This technical summary is based on the academic paper "Leakage-free cooling channels for Die-cast housing components" published by Dirk Lehmhus, Christoph Pille, Dustin Borheck, et al. in Giesserei (2018). It was analyzed and summarized for HPDC experts by CASTMAN experts with the help of LLM AI such as Gemini, ChatGPT, and Grok.
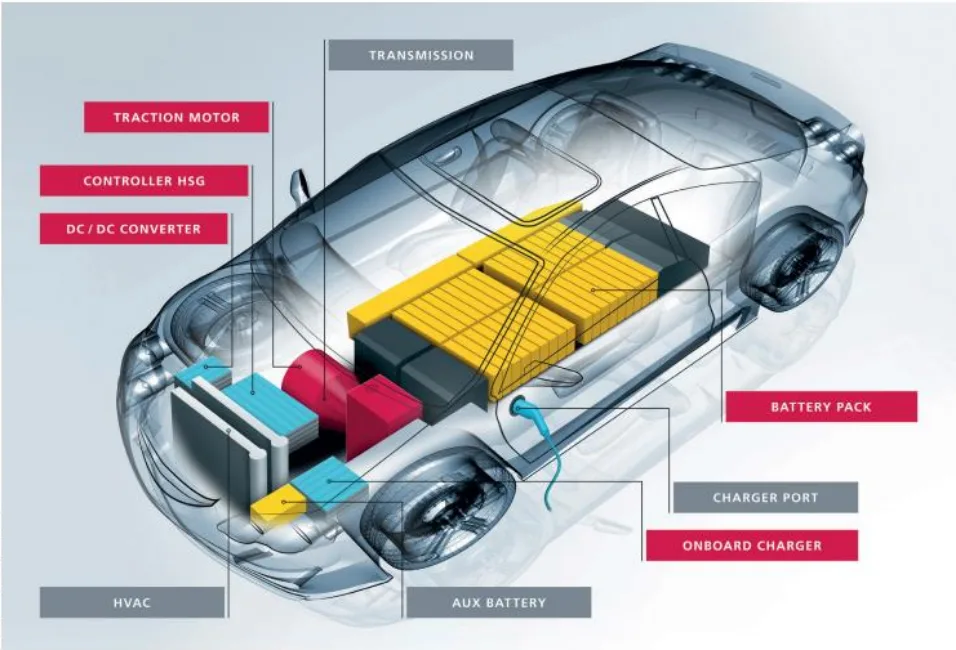
Keywords
- Primary Keyword: Die-cast cooling channels
- Secondary Keywords: HPDC for e-mobility, ZLeak Tube technology, Thermal management in die casting, Casting simulation (WinCast), Aluminum tube inserts, Electric motor housing casting, Heat transfer coefficient in die casting
Executive Summary
- The Challenge: The rise of electro-mobility demands advanced thermal management for components like batteries and motors. Integrating complex, leakage-free cooling channels into single-piece High-Pressure Die Casting (HPDC) housings without tube collapse or resorting to expensive multi-part assemblies has been a major manufacturing hurdle.
- The Method: Researchers in the "CoolCast" project conducted extensive trials on the "ZLeak Tube" technology—a specialized aluminum tube insert with a stabilizing, removable two-layer filler. They tested various alloys, wall thicknesses, and HPDC process parameters, using both physical experiments and advanced WinCast expert casting simulation to analyze the results.
- The Key Breakthrough: The study successfully proves that the ZLeak Tube technology is not only feasible but also highly predictable in HPDC applications. Crucially, casting simulations can accurately model pipe compression and displacement, enabling designers to engineer robust, complex cooling paths and optimize the die and process before cutting steel.
- The Bottom Line: This research validates a powerful new method for producing monolithic die-cast components with intricate, integrated cooling systems. It offers a clear, data-driven pathway for manufacturing the high-performance, thermally-optimized parts essential for the next generation of electric vehicles.
The Challenge: Why This Research Matters for HPDC Professionals
As the automotive industry pivots to electro-mobility, effective thermal management has become paramount. Key components like the battery pack, power electronics, and traction motor generate significant heat and require sophisticated cooling to maintain optimal performance and longevity (initial image). High-Pressure Die Casting (HPDC) is the ideal process for producing the lightweight, complex housings these components require, but integrating internal cooling channels has always been a significant challenge.
For decades, engineers have faced frustrating limitations. Attempting to cast-in standard, unreinforced aluminum tubes often results in their collapse under the immense pressure and heat of the molten metal (Image 1). Alternative solutions each come with their own drawbacks:
- Two-piece housings: Require additional molds, complex joining and sealing processes, and are susceptible to thermal stress at the joint, increasing costs and potential failure points.
- Steel tube inserts: Can withstand the casting process but create thermal expansion mismatches with the aluminum casting, leading to gap formation, reduced heat transfer, and potential corrosion issues.
This research addresses this critical industry need by validating a new approach to create geometrically complex, leakage-free cooling channels directly within a single die-cast part, combining performance with economic efficiency.
The Approach: Unpacking the Methodology
To tackle this challenge, the "CoolCast" project brought together industry leaders including MH Technologies (developer of the tube tech), ae group ag (die casting), Schaufler Tooling GmbH (tool making), and RWP GmbH (simulation), in cooperation with Fraunhofer IFAM.
The core of the investigation was the patented ZLeak Tube technology. This innovative approach uses an aluminum tube insert filled with a unique two-layer core: a water-soluble outer layer and a coarse-grained, media-permeable inner core (Image 2). This filler provides the structural stability needed to withstand the HPDC process and can be easily flushed out afterward.
The research team conducted a rigorous experimental program using a Bühler-SC/N-66 die casting machine. They tested various tube inserts in a specialized mold (Image 3), varying key parameters:
- Pipe Material: Aluminum alloys EN AW-6063 and EN AW-3003.
- Pipe Geometry: Outer diameter of 12 mm with wall thicknesses of 1 mm, 1.5 mm, and 2 mm.
- Process Parameters: Casting pressures from 600 to 1200 bar, casting piston speeds from 2.5 to 4.5 m/s, and pipe preheating temperatures from room temperature to 200°C.
Parallel to physical trials, the team used WinCast expert simulation software to model the mold filling, solidification, and thermal stresses. The simulation results were then validated against experimental data, including tests with interrupted shots to verify melt flow progression (Image 4).
The Breakthrough: Key Findings & Data
The study yielded several critical findings that demonstrate the viability and predictability of this technology for industrial applications.
- Finding 1: Pipe Compression is Predictable and Pressure-Dependent. The experiments revealed an approximately linear relationship between the maximum casting pressure and the compression (reduction in inner diameter) of the tube. As shown in Image 5, pipes with a 1 mm wall thickness compressed significantly more than those with 1.5 mm or 2 mm walls. Furthermore, the EN AW-3003 alloy tubes exhibited lower compression than similar tubes made from EN AW-6063, highlighting the importance of material selection.
- Finding 2: Displacement is Driven by Thermal Effects and Mechanical Constraints. Contrary to what one might expect, recompression pressure had only a minor effect on the displacement (movement) of the pipes within the mold. The dominant factors were thermal influences from the melt flow and the mechanical setup. As seen in Image 6, preheating the pipes significantly reduced their displacement. Using a movable bearing on one end of the pipe also proved effective in mitigating relocation.
- Finding 3: Simulation Accurately Models Real-World Behavior. A key outcome of the project is the validation of the casting simulation. The software was able to predict temperature-time curves at any point in the pipe, showing peak temperatures reaching 530°C, which corresponds to a significant loss of material strength (Image 7). Most importantly, there was a strong correlation between the pipe displacement predicted by the simulation and the actual measured displacement in the cast parts (Image 8), proving the tool's reliability for design and process engineering.
- Finding 4: Heat Transfer Can Be Quantified and Optimized. Using a custom test setup (Image 9), the researchers measured the heat transfer coefficient (HTC) between the tube and the casting. The results in Image 10 show that HTC tends to increase with recompression pressure for EN AW-6063 and that values for EN AW-3003 are generally higher. The study also acknowledges that microscopic gaps can form at the interface (Image 11, Image 13), which affects thermal performance and represents an area for further optimization.
Practical Implications for HPDC Products
This research offers immediately applicable insights for engineers and designers working on advanced die-cast components.
- For Process Engineers: The findings provide a clear guide for process control. Pipe compression can be managed by adjusting recompression pressure within a predictable range (Image 5). To minimize pipe movement and ensure positional accuracy, focus should be on thermal management strategies like preheating the inserts and optimizing melt flow, rather than solely on pressure adjustments (Image 6).
- For Quality Control: The validated simulation model (Image 8) is a powerful predictive quality tool. By using virtual sensors (Image 7), engineers can monitor thermal conditions and predict stress in difficult-to-measure areas of the pipe before the first part is cast, saving time and reducing scrap.
- For Die Design: This technology grants designers new freedom. The ability to create pipes with bending radii as tight as 1.5 times the diameter allows for highly complex and efficient cooling channel layouts, as demonstrated in the electric motor housing prototype (Image 12). Designers can now incorporate predictable levels of pipe compression and displacement into their CAD models, ensuring the final part meets all geometric tolerances.
Paper Details
Leakage-free cooling channels for Die-cast housing components
1. Overview:
- Title: Leakage-free cooling channels for Die-cast housing components
- Author: DIRK LEHMHUS, CHRISTOPH PILLE, DUSTIN BORHECK, BREMEN, FELICIA BUMBU, THOMAS SCHWEGLER, LAI CHINGEN, JUSTIN LEE, JINHO YOO, IN CHEON, KOREA, PETER LUTZE, GERS TUNGEN AND REINHARD VOMHOF, KONRAD WEISS, ROETGEN
- Year of publication: 2018
- Journal/academic society of publication: Giesserei
- Keywords: Electro mobility, Die-cast, Cooling channels, Housing components, ZLeak Tube, Casting simulation
2. Abstract:
The increasing power density of electric vehicle components necessitates advanced thermal management solutions. This paper investigates the feasibility of integrating complex, media-carrying cooling channels directly into High-Pressure Die Casting (HPDC) components using the "ZLeak Tube" technology, which employs a sacrificial-filled aluminum tube insert. Through a combination of physical casting trials and numerical simulation, the study analyzes the influence of process parameters—such as casting pressure, piston speed, and preheating—on the stability, compression, and displacement of the tube inserts. The research validates that the technology is stable under HPDC conditions and that its behavior is predictable using simulation tools, paving the way for the design and manufacture of single-piece, lightweight housings with integrated, leakage-free cooling for applications like electric motor and power electronics housings.
3. Introduction:
The advancement of electro-mobility presents new design challenges, with a primary focus shifting from purely power density to the optimization of thermal conditions. Geometrically complex cooling channels must be integrated into housings for batteries, power electronics, and motors during the manufacturing process. This requires new concepts that balance performance and economy. Traditional methods, such as casting in unsupported aluminum tubes or using multi-piece housings, have significant drawbacks. This study explores a new approach for creating integrated cooling channels in one-piece HPDC components to meet the thermal demands of modern electric drivetrains.
4. Summary of the study:
Background of the research topic:
Thermal management is a key design point for numerous assemblies in electric vehicles. Heat dissipation must be controlled to ensure optimal temperature and prevent power and capacity losses, particularly in battery elements, power electronics, and traction motors. HPDC is a preferred method for producing these housings, but integrating the necessary hollow channel structures is a significant manufacturing challenge.
Status of previous research:
Previous approaches for creating cooling channels in housings have included low-pressure or gravity casting with sand cores (lower productivity), two-piece HPDC housings (expensive, additional processing and joining steps), and casting-in steel pipes (thermal expansion mismatch). While casting-in tubes is used for hydraulic lines, using unreinforced aluminum tubes for cooling is problematic as they are not stable in the HPDC process (Image 1). Filler-based concepts like the Combicore approach exist, and this research builds on an alternative patented filler technology.
Purpose of the study:
The "CoolCast" project aimed to investigate and validate the use of the ZLeak Tube technology for creating cooling channels in HPDC parts. The key objectives were to determine the process limits, understand the effect of process parameters on pipe compression and deformation, validate the ability of casting simulation to represent these effects, and evaluate the application-related properties of the resulting cooling channels.
Core study:
The study involved casting experiments with straight and curved ZLeak Tube inserts made from different aluminum alloys (EN AW-6063, EN AW-3003) and wall thicknesses. These experiments were conducted on a HPDC machine while varying casting pressure, piston speed, and insert preheating temperature. The resulting castings were analyzed for pipe compression and displacement. The physical results were compared against predictions from WinCast expert simulation software. Additionally, the heat transfer coefficient between the pipe and casting was experimentally determined. Finally, the knowledge was applied to a demonstrator component resembling an electric motor housing.
5. Research Methodology
Research Design:
The research combined physical experimentation with numerical simulation. A multi-phase project structure was used, starting with simple test geometries (straight pipes, Image 3a) and progressing to more complex ones (curved pipes, Image 3b) and finally a full demonstrator component (Image 12). This allowed for systematic determination of correlations between process parameters and casting outcomes.
Data Collection and Analysis Methods:
Data was collected through physical measurements of the cast parts using X-ray analysis to determine pipe compression and displacement. Process data (pressure, speed) was recorded from the die casting machine. A custom test rig (Image 9) was built to measure the heat transfer coefficient. The simulation software WinCast expert was used to generate predictive data on melt flow, temperature profiles, stress, and deformation. The experimental and simulation data were then quantitatively compared (Image 8).
Research Topics and Scope:
The scope included:
- Pipe materials: EN AW-6063, EN AW-3003.
- Pipe geometry: 12mm OD with 2mm, 1.5mm, and 1mm wall thicknesses.
- Process parameters varied: Casting pressure (600-1200 bar), piston speed (2.5-4.5 m/s), pipe preheating (RT, 100°C, 200°C).
- Analysis of pipe compression, displacement, and heat transfer coefficient.
- Validation of casting simulation predictions against experimental results.
- Application to a demonstrator component with a helical cooling channel.
6. Key Results:
Key Results:
- Pipe compression shows an approximately linear dependence on the maximum casting pressure; EN AW-3003 alloy shows less compression than EN AW-6063 (Image 5).
- Pipe displacement is primarily influenced by thermal factors (melt flow, preheating temperature) and mechanical constraints (bearing type), with recompression pressure having a minor effect (Image 6).
- Casting simulation with WinCast expert accurately predicts pipe temperature during filling (up to 530°C) and the final displacement of the pipe, validating its use for predictive engineering (Image 7, Image 8).
- The heat transfer coefficient between the pipe and casting is measurable and tends to increase with recompression pressure for EN AW-6063. The presence of a micro-gap at the interface is a key factor affecting heat transfer (Image 10, Image 11).
- The technology was successfully applied to a demonstrator electric motor housing, proving its feasibility for producing complex components with helical cooling channels (Image 12, Image 13).
Figure Name List:
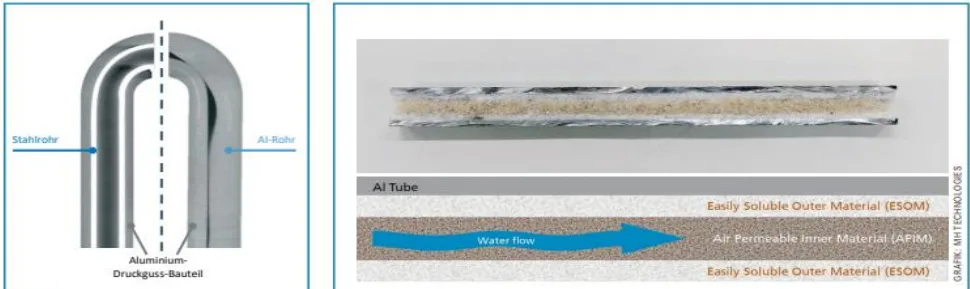
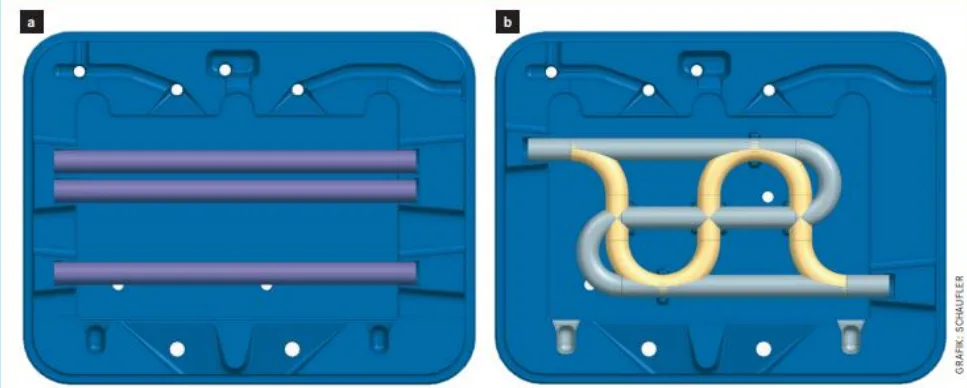
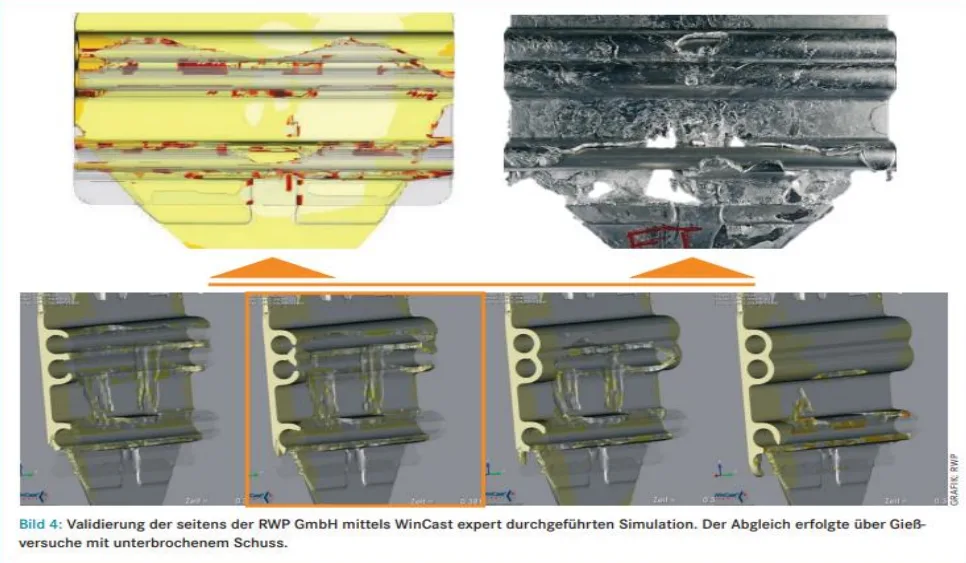
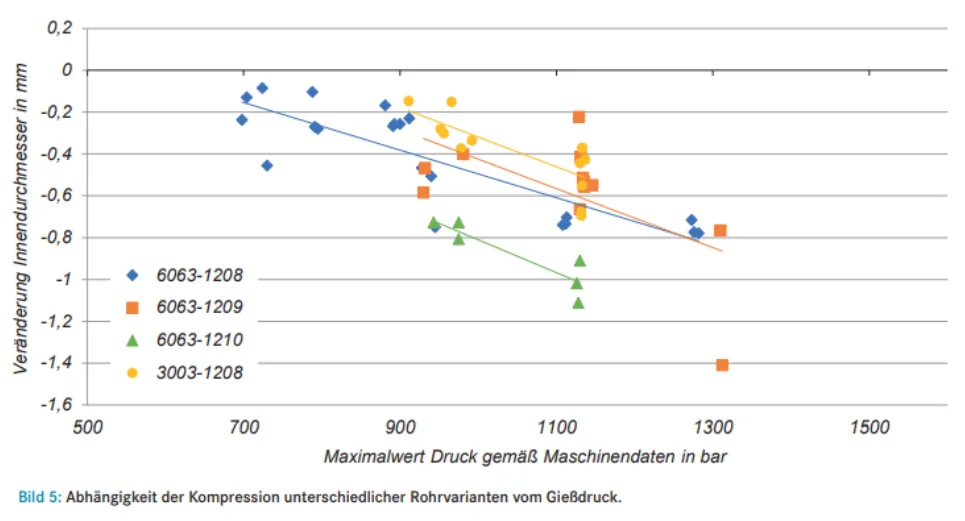
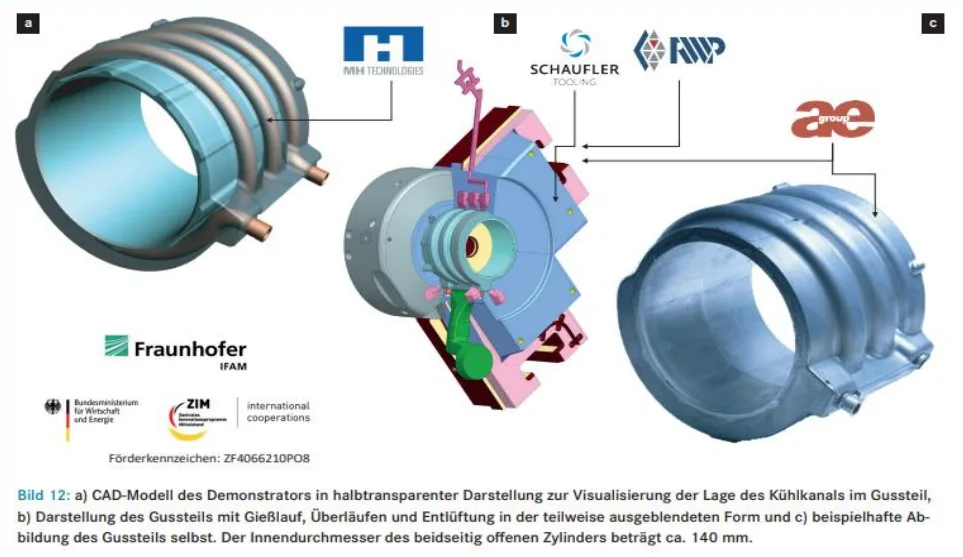
- Image 6: Dependence of the displacement of different pipe variants on the parameters or boundary conditions: a) recompression pressure, b) plunger speed, c) preheating temperature of the pipes, d) type of bearing.
- Image. 7: The simulation allows the determination of temperature-time curves for any position both in the cast part and in the depositors. In this specific case, temperatures of up to 530°C occur in the area of the pipe during the course of the mold filling and solidification, with a corresponding loss of strength.
- Image. 8: Comparison between the predicted and measured displacement of the pipe next to the gate under standard conditions, which is predicted by the casting simulation, meaning Pipe material EN AW-6063, wall thickness 2 mm (6063-1208), casting pressure nominal 800 bar, casting piston speed 2.5 m / s, temperature of mold and melt 220° C respectively 730 ° C, no preheating of the pipes, both side fixed bearing.
- Image. 9: Functional principle of the test setup for determining the heat transfer coefficient between pipe and casting. The embedded sketch illustrates which section of the casting was used for the measurements.
- Image. 10: Measurement results for the dependence of the heat transfer coefficient on the compression pressure, casting piston speed and preheating for the material variant EN AW-6063 and on the compression pressure for EN AW-3003.
- Image. 11: Problem of gap formation and its influence on the effective heat transfer coefficient.
- Image 12: a) CAD model of the demonstrator in a semi-transparent representation to visualize the position of the cooling channel in the casting, b) Representation of the cast part with pouring runner, overflows and ventilation in the partially hidden form and c) exemplary illustration of the cast part itself. The inner diameter of the cylinder, which is open on both sides, is approx. 140 mm.
- Image 13: CT-shot of the demonstrator with clearly visible gap between pipe and cast (compare enlarged detail on the right). The embedded picture shows the position of the cutting plane.
7. Conclusion:
The results of the CoolCast project prove the feasibility and predictability of the ZLeak Tube technology in die casting. This new solution can be used to implement media-carrying channels based on aluminum tubes in die-cast components, opening promising prospects for producing central components of the electric drivetrain that require precise temperature control. The pipes are stable up to recompression pressures of 1200 bar. The slight decrease in diameter and the thermal relocation of the pipes can be accurately predicted by casting simulation and therefore accounted for in the part design. This technology gives designers greater freedom, allowing for material savings and larger cooling channel diameters. While further optimization of the thermal connection between the channel and the cast part is possible, the technology already fulfills target requirements and increases the attractiveness of HPDC for e-mobility applications.
8. References:
- [1] Giesserei 105 (2018), [No.3], pp. 32-37
- [2] Heiselbetz, C.; Feikus, F. J.; Kniewallner, L.; Rafetzeder, M.; Luszczak, M. Challenges posed by E-Drive components:Casting solutions. Conference fee Casting technology in engine construction 2017, 01.-02. February 2017, Magdeburg.
- [3] SAE International Journal of Engines 2(2009), [No. 1], pp. 314-326.
- [4] Lahaye-Geusen, M. Light and compact housing for eight-speed automatic transmission lots of functionalities in a small space. https://automobilgestaltung.industrie. de / general / much-function-in-little space / (accessed 19.07.2021)
- [5] Foundry experience exchange 3/4 (2013) pp. 6-9.
- [6] www.mhrnd.com (accessed July 19, 2021)
- [7] Kim, J. S.; Yoo, J. High Pressure Die Casting Core and Preparation Method of High Pressure Die Casting Core. Korean patent KR101965669B1, date of Publication 04/04 2019.
Expert Q&A: Your Top Questions Answered
Q1: Why is this ZLeak Tube technology better than just casting-in a standard hollow aluminum tube?
A1: A standard hollow aluminum tube will collapse under the extreme pressures and temperatures typical of the HPDC process, as demonstrated in Image 1. The ZLeak Tube's innovative two-layer filler provides the necessary internal structural support to withstand these forces during casting. Afterwards, the filler is designed to be easily and completely rinsed out, leaving a perfectly formed, leakage-free channel (Image 2).
Q2: We're concerned about pipes moving during the shot. What is the biggest factor we need to control?
A2: According to the research, the most significant factors influencing pipe displacement are thermal effects from the melt flow and the mechanical constraints of how the pipe is held (its bearings). The study clearly shows that preheating the pipe inserts and using a design with a movable bearing on one side are highly effective at reducing displacement. These factors were more impactful than adjusting the recompression pressure (Image 6).
Q3: Can we trust simulations to predict how these tube inserts will behave in our specific die design?
A3: Yes. A key outcome of this project was the strong validation of the casting simulation software. The study found an excellent correlation between the pipe displacement predicted by the WinCast expert software and the actual measured results from the physical castings (Image 8). This proves that simulation is a reliable tool for predicting the behavior of these inserts, allowing you to optimize your die design and process parameters with confidence.
Q4: What kind of recompression pressure can these filled tubes withstand?
A4: The study tested recompression pressures up to 1200 bar. The ZLeak tubes remained stable across this entire range. The results show a predictable, approximately linear compression (diameter reduction) with increasing pressure (Image 5), which can be accounted for during the design phase. This confirms their suitability for demanding high-pressure die casting processes.
Q5: How does the choice of aluminum alloy for the tube affect its performance in the casting?
A5: The paper's comparison of EN AW-6063 and EN AW-3003 alloys revealed important differences. For the same geometry, the EN AW-3003 tubes showed less compression under pressure (Image 5) and a higher heat transfer coefficient to the casting (Image 10). This suggests that the choice of tube alloy is a critical design parameter that can be selected to optimize for either maximum stability or thermal performance.
Q6: Does the tube's wall thickness significantly impact its stability during casting?
A6: Within the limits studied for the EN AW-6063 alloy, the stability did not depend significantly on wall thickness when comparing 1.5 mm and 2 mm versions. However, a much thinner 1 mm wall showed a more pronounced reduction in diameter (Image 5). This implies that for a given stability requirement, you could potentially use a thinner wall (e.g., 1.5 mm) to save material or design a larger internal channel diameter without compromising the integrity of the insert during the casting process.
Conclusion & Next Steps
This research provides a valuable roadmap for enhancing thermal management in HPDC components, a critical enabler for the future of e-mobility. The findings validate the ZLeak Tube technology as a robust and predictable method for creating complex, integrated cooling channels, offering a clear, data-driven path toward improving quality, reducing manufacturing complexity, and optimizing the performance of electric drivetrain components.
At CASTMAN, we are dedicated to applying the latest industry research to solve our customers' most challenging die casting problems. If the issues discussed in this paper resonate with your operational goals, contact our engineering team to discuss how we can help you implement these advanced principles in your components.
Copyright
- This material is a paper by "Dirk Lehmhus, Christoph Pille, Dustin Borheck, et al.". Based on "Leakage-free cooling channels for Die-cast housing components".
- Source of the paper: https://www.ifam.fraunhofer.de/ (as part of the CoolCast Project, Funding code ZF4066210PO8)
This material is for informational purposes only. Unauthorized commercial use is prohibited. Copyright © 2025 CASTMAN. All rights reserved.