This introductory paper is the research content of the paper "Materials & Modifications to Die Cast the Copper Conductors of the Induction Motor Rotor" published by DIE CASTING ENGINEER.
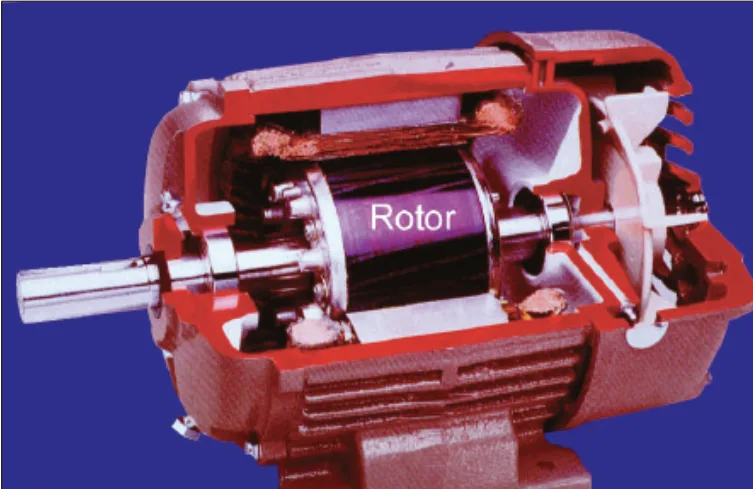
1. Overview:
- Title: Materials & Modifications to Die Cast the Copper Conductors of the Induction Motor Rotor
- Author: John G. Cowie, Edwin F. Brush, Jr., Dale T. Peters, Stephen P. Midson
- Publication Year: September 2001
- Published Journal/Society: DIE CASTING ENGINEER
- Keywords: (The paper does not explicitly list keywords, but based on the content, relevant keywords would include: copper die casting, induction motor rotor, mold materials, high-temperature alloys, motor efficiency, thermal fatigue)
2. Abstract
Articles on materials appearing in materials issues have generally focused on the common aluminum-, zinc- and magnesium-based die casting alloys. This report differs in that it deals with pressure die casting of a relatively high melting metal, pure copper. Short mold life is the limiting factor in achieving a cost effective die casting operation for high melting metals and alloys. This study, where the primary objective was a more efficient induction motor via a copper-containing rotor, was forced to address the mold or die material issue. Generalizations about the properties of mold materials and modifications to the thermal environment of the die set necessary to achieve cost effective mold life in service were concluded from this study. Properties of the cast copper in the rotor structure and the performance of the cast copper rotor in motor tests are also reported.
3. Research Background:
Background of the research topic:
Die casting is a widely recognized low-cost manufacturing process for large production volumes, commonly used with aluminum, zinc, and magnesium alloys. Induction motor rotors typically consist of a "squirrel cage" structure made of conductor bars and shorting rings. Traditionally, aluminum has been used due to its high electrical conductivity and ease of die casting (Figure 1,2).
Status of previous research:
Motor manufacturers have long recognized that replacing aluminum with copper in the rotor's conductor structure would significantly increase motor efficiency. Some special purpose and large motors use fabricated copper rotors, but this is a costly and slow process. Studies by the International Copper Research Association identified tungsten and molybdenum as potential mold materials for copper die casting.
Need for research:
A 1% increase in motor efficiency in the 1 to 125 Hp range could save 20 billion kWhrs per year. However, conventional tool steel molds used for aluminum die casting are inadequate for copper due to copper's higher melting point (1083°C vs. 660°C for aluminum). A durable and cost-effective mold material is required for the economical production of die-cast copper rotors.
4. Research purpose and research question:
Research purpose:
To develop a cost-effective die casting process for manufacturing copper induction motor rotors, focusing on identifying suitable mold materials and process modifications to achieve sufficient mold life.
Core research:
- Identify and evaluate candidate mold materials for copper die casting.
- Determine optimal die operating temperatures and thermal management strategies.
- Assess the quality and properties of die-cast copper.
- Evaluate the performance of die-cast copper rotors in motor tests.
5. Research methodology
The research involved a multi-disciplinary approach, including:
- Collaboration: A consortium of companies, including motor manufacturers, die casting equipment manufacturers, and research organizations (CDA/ICA, Trex Enterprises).
- Funding: International Copper Association, Air Conditioning and Refrigeration Technical Institute, U.S. Department of Energy (DOE) and Office of Industrial Technologies(OIT).
- Material Selection: Candidate mold materials were selected based on high-temperature strength, thermal properties, and cyclic oxidation resistance. Materials tested included:
- H-13 tool steel (baseline)
- Molybdenum-based alloy (TZM)
- Tungsten alloy (Anviloy 1200)
- Nickel-based alloys (INCONEL alloys 601, 617, 625, 718, and MA 754)
- Test Mold Design: A test mold was designed to simulate the conditions at one gate of a motor rotor mold (Figure 3, 4). This mold produced a two-pound flat semi-circular casting.
- Melting and Casting: High-purity copper was induction melted and cast using a 750-ton horizontal real-time, computer-shot-controlled die casting machine.
- Thermal Modeling: Computer analyses of heat transfer to the die casting molds were conducted to guide die design and material selection.
- Testing and Evaluation:
- Die materials were tested simultaneously in the test mold.
- Die temperatures were controlled using electrical resistance heaters and monitored with thermocouples.
- Cast copper quality was assessed through microstructural analysis, chemical analysis, and electrical conductivity measurements.
- Motor performance was evaluated by motor manufacturers using dynamometer test benches.
6. Key research results:
Key research results and presented data analysis:
- H-13 Tool Steel: Deteriorated rapidly due to heat checking and cracking, but produced over 750 castings before becoming unusable.
- TZM and Anviloy: Showed minimal heat checking after extended runs (over 900 shots), but Anviloy exhibited minor cracking at sharp radii. TZM suffered surface degradation due to oxidation.
- Nickel-Base Alloys: INCONEL alloys 617 and 625 performed best, showing minimal cracking at operating temperatures of 625-650°C. INCONEL alloy 754 cracked early due to low ductility.
- Optimal Die Temperature: Operating dies at elevated temperatures (above 550°C for TZM/Anviloy, 625°C for nickel-base alloys) was crucial for extending die life by minimizing thermal fatigue.
- Cast Copper Quality: Die-cast copper exhibited sound microstructure with minimal porosity and high electrical conductivity (averaging 98% IACS or higher).
- Rotor Die Casting Trials: Copper motor rotors were successfully die-cast using a modified process. Machine parameters were found to have a surprisingly small impact on rotor quality.
- Motor Performance: Copper rotors showed significant improvements in motor efficiency compared to aluminum rotors. Overall motor losses were reduced by 14-23%, and rotor losses were reduced by about 40%.
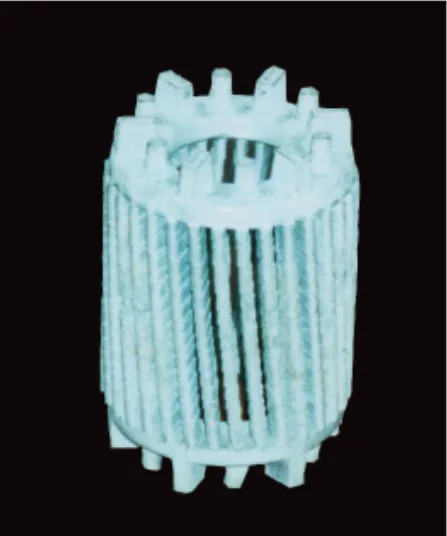
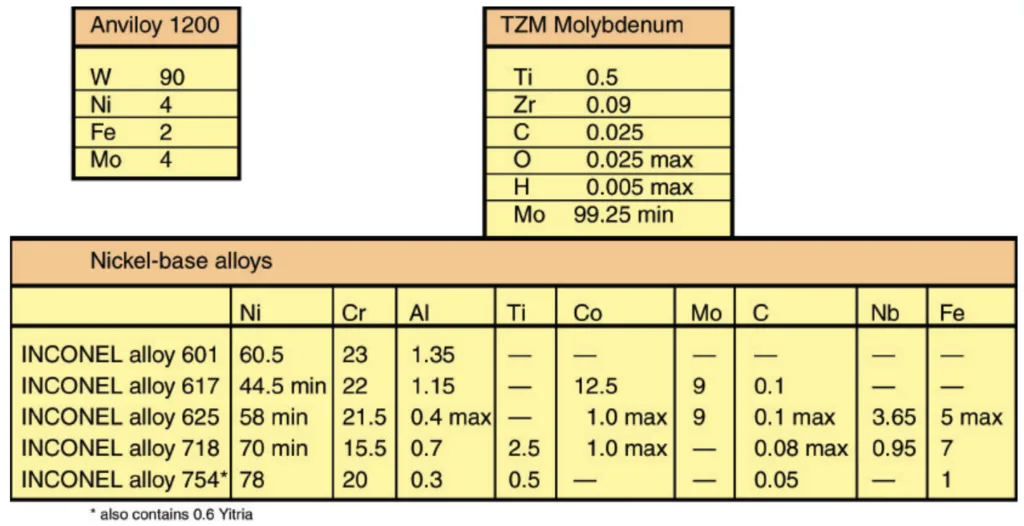
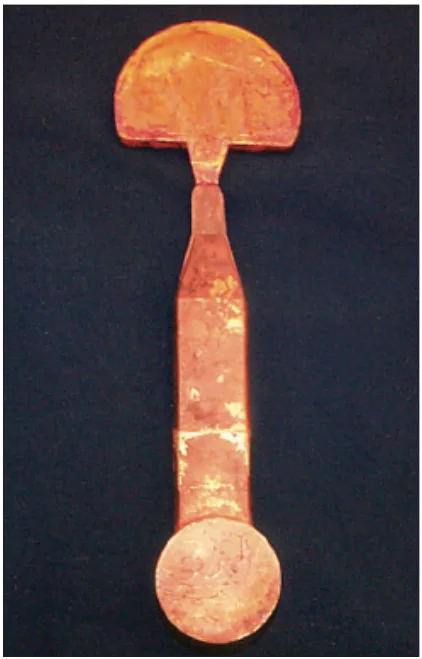

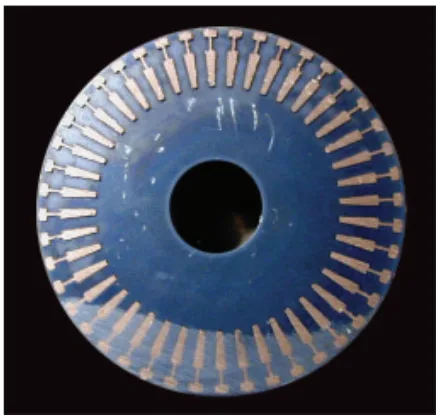
List of figure names:
- Fig. I - Exploded view of typical induction motor.
- Fig. 2 - The aluminum “squirrel cage" of a small motor rotor.
- Fig. 3 - Test casting used to evaluate and compare candidate mold materials.
- Fig. 4 - Detail of the die inserts for the test castings.
- Fig. 5- Microstructure of die cast copper specimen from the gate area of a casting produced in the H-13 tool steel die set.
- Fig. 6 - Top: Moving half TZM and Anviloy die inserts after 940 shots.
- Fig. 7 Die cast copper rotor about to be ejected from the center platen portion of the 750 ton machine.
- Fig. 8 - Horizontal pressure die caster with tooling for rotor casting in closed position.
- Fig. 9- Cross-section of rotor showing copper filling the slot openings by the pressure.
7. Conclusion:
Summary of key findings:
- INCONEL alloys 601, 617, and 625, operated at 600-650°C, are promising mold materials for die casting copper motor rotors.
- Operating dies at elevated temperatures is essential to extend die life by reducing thermal fatigue.
- Die-cast copper rotors can be produced with high purity and conductivity.
- The die casting process for copper rotors is robust, allowing for a wide range of machine parameters.
- Copper rotors significantly improve motor efficiency compared to aluminum rotors.
The research demonstrates the feasibility of die casting copper induction motor rotors, providing a pathway to significantly improve motor efficiency. The identification of suitable mold materials and process parameters is crucial for the commercial viability of this technology. The practical implications include substantial energy savings and reduced operating costs for electric motors.
8. References:
- [References]
(The provided document does not contain a dedicated reference section. References are implied within the text, such as mentions of the International Copper Research Association, U.S. Department of Energy, and specific publications like IEC 34-2 and IEEE Std. I12 Method B.)
9. Copyright:
- This material is a paper by "John G. Cowie, Edwin F. Brush, Jr., Dale T. Peters, Stephen P. Midson": Based on "Materials & Modifications to Die Cast the Copper Conductors of the Induction Motor Rotor".
- Source of paper: www.diecasting.org/dce (No DOI URL provided, only the website)
This material was created to introduce the above paper, and unauthorized use for commercial purposes is prohibited. Copyright © 2025 CASTMAN. All rights reserved.