How Smoothed Particle Hydrodynamics (SPH) Delivers Unprecedented Accuracy in Predicting HPDC Filling and Defects
This technical brief is based on the academic paper "Simulation of casting complex shaped objects using SPH" by P.W. Cleary, J. Ha, M. Prakash, and T. Nguyen, published in the proceedings of the Shape Casting: The John Campbell Symposium by TMS (The Minerals, Metals, & Materials Society) (2005). It is summarized and analyzed for HPDC professionals by the experts at CASTMAN.
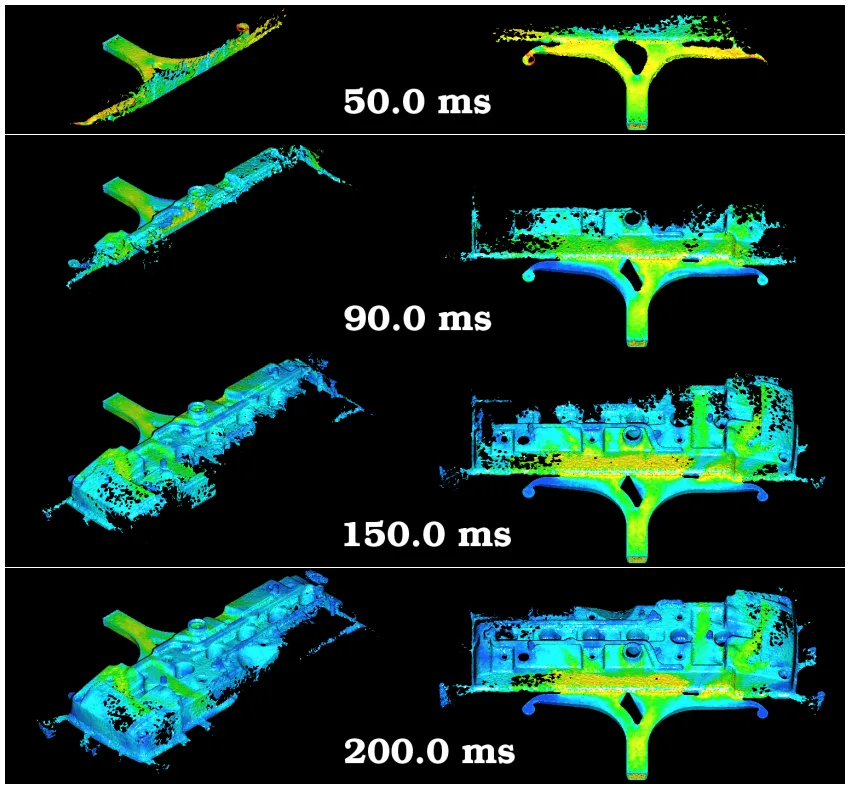
Keywords
- Primary Keyword: SPH Simulation for HPDC
- Secondary Keywords: High-Pressure Die Casting, Smoothed Particle Hydrodynamics, casting simulation, die filling analysis, porosity prediction, complex shaped castings, short shot validation
Executive Summary
- The Challenge: The high speeds and geometric complexity of High-Pressure Die Casting (HPDC) create chaotic, fragmented fluid flow that is notoriously difficult to model accurately, leading to unpredictable defects like porosity.
- The Method: Researchers applied a grid-free, Lagrangian simulation technique called Smoothed Particle Hydrodynamics (SPH), which approximates the liquid metal as a collection of moving particles, to model the die filling process.
- The Key Breakthrough: SPH simulations provided unprecedented detail of the fluid's free surface, including fragmentation, splashing, and void formation. The models accurately predicted the final fill locations, which correlate strongly with porosity, and were validated against physical short-shot experiments.
- The Bottom Line: The study demonstrates that SPH is a powerful, accurate, and practical tool for simulating large-scale, complex automotive castings, enabling engineers to optimize die and gating design to improve final product quality.
The Challenge: Why This Research Matters for HPDC Professionals
In the world of HPDC, producing high-volume, low-cost components for industries like automotive and electronics is paramount. However, the very nature of the process—injecting liquid metal at speeds up to 100 m/s into intricate dies—creates a significant engineering challenge. This process results in strongly three-dimensional fluid flow with significant free surface fragmentation and splashing.
For engineers, the order in which the die fills and the effectiveness of air vents are critical for creating homogeneous parts with minimal entrapped voids. Poor control over die filling leads to porosity, cold shuts, and other defects that compromise part integrity and increase scrap rates. Traditional simulation methods can struggle to capture the complex, splashing free-surface flows found in HPDC. This research addresses the need for a more robust and accurate simulation technique to tackle these fundamental challenges.
The Approach: Unpacking the Methodology
To overcome the limitations of traditional grid-based methods, the researchers employed Smoothed Particle Hydrodynamics (SPH). As described in the paper, SPH is a Lagrangian, grid-free method that is exceptionally well-suited for modeling complex, splashing flows.
Instead of using a fixed mesh, SPH approximates the material (e.g., liquid aluminum) with a collection of particles. These particles are moving interpolation points that carry physical properties like mass, velocity, and temperature. The interactions between particles are calculated in a way that ensures their collective motion is consistent with the Navier-Stokes equations that govern real fluid flow. This particle-based approach allows the simulation to naturally and easily model complex behaviors like surface fragmentation, splashing, and the merging of fluid fronts without the numerical difficulties faced by grid-based techniques.
The Breakthrough: Key Findings & Data
The study presented SPH simulations of four different industrial components, showcasing the method's capability and accuracy across a range of complexities and scales.
- Finding 1: Detailed Flow in Large Automotive Parts: The simulation of a large engine rocker cover (Figure 1) revealed how the complex die contours and gate design led to preferential "race tracking" of fluid around the perimeter, creating large, long-lived voids in the center. This level of detail in predicting void formation is critical for optimizing gate and runner design.
- Finding 2: Capturing Jet Fragmentation and Merging: In the simulation of an automotive differential cover (Figure 2), the SPH method clearly showed the initial jets of aluminum fragmenting, moving along the part's contours, and eventually merging. The simulation accurately predicted the back-filling pattern and identified the central void region as the last area to be filled, a prime location for entrapped air.
- Finding 3: Predicting Porosity from Flow Behavior: For an electronic housing (Figure 3), the simulation showed how the Y-shaped runner led to an uneven fill. The model predicted the formation of large, long-lived voids that were the last regions to fill, correctly identifying areas that could be expected to have elevated levels of porosity.
- Finding 4: Thermal and Flow Coupling Validation: The simulation of a thin coaster (Figure 5) included coupled heat transfer and solidification. The model showed how the metal cooled and became more viscous as it contacted the die walls, impacting the fill pattern. A comparison of a simulated short shot with an experimental one (Figure 6) showed very good agreement, validating the model's ability to predict flow restriction due to solidification, a key factor in preventing cold shuts.
Practical Implications for Your HPDC Operations
The results of this paper are not just academic; they have direct, practical applications for improving real-world manufacturing outcomes.
- For Process Engineers: The detailed flow patterns, such as those seen in the rocker cover simulation (Figure 1), provide a clear visual guide to how gating and process parameters influence the fill. This research suggests that using SPH simulations can help optimize shot profiles and gate designs to ensure a more uniform fill and minimize void formation.
- For Quality Control: The strong correlation between the last locations to fill in the simulations and known porosity issues in manufactured parts provides a powerful predictive tool. By analyzing SPH results, QC teams can anticipate high-risk areas for defects before the first tool is even cut.
- For Die Design: This study provides compelling evidence that SPH is an effective tool for evaluating the performance of different gate and runner systems. As shown in the door lock plate example (Figure 4), the simulation can identify hard-to-fill regions and potential weld lines, allowing designers to modify the die to improve metal flow and prevent defects. The short shot validation (Figure 6) proves the model's reliability for this purpose.
Paper Details
Simulation of casting complex shaped objects using SPH
1. Overview:
- Title: Simulation of casting complex shaped objects using SPH
- Author: P.W. Cleary, J. Ha, M. Prakash, T. Nguyen
- Year of publication: 2005
- Journal/academic society of publication: Shape Casting: The John Campbell Symposium, TMS (The Minerals, Metals, & Materials Society)
- Keywords: SPH, high pressure die casting
2. Abstract:
The geometric complexity and high fluid speeds involved in High Pressure Die Casting (HPDC) combine to give strongly three dimensional fluid flow with significant free surface fragmentation and splashing. A Lagrangian simulation technique that is particularly well suited to modelling HPDC is Smoothed Particle Hydrodynamics (SPH). Materials are approximated by particles that are free to move around rather than by fixed grids, enabling the accurate prediction of fluid flows involving complex free surface motion. Four examples of SPH simulated HPDC flows are presented, ranging from zinc casting of a door lock plate to aluminium casting of a full engine rocker cover. These show unprecedented detail in the fluid free surfaces, particularly in the extent of fragmentation and void formation. SPH has other attractive features for the prediction of casting, including easy prediction of shrinkage, feeding, some forms of porosity generation and surface oxide formation. Flow predictions coupled to heat transfer and solidification are validated using short shots. The bulk features of the final solid castings are in good agreement with the predictions. These results combine to demonstrate that SPH modelling of HPDC has now reached a level where both isothermal and thermal simulations can be performed in reasonable computation times for large scale automotive castings and provide a good degree of predictive accuracy.
3. Introduction:
HPDC is a critical manufacturing process for high-volume components in the automotive, household, and electronics industries. The process involves injecting liquid metal at very high speeds (30-100 m/s) into a die. The complexity of the dies leads to highly three-dimensional flow with significant splashing and surface fragmentation. The filling sequence and air vent positioning are crucial for producing homogeneous parts with minimal voids. Numerical simulation is a powerful and cost-effective tool for studying and optimizing die design and filling processes to improve product quality and productivity.
4. Summary of the study:
Background of the research topic:
Modeling HPDC flows is challenging due to the complex, high-speed, and fragmented nature of the free surface. A simulation technique that can handle these phenomena effectively is needed.
Status of previous research:
Smoothed Particle Hydrodynamics (SPH) was developed for astrophysical applications and later extended to incompressible flows, heat conduction, and convection. Its application to HPDC has been a subject of ongoing development and validation, with previous work demonstrating good agreement with water analogue experiments.
Purpose of the study:
This paper aims to demonstrate the use of 3D SPH to predict the filling of four different industrial components. It seeks to examine the accuracy of SPH solutions by comparing them to short shot experiments and to show that SPH modeling is now a mature technique for large-scale industrial castings.
Core study:
The paper presents SPH simulations for four industrial parts:
1. An aluminum engine rocker cover (large, complex geometry).
2. An aluminum automotive differential cover (demonstrating jet merging).
3. An aluminum electronic housing (showing asymmetric filling and void formation).
4. Zinc door lock plates (a very high-speed, thin-gated casting).
Additionally, a thermal simulation of a coaster is presented and validated against a physical short shot experiment.
5. Research Methodology
Research Design:
The study utilized the Smoothed Particle Hydrodynamics (SPH) method to simulate the die filling process for several industrial components. SPH is a particle-based, grid-free Lagrangian method. The simulations were designed to capture the complex free-surface flow, fragmentation, and void formation inherent in HPDC. For one case (the coaster), a full coupled thermal and flow simulation was performed, including heat conduction into the solid die.
Data Collection and Analysis Methods:
The primary data was generated by the SPH simulations, which solve the SPH continuity and momentum equations for millions of particles. The output is a time-series visualization of the particle positions, colored by variables like speed or temperature. The accuracy of the thermal simulation was validated by comparing a simulated "short shot" (a partially filled casting) with a physical short shot experiment of an aluminum coaster.
Research Topics and Scope:
The research covers the application of SPH to simulate the isothermal filling of four complex industrial HPDC parts made of aluminum and zinc. It also explores a fully coupled thermal-flow simulation to model solidification. The scope ranges from small, thin zinc parts requiring over 2 million particles to large automotive castings like an engine rocker cover.
6. Key Results:
Key Results:
The SPH simulations successfully predicted the complex filling patterns for all four industrial components. The models showed unprecedented detail in free surface fragmentation and the formation of large, persistent voids. The locations identified as the last to fill in the simulations correlated well with known areas of porosity in the actual manufactured parts. The thermal simulation of the coaster, when compared to an experimental short shot, demonstrated very good agreement, validating the model's ability to predict flow behavior influenced by cooling and solidification. The study concludes that SPH has reached a level of maturity where it can provide a good degree of predictive accuracy for large-scale automotive castings.
Figure Name List:
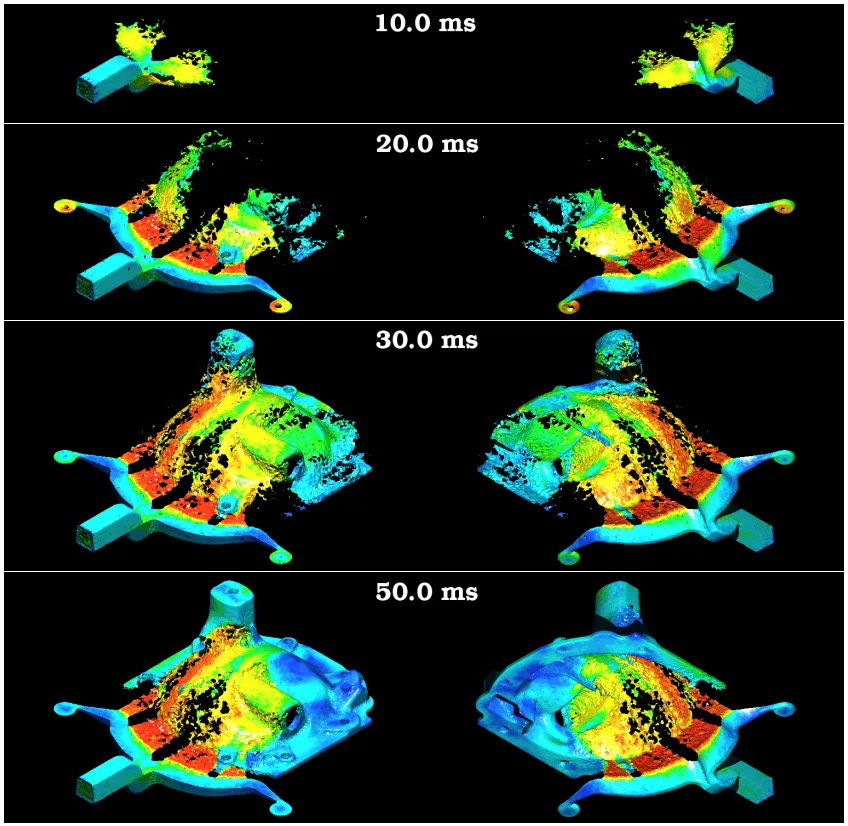
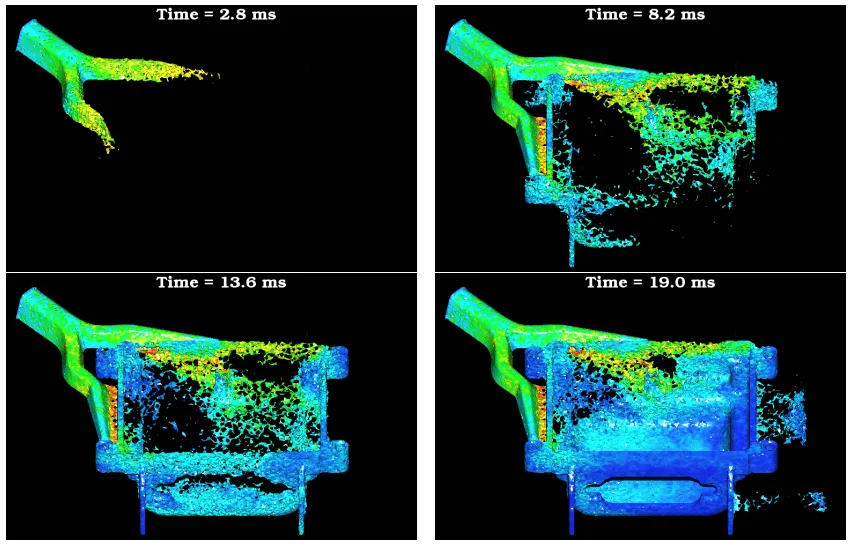
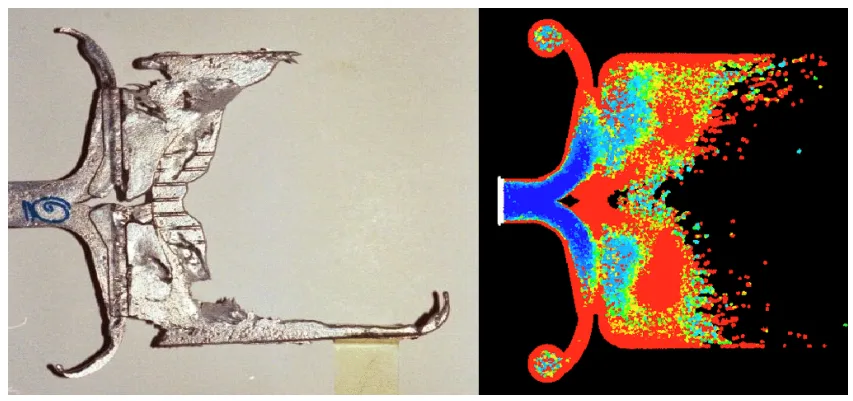
- Figure 1: Filling of an engine rocker cover with fluid coloured by speed.
- Figure 2: Filling of differential cover with the fluid coloured by speed.
- Figure 3: An electronic housing filled from a Y shaped runner (coloured by speed).
- Figure 4: Filling by zinc of the front and back plates of a door lock (coloured by speed).
- Figure 5: Filling of coaster with fluid coloured by temperature.
- Figure 6: Short shot: experiment (left), simulation (right).
7. Conclusion:
The filling of several industrial components, from a zinc door lock to a full aluminum engine rocker cover, was simulated using SPH. The predictions show high detail, and the last locations to fill correlate well with porosity/voidage observations from manufacturers. As part of the validation, SPH simulations of short shots for a simple coaster highlighted the ability to predict complexities like cold shuts caused by heat transfer and solidification. The paper concludes that SPH is a mature and accurate predictive tool for HPDC.
8. References:
- [1] Monaghan, J.J., “Smoothed particle hydrodynamics", Annual Review of Astronomy and Astrophysics., 30, (1992), 543-574.
- [2] Monaghan, J.J., “Simulating free surface flows with SPH", J. Computational Physics., 110, (1994), 399-406.
- [3] Cleary, P.W. & Monaghan, J.J., “Conduction modelling using smoothed particle hydrodynamics", J. Comp. Phys., 148, (1999), 227-264.
- [4] Cleary, P.W.,“Modelling confined multi-material heat and mass flows using SPH", Applied Mathematical Modelling, 22, (1998), 981-993.
- [5] Cleary, P.W., Ha, J., Prakash, M. and Nguyen, T., “3D SPH Flow Predictions and Validation for High Pressure Die Casting of Automotive Components", to appear: App Math. Modelling, (2004).
- [6] Cleary, P.W., Ha, J., and Ahuja, V., “High pressure die casting simulation using smoothed particle hydrodynamics”, Int. J. Cast Metals Research, 12, (2000), 335-355.
- [7] Ha, J. and Cleary, P.W., “Comparison of SPH simulations of high pressure die casting with the experiments and VOF simulations of Schmid and Klein”, Int. J. Cast Metals Research, 12, (2000), 409-418.
- [8] Ha, J., Cleary, P. W., Alguine, V. and Nguyen, T., “Simulation of die filling in gravity die casting using SPH and MAGMAsoft”, Proc. 2nd Int. Conf. on CFD in Minerals and Process Industries,Melbourne, Australia, 1999, 423-428.
Conclusion & Next Steps
This research provides a valuable roadmap for enhancing quality control in HPDC. The findings offer a clear, data-driven path toward improving die design, reducing defects like porosity and cold shuts, and optimizing the entire production process by accurately predicting complex fluid flow.
At CASTMAN, we are dedicated to applying the latest industry research to solve our customers' most challenging die casting problems. If the issues discussed in this paper resonate with your operational goals, contact our engineering team to discuss how we can help you implement these advanced principles in your components.
Expert Q&A: Your Top Questions Answered
Q1: What is the single biggest advantage of SPH for simulating complex HPDC parts?
A1: According to the paper's abstract and introduction, the key advantage is its ability to naturally and accurately model complex free surface behavior, including fragmentation and splashing, which is a defining characteristic of HPDC flow.
Q2: How was the accuracy of the SPH simulation verified in the paper?
A2: The accuracy was validated by comparing a simulated short shot of a cast aluminum coaster with a physical, experimental short shot. As shown in Figure 6, the predicted front profile was in "very good agreement with the experiment."
Q3: Can this SPH simulation method handle the effects of heat transfer and solidification?
A3: Yes. The paper explicitly demonstrates this with the simulation of a coaster filling with solidifying metal, as detailed in the section "Filling of the coaster with solidifying metal" and visualized in Figure 5, where the fluid is colored by temperature.
Q4: What specific types of casting defects can this simulation method help predict?
A4: The paper states that the simulations can predict the last locations to fill, which "correlate well with porosity/voidage observations." It also mentions in the conclusion that the method can highlight the possibility of predicting "cold shuts" by modeling heat transfer and solidification.
Q5: What is the scale of simulations possible with SPH, according to this 2005 paper?
A5: The paper demonstrates that SPH can handle large-scale industrial parts. The simulation of the engine rocker cover is described as the "geometrically largest part that has so far been simulated using SPH," and the door lock plate simulation involved "more than 2 million" particles, showing its capability for both large and highly detailed models.
Q6: What is the direct, practical takeaway from this paper for a die designer?
A6: The core takeaway, based on the paper "Simulation of casting complex shaped objects using SPH," is that SPH simulation offers a powerful and cost-effective way to study the effectiveness of different die and gating system designs. By visualizing the fill pattern, designers can proactively identify and correct issues that lead to voids and other defects before manufacturing begins.
Copyright
- This material is an analysis of the paper "Simulation of casting complex shaped objects using SPH" by P.W. Cleary, J. Ha, M. Prakash, and T. Nguyen.
- Source of the paper: https://www.researchgate.net/publication/291145862SimulationofcastingcomplexshapedobjectsusingSPH
- This material is for informational purposes only. Unauthorized commercial use is prohibited.
- Copyright © 2025 CASTMAN. All rights reserved.