Daniel Liang, Xu Yang, Jiabin Yu, Victor Zhou
Abstract
This paper introduces the recent technological progress in China on the manufacture of die cast Copper Motor Rotors (CMR) for induction motors. This manufacturing process provides a simple and practical means for large-scale economical production of high-efficiency induction motors. Rotor die casting obstacles/solutions are presented along with analyses and technical characteristics of cast copper rotor motors. The paper covers examples of the use of cast copper rotors in both high efficiency single-phase motors and IE3/IE4 motors.
Index Terms—Induction Motor, Copper Rotor, Efficiency
I. INTRODUCTION
The most widely used motor today is the squirrel-cage induction motor. In the Chinese market, the output of small- and medium-power squirrel-cage induction motors accounted for about 71 percent of the motors produced in 2009. It has always been a difficult technical problem to increase the efficiency of small- and mediumpower induction motors and it is all the more difficult to manufacture highly efficient motors with a small physical size. Since rotor losses take up around 20-25 percent of the total motor losses, reducing rotor losses has become an important technical means for increasing motor efficiency. The conductivity of copper is about 170 percent of that of aluminum, and replacing the traditional aluminum with copper can reduce the resistance of rotor-bars and end-rings, thereby reducing rotor losses and improving motor efficiency. Lower motor losses mean less electrical energy being converted to heat energy, and allow the motor to operate at a lower temperature. This means that motors can use smaller fans or no fans which reduces the windage and friction losses. This all plays a role in improving motor efficiency. Higher operating temperatures shorten motor life. For every 10°C rise in operating temperature, the insulation life will be reduced by one-half. So motors based on copper rotors have a longer life and more stable operation during that life. Furthermore, by using copper in the rotor, it is possible to use less material to produce motors which have the same power and efficiency as traditional motors. Because of these advantages of CMR motors, motor designers have greater flexibility in developing new motors - they can focus on raising efficiency, or lowering cost, on smaller size, lower weight, or on finding the best solution to Daniel Liang is with the Copper Alliance, 1202, Canway Building, Nanlishi Road, Beijing, China (daniel.liang@copperalliance.asia). Xu Yang is with Yunnan Copper Die-casting Co. Ltd., Erhuanxilu, Kunming, Yunnan, China (yangxum@yncopperdc.cn). Jiabin Yu is with Nanyang Explosion Protection Group Co.,Ltd., 22, Zhongjinglu, Nanyang, Henan, China (jiabin-127@163.com). Victor Zhou is with the Copper Alliance, 1202, Canway Building, Nanlishi Road, Beijing, China (Victor.zhou@copperalliance.asia). balance among these aspects. Besides being used in the industrial motor arena, the characteristics of CMR also make it competitive in other arenas, such as electric vehicles, submersible pumps, cranes, aircraft pumps, high-speed spindle motors, nuclear plant motors and military motors. Because of the high melting point of copper, it is more difficult to cast copper rotors in the way that it is done for aluminum rotors. Copper’s high melting temperature challenges casting-die designs and materials. The melting point of aluminum is 660°C, and the melting point of copper is 1083°C. If amelioration steps are not taken, the higher temperature reduces the die life and increases the die depreciation rate. In the past, fabricated-copper-rotors were the only choice for motor manufacturers wanting to implement copper rotors. Compared to cast copper rotors, fabricated-copper-rotors have a higher mass-produced cost as well as a lower adaptability to rotor-bar geometries. A group of companies led by the International Copper Association (ICA) has done much work to solve the problems associated with die casting of copper rotors. They have developed more appropriate die materials and casting processes for rotor production and made it possible for the economical mass production of copper rotors. Recent developments in the die casting process and copper rotor motor design are discussed in the following sections of this paper.
II. DIE CASTING PROCESS: THE ENABLER OF HIGH EFFICIENCY COPPER ROTOR MOTORS
There are three main obstacles to be overcome in the die casting of copper:
(1) Control of the procedure for melting pure copper:
Copper must be prevented from oxidizing when melted. When molten copper is formed, it reacts with oxygen in the air to form cuprous oxide, which greatly reduces its electrical conductivity. When conductivity is lowered, it undesirably lowers motor efficiency. While it is easy to prevent oxidation in a laboratory setting, it is more difficult during mass production in a factory. In order to produce copper rotors at large scale, an appropriate method is needed to prevent molten copper from oxidizing.
(2) Optimizing the copper casting procedures:
Molten copper is a very fluid material and, apart from its high melting temperature, is otherwise readily able to be die cast. The high rate of introduction of liquid metal into the die cavity, and the metal’s shrinkage during solidification, generally results in some distributed porosity in the casting. This issue is not limited to copper, however, as porosity in the end rings and conductor bars of die-cast aluminum rotors has also long been a problem. Historical optimization of the aluminum die casting procedure has brought porosity down to acceptable levels. Similar optimization is needed within copper casting procedures.
(3) Prolonging the die life:
The last but most import obstacle is caused by the higher melting point of copper compared to that of aluminum. A copper rotor must be cast at a temperature of at least 1200ºC. This takes a considerable toll on die life, and, if not addressed, increases the cost of producing copper rotors. Experience teaches us that if we use conventional aluminum-die materials and designs, the life of a copper die is only 1% of that of an aluminum die. Since 1994, the ICA has conducted much research and development around the above-mentioned obstacles and made much progress. In China, ICA has been cooperating with Yunnan Copper Die-casting Technology Co., Ltd and Nanyang Explosion Protection Group Co., Ltd to optimize the design of the die-casting production process for copper rotors. What follows is some of the learning that has flowed from that cooperation.
Currently, cast copper rotors are being mass-produced using the following solutions to the above three obstacles:
(1) Copper melting technology:
A gas-blanket protection method is used throughout the whole process of melting the copper. This method keeps the oxygen content of the melting copper in an acceptable 300 to 600ppm range.
(2) Copper die casting process:
Software simulating the die casting of copper in a horizontal casting machine has been developed in order to aid the optimization of the casting process and die design.
The software:
Simulates the whole casting process
Simulates the entire filling process
Simulates the temperature and flow fields
Estimates the filling time
Predicts defects such as porosity or poor fill
Is used for the optimization of the die design
In copper die casting, most of the defects are formed during the solidification process. The software simulates the solidification process and clearly predicts where defects may occur and suggests how to minimize them. The simulation shows the effect of different gate positions. It also helps in optimizing the design of the die runner system. The illustration in Figure 1 shows the influence of different gate positions on the fill process.
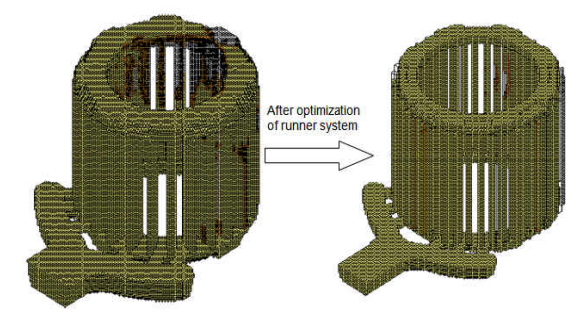
(3) Die life increase:
Because of the higher temperatures, the life of an un optimized copper rotor die which uses conventional materials and designs is only 600 cycles compared to 50,000 cycles for a comparable aluminum die. Increasing the die life to acceptable levels has required many detailed changes, of which the most important have been: die-pre-heating, die material optimization and mold construction optimization. Each of these is covered in more detail below:
a) Die pre-heating
We have obtained higher die lives by preheating the die to near the temperature of molten copper. If the die is not preheated, the resulting thermal shock during filling leads to cracks and greatly reduces the die life. It has been our experience that the die must be preheated by 500~600 degrees, which pushes the limits of typical die heating systems and requires specially designed heaters. Generally speaking, standard heating systems are limited by their heating wires only being able to withstand around 500 ºC. Careful heater design is required so that the temperature field of the die is kept uniform; if it is not, the die deforms and requires early repair. There are many methods available to preheat a die. For copper, we have found the electrical one the best. In order to achieve temperature uniformity, we have worked with Tsinghua University to develop software that simulates the die temperature field. This software divides the image of the die on a 3D grid. Each specific point is calculated using finite element methods to obtain the entire temperature field of the die. This software not only simulates the temperature in the preheating stage, but also in the casting stage. The software has helped us optimize the design for both the heating and the cooling systems of the die. Figure 2 presents an example of the die temperature field obtained from the simulation software.
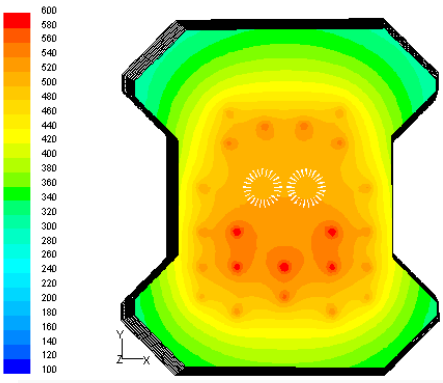
b) Die material optimization
We found that key components in the die system had to be moved to a high-temperature tungsten-based hot-mold steel to prevent their early failure. Those components included the shot sleeve and plunger that feed the molten metal to the die and the mold cavity itself. We believe that the reason for the better performance of this new material is its high temperature abrasion resistance and modulus. Surface case hardening of the plunger and shot sleeve was also found to delay the onset of micro-cracking of the plunger and increased its life.
c) Mold construction optimizaiton
Changing the architechture of the die so that it included replaceable inserts led to a die-life increase of 2-4 times. In particular, designing the mid-mold inserts (which surround the lamination-stack and end rings) so that they could be rotated and exchanged provided for rapid insert change-overs with minimal loss of in-process casting time. Only the inserts were changed during running, leaving the main structure of the die in place on the press. In addition we optimized our six-cavity mold design in order to reduce mold porosity caused by inconsistent filling from part to part. Figure 3 shows the original six-cavity mold (left) and the runner system after optimization (right). These diagrams are vertical sections through the die, with the rotor axes being horizontal in our set-up. Unlike the standard center-directed runners (left), the optimized runner system (right) follows the flow of melted metal as it flows from bottom to top.
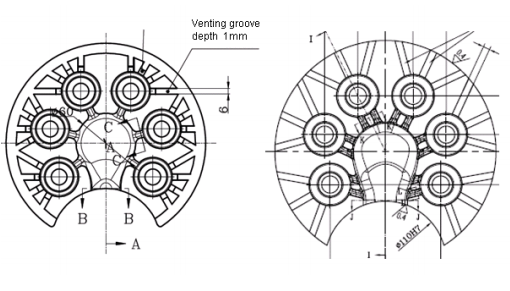
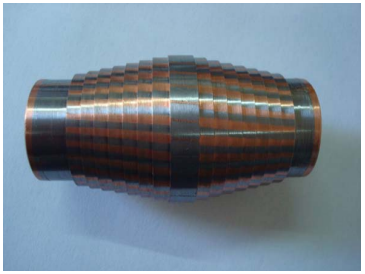
Thanks to the improvements enabled by these methods, and the guidance from many trials on our horizontal die casting machines, we have increased the life expectancy of our die to many thousands of cycles, reduced production costs and improved our product quality, as shown in Figure
4
This work has matured our horizontal die casting equipment/processes and allowed us to move into commercial mass-production of copper rotors. Our yield rate on copper rotors has been improved to 92-98 percent under mass-production conditions.
III. DEVELOPMENTS IN IE3/IE4 COPPER ROTOR MOTORS
Mature copper die-casting technology has provided a simple, reliable, economical and practical way to improve the efficiency of motors for motor manufacturers. In China, highly efficient single-phase motors and a series of motors at IE3 and IE4 efficiency levels have been successfully developed through cooperation with motor manufacturers. With the cast copper rotors, the efficiency of 0.75kW single-phase motors has reached 86 percent, up by about 8 percentage points. Table I shows the efficiency improvement through the use of copper rotors. The efficiency level of single-phase motors with cast copper rotors has moved towards that of three-phase high efficiency
motors.
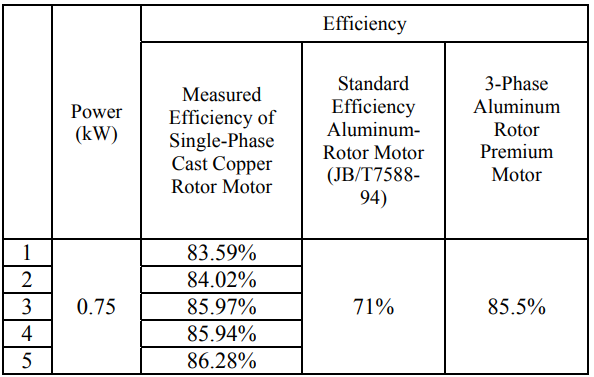
A. Achieving IE3 performance
In China, motor manufacturers use cast copper rotors to manufacture a full range of motors at IE3 efficiency levels from 0.75-22kW. In addition to reaching IE3 efficiency levels, copper rotor motors must also meet other technical requirements set for conventional motors so as to enable the motors to remain in proper working condition. In the following paragraphs, we illustrate these other technical characteristics of high-efficiency cast copper rotor motors by comparing and analyzing both copper rotor motors and the YX3 aluminum rotor motors (Chinese motor standard, roughly equivalent to IE2).
(1) Efficiency:
All copper rotor motor efficiencies are in accordance with the IE3 standard in IEC60034-30 and the test method for efficiency follows IEEE112 B.
(2) Temperature increase:
The conductivity of copper is around 170% of aluminum which can effectively reduce the losses in rotors. Additionally, the copper bars have about double the thermal conductivity of aluminum bars; accordingly, the use of copper in rotors can effectively reduce temperatures, allowing smaller air-gaps and reduced noise. The temperature increase, vibration and noise performance is better than that of YX3 motors
(3) Power factor:
We have found that the power factors of 0.75kW-7.5kW motors have, unhappily, been reduced by the use of copper. The reduction of power factors can be attributed to the higher efficiency, changes in start-up properties and the higher conductivity materials. This can be seen from the experimental data in Table 2 which compares the power factors of copper rotor high efficiency and super premium motors with YX3 series motors. Lower power factors lead to larger losses in cables and transformers and higher voltage drops. In practice, the slight reduction in power factor is not a concern as a power factor compensator can be used to raise the power factor. The cost of a power factor compensator accounts for only 1-3 percent of the total motor costs. This use of reactive power compensation reduces the losses in the network, fully utilizes the power capacitor, effectively lowers voltage turbulence and helps the motor operate within the designed voltage drop requirement.
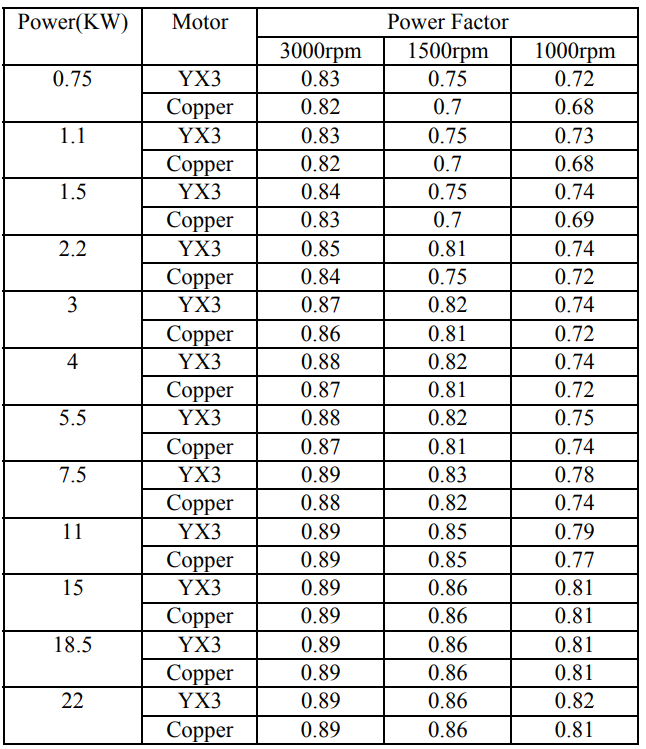
(4) Maximum torque multiple:
The value of the maximum torque multiple (=starting torque multiple) and the overload capacity are important characteristics of motors. Improving the torque multiple increases the motor’s capacity to fend-off overload damage. The maximum torque multiple of cast copper motors is higher than equivalent YX3 motors. Experimental details illustrating this are presented in Table III. The average maximum torque multiples of YX3 series motors is 2.4 times, while the average actual tested maximum torque multiples of copper rotor motors is 2.89 times. This is a more than 20 percent increase, which meets the requirements in the NEMA C design of US NEMA MG1. It demonstrates that the overload capacity of cast copper rotor motors is much better than that of conventional aluminum rotor motors.
(5) Locked torque multiples and locked current multiples:
Although copper’s increased conductivity increases motor efficiency, if the rotor bar geometry is not altered, the locked torque of a copper rotor motor is lower and locked current multiples are higher than conventional aluminum rotor motors. The rotor-bar geometry must be optimized to match the properties of copper to ensure that the locked performance of cast copper motors is as good as or better than conventional aluminum rotor motors. From the analysis of actual test data from motors, and with an optimized conductor-bar geometry, we find that when the cast copper rotor motors are designed for IE3 super premium efficiency, the maximum torque multiples show a clear increase, along with a higher overload capacity. The locked current multiples are lower than in conventional aluminum rotor motors, and the locked torque is stable with the motor having a better start-up performance. Power factors have been reduced to a certain extent but can be offset by power factor compensators. We conclude that the main performance parameters of IE3 copper rotor motors are reasonable after the designs have been optimized for copper in theory and on the test bench.
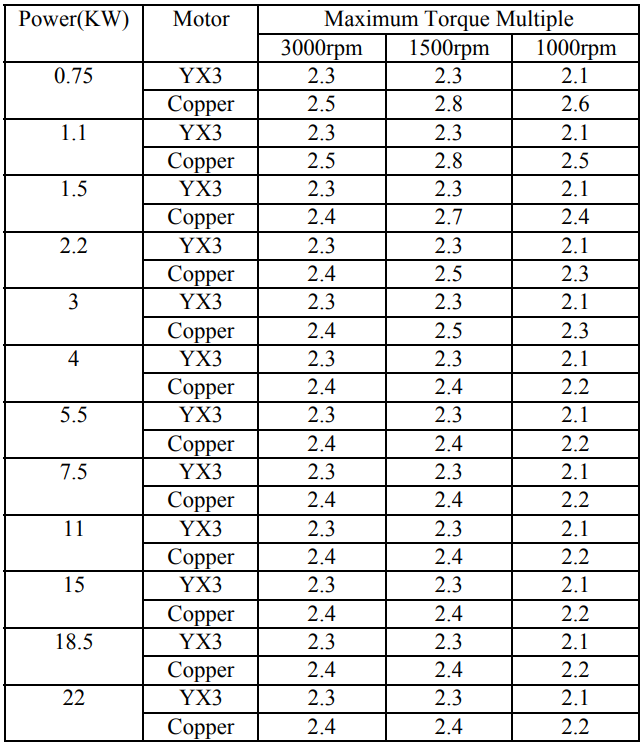
B. Achieving IE4 performance
In 2011, Nanyang Explosion Protection Group Co., Ltd announced China’s first IE4 efficiency motor by using cast copper rotors. At 30kW, with 6 poles and an efficiency of 94.3 percent, this optimized series of motors is mainly used in heavy duty applications such as pumps and compressors. As shown in Table IV, their efficiency levels exceed the currently-used permanent magnet motors.
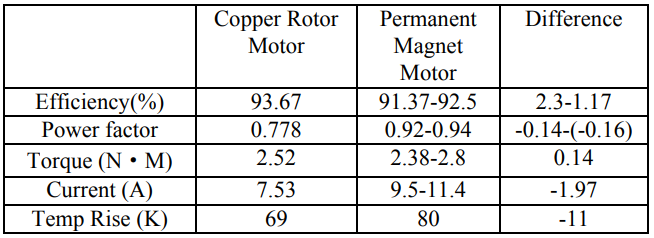
COMPARISON BETWEEN COPPER ROTOR MOTOR AND PM MOTORS
Copper rotor motors are ideal solutions for IE4 motors. Although the efficiency increase from IE3 to IE4 is not as much as that from IE2 to IE3, it is much more difficult to produce IE4 motors than IE3 motors. For example, for IE4 4 poles motors, the average efficiency level is around 94%, meaning the motor losses are only 6%, which is difficult to achieve using traditional materials and methods. A new material, new design, new technology or advanced processing is needed. In order to meet the IE4 efficiency standard, each type of loss must be further addressed:
(1) Stator copper loss
Reducing the stator copper loss is generally done by enlarging the stator slot and reducing the air gap. These measures are easier to implement on motors having large stator outer diameters.
(2) Rotor bar loss
Moving to cast copper rotor bars are a very effective way to increase motor efficiency to IE4 levels at a reasonable cost. Accordingly, the successful development of cast copper technology has been a very significant development for realizing IE4 motors.
(3) Iron loss
To reduce the iron loss, the approaches used include reducing the silicon-steel sheet thickness (from the conventional 0.50mm-thickness to 0.35mm-thickness) and using low-loss, cold-rolled silicon steel. An additional loss-reduction measure is the use of an anaerobic annealing process to reduce the internal stress generated during the lamination punching process. The annealing process can repair the deformed grain, the distorted lattice and the poorly-arranged magnetic domains caused by shearing at the lamination edges. As a result, the hysteresis loss in the silicon steel sheet is effectively reduced and the magnetic properties of the silicon steel sheet are recovered. In the development of a 0.75kW-4 super-high efficiency cast-copper-rotor motor, Nanyang Motor Co. Ltd. used this post-punching annealing process. As a result, the iron loss was reduced by 30% as compared with the process without annealing.
(4) Mechanical losses
For IE4 motors, we have found that the use of backwards style fans together with an accompanying conical fan cover increases air flow and reduces mechanical loss.
IV. CONCLUSION
Implementing a copper rotor is one of the simplest and most effective ways of improving an induction motor’s efficiency. The current development of die-casting technology has made it possible to mass produce high quality copper rotors both technically and economically. Copper rotor motors are proving a cost-effective way of meeting the new high-efficiency IE3 and IE4 standards. As the energy efficiency level of motors continues to improve, the era of highly efficient copper rotor motors has dawned.
V. REFERENCES
[1] Xingzhi Zhang, Wei Ni, and Bingfen Zhang, "Study of copper die-cast rotor ofsingle phase motors," China Micro Motor, pp. 31-37, 2010. [2] Li Zhi-qiang, Huang Jian, Zhang Wei, Chen Li-xia, Gu Wei-dong, Liu Fu-qian "Considerations about development of premium efficiency copper rotor three phase asynchronous motor series," Electric Machines & Control Application, pp. 17-20, 2010. [3] Rainer Kimmich, Martin Doppelbauer, "Performance characteristics of drive motors optimized for die-cast copper cages," EEMODS’05 Conference Proceedings, 2005.
VI. BIOGRAPHIES
Daniel Liang was born in Shanxi in China in 1978, received his M.S and B.S. degrees in Thermal Energy and Power from Tsinghua University, China. He is the Project Manager for the Copper Motor Rotor work at the International Copper Association. He also devotes his time to increasing energy-savings in motor-driven systems. Before joining ICA in 2003, Mr. Liang worked at Motorola as a senior mechanical engineer. He has much experience in tooling design and the casting process. Mr. Liang has authored or co-authored over 10 technical papers and holds 6 patents. Xu Yang is the Vice General Manager of Yunnan Copper Die Casting Co. Ltd. He is responsible for copper rotor R&D, production management and market development. Mr. Yang graduated from Chong Qing University in June 2000, with a bachelors degree in equipment engineering. He has authored or co-authored 6 technical papers and holds 8 patents. Jiabin Yu is a senior engineer at Nanyang Explosion Protection Group Co., Ltd. She is in charge of R&D work on high efficiency motors as well as copper rotor motors. Ms. Yu has more than 7 years experience with copper rotor motors and has designed more than 10 types of copper rotor motors. Ms. Yu graduated from Hu Nan Institute of Engineering with a bachelors degree in electrical motor engineering. She has authored or co-authored over 12 technical papers and holds 8 patents. Victor Zhou is the Director of China and South East Asia for the International Copper Association. He is responsible for managing the successful operations of market and technology development programs which include copper motor rotors for various applications. Mr. Zhou received his B.S. degree in Electrical Engineering and M.S. degree in System Engineering from Tianjin University, China, and his MBA from Peking University, China. He has authored or co-authored over 10 technical papers and holds 6 patents.