This introductory paper is the research content of the paper ["Development of High Ductility Al-Zn-Mg Casting Alloys for Automotive Structural Components"] published by [MS&T19®].
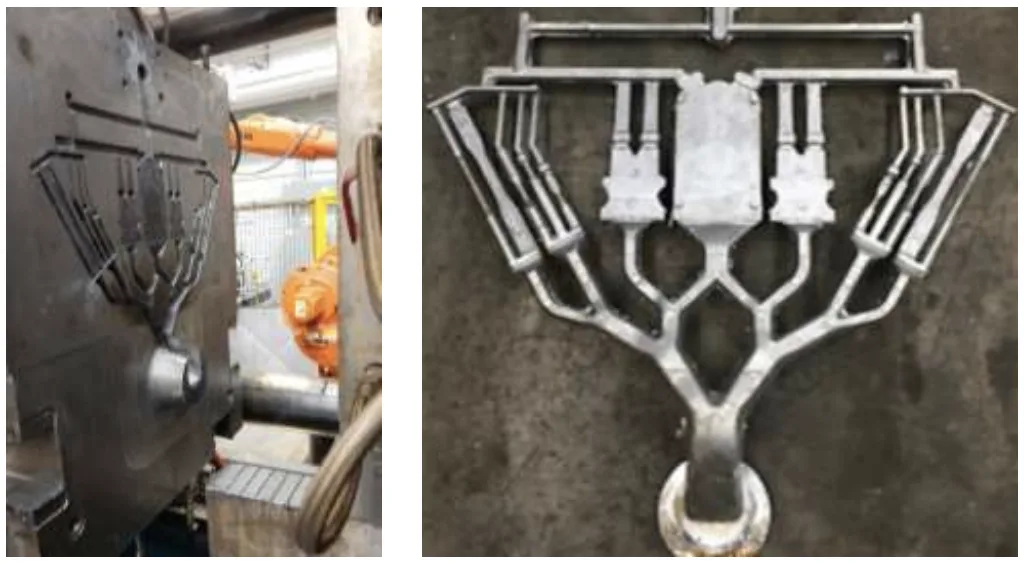
1. Overview:
- Title: Development of High Ductility Al-Zn-Mg Casting Alloys for Automotive Structural Components
- Author: A. Lombardi, G. Byczynski, C. Wu, X. Zeng, S. Shankar, G. Birsan, and K. Sadayappan
- Publication Year: 2019
- Publishing Journal/Academic Society: Materials Science and Technology 2019 (MS&T19)
- Keywords: High Pressure Die Casting, Automotive Structural Components, Aluminum Alloys
2. Abstracts / Introduction
This research paper addresses the development of novel Al-Zn-Mg alloys designed for automotive structural components, aiming to meet the increasing demand for lightweighting in the automotive industry. The study focuses on alloys requiring high elongation (EL~10%) and moderate yield strength (YS~130-200 MPa), crucial for replacing ferrous components and enhancing fuel efficiency in internal combustion engines and extending the range of electric vehicles. The research introduces Nemalloy HE700, a high elongation variant, and compares its tensile properties in both the as-cast (F-temper) and solution heat-treated (T4-temper) conditions with Nemalloy HS700/701 and existing structural die casting alloys like Silafont-36 and Mercaloy 367. The introduction highlights the growing utilization of aluminum alloys in automotive powertrain and structural components, emphasizing the stringent crash safety specifications for structural parts that necessitate alloys with high elongation and yield strength. Current alloys like Mercaloy 367, Silafont 36, and Castasil 37, while used in HPDC, exhibit limitations such as susceptibility to die soldering and the requirement for heat treatment to achieve desired mechanical properties. The paper introduces the development of Nemalloy HS700 and HS701, which showed improved strength but required further elongation enhancement, leading to the development of Nemalloy HE700, designed to achieve high elongation in the as-cast condition, eliminating the need for heat treatment for certain applications.
3. Research Background:
Background of the Research Topic:
The automotive industry is increasingly focused on lightweighting to improve fuel efficiency in vehicles with internal combustion engines and to extend the driving range of battery electric vehicles (BEV). Aluminum alloys are recognized as promising materials for automotive structural components due to their favorable strength-to-weight ratio, stiffness, ductility, and recyclability. While aluminum alloys are already used in powertrain components, their application in structural and body-in-white components (e.g., shock towers, longitudinal members, side impact beams) and electric vehicle components like battery trays is expanding. These structural components demand alloys that meet stringent crash safety specifications, requiring a combination of high elongation (EL~10%) and relatively high yield strength (YS ~130-200 MPa).
Status of Existing Research:
Current cast aluminum structural components are primarily manufactured using Al-Si based alloys such as Mercaloy 367, Silafont 36 / Aural 2, and Castasil 37, processed via high pressure die casting (HPDC). These Al-Si alloys offer good castability in HPDC and possess YS and EL suitable for some structural applications. However, they exhibit high susceptibility to die soldering due to low Fe concentrations, leading to component distortion, cracking, and increased tool wear. Furthermore, alloys like Silafont-36 and Mercaloy 367 necessitate heat treatment (solution heat treatment and artificial aging) to fully develop mechanical properties, increasing production costs and potentially requiring straightening operations to correct heat treatment-induced distortion.
Necessity of the Research:
To overcome the limitations of existing commercial Al structural die casting alloys, particularly die soldering susceptibility and the need for heat treatment, and to meet the increasing demand for high strength and high elongation in automotive structural components, there is a necessity to develop new alloy systems. This research aims to develop and characterize a new Al-Zn-Mg alloy, Nemalloy HE700, designed to achieve high elongation and adequate yield strength in the as-cast condition, potentially eliminating the need for costly and time-consuming heat treatment processes.
4. Research Purpose and Research Questions:
Research Purpose:
The primary research purpose is to develop and evaluate a high ductility Al-Zn-Mg die casting alloy, Nemalloy HE700, for automotive structural components. This alloy is designed to achieve a superior combination of mechanical properties, specifically high elongation and moderate yield strength, in the as-cast condition, thereby reducing or eliminating the need for heat treatment and mitigating issues associated with die soldering prevalent in existing Al-Si alloys.
Key Research:
The key research focuses on characterizing the tensile properties of Nemalloy HE700 in both the as-cast (F-temper) and solution heat-treated (T4-temper) conditions. The study compares these properties with those of Nemalloy HS700/701 and industry standard structural die casting alloys, Mercaloy 367 and Silafont-36, to assess the performance and potential of Nemalloy HE700 as a replacement for current alloys in automotive structural applications. The effect of short T4 heat treatment on Nemalloy HE700 is also investigated to optimize processing parameters for industrial applications.
5. Research Methodology
Research Design:
The research employed an experimental design involving casting trials and mechanical property evaluation. Casting trials for Nemalloy HE700, HS700/701, and Mercaloy 367 were conducted using a 1200 Ton HPDC machine with high vacuum assist at the Canmet Materials research facility. A “test specimen” die (Figure 1) was utilized to produce ASTM B557 standard tensile bars, fatigue bars, and flat plates. Samples were prepared in as-cast (F-temper) and heat-treated (T4-temper using SHT3 parameters and short T4) conditions.
Data Collection Method:
Tensile testing was performed to evaluate the mechanical properties of the alloys. Tensile samples were tested at ambient temperature with a loading rate of 1 mm/min after a natural aging period. For as-cast samples, a natural aging time of approximately 14 days was used. For heat-treated samples, natural aging of 7 days followed the heat treatments. Hardness measurements were also implicitly considered as aging time was determined based on hardness stabilization.
Analysis Method:
The collected tensile data, including Yield Strength (YS), Ultimate Tensile Strength (UTS), and Elongation (EL), were analyzed and compared across different alloys (Nemalloy HE700, HS700/701, Mercaloy 367, Silafont-36) and temper conditions (F and T4). Graphical representations (Figures 2, 3, and 4) were used to visualize and compare the tensile properties.
Research Subjects and Scope:
The primary research subject was the newly developed Nemalloy HE700 Al-Zn-Mg alloy. Comparative analyses included Nemalloy HS700/701, Mercaloy 367, and Silafont-36. The scope of the research was limited to the evaluation of tensile properties and hardness in as-cast and T4-temper conditions, focusing on the suitability of Nemalloy HE700 for automotive structural components.
6. Main Research Results:
Key Research Results:
- As-Cast Condition (F-temper): Nemalloy HE700 exhibited an average YS of approximately 130 MPa, UTS of 260 MPa, and elongation of 11.2%. Nemalloy HS701 showed higher strength (YS ~190 MPa, UTS ~325 MPa) but lower elongation (~8%). Both Nemalloy HE700 and HS701 demonstrated similar or superior as-cast mechanical properties compared to Mercaloy 367 (YS ~150 MPa, UTS ~305 MPa, EL ~7.6%).
- SHT3 Heat Treated Condition (T4-temper): After SHT3 heat treatment, Nemalloy HE700 achieved an average YS of approximately 155 MPa, UTS of 305 MPa, and elongation of 13.8%. Nemalloy HS701 reached YS of 205 MPa, UTS of 370 MPa, and elongation of 10.5%.
- Short T4 Heat Treatment: A short T4 heat treatment at 475 °C for 2 hours for Nemalloy HE700 resulted in a YS of approximately 155 MPa, UTS of 320 MPa, and elongation of 16.5%, comparable to the SHT3 treated condition and significantly improved compared to the as-cast condition.
Analysis of presented data:
The data indicates that Nemalloy HE700 offers a superior combination of ductility and strength in the as-cast condition compared to existing structural die casting alloys like Mercaloy 367 and Silafont-36. The as-cast properties of Nemalloy HE700 meet the requirements for many automotive structural components, potentially eliminating the need for heat treatment and associated costs and distortions. While Nemalloy HS701 provides higher strength, Nemalloy HE700 excels in elongation. Furthermore, a short T4 heat treatment effectively enhances the mechanical properties of Nemalloy HE700, achieving properties comparable to the more extensive SHT3 heat treatment, making it industrially viable.
Figure Name List:
- Figure 1. (a) Image of “test specimen” HPDC die used in this study, (b) Image of “test specimen" casting using Nemalloy HE700.
- Figure 2. As-cast tensile properties of Nemalloy HE700, HS700/701 and Mercaloy 367 produced in the test specimen die.
- Figure 3. Tensile properties of Nemalloy HE700 and HS700/701 produced in the test specimen die and heat treated to T4 temper using the SHT3 parameters.
- Figure 4. Effect of solution heat treatment time (at 475 °C) on the tensile properties of Nemalloy HE700 in the T4 temper.
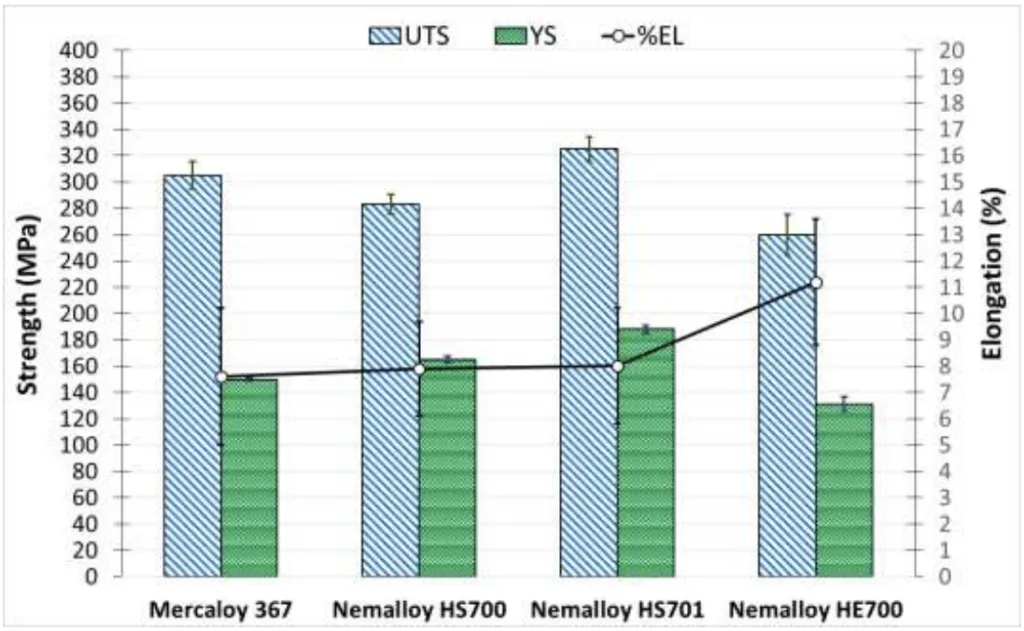
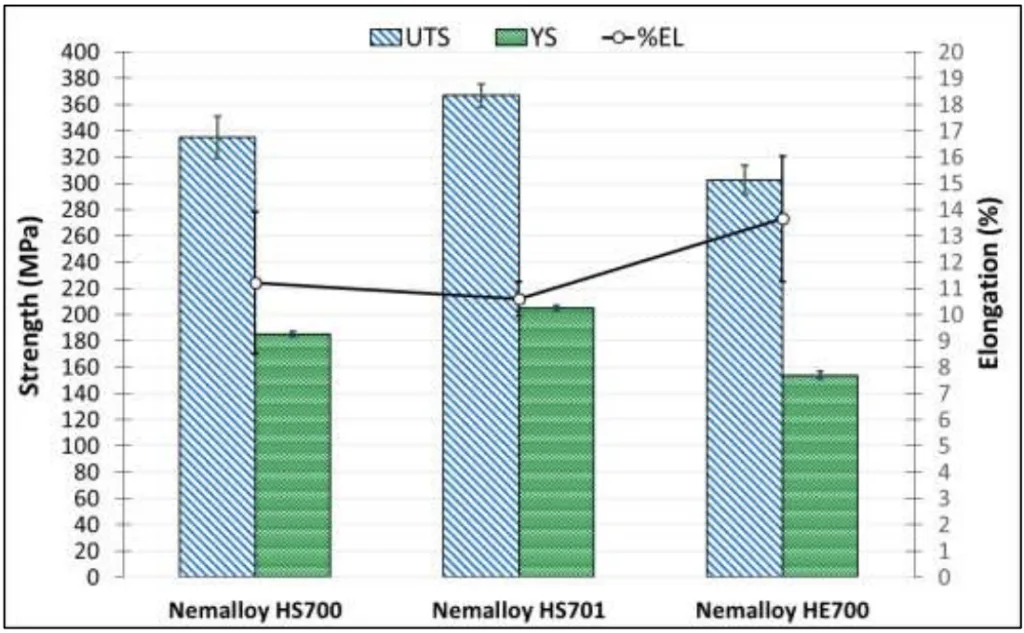
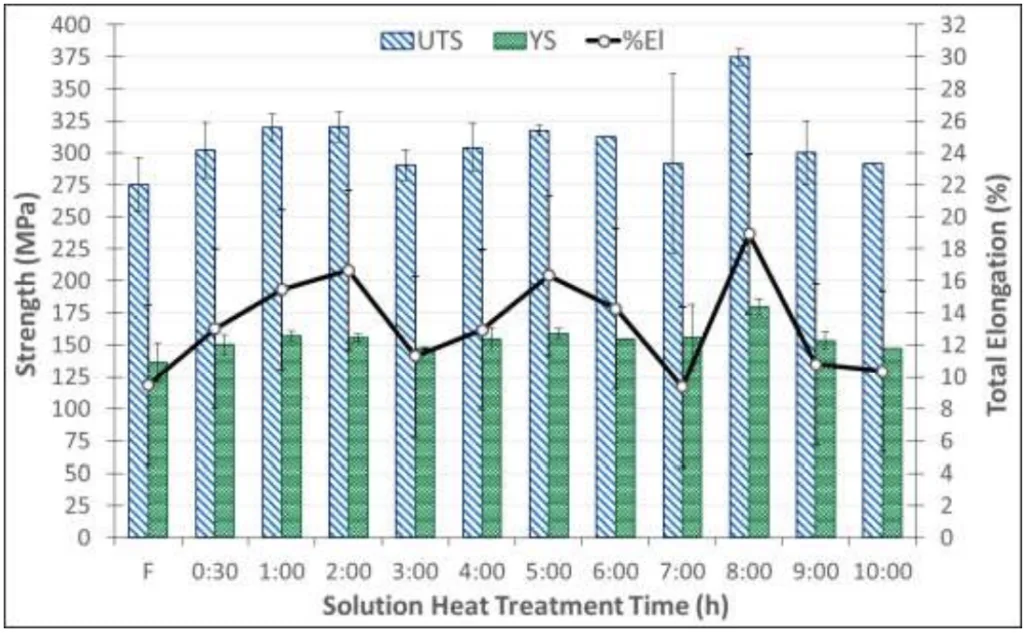
7. Conclusion:
Summary of Key Findings:
This research successfully developed and characterized Nemalloy HE700, a high ductility Al-Zn-Mg die casting alloy. Key findings include:
- Nemalloy HE700 exhibits excellent as-cast properties (YS ~130 MPa, UTS ~260 MPa, EL ~11.2%), meeting or exceeding specifications for many automotive structural components without heat treatment.
- Nemalloy HS701, a high strength variant, offers higher strength (YS ~190 MPa, UTS ~325 MPa, EL ~8%) in the as-cast condition, suitable for parts requiring higher strength and tolerating lower elongation.
- Nemalloy HE700 demonstrates significantly higher elongation and comparable yield strength in the as-cast condition compared to widely used structural Al die casting alloys like Silafont-36 and Mercaloy 367.
- Heat treatment of Nemalloy HE700 to the T4 temper, using both SHT3 parameters and a short 2-hour treatment at 475°C, effectively increases YS and UTS while maintaining or enhancing elongation, making it suitable for applications requiring even higher mechanical properties.
Academic Significance of the Study:
This study contributes to the field of die casting metallurgy by introducing a novel Al-Zn-Mg alloy system, Nemalloy HE700, specifically designed for high ductility in structural applications. The research provides valuable data on the mechanical properties of this alloy in as-cast and heat-treated conditions, expanding the understanding of Al-Zn-Mg alloys for HPDC and offering a potential alternative to traditional Al-Si alloys.
Practical Implications:
The development of Nemalloy HE700 has significant practical implications for the automotive industry. Its excellent as-cast properties can potentially eliminate the need for heat treatment for many structural components, reducing manufacturing costs and cycle time. The alloy's high ductility and adequate strength make it a promising candidate for replacing ferrous components and existing aluminum alloys in automotive structural applications, contributing to vehicle lightweighting and improved fuel efficiency or extended range for electric vehicles. The industrially friendly short T4 heat treatment further enhances its applicability for components requiring higher mechanical properties.
Limitations of the Study and Areas for Future Research:
The paper does not explicitly discuss limitations or areas for future research. However, implicitly, further research could explore:
- Detailed microstructure characterization of Nemalloy HE700 under different processing conditions to further optimize alloy composition and heat treatment parameters.
- Performance evaluation under crash and fatigue loading conditions to validate its suitability for structural automotive applications.
- Die soldering behavior of Nemalloy HE700 compared to Al-Si alloys to quantify its advantage in reducing die soldering issues.
- Cost-benefit analysis of using Nemalloy HE700 compared to existing alloys, considering material cost, processing cost (including heat treatment), and performance benefits.
8. References:
- 1. https://www.mercalloy.com/mercalloy-family/high-strength/
- 2. http://rheinfelden-alloys.eu/wp-content/uploads/2015/07/05-Silafont-Processing.pdf.
- 3. S. Shankar, D. Apelian, “Mechanism and Preventative Measures for Die Soldering during Al Casting in a Ferrous Mold”, JOM, 54 (8) (2002), 47-54.
- 4. C. Wu, X. Zeng, S. Shankar, G. Birsan, K. Sadayappan, A. Lombardi and G. Byczynski, “Microstructure and Uniaxial Tensile Properties of Heat Treatable Al-Zn Alloy for Structural HPDC Components” (Paper presented at NADCA Die Casting Congress, Indianapolis, Indiana, 15-17 October 2018, 7.
9. Copyright:
- This material is "A. Lombardi, G. Byczynski, C. Wu, X. Zeng, S. Shankar, G. Birsan, and K. Sadayappan"'s paper: Based on "Development of High Ductility Al-Zn-Mg Casting Alloys for Automotive Structural Components".
- Paper Source: DOI 10.7449/2019/MST_2019_1049_1056
This material was created to introduce the above paper, and unauthorized use for commercial purposes is prohibited.
Copyright © 2025 CASTMAN. All rights reserved.