This article introduces the paper "Strength Analysis of Aluminum Alloy Window Wiper Manufactured by Die Casting," published in the Journal of the Korean Society of Manufacturing Technology Engineers in 2016. This study investigates the feasibility of using aluminum alloy and die casting to produce lightweight and high-strength window wipers for automobiles, addressing the growing need for vehicle weight reduction due to environmental regulations and fuel efficiency demands.
1. Overview:
- Title: Strength Analysis of Aluminum Alloy Window Wiper Manufactured by Die Casting
- Authors: Seunghyun Cho, Jeungho Lee, Hangoo Kim
- Publication Year: 2016
- Publishing Journal/Academic Society: Journal of the Korean Society of Manufacturing Technology Engineers
- Keywords: Window wiper, Al alloy, Strength, Die-casting, FEA
2. Research Background:
- Social/Academic Context of the Research Topic:
The automotive industry has been facing increasing pressure to reduce vehicle weight due to the trend of vehicle specification upgrades since the 1990s, which has led to an average weight increase of 15 kg per year. Simultaneously, stringent environmental regulations aimed at reducing exhaust emissions necessitate vehicle lightweighting as an unavoidable trend. Research efforts to reduce vehicle weight are continuously being conducted through various approaches, including:- Application of lightweight composite materials [1-3]
- Use of non-ferrous alloys [4-6]
- Changes in manufacturing methods [7, 8]
These efforts are consistently being pursued [9-12]. Recently, the application of aluminum (Al) for weight reduction in automotive parts, including chassis components, has been actively researched.
- Limitations of Existing Research:
Conventional steel window wipers, while strong, contribute to vehicle weight. The limitations of steel window wipers are primarily related to their density and the multi-step manufacturing processes involved. Traditional steel window wipers are typically composed of three parts – hook rod, retainer, and arm head – and are manufactured through multiple processes such as bending, welding, and pressing. - Necessity of the Research:
To address the limitations of traditional steel window wipers and contribute to vehicle lightweighting, this research explores the application of Al-Mg alloy, which has been developed for automotive parts [13]. The study focuses on analyzing the strength of a window wiper designed for die casting using this Al alloy, aiming to achieve weight reduction and simplify the manufacturing process while maintaining or improving strength compared to steel wipers. The research aims to demonstrate the potential of Al alloys as a wrought alloy alternative for various automotive body applications to facilitate vehicle lightweighting.
3. Research Purpose and Research Questions:
- Research Purpose:
The primary purpose of this research is to analyze the strength of an aluminum alloy window wiper manufactured using the die-casting method. This analysis is conducted using Finite Element Analysis (FEA) based on KS standards for window wiper strength evaluation. The study aims to demonstrate the feasibility of replacing conventional steel window wipers with lighter and more cost-effective aluminum alloy wipers produced through die casting. - Key Research Questions:
- Can an aluminum alloy window wiper, designed and manufactured using die casting, achieve a strength level comparable to or greater than that of a conventional steel window wiper?
- What is the degree of weight reduction achievable by replacing steel with aluminum alloy in window wiper manufacturing?
- How does the die-casting manufacturing process affect the design and strength of the aluminum alloy window wiper?
- Can the use of aluminum alloy and die casting simplify the manufacturing process and improve cost competitiveness compared to traditional steel window wiper manufacturing?
- Research Hypotheses:
- It is hypothesized that an optimized aluminum alloy window wiper design, specifically tailored for die casting, can achieve a strength level exceeding that of a conventional steel window wiper.
- It is also hypothesized that the use of aluminum alloy and die casting will result in a significant weight reduction compared to steel window wipers, contributing to overall vehicle lightweighting and improved fuel efficiency.
- Furthermore, it is hypothesized that the die-casting process will simplify the manufacturing process and enhance the cost-effectiveness of window wiper production.
4. Research Methodology
- Research Design:
This research employs a comparative study approach using Finite Element Analysis (FEA). The strength of window wipers made of both steel and aluminum alloy are analyzed and compared under identical loading conditions based on Korean Industrial Standards (KS). The design of the aluminum alloy window wiper is iteratively modified over four design stages to optimize its strength while considering the constraints of the die-casting process. - Data Collection Method:
Data for the research is collected through computer simulations using FEA software, MSC/Marc 2013 [14]. Material properties for steel and aluminum alloy, as specified in Table 1 of the paper, are used as input parameters for the simulations. The loading conditions are defined based on KS standards (KS R 3012:2007 and KS R 3015: 2007) for window wiper performance testing. - Analysis Method:
The primary analysis method is Finite Element Analysis (FEA). The FEA simulations are used to calculate the displacement of the window wipers under pressure, which is a key indicator of strength according to KS standards. The deformation test method under pressure, as depicted in Fig. 2, and the boundary conditions for FEA, as shown in Fig. 3, are directly based on KS standards. The displacement results for different designs and materials are compared to evaluate the strength and performance of the aluminum alloy window wiper relative to the conventional steel wiper. - Research Subjects and Scope:
The research focuses on window wipers designed for heavy-duty trucks, specifically the Trago model of H company. The materials considered are steel (conventional material) and a newly developed Al-Mg-Al₂Ca alloy suitable for die casting. The scope of the research includes:- Strength analysis of conventional steel window wipers.
- Strength analysis of initial aluminum alloy window wiper designs based on direct material substitution.
- Iterative design modifications of the aluminum alloy window wiper to optimize strength for die casting manufacturing.
- Comparison of weight and strength performance between steel and optimized aluminum alloy window wipers.
- Consideration of die-casting process constraints in the design optimization process.
5. Main Research Results:
- Key Research Results:
The key finding of this research is that the final optimized aluminum alloy window wiper design, achieved through four design iterations considering the die-casting process, demonstrated a significant improvement in strength and weight reduction compared to the conventional steel window wiper. According to the FEA results:- The strength of the final aluminum alloy window wiper improved by 55% over that of the steel window wiper. This is indicated by a reduction in displacement under the same pressure.
- The weight of the aluminum alloy window wiper was approximately 45% less than the steel window wiper.
- Statistical/Qualitative Analysis Results:
- Displacement Analysis: Fig. 5 shows the displacement to the normal direction of a conventional steel and aluminum alloy window wiper under 114.94 kPa pressure. The steel wiper exhibits a displacement of 1.51 mm, while the initial aluminum alloy wiper shows a significantly larger displacement of 4.48 mm, indicating lower strength.
- Fig. 6 compares the displacement of conventional steel and aluminum alloy models under varying pressures (76.63 kPa, 114.94 kPa, 143.68 kPa). Across all pressure levels, the aluminum alloy model shows considerably higher displacement than the steel model.
- Fig. 7, Fig. 8, Fig. 9, and Fig. 10 illustrate the displacement results for the first, second, third, and fourth design iterations of the aluminum alloy window wiper, respectively. Each design modification progressively reduces the displacement, indicating improved strength.
- Fig. 11 shows the displacement distribution of the final optimized aluminum alloy window wiper under 114.94 kPa pressure, with a significantly reduced displacement of 0.836 mm.
- Weight Reduction: The weight of the steel window wiper was calculated to be 0.219 kg, while the final aluminum alloy window wiper design achieved a weight of 0.159 kg, representing approximately a 45% reduction.
- Data Interpretation:
The FEA results clearly demonstrate that by iteratively modifying the design of the window wiper to accommodate the die-casting process and enhance strength, an aluminum alloy window wiper can be developed that surpasses the strength of a conventional steel wiper while achieving substantial weight reduction. The initial direct substitution of aluminum alloy in the original steel design resulted in significantly lower strength. However, through design optimization focusing on increasing thickness in critical areas, unifying parts for die casting, and adding reinforcing features like ribs and fillets, the strength was progressively improved. The final design successfully achieved both strength enhancement and weight reduction. - Figure Name List:
- Fig. 1 Structure of window wiper
- Fig. 2 Deformation test under pressure of KS standard (KS R 3012:2007)
- Fig. 3 Boundary conditions for FEA
- Fig. 4 Stress-strain property of Al alloy
- Fig. 5 Displacement to the normal direction of a conventional steel window wiper under pressure of 114.94 kPa
- Fig. 6 Displacement to the normal direction of a conventional window wiper model under pressure
- Fig. 7 1st design changed for Al alloy window wiper considering die-casting process
- Fig. 8 2nd. design changed for Al alloy window wiper considering die-casting process
- Fig. 9 3rd design changed for Al alloy window wiper considering assembly process
- Fig. 10 4th. design changed for Al alloy window wiper
- Fig. 11 Displacement to the normal direction of a final optimized Al alloy window wiper under pressure of 114.94 KPa
- Fig. 12 Rapid prototype manufacturing and interference test for heavy truck
- Fig. 13 Pilot product manufacturing
- Fig. 14 Benefits of die-casting process for a window wiper
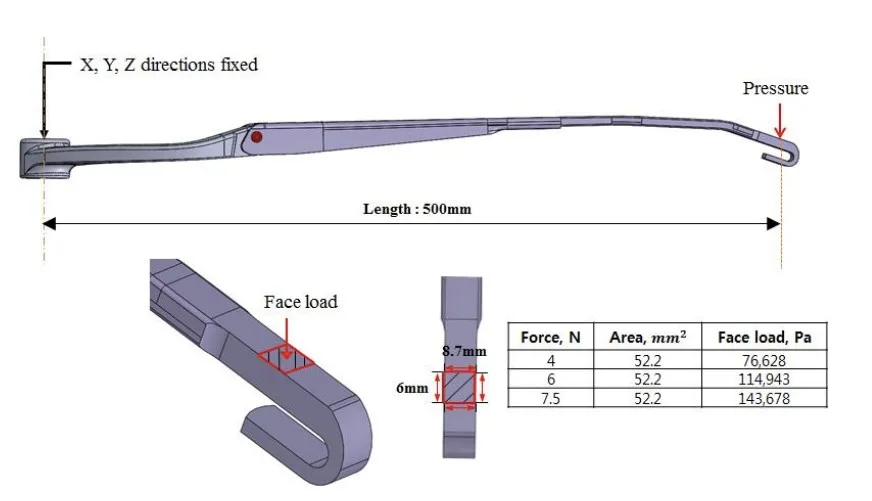
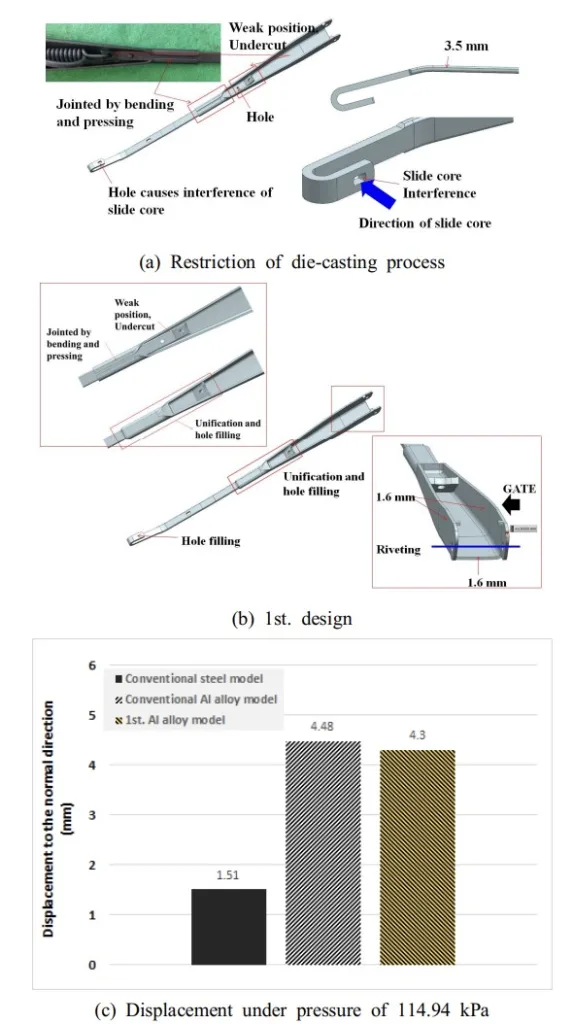
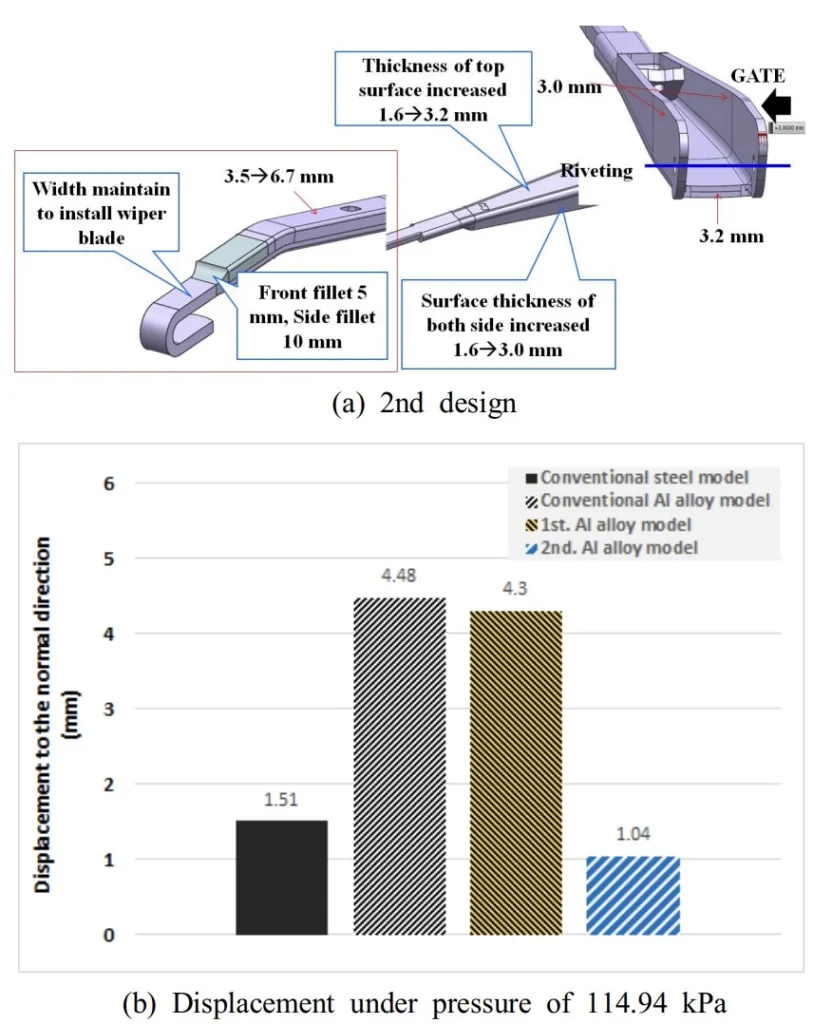
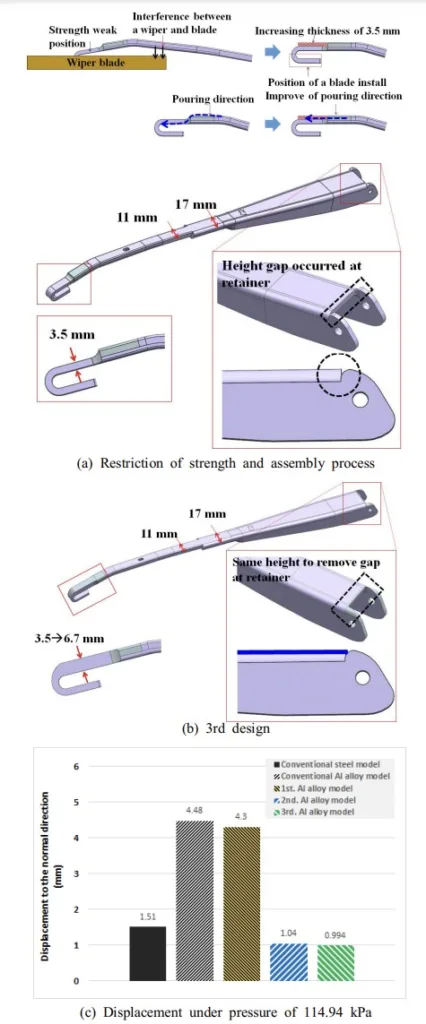
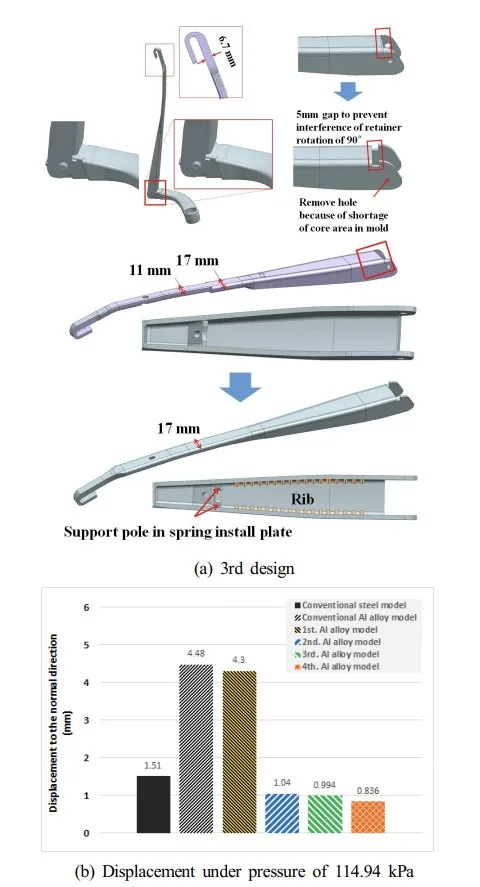
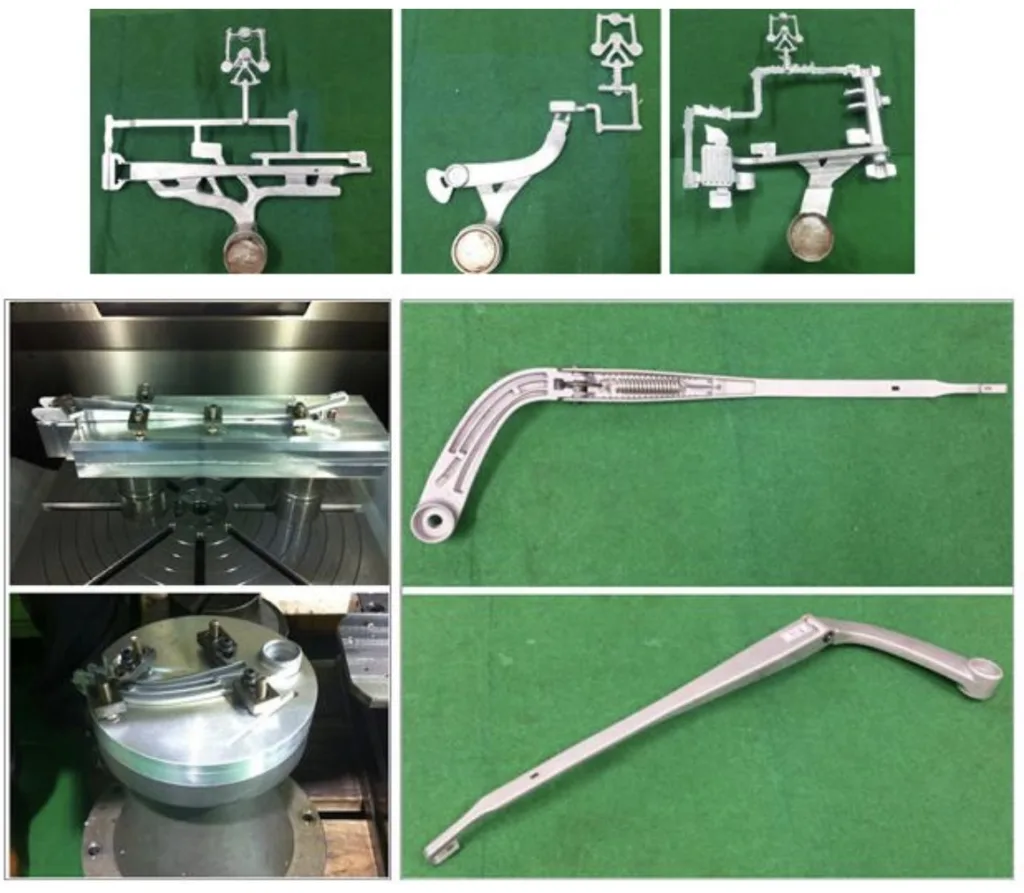
6. Conclusion and Discussion:
- Summary of Main Results:
This study successfully demonstrated the feasibility of developing a high-strength, lightweight window wiper using aluminum alloy and die-casting technology. Through iterative FEA-driven design optimization, the final aluminum alloy window wiper design achieved a 55% improvement in strength and a 45% reduction in weight compared to a conventional steel window wiper. The optimized design is specifically tailored for die-casting manufacturing, enabling a simplified and potentially more cost-effective production process. - Academic Significance of the Research:
This research contributes to the body of knowledge in lightweight automotive component design and manufacturing. It highlights the potential of aluminum alloys and die casting as viable alternatives to traditional materials and manufacturing methods for structural automotive parts. The detailed design optimization process presented in the paper provides a valuable case study for engineers seeking to apply die casting and aluminum alloys in similar applications. The study also underscores the importance of considering manufacturing process constraints during the design phase to achieve optimal performance. - Practical Implications:
The successful development of a lightweight aluminum alloy window wiper through die casting has several significant practical implications for the automotive industry:- Improved Cost Competitiveness: Die casting offers the potential for simplified manufacturing processes and reduced material waste, leading to improved cost competitiveness compared to the multi-step processes involved in steel window wiper production.
- Simplified Manufacturing Process: Die casting allows for the integration of multiple parts into a single component, simplifying assembly and reducing the number of manufacturing steps.
- Module Downsizing for Driving Motor Capacity: The significant weight reduction achieved with the aluminum alloy wiper allows for the possibility of downsizing the driving motor capacity required for window wiper operation, further contributing to vehicle weight and energy efficiency improvements.
- Contribution to Vehicle Lightweighting and Fuel Efficiency: The 45% weight reduction in the window wiper component directly contributes to overall vehicle lightweighting, which is crucial for meeting increasingly stringent fuel efficiency and emission regulations.
- Limitations of the Research:
The primary limitation of this research is that the strength analysis is based solely on FEA simulations. While FEA provides valuable insights into structural performance, it is essential to validate these findings through physical testing and real-world performance evaluations. Factors such as long-term durability, fatigue performance, and corrosion resistance of the aluminum alloy window wiper in actual operating conditions were not directly assessed in this study and require further investigation.
7. Future Follow-up Research:
- Directions for Follow-up Research:
Future research should focus on validating the FEA results through experimental testing and real-world vehicle evaluations. This includes:- Physical Prototype Testing: Manufacturing physical prototypes of the optimized aluminum alloy window wiper design and conducting laboratory tests to measure its strength, durability, and fatigue performance.
- Real Vehicle Testing: Integrating the aluminum alloy window wiper into vehicles and conducting field tests under various operating conditions to assess its performance and durability in real-world scenarios.
- Durability and Corrosion Resistance Assessment: Conducting long-term durability and corrosion resistance tests to ensure the long-term reliability of the aluminum alloy window wiper in automotive environments.
- Areas Requiring Further Exploration:
Further research could also explore:- Optimization of Al Alloy Composition: Investigating different aluminum alloy compositions to further optimize the strength-to-weight ratio and cost-effectiveness of the die-cast window wiper.
- Die Casting Process Parameter Optimization: Optimizing die casting process parameters to enhance the mechanical properties and surface finish of the aluminum alloy window wiper, potentially further improving its performance and reducing manufacturing costs.
- Cost Analysis: Conducting a detailed cost analysis to compare the overall manufacturing cost of aluminum alloy die-cast window wipers with traditional steel window wipers, considering material costs, manufacturing process costs, and potential long-term benefits.
8. References:
[1] Jin, S. W., Park, D. H., Lee, G. S., Kim, C. W., 2013, Material Optimization of BIW for Minimizing Weight, The Korean Society of Automotive Engineers, 21:4 16-22.
[2] Park, K. S., Kong, C. D., Park, H. B., 2015, Structural Design of Light Weight Natural Fiber Composites for Next Generation Automobile Bonnet, Composites Research, 28:2 46-51.
[3] Kim, K. S., KBae, K. M., Oh, S. Y., Seo, M. K., Kang, C. K., Park, S. J., 2012, Trend of Carbon Fiber-reinforced Composites for Lightweight Vehicles, Elastomers and Composites, 47:1 65-75.
[4] Kim, G. J., Lim, J. H., Park, J. H., Choi, B. I., Lee, J. W., Kim, Y. J., 2012, Light-weight Design of Automotive AA6061 Rear Sub-frame Based on CAE Simulation, The Korean Society of Automotive Engineers, 20:3 77-82.
[5] Park, S. C., Shin, K. S., 1996, Mg Alloys for Weight Reduction of Automobiles, Bulletin of the Korean Inst. of Met & Mat, 9:2 160-171.
[6] Sanji, K., 1995, Automobile Weight Reduction and Quality Improvement of Al-Alloy Castings, Journal of Korea Foundry Society, 15:2 127-137.
[7] So, S. W., Whang, H. T., Lee, J. -H., Choi, H. W., 2011, Development of Automotive Lower Arm using Hybrid Manufacturing Process, KSMTE, 20:2 214-218.
[8] Kim, E. S., 2012, A Study of Optimal Design for Mg Armrest Frame by using Response Surface Method, KSMTE, 20:5 797-804.
[9] Choi, B. S., Lee, D. Y., Jin, C. K., 2013, Study of Plastic Deformation of Steel Wire for Weight Reduction of Automotive Weather Strip, The Korean Society of Automotive Engineers, 21:5 82-86.
[10] Park, J. H., Kim, K. J., Yoon, J. G., 2013, Light-weight Design of Automotive Spring Link Based on Computer Aided Engineering, The Korean Society of Automotive Engineers, 21:5 157-161.
[11] Kim, Y. S., Kim., I. K., Tark, J. H., Kim, D. S., 1999, A Study of Light Weight of Tie Rod End in Auto Supplies, The Korean Society for Power System Engineering, 3:3 70-75.
[12] Cho, J. G., Koo, J. S., Jun, H. S., 2013, A Weight-reduction Design Method by Underframe Material Substitution in a Box-type Bodyshell with Cut-outs, The Korean Society of Automotive Engineers, 21:2 45-54.,
[13] Ha, S. H., Yoon, Y. O., Kim, S. K., 2014, Effect of Al2Ca on Oxidation Resistance and Tensile Property of Al-5Mg Alloy, Journal of Korea Foundry Society, 34:6 194-199.
[14] MSC/MARC, 2013, MSC/MARC User's Manual Volume A, MSC Software Corporation.
9. Copyright:
- This material is Seunghyun Cho, Jeungho Lee, Hangoo Kim's paper: Based on Strength Analysis of Aluminum Alloy Window Wiper Manufactured by Die Casting.
- Paper Source: http://dx.doi.org/10.7735/ksmte.2016.25.3.204
This material was summarized based on the above paper, and unauthorized use for commercial purposes is prohibited.
Copyright © 2025 CASTMAN. All rights reserved.