Ya’nan Wu1, a, Guojie Huang1, b, Lei Cheng1,c, Daniel Liang2,d, Wei Xiao1,e
1State Key Laboratory of Nonferrous Metals and Processes, General Research Institute for
Nonferrous Metals, Beijing 100088, China
2Motor System,International Copper Association Asia, Tian Zuo International Center,
Beijing 100081, China
aynwu19@163.com, bhuangguojie@grinm.com, cchenglei@grinm.com,
dDaniel.liang@copperalliance.asia, ewxiao@ustb.edu.cn
Keywords: Numerical Simulation, Copper Rotors, FLOW-3D, Die Casting.
Abstract
The parametric optimization of process parameter in cold chamber die casting for an
industrial component (copper motor rotors) was analyzed. The filling process was successfully
simulated based on software FLOW-3D. The distribution of gas entrapment, temperature field and
surface defect during the mold filling process were discussed in details. The numerical results showed
that the pouring velocity had the most significant influence on the filling time, followed by the filling
temperature and the die temperature. As for the filling properties, the effect of the pouring
temperature was dominant. From the simulation results, the places of defect in the copper rotor were
forecasted, and the reasons of the defect were well explained. Thus, the technological parameters
could be improved in numerical simulation, and the simulation results would be further validated in
practice.
Introduction
Induction motors account for approximately 50% of the overall electricity use in industrialized
countries. In the agricultural and commercial areas, power consumption by motors is quite
substantial. On an average, the energy consumed by a motor during its life cycle is 60-100 times the
initial cost of the motor. Therefore efficiency of the motor is of paramount importance both during
selection and operation. Even small increase in efficiency improvement can make a big difference in
energy savings with accompanying decrease in air contamination [1,2].
For electric motors, copper rotors are significantly more efficient than aluminum ones [3].
However, we should balance the properties of high efficiencies, low costs, small sizes and lower
weights of the copper rotors [4,5,6]. Die casting is always used in the manufacture of motor rotors, for
its advantages of high production efficiency, high production quality and high precision [7]. The two
main challenges in copper rotor die-casting are the low tool life and the distribution of porosity.
Numerical simulation is a cost-effective tool to visibly analyze the filling process. Through the study
of numerical simulation, we can design a more reasonable die casting process, which can improve the
casting quality and make the copper rotors a longer life and a higher stability.
A lot of effort has been made by many researchers in the fields of numerical simulations for die
casting of aluminium, magnesium, zinc and pewter alloys [8]. However, simulation work in copper
die casting has rarely been published and the filling pattern of the copper die casting process has not
been well understood. For above mentioned reasons, the objective of this study was to optimize the
filling process of copper rotor based on software FLOW-3D. The behavior of metal flow in the filling
process was investigated. The gas entrapment, temperature field and surface defect of the rotor were
also investigated by the simulation.
Numerical Simulation
Mathematical Modeling. A commercial CAE package (FLOW-3D) was used for numerical
analysis. The software is based on the finite volume method (FVM). Incompressible non-Newtonian
flow with heat transfer is considered, which is described by the continuity equation, the
Navier-Stokes equation and the energy equation. These equations were solved by the FLOW-3D
software for a steady-state solution. As such, it is therefore believed to have a high accuracy by
considering the heat loss during the mould filling stage.
The basic governing equations are presented as follows:
....
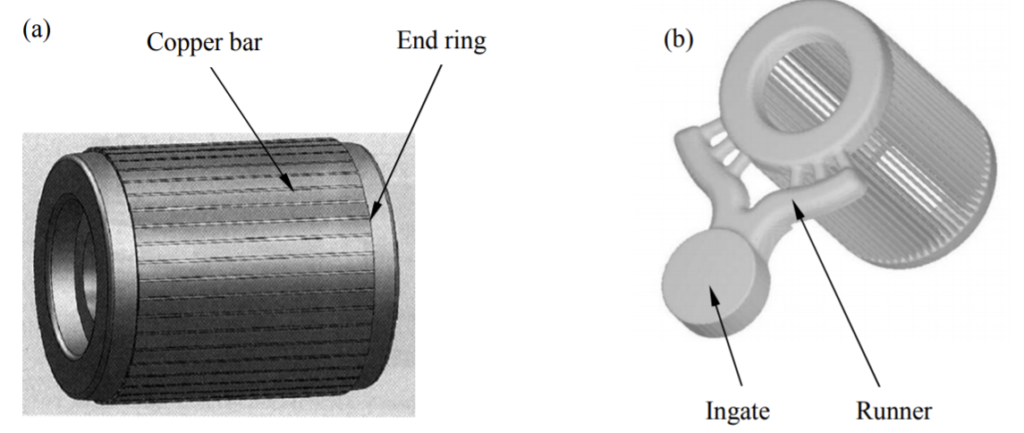
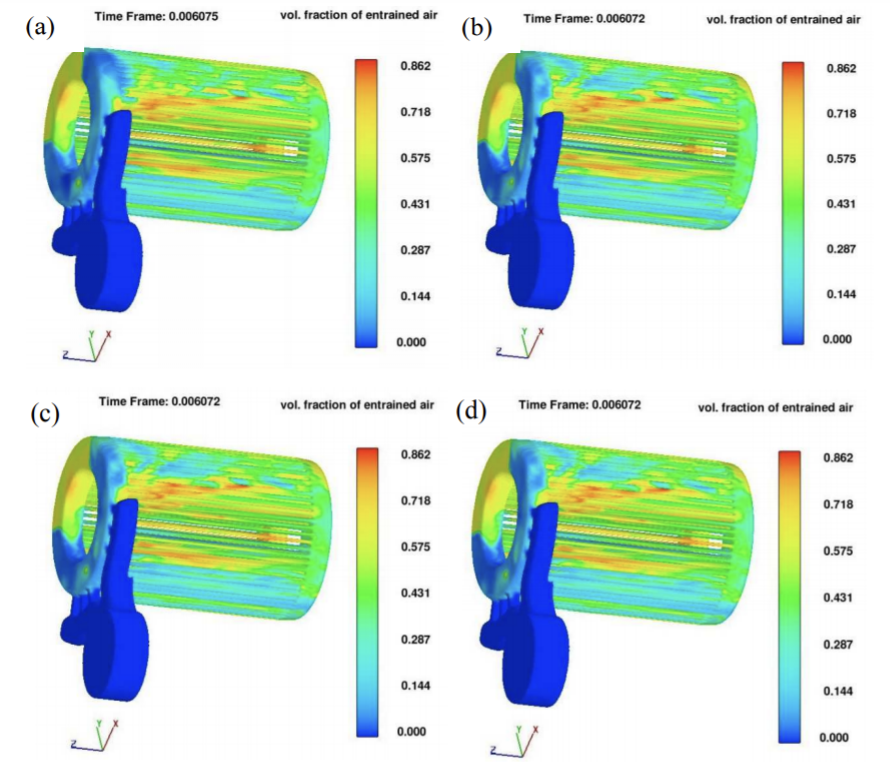
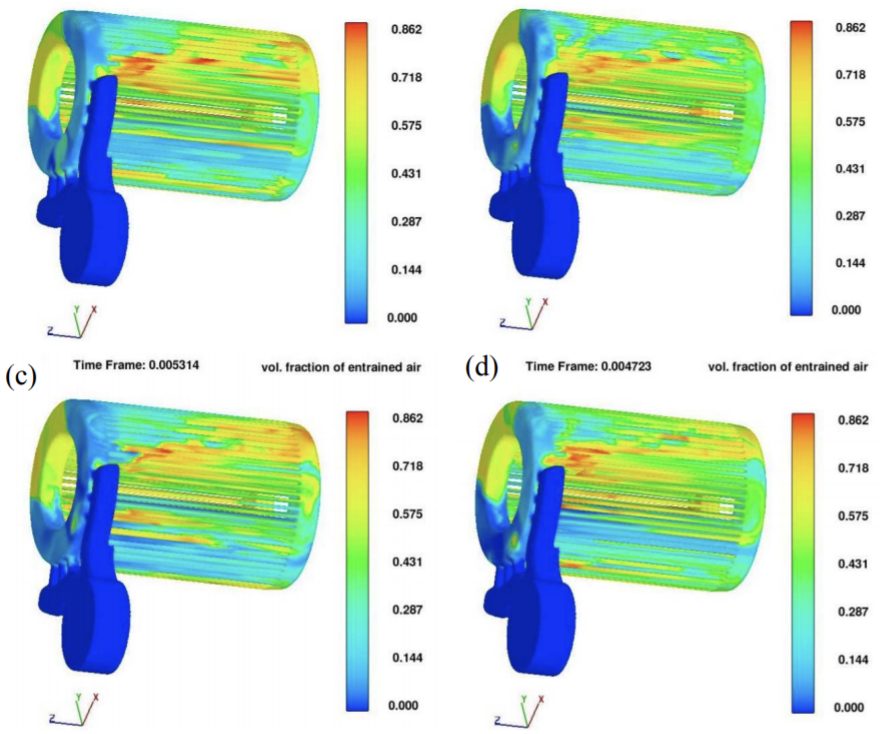
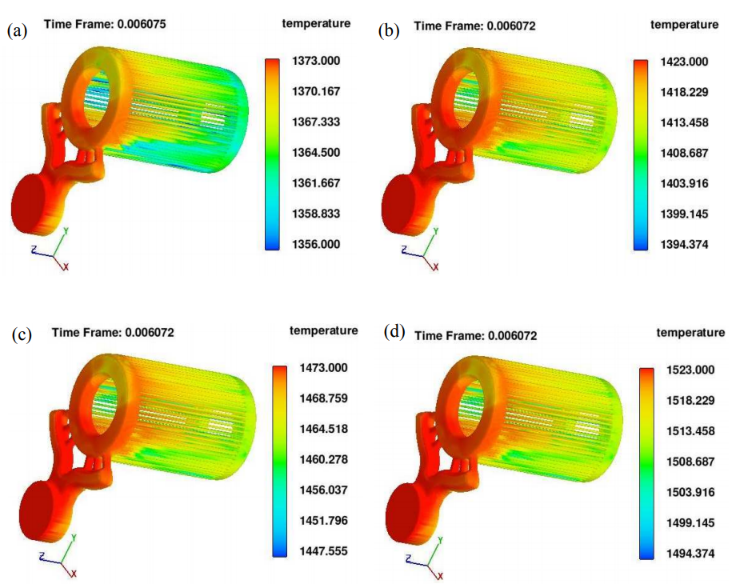
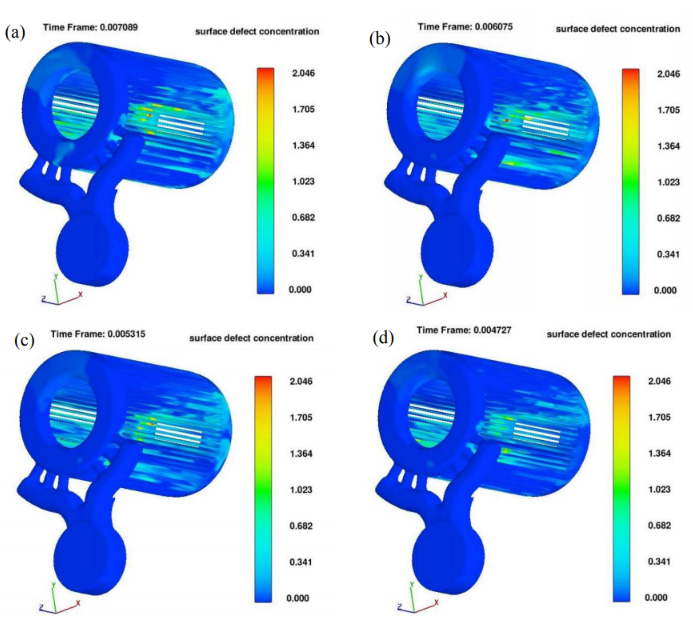
(a) L1; (b) L2; (c) L3; (d) L4
Conclusions
The concluding remarks out of the present study are depicted below.
(1) The best combination of parameters is L2, filling temperatures: 1100℃, pouring velocities:
35 m·s-1, die temperatures: 300℃.
(2)The pouring velocity has the most significant influence on the filling quality.
(3)The last filled regionof the casting has the largest fraction of entrained air, which is in
agreement with the practical product.
(4) As the pouring velocity increases, the flow of melt insidethe die cavity can be more turbulent,
leading to the formation of oxide films and cold shots. At constant filling temperature, a higher
pouring velocity brings lower surface defect concentration. The surface defect concentration is at a
scale of 0-2.046%.
References
[1] Peters D T, Cowie J G, Brush E F, et al. Performance of Motors with Die-cast Copper Rotors in
Industrial and Agricultural Pumping Applications,J. IEEE International Conference on Electric
Machines and Drives, (2005)987-992.
[2] Brush E F, Peters D T, Cowie J G, et al. Recent Advances in Development of the Copper Motor
Rotor J. 2003.
[3] Brush E F, Cowie J G, Peters D T, et al. Die-Cast Copper Motor Rotors: Motor Test Results,
Copper Compared to Aluminum, J. Energy Efficiency in Motor Driven Systems. Springer Berlin
Heidelberg,(2003)128-135.
[4] Cowie J G, Peters D T, Jr E F B, et al. Materials & modifications to die cast the copper
conductors of the induction motor rotor, J. Die Casting Engineer, 45(2001)38-47.
[5] Stark C, Cowie J G, Peters D T, et al. Copper in the Rotor for Lighter, Longer Lasting
Motors,2010.
[6] Liang D, Yang X, Yu J, et al. Experience in China on the die-casting of copper rotors for induction
motors,J. Electrical Machines (ICEM), (2012)256-260.
[7] Cleary P W, Savage G, Ha J, et al. Flow analysis and validation of numerical modelling for a thin
walled high pressure die casting using SPH, J. Computational Particle Mechanics, 1(2014)229-243.
[8] ZHAO Hai-dong, BAI Yan-fei, OUYANG Xiao-xian, et al. Simulation of mold filling and
prediction of gas entrapment on practical high pressure die castings, J. Transactions of Nonferrous
Metals Society of China, 20(2010)2064-2070.