This article introduces the paper "Development of water soluble cores for investment casting – A review" presented in INDIAN ENGINEERING EXPORTS
1. Overview:
- Title: Development of water soluble cores for investment casting – A review
- Author: GANESH VIDYARTHEE & NANDITA GUPTA
- Publication Year: JANUARY 2020
- Publishing Journal/Academic Society: INDIAN ENGINEERING EXPORTS
- Keywords: Investment Casting, water soluble cores, salt cores, mechanical properties, environmental impact.
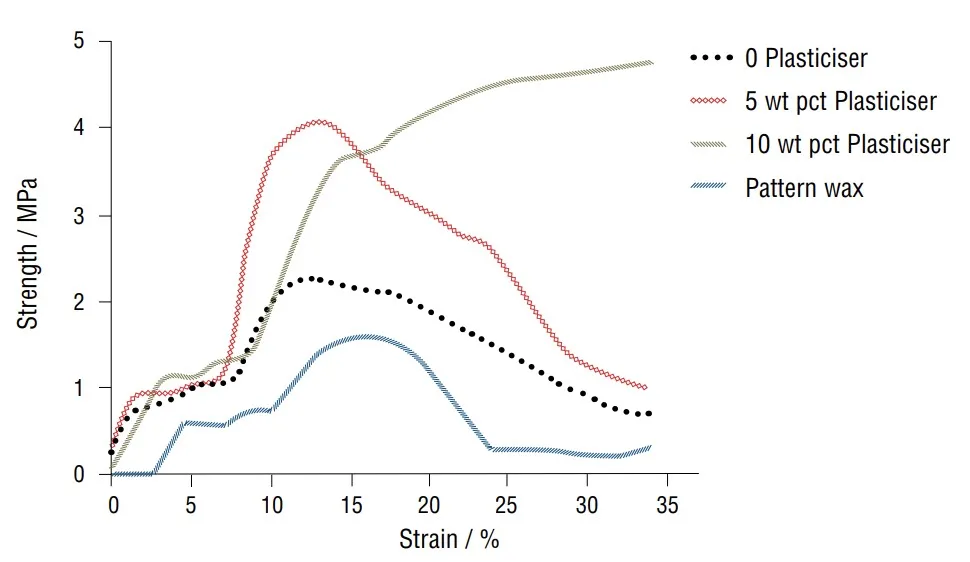
2. Research Background:
Investment Casting utilizes wax patterns for creating complex castings. Cores are essential for forming internal geometries like undercuts and channels within these castings. Traditionally, core removal post-casting involves methods such as solvent use, steam autoclaving, or flash firing at high temperatures. These conventional methods increase production costs and are often inefficient. For castings with intricate internal features, traditional ceramic or salt cores are sometimes avoided, opting for direct wax patterns where feasible. However, creating complex wax patterns can be challenging.
Water-soluble salt cores emerged in foundries in the 1970s, with significant adoption in the 1990s, particularly for mass-producing diesel engine pistons. Simple shapes like rings and holes are manufactured from compacted cooking salt (NaCl) under high pressure, enabling blank casting and facilitating complex designs. However, mechanically cleaning areas accessed via these cores can be difficult. Existing salt cores meet primary strength (cold strength) and hot strength (650-700°C) requirements but face limitations.
Current salt core manufacturing involves casting salt melt in core boxes, oven storage at a minimum of 200°C to prevent moisture absorption, and compaction of mildly moistened salt under high pressure. Grain conglomeration and recrystallization occur under low pressure (30-50 MPa) at 500-750°C or high pressure (136-362.8 MPa) at a lower sintering temperature (180-300°C) for stress release. Another method involves shooting a mixture with inorganic binders like Na-2CO3, hardened by CO2 or thermal dehydration (180-210°C). These salt cores generally exhibit low strength and are unsuitable for high-pressure casting applications.
Polyvinyl Glycol (PVG) is explored as a water-soluble waxy material for cores. PVG can be leached from wax patterns due to its water solubility and low hygroscopic coefficient, allowing cores to remain longer. It is non-toxic and commercially available. However, PVG cores are deficient as they are intended for use in pasty conditions and are prone to surface cracks upon solidification.
This research addresses the need to improve salt core technology by investigating binder variations to enhance strength, considering salt crystal shapes and granulometry, and exploring composite salts with additives, along with hydration and dissolution kinetics in water.
3. Research Purpose and Research Questions:
Research Purpose:
The primary aim of this research is to explore the potential of using salt cores in investment casting. This includes evaluating the feasibility of salt core utilization and focusing on developing enhanced mechanical properties for castings made with these cores. Furthermore, the study investigates the environmental benefits associated with using these water-soluble cores.
Key Research Questions:
This study implicitly seeks to answer the following key questions:
- Can the mechanical strength of water-soluble salt cores be improved through modifications in composition and the addition of plasticizers?
- What is the optimal composition of water-soluble salt cores, incorporating polyethylene glycol, mica powder, sodium chloride, and plasticizer, to achieve a balance of mechanical strength, hygroscopic properties, and solubility?
- How does the addition of plasticizer affect the compressive strength, bending strength, hygroscopic coefficient, and solubility rate of the developed salt cores?
- Is it possible to develop a water-soluble core material that is environmentally friendly, easy to remove after casting, and suitable for producing dimensionally accurate and smooth castings in investment casting?
Research Hypotheses:
While not explicitly stated, the research operates under the hypothesis that:
- By carefully controlling the composition of salt cores, particularly by incorporating plasticizers and additives like mica powder and polyethylene glycol, it is possible to significantly improve their mechanical properties, making them more suitable for investment casting applications.
- The developed water-soluble cores will offer environmental advantages due to the potential for recycling salt and water used in the core removal process.
4. Research Methodology
Research Design:
The research employs an experimental design to evaluate the properties of water-soluble cores with varying compositions. Three different compositions of core materials were prepared by varying the amount of plasticizer (0%, 5%, and 10% by weight).
Data Collection Method:
The following tests were conducted to assess the properties of the developed core materials:
- Compressive Strength Test: Measured using a universal strength testing machine to determine the compressive strength of the core samples.
- Bending Strength Test: Performed using a three-point bending fixture to evaluate the flexural strength of the core materials.
- Hygroscopic Property Test: Samples were exposed to air at room temperature (50-70% relative humidity) for one month, and the change in mass was measured to calculate the hygroscopic coefficient.
- Solubility Test: Samples were immersed in water to determine the solubility rate of the core material.
Analysis Method:
Quantitative analysis was used to evaluate the data collected from the tests. This included:
- Calculating the compressive strength and bending strength values for each composition.
- Determining the hygroscopic coefficient using the formula: H = [(Wt-Wo)/W0] × 100%, where Wt is the mass after one month and Wo is the initial mass.
- Calculating the solubility rate using the formula: R = M/(S×T), where M is the mass dissolved, S is the surface area, and T is the dissolution time.
- Graphical analysis was performed to visualize the relationship between compressive stress and strain (Figure 1) and the relationship between bend strength and plasticizer content (Figure 2). Microscopic analysis was conducted to examine the fracture surface of the core materials (Figure 3).
Research Subjects and Scope:
The research focused on developing and testing water-soluble cores made from the following materials:
- Polyethylene Glycol
- Mica Powder
- Sodium Chloride
- Plasticiser (varied at 0%, 5%, and 10% by weight)
- Solvent (to dissolve polyethylene glycol)
The scope of the research was limited to evaluating the mechanical properties (compressive and bending strength), hygroscopic properties, and solubility of these composite core materials. The samples were prepared in dimensions of 6mm x 6mm x 10mm for testing.
5. Main Research Results:
Key Research Results:
- A novel water-soluble core material was successfully developed.
- The yield strength of the soluble core material reached up to 1 MPa.
- The highest compressive strength achieved was 4 MPa (Figure1).
- The bending strength of the soluble core materials ranged from 4.08 to 6.65 MPa (Table4).
- The hygroscopic coefficient ranged from 0.06% to 0.22% per month under ambient conditions (Table2).
- The solubility rate of core materials decreased with increasing plasticizer content (Table3).
- Exposing the core without plasticizer for one hour resulted in a loose surface (Table3).
- 5% plasticizer content provided a modified compressive strength suitable for core production.
- Mica was identified as a good, economical, and eco-friendly additive for strength and smoothness.
- Polyethylene, being ductile and non-toxic, contributes to bond strength.
- An increase in plasticizer content led to an increase in bond strength (Figures 2, 3).
- Mica and polyethylene contribute to the stability of water-soluble cores and reduce moisture absorption.
- Up to 5% polyethylene glycol prevents crack formation, provides a smooth surface, and stabilizes the core. Beyond 5%, it reduces the solubility rate.
- A recommended mixture for optimum strength is composed of 43% polyethylene glycol, 30% mica powder, 25% sodium chloride powder, and 5% plasticizer.
- This type of soluble core is robust enough to withstand composite pattern injection and can be leached out in a suitable time. Hardness is important in preventing cracks. Increased strength due to plasticizer reduces collapsibility and may require longer core removal times.
Statistical/Qualitative Analysis Results:
- Table1: Component of soluble core material (wt %) shows the compositions of the three samples with varying plasticizer content (0%, 5%, 10%).
- Table2: Mass and hygroscopic coefficient of the core material presents the mass change and hygroscopic coefficient for the three compositions after one month of air exposure. The hygroscopic coefficient decreases with increasing plasticizer.
- Table3: Different sample mass, surface area, and soluble time shows the solubility rate for different plasticizer contents. Solubility rate decreases with increasing plasticizer.
- Table4: Bending strength indicates that bending strength increases with increasing plasticizer content, ranging from 4.08 MPa (0% plasticizer) to 6.65 MPa (10% plasticizer).
- Figure1: Compressive stress and strain curves of wax and core material illustrates the compressive strength of core materials with 0%, 5%, and 10% plasticizer, compared to pattern wax. 5% plasticizer shows modified compressive strength.
- Figure2: Relationship between bend strength and the amount of plasticizer and 10 wt pct (c) 15 wt pct demonstrates the increase in bend strength with increasing plasticizer content.
- Figure3: Fracture surface micrograph of the soluble core material with plasticiser 0 (a), 5 wt pct (b) and 10 wt pct (c) 15 wt pct provides visual evidence of the core structure with different plasticizer levels.
Data Interpretation:
The results indicate that incorporating plasticizer into the water-soluble core composition enhances its mechanical properties, particularly bending and compressive strength. The addition of mica powder and polyethylene glycol contributes to core stability and reduces moisture absorption. While plasticizer improves strength, it also reduces the solubility rate. A balance is achieved with a 5% plasticizer content, offering improved strength without significantly compromising solubility. The recommended composition provides optimal strength for investment casting applications.
Figure Name List:
- Figure1: Compressive stress and strain curves of wax and core material
- Figure2: Relationship between bend strength and the amount of plasticizer and 10 wt pct (c) 15 wt pct
- Figure3: Fracture surface micrograph of the soluble core material with plasticiser 0 (a), 5 wt pct (b) and 10 wt pct (c) 15 wt pct
- Table1: Component of soluble core material (wt %)
- Table2: Mass and hygroscopic coefficient of the core material
- Table3: Different sample mass, surface area, and soluble time
- Table4: Bending strength
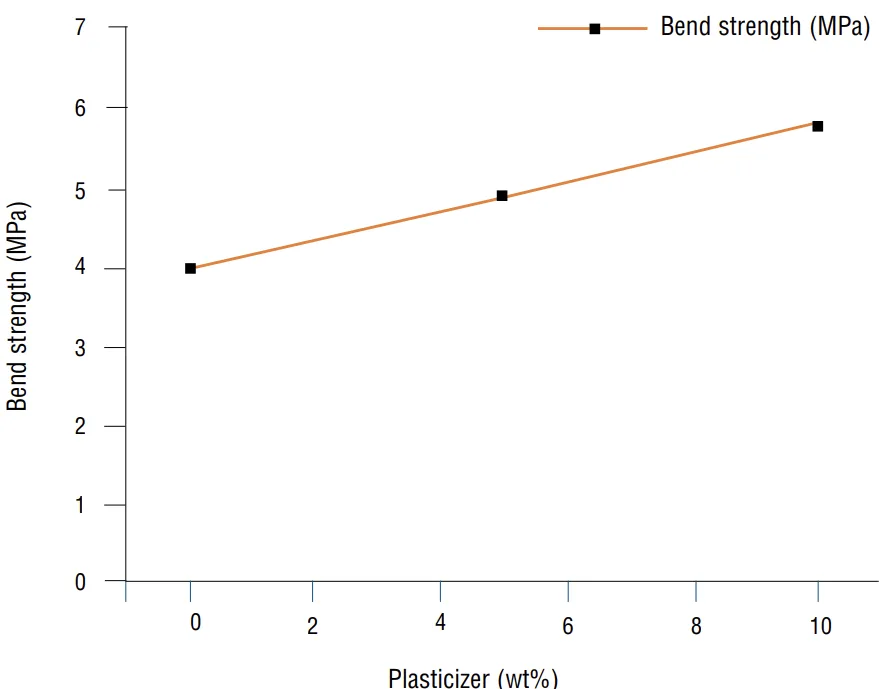
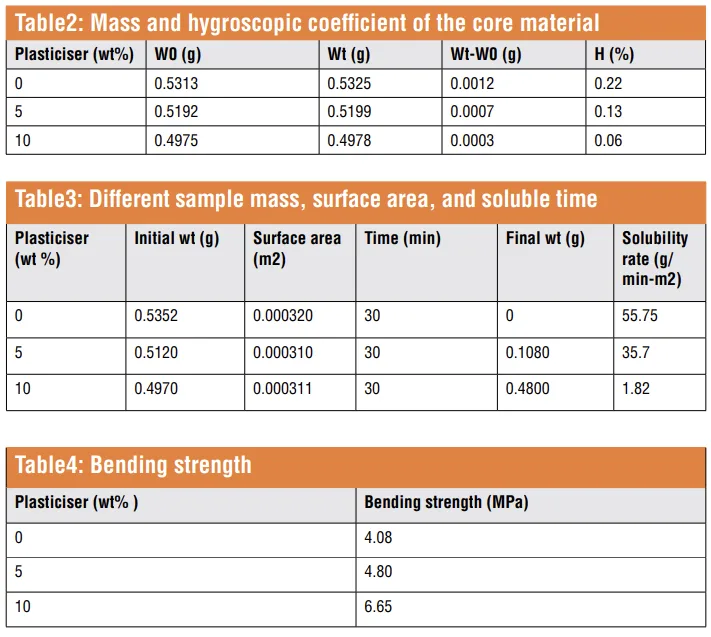
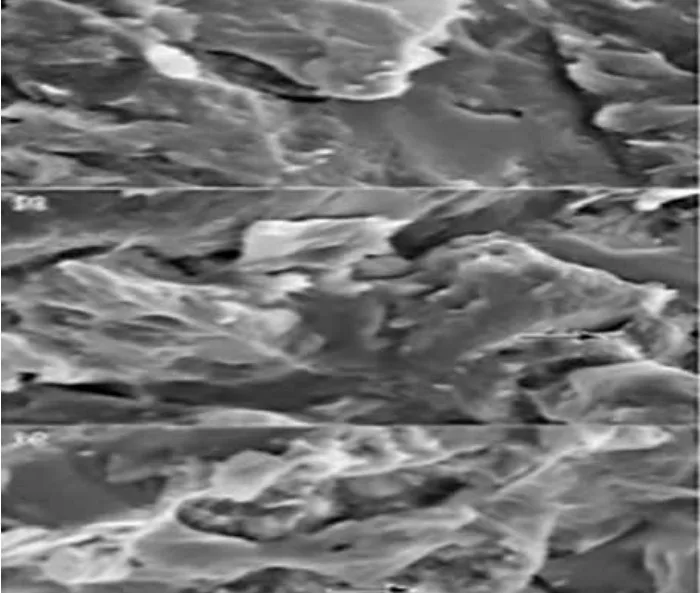
6. Conclusion and Discussion:
Summary of Main Results:
This research successfully developed a novel water-soluble core material for investment casting with enhanced mechanical properties. The developed cores enable the production of dimensionally accurate and smooth castings without requiring protective coats. These cores are water-soluble, offering the potential for recycling salts and water, making them environmentally friendly. They possess sufficient storage stability under normal climatic conditions and exhibit improved mechanical properties compared to traditional salt cores.
Academic Significance of the Research:
This study contributes to the field of investment casting by demonstrating the feasibility of using modified salt core compositions to overcome limitations associated with conventional core materials. The research provides valuable data on the impact of plasticizers and additives on the mechanical, hygroscopic, and solubility characteristics of water-soluble cores. This work expands the understanding of water-soluble core technology and offers a basis for further research and development in this area.
Practical Implications:
The findings of this research have significant practical implications for the investment casting industry. The developed water-soluble core offers a viable alternative to traditional cores, simplifying core removal processes and potentially reducing production costs. The recommended core composition, comprising 43% polyethylene glycol, 30% mica powder, 25% sodium chloride, and 5% plasticizer, provides a directly applicable formulation for industrial use. The environmental friendliness of these cores further enhances their appeal for sustainable manufacturing practices.
Limitations of the Research:
The study acknowledges that salt cores, in general, suffer from contraction and volume shrinkage during solidification. Additionally, high density in some core formulations can impede water dissolution, making core removal challenging in certain cases.
7. Future Follow-up Research:
Directions for Follow-up Research:
Future research should focus on addressing the limitations identified in this study. Key directions for follow-up research include:
- Investigating methods to eliminate or minimize shrinkage and volume contraction during the solidification of salt cores. The paper suggests exploring mixtures of salt and sand with a melting point of 820°C to mitigate shrinkage.
- Exploring techniques for producing cores under pressure to improve density control and potentially enhance dissolution characteristics.
- Further optimization of the core composition and manufacturing process to achieve even higher mechanical strength and improved solubility rates.
- Investigating the recyclability and environmental impact in more detail, including life cycle assessments.
Areas Requiring Further Exploration:
Further exploration is needed in areas such as:
- The long-term storage stability of the developed cores under various environmental conditions.
- The performance of these cores with different casting alloys and complex casting geometries.
- The economic feasibility of large-scale production and implementation of these water-soluble cores in industrial settings.
8. References:
- Suo Tu et al. 'Fabrication and Characterization of High-Strength Water Soluble Composite Salt Core for Zinc Alloy Die Castings, # Springer-Verlag London Ltd, 2017
- Z Xiao et al. 'A Water-Soluble Core Material for Manufacturing Hollow Composite Sections, Composite Structures 182 (2017), p 380-90
- Jing-jing Liang et al. 'Influence of Zircon on Cristobalite Crystallization of Silica-Based Ceramic Cores,' Journal of Ceramic Processing Research, vol 17, no.8, (2016), p 845-50
- Jaroslav Beòo et al. 'Development of Composite Salt Cores for Foundry Applications, MTAEC9, 49(4) 619 (2015)
- P Jelínek et al. 'Advances in Technology of Soluble Cores for Die Castings,' Archives of Foundry Engineering, vol 15, issue 2, 2015, p 29-34
- EliSka Adámková et al. 'Water-Soluble Cores – Verifying Development Trends,' MTAEC9, 49(1) 61 (2015)
- P Jelínek et al. 'Lost Cores for High-Pressure Die Casting,' Archives of Foundry Engineering, vol 15, issue 2, 2014, p 101-04
- Petr Jelínek et al. 'Development of Foundry Cores Based on Inorganic Salts,' Materials and Technology 47 (2013) 6, p 689-93
- Fei Wang et al. 'Gel-Casting of Fused Silica Based Core Packing for Investment Casting Using Silica Sol as a Binder, Journal of the European Ceramic Society 33 (2013), p 2745-49
- Weiguo Jiang et al. 'Preparation and Properties of Novel Water Soluble Core Material, J. Mater. Sci. Technol., 2010, 26(3), p 270-75
- Ladisla Tomek et al. 'Water Soluble Cores for Aluminium Investment Castings, 13th World Conference on Investment Casting, 2012, Kyoto, Japan
- Yaokawa J et al. 'Strength of Salt Core Composed of Alkali Carbonate and Alkali Chloride Mixtures made by Casting Technique, Mater Trans, 2007, 48(5):1034-41
- MJ Nadolski et al. 'The Investigation of properties of Investment casting moulds reinforced with ceramic fibre, Archives of Foundry Engg, Vol 7, Issue 4/2007, 127-30
- J Barbosa et al. 'Characterisation of Metal/Mould Interface on Investment Casting of c-TiAl, International Journal of Cast Metals Research, 2006, vol 19, no.6
- S Sabau, 'Numerical Simulation of the Investment Casting Process, AFS Transactions 2005 © American Foundry Society, Schaumburg, IL, USA
9. Copyright:
This material is GANESH VIDYARTHEE & NANDITA GUPTA's paper: Based on Development of water soluble cores for investment casting – A review.
Paper Source:
This material was summarized based on the above paper, and unauthorized use for commercial purposes is prohibited.
Copyright © 2025 CASTMAN. All rights reserved.