requirements of high and low pressure die casting. In addition, the yield of the salt core must match with high pressure die casting, and the tensile strength of the salt core must be at least 20 MPa. In addition, it must be well soluble and easy to clean, and must not be responsive to alloying and recycling use.
Considering the yield of high pressure die casting and the molding of the core for sale, the main method of making the salt core is the injection method. During die casting, the solidification time of the salt core is longer than that of the alloy, which adversely affects the production efficiency. In order to provide standards for salt core production and simulation of filling and solidification, it is necessary to establish a salt core evaluation system, and it is useful to find the possibility of cracking risk during die casting.
-Smooth surface quality -High thermal shock resistance -Water soluble -Thermal insulation | -No chemical binders used -No separate coating material used -Do not use harmful substances -Integrated core support structure | -Possible to design complex internal flow channels -Undercut molding possible -Surface quality specification available -Can be combined with other salt cores | -Part integration possible -Near net shape manufacturing - Increased productivity |
![]() | ![]() | ![]() | ![]() |
For die casting inquiries, please send an email to sales@castman.co.kr