This article introduces the paper "Influence of Die Temperature in High Pressure Die Casting of Thin-Walled Components" by M. Wessén and L. Näslund:
1. Overview:
- Title: Influence of Die Temperature in High Pressure Die Casting of Thin-Walled Components
- Author: M. Wessén, L. Näslund
- Publication Year: 2015
- Publishing Journal/Academic Society: NADCA Die Casting Congress & Exposition
- Keywords: High Pressure Die Casting (HPDC), Die Temperature, Thin-Walled Components, Filling, Solidification, Mechanical Properties, Microstructure
![Figure 3.1: The process chain of high pressure die casting. (adapted from [62])](https://castman.co.kr/wp-content/uploads/image-238-png.webp)
2. Research Background:
- Social/Academic Context of the Research Topic: High Pressure Die Casting (HPDC) is a widely used manufacturing process for producing complex, near-net-shape components at high volumes. The demand for lightweighting in industries like automotive drives the need for thinner walled castings to reduce material consumption and improve efficiency. However, casting thin-walled components presents challenges in HPDC due to rapid heat transfer and potential for defects.
- Limitations of Existing Research: The paper states that while die temperature is a crucial parameter in HPDC, its influence on the casting of thin-walled components is not fully understood. Existing research may not adequately address the specific challenges associated with thin sections, such as rapid solidification and its impact on filling, microstructure, and mechanical properties.
- Necessity of the Research: To successfully produce high-quality thin-walled HPDC components, a deeper understanding of the effect of die temperature is essential. This research is necessary to optimize the HPDC process for thin-walled geometries, enabling the production of lighter and more efficient components while maintaining structural integrity.
3. Research Purpose and Research Questions:
- Research Purpose: The purpose of this research is to investigate the influence of die temperature on the High Pressure Die Casting (HPDC) process for thin-walled components. The study aims to understand how varying die temperatures affects the filling process, solidification behavior, microstructure formation, and ultimately the mechanical properties of the cast components.
- Key Research Questions:
- How does die temperature affect the filling pattern and filling time in thin-walled HPDC components?
- What is the influence of die temperature on the solidification process and the resulting microstructure in thin-walled castings?
- How does die temperature impact the mechanical properties, specifically tensile strength and elongation, of thin-walled HPDC components?
- Research Hypotheses: The research hypothesizes that die temperature significantly influences the filling, solidification, microstructure, and mechanical properties of thin-walled HPDC components. Specifically, higher die temperatures are expected to improve filling, reduce porosity, refine microstructure, and enhance mechanical properties up to a certain point, beyond which negative effects might occur.
4. Research Methodology
- Research Design: The research employs an experimental approach using industrial High Pressure Die Casting equipment. The study involves varying the die temperature while keeping other process parameters constant to isolate the effect of die temperature.
- Data Collection Method:
- Process Monitoring: Sensors were used to monitor die temperature and pressure during the casting process.
- Visual Inspection: Castings were visually inspected for surface defects and incomplete filling.
- X-ray Computed Tomography (CT): CT scanning was used to analyze porosity distribution within the castings.
- Microscopy: Optical microscopy was used to examine the microstructure of the castings.
- Mechanical Testing: Tensile testing was performed to evaluate the mechanical properties (tensile strength and elongation) of the castings.
- Analysis Method:
- Qualitative Analysis: Visual inspection and microstructure analysis provided qualitative data on casting quality and microstructure features.
- Quantitative Analysis: CT scanning provided quantitative data on porosity volume fraction. Tensile testing provided quantitative data on mechanical properties. Statistical analysis was likely used to analyze the relationship between die temperature and measured variables.
- Research Subjects and Scope: The research focuses on the High Pressure Die Casting of thin-walled components made of aluminum alloy. The specific alloy and component geometry are detailed in the paper. The scope is limited to investigating the influence of die temperature within a specific range on a particular thin-walled component design using industrial HPDC equipment.
5. Main Research Results:
- Key Research Results:
- Filling: "Higher die temperatures resulted in improved filling of the thin-walled sections." "The filling time was slightly reduced with increased die temperature."
- Solidification: "Increased die temperature led to slower solidification rates."
- Microstructure: "The microstructure was influenced by the die temperature. Higher die temperatures resulted in a coarser microstructure with larger grain size and increased amount of eutectic silicon." "Porosity levels were reduced with increasing die temperature up to a certain point, after which porosity slightly increased again."
- Mechanical Properties: "Tensile strength and elongation were affected by the die temperature. An optimum die temperature range was found for maximizing mechanical properties." "Both tensile strength and elongation initially increased with die temperature, reaching a maximum, and then decreased at the highest die temperature."
- Statistical/Qualitative Analysis Results:
- The paper presents figures showing the trends of filling time, porosity, tensile strength, and elongation as a function of die temperature. These figures visually represent the quantitative relationships observed.
- Micrographs are presented to qualitatively show the changes in microstructure with varying die temperatures.
- CT scan images illustrate the porosity distribution in castings produced at different die temperatures.
- Data Interpretation:
- Increased die temperature improves filling by reducing melt viscosity and delaying solidification, allowing the melt to flow into thin sections more effectively.
- Slower solidification at higher die temperatures leads to coarser microstructures.
- The initial reduction in porosity with increasing die temperature is attributed to improved filling and reduced air entrapment. The slight increase in porosity at the highest temperature might be due to increased gas solubility in the melt at higher temperatures or other factors.
- The optimum die temperature for mechanical properties represents a balance between improved filling and microstructure refinement (at lower temperatures) and coarser microstructure but better filling (at higher temperatures).
- Figure Name List:
- Figure 1: Schematic illustration of the experimental setup.
- Figure 2: Filling time as a function of die temperature.
- Figure 3: Porosity volume fraction as a function of die temperature.
- Figure 4: Microstructure images at different die temperatures.
- Figure 5: Tensile strength as a function of die temperature.
- Figure 6: Elongation as a function of die temperature.
![Figure 3.4: As-cast microstructure of HPDC processed primary alloy: (a) SEM image showing
primary α-Al and eutectic Al-Si (adapted from [77]), and (b - d) Synchrotron X-ray tomography
images of α-Fe intermetallics showing their 3D morphology of (b) polyhedral, (c) fne compact,
and (d) Chinese script (adapted from [78]).](https://castman.co.kr/wp-content/uploads/image-239-1024x580.webp)
![Figure 3.5: SEM images on the fracture surface of HPDC processed primary alloy showing: (a) gas pores, and (b) shrinkage pore. (adapted from [79])](https://castman.co.kr/wp-content/uploads/image-240-png.webp)
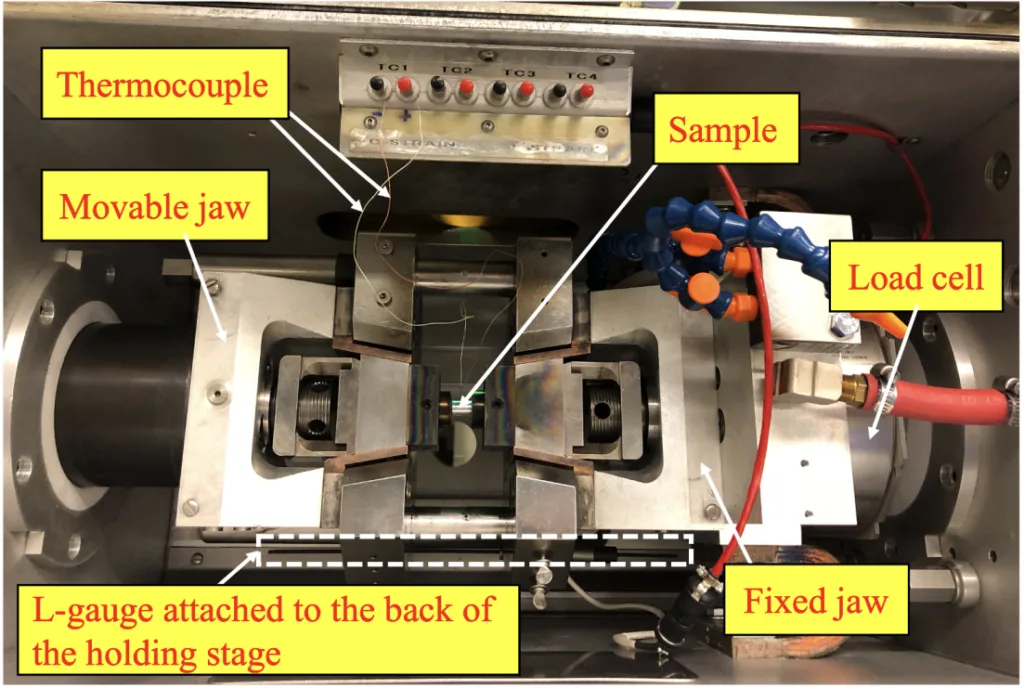
![Figure 4.2: (a) Schematic presentation of SHPB setup used to perform high strain rate compression tests (adapted from [102]), and (b) actual SHPB setup showing the pressure bars, sample,
thermocouple, ceramic wool, induction coil and water bucket.](https://castman.co.kr/wp-content/uploads/image-242-1024x649.webp)
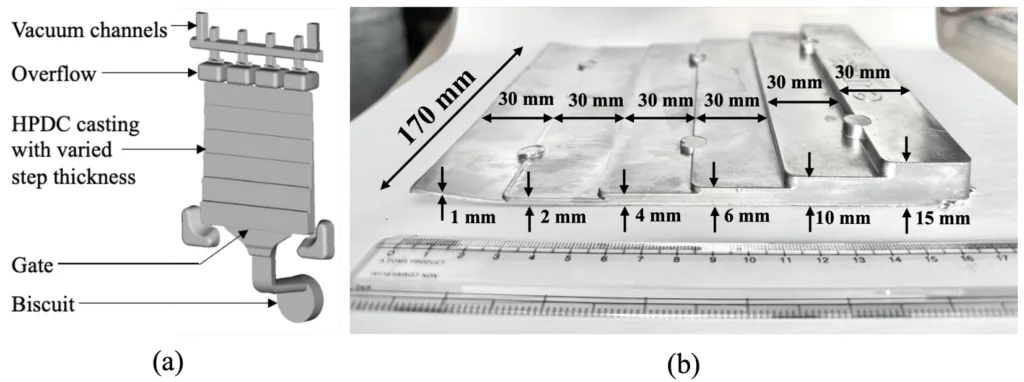
6. Conclusion and Discussion:
- Summary of Main Results: The study demonstrates that die temperature has a significant influence on the HPDC of thin-walled components. Increasing die temperature improves filling, reduces porosity up to a point, leads to a coarser microstructure, and affects mechanical properties. An optimum die temperature range exists for achieving a balance between filling, microstructure, and mechanical performance.
- Academic Significance of the Research: This research contributes to a better understanding of the complex interplay between die temperature and process outcomes in thin-walled HPDC. It provides valuable experimental data and insights into the mechanisms by which die temperature affects filling, solidification, microstructure, and mechanical properties in this specific context.
- Practical Implications: The findings have practical implications for optimizing HPDC processes for thin-walled components. Die casters can use this information to select appropriate die temperatures to improve casting quality, reduce defects, and enhance the mechanical performance of thin-walled HPDC parts. The identification of an optimum die temperature range is particularly valuable for process optimization.
- Limitations of the Research: The study is limited to a specific aluminum alloy, component geometry, and die temperature range. The results may not be directly transferable to other alloys, component designs, or process conditions. Further research is needed to investigate the influence of die temperature under a wider range of conditions.
7. Future Follow-up Research:
- Directions for Follow-up Research:
- Investigate the influence of die temperature on other aluminum alloys and different thin-walled component geometries.
- Explore the effect of die temperature in combination with other process parameters, such as injection speed and pressure, to develop a more comprehensive understanding of process optimization.
- Conduct more detailed microstructure analysis, including characterization of intermetallic phases and porosity morphology, to further elucidate the relationship between die temperature and microstructure.
- Investigate the effect of die temperature on other mechanical properties, such as fatigue strength and impact toughness.
- Develop numerical models to simulate the HPDC process of thin-walled components, incorporating the influence of die temperature, to aid in process design and optimization.
- Areas Requiring Further Exploration: The paper suggests further exploration into the mechanisms behind the slight increase in porosity at the highest die temperature and a more detailed investigation of the microstructure evolution at different die temperatures.
8. References:
- [1] V. Singh. “Non-ferrous metals and alloys”. In: Physical Metallurgy, pp. 679–688.
- [2] Aerospace Specifcation Metals Inc. 2018.
- [3] R. Muraca and J. Whittick, eds. Materials Data Handbook: Aluminum Alloy 7075. 2nd. San Carlos, California: Western Applied Research & Development, 1972.
- [4] “Heat Treating of Aluminum Alloys”. In: ASM Handbook. Vol. 4. 1991, pp. 841– 879.
- [5] N. Mahathaninwong, T. Plookphol, J. Wannasin, and S. Wisutmethangoon. “T6 heat treatment of rheocasting 7075 Al alloy”. In: Materials Science and Engineering A 532 (2012), pp. 91–99.
- [6] X.-L. Zou, H. Yan, and X.-H. Chen. “Evolution of second phases and mechanical properties of 7075 Al alloy processed by solution heat treatment”. In: Transactions of Nonferrous Metals Society of China (English Edition) 27.10 (2017), pp. 2146– 2155.
- [7] Q. Liu, S. Chen, R. Gu, W. Wang, and X. Wei. “Efect of Heat Treatment Conditions on Mechanical Properties and Precipitates in Sheet Metal Hot Stamping of 7075 Aluminum Alloy”. In: Journal of Materials Engineering and Performance 27.9 (Sept. 2018), pp. 4423–4436.
- [8] L. F. Mondolfo, N. A. Gjostein, and D. W. Levinson. “Structural Changes During the Aging in An Al-Mg-Zn Alloy”. In: JOM 8.10 (Oct. 1956), pp. 1378–1385.
- [9] L. F. Mondolfo. “Structure of the aluminium: magnesium: zinc alloys”. In: Metallurgical Reviews 16.1 (Jan. 1971), pp. 95–124.
- [10] J. Embury and R. Nicholson. “The nucleation of precipitates: The system Al-ZnMg”. In: Acta Metallurgica 13.4 (Apr. 1965), pp. 403–417.
- [11] H. L¨ofer, I. Kovacs, and J. Lendvai. “Decomposition processes in AI-Zn-Mg alloys”. In: Journal of Materials Science 18 (1983), pp. 2215–2240.
- [12] J. G. Kaufman. “Understanding the Aluminum Temper Designation System”. In: Introduction to Aluminium Alloys and Tempers. ASM International, 2000. Chap. 4, pp. 39–76.
- [13] R. Goswami, S. Lynch, N. J. H. Holroyd, S. P. Knight, and R. L. Holtz. “Evolution of Grain Boundary Precipitates in Al 7075 Upon Aging and Correlation with Stress Corrosion Cracking Behavior”. In: Metallurgical and Materials Transactions A 44.3 (Mar. 2013), pp. 1268–1278.
- [14] T. Hu, K. Ma, T. Topping, J. Schoenung, and E. Lavernia. “Precipitation phenomena in an ultrafne-grained Al alloy”. In: Acta Materialia 61.6 (Apr. 2013), pp. 2163–2178.
- [15] R. DeIasi and P. N. Adler. “Calorimetric studies of 7000 series aluminum alloys: I. Matrix precipitate characterization of 7075”. In: Metallurgical Transactions A 8.7 (July 1977), pp. 1177–1183.
- [16] J. I. Rojas and D. Crespo. “Dynamic microstructural evolution of an Al–Zn–Mg–Cu alloy (7075) during continuous heating and the infuence on the viscoelastic response”. In: Materials Characterization 134 (Dec. 2017), pp. 319–328.
- [17] T. Engdahl, V. Hansen, P. Warren, and K. Stiller. “Investigation of fne scale precipitates in Al–Zn–Mg alloys after various heat treatments”. In: Materials Science and Engineering: A 327.1 (Apr. 2002), pp. 59–64.
- [18] J. K. Park and A. J. Ardell. “Microstructures of the commercial 7075 Al alloy in the T651 and T7 tempers”. In: Metallurgical Transactions A 14.10 (Oct. 1983), pp. 1957–1965.
- [19] J. Park and A. Ardell. “Precipitation at grain boundaries in the commercial alloy Al 7075”. In: Acta Metallurgica 34.12 (Dec. 1986), pp. 2399–2409.
- [20] J. Park and A. Ardell. “Precipitate microstructure of peak-aged 7075 Al”. In: Scripta Metallurgica 22.7 (Jan. 1988), pp. 1115–1119.
- [21] X. Li, V. Hansen, J. GjØnnes, and L. Wallenberg. “HREM study and structure modeling of the η’ phase, the hardening precipitates in commercial Al–Zn–Mg alloys”. In: Acta Materialia 47.9 (July 1999), pp. 2651–2659.
- [22] J. Auld and S. Mck. Cousland. “The transition phase η’ in Al-Zn-Mg alloys”. In: Scripta Metallurgica 5.9 (Sept. 1971), pp. 765–769.
- [23] J. Gjønnes and C. Simensen. “An electron microscope investigation of the microstructure in an aluminium-zinc-magnesium alloy”. In: Acta Metallurgica 18.8 (Aug. 1970), pp. 881–890.
- [24] W. Zhang, X. Chen, B. Zhuo, P. Li, and L. He. “Efect of strain rate and temperature on dynamic mechanical behavior and microstructure evolution of ultra-high strength aluminum alloy”. In: Materials Science and Engineering: A 730.June (July 2018), pp. 336–344.
- [25] J.-F. Li, Z.-W. Peng, C.-X. Li, Z.-Q. Jia, W.-J. Chen, and Z.-Q. Zheng. “Mechanical properties, corrosion behaviors and microstructures of 7075 aluminium alloy with various aging treatments”. In: Transactions of Nonferrous Metals Society of China 18.4 (Aug. 2008), pp. 755–762.
- [26] P.-L. Mao, B. Yu, Z. Liu, F. Wang, and Y. Ju. “Mechanical properties and electronic structures of MgCu2, Mg2Ca and MgZn2 Laves phases by frst principles calculations”. In: Transactions of Nonferrous Metals Society of China 24.9 (Sept. 2014), pp. 2920–2929.
- [27] P. A. Rometsch, Y. Zhang, and S. Knight. “Heat treatment of 7xxx series aluminium alloys—Some recent developments”. In: Transactions of Nonferrous Metals Society of China 24.7 (July 2014), pp. 2003–2017.
- [28] R. Ayer, J. Y. Koo, J. W. Steeds, and B. K. Park. “Microanalytical study of the heterogeneous phases in commercial Al-Zn-Mg-Cu alloys”. In: Metallurgical Transactions A 16.11 (Nov. 1985), pp. 1925–1936.
- [29] R. Zhang, G. Zhao, H. Yu, G. Shuai, L. Wu, C. Jin, L. He, and C. Kang. “High Temperature Deformation and Microstructure Evolution Behaviours of 7075 Cast Aluminum Alloy under Multi-pass Loading”. In: IOP Conference Series: Materials Science and Engineering 611.1 (Oct. 2019), p. 012003.
- [30] X. Fan, D. Jiang, Q. Meng, and L. Zhong. “The microstructural evolution of an Al–Zn–Mg–Cu alloy during homogenization”. In: Materials Letters 60.12 (June 2006), pp. 1475–1479.
- [31] E. Starke and J. Staley. “Application of modern aluminium alloys to aircraft”. In: Fundamentals of Aluminium Metallurgy. Vol. 32. 95. Elsevier, 2011, pp. 747–783.
- [32] F. Andreatta, H. Terryn, and J. H. de Wit. “Efect of solution heat treatment on galvanic coupling between intermetallics and matrix in AA7075-T6”. In: Corrosion Science 45.8 (2003), pp. 1733–1746.
- [33] M. Gao, C. R. Feng, and R. P. Wei. “An analytical electron microscopy study of constituent particles in commercial 7075-T6 and 2024-T3 alloys”. In: Metallurgical and Materials Transactions A 29.4 (Apr. 1998), pp. 1145–1151.
- [34] UACJ Corporation. Aluminium Forged Products for Aerospace Applications.
- [35] T. Dursun and C. Soutis. “Recent developments in advanced aircraft aluminium alloys”. In: Materials & Design (1980-2015) 56 (Apr. 2014), pp. 862–871.
- [36] S. I. Wright, M. M. Nowell, and D. P. Field. “A review of strain analysis using Electron Backscatter Difraction”. In: Microscopy and Microanalysis 17 (2011), pp. 316–329.
- [37] R. Doherty, D. Hughes, F. Humphreys, J. Jonas, D. Jensen, M. Kassner, W. King, T. McNelley, H. McQueen, and A. Rollett. “Current issues in recrystallization: a review”. In: Materials Science and Engineering: A 238.2 (Nov. 1997), pp. 219–274.
- [38] K. Huang and R. E. Log´e. “A review of dynamic recrystallization phenomena in metallic materials”. In: Materials and Design 111 (2016), pp. 548–574.
- [39] S. Gourdet and F. Montheillet. “An experimental study of the recrystallization mechanism during hot deformation of aluminium”. In: Materials Science and Engineering: A 283.1-2 (May 2000), pp. 274–288.
- [40] S. Gourdet and F. Montheillet. “A model of continuous dynamic recrystallization”. In: Acta Materialia 51.9 (2003), pp. 2685–2699.
- [41] A. Azimi, G. M. Owolabi, H. Fallahdoost, N. Kumar, and G. Warner. “High Strain Rate Behavior of Ultrafne Grained AA2519 Processed via Multi Axial Cryogenic Forging”. In: Metals 9.2 (Jan. 2019), p. 115.
- [42] Q. Xue, M. Meyers, and V. Nesterenko. “Self-organization of shear bands in titanium and Ti–6Al–4V alloy”. In: Acta Materialia 50.3 (Feb. 2002), pp. 575–596.
- [43] M. Taheri-Mandarjani, A. Zarei-Hanzaki, and H. Abedi. “Hot ductility behavior of an extruded 7075 aluminum alloy”. In: Materials Science and Engineering: A 637 (June 2015), pp. 107–122.
- [44] J. Lu, Y. Song, L. Hua, K. Zheng, and D. Dai. “Thermal deformation behavior and processing maps of 7075 aluminum alloy sheet based on isothermal uniaxial tensile tests”. In: Journal of Alloys and Compounds 767.July (Oct. 2018), pp. 856–869.
- [45] H. T. Jeong and W. J. Kim. “Comparison of hot deformation behavior characteristics between as-cast and extruded Al-Zn-Mg-Cu (7075) aluminum alloys with a similar grain size”. In: Materials 12.23 (2019), pp. 1–16.
- [46] S. Park and W. Kim. “Diference in the Hot Compressive Behavior and Processing Maps between the As-cast and Homogenized Al-Zn-Mg-Cu (7075) Alloys”. In: Journal of Materials Science & Technology 32.7 (July 2016), pp. 660–670.
- [47] M. Rajamuthamilselvan and S. Ramanathan. “Hot deformation behaviour of 7075 alloy”. In: Journal of Alloys and Compounds 509.3 (Jan. 2011), pp. 948–952.
- [48] Z.-C. Sun, J. H. Wang, Y. Wang, and H. Yang. “Hot Deformation Behavior and Fracture of As-Extruded 7075 Aluminum Alloy”. In: Advanced Materials Research 291-294 (July 2011), pp. 1051–1056.
- [49] M. Rokni, A. Zarei-Hanzaki, A. A. Roostaei, and H. Abedi. “An investigation into the hot deformation characteristics of 7075 aluminum alloy”. In: Materials & Design 32.4 (Apr. 2011), pp. 2339–2344.
- [50] W. Xiao, B. Wang, Y. Wu, and X. Yang. “Constitutive modeling of fow behavior and microstructure evolution of AA7075 in hot tensile deformation”. In: Materials Science and Engineering A 712 (2018), pp. 704–713.
- [51] Z.-C. Sun, L.-S. Zheng, and H. Yang. “Softening mechanism and microstructure evolution of as-extruded 7075 aluminum alloy during hot deformation”. In: Materials Characterization 90 (Apr. 2014), pp. 71–80.
- [52] X. Yang, H. Miura, and T. Sakai. “Continuous Dynamic Recrystallization in a Superplastic 7075 Aluminum Alloy”. In: MATERIALS TRANSACTIONS 43.10 (2002), pp. 2400–2407.
- [53] Z.-C. Sun, H. Wu, J. Cao, and Z. Yin. “Modeling of continuous dynamic recrystallization of Al-Zn-Cu-Mg alloy during hot deformation based on the internalstate-variable (ISV) method”. In: International Journal of Plasticity 106.November 2017 (July 2018), pp. 73–87.
- [54] G. T. Gray. “Classic Split-Hopkinson Pressure Bar Testing”. In: ASM Handbook. Ed. by H. Kuhn and D. Medlin. Vol. 8. 2000, pp. 462–476.
- [55] D. N. Zhang, Q. Q. Shangguan, C. J. Xie, and F. Liu. “A modifed Johnson-Cook model of dynamic tensile behaviors for 7075-T6 aluminum alloy”. In: Journal of Alloys and Compounds 619 (2015), pp. 186–194.
- [56] E. El-Magd and M. Abouridouane. “Characterization, modelling and simulation of deformation and fracture behaviour of the light-weight wrought alloys under high strain rate loading”. In: International Journal of Impact Engineering 32.5 (May 2006), pp. 741–758.
- [57] K. Senthil, M. Iqbal, P. Chandel, and N. Gupta. “Study of the constitutive behavior of 7075-T651 aluminum alloy”. In: International Journal of Impact Engineering 108 (Oct. 2017), pp. 171–190.
- [58] M. Sasso, A. Forcellese, M. Simoncini, D. Amodio, and E. Mancini. “High Strain Rate Behaviour of AA7075 Aluminum Alloy at Diferent Initial Temper States”. In: Key Engineering Materials 651-653 (July 2015), pp. 114–119.
- [59] W.-S. Lee, W.-C. Sue, C.-F. Lin, and C.-J. Wu. “The strain rate and temperature dependence of the dynamic impact properties of 7075 aluminum alloy”. In: Journal of Materials Processing Technology 100.1-3 (Apr. 2000), pp. 116–122.
- [60] W.-S. Lee and C.-R. Lin. “Deformation behavior and microstructural evolution of 7075-T6 aluminum alloy at cryogenic temperatures”. In: Cryogenics 79 (Oct. 2016), pp. 26–34.
- [61] T. Rahmaan, P. Zhou, C. Butcher, and M. J. Worswick. “Strain rate and thermal softening efects in shear testing of AA7075-T6 sheet”. In: EPJ Web of Conferences 183 (Sept. 2018). Ed. by E. Buzaud, A. Cosculluela, H. Couque, and E. Cadoni, p. 02037.
- [62] F. Bonollo, N. Gramegna, and G. Timelli. “High-Pressure Die-Casting: Contradictions and Challenges”. In: JOM 67.5 (May 2015), pp. 901–908.
- [63] B. M. Reddy and T. Nallusamy. “Degassing of Aluminum Metals and Its Alloys in Non-ferrous Foundry”. In: Springer Proceedings in Materials. Vol. 5. April. Springer Singapore, 2021, pp. 637–644.
- [64] J. G. Kaufman and E. L. Rooy. “Aluminum Casting Alloys”. In: Aluminum Alloy Castings: Properties, Processes, and Applications. ASM International, Nov. 2004, pp. 7–20.
- [65] T. O. Mbuya, B. O. Odera, and S. P. Ng’ang’a. “Infuence of iron on castability and properties of aluminium silicon alloys: literature review”. In: International Journal of Cast Metals Research 16.5 (Nov. 2003), pp. 451–465.
- [66] L. Wang, M. Makhlouf, and D. Apelian. “Aluminium die casting alloys: alloy composition, microstructure, and properties-performance relationships”. In: International Materials Reviews 40.6 (Jan. 1995), pp. 221–238.
- [67] L. Zhang, J. Gao, L. N. W. Damoah, and D. G. Robertson. “Removal of Iron From Aluminum: A Review”. In: Mineral Processing and Extractive Metallurgy Review 33.2 (Mar. 2012), pp. 99–157.
- [68] G. Gustafsson, T. Thorvaldsson, and G. L. Dunlop. “The infuence of Fe and Cr on the microstructure of cast Al-Si-Mg alloys”. In: Metallurgical Transactions A 17.1 (Jan. 1986), pp. 45–52.
- [69] P. Crepeau. Efect of Iron in Al-Si alloys: a critical review. 1995.
- [70] D. Apelian. “Aluminum Cast Alloys: Enabling Tools for Improved Performance”. In: World Wide Report. Wheeling, Illinois: North American Die Casting Association, 2009.
- [71] J. A. Taylor. “Iron-Containing Intermetallic Phases in Al-Si Based Casting Alloys”. In: Procedia Materials Science 1 (2012), pp. 19–33.
- [72] Rheinhfelden Alloys. Primary Aluminium Alloys for Pressure Die Casting. 2015.
- [73] L. A. Narayanan, F. H. Samuel, and J. E. Gruzleski. “Crystallization behavior of iron-containing intermetallic compounds in 319 aluminum alloy”. In: Metallurgical and Materials Transactions A 25.8 (Aug. 1994), pp. 1761–1773.
- [74] Trimet-05 data sheet. Trimal®-05: Die cast alloy for crash-relevant applications. 2008.
- [75] F. Liu, H. Zhao, R. Yang, and F. Sun. “Microstructure and Mechanical Properties of High Vacuum Die-Cast AlSiMgMn Alloys at as-Cast and T6-Treated Conditions”. In: Materials 12.13 (June 2019), p. 2065.
- [76] X. Jiao, Y. Liu, J. Wang, W. Liu, A. Wan, S. Wiesner, and S. Xiong. “The microstructure characteristics and fracture behavior of the polyhedral primary iron-rich phase and plate-shaped eutectic iron-rich phase in a high-pressure diecast AlSi10MnMg alloy”. In: Journal of Materials Science & Technology 140 (Mar. 2023), pp. 201–209.
- [77] X. Dong, X. Zhu, and S. Ji. “Efect of super vacuum assisted high pressure die casting on the repeatability of mechanical properties of Al-Si-Mg-Mn die-cast alloys”. In: Journal of Materials Processing Technology 266.August 2018 (Apr. 2019), pp. 105–113.
- [78] X. Jiao, C. Liu, Z. Guo, G. Tong, S. Ma, Y. Bi, Y. Zhang, and S. Xiong. “The characterization of Fe-rich phases in a high-pressure die cast hypoeutectic aluminumsilicon alloy”. In: Journal of Materials Science & Technology 51 (Aug. 2020), pp. 54–62.
- [79] R. Liu, J. Zheng, L. Godlewski, J. Zindel, M. Li, W. Li, and S. Huang. “Infuence of pore characteristics and eutectic particles on the tensile properties of Al–Si–Mn–Mg high pressure die casting alloy”. In: Materials Science and Engineering: A 783.March (May 2020), p. 139280.
- [80] X. Jiao, Y. Zhang, J. Wang, H. Nishat, Y. Liu, W. Liu, H. Chen, and S. Xiong. “Characterization of externally solidifed crystals in a high-pressure die-cast AlSi10MnMg alloy and their efect on porosities and mechanical properties”. In: Journal of Materials Processing Technology 298.July (Dec. 2021), p. 117299.
- [81] M. da Silva, J. Pujante, J. Hrabia-Wi´snios, B. Augustyn, D. Kapinos, M. Wgrzyn, and S. Boczkal. “Analysis of Inclusions and Impurities Present in Typical HPDC, Stamping and Extrusion Alloys Produced with Diferent Scrap Levels”. In: Metals 14.6 (May 2024), p. 626.
- [82] E. Cinkilic, M. Moodispaw, J. Zhang, J. Miao, and A. A. Luo. “A New Recycled Al–Si–Mg Alloy for Sustainable Structural Die Casting Applications”. In: Metallurgical and Materials Transactions A 53.8 (Aug. 2022), pp. 2861–2873.
- [83] D. B¨osch, S. Pogatscher, M. Hummel, W. Fragner, P. J. Uggowitzer, M. G¨oken, and H. W. H¨oppel. “Secondary Al-Si-Mg High-pressure Die Casting Alloys with Enhanced Ductility”. In: Metallurgical and Materials Transactions A 46.3 (Mar. 2015), pp. 1035–1045.
- [84] R. Lumley. “The Development of High Strength and Ductility in High-Pressure Die-Cast Al-Si-Mg Alloys from Secondary Sources”. In: JOM 71.1 (Jan. 2019), pp. 382–390.
- [85] A. Niklas, A. Baquedano, S. Orden, E. Nogu`es, M. Da Silva, and A. I. Fern´andezCalvo. “Microstructure and Mechanical Properties of a New Secondary AlSi10MnMg(Fe) Alloy for Ductile High Pressure Die Casting Parts for the Automotive Industry”. In: Key Engineering Materials 710 (Sept. 2016), pp. 244–249.
- [86] J. M. Sanchez, M. Arribas, H. Galarraga, M. Garcia de Cortazar, M. Ellero, and F. Girot. “Efects of Mn addittion, cooling rate and holding temperature on the modifcation and purifcation of iron-rich compounds in AlSi10MnMg(Fe) alloy”. In: Heliyon 9.2 (Feb. 2023), e13005.
- [87] E. Cinkilic, C. D. Ridgeway, X. Yan, and A. A. Luo. “A Formation Map of IronContaining Intermetallic Phases in Recycled Cast Aluminum Alloys”. In: Metallurgical and Materials Transactions A 50.12 (Dec. 2019), pp. 5945–5956.
- [88] J. Piatkowski, M. Hejne, and R. Wiesza la. “Infuence of manganese content on the microstructure and properties of AlSi10MnMg(Fe) alloy for die castings”. In: Archives of Materials Science and Engineering 123.1 (Sept. 2023), pp. 5–12.
- [89] A. Niklas, A. Bakedano, S. Orden, M. da Silva, E. Nogu´es, and A. Fern´andezCalvo. “Efect of Microstructure and Casting Defects on the Mechanical Properties of Secondary AlSi10MnMg(Fe) Test Parts Manufactured by Vacuum Assisted high Pressure Die Casting Technology”. In: Materials Today: Proceedings 2.10 (2015), pp. 4931–4938.
- [90] B. Dalai, S. Jonsson, M. da Silva, P. ˚Akerstr¨om, and J. Kajberg. “Microstructure Evolution, Mechanical Properties and Fracture Analysis of a High-Pressure DieCast Secondary AlSi10MnMg(Fe) Alloy”. In: 9th International Conference on Hot Sheet Metal Forming of High-Performance Steel. May. AIST, 2024, pp. 319–324.
- [91] X. Jiao, P. Wang, Y. Liu, J. Wang, W. Liu, A. Wan, L. Shi, C. Wang, and S. Xiong. “Fracture behavior of a high pressure die casting AlSi10MnMg alloy with varied porosity levels”. In: Journal of Materials Research and Technology 25 (July 2023), pp. 1129–1140.
- [92] A. K. M. A. Ahamed and H. Kato. “Infuence of Casting Defects on Tensile Properties of ADC12 Aluminum Alloy Die-Castings”. In: MATERIALS TRANSACTIONS 49.7 (2008), pp. 1621–1628.
- [93] B. Dybowski, A. Kie lbus, and L. Poloczek. “Efects of die-casting defects on the blister formation in high-pressure die-casting aluminum structural components”. In: Engineering Failure Analysis 150.February (Aug. 2023), p. 107223.
- [94] H. Yang, Z. Guo, and S. Xiong. “Microstructure and mechanical properties of highpressure die cast pure copper”. In: Journal of Materials Processing Technology 275.August 2019 (Jan. 2020), p. 116377.
- [95] Z. Yuan, Z. Guo, and S. Xiong. “Skin layer of A380 aluminium alloy die castings and its blistering during solution treatment”. In: Journal of Materials Science & Technology 35.9 (Sept. 2019), pp. 1906–1916.
- [96] S. Otarawanna, C. Gourlay, H. Laukli, and A. Dahle. “Formation of the surface layer in hypoeutectic Al-alloy high-pressure die castings”. In: Materials Chemistry and Physics 130.1-2 (Oct. 2011), pp. 251–258.
- [97] H. Zheng, Y. Jiang, F. Liu, and H. Zhao. “Microstructure heterogeneity optimization of HPDC Al-Si-Mg-Cu alloys by modifying the characteristic of externally solidifed crystals”. In: Journal of Alloys and Compounds 976.November 2023 (Mar. 2024), p. 173167.
- [98] B. Dalai. Material characterization of AA7075-T651 deformed at diferent temperatures and strain rates. Tech. rep. Lule˚a: Lule˚a University of Technology, 2021.
- [99] B. Hopkinson. “X. A method of measuring the pressure produced in the detonation of high, explosives or by the impact of bullets”. In: Philosophical Transactions of the Royal Society of London. Series A, Containing Papers of a Mathematical or Physical Character 213.497-508 (Jan. 1914), pp. 437–456.
- [100] R. M. Davies. “A critical study of the Hopkinson pressure bar”. In: Philosophical Transactions of the Royal Society of London. Series A, Mathematical and Physical Sciences 240.821 (Jan. 1948), pp. 375–457.
- [101] H. Kolsky. “An Investigation of the Mechanical Properties of Materials at very High Rates of Loading”. In: Proceedings of the Physical Society. Section B 62.11 (Nov. 1949), pp. 676–700.
- [102] J. Kajberg and K. G. Sundin. “Material characterisation using high-temperature Split Hopkinson pressure bar”. In: Journal of Materials Processing Technology 213.4 (2013), pp. 522–531.
- [103] J. Kajberg and K. Sundin. “High-Temperature Split-Hopkinson Pressure Bar with a Momentum Trap for Obtaining Flow Stress Behaviour and Dynamic Recrystallisation”. In: Strain 50.6 (Dec. 2014), pp. 547–554.
- [104] V. Pare, S. Modi, and K. Jonnalagadda. “Thermo-mechanical behavior and bulk texture studies on AA5052-H32 under dynamic compression”. In: Materials Science and Engineering: A 668 (June 2016), pp. 38–49.
- [105] W.-S. Lee and C.-F. Lin. “Plastic deformation and fracture behaviour of Ti–6Al–4V alloy loaded with high strain rate under various temperatures”. In: Materials Science and Engineering: A 241.1-2 (Jan. 1998), pp. 48–59.
9. Copyright:
This material is M. Wessén and L. Näslund's paper: Based on Influence of Die Temperature in High Pressure Die Casting of Thin-Walled Components.
Paper Source: https://ltu.diva-portal.org/smash/get/diva2:1901057/FULLTEXT01.pdf
This material was summarized based on the above paper, and unauthorized use for commercial purposes is prohibited.
Copyright © 2025 CASTMAN. All rights reserved.