A Breakthrough in Smart Casting: Embedding Electronics Directly into Molten Aluminum
This technical brief is based on the academic paper "Micromachined Thermogenerator Directly Integrated into Metal Parts: Technological Aspects of the Embedding Process" by A. Ibragimov, H. Pleteit, C. Pille, and W. Lang, published in the 1st Joint International Symposium on System-Integrated Intelligence 2012. It is summarized and analyzed for HPDC professionals by the experts at CASTMAN.
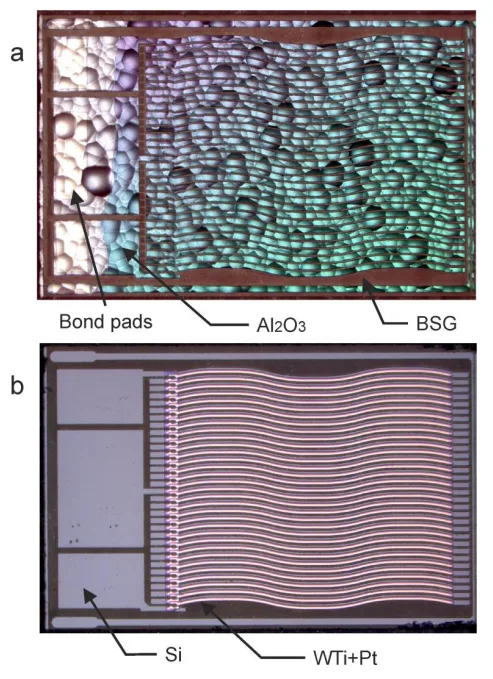
Keywords
- Primary Keyword: Embedding sensors in metal casting
- Secondary Keywords: High-pressure die casting (HPDC), thermogenerator integration, semiconductor embedding, smart casting, aluminum casting process, sensor protection framework
Executive Summary
- The Challenge: To successfully embed sensitive semiconductor (sc) devices directly into metal components during high-temperature, high-pressure die casting without destroying the electronics.
- The Method: Researchers developed a process using a thermogenerator (TG) as a demonstrator. The TG was fixed within a specially designed, removable polycarbonate framework and then subjected to a high-pressure die casting (HPDC) process with liquid aluminum at 700°C.
- The Key Breakthrough: The study demonstrated the fundamental feasibility of the concept. After the casting and removal of the protective framework, 28% of the embedded thermogenerators were fully functional, surviving direct contact with molten aluminum.
- The Bottom Line: The preparation of the semiconductor device, particularly the design of its protective framework, is critical to success. The primary cause of failure was not the extreme temperature but the mechanical deformation of the final cast part, highlighting the need for structural reinforcement in the component design.
The Challenge: Why This Research Matters for HPDC Professionals
For decades, engineers have sought to create "smart" metal parts with integrated electronic functionality. Bringing sensors or other devices into direct contact with a metal workpiece can dramatically improve sensitivity and create robust, self-contained systems. However, the extreme conditions of metal casting have been a major barrier.
Previous attempts, as noted in the paper (Ref. [1-4]), faced significant limitations:
- Thick Protective Layers: Using bulky insulation (Ref. [1-2]) protects the electronics but decouples them from the metal part, making them unsuitable for sensing applications.
- Incompatible Substrates: Using steel substrates for sensors (Ref. [3-4]) is incompatible with standard semiconductor manufacturing and limits the complexity of the devices that can be used.
This research tackles the core challenge head-on: closing the gap between these approaches to prove that standard semiconductor devices can be directly integrated into a metal workpiece during its formation from the melt.
The Approach: Unpacking the Methodology
To prove the concept, the researchers selected a Seebeck-effect based thermogenerator (TG) as their demonstrator device (Figure 1). The TG, built on a borosilicate glass (BSG) substrate with an Al₂O₃ isolation layer, was chosen for its relative simplicity and thermal stability.
The embedding process was a multi-stage operation designed to protect the fragile device:
- Framework Manufacturing: A protective framework was manufactured from polycarbonate. After initial designs proved problematic, the final method involved drilling holes into a solid plastic mounting and using thermally stable vacuum rubber plugs to fix the TGs (Figure 5).
- Protective Measures: For additional safety, a second passivation layer of glass paste was applied to the TGs and annealed at 430°C.
- Casting Process: The plastic mounting containing the TGs was placed into a die casting mold. A high-pressure die casting (HPDC) process was performed using a 'BÜHLER SCN/66' unit.
- Casting Parameters: An aluminum alloy (AlSi9Cu3) was cast at 700°C with a plunger speed of 0.6 m/s and a redensification pressure of 300 bar.
- Unveiling: After casting (Figure 6), the protective plastic parts were mechanically stripped off while still hot, laying the thermogenerators open (Figure 7).
The Breakthrough: Key Findings & Data
The study yielded critical insights into the feasibility and challenges of embedding electronics in cast metal.
- Low-Temperature Validation: An initial experiment embedding the TG in molten tin (232°C) was successful (Figure 2), proving the TG's basic integrity and the effectiveness of its Al₂O₃ insulating layer against short circuits.
- High-Temperature Survivability: The most significant finding was that the TGs could survive the HPDC process with aluminum at 700°C. A subsequent functionality test revealed a percent yield of 28%.
- Failure Analysis: The primary cause of failure was not thermal shock or melt infiltration. Instead, it was the mechanical deformation of the final cast aluminum part. The 55-mm long wall where the TGs were embedded was a mechanical weak point. The analysis showed that when the bending of this wall exceeded 4 mm, no TGs survived, regardless of other protective measures (Figure 8).
- Framework is Key: The research underscored that the success of the embedding process is highly dependent on the design of the protective framework and the mechanical stability of the final cast component.
Practical Implications for Your HPDC Operations
The findings from this paper, while academic, offer tangible insights for manufacturers looking to innovate with smart-casting technology.
- For Process Engineers: This research provides a validated proof-of-concept for integrating electronics at temperatures up to 700°C. The 28% yield demonstrates that with a refined process, commercial viability is within reach. The methodology of using a sacrificial, removable framework is a key takeaway for process design.
- For Quality Control: The strong correlation between the final part's mechanical deformation and component failure (as seen in Figure 8) provides a critical quality metric. Ensuring the straightness and rigidity of cast parts with embedded electronics is paramount to achieving high yields.
- For Die and Product Design: This study emphasizes that designers must account for the fragility of embedded components. The final product must be designed not only for its primary function but also to act as a rigid, protective housing for the integrated electronics. The area around the embedded device may require reinforcement to prevent post-casting flex and deformation.
Paper Details
Micromachined Thermogenerator Directly Integrated into Metal Parts: Technological Aspects of the Embedding Process
1. Overview:
- Title: Micromachined Thermogenerator Directly Integrated into Metal Parts: Technological Aspects of the Embedding Process
- Author: A. Ibragimov, H. Pleteit, C. Pille and W. Lang
- Year of publication: 2012
- Journal/academic society of publication: 1st Joint International Symposium on System-Integrated Intelligence 2012: New Challenges for Product and Production Engineering
- Keywords: Aluminum, Casting, Energy Harvesting.
2. Abstract:
The goal of the research is to demonstrate feasibility of the incorporating of semiconductor (sc) devices into metal workpieces during their forming form the melt. Alongside with the mechanical and thermal stability of the sc-device itself preparations to the embedding process are important to the overall success. The preparation stage is the focus of this paper and includes manufacturing of the adequate framework and fixing of the sc-devices in it. Frameworks were manufactured from polycarbonate and the thermogenerators, which were chosen as demonstrators, were fixed in them using plugs from vacuum rubber. The frameworks were subsequently placed into the casting mould and a high pressure die casting process with liquid aluminium was performed. After the mechanical removing of the protective plastic cover and plugs, the thermogenerators were laid open. The subsequent functionality test gave a percent yield of 28%. The failure analyse shows the need of further development of the framework.
3. Introduction:
The paper introduces the advantages of bringing functional elements directly into metal workpieces, such as improved sensor sensitivity and robust protection for electronics. It reviews previous attempts, noting their limitations, such as the use of thick protective layers that hinder sensing or the use of non-standard steel substrates that are incompatible with semiconductor technology. The main goal is to bridge this gap and demonstrate the feasibility of embedding standard semiconductor structures into a metal workpiece as it is formed from the melt.
4. Summary of the study:
Background of the research topic:
The research is set against the challenge of integrating sensitive electronics into metal parts during high-temperature manufacturing processes like casting. The potential benefits are significant, but the technical hurdles of thermal and mechanical stress have limited practical applications.
Status of previous research:
Previous work either used thick protective layers for components like RFID chips, which isolates them from the working body, or embedded thin-film sensors on steel substrates, which limits device complexity and is not compatible with common semiconductor technology. This paper aims to overcome these limitations.
Purpose of the study:
The primary purpose was to conduct a "proof-of-concept" study to demonstrate that a semiconductor device could be successfully embedded into a metal part during its formation from a molten state. The research focused on the technological aspects of the embedding process itself, including the preparation of the device and its protective framework.
Core study:
The core of the study involved developing and testing a methodology for embedding a thermogenerator (TG) into an aluminum part using high-pressure die casting (HPDC). This included designing a removable protective framework, refining the method of fixing the TG within it, performing the casting at 700°C, and analyzing the results to determine the success rate and causes of failure.
5. Research Methodology
Research Design:
The research was designed as a multi-step experimental process. It began with a low-temperature validation using molten tin, followed by the main experiment using HPDC with molten aluminum. A Seebeck-effect thermogenerator (TG) was chosen as the demonstrator device. The key variable under investigation was the design of the protective framework used to hold the TG during casting.
Data Collection and Analysis Methods:
Data was collected through post-casting inspection and functionality testing of the embedded TGs. A failure analysis was performed to identify the root causes of non-functional devices, which involved examining the mechanical integrity of both the TGs and the final cast aluminum part. The yield of functional devices was calculated as a percentage.
Research Topics and Scope:
The scope was focused on the technological feasibility of the embedding process. It covered the choice of a suitable demonstrator device (TG), the design and manufacturing of a protective framework, the execution of an HPDC process with aluminum, and the analysis of the outcomes. The research did not extend to optimizing the TG's performance, but rather to ensuring its survival.
6. Key Results:
Key Results:
- The concept of embedding a semiconductor device during casting was proven feasible, first in low-temperature tin and then in high-temperature aluminum.
- The Al₂O₃ isolation layer on the TG was sufficient to prevent electrical short circuits with the surrounding metal.
- A functional yield of 28% was achieved for TGs embedded in aluminum via HPDC at 700°C.
- The primary cause of failure was identified as the mechanical deformation of the cast aluminum part itself. When the part's bending exceeded 4 mm, the embedded TGs cracked and failed.
- The preparation stage, including the design of the framework and the method of fixing the chips, was determined to be critically important to the overall success.
Figure Name List:
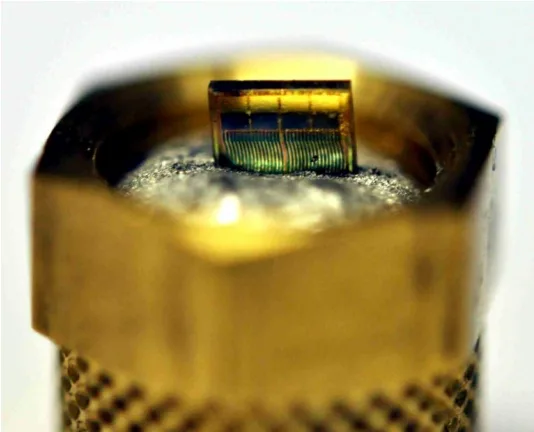

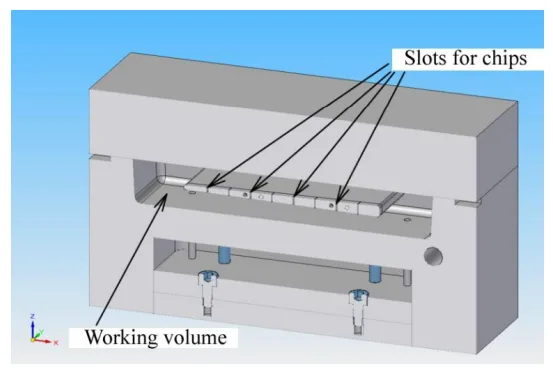
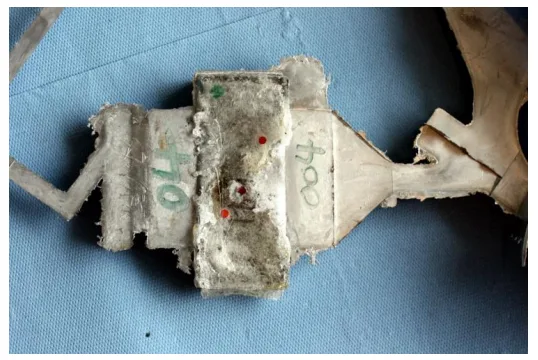
Figure 6. Mounting with three TG embedded in cast aluminium.
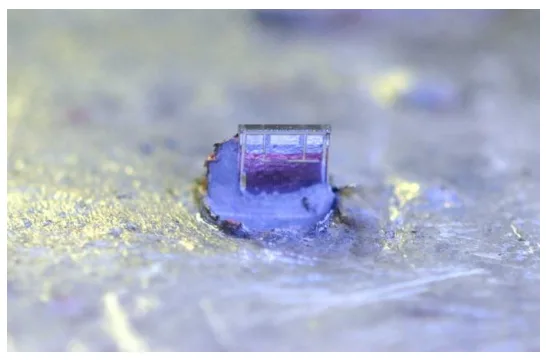
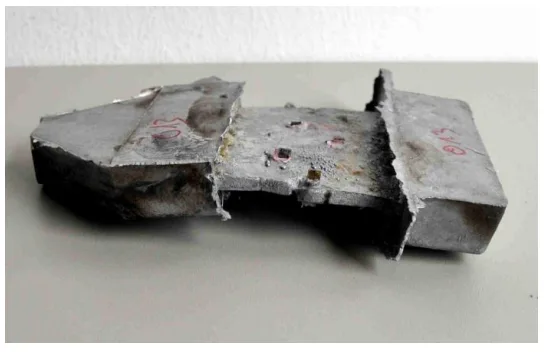
- Figure 1. Thermogenerator: (a) view from the structured side, (b) view through the transparent BSG-substrate.
- Figure 2. TG embedded into tin.
- Figure 3. Schematic of the embedding process with a removable plastic protection.
- Figure 4. Section of the puncheon for the initial embedding into the plastic component.
- Figure 5. Plastic mounting with three TGs fixed in it using resin plugs.
- Figure 6. Mounting with three TG embedded in cast aluminium.
- Figure 7. Half embedded TG after removing protective plastic.
- Figure 8. Deformation of an aluminum casting part.
7. Conclusion:
The paper successfully demonstrated the feasibility of directly incorporating semiconductor devices into metal structural parts during casting from a molten mass. A thermogenerator was successfully embedded in both tin and aluminum, surviving temperatures up to 700°C while retaining functionality. The research highlights the critical importance of the preparation process, including the manufacturing of the framework and the method of fixing the chips. The mechanical stability of the final cast part was identified as a key factor for device survival, a problem that must be addressed in future work through improved framework and part design.
8. References:
- [1] Busse, M., Wöstmann, F.-J., Müller, T., Melz, T., Spies, P., 2006, Intelligente Gussteile – Einsatz adaptronischer Komponenten in Kombination mit Gussteilen. In: Giesserei 2006, 93/04:48-53.
- [2] Pille, C., 2010, In-Process-Embedding of Piezo Sensors and RFID Transponders into Cast Parts for Autonomous Manufacturing Logistics Gessner, T. (ed.): Smart Systems Integration.
- [3] Kobliska, J. et al., 2005, Rapid fabrication of smart tooling with embedded sensors by casting in molds made by three dimensional printing, Proceedings of the SFF Symposium.
- [4] Cheng, X. et al., 2007, Study on embedding and integration of microsensors into metal structures for manufacturing applications, J. Manuf. Sci. Eng., 129:416.
- [5] Ibragimov, A., Pleteit, H., Pille, C., and Lang, W., 2012, IEEE Electron Device Lett., 33/2:233-235.
Conclusion & Next Steps
This research provides a valuable roadmap for enhancing component functionality through direct electronic integration in casting. The findings offer a clear, data-driven path toward creating a new class of "smart" metal parts, improving quality and enabling new applications.
CASTMAN is committed to applying cutting-edge industry research to solve our customers’ most challenging technical problems. If the problem discussed in this white paper aligns with your research goals, please contact our engineering team to discuss how we can help you apply these advanced principles to your research.
Expert Q&A:
- Q1: What was the main goal of this research?
- A: The primary goal was to demonstrate the feasibility of incorporating semiconductor (sc) devices directly into metal workpieces during their formation from a molten state, as stated in the paper's Summary.
- Q2: What specific device was used as a demonstrator and why?
- A: A Seebeck-effect based thermogenerator (TG) was chosen. The paper explains this choice was made because the device was not overly complex, allowing the research to focus on the embedding process itself, while its structure and functionality would be useful for future, more complex devices.
- Q3: What was the success rate of the embedding process in aluminum, and what was the primary cause of failure?
- A: The functionality test showed a success rate, or percent yield, of 28%. The failure analysis concluded that the main cause of cracks in the failed TGs was the deformation of the cast metal part itself. As shown in Figure 8, when the bending of the aluminum part exceeded 4 mm, the TGs did not survive.
- Q4: What materials and process conditions were used for the high-temperature casting?
- A: The experiment used a high-pressure die casting (HPDC) process. The molten metal was an AlSi9Cu3 aluminum alloy teemed at 700°C, with a plunger speed of 0.6 m/s and a redensification of 300 bar.
- Q5: How were the sensitive parts of the thermogenerator protected during the casting process?
- A: Protection was multi-faceted. First, the TG itself has an Al₂O₃ isolation layer to prevent short circuits. Second, a removable plastic framework with vacuum rubber plugs was used to cover the ends of the TG, preventing direct contact with the melt in those areas and providing a means of holding it in the mold, as detailed in Figure 3 and Figure 5.
Copyright
- This material is an analysis of the paper "Micromachined Thermogenerator Directly Integrated into Metal Parts: Technological Aspects of the Embedding Process" by A. Ibragimov et al.
- Source of the paper: 1st Joint International Symposium on System-Integrated Intelligence 2012: New Challenges for Product and Production Engineering, pp. 204-207.
- This material is for informational purposes only. Unauthorized commercial use is prohibited.
- Copyright © 2025 CASTMAN. All rights reserved.