by
Mihály Réger 1, József Gáti 1, Ferenc Oláh 1,2, Richárd Horváth 1,*, Enikő Réka Fábián 1 and Tamás Bubonyi 3
1Bánki Donát Faculty of Mechanical and Safety Engineering, University of Óbuda, H-1081 Budapest, Hungary
2Doctoral School on Materials Sciences and Technologies, University of Óbuda, H-1081 Budapest, Hungary
3Institute of Metal Formation and Nanotechnology, University of Miskolc, H-3515 Miskolc, Hungary
*Author to whom correspondence should be addressed.
Crystals 2023, 13(7), 1014; https://doi.org/10.3390/cryst13071014
Received: 9 June 2023 / Revised: 22 June 2023 / Accepted: 24 June 2023 / Published: 26 June 2023
(This article belongs to the Special Issue Advanced Crystalline Materials, Mechanical Properties and Innovative Production Systems)
Abstract
The porosity of die-cast aluminum alloys is a determining factor for the quality of the product. In this paper, we studied the porosity of a selected part of a die-cast AlSi9Cu3(Fe) compressor part by computer tomography and metallography. In the case of this part, the achievable resolution by CT, a non-destructive testing method, was 30 μm—this method could not detect smaller cavities. Based on metallographic analysis, the percentage of defects larger than 30 μm ranges from 10 to 30% of the total number of defects, which represents 75–95% of the defective area (area ratio). Impregnation with methacrylate resin (used to seal cavities to prevent leakage) can be detected with UV-illuminated optical microscopic examination on metallographically prepared specimens. As confirmed by scanning electron microscopy, partial filling and partial impregnation can occur in a system of shrinkage cavities.
Keywords:
aluminum alloy; die casting; gas tightness requirement; porosity; impregnation; computed tomography; metallography; UV illumination; scanning electron microscope
1. Introduction, Background
The solidification of aluminum alloys is accompanied by a shrinkage of about 5–7% [1,2]. The change in crystallization volume and the degree of gas porosity and air entrapment can be compensated for with a variety of die-casting processes (e.g., melt treatment, post-pressure, post-compression). With these methods, porosity can be reduced to 0.2–0.5% in quality casting [3,4,5]. This amount of porosity is unacceptable where gas permeability is not allowed. Porosity cavities can be sealed, and leakage can be prevented by impregnation with methacrylate resin. Cast products are usually impregnated when they are fully finished. The main steps of the process are as follows: vacuuming, immersion in resin under vacuum; application of atmospheric pressure on the liquid surface of the impregnation resin, lifting out; washing with cold water; and washing with hot water, during which the resin is cured between 90 and 95 °C [6]. The technology is generally efficient and reliable, but leaking is nevertheless common. In order to detect leaking castings, a helium leakage test is carried out on each casting in the assembly line.
Leakage is primarily associated with the machined surfaces, as the external surface of a casting usually seals the internal shrinkage cavity system in a gas-tight manner (the bi-film oxide layer effect on leakage is not investigated in this study). The inherently closed cavity network inside a cast piece can become an open system during machining. The internal surface of holes and threads can cut spatial porosity cavity systems, and, as a result, leakage often occurs through the internal holes.
The reason for leakage in impregnated castings is assumed to be the limited impregnation efficiency of the complex-shaped shrinkage cavity system with different cross-sections. Both vacuuming and saturation with resin may be impeded by small cross-sections in a cavity system with complex geometry, particularly if the cavity system includes capillary sections.
In aluminum alloy die-cast pieces, porosity can develop, mainly in the larger cross-sections. Even if porosity is adequate for the casting as a whole, the degree of local porosity may be critical from the point of view of gas tightness in certain casting sections. Technological solutions to reduce the porosity of the casting will result in the compaction of the porous material area. These solutions reduce the volume of porosity to a significant degree but do not necessarily eliminate the shrinkage cavity system. Compression may also result in a reduction of cavity and channel dimensions in the cavity system in the typical cross-sections.
X-ray computed tomography (CT) is among the most widespread non-destructive examination methods used to analyze the porosity and shrinkage cavity system of a sample [7,8,9]. CT is an imaging method based on the absorption of X-rays in materials and makes non-destructive three-dimensional analysis of samples and their internal structures possible.
As the thickness of the sections increases, the resolution of the X-ray image decreases (larger focal spot used), and less detailed information can be extracted from the images. Different types of CT equipment work with different sample sizes; thus, their resolution varies. The resolution of industrial CT is 5–150 μm, that of micro-CT is 1–100 μm, and that of nano-CT is around 0.5 μm. With X-ray microscopy, resolutions as low as 100 nm can be achieved [10]. Recently, Zhuang et al. [11] developed a method to analyse porosities below the resolution of CT. The accuracy and analysis of the results are influenced by a number of additional factors, such as transparency and segmentation [12,13,14].
Limodin [15] studied the relationship between the porosity and mechanical properties of an Al–Si–Mg alloy. The micro-CT study was performed with a voxel size of 1.7 μm. The author notes that a compromise between resolution and sample size had to be found, as a high resolution provides less representative results. In the end, the decision was made to analyse the volume fractions of 3.8 and 18 mm3. The images were processed and binarized with the ImageJ software. In the 18 mm3 sample, 1104 pores were identified (61 pores/mm3). The size distribution of the complex-shaped pores was given as a function of the Feret diameter, with the most common value being 16 pores/mm3 at Feret diameters between 30 and 40 μm.
The porosity of the aluminum alloys produced by die casting is of crucial importance, not only because of gas tightness but also because of the fatigue properties. To this end, Garb and co-workers [16] conducted an extensive series of micro-CT studies to statistically characterize the microporosity of aluminum castings. They used two different resolutions (3 and 8 μm) to find out how resolution affects the accuracy of determining the porosity distribution. Resolution limits the size of the volume, which can be investigated. A cylindrical sample of 6 mm in diameter with a length of 5.4 mm was used at a resolution of 3 μm, and a 15.5 mm long sample was used at an 8 μm resolution (the sample volumes were 0.155 and 0.490 cm3). In the 0.155 cm3 volume investigated at a 3 μm resolution, approximately 7000 pores were detected. Different statistical distribution functions were fitted to the equivalent diameters of the identified pores; the maximum for the distribution curve was between 8 and 10 μm. The authors found that the shrinkage pores often contain large-volume patches connected by thin cavities with dimensions below the resolution. Investigations under nearly identical conditions and similar results are reported in a study by Weidt et al. [17], who reported investigations under nearly identical conditions and similar results in a study on Al–Si–Cu alloys.
The relationship between fatigue characteristics and pores, revealed by micro-CT and metallographic examination, is discussed in the study by Nicoletto et al. [18]. The tested volume of the AlSi7Mg sample was 12.5 mm3, and the voxel size was 1.7 μm. The authors presented some pore shapes revealed by CT and metallography but no statistical data on the dimensions and distribution. They concluded that the identified pores could be considered a complex system of larger hollow spaces and narrow channels connecting them. Recently, additive manufacturing of aluminum alloys by selective laser melting (SLM) is also of research interest. Zhang et al. [19] investigated the SLM-built AlSi10Mg thin-walled parts and their macro-mechanical behavior in correlation with the relative densities.
There is very little reliable test information available in the literature on the impregnation of hollow systems with complex geometries in aluminum alloy castings. Publications of impregnant producers provide some informative data. According to laboratory impregnation experiments on sintered metal alloys with a controlled pore structure [20], cavities with a size below 100 μm are totally filled in every case. The impregnation problem may be mainly the sealing of larger pores between 100 and 500 μm, about one-third of which were not sealed in the experiments. Above a pore size of 500 μm, impregnation has been shown to be essentially ineffective in ensuring the gas tightness of sintered samples. The pore structure of Al–Si–X die-cast components with gas tightness requirements contains cavities and channels typically below 100 μm; however, impregnation often fails to seal the leak paths.
Soga et al. [21] detected and studied the impregnating resin in a cavity system by computed tomography. The technique is based on the detection of contrast differences caused by the impregnating resin, the aluminum matrix and the gases in the cavities. They reported that, in simple-geometry castings, the filling of larger (several mm) cavities with resin could be assessed (voxel size 100 μm). The authors do not discuss the possibilities of investigating smaller cavities (10–100 μm) or more complex spatial geometries.
Many details of porosity problems and the formation of leakage paths are still unclear. In this study, an impregnated cast part—produced with a gas tightness requirement and nevertheless showing leakage, despite impregnation—was examined in detail. The aim of the investigations was to determine the location and geometric characteristics of potential leaking paths in the casting. The shape and size of the cavities and porosities in the investigated castings were determined using metallographic and micro-CT methods. The parallel metallographic and micro-CT analyses of the continuity defects identified in a given cross-section of the cast part provide an opportunity to compare the advantages and disadvantages, as well as the limitations of both methods.
2. Materials and Testing Methods
We determined the porosity map of a selected part of a mass-produced EN AC 46000 AlSi9Cu3(Fe) die-casting (compressor) part. The impregnated casting, finished after pressure die-casting, showed leakage between the inner and outer space in the helium inspection test prior to assembly and was therefore taken out of production. The leakage was identified in the greater wall thickness of the thin-walled cylindrical casting. The front face of the shell is machined, and the sides have cast surfaces. This part contains holes for connecting the associated elements, one of which has a threaded internal surface. Leakage to the external space is through the inner part of the threaded hole.
A detailed structural analysis was conducted on the cast piece (Figure 1). The machined specimen contains a volumetric size of about 4.5 cm3, including the threaded bore. Therefore, it can be assumed that there are discontinuities associated with leakage in this region. The defect distribution characteristics were determined by computed tomography (micro-CT) and metallographic analysis, for which the sample was embedded in metallographic resin. The tests were carried out within the planes presented in Figure 1. The examined planes were parallel to the base plane. The sample was studied by light optical microscopy (LOM), without etching, after metallographic preparation (grinding and polishing). Lower magnification metallographic images, showing the complete cross-section of the sample, were produced with an OLYMPUS DSX1000 (Olympus Scientific Solutions Americas Corp., Waltham, MA, USA) opto-digital microscope with a resolution of 3.4 μm. Higher-resolution images of the elements of the revealed structure were produced with the opto-digital microscope (LOM) and a JEOL JSM 5310 LA scanning electron microscope (SEM).
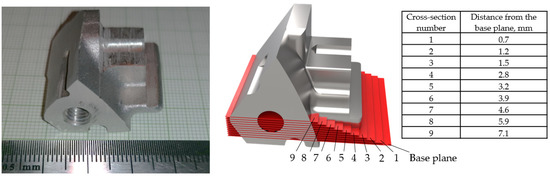
Figure 1. The sample from the leakage region and positions of the cross-sections examined by metallography.
The micro-CT scans were performed on the YXLON FF35 (YXLON International GmbH, Hamburg, Germany) machine at the 3D Laboratory of the University of Miskolc. Porosity was studied by porosity/inclusion analyses using the VGStudio MAX 3.0 software at the 3D laboratory of Óbuda University. The relatively large sample volume allowed a resolution of 30 μm, which meant the detection of 2·× 108 spatial pixels (the size of the resulting file was 196 GByte). Limodin [14], Garb [15], and Weidt [16] measured approximately the same number of voxels but used a significantly smaller sample to achieve a better resolution. The results of the porosity analysis in a 3D reconstructed image are shown in Figure 2.
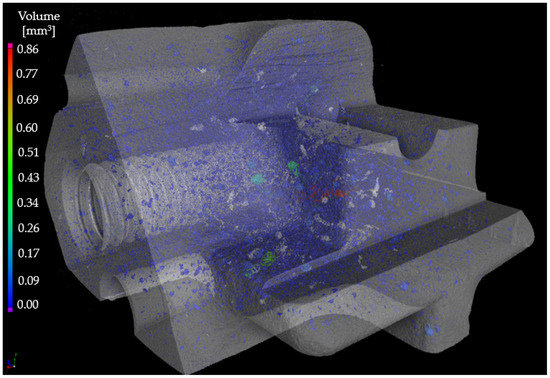
Figure 2. Volumetric distribution of porosities in a 3D reconstructed CT image at 60% transparency.
The position of the plane in the optical image can also be reconstructed from the spatial micro-CT results and thus, the metallographic and CT scan results can be combined for a given scan section. The ImageJ 1.52a image processing software was used to analyse the images acquired by both methods.
The impregnation resin fluoresces in ultraviolet light, and thus, the filling of cavities in metallographic surfaces with impregnation resin can be checked with the use of UV illumination. The UV-illuminated micrographs were produced with an OLYMPUS DSX1000 opto-digital microscope with a Labino 135 UV reflector.
We could not detect the impregnation resin in the cavities by micro-CT scanning.
3. Results and Discussion
Shrinkage cavities, gas porosities and other discontinuity defects in the polished surface section of the test specimen, revealed by metallography, were identified by optical microscopy. We observed gas porosities and microcavities on the metallographically prepared surfaces. Figure 3 shows some characteristic defects of the studied part at a distance of 0.7 mm from the base plane (level 1). Spherical gas pores and discrete shrinkage cavities are clearly visible at low magnifications; however, the characterization of microcavities requires higher resolutions. Figure 3a,b show the typical appearance of gas pores, shrinkage cavities and microcavities.
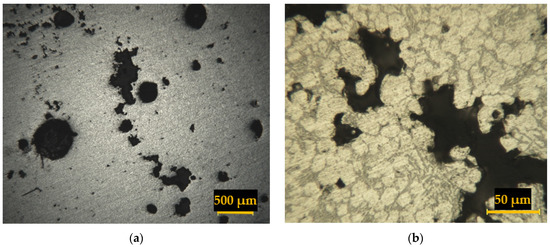
Figure 3. Porosity, as shown by optical microscopy; (a) gas porosities and shrinkage; (b) microporosity.
A high-resolution view of several cm2 sample areas was produced from a series of panoramic images. Depending on the actual size of the sample area, each macro image was produced by automatically stitching 48–72 photographs at a magnification of 100×.
From the 3D CT-scan data set, the position of the metallographic plane can be determined from the geometric data of the specimen; thus, a two-dimensional CT image of the investigated plane can be reconstructed. The comparison of the image produced by the optical microscope and the CT image showing the same plane allows a joint analysis of the results of the destructive and non-destructive tests.
We performed a systematic comparison of the optical and CT examination results in nine examined planes. The sections were marked in a position parallel to the base plane (see Figure 1) at a distance of 0.7–7.1 mm from it. Figure 4 shows the cross-section explored in a plane that is 3.9 mm from the base plane (cross-section 6). The images in Figure 4a,b show the total area of the sample; in this section, the convex area of the sample is 6.3 cm2. The position of the threaded hole and the location of the larger individual defects show that the metallographic section and the 2D CT image represent the same plane. The cross-section examined shows a large number of small to large continuity gaps, most of which can be matched with the two inspection methods. The enlarged images of the section marked in Figure 4a are shown in Figure 4c. Again, the larger individual continuity defects look the same with both methods; however, the identification of the smaller defects is not straightforward. The one order of magnitude lower resolution of the CT image and its inherently poorer image quality result in blurred contours of smaller defects and, thus, an uncertain identification of shapes. This difference is clearly visible with a higher magnification of the surface area, as shown in Figure 4b (Figure 4c). The contour of the large cavity is significantly blurred, and some small cavities are not even identifiable in the CT image. Although the resolution of the CT images is 30 μm, the lower limit of the sizes of objects that can be identified with confidence is around 50 μm due to image quality.
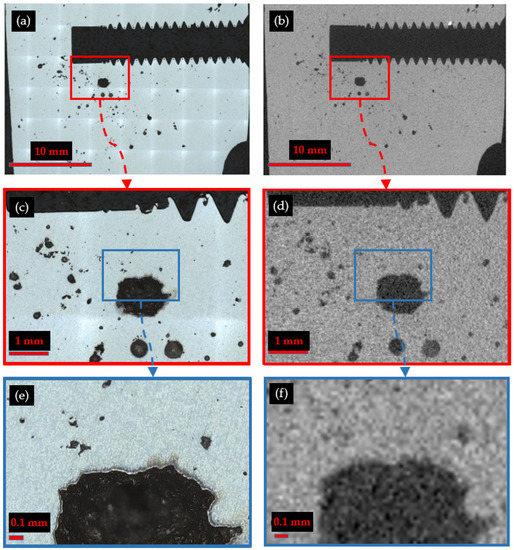
Figure 4. Optical microscopy (left) and micro-CT (right) images of cross-section 6. (a) Image of the complete section by optical microscopy (LOM); (b) image of the section by CT; (c) magnification of the marked area in (a) (LOM); (d) magnification of the marked area in (b); (e) magnification of the marked area in (c); (f) magnification of the marked area in (d).
The cross-sectional images were binarized with the use of the automatically offered threshold of the ImageJ software. No image correction was applied. In the case of the CT images, due to the poorer image quality, the number of false signals of a few pixels in size increased during binarization. We did not modify the binarized image in any way. Figure 5 shows the optical and CT images of Figure 4d after binarization. The binarized CT image on the right shows several continuity gaps of 1 pixel in size, which are not found in the optical image (left), which we consider the reference. In order to reliably evaluate the area of larger cavities, we did not apply erosion and dilation to the image. Optical microscopy images can have similar defects, but to a lesser extent, due to the significantly better image quality.
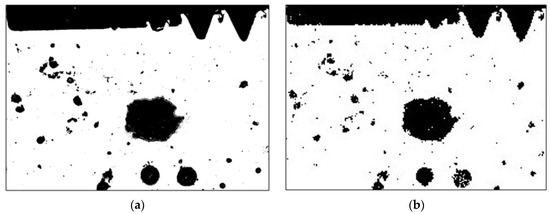
Figure 5. Images of cross-section 6 after binarization; (a) optical microscopy; (b) micro-CT.
In the full cross-section of the sample (Figure 5), 3901 defects can be detected in the optical microscopy image and 849 defects in the CT image.
The diagram in Figure 6a shows the size distribution of the identified defects. In this diagram, the diameter of a circle with the same area as the defect area, the so-called equivalent circle diameter, is used to characterize the size of the defect. The frequency of defects increases sharply with decreasing size, based on both the metallographic and CT examination results. The higher value identified in the CT image in the 35 μm equivalent defect size category is caused by the binarization of the gray image, as explained above. The 35 μm equivalent defect size category is representative of the presence of continuity defects of a few pixels in the CT image.
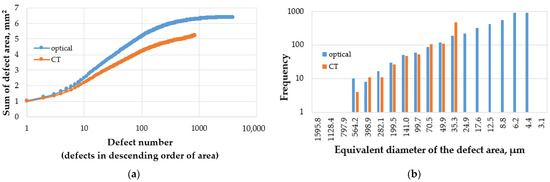
Figure 6. Assessment of the discontinuities identified in cross-section 6. (a) Frequency distribution of defect size (equivalent circular diameter); (b) sum of defect areas in descending order.
More than 3.000 defects, or about 78% of the total number of defects, cannot be detected by CT because their size falls below the resolution of CT, in the equivalent diameter range of 4–30 μm. However, this amount of defects account for about 19% of the area of defects, i.e., more than 80% of the defect area in the examined section was detectable by CT. We sorted the detected defects in decreasing order as a function of their area measured in the plane and then plotted the sum of the defect areas 1 to n (n ≤ number of defects) (Figure 6b). The value of the points representing the sum function provides the sum of the area of the detected defects, with a maximum value of 6.4 mm for optical microscopy and 5.3 mm for CT.
The area sum function for CT is continuously below the area sum function determined by optical microscopy. The area of the first defect, i.e., the largest defect (the largest defect in the images in Figure 2), is 1.03 mm2 in the optical microscopy image and 0.98 mm2 in the CT image. The summed areas of the first ten largest defects show a similar difference, with 2.48 and 2.17 mm2, respectively. The cumulative defect area up to the first 849 defects (all the defects detected by CT) is 6.259 mm2, determined by optical microscopy, and 5.222 mm2, determined by CT. The cumulative area of the 3901 defects detected by optical microscopy is 6.340 mm2. The 3901 − 849 = 3052 defects identified on the metallographic section account for 6.340 − 6.259 = 0.081 mm2 of the cumulative defect area, proportionally 1.3% of the total value.
As shown above, there is a systematic discrepancy between the defect area sum functions determined by optical microscopy and CT scanning. This is proved by the linear correlation coefficient (R = 0.993) between the defect area data pairs determined with the two methods. The tangent of the line fitted to the data pairs is m = 0.912, i.e., the defect area on the sample surface determined by CT is, on average, 91.2% of the defect area measured with the help of optical microscopy. The sections shown in Figure 5 have the same field of view at the same magnification; the area of the shapes extracted from the CT images is smaller than that of the shapes detected by optical microscopy. The difference is presumably due to the different imaging quality and different resolution.
We performed the above analysis on nine sections of the test sample. Table 1 shows the results of the measurement series. Based on the mean value in Table 1, 83% of the defect area detected by metallographic (optical microscopy) examination can be identified on CT scans, i.e., approximately 17% of the defect areas are not detected by CT scans. This 17% area ratio represents 80% of the total number of defects. We calculated the linear correlation of the defect area data pairs that were measured by optical microscopy and CT scans; the data were sorted in descending order of size. The average correlation coefficient for the nine sections is R = 0.981. The proportion of defect areas identified by CT scanning and optical microscopy ranges from 0.644 to 0.942, with an average value of m = 0.827.
Table 1. Results of a series of measurements in nine sections of the sample.
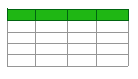
Based on metallography and optical analyses, the number of defects larger than 100 μm is 3–5%, and this represents 65–80% of the discontinuity area. The percentage of defects larger than 30 μm (i.e., the resolution of CT) ranges from 10 to 30% of the total number of defects in the nine sections. This 10–30% number of defects represents 75–95% of the total number of defects detected (Table 2).
Table 2. Defect size rates in nine cross-sections of the sample by equivalent diameter range.
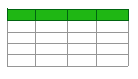
4. The Filling of the Cavities
The gas tightness of castings can be ensured by sealing the leakage paths and impregnating the cavity systems connecting the outer and inner spaces. Thousands of cavities, identified by optical microscopic metallographic analysis and CT scans, as described in Figure 6, may be part of an interconnected microcavity system, even running to the machined surface, or a localized isolated continuity gap. The latter has essentially no effect on gas tightness. Due to the complex spatial shape of a leaking cavity system, it is not possible to determine from a cavity identified in a planar section whether it plays a role in leakage or not. If the cavity contains impregnation resin, its continuation is certainly connected to an external surface; however, if the presence of resin cannot be verified and the casting is proven to leak, the cavity is part of a leaking pathway. The CT scan does not detect sections of the spatial cavity system below the detection limit. In this case, at 30 μm, the filling of the cavity with resin cannot be demonstrated with this scan. Conventional bright-field microscopy cannot be used to show resin in the cavities since the cavity appears as a dark-toned spot, as seen in Figure 4 and Figure 5, whether the resin is present or not. The detection of resin in the cavities is only possible by scanning electron microscopy on a metallographically prepared section, fractured surface or by examination under UV light. Both methods are only suitable for the identification of the impregnating agent on the examined surface.
We detected impregnation resin in the cavities by scanning electron microscopy in sections 5, 6, and 9 and by UV-illuminated optical microscopy in section 9. Figure 7 shows some typical images of impregnation resin-saturated and non-saturated cavities.
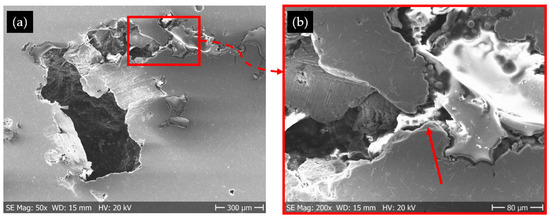
Figure 7. Some characteristic cavities identified on the metallographically prepared surface in section 5. (a) Complex cavity; (b) magnification of the area marked in (a).
Figure 7 shows a complex cavity partially filled with resin. The continuity gap extending below the plane of the section on the left side of Figure 7a forms a system with a thinner channel on the right. The meeting point of the smaller and larger cross-sectional cavity sections—the detail marked in Figure 7a—is shown enlarged in the image in Figure 7b. In the cavity system, a 15–20 μm constriction can be identified in the section marked with an arrow, the right side of which contains resin, while the left side does not. It can be assumed that during impregnation, the resin flowed into the cavity system through the cavity section on the right; however, for some reason, the filling of the left-hand section could not be completed. The constriction marked by the arrow must have increased the flow resistance, and thus the pressure difference or the time available was probably not sufficient to fill the cavity on the left.
Figure 8a shows the entire surface of cross-section 9 using LOM when the sample is under UV light. Due to the fluorescence of the impregnation resin, the discontinuities filled with resin glow in a bluish-white color, while the base matrix has a purple tint. The structure of the metallographic embedding resin is visible around the part and in the bore in Figure 8c,d.
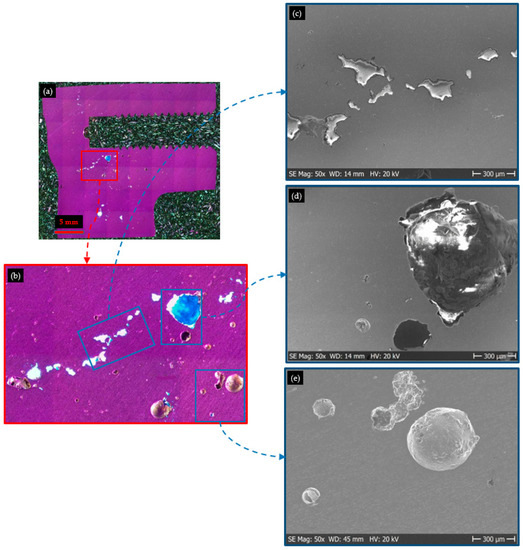
Figure 8. Material continuity defects identified in cross-section 9. (a) The entire surface under UV illumination (LOM); (b) the appearance of cavities under UV; (c) cavities filled with resin (SEM image); (d) a large cavity with resin (SEM image); (e) spherical cavities without resin (SEM image).
Due to the unidirectional UV illumination, the edges of the cavities are shimmering white, and thus automatic image analysis is limited for these images. Visual inspection of each area at higher magnifications reveals that the impregnating resin covers approximately half of the total cavity surface. The number of unsaturated cavities, mainly small ones, is significantly higher than the number of saturated cavities. The spherical continuity gaps, with a few exceptions, are generally free of resin and can probably be considered separated gas inclusions.
Figure 8b shows a larger magnification of the resin-filled cavity near the hole. Figure 8d shows a scanning electron micrograph of the larger cavity and its surroundings in the upper-right-third of the image. The large cavity clearly contains resin, and the surrounding smaller cavities, which are spherical and irregular in shape, do not. The presence of resin is also clearly visible in the scanning electron micrograph of the string-like shrinkage cavity row (Figure 8c), but the impregnating agent cannot be identified in the spherical cavity in Figure 8e (the cavities in the lower-right-third of Figure 8b). The UV-illumination optical microscopy inspection procedure clearly identifies cavities containing an impregnating resin on the metallographic section in our experience.
5. Conclusions
Die-cast aluminum alloy components with gas tightness requirements manufactured with high care in melt treatment and casting technology can still have leaking problems after impregnation, especially in castings with larger cross-sections. In order to map the nature and location of the possible leakage pathways, a detailed investigation of the material continuity defects and porosity of the casting is required. Leakage is likely to occur along contiguous leak paths with complex geometries of holes produced by gases and shrinkage cavities. The investigations presented in this study were carried out on a cast part, showing leakage. The inner structure of the cast part was analyzed by metallographic macro photography through an optical microscope and micro-CT images of the same planes in nine parallel cross-sectional positions. The optical microscopic and micro-CT procedures allowed resolutions of 3.5 and 30 μm, respectively.
The statistical evaluation of the cavities in the investigated planes (see Table 1 and Table 2) shows that the defect density in the critical part of the casting is very high, exceeding 10 defects/mm2 based on the optical microscopic examinations. However, the typical defect size is small; 80% of the defects are less than 30 μm. Overall, the ratio of the defected area is 1.3% for the surfaces tested. The defect density and defect rate, determined by the micro-CT examination, were significantly lower, which is a consequence of the lower resolution of this examination technique. For the defects larger than 60 microns, optical and micro-CT analyses yielded approximately the same statistical characteristics.
The cavity systems attached to the surface were partially saturated with resin during impregnation. In the case of the tested casting, the presence of impregnation resin in the cavity was not detectable by the micro-CT method. This is because the typical cavity size and cross-section are very small in relation to the wall thickness of the casting, and the resin comprises a small atomic number of elements. Therefore, there is minimal contrast difference between the resin-saturated and non-saturated cavities. Optical microscopy under UV illumination is suitable for the detection of impregnation resin in cavities.
Author Contributions
Conceptualization, M.R. and R.H.; methodology, M.R.; software, F.O., E.R.F. and T.B.; validation, M.R., J.G. and F.O.; formal analysis, M.R.; investigation, M.R.; resources, M.R.; writing—original draft preparation, M.R.; writing—review and editing, M.R. and R.H.; visualization, R.H. and F.O.; supervision, R.H. All authors have read and agreed to the published version of the manuscript.
Funding
This research was funded by the 2019-1.1.1-Market KFI-2019-00462 project and by the UNKP-22-3 New National Excellence Program of the Ministry of Human Capacities, Hungary.
Data Availability Statement
The data presented in this study are available on request from the corresponding author.
Acknowledgments
The authors would like to thank István Somogyi, Quality Engineer of Hanon Systems Auto Parts Hungary Ltd.; Viktor Nyeste, Technical Associate of Hanon Systems; and Sándor Orosz, Technical Manager of Euraseal Service Ltd. for providing the samples and technological information for the research; and Ádám Filep, Research Fellow of the Institute of Physical Metallurgy, Metalforming and Nanotechnology, University of Miskolc, for his assistance in the implementation of the CT scan.
Conflicts of Interest
The authors declare no conflict of interest. The funders had no role in the design of the study; in the collection, analyses, or interpretation of data; in the writing of the manuscript; or in the decision to publish the results.
References
- Anggraini, L. Analysis of Porosity Defects in Aluminum as Part Handle Motor Vehicle Lever Processed by High-pressure Die Casting IOP Conf. Ser. Mater. Sci. Eng. 2018, 367, 012039. [Google Scholar]
- Felberbaum, M. Porosity in Aluminum Alloys. Ph.D Thesis, EPFL, Lausanne, Switzerland, 2010. [Google Scholar]
- Hanxue, C.; Mengyao, H.; Chao, S.; Peng, L. The influence of different vacuum degree on the porosity and mechanical properties of aluminum die casting. Vacuum 2017, 146, 278–281. [Google Scholar]
- Szalva, P.; Orbulov, I.N. The Effect of Vacuum on the Mechanical Properties of Die Cast Aluminum AlSi9Cu3(Fe) Alloy. Int. J. Metalcast. 2019, 13, 853–864. [Google Scholar] [CrossRef][Green Version]
- Lordan, E.; Zhang, Y.; Dou, K.; Jacot, A.; Tzileroglou, C.; Wang, S.; Wang, Y.; Patel, J.; Lazaro-Nebreda, J.; Zhou, X.; et al. High-Pressure Die Casting: A Review of Progress from the EPSRC Future LiME Hub. Metals 2022, 12, 1575. [Google Scholar] [CrossRef]
- Campbell, J. Complete Casting Handbook: Metal Casting Processes, Metallurgy, Techniques and Design; Butterworth-Heinemann: Oxford, UK, 2015. [Google Scholar]
- Carmignato, S. Computed tomography as a promising solution for industrial quality control and inspection of castings. Metall. Sci. Technol. 2012, 1–30, 5–14. [Google Scholar]
- Fuchs, P.; Kröger, T.; Garbe Christoph, S. Defect detection in CT scans of cast aluminum parts: A machine vision perspective. Neurocomputing 2021, 453, 85–96. [Google Scholar] [CrossRef]
- Jolly, M.R.; Prabhakar, A.; Sturzu, B.; Hollstein, K.; Singh, R.; Thomas, S.; Shaw, A. Review of non-destructive testing (NDT) techniques and their applicability to thick walled composites. Procedia CIRP 2015, 38, 129–136. [Google Scholar] [CrossRef][Green Version]
- Vásárhelyi, L.; Kónya, Z.; Kukovecz, Á.; Vajtai, R. Microcomputed tomography-based characterization of advanced materials: A review. Mater. Today Adv. 2020, 8, 1–13. [Google Scholar] [CrossRef]
- Zhuang, L.; Shin, H.S.; Yeom, S.; Pham, C.N.; Kim, Y.J. A novel method for estimating subresolution porosity from CT images and its application to homogeneity evaluation of porous media. Sci. Rep. 2022, 12, 16229. [Google Scholar] [CrossRef]
- Jaques, V.A.; Du Plessis, A.; Zemek, M.; Šalplachta, J.; Stubianová, Z.; Zikmund, T.; Kaiser, J. Review of porosity uncertainty estimation methods in computed tomography dataset. Meas. Sci. Technol. 2021, 32, 122001. [Google Scholar] [CrossRef]
- Kokhan, V.; Grigoriev, M.; Buzmakov, A.; Uvarov, V.; Ingacheva, A.; Shvets, E. Segmentation criteria in the problem of porosity determination based on CT scans. Twelfth Int. Conf. Mach. Vis. 2020, 11433, 378–385. [Google Scholar] [CrossRef][Green Version]
- Reedy, C.L.; Reedy, C.L. High-resolution micro-CT with 3D image analysis for porosity characterization of historic bricks. Herit. Sci. 2022, 10, 83. [Google Scholar] [CrossRef]
- Limodin, N.; El Bartali, A.; Wang, L.; Lachambre, J.; Buffiere, J.Y.; Charkaluk, E. Application of X-ray microtomography to study the influence of the casting microstructure upon the tensile behaviour of an Al–Si alloy. Nucl. Instrum. Methods Phys. Res. Sect. B Beam Interact. Mater. At. 2014, 324, 57–62. [Google Scholar] [CrossRef]
- Garb, C.; Leitner, M.; Tauscher, M.; Weidt, M.; Brunner, R. Statistical analysis of micropore size distributions in Al–Si castings evaluated by X-ray computed tomography. Int. J. Mater. Res. 2018, 109, 889–899. [Google Scholar] [CrossRef]
- Weidt, M.; Hardin, R.A.; Garb, C.; Rosc, J.; Brunner, R.; Beckermann, C. Prediction of porosity characteristics of aluminium castings based on X-ray CT measurements. Int. J. Cast Met. Res. 2018, 31, 289–307. [Google Scholar] [CrossRef]
- Nicoletto, G.; Konečná, R.; Fintova, S. Characterization of microshrinkage casting defects of Al–Si alloys by X-ray computed tomography and metallography. Int. J. Fatigue 2012, 41, 39–46. [Google Scholar] [CrossRef]
- Zhang, Y.; Majeed, A.; Muzamil, M.; Lv, J.; Peng, T.; Patel, V. Investigation for macro mechanical behavior explicitly for thin-walled parts of AlSi10Mg alloy using selective laser melting technique. J. Manuf. Process. 2021, 66, 269–280. [Google Scholar] [CrossRef]
- Lloyd, G. Finding a Solution to the Eternal Problem of Porosity in Casting. Die Cast. Eng. 2012, 40, 1–7. [Google Scholar]
- Soga, N.; Bandara, A.; Kan, K.; Koike, A.; Aoki, T. Micro-computed tomography to analyze industrial die-cast Al-alloys and examine impregnation polymer resin as a casting cavity sealant. Prod. Eng. 2021, 15, 885–896. [Google Scholar] [CrossRef]