This article introduces the paper 'Improving Die Casting Melt Quality and Casting Results with Melt Quality Analysis and Filtration' published by 'Proceedings, 4th International Conference on Molten Aluminum Processing, AFS'.
1. Overview:
- Title: Improving Die Casting Melt Quality and Casting Results with Melt Quality Analysis and Filtration
- Author: Dr. David V. Neff
- Publication Year: Not specified in the paper.
- Publishing Journal/Academic Society: Conference Proceedings: 4th International Conference on Molten Aluminum Processing, AFS
- Keywords: die casting, melt quality, filtration, bonded particle filter, aluminum, inclusions, melt cleanliness, reduced pressure test, Qualiflash, Prefil Footprinter, PodFA, K-Mold, Tatur test, mechanical testing
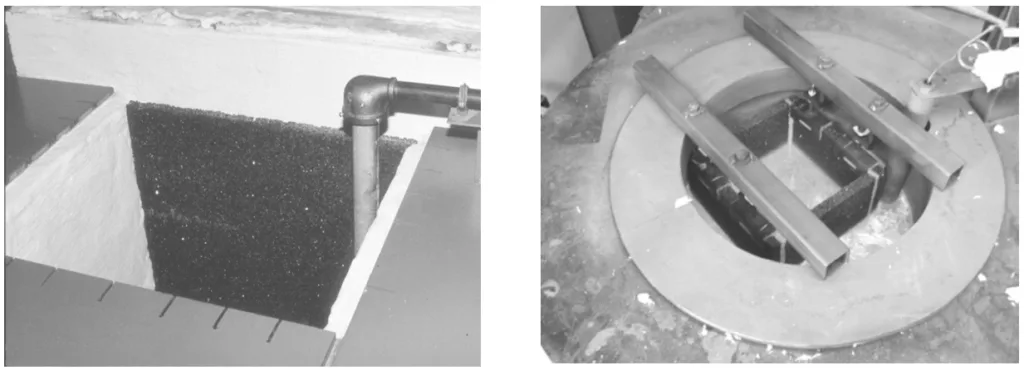
2. Abstracts or Introduction
ABSTRACT
The use of aluminum castings in automotive applications continues to expand at a significant pace. High volume requirements are served by high pressure, low pressure, permanent mold, and precision sand casting processes. The engineered requirements for these applications demand a high degree of casting integrity, which begins with the aluminum alloy melt conditions.
Information is presented in this paper on several shop floor and laboratory methods of evaluating melt quality cleanliness, especially with respect to inclusions, and the benefits to be derived from sustained-usage, in-furnace filtering systems employing the bonded particle filter.
Substantial gains can be made in reduction of machining defects, improved surface finish, increased elongation, reduced leakers, and overall scrap reduction---all with minimal cost, effort, and risk utilizing bonded particle filtration.
INTRODUCTION
The growth in aluminum casting production and process technology has been very significant over the past decade. Increased automotive usage for engine components, structural components, wheels, and other functional castings is a major component of this growth. The higher property requirements of such castings have demanded excellent metal quality and melt treatment processes to provide more stringent controls on metal cleanliness—control of inclusions and hydrogen content to minimize porosity/microporosity. Melt treatments to produce clean metal include fluxing and/or flux injection, degassing, and filtration. Filtration processes are now employed in virtually every aluminum shape casting operation. Typical benefits that are expected, and achieved, include (1) greater metal fluidity and feeding capability during the casting process; (2) higher casting properties; (3) improved machinability; (4) better surface finish; and (5) overall reduction in scrap and reject castings.
In pressure diecasting, certain gravity diecasting or permanent mold processes, and high volume green or chem-bonded sand casting processes, it is often not practical to provide absolute point-of-pour, in-the-mold filtration. Consequently the remaining option is to employ filters in melting/remelt furnaces and in casting furnaces as close to the point-of-cast as possible. The bonded particle filters have emerged as the preferred filter of choice in such in-furnace applications in most instances (Neff, 1995). This filter is an aggregrate of silicon carbide bonded with a proprietary ceramic binder which resists any degradation in molten aluminum for long periods of time. The silicon carbide material is also very durable and thermally conductive, making it most suitable for extended, continuous usage over long periods of time. The bonded particle filter's lower porosity, tortuosity of internal structure, and affinity of the binder system to capture and retain inclusions enhances the overall inclusion removal efficiency of this filter.
Typical configurations include a Vertical Gate Filter, Figure 1a, separating the hearth from the dip-out well, in a casting furnace or the 'box filter' (Figure ib). The latter can be confugured to a variety of geometric shapes and sizes to suit furnace geometry and ladle size, and has the advantage of providing greater surface area; metal to be cast is auto-ladled from, or manually dipped from the interior of the filter vessel placed in a holding furnace or crucible furnace.
3. Research Background:
Background of the Research Topic:
The aluminum casting industry, particularly in automotive applications, has experienced substantial growth. This expansion is driven by the demand for high-volume production of complex components using processes like high pressure die casting, low pressure die casting, permanent mold casting, and precision sand casting. These applications necessitate aluminum castings with superior integrity, which is fundamentally dependent on the quality of the aluminum alloy melt. Achieving high casting integrity requires meticulous control over melt conditions, especially concerning melt cleanliness.
Status of Existing Research:
Melt treatment processes, including fluxing, degassing, and filtration, are critical for producing clean aluminum melts. Filtration, in particular, has become a standard practice in virtually all aluminum shape casting operations. Bonded particle filters have become the favored technology for in-furnace filtration applications. These filters, composed of silicon carbide aggregates with a proprietary ceramic binder, offer resistance to degradation in molten aluminum and are designed for sustained, continuous use. Their structural characteristics, including lower porosity and tortuosity, coupled with the binder's inclusion affinity, contribute to enhanced inclusion removal efficiency.
Necessity of the Research:
While filtration is widely adopted, quantifying its effectiveness and the resultant improvements in melt quality remains crucial. Die casters require methods to assess filtration performance beyond macroscopic observations. Quantitative and semi-quantitative techniques are needed to evaluate melt cleanliness improvements achieved through bonded particle filtration in both production and experimental settings. This evaluation is essential to optimize casting processes, reduce defects, and enhance the overall quality of die cast components.
4. Research Purpose and Research Questions:
Research Purpose:
The primary research purpose is to demonstrate and quantify the efficacy of bonded particle filtration in enhancing die casting melt quality and subsequent casting outcomes. This study aims to showcase the benefits of in-furnace filtration systems employing bonded particle filters through rigorous evaluation of melt cleanliness and casting performance.
Key Research:
This research focuses on evaluating various established and emerging techniques for assessing molten metal cleanliness in the context of die casting. The study investigates the application of methods such as:
- Reduced Pressure Test
- Actual hydrogen measurement (Alscan, Hyscan, Leco analysis)
- Qualiflash fluidity test
- Prefil Footprinter test
- PodFA (Porous Disc Filtration Apparatus) or LAIS (Liquid Aluminum Inclusion Sampler) test
- Mechanical testing
- Tatur test
- K-Mold test
The core of the research involves applying these techniques to assess melt quality improvements resulting from bonded particle filtration in production-scale experiments and ongoing production environments.
Research Hypotheses:
It is hypothesized that the implementation of bonded particle filtration will lead to a significant improvement in molten metal cleanliness. This improvement is expected to manifest in:
- Enhanced metal fluidity and feeding capability during die casting.
- Superior casting mechanical properties, particularly elongation.
- Improved machinability of die cast components.
- Enhanced surface finish of castings.
- Reduction in overall scrap and reject rates in die casting production.
5. Research Methodology
Research Design:
The research employs a combination of laboratory-scale evaluations and production foundry trials to comprehensively assess the impact of bonded particle filtration. Laboratory experiments were conducted on production-sized melts to simulate industrial conditions under controlled settings. Production trials were performed in operational pressure and gravity die casting foundries to validate laboratory findings in real-world manufacturing environments.
Data Collection Method:
Melt quality data was collected using a range of analytical techniques, including:
- Reduced Pressure Test: To assess overall melt cleanliness and estimate hydrogen content.
- Alscan: For real-time measurement of hydrogen content in molten metal.
- Qualiflash: To evaluate molten metal fluidity.
- Prefil Footprinter: To provide real-time analysis of metal cleanliness relative to industry benchmarks.
- PodFA: For metallographic evaluation of inclusions concentrated on a test filter.
- Mechanical Testing: To determine tensile and yield strength, elongation, and fatigue strength using cast test bars.
- Tatur Test: To measure shrinkage and porosity distribution.
- K-Mold Test: A shop-floor test for visual examination of macro defects on fractured samples.
Casting performance data, such as scrap rates, machining defects, and surface finish quality, were also collected from production trials.
Analysis Method:
Quantitative data from techniques like Alscan, Prefil Footprinter, mechanical testing, and Tatur test were statistically analyzed to determine the significance of improvements due to filtration. Semi-quantitative methods like Reduced Pressure Test, Qualiflash, PodFA, and K-Mold were used to provide comparative assessments of melt cleanliness and defect levels. Results from filtered and unfiltered melts were compared to quantify the benefits of bonded particle filtration. Metallographic examination and image analysis were utilized for inclusion assessment in PodFA tests.
Research Subjects and Scope:
The primary material under investigation was LM24 (A380) aluminum alloy, a common alloy in die casting. The study focused on in-furnace filtration systems utilizing 8 grit Metaullics Box Filters, a type of bonded particle filter. The research scope encompassed evaluating melt quality and casting results in both laboratory simulations and actual production environments within pressure and gravity die casting foundries.
6. Main Research Results:
Key Research Results:
The study demonstrated that bonded particle filtration significantly improves die casting melt quality and casting results. Key findings include:
- Enhanced Melt Cleanliness: Prefil Footprinter tests (Figure 9a, 9b), PodFA analysis (Figure 10, 11), and K-Mold tests (Figure 12a, 12b) consistently showed improved melt cleanliness with bonded particle filtration compared to unfiltered melts and industry standards.
- Improved Metal Fluidity: Qualiflash tests (Figure 13a) and Prefil Footprinter curves (Figure 9a, 9b) indicated enhanced metal fluidity in filtered melts, suggesting better die filling capability.
- Increased Elongation: Mechanical testing (Table 2) revealed a significant improvement in elongation for filtered samples, a critical property for structural castings. Tensile and yield strength were not significantly affected, as expected for moderately clean melts.
- Reduction in Defects: Production foundry data (Table 3) and K-Mold results (Figure 12b) indicated a reduction in hardspots, leakers, scrap rates, and tool breakage in machining operations when using filtered metal.
- Tatur Test Improvements: Tatur test results (Table 1) showed a 3% difference in shrinkage volume and a 10% higher feeding distance for filtered material, suggesting improved feeding characteristics.
Analysis of presented data:
- Prefil Footprinter Curves (Figure 9a, 9b): Showed that filtered metal exhibited a steeper curve, indicating faster flow rate and thus better fluidity, aligning with ‘clean metal’ industry standards. Production foundry Prefil results (Figure 9b) confirmed significant improvement with filtration.
- PodFA Results (Figure 10, 11): Demonstrated a reduction in total inclusion content with 8 grit bonded particle filters compared to 20 ppi ceramic foam filters and unfiltered melts. Figure 11 further highlighted the improvement achieved by filtration even after flux injection.
- K-Mold Test Results (Figure 12a, 12b): Clearly distinguished between filtered and unfiltered melts, with filtered samples showing consistently lower K-factor values (fewer defects). Production diecaster K-Mold results (Figure 12b) corroborated these findings with excellent results on 380 alloy.
- Qualiflash Results (Figure 13a): Demonstrated significant improvement in fluidity (higher Q Level) with the box filter in laboratory settings.
- Tatur Test Results (Table 1): Indicated a positive impact of filtration on shrinkage and feeding characteristics, with filtered material showing reduced shrinkage volume and improved feeding distance.
- Mechanical Property Data (Table 2): Highlighted a notable increase in elongation for filtered samples, while tensile and yield strength remained largely unaffected.
- Foundry Benefit Data (Table 3): Provided real-world examples of foundries experiencing benefits like eliminated hardspots, reduced leakers, extended tool life, and reduced scrap rates due to in-furnace bonded particle filtration.
Figure Name List:
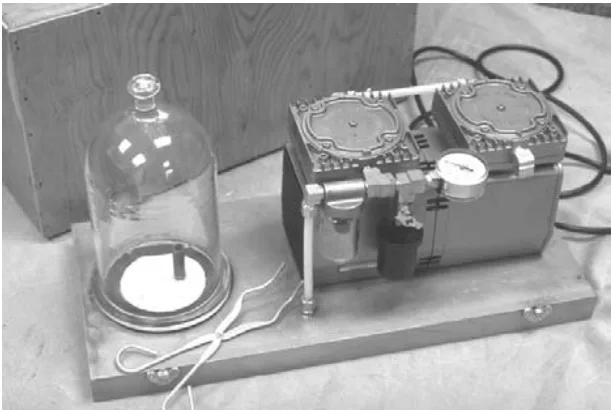
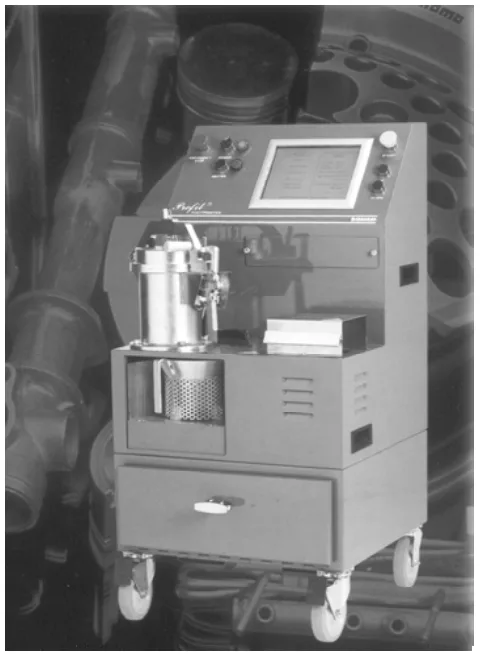
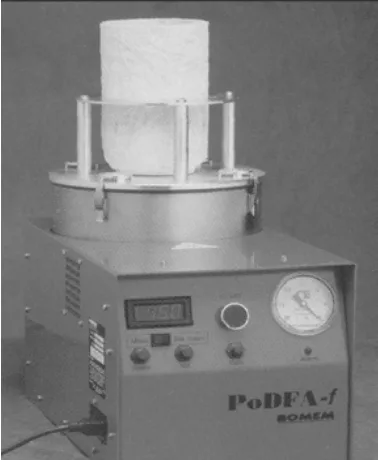
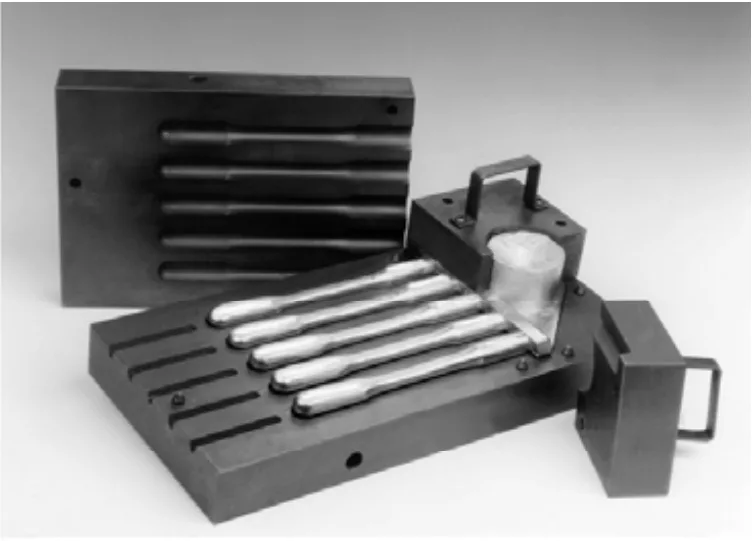
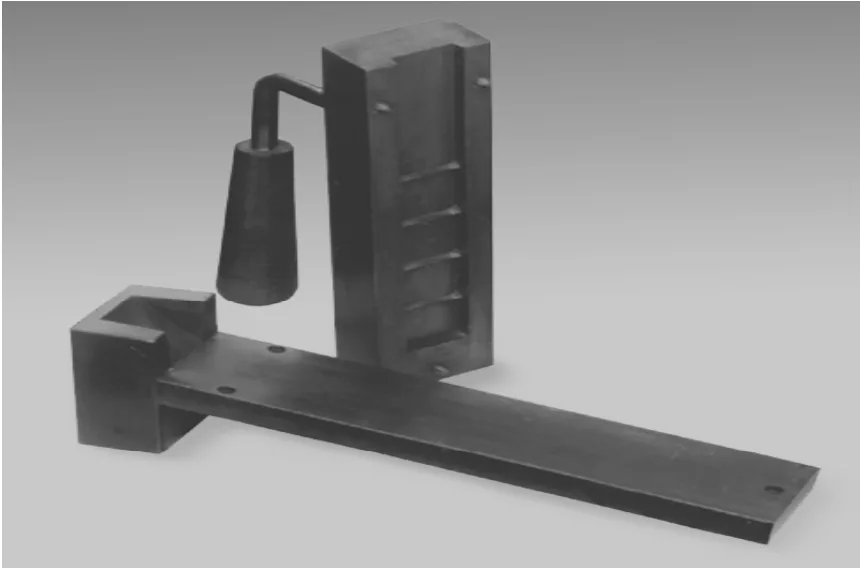
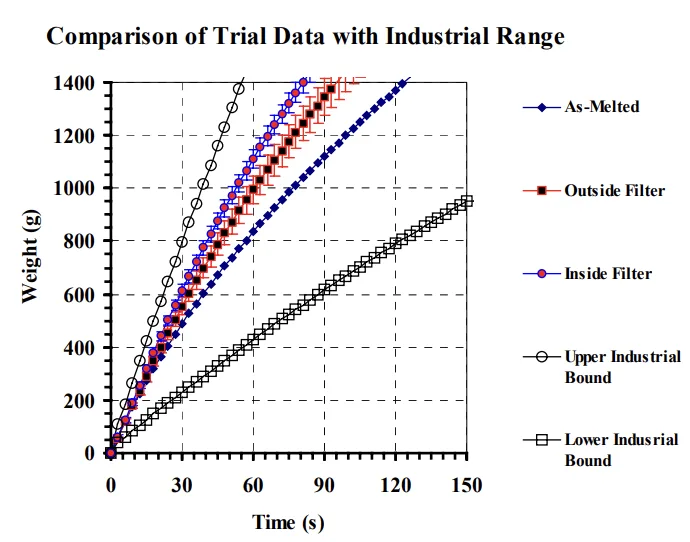
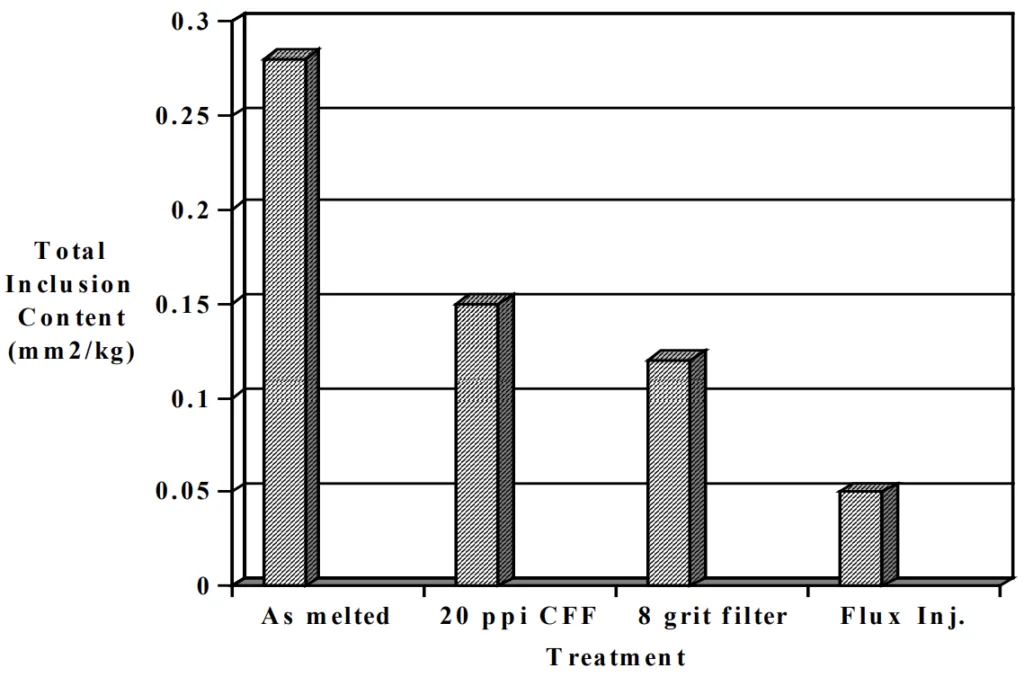
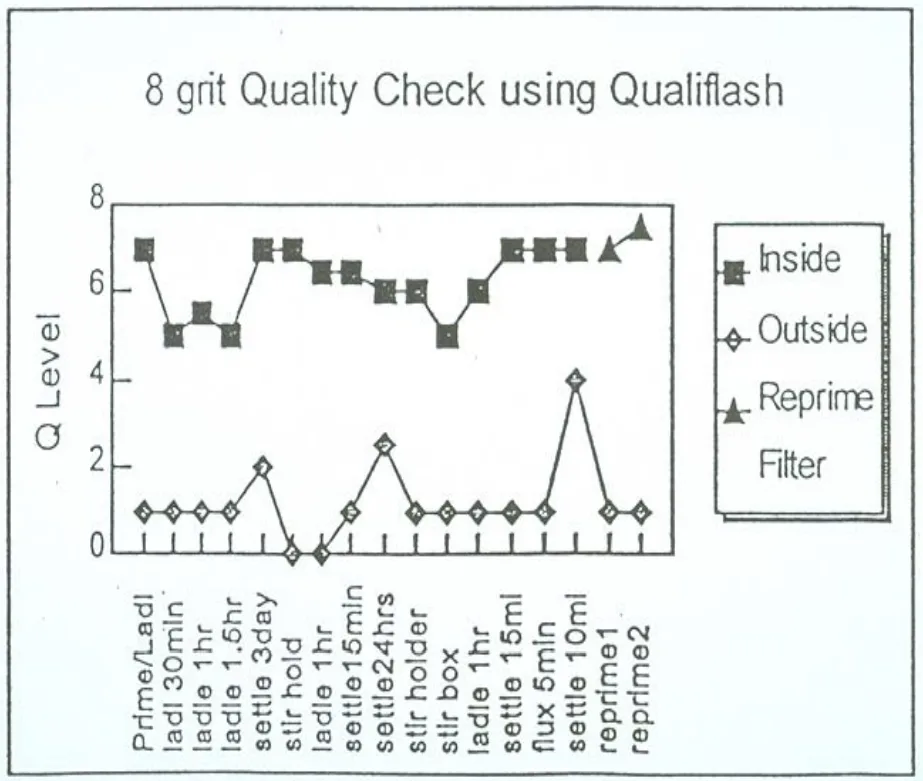
- Figure 1a: Vertical Gate Filters are placed in the outlet well or dipwell of a casting furnace.
- Figure 1b: A box filter is useful in crucible furnaces our dipwells of other furnace types.
- Figure 2: The Reduced Pressure Test is the most common tool used by foundries and diecasters to assess metal quality.
- Figure 3: The Qualiflash test measures molten metal fluidity semi-quantitatively.
- Figure 4: The Prefil Footprinter provides real-time analysis of metal cleanliness relative to accumulated industry data. (N-Tec)
- Figure 5: The PodFA test is a common method to evaluate metal cleanliness using metallography on the collected sample.
- Figure 6: A multiple test bar mold is used to cast specimens for mechanical testing. (N-Tec)
- Figure 7: The Tatur test measures shrinkage and porosity. (N-Tec).
- Figure 8: The K-Mold is a simple shop-floor, real-time test which evaluates macro-cleanliness.
- Figure 9a: The Prefil curve demonstrates improved fluidity with the filter compared with normal industry data.
- Figure 9b: Production foundry Prefil results verify benefits of filtration.
- Figure 10: PodFA results show improvement of 8 grit bonded particle filter over 20 ppi ceramic foam filter.
- Figure 11: PodFA results show further improvement by filtration after flux injection.
- Figure 12a: Laboratory K-mold results after continuous re-use of the same metal.
- Figure 12b: Production diecaster K-Mold results show excellent results on 380 alloy.
- Figure 13a: Laboratory results with Qualiflash show significant improvement with the box filter.
7. Conclusion:
Summary of Key Findings:
This research conclusively demonstrates the beneficial impact of bonded particle filtration on die casting melt quality and casting performance. Utilizing a range of melt quality evaluation techniques and production data, the study confirms that in-furnace filtration with bonded particle filters effectively enhances melt cleanliness, improves metal fluidity, increases elongation, and reduces casting defects and scrap rates. These improvements translate to tangible benefits in die casting operations, contributing to higher quality castings and reduced production costs.
Academic Significance of the Study:
This study provides a comprehensive evaluation of various melt quality assessment methodologies in the context of die casting. It scientifically validates the effectiveness of bonded particle filtration as a critical melt treatment process for achieving superior aluminum melt quality. The research contributes to the fundamental understanding of how filtration impacts melt cleanliness and subsequently influences casting properties.
Practical Implications:
The findings offer significant practical implications for the die casting industry. The research strongly advocates for the adoption of in-furnace filtration using bonded particle filters as a best practice to enhance casting quality and operational efficiency. The study highlights the importance of employing melt quality evaluation techniques for process monitoring and optimization. Die casters can leverage these findings to implement effective filtration strategies, reduce defects, improve machinability, and ultimately enhance the marketability of their castings.
Limitations of the Study and Areas for Future Research:
While the study provides robust evidence for the benefits of bonded particle filtration, it acknowledges that specific results may vary depending on foundry-specific conditions, alloy types, and casting processes. Future research could explore:
- Optimization of filtration parameters (e.g., filter pore size, flow rate) for different alloys and casting applications.
- Long-term performance and durability assessment of bonded particle filters in industrial settings.
- Detailed cost-benefit analysis of implementing in-furnace filtration in diverse die casting operations.
- Investigation of the impact of filtration on other casting defects and mechanical properties beyond those evaluated in this study.
- Development of real-time melt quality monitoring and control systems integrated with filtration processes.
8. References:
- 1. Neff, D., "continuous, Sustained, “Re-useable” Filtration Systems for Aluminum Foundries and Diecasters, Proceedings, 4th International Conference on Molten Aluminum Processing, AFS, Orlando, November, 1995, р.121
- 2. Law, J., Tian, C., Murray, M., “Experiences in the Measurement of Molten Metal Quality in a High Pressure Diecasting Foundry", Transacations, NADCA 1999, p.235
- 3. Evans, C., Willmert, W., “Qualiflash as it Relates to Filtration and Degassing for Foundry and Extrusion Alloys" Proceedings, Fifth International Conference, Molten Aluminum Processing, AFS, Orlando, November, 1998, p. 349
9. Copyright:
- This material is "Dr. David V. Neff"'s paper: Based on "Improving Die Casting Melt Quality and Casting Results with Melt Quality Analysis and Filtration".
- Paper Source: Not specified in the paper.
This material was summarized based on the above paper, and unauthorized use for commercial purposes is prohibited.
Copyright © 2025 CASTMAN. All rights reserved.