This introduction paper is based on the paper "Development of Water-Soluble Composite Salt Sand Cores Made by a Hot-Pressed Sintering Process" published by "ARCHIVES of FOUNDRY ENGINEERING".
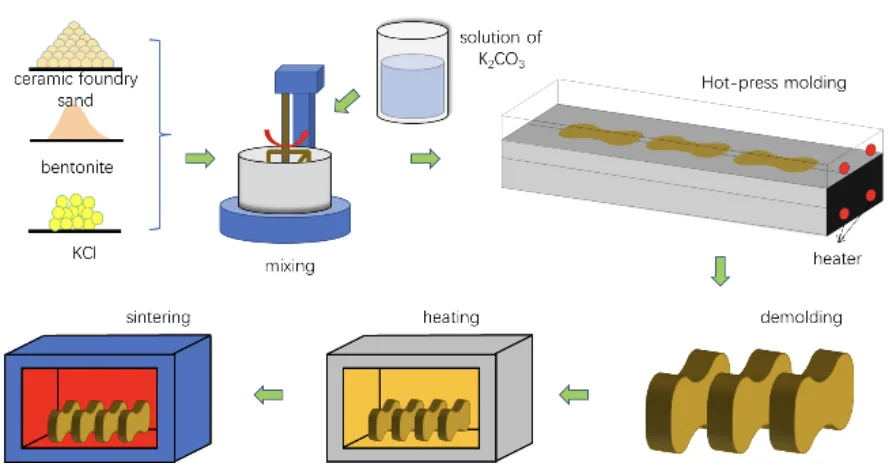
1. Overview:
- Title: Development of Water-Soluble Composite Salt Sand Cores Made by a Hot-Pressed Sintering Process
- Author: Xiaona Yang, Long Zhang, Xing Jin, Jun Hong, Songlin Ran, Fei Zhou
- Year of publication: 2023
- Journal/academic society of publication: ARCHIVES of FOUNDRY ENGINEERING (Published quarterly as the organ of the Foundry Commission of the Polish Academy of Sciences)
- Keywords: Water-soluble cores, Hollow composite castings, Salt cores, Collapsibility
2. Abstract:
A wide variety of water-soluble cores are widely used in hollow composite castings with internal cavities, curved channels, and undercuts. Among them, the cores made by adding binders of inorganic salts in the form of aqueous solutions have excellent solubility in water. However, excellent collapsibility is often accompanied by poor moisture absorption resistance. In this study, a water-soluble core with moderate strength and moisture absorption resistance was prepared by hot pressing and sintering the core sand mixture of sand, bentonite, and composite salts, and a tee tube specimen was cast. The experimental results showed that the cores with KCl-K2CO3 as binder could obtain strength of more than 0.9 MPa and still maintain 0.3 MPa at 80±5% relative humidity for 6 hours; the subsequent sintering process can significantly improve the resistance to moisture absorption of the hot pressed cores (0.6 MPa after 24 hours of storage at 85±5% relative humidity); the water-soluble core prepared by the post-treatment can be used to cast tee pipe castings with a smooth inner surface and no porosity defects, and it is easy to remove the core.
3. Introduction:
The water-soluble core is a component made of water-soluble salt as the primary material [1-4] or binder [5-7] for forming the inner surface of castings. It is widely used in high-pressure die casting and other casting processes (gravity, low-pressure) for manufacturing castings with complex cavities or curved channels, particularly for lightweight and integrated components in automotive and sanitary ware industries [8-11]. This is due to their excellent water-soluble collapsibility and environmental friendliness. While high-strength cores (often made by casting salt melts) are needed for die casting, lower strength cores are suitable for gravity or low-pressure casting, allowing for processes like pressure sintering or binder bonding. However, many water-soluble cores, especially those with excellent collapsibility like K2CO3-bonded cores [14], suffer from poor moisture absorption resistance, limiting their direct use in humid environments [15]. Using KCl as a binder offers better humidity resistance but lower solubility leads to higher water content and potentially lower strength. This paper explores a composite KCl-K2CO3 salt binder system, prepared by hot pressing followed by sintering, aiming to leverage the high strength of K2CO3 and the better humidity resistance of KCl.
4. Summary of the study:
Background of the research topic:
Water-soluble cores are essential for producing hollow castings with complex internal geometries (cavities, channels, undercuts). Their key advantages are excellent collapsibility in water and environmental friendliness, making them suitable for lightweighting applications in various industries. However, a common challenge is balancing good collapsibility with sufficient resistance to moisture absorption during storage and handling.
Status of previous research:
Previous research explored various water-soluble core types:
- Casting method: Mainly for high-strength cores in die casting.
- Pressure sintering: Jaroslav [12] used slightly wet KCl for gravity casting magnesium alloys.
- Binder bonding: Liu [13] used MgSO4 binder with microwave heating.
- Hot pressing: Zhang [14] used K2CO3 aqueous solution binder, achieving high strength (up to 2.5 MPa) suitable for gravity casting, but these cores were susceptible to moisture absorption.
- Post-treatment: Zhang et al. [15] improved humidity resistance of K2CO3 cores using a precipitation method involving CaCl2 and heating, converting K2CO3 to less hygroscopic KCl.
- Direct KCl binder use is limited by its lower solubility, requiring more water, which can reduce strength.
Purpose of the study:
The study aimed to develop a water-soluble sand core using a composite KCl-K2CO3 salt binder prepared via a two-step process: low-temperature hot pressing followed by higher-temperature sintering. The goal was to achieve a core with moderate strength, significantly improved moisture absorption resistance compared to simple hot-pressed cores, while maintaining good water-soluble collapsibility for easy removal after casting.
Core study:
The research involved preparing water-soluble sand cores using silica sand, bentonite, and a composite binder of KCl and K2CO3. The process involved hot pressing the mixture, followed by a sintering step. The study systematically investigated the influence of various parameters on core properties:
- Hot Pressing Stage: Effects of heating time, KCl/K2CO3 ratio, heating temperature, composite salt content (sand ratio), and bentonite content on the initial tensile strength. Moisture absorption and storage strength under controlled humidity were also evaluated for hot-pressed cores.
- Sintering Stage: Effects of sintering temperature and time on the final tensile strength. Evaluation of moisture absorption rate and storage strength of sintered cores.
- Core Properties: Measurement of gas evolution, tensile strength after soaking in water (collapsibility), and microstructural analysis using SEM-EDX.
- Casting Trial: A practical test casting a simple hollow aluminum alloy component (tee pipe) using the developed core.
5. Research Methodology
Research Design:
The study employed an experimental approach. Water-soluble sand core samples ("8" dog-bone shape) were prepared using a hot-pressing method followed by a sintering process. Key parameters like binder composition (KCl/K2CO3 ratio), binder amount, bentonite content, heating temperature/time, and sintering temperature/time were systematically varied. The properties of the resulting cores were measured and analyzed. Finally, a casting trial was conducted to validate the core's performance in a practical application.
Data Collection and Analysis Methods:
- Materials: Dalin silica sand (70/100 mesh), analytical grade K2CO3 and KCl, 400 mesh bentonite.
- Sample Preparation: Raw sand, bentonite, and KCl were mixed. K2CO3 solution was added and mixed. The mixture was pressed in a heated mold (hot pressing) and demolded. Samples were then heated in an oven and subsequently sintered in a resistance box at higher temperatures.
- Property Testing:
- Tensile Strength (Initial and Storage): Measured using a SWY universal hydraulic strength testing machine. Storage strength was measured after exposing samples to controlled humidity (80±5% RH or 85±5% RH) for specific durations.
- Moisture Absorption Rate: Calculated from weight gain measured by a JA5003N electronic balance after exposure to controlled humidity. Formula: w = (Mt-Mo)/Mo×100%.
- Water Solubility/Collapsibility: Assessed by measuring the decrease in tensile strength after immersing samples in water for varying times.
- Microstructure: Observed using Scanning Electron Microscopy (SEM, FEI Co., Ltd., Netherlands), with elemental analysis via Energy Dispersive X-ray spectroscopy (EDX).
- Gas Evolution: Measured and compared to other core types (data from reference [13]).
- Casting Test: A tee pipe was cast using ZL101A aluminum alloy at 700 °C pouring temperature. Core removal and casting quality were assessed visually.
Research Topics and Scope:
The research focused on developing and characterizing water-soluble cores bonded with a KCl-K2CO3 composite salt system using a hot-press sintering process. The scope included:
- Optimizing the hot-pressing parameters (binder composition, salt content, bentonite addition, temperature, time) for initial strength.
- Investigating the moisture absorption behavior and storage strength of hot-pressed cores.
- Determining the effect of sintering temperature and time on final tensile strength, moisture resistance, and storage strength.
- Understanding the mechanism of strength development and moisture resistance improvement through thermodynamic analysis (Gibbs free energy) and microstructural observation (SEM-EDX).
- Evaluating the core's gas evolution characteristics.
- Assessing the core's collapsibility by measuring strength loss during water soaking.
- Validating the core's performance through an aluminum alloy casting trial.
6. Key Results:
Key Results:
- Hot-pressed cores using KCl-K2CO3 binder (optimum near 60 wt.% K2CO3 in composite salt, 10 wt.% composite salt to sand, 1 wt.% bentonite, heated ~140-160 °C for 1h) achieved initial tensile strength > 0.9 MPa.
- However, these hot-pressed cores showed significant strength loss in humid conditions (reduced to ~0.3 MPa after 6 hours at 80±5% RH) due to moisture absorption (deliquescence), limiting their application.
- Subsequent sintering (e.g., at 750 °C for 1h) significantly improved moisture resistance. Sintered cores maintained higher strength (e.g., 0.58 MPa after 24 hours at 85±5% RH) and had much lower moisture absorption rates compared to unsintered cores.
- Thermodynamic analysis (Fig. 9) suggests K2CO3 reacts with SiO2 and Al2O3 (from sand and bentonite) during sintering to form potassium silicates (K2O*mSiO2) and aluminosilicates (KAlSimOn), which likely have lower hygroscopicity than K2CO3.
- Sintered cores exhibited low gas evolution (6.6 mL/g for 750 °C sintering), favorable for casting aluminum alloys (Table 1).
- Despite improved moisture resistance, the sintered cores retained excellent water-soluble collapsibility, rapidly losing strength upon soaking in water (< 0.2 MPa after 60 seconds), ensuring easy removal from castings (Fig. 12).
- SEM analysis (Fig. 13) showed sintering created smoother salt coatings and more robust bonding bridges compared to unsintered cores. Exposure to humidity caused cracks in the sintered structure, explaining the eventual strength decrease. EDX analysis (Fig. 14) confirmed the presence of K, Cl, Si, O, and elements from bentonite (Al, Mg, Fe) in relevant locations.
- A casting trial using ZL101A aluminum alloy successfully produced a hollow tee pipe casting with a smooth internal surface and no defects, demonstrating the core's ability to withstand casting conditions and be easily leached out afterwards (Fig. 15).
Figure Name List:
- Fig. 1. The flowchart of the manufacturing process
- Fig. 2. Effect of heating time and proportion of composite salts on the tensile strength of water-soluble cores
- Fig. 3. Effect of placement time and K2CO3 proportion on water absorption of water-soluble cores
- Fig. 4. Effect of placement time and K2CO3 proportion on storage strength of water-soluble cores
- Fig. 5. Effect of heating temperature on the tensile strength of water-soluble cores
- Fig. 6. Effect of composite salt content on the tensile strength of water-soluble cores
- Fig. 7. Effect of bentonite content on the tensile strength of water-soluble cores
- Fig. 8. Effect of sintering temperature and sintering time on tensile strength sintered for (a) 30 min, (b) 60 min, and (c) 90 min
- Fig. 9. Gibbs free energies variation of reactions
- Fig. 10. Effect of placement time and sintering temperature on the moisture absorption rate of water-soluble cores
- Fig. 11. Effect of storage time and sintering temperature on the storage strength of water-soluble cores
- Fig. 12. Effect of soaking time on tensile strength
- Fig. 13. Fracture morphology of the water-soluble cores. (a) water-soluble core without sintering; (b) a single sand particle coated with K2CO3 and KCl; (c) water-soluble core sintered at 700 °C for 1 h; (d) water-soluble core sintered at 750 °C for 1 h; (e) water-soluble core of (c) placed in the RH of 85-90% for 24 h; (f) water-soluble core of (e) placed in the RH of 85-90% for 24 h.
- Fig. 14. EDX analysis of water-soluble core at the point of (a) and (b) in fig. 14(b), (c) and (d) in fig. 14(c)
- Fig. 15. The photo of aluminum alloy casting fabricated by water-soluble core and leached by water. (a) Casting molds with water-soluble cores fixed; (b) Aluminum alloy casting with the water-soluble core; (c) Dissected casting
7. Conclusion:
The study developed and optimized a water-soluble KCl-K2CO3 bonded sand core using a hot-press sintering process. Key conclusions are:
1) The un-sintered (hot-pressed only) composite salt core achieved strength > 0.9 MPa but reduced to 0.3 MPa after 6 hours at 80 ± 5% RH. Optimal conditions found were: 10 wt.% composite salts (with 60 wt.% K2CO3), 1 wt.% bentonite, curing at 140 °C for 1 h. This meets gravity casting needs but has limited applicability due to humidity sensitivity.
2) Sintering at 750 °C for 1 h effectively improved the anti-hygroscopic properties of the core, reduced gas evolution (6.6 mL/g), and allowed for collapse within 80 minutes of soaking.
3) The improved moisture resistance of sintered cores is attributed to KCl and the formation of reaction products (K2O*mSiO2 and KAlSimOn) which are less hygroscopic than K2CO3. The sintered core maintained high tensile strength even after 24 h exposure at 85±5% RH. The presence of readily soluble KCl ensures good leachability after casting.
8. References:
- [1] Huang, R. & Zhang, B. (2017). Study on the composition and properties of salt cores for zinc alloy die casting. International Journal of Metalcasting. 11(3), 440-447. DOI: 10.1007/s40962-016-0086-7.
- [2] Tu, S., Liu, F., Li, G., Jiang, W., Liu, X. & Fan, Z. (2018). Fabrication and characterization of high-strength water-soluble composite salt core for zinc alloy die castings. The International Journal of Advanced Manufacturing Technology. 95(1-4), 505-512. DOI: 10.1007/s00170-017-1208-y.
- [3] Yaokawa, J., Miura, D., Anzai, K., Yamada, Y. & Yoshii H. (2007). Strength of salt core composed of alkali carbonate and alkali chloride mixtures made by casting. Materials Transactions. 48(5), 1034-1041. DOI: 10.2320/matertrans.48.1034.
- [4] Lichý, P., Beňo, J. & Morys, M. (2014). Influence of ecologically friendly cores on surface quality of castings based on magnesium alloys. Metalurgija. 53(3), 303-306.
- [5] Xiao, Z., Harper, L.T., Kennedy, A.R. & Warrior, N.A. (2017). A water-soluble core material for manufacturing hollow composite sections. Composite Structures. 182(15), 380-390. DOI: 10.1016/j.compstruct.2017.09.058.
- [6] Beňo, J., Adámková, E., Mikšovský, F. & Jelínek, P. (2015). Development of composite salt cores for foundry applications. Materiali in Tehnologije. 49(4), 619-623. DOI: 10.17222/mit.2013.160.
- [7] Jelínek, P., Mikšovský, F., Beňo, J. & Adámková, E. (2013). Development of foundry cores based on inorganic salts. Materiali in Tehnologije. 47(6), 689-693.
- [8] Cornacchia, G., Dioni, D., Faccoli, M., Gislon, C., Solazzi, L., Panvini, A. & Cecchel, S. (2019). Experimental and numerical study of an automotive component produced with innovative ceramic core in high pressure die casting (HPDC). Metals. 9(2), 217, 1-21. DOI: 10.3390/met9020217.
- [9] Liu, F., Fan, Z., Liu, X., He, J. & Li, F. (2016). Aqueous gel casting of water-soluble calcia-based ceramic core for investment casting using epoxy resin as a binder. The International Journal of Advanced Manufacturing Technology. 86(5-8), 1235-1242. DOI: 10.1007/s00170-015-8227-3.
- [10] Fuchs, B., Eibisch, H. & Korner, C. (2013). Core viability simulation for salt core technology in high-pressure die casting. International Journal of Metalcasting. 7, 39-45. DOI: 10.1007/BF03355557.
- [11] Liu, F., Tu, S., Gong, X., Li, G., Jiang, W., Liu, X. & Fan, Z. (2020). Comparative study on performance and microstructure of composite water-soluble salt core material for manufacturing hollow zinc alloy castings. Materials Chemistry and Physics. 252, 1-10. DOI: 10.1016/j.matchemphys.2020.123257.
- [12] Beňo, J., Lichý, P., Cagala, M., Jelínek, P., Bruska, M., Gál, K., Morys, M. (2013). Utilization of ecological friendly cores for magnesium alloys castings. In METAL 2013 : 22nd International Conference on Metallurgy and Materials, 15 – 17 May 2013. Brno, Czech Republic: Tagner.
- [13] Liu, F., Jiang, P., Huang, Y., Jiang, W., Liu, X. & Fan, Z. (2018). A water-soluble magnesium sulfate bonded sand core material for manufacturing hollow composite castings. Composite Structures. 201, 553-560. DOI: 10.1016/j.compstruct.2018.06.084.
- [14] Zhang, L., Li, Y. & Chen, Q. (2011). Optimization of the mixture design of the fomula for water-soluble cores. Journal of Huazhong University of Science and Technology (Natural Science Edition). 39(3), 6-9.
- [15] Zhang, L., Li, Y. & Zhao, W. (2011). Improvement of humidity resistance of water soluble core by precipitation method. China Foundry. 8(2), 212-217.
- [16] Bruch, L.W., Glebov, A., Toennies, J.P. & Weiss, H. (1995). A helium atom scattering study of water adsorption on the NaCl(100) single crystal surface. The Journal of Chemical Physics. 103(12), 5109-5120. DOI: 10.1063/1.470598.
9. Copyright:
- This material is a paper by "Xiaona Yang, Long Zhang, Xing Jin, Jun Hong, Songlin Ran, Fei Zhou". Based on "Development of Water-Soluble Composite Salt Sand Cores Made by a Hot-Pressed Sintering Process".
- Source of the paper: https://doi.org/10.24425/afe.2023.146662
This material is summarized based on the above paper, and unauthorized use for commercial purposes is prohibited.
Copyright © 2025 CASTMAN. All rights reserved.