This paper summary is based on the article Automobile Parts Casting-Methods and Materials Used: A Review presented at the Materials Today: Proceedings, Elsevier
1. Overview:
- Title: Automobile Parts Casting-Methods and Materials Used: A Review
- Author: Madhav Goenka, Chico Nihal, Rahul Ramanathan, Pratyaksh Gupta, Aman Parashar, Joel J
- Publication Year: 2020
- Publishing Journal/Academic Society: Materials Today: Proceedings, Elsevier, ICMMM 2019
- Keywords: Centrifugal Casting; Die Casting; Engine Block; Piston; Al-Si Alloys; CGI
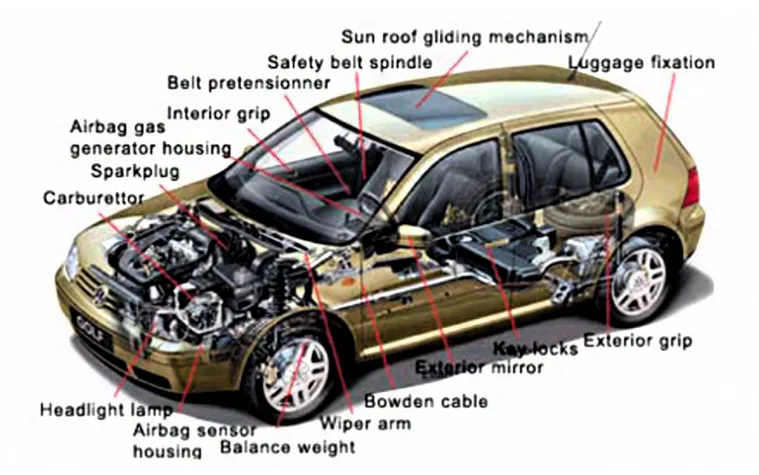
2. Research Background:
In the contemporary automotive industry, a paramount objective for manufacturers is the reduction of vehicle kerb weight while simultaneously enhancing component strength to adhere to stringent safety standards such as those stipulated by the New Car Assessment Programme (NCAP). This dual imperative necessitates the exploration and implementation of innovative manufacturing methodologies and advanced materials in automobile part production. Consequently, there is an exigency to review and evaluate the spectrum of casting processes employed in the automotive sector, alongside the materials that are integral to component fabrication. This review addresses this need by providing a comprehensive overview of established and contemporary casting techniques and their material applications in automotive engineering.
3. Research Purpose and Research Questions:
- Research Purpose: This paper aims to elucidate the diverse casting processes utilized in the manufacturing of automobile components and to delineate the materials commonly employed in these processes. Furthermore, it seeks to identify the most appropriate materials for specific automotive components in conjunction with a concise evaluation of the advantages and disadvantages inherent in each casting method.
- Key Research Questions:
- What are the principal casting processes currently deployed in the production of automobile parts?
- Which materials are predominantly utilized in conjunction with these casting methodologies for automotive component manufacturing?
- What are the comparative advantages and limitations associated with each of the discussed casting processes?
- Which materials are optimally suited for specific automotive components based on the casting process and performance requirements?
- Research Hypotheses: As a review paper, explicit research hypotheses are not formulated. However, the implicit proposition is that the selection of casting processes and materials for automobile parts is contingent upon a multifaceted evaluation of performance criteria, cost-effectiveness, and production scalability. The paper implicitly posits that die casting is a widely applicable method, while other processes offer specific advantages for certain applications or material requirements.
4. Research Methodology
- Research Design: This study adopts a review-based research design, synthesizing existing literature and industrial practices pertaining to casting methods and materials in the automotive domain.
- Data Collection Method: The methodology is predicated on a comprehensive review of scholarly articles, industry reports, and technical literature relevant to automotive casting processes and material applications.
- Analysis Method: The analytical approach is descriptive and comparative, involving the summarization and synthesis of information pertaining to various casting techniques, including Green sand casting, Centrifugal casting, Lost-foam casting, Die casting, and Squeeze casting. The analysis encompasses a comparative evaluation of the pros and cons of each method, alongside the materials typically associated with each process.
- Research Subjects and Scope: The scope of this review encompasses the principal casting methodologies (Green sand casting, Centrifugal casting, Lost-foam casting, Die casting, Squeeze casting) and materials (Cast irons, Al-Si alloys, Magnesium alloys, Titanium casts, Metal Matrix Composites (MMCs), Zinc alloys) employed in the fabrication of diverse automotive components, such as engine blocks, pistons, valve covers, wheels, and transmission housings.
5. Main Research Results:
- Key Research Results: The review elucidates the application of various casting processes in the automotive industry, highlighting Die casting as a ubiquitous method for mass production due to its capacity to produce lightweight, easily handled, and cost-effective parts, particularly from aluminium and zinc alloys. Green sand casting is presented as a cost-effective alternative for components with less stringent dimensional accuracy and surface finish requirements. Centrifugal casting is identified as advantageous for cylindrical components, yielding parts with reduced porosity and enhanced metallurgical cleanliness. Lost foam casting is recognized for its reliability in manufacturing engine blocks and intricate geometries. Squeeze casting is noted for its ability to enhance mechanical properties and reduce porosity in cast components. The paper also discusses material selection criteria for each process and component type, emphasizing the use of Al-Si alloys for their high strength-to-weight ratio and thermal conductivity. Compacted Graphite Iron (CGI) is highlighted as a preferred material over Grey cast iron for engine blocks due to its superior mechanical properties.
- Statistical/Qualitative Analysis Results:
- Table 1. Differences in mechanical properties of CGI and Grey cast iron An example of a column heading Grey Cast Iron Compacted Graphite Cast Iron Modulus of Elasticity; GPa 98-110 170-190 Tensile Strength; Mpa 160-320 300-600
- Table 2. Typical die temperatures and life of Al and Mg [16] Parameters Al Mg Max die life (number of cycles) 10,00,000 1,00,000 Die temperature (°C) 288 260 Casting temperature (°C) 660 760
- Centrifugal casting of pistons resulted in a hardness increase of 23.7 HRB from piston skirt to head, a 23% reduction in the coefficient of linear expansion, and a 70.4% improvement in wear resistance compared to gravity permanent mould casting.
- Addition of Strontium (Sb) and Antimony (Sr) to AlSi6Cu2Mg alloy reduces fluidity by 25% and 15% respectively.
- Data Interpretation: The data presented underscores the trade-offs between different casting processes and materials. Green sand casting offers cost advantages but sacrifices dimensional precision and surface quality. Die casting excels in mass production of intricate, lightweight parts but may incur higher tooling costs. Centrifugal casting is optimal for cylindrical forms requiring high integrity. Squeeze casting enhances mechanical properties, making it suitable for high-performance applications. The selection of CGI over Grey cast iron for engine blocks is justified by its superior mechanical strength, as quantified in Table 1. Die life and temperature considerations, as shown in Table 2, are critical parameters in die casting process design and material selection. The improvements observed in centrifugal cast pistons highlight the process's potential for enhancing component performance.
- Figure Name List:
- Fig. 1. Aluminium Die Cast Parts.
- Fig. 2. Flow chart of manufacturing of MMC pistons using squeeze casting.
- Fig. 3. The process of squeeze casting.

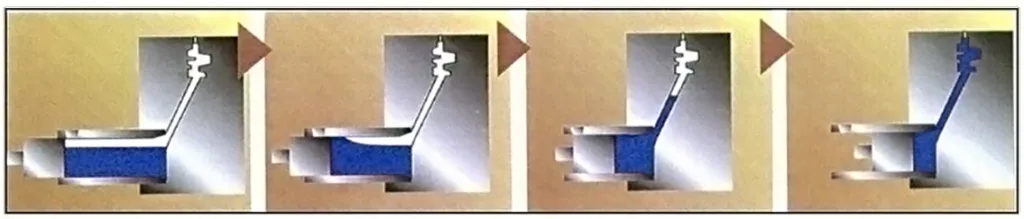
(c) Plunger moving to reach the gate of molten metal; (d) Plunger moving to completely filling of die cavity.
6. Conclusion and Discussion:
- Summary of Main Results: This review concludes that Die casting is extensively employed in the automotive industry for producing a wide array of components, despite its relatively higher cost. Green sand casting serves as a more economical alternative for parts where dimensional accuracy and surface finish are less critical. Specialized casting processes, such as centrifugal casting, lost foam casting and squeeze casting, are deployed based on specific component requirements and material characteristics. The paper elucidates the critical process parameters and material considerations for each casting method, providing a comprehensive guide for automotive component manufacturing.
- Academic Significance of the Research: This review contributes to the academic body of knowledge by consolidating information on casting processes and materials relevant to the automotive sector. It serves as a valuable resource for researchers and engineers seeking a comprehensive overview of established and contemporary casting techniques and their applications in automotive engineering.
- Practical Implications: The findings of this review offer practical guidance for automotive engineers and manufacturing professionals in selecting the most appropriate casting methods and materials for specific automotive components. The comparative analysis of process advantages and limitations, coupled with material recommendations, aids in optimizing component design, manufacturing efficiency, and cost-effectiveness.
- Limitations of the Research: As a review paper, this study is inherently limited by its reliance on existing literature and does not present novel experimental data or in-depth analyses of specific casting processes. The depth of analysis for each casting method and material is constrained by the scope of the reviewed literature.
7. Future Follow-up Research:
- Directions for Follow-up Research: Future research endeavors could focus on the optimization of individual casting processes for specific automotive materials and components. Further exploration into novel casting techniques and the development of advanced materials tailored for enhanced performance and weight reduction in automotive applications are warranted.
- Areas Requiring Further Exploration: Specific areas for future investigation include the optimization of process parameters for each casting method, the development of new alloy compositions with improved castability and performance characteristics, the application of computational simulation and modeling tools for process design and optimization, and comprehensive cost-benefit analyses of different casting methodologies in automotive mass production scenarios.
8. References:
- [1] H. Nguyen, "Manufacturing Processes and Engineering Materials Used in Automotive Engine Block," Mater. Sci. Eng. Sect. B, EGR250, pp. 11-23, 2005.
- [2] A. V. Adedayo, "Effects of addition of iron (Fe) filings to green moulding sand on the microstructure of grey cast iron," J. Brazilian Soc. Mech. Sci. Eng., vol. 32, no. 2, pp. 171-175, 2010.
- [3] D. Anantha Padmanaban and G. Kurien, "Silumins: The automotive alloys," Adv. Mater. Process., vol. 170, no. 3, pp. 28–30, 2012.
- [4] G. Chirita, D. Soares, and F. S. Silva, "Advantages of the centrifugal casting technique for the production of structural components with Al-Si alloys," Mater. Des., vol. 29, no. 1, pp. 20–27, 2008.
- [5] N. Periyasamy, "Thermal Analysys and Material Optimization of Piston in IC Engine," no. 3, pp. 1132-1144, 2018.
- [6] Q. Bakhsh, D. Ali, A. Ahmed, M. S. Wahab, K. Kamarudin, and A. A. Raus, "Mechanical Properties, Material and Design of the Automobile Piston: An Ample Review," Indian J. Sci. Technol., vol. 9, no. 36, pp. 5-11, 2016.
- [7] P. Scarber, H. Littleton, and A. Druschitz, "Preliminary Study of Compacted Graphite Iron Engine Blocks Produced by the Lost Foam Casting Process," AFS Trans, pp. 881-890, 2009.
- [8] R. Colás, J. Talamantes-Silva, S. Valtierra, F. Morales, and A. J. Pérez-Unzueta, "Cast-In Hypereutectic Aluminum Liners for Engine-Blocks," J. Manuf. Sci. Eng., vol. 131, no. 1, p. 014502, 2009.
- [9] M. Javidani and D. Larouche, "Application of cast Al-Si alloys in internal combustion engine components," Int. Mater. Rev., vol. 59, no. 3, pp. 132-158, 2014.
- [10] E. Aguirre-De La Torre, U. Afeltra, C. D. Gómez-Esparza, J. Camarillo-Cisneros, R. Pérez-Bustamante, and R. Martínez-Sánchez, "Grain refiner effect on the microstructure and mechanical properties of the A356 automotive wheels," J. Mater. Eng. Perform., vol. 23, no. 2, pp. 581-587, 2014.
- [11] B. Zhang, S. L. Cockcroft, D. M. Maijer, J. D. Zhu, and A. B. Phillion, "Casting defects in low-pressure die-cast aluminum alloy wheels," Jom, vol. 57, no. 11, pp. 36-43, 2005.
- [12] M. V. Kevorkijan, "MMCs for automotive applications," Am. Ceram. Soc. Bull., vol. 77, no. 12, pp. 53-59, 1998.
- [13] S. W. Youn, C. G. Kang, and P. K. Seo, "Thermal fluid/solidification analysis of automobile part by horizontal squeeze casting process and experimental evaluation," J. Mater. Process. Technol., vol. 146, no. 3, pp. 294-302, 2004.
- [15] Wu Shenqing and Li Jun, "Application of ceramic short fiber reinforced Al alloy matrix composites on piston for internal combustion engines."
- [16] Schrader, George F, Elshennawy, Ahmad K, Doyle, Lawrence E, "Manufacturing processes and materials", SME, p.186, ISBN 978-0-87263-517-3.
9. Copyright:
- This material is "Madhav Goenka et al."'s paper: Based on "Automobile Parts Casting-Methods and Materials Used: A Review".
- Paper Source: https://www.sciencedirect.com/journal/materials-today-proceedings/vol/22/suppl/C
This material was summarized based on the above paper, and unauthorized use for commercial purposes is prohibited.
Copyright © 2025 CASTMAN. All rights reserved.