This introduction paper is based on the paper "The coating failure of coated core pin for die casting process" published by "NADCA Transactions".
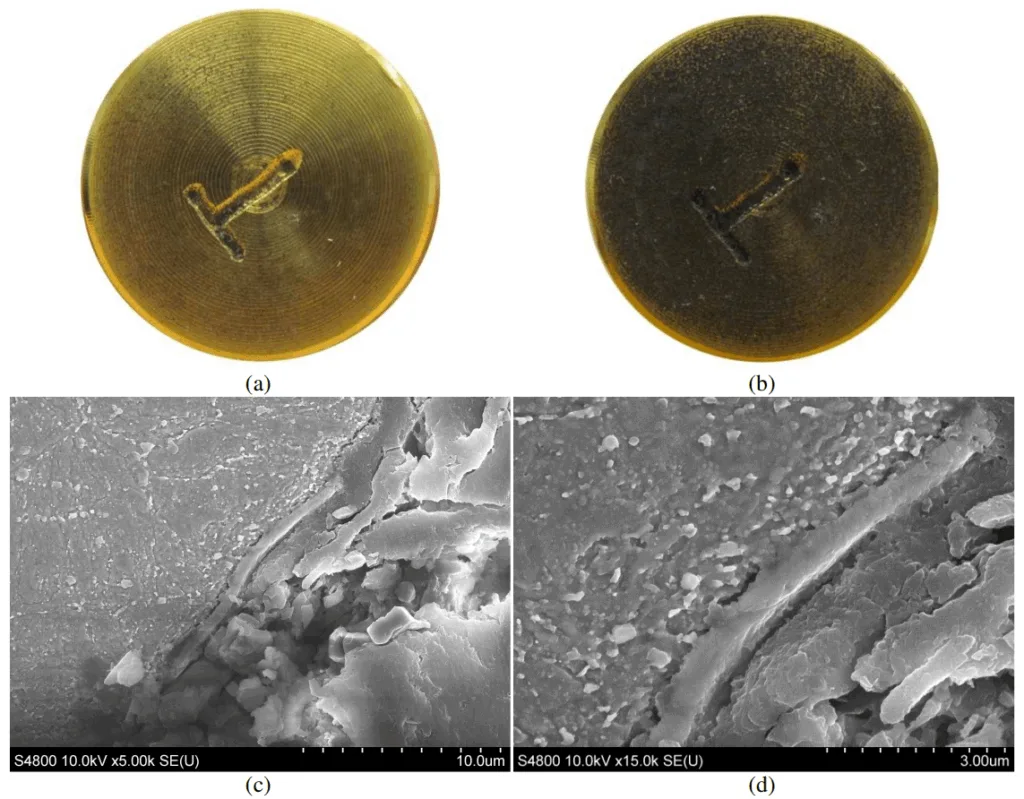
1. Overview:
- Title: The coating failure of coated core pin for die casting process
- Author: J. Song, T. DenOuden, Q. Han
- Year of publication: 2012
- Journal/academic society of publication: NADCA Transactions (T12-081)
- Keywords: die soldering, coating failure, mechanism, ultrasonic vibration
2. Abstract:
Soldering of core pins is one of the issues limiting the productivity of aluminum castings using high pressure die casting process. Ceramic coating is usually applied on the core pins to reduce die soldering. As a result, the coating lifetime governs the soldering process and the core pin lifetime. This study was designed to analyze the failure mechanisms of coatings on core pins under conditions similar to that of diecasting conditions. High intensity ultrasonic vibration was applied on the coated core pins to accelerate the experiments. The coated core pins were vibrated for certain times in water, oil salt bath, molten zinc, and molten A380 alloys at various temperatures. SEM and XRD were used to characterize coating failure of the tested core pins. Experimental results indicate that coating detachment from the steel matrix is the main failure mechanism of the coatings tested at low temperatures in water, oil, molten salt, and molten zinc. Coating failure accelerates as the temperature of the melt is increased. At high temperatures, coating fragmentation as well as detachment occurs on core pins tested in molten zinc and A380 alloy. The reactions between zinc or aluminum with steel at the coating failure locations cause coating fragmentation and accelerate coating failure at high temperatures.
3. Introduction:
High pressure die casting (HPDC) is a highly efficient method for manufacturing lightweight metal parts. Small die features like core pins, with a high surface to volume ratio, can heat up easily, leading to "soldering," where aluminum adheres to the die material (steel). Soldering increases costs due to expensive dies and production downtime, and it degrades product quality, especially pressure tightness [7].
Soldering is linked to the "washout" of the protective film on the die surface [1-2]. Without this film, molten alloy contacts the die, leading to iron dissolution into the melt and diffusion of melt elements into the die, forming an intermetallic layer [1, 2-11]. Previous research by Han et al indicated that die soldering results from a reaction between molten aluminum alloy and steel, forming liquid phases at reaction temperatures that act as a glue [5, 7, 9, 11-12]. Shankar and Apelian observed a pyramid-shaped intermediate phase layer where soldering begins [6, 8, 10]. Prior work by the authors [2, 12] proposed a five-step mechanism for soldering on coated core pins, starting with local coating failure, pit formation due to aluminum-steel reaction, pit growth leading to coating fragmentation and detachment, connection of neighboring pits, and finally, severe casting surface damage or core pin failure. The soldering process is thus determined by coating failure and the reaction between the steel matrix and molten material. However, it remains unclear how local coating failure occurs and how thermal fatigue and steel dissolution rate affect it.
4. Summary of the study:
Background of the research topic:
Soldering on core pins is a significant issue in high pressure die casting (HPDC) of aluminum alloys, limiting productivity and core pin lifetime. Ceramic coatings are applied to mitigate soldering, making coating lifetime a critical factor. Understanding the failure mechanisms of these coatings is essential for improving die casting operations.
Status of previous research:
Previous studies have established that soldering is related to the washout of protective films and the formation of intermetallic layers [1-11]. Han et al. identified the reaction between molten aluminum and steel as the cause of soldering [5, 7, 9, 11-12]. Shankar and Apelian described the morphology of initial soldering sites [6, 8, 10]. The authors' earlier work [2, 12] detailed a multi-step soldering mechanism on coated core pins, initiated by local coating failure. It was known that the soldering process is governed by coating failure and the steel-molten metal reaction.
Purpose of the study:
This study focused on understanding the coating failure of coated core pins as a result of 1) heating effect that causes microstructure evolution in the steel matrix, 2) temperature effect that may weaken the bond between the ceramic coating and the steel pin, and 3) the effect of chemical reaction between the molten material and the steel. Defects in the ceramic coating that are caused during the coating processes are not considered in this study. The life time of coated core pin was evaluated using a recently developed accelerated testing method [9].
Core study:
The research involved investigating the microstructure evolution of H-13 steel subjected to various heat treatments (270°C, 450°C, and 700°C). An accelerated testing method using high-intensity ultrasonic vibration was employed to evaluate the lifetime of TiN and Lumena coated H-13 core pins. These pins were tested in different media: water (room temperature), oil (270°C), molten salt (700°C), molten zinc (450°C and 700°C), and molten A380 aluminum alloy (700°C). The study analyzed coating failure mechanisms, dissolution rates of H-13 steel in molten metals, and the influence of temperature and chemical reactions. SEM and XRD were used for characterization.
5. Research Methodology
Research Design:
The study was designed to investigate H-13 steel microstructure changes due to thermal cycling and to evaluate coating failure mechanisms under simulated die casting conditions. This involved:
- Heat treatment of H-13 steel samples to study microstructure evolution at different temperatures.
- Accelerated testing of coated (TiN and Lumena) H-13 core pins using ultrasonic vibration in various liquid media at different temperatures to assess coating lifetime and failure modes.
- Measurement of H-13 steel dissolution rates in reactive molten metals (zinc and A380 alloy).
Data Collection and Analysis Methods:
- Microstructure Evolution of H-13 Steel: H-13 test bars were heat-treated at 270°C, 450°C, and 700°C for 20 hours and then water-quenched. Hardness was measured (HRC scale). Microstructures were examined using Scanning Electron Microscopy (SEM) with Energy Dispersive Spectroscopy (EDS). Phase diagrams (calculated using ThermoCalcTM and from ASM Handbook [13]) were used for analysis.
- Accelerated Coating Failure Tests: Coated core pins were subjected to high-intensity ultrasonic vibration while immersed in:
- Water (room temperature) and oil (270°C) for 15 minutes (TiN coating).
- Molten NaCl+KCl salt (700°C) for 120 seconds (TiN coating).
- Molten zinc (450°C and 700°C) and molten A380 alloy (700°C) with incremental exposure times (Lumena coating).
- Dissolution Rate Measurement: For tests in molten zinc and A380, test bars were removed at specific time increments, cleaned with NaOH solution, and weight changes were measured to calculate dissolution rates.
- Characterization: Coating failure and soldering morphology were examined using SEM with EDS. X-ray Diffraction (XRD) was used to identify intermetallic phases formed during reaction with molten zinc.
Research Topics and Scope:
- Microstructural evolution of H-13 tool steel at temperatures relevant to die casting (270°C, 450°C, 700°C) and its potential impact on coating adhesion due to phase transformations (e.g., austenite formation and subsequent martensitic transformation).
- The effect of temperature on the failure of TiN coatings in non-reactive media (water, oil, molten salt) to isolate thermal and mechanical effects.
- The combined effect of temperature and chemical reaction on the failure of Lumena coatings and the soldering of H-13 steel in molten zinc and molten A380 alloy.
- Determination of dissolution rates of H-13 steel in molten zinc and A380 alloy at different temperatures.
- Identification of failure mechanisms such as coating detachment, fragmentation, and the role of bonding strength.
6. Key Results:
Key Results:
- Microstructure Evolution of H-13 Steel:
- H-13 steel undergoes significant microstructure change at 700°C, with partial transformation to austenite, which then transforms to ferrite and carbides upon holding, or back to martensite on cooling. This transformation involves a ~4% volume change, potentially stressing the coating.
- Hardness of H-13 steel significantly decreased after heat treatment at 700°C (from ~45 HRC to 22.7 HRC), indicating substantial microstructural change. Little change was observed at 270°C and 450°C.
- Coating Performance in Non-Reactive Media (TiN coating):
- At low temperatures (room temperature water, 270°C oil), the TiN coating remained well-attached even after 15 minutes of ultrasonic vibration.
- At 700°C in molten salt, TiN coating showed partial failure after 60 seconds and near complete detachment after 2 minutes, indicating temperature significantly accelerates coating failure even without chemical reaction.
- Coating Performance in Reactive Media (Lumena coating):
- In molten zinc at 450°C, Lumena coating showed cracking and detachment after 20 seconds of ultrasonic vibration, but no significant soldering of the H-13 steel was observed. The dissolution rate of H-13 in zinc at 450°C was nearly zero.
- In molten zinc at 700°C, Lumena coating failed rapidly (spots after 5s, ~90% failure after 10s, complete failure by 15s). Severe reaction and soldering of H-13 steel occurred. The dissolution rate of H-13 in zinc at 700°C was high (1.395 mm/min). Intermetallic phases FeZn13 and Fe3Zn10 (dominant) were formed.
- The reaction layer thickness between H-13 and molten zinc at 700°C was ~10-20 microns, much thicker than with A380 alloy (<1.5 microns).
- The dissolution rate of H-13 in A380 alloy at 700°C was 0.585 mm/min.
- Failure Mechanisms:
- Coating detachment from the steel matrix is a main failure mechanism at low temperatures.
- At high temperatures, both coating fragmentation and detachment occur.
- Reactions between zinc/aluminum and steel at coating failure locations accelerate further coating fragmentation and failure.
- Coating failure can occur even if the H-13 matrix does not react with the molten material (e.g., 450°C zinc), suggesting that decreased bonding strength at higher temperatures contributes to failure.
- The combination of phase transformation stresses in H-13 and decreased coating-matrix bonding strength at high temperatures dramatically reduces coating lifetime.
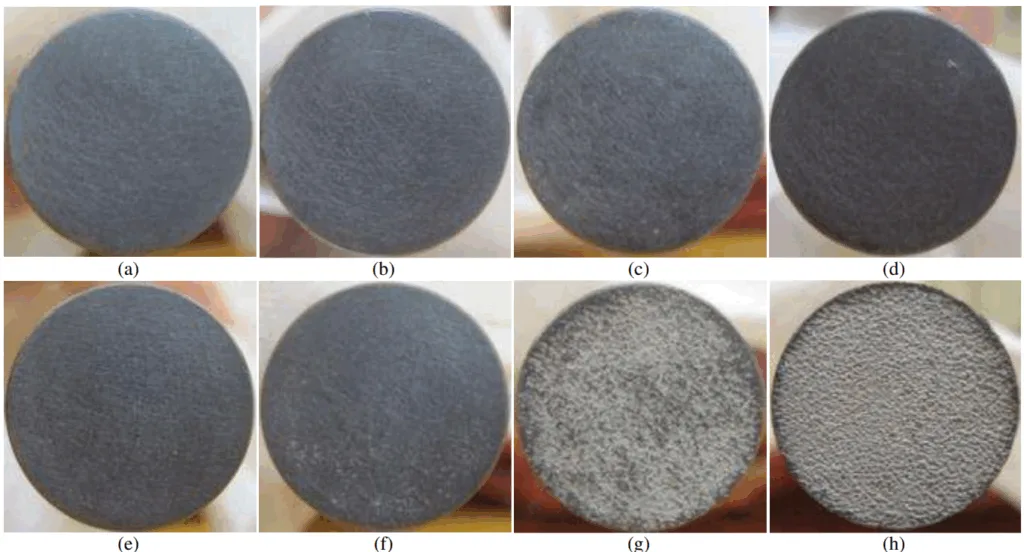
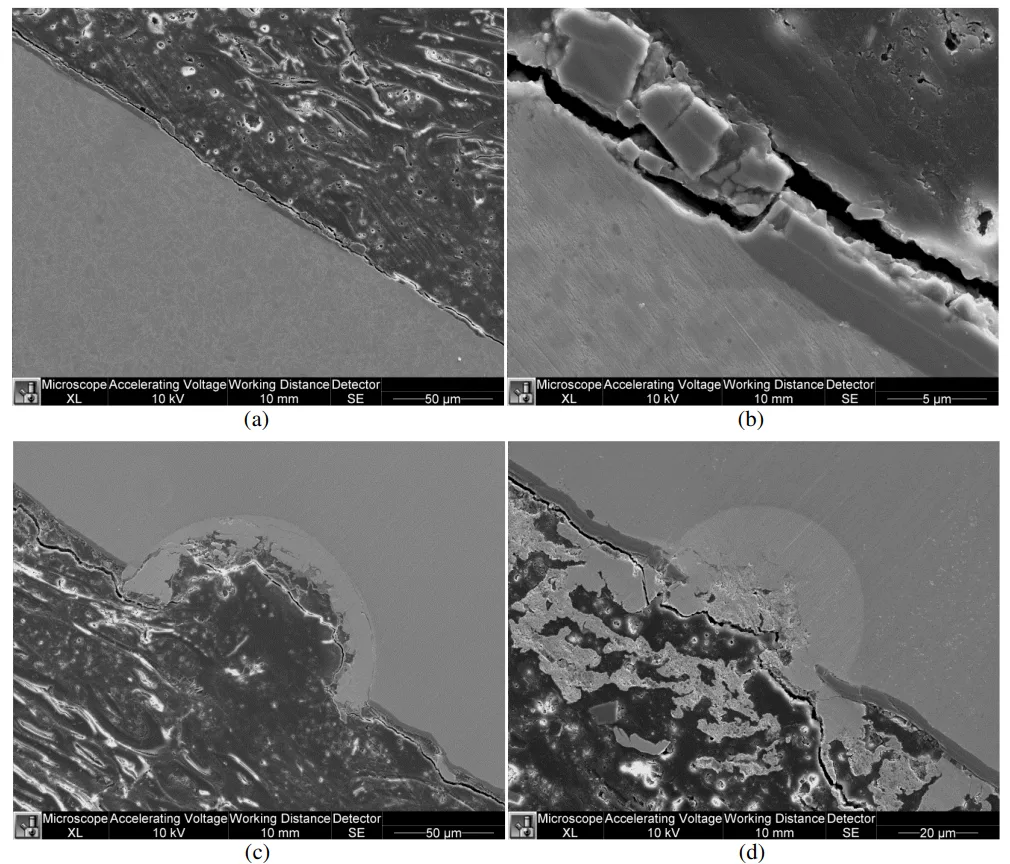
Figure Name List:
- Figure 1: The test bars used for accelerated soldering testing. The core pins with 128 mm long by 18mm in diameter were coated with a layer of Lumena (left), and TiN (right).
- Figure 2: Phase diagram (a) and Isothermal transformation diagram (b) of the H-13 tool steel.
- Figure 3: Microstructure of the H-13 bar at different heat treatment temperatures. a) room temperature with 1000X; b) 700 degree C with 1000X; c) room temperature; d) 270 degree C; e) 450 degree C and f) 700 degree C. c-f) are in 5000X
- Figure 4: The hardness data of the H-13 matrix at different heat treatment temperatures.
- Figure 5: Accelerated test results on H-13 at 270 degree C oil after 15 minutes tested (a) and at 700 degree C molten salt after 2 minutes ultrasonic vibration (b) with the TiN coating Coating; SEM morphologies at 700 degree C molten salt (c and d).
- Figure 6: Accelerated test results on H-13 in 450 degree C zinc molten (a-d) and in 700 degree C zinc molten (e-h) with the Lumena coating at a) and e) 0 seconds, b) and f) 5 seconds, c) and g) 10 seconds, and d) and h) 15 seconds;
- Figure 7: The XRD pattern of the H-13 bar under the ultrasonic vibration in 700 degree C zinc molten (a); the zinc iron phase diagram (b).
- Figure 8: SEM graphs of the H-13 bar under ultrasonic vibration with Lumena coating in zinc molten. (a-b) 450 degree C (20 seconds) and (c-d) 700 degree C (5 seconds).
- Figure 9: The dissolution depth verses ultrasonic vibration applied time of zinc and A380 molten alloy.
7. Conclusion:
Microstructural changes in the H-13 matrix at 700°C can lead to an additional 4% deformation, exceeding thermal expansion effects, which can stress the coating. The study demonstrated that coating failure occurred even at 450°C, where the H-13 matrix did not significantly change its microstructure nor react with molten materials. This suggests that a decrease in bonding strength between the coating and the matrix with increasing temperature is a critical factor in coating failure. At higher temperatures, the combined effects of stress from phase transformations in the steel and reduced bonding strength dramatically shorten the coating lifetime.
The dissolution rate of the H-13 steel, which reflects the soldering rate, is strongly temperature-dependent. For zinc alloy, the rate increased from nearly zero at 450°C to 1.395 mm/min at 700°C. This rate is governed by the reaction kinetics and the solubility of iron in the molten metal. The low solubility of iron in zinc at 450°C limits dissolution. The dissolution rate in molten zinc at 700°C was more than twice that in A380 alloy at the same temperature, indicating that soldering occurs more rapidly with zinc.
8. References:
- [1] Chu, Y., Cheng, P., Shivpuri, R., "A Study of Erosive Wear in Die Casting Dies: Surface Treatments and Coatings," NADCA Transactions 1993.
- [2] Song, J., DenOuden, T., and Han, Q., "Soldering analysis of core pin", NADCA Transactions 2011
- [3] Tentardini, E. K., Kunrath, A. O., Aguzzoli, C., Castro, M. J., Moore, J., Baumvol, I. J. R., Soldering mechanisms in materials and coatings for aluminum die casting, Surface & Coatings Technology, vol 202, No 16 (2008) .
- [4] Chen, Z. W., Jahedi, M. Z., Mechanisms of die failure caused by die/casting soldering during high pressure die casting of aluminium alloys, vol 20, No 6 (2001)
- [5] Han, Q., Viswanathan, S., Analysis of the mechanism of die soldering in aluminum die casting, Metallurgical and Materials Transactions a-Physical Metallurgy and Materials Science, vol 34, No 1 (2003).
- [6] Shankar, S., Apelian, D., Metallurgical and Material Die soldering: Mechanism of the interface reaction between molten aluminum alloy and tool steel, Transactions B-Process Metallurgy and Materials Processing Science, vol 33, No 3 (2002).
- [7] Han, Q., and Jian, X., "Ultrasound Assisted Die Casting Process," NADCA Transactions 2009,.
- [8] Shankar, S., Apelian, D., Die soldering: Effect of process parameters and alloy characteristics on soldering in the pressure die casting process, International Journal of Cast Metals Research, vol 15, No 2 (2002).
- [9] Han, Q., Xu, H., Ried, P. P., Olson, P., Accelerated method for testing soldering tendency of core pins, International Journal of Cast Metals Research, vol 23, No 5 (2010)
- [10] Shankar, S., Apelian, D., Mechanism and preventive measures for die soldering during Al casting in a ferrous mold, Jom-Journal of the Minerals Metals & Materials Society, vol 54, No 8 (2002)
- [11] Han, Q., Kenik, E. A., Viswanathan, S., "Die soldering in aluminum die casting", Light Metals: Proceedings of Sessions, TMS Annual Meeting, pp 765-770, (2000)
- [12] Song, J., DenOuden, T., and Han, Q., “Mechanisms of soldering formation on coated core pin", Materials and metallurgical transactions A. vol 43 pp415-421 (2012)
9. Copyright:
- This material is a paper by "J. Song, T. DenOuden, Q. Han". Based on "The coating failure of coated core pin for die casting process".
- Source of the paper: DOI not available in the provided document.
This material is summarized based on the above paper, and unauthorized use for commercial purposes is prohibited.
Copyright © 2025 CASTMAN. All rights reserved.