This introduction paper is based on the paper "New Trends in Aluminum Die Casting Alloys for Automotive Applications" published by "The Eurasia Proceedings of Science, Technology, Engineering & Mathematics (EPSTEM)".
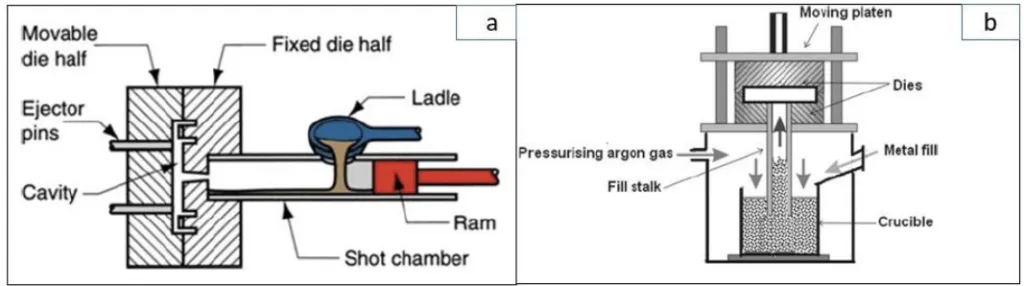
1. Overview:
- Title: New Trends in Aluminum Die Casting Alloys for Automotive Applications
- Author: Tanya A. BASER, Elif UMAY, Volkan AKINCI
- Year of publication: 2022
- Journal/academic society of publication: The Eurasia Proceedings of Science, Technology, Engineering & Mathematics (EPSTEM), Volume 21, Pages 79-87 (Presented at IConTES 2022: International Conference on Technology, Engineering and Science)
- Keywords: Light weighting, Aluminum casting alloys, Fuel consumption.
2. Abstract:
In order to provide ecological balance, new technologies are being developed to reduce fuel consumption. Within these new technologies, usage of light alloys such as aluminum and magnesium has gained great importance in the automotive applications. The advantages of aluminum alloys in terms of light weight, recycling, machinability and corrosion resistance led to increase application area of these alloys. Due to these characteristics of aluminum alloys, fuel-saving light-weight material selection plays an important role for automotive parts. Aluminum applications increase not only in automotive, but also in aerospace, space shuttle, marine, and defense applications. According to the production methods, aluminum alloys are generally classified as casting, sheet, forging and extrusion. Aluminum die casting alloys are generally used the production of suspension systems, engines and gears parts. However, with the developing aluminum casting technologies, the aluminum die casting method makes it possible to manufacture multiple body parts in one piece. It is predicted that number of aluminum die casting parts will increase, especially in electric vehicles. In this study, the importance of the use of aluminum die casting alloys in the automotive industry is emphasized. Research and trends so far of the development of aluminum die casting alloys are also summarized.
3. Introduction:
Weight reduction using light-weight materials is crucial for improving fuel economy and reducing harmful emissions, particularly CO2. Replacing steel with medium or high strength aluminum alloys is a key strategy for automotive lightweighting. Aluminum, the second most abundant metal element on Earth and the most used metal after steel, is preferred for its light weight, low density, good formability, and high corrosion resistance. Energy saving efforts have highlighted the role of light, economical vehicles, making aluminum alloys widely used in passenger cars, buses, trains, and marine applications. Aluminum's use in aviation and defense industries has paved the way for its adoption in the automotive sector.
4. Summary of the study:
Background of the research topic:
The need for ecological balance and reduced fuel consumption drives the development of new automotive technologies, emphasizing the use of light alloys like aluminum. Aluminum's inherent advantages (light weight, recyclability, machinability, corrosion resistance) make it critical for fuel-saving lightweight material selection in automotive parts, as well as in aerospace, marine, and defense sectors. Aluminum alloys are produced via casting, sheet forming, forging, and extrusion, with die casting commonly used for suspension systems, engines, and gear parts. Developing casting technologies now enable the production of large, integrated body parts, particularly relevant for electric vehicles (EVs).
Status of previous research:
Aluminum casting is widely used in the automotive industry for complex parts. Significant improvements in casting technologies allow the production of high-quality die-cast components comparable to wrought products, sometimes using substantial amounts of scrap for lower costs. Advanced molten metal handling and processes like hot isostatic pressing have improved quality by reducing impurities and porosity. Aluminum die casting alloys have established classification systems (3 digits + decimal) and can be heat treated. Master alloys and grain refinement (using AlTi5B1, Al3B, TiAl3, AlB2) are employed to enhance properties, especially for Al-Si alloys. The 300 series alloys (Al-Si based with Cu or Mg) are common for automotive housings and brackets.
Purpose of the study:
This study aims to emphasize the importance of using aluminum die casting alloys in the automotive industry. It also summarizes the research conducted so far and the current trends regarding the development and application of these alloys.
Core study:
The study reviews aluminum die casting alloys and their application trends in the automotive industry. It covers:
- Alloy characteristics: Discusses features like energy saving, light weight, classification, heat treatment, use of master alloys, and grain refinement processes. Highlights the preference for 300 series alloys.
- Casting Methods: Details common methods including sand mold casting, precision casting, and high pressure die casting (HPDC). Notes the increasing demand for HPDC due to part complexity and porosity requirements. Describes the advantages of die casting generally (efficiency, economics, geometry range, high-speed production, dimensional accuracy, strength-to-weight ratio, finishing options). Explains HPDC (injection under high pressure) and Low Pressure Die Casting (LPDC), outlining their respective advantages, disadvantages (e.g., HPDC costs, LPDC cycle time), and typical applications (e.g., LPDC for engine blocks, wheels).
- Applications & Trends: Focuses on the automotive industry's drive for weight reduction for fuel economy and performance. Quantifies potential fuel savings (0.6 L per 100 kg reduction per 100 km) and CO2 reduction. Provides examples of die-cast parts (fasteners, brakes, engine components, stators, brackets, heat sinks, structural components like cross car beams, engine cradles, shock towers). Discusses the increasing popularity of structural die castings, especially in premium vehicles and EVs to offset battery weight. Highlights the significant growth in aluminum content per vehicle, with casting remaining dominant but shifting from powertrain to structural applications. Introduces the major trend of "mega-giga casting" adopted by companies like Tesla and Volvo to produce large, single-piece structural components (like floor pans or rear bodies), replacing dozens of smaller parts, reducing assembly complexity, time, and cost, particularly beneficial for EVs.
5. Research Methodology
Research Design:
The study employs a literature review and trend analysis approach. It synthesizes information from existing academic papers, industry reports, and technical publications.
Data Collection and Analysis Methods:
Information was gathered by reviewing published research, conference proceedings, industry reports (e.g., Ducker Frontier, Center for Automotive Research), and technical articles related to aluminum alloys, die casting processes, and automotive applications. The collected data was analyzed to identify key developments, applications, and emerging trends.
Research Topics and Scope:
The research focuses specifically on aluminum die casting alloys within the context of the automotive industry. The scope includes the properties of these alloys, various casting methods (especially die casting variants like HPDC and LPDC), current applications (powertrain, chassis, structural), and future trends driven by lightweighting, electrification (EVs, hybrids), and advanced manufacturing processes like mega-casting.
6. Key Results:
Key Results:
- Aluminum die casting is a critical technology for automotive lightweighting, driven by the need for improved fuel economy and reduced emissions.
- Aluminum alloys provide significant benefits including light weight, recyclability (nearly 90% recycled), machinability, and corrosion resistance.
- Technological advancements enable high-quality, complex die-cast parts, including large structural components, with properties comparable to wrought products.
- High Pressure Die Casting (HPDC) is essential for high-volume automotive production; trends include thin-walled castings and very large "mega-castings".
- Aluminum content per vehicle is steadily increasing, projected to exceed 250 kg on average. Casting remains the dominant form, but its application is shifting from powertrain components (due to downsizing) towards structural castings, especially for Battery Electric Vehicles (BEVs) and hybrids.
- Mega-casting, producing large monolithic structures (e.g., replacing 70+ parts with one), is a significant emerging trend (Tesla, Volvo, etc.) aimed at reducing weight, complexity, assembly time, and cost, while improving vehicle efficiency.
- Established practices like grain refinement and the use of master alloys continue to be important for optimizing alloy properties. 300-series Al-Si alloys are widely used.
- Weight reduction through aluminum usage yields substantial fuel savings (approx. 0.6 L/100km per 100 kg reduction) and contributes to CO2 emission reduction goals.
- Figure 3. Examples of aluminum die casting components (Cheșa, 2019).
- Figure 4. Examples for Al casting structural parts; cross car beam (a), engine cradle (b), control arm (c) , shock tower (d) (Hirsch et al, 2011, Baser, 2012, Hartlieb, 2013).
- Figure 5. The long term aluminum growth by product forms (Ducker Frontier, 2020).
- Figure 6. Emerging manufacturing processes in the automotive applications (Center for Automotive Research, 2019).
- Figure 7. Production of Tesla Model 3 is revealed Tesla model Y by mega-giga casting technology (Duckers, 2022).
- Figure 8. The megacasting replaces many stamped parts at the rear of this Volvo’s chassis (Carney, 2022)
Figure Name List:
- Figure 1. Classification of aluminum alloys in automotive by production method (Ozcomert, 2006).
- Figure 2. Illustration of; high pressure die casting (a), low pressure die casting (b) methods (Bonollo et al, 2015).
- Figure 3. Examples of aluminum die casting components (Cheșa, 2019).
- Figure 4. Examples for Al casting structural parts; cross car beam (a), engine cradle (b), control arm (c), shock tower (d) (Hirsch et al, 2011, Baser, 2012, Hartlieb, 2013).
- Figure 5. The long term aluminum growth by product forms (Ducker Frontier, 2020).
- Figure 6. Emerging manufacturing processes in the automotive applications (Center for Automotive Research, 2019).
- Figure 7. Production of Tesla Model 3 is revealed Tesla model Y by mega-giga casting technology (Duckers, 2022).
- Figure 8. The megacasting replaces many stamped parts at the rear of this Volvo's chassis (Carney, 2022).
7. Conclusion:
Global competition and ecological preservation demands push automotive manufacturers towards new solutions, aiming for reasonable product costs, production efficiency, lower fuel consumption, effective recycling, and improved comfort without compromising safety. Light metals, particularly aluminum alloys, have become indispensable due to their high engineering properties. Aluminum die casting alloys are a crucial group for industrial applications, especially automotive. While challenges existed, advances in casting technology, mainly in pressure die casting (especially HPDC), enable the production of high-integrity, complex parts (both thin and thick). HPDC is efficient for reducing porosity and suitable for high production rates, accounting for about 50% of global light metal casting production. Applications range from engine parts to structural components, which are increasingly popular. Advanced manufacturing processes like high-pressure thin-walled aluminum die casting are vital, with applications expected to increase towards 2040. While traditional powertrain castings decrease due to engine downsizing, a strong trend towards structural castings exists, particularly for BEVs and plug-in hybrids. The emergence of "mega-giga casting" technology (e.g., Tesla, Volvo) for producing large, single-piece aluminum structures represents a significant future direction.
8. References:
- Alam, T., & Ansari, A. H. (2017). Review on aluminium and its alloys for automotive applications. Int. J. Adv. Technol. Eng. Sci, 5, 278-294.
- Baser, T. A. (2012). Aluminum alloys and automotive applications. Journal of Engineering and Machine, 53 (635): 51-58.
- Baser, T. A., Usta M., Cetin H., Ozcan S., Celiker, T. (2013). A study of bending on AA6XXX extruded profiles, 7th International Conference and Exhibition on Design and Production of Machines and Dies/Molds, 77.
- Brinkman, CH. J., Engler, O., Hirsch J., & Schroder, D. (2010). INALCO2010. GDA-Aluminium Congress, Essen/Germany
- Carney, D. (2022, March 14). Design news, automotive engineering. https://www.designnews.com/automotive-engineering/volvo-joins-tesla-giga-press-club
- Center for Automotive Research (CAR). 2019 Center for Automotive Research Annual Report. https://www.cargroup.org/2019-annual-report/
- Chesa, A., & Graz, T. (2019, June). Present and future in automotive applications (Master's thesis). Die Casting Technology
- Criqui, B. (2009). Proc. Int. SLC Conference on innovative developments for lightweight vehicle structures, May, 2009, Germany, p. 157
- Cuniberti, A., Tolley, A., Riglos, M. C., & Giovachini, R. (2010). Influence of natural aging on the precipitation hardening of an AlMgSi alloy. Materials Science and Engineering: A, 527(20), 5307-5311.
- Dalquist, S., & Gutowski, T. (2004, January). Life cycle analysis of conventional manufacturing techniques: sand casting. In ASME International Mechanical Engineering Congress And Exposition (Vol. 47136, pp. 631-641).
- Ducker Frontier (2019, October 10). Aluminum Content in European Cars, European Aluminium Public Summary. https://www.european-aluminium.eu/media/2714/aluminum-content-in-european-cars_european-aluminium_public-summary_101019-1.pdf
- Ducker Frontier (2020, April). North America light vehicle aluminum content and outlook final report summary.
- Ducker Worlwide (2017, September 25). Automotive lightweighting insights. https://societyofautomotiveanalysts.wildapricot.org/resources/Documents/SAA_Ducker%20Worldwide%20Automotive%20Lightweighting%20September%2025%202017%20Distribution.pdf
- Duckers (2022, May 11). Mega-casting trends for automotive manufacturers. https://www.linkedin.com/pulse/mega-casting-trends-automotive-manufacturers-2022-ducker worldwide/?trk=organization-update-content_share-article
- Engler, O., Brinkman, H. J. & Hirsch, J. (2010). Strategien des karosseriebaus,, Bad Neuheim, Ed. Automotive Circle International.
- Glazoff, M. V., Zolotorevsky, V. S., & Belov, N. A. (2010). Casting aluminum alloys. Elsevier.
- Graf, A. (2021). Aluminum alloys for lightweight automotive structures. In Materials, Design and Manufacturing for Lightweight Vehicles (pp. 97-123). Woodhead Publishing.
- Hartlieb, M., & Rheinfelden, KG. (2013). Primary aluminium alloys for pressure die casting. A company of the Aluminium Rheinfelden Group, Friedrichstraße 80, Alloys GmbH & Co.
- Hirsch, J. (2011). Aluminium in innovative light-weight car design. Materials Transactions, 52(5), 818-824.
- Kaufman, J. G., & Rooy, E. L. (2004). Aluminum alloy castings: properties, processes, and applications. Asm International.
- Kelly, J. C., Sullivan, J. L., Burnham, A., & Elgowainy, A. (2015). Impacts of vehicle weight reduction via material substitution on life-cycle greenhouse gas emissions. Environmental Science & Technology, 49(20), 12535-12542.
- Kridli, G. T., Friedman, P. A., & Boileau, J. M. (2021). Manufacturing processes for light alloys. In Materials, Design And Manufacturing For Lightweight Vehicles (pp. 267-320). Woodhead Publishing.
- Ozcomert, M. (2006). Aluminum in automotive industry (Master thesis).Istanbul Trade Center.
- Palencia, J. C. G., Furubayashi, T., & Nakata, T. (2012). Energy use and CO2 emissions reduction potential in passenger car fleet using zero emission vehicles and lightweight materials. Energy, 48(1), 548-565.
- Pattnaik, S., Karunakar, D. B., & Jha, P. K. (2012). Developments in investment casting process a review. Journal of Materials Processing Technology, 212(11), 2332-2348.
- Reddy, B. M., & Nallusamy, T. (2021). Degassing of aluminum metals and its alloys in non-ferrous foundry. In Advances in Materials Research (pp. 637-644). Springer, Singapore.
- Smith, L. J. B., Corbin, S. F., Hexemer, R. L., Donaldson, I. W., & Bishop, D. P. (2014). Development and processing of novel aluminum powder metallurgy materials for heat sink applications. Metallurgical and Materials Transactions A, 45(2), 980-989.
- Spittle, J. A. (2006). Grain refinement. In Shape Casting Of Aluminium Alloys.
- Taub, A. I., Krajewski, P. E., Luo, A. A., & Owens, J. N. (2007). The evolution of technology for materials processing over the last 50 years: the automotive example. Jom, 59(2), 48-57.
- Wang, W., Stoll, H. W., & Conley, J. G. (2010). Rapid tooling guidelines for sand casting. Springer.
- Zeytin H. (2000). Aluminum alloys and automotive applications in future, MAM MKTAE Project Number: 50H5602.
9. Copyright:
- This material is a paper by "Tanya A. BASER, Elif UMAY, Volkan AKINCI". Based on "New Trends in Aluminum Die Casting Alloys for Automotive Applications".
- Source of the paper: [DOI URL Not Provided in Paper] (Published in The Eurasia Proceedings of Science, Technology, Engineering & Mathematics (EPSTEM), 2022, Vol 21, pp 79-87)
This material is summarized based on the above paper, and unauthorized use for commercial purposes is prohibited.
Copyright © 2025 CASTMAN. All rights reserved.