Joshua Thomas JamesonBurda, Elizabeth A.Moorea, HeshamEzzatbRandolphKirchainaRichardRotha
a Materials Systems Laboratory, Massachusetts Institute of Technology, 77 Massachusetts Ave, E19-695, Cambridge, MA 02139, United States
b WorldAuto Steel/American Iron and Steel Institute, 2000 Town Center, Suite 320, Southfield, MI 48075, United States
Highlights
- Global demand for and adoption of battery electric vehicles is on the rise.
- To achieve increased driving range, there is increased interest in lightweighting.
- Increased battery energy density and motor improvements can lower costs.
- As these costs decline, the need for high cost lightweight materials will diminish.
- Cost tradeoffs and technological advances can impact decision-making.
Abstract
Demand for battery electric vehicles (BEVs) has grown over the past decade as a result of climate action targets and energy policies globally. To improve driving range and minimize battery costs, BEV manufacturers have adopted lightweight materials with the objective of reducing energy requirements and enabling the use of smaller, less expensive batteries. However, improvements in battery energy density and electric motor technologies have enhanced vehicle performance and lowered costs independently. Thus, the need for expensive lightweight materials for mass savings could diminish as these technologies rapidly advance. This study evaluates lightweight material substitution cost tradeoffs and their changes over time for an advanced high strength steel and aluminum BEV design. Process-based cost modeling methods assess cost tradeoffs for body and closures and mass scaling estimations inform costs in the battery and motor, chassis, and other vehicle systems. Under current conditions, a steel design costs $595 less per vehicle than aluminum, where steel’s cost advantage is in body and closures manufacturing and aluminum’s advantage is in battery, motor, and chassis manufacturing cost. As lightweighting advantages of battery and motor costs decline over time, the cost gap grows wider, with a $743 per vehicle cost advantage for steel. These results underscore the importance of accounting for technological advancements and learning when projecting BEV costs. This material substitution decision ultimately has implications for energy systems and long-term profitability of BEV business models. As BEV performance and costs improve, there will be an increase in demand for BEVs, electricity, and charging infrastructure.
Keywords
Electric vehicles, Lithium-ion battery, Air cooling, Battery thermal management system, Review
Korea
배터리 전기 자동차 (BEV)에 대한 수요는 전 세계적으로 기후 행동 목표와 에너지 정책의 결과로 지난 10 년 동안 증가했습니다. 주행 거리를 개선하고 배터리 비용을 최소화하기 위해 BEV 제조업체는 에너지 요구 사항을 줄이고 더 작고 저렴한 배터리를 사용할 수 있도록 경량 소재를 채택했습니다. 그러나 배터리 에너지 밀도와 전기 모터 기술의 개선으로 차량 성능이 향상되고 비용이 독립적으로 절감되었습니다. 따라서 대량 절약을 위한 고가의 경량 재료에 대한 필요성은 이러한 기술이 빠르게 발전함에 따라 감소 할 수 있습니다. 이 연구는 고급 고강도 강철 및 알루미늄 BEV 설계에 대한 경량 재료 대체 비용 절충과 시간 경과에 따른 변화를 평가합니다. 프로세스 기반 비용 모델링 방법은 차체 및 폐쇄에 대한 비용 절충을 평가하고 질량 확장 추정은 배터리 및 모터, 섀시 및 기타 차량 시스템의 비용을 알려줍니다. 현재 상황에서 강철 디자인은 알루미늄보다 차량 당 595 달러 더 저렴합니다. 강철의 비용 이점은 차체 및 폐쇄 제조에 있고 알루미늄의 이점은 배터리, 모터 및 섀시 제조 비용에 있습니다. 배터리 및 모터 비용의 경량화 이점이 시간이 지남에 따라 감소함에 따라 비용 격차는 더 넓어지고 강철의 경우 차량 당 비용 이점이 $ 743입니다. 이러한 결과는 BEV 비용을 예측할 때 기술 발전과 학습에 대한 설명의 중요성을 강조합니다. 이 물질 대체 결정은 궁극적으로 에너지 시스템과 BEV 비즈니스 모델의 장기적인 수익성에 영향을 미칩니다.
Graphical abstract

Introduction
The adoption of electric vehicles (EVs) is growing, with the global
stock of EVs exceeding 7 million in 2019. Under future market scenarios,
the stock of EVs could rapidly grow to 130 million EVs in 2030 [1] given:
1) efforts to mitigate greenhouse gas (GHG) emissions [2], 2) increased
accessibility to EVs through policy tools and climate action targets [1,3]
and 3) falling costs of ownership [4,5]. Continued battery electric
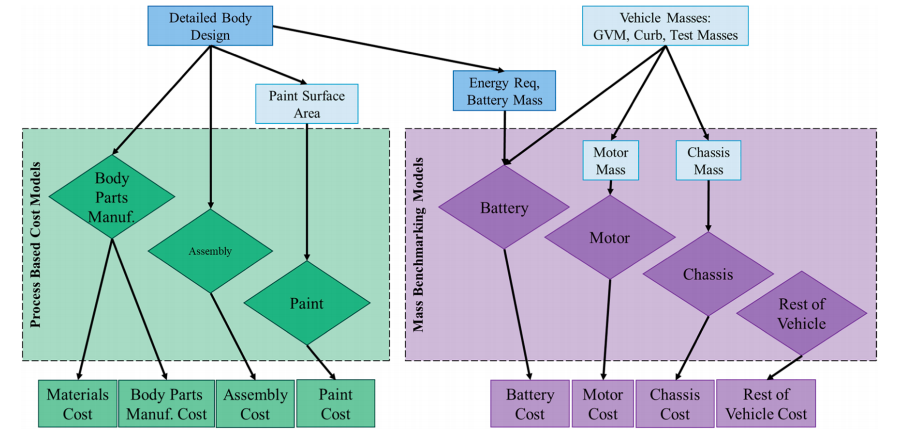
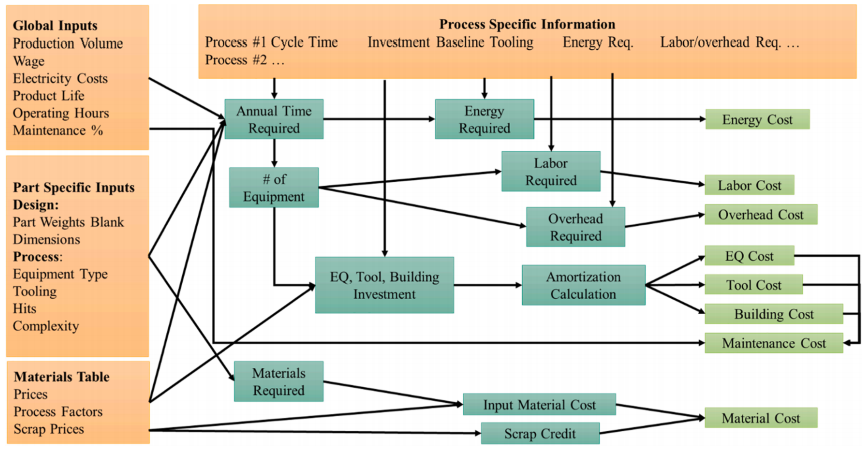
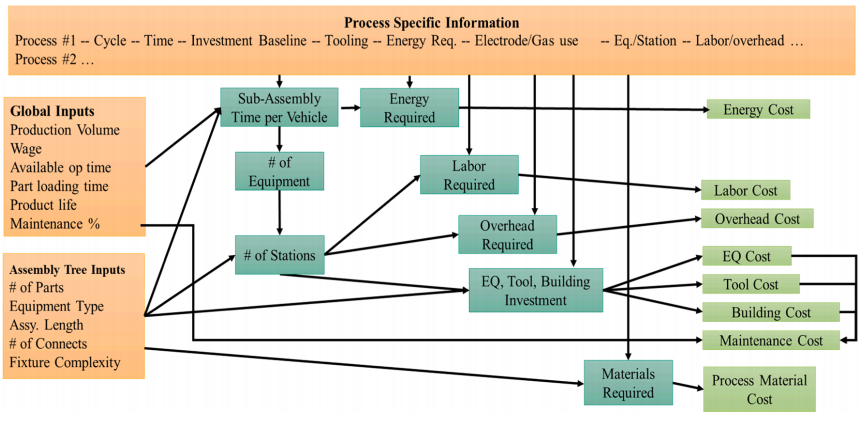
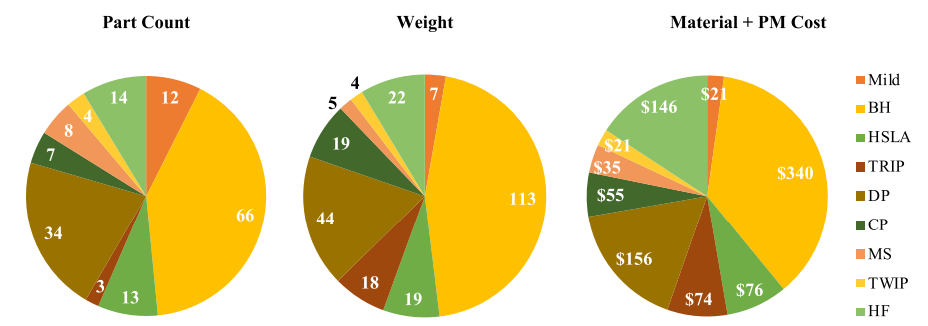
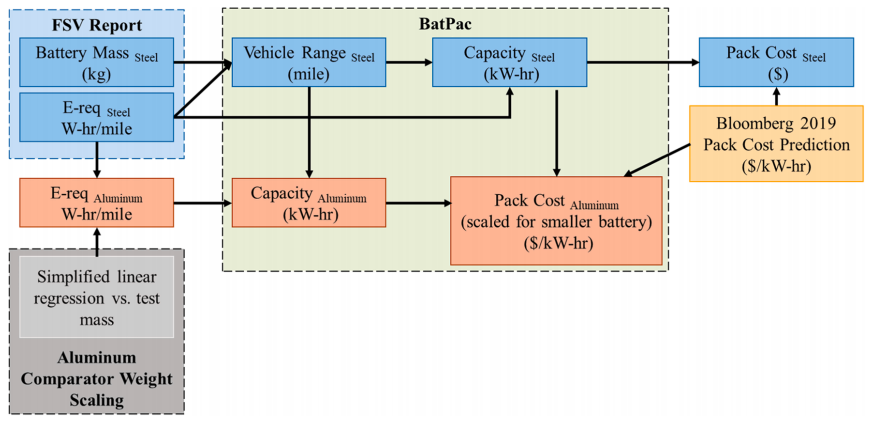
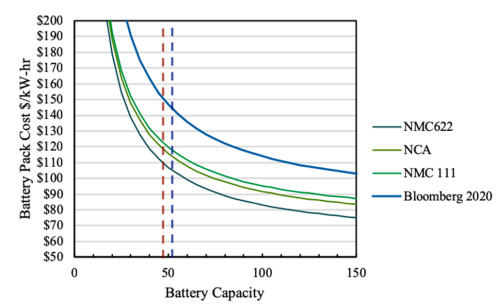
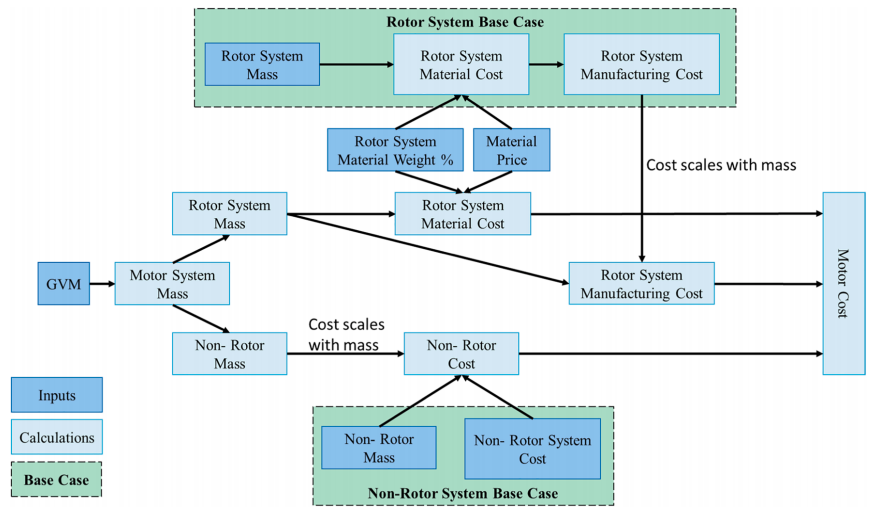
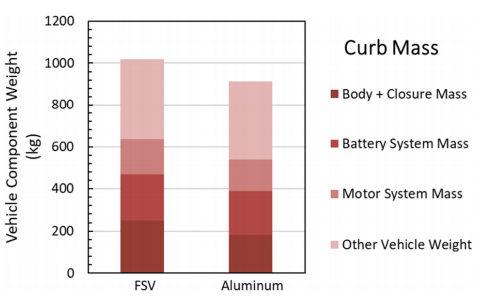
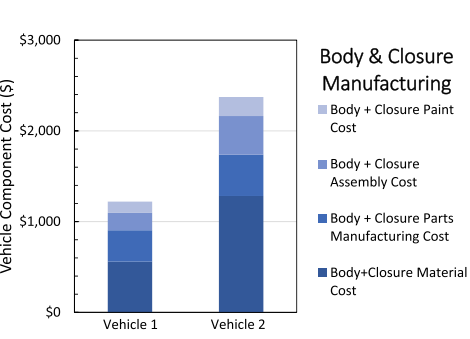
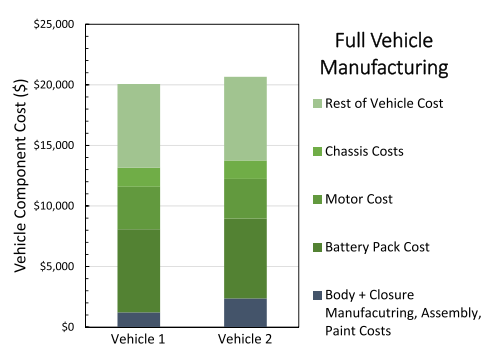
References
[1] IEA. Global EV Outlook 2019 – Analysis - IEA. Iea 2019. https://www.iea.org/
reports/global-ev-outlook-2019 (accessed February 28, 2020).
[2] Hill G, Heidrich O, Creutzig F, Blythe P. The role of electric vehicles in near-term
mitigation pathways and achieving the UK’s carbon budget. Appl Energy 2019;
251:113111. https://doi.org/10.1016/j.apenergy.2019.04.107.
[3] Wang N, Pan H, Zheng W. Assessment of the incentives on electric vehicle
promotion in China. Transp Res Part A Policy Pract 2017;101:177–89. https://doi.
org/10.1016/j.tra.2017.04.037.
[4] Needell ZA, McNerney J, Chang MT, Trancik JE. Potential for widespread
electrification of personal vehicle travel in the United States. Nat Energy 2016;1:
1–7. https://doi.org/10.1038/nenergy.2016.112.
[5] Zhuge C, Wei B, Shao C, Dong C, Meng M, Zhang J. The potential influence of costrelated factors on the adoption of electric vehicle: An integrated micro-simulation
approach. J Clean Prod 2020;250:119479. https://doi.org/10.1016/j.
jclepro.2019.119479.
[6] Canals Casals L, Martinez-Laserna E, Amante García B, Nieto N. Sustainability
analysis of the electric vehicle use in Europe for CO2 emissions reduction. J Clean
Prod 2016;127:425–37. https://doi.org/10.1016/j.jclepro.2016.03.120.
[7] Aziz M, Oda T, Mitani T, Watanabe Y, Kashiwagi T. Utilization of Electric Vehicles
and Their Used Batteries for Peak-Load Shifting. Energies 2015;8:3720–38. https://
doi.org/10.3390/en8053720.
[8] Xi X, Sioshansi R. Quantifying the Energy-Storage Benefits of Controlled Plug-in
Electric Vehicle Charging. Int J Energy Power 2016;5:26. https://doi.org/10.143
55/ijep.2016.05.004.
[9] Bellan R. The Grim State of Electric Vehicle Adoption in the U.S. CityLab 2018.
[10] Nazari F, Rahimi E, Mohammadian A (Kouros). Simultaneous estimation of battery
electric vehicle adoption with endogenous willingness to pay. ETransportation
2019;1:100008. https://doi.org/10.1016/j.etran.2019.100008.
[11] Hsieh IYL, Pan MS, Chiang YM, Green WH. Learning only buys you so much:
Practical limits on battery price reduction. Appl Energy 2019;239:218–24. https://
doi.org/10.1016/j.apenergy.2019.01.138.
[12] Breetz HL, Salon D. Do electric vehicles need subsidies? Ownership costs for
conventional, hybrid, and electric vehicles in 14 U.S. cities. Energy Policy 2018;
120:238–49.. https://doi.org/10.1016/j.enpol.2018.05.038.
[13] Palmer K, Tate JE, Wadud Z, Nellthorp J. Total cost of ownership and market share
for hybrid and electric vehicles in the UK. US and Japan. Appl Energy 2018;209:
108–19. https://doi.org/10.1016/j.apenergy.2017.10.089.
[14] Elgowainy A, Han J, Ward J, Joseck F, Gohlke D, Lindauer A, et al. Current and
Future United States Light-Duty Vehicle Pathways: Cradle-to-Grave Lifecycle
Greenhouse Gas Emissions and Economic Assessment. Environ Sci Technol 2018;
52:2392–9. https://doi.org/10.1021/acs.est.7b06006.
[15] Hagman J, Ritz´en S, Stier JJ, Susilo Y. Total cost of ownership and its potential
implications for battery electric vehicle diffusion. Res Transp Bus Manag 2016;18:
11–7. https://doi.org/10.1016/j.rtbm.2016.01.003.
[16] Abotalebi E, Scott DM, Ferguson MR. Can Canadian households benefit
economically from purchasing battery electric vehicles? Transp Res Part D Transp
Environ 2019;77:292–302. https://doi.org/10.1016/j.trd.2019.10.014.
[17] Moon S, Lee DJ. An optimal electric vehicle investment model for consumers using
total cost of ownership: A real option approach. Appl Energy 2019;253:113494.
https://doi.org/10.1016/j.apenergy.2019.113494.
[18] Desai RR, Chen RB, Hittinger E, Williams E. Heterogeneity in Economic and Carbon
Benefits of Electric Technology Vehicles in the US. Environ Sci Technol 2020;54:
1136–46. https://doi.org/10.1021/acs.est.9b02874.
[19] Shi X, Pan J, Wang H, Cai H. Battery electric vehicles: What is the minimum range
required? Energy 2019;166:352–8. https://doi.org/10.1016/j.
energy.2018.10.056.
[20] Lewis AM, Kelly JC, Keoleian GA. Vehicle lightweighting vs. electrification: Life
cycle energy and GHG emissions results for diverse powertrain vehicles. Appl
Energy 2014;126:13–20.. https://doi.org/10.1016/j.apenergy.2014.03.023.
[21] Kleiner M, Geiger M, Kleiner M, Geiger M, Klaus A. Manufacturing of Lightweight
Components by Metal Forming 2003. https://doi.org/10.1016/S0007-8506(07)
60202-9.
[22] Kim HJ, McMillan C, Keoleian GA, Skerlos SJ. Greenhouse Gas Emissions Payback
for Lightweighted Vehicles Using Aluminum and High-Strength Steel. J Ind Ecol
2010;14:929–46. https://doi.org/10.1111/j.1530-9290.2010.00283.x.
[23] Zanchi L, Delogu M, Ierides M, Vasiliadis H. Life cycle assessment and life cycle
costing as supporting tools for EVs lightweight design. Smart Innov. Syst. Technol.,
vol. 52, Springer Science and Business Media Deutschland GmbH; 2016, p. 335–48.
https://doi.org/10.1007/978-3-319-32098-4_29.
[24] Egede P. Electric Vehicles, Lightweight Design and Environmental Impacts,
Springer. Cham 2017:9–40. https://doi.org/10.1007/978-3-319-40277-2_2.
[25] Kelly JC, Sullivan JL, Burnham A, Elgowainy A. Impacts of Vehicle Weight
Reduction via Material Substitution on Life-Cycle Greenhouse Gas Emissions.
Environ Sci Technol 2015;49:12535–42. https://doi.org/10.1021/acs.
est.5b03192.
[26] Ducker. Event Recap: Global Automotive Lightweighting Summit 2019 -
DuckerFrontier n.d. https://www.duckerfrontier.com/insights/global-automotivelightweighting/ (accessed March 16, 2020).
[27] Goldie-Scot L. A Behind the Scenes Take on Lithium-ion Battery Prices | Bloomberg
NEF. BloombergNEF 2019.
[28] Eia. Transportation sector energy consumption Figure 8-1. Delivered
transportation energy consumption by country grouping, 2012-40 (quadrillion
Btu). n.d.
[29] Lipman TE. Manufacturing and lifecycle costs of battery electric vehicles, directhydrogen fuel cell vehicles, and direct-methanol fuel cell vehicles. Proc. Intersoc.
Energy Convers. Eng. Conf., vol. 2, IEEE; 2000, p. 1352–8. https://doi.org/
10.1109/iecec.2000.870950.
[30] Price B, Dietz E, Richardson J. Life cycle costs of electric and hybrid electric vehicle
batteries and End-of-Life uses. IEEE Int. Conf. Electro Inf. Technol. 2012. https://
doi.org/10.1109/EIT.2012.6220712.
[31] Cuenca RM, Gaines LL, Vyas AD. Evaluation of electric vehicle production and
operating costs. Argonne, IL (United States) 2000. https://doi.org/10.2172/
764206.
[32] Kim HJ, Keoleian GA, Skerlos SJ. Economic Assessment of Greenhouse Gas
Emissions Reduction by Vehicle Lightweighting Using Aluminum and HighStrength Steel. J Ind Ecol 2011;15:64–80. https://doi.org/10.1111/j.1530-
9290.2010.00288.x.
[33] Luk JM, Kim HC, De Kleine R, Wallington TJ, MacLean HL. Review of the Fuel
Saving, Life Cycle GHG Emission, and Ownership Cost Impacts of Lightweighting
Vehicles with Different Powertrains. Environ Sci Technol 2017;51:8215–28.
https://doi.org/10.1021/acs.est.7b00909.
[34] Wu D, Guo F, Field FR, De Kleine RD, Kim HC, Wallington TJ, et al. Regional
Heterogeneity in the Emissions Benefits of Electrified and Lightweighted LightDuty Vehicles. Environ Sci Technol 2019;53:10560–70. https://doi.org/10.1021/
acs.est.9b00648.
[35] EDAG. Future Steel Vehicle - Phase 2 Report. Southfield, MI: 2011.
[36] Farooq MA, Roth R, Kirchain R. Lightweighting technologies: Analyzing strategic
and economic implications of advanced manufacturing processes. Int J Prod Econ
2018;206:268–79. https://doi.org/10.1016/j.ijpe.2018.10.003.
[37] Kirchain RE, Field FR. MODELING FEATURES OF COST. 2001.
[38] Malen DE, Hughes J. Mass Benchmarking Using Statistical Methods Applied to
Automotive Closures. SAE Int J Mater Manuf 2015;8:853–63. https://doi.org/
10.2307/26268781.
[39] Kochhan R, Fuchs S, Reuter B, Burda P, Matz S, Lienkamp M. An Overview of Costs
for Vehicle Components, Fuels and Greenhouse Gas Emissions. n.d.
[40] Akafuah N, Poozesh S, Salaimeh A, Patrick G, Lawler K, Saito K. Evolution of the
Automotive Body Coating Process—A Review. Coatings 2016;6:24. https://doi.
org/10.3390/coatings6020024.
[41] Hilt M. Automotive painting processes - today and tomorrow Introduction - Closed
chain in painting technology due to integration of FPL (research institute) into
Introduction -. Coating components Solvents Paint Additives Pigments Binders
2011.
[42] Fundamentals of Automobile Body Structure Design n.d. https://www.sae.org/
publications/books/content/r-394/ (accessed February 28, 2020).
[43] Malen D. Mass Benchmarking Analysis of Battery Electric Vehicles. 2018.
[44] Materials Benedyk JC. Design, and Manufacturing for Lightweight Vehicles.
Woodhead Publishing Limited 2010. https://doi.org/10.1533/
9781845697822.1.79.
[45] Mao T, Altan T. Aluminum sheet forming for automotive applications. Stamp J:
Part I; 2013.
[46] Malen DE, Gobbels ¨ R, Wohlecker R. Estimation of secondary mass changes in
vehicle design. SAE Int J Mater Manuf 2013;6:174–83. https://doi.org/10.4271/
2013-01-0655.
[47] Nelson PA, Gallagher KG, Bloom I, Dees DW. Modeling the Performance and Cost
of Lithium-Ion Batteries for Electric-Drive Vehicles. 2011.
[48] Dai Q, Kelly JC, Dunn JB, Benavides PT. Update of Bill-of-materials and Cathode
Materials Production for Lithium-ion Batteries in the GREET. Model 2018.
[49] Ahmed S, Trask SE, Dees DW, Nelson PA, Lu W, Dunlop AR, et al. Cost of
automotive lithium-ion batteries operating at high upper cutoff voltages. J Power
Sources 2018;403:56–65. https://doi.org/10.1016/j.jpowsour.2018.09.037.
[50] Berg EJ, Villevieille C, Streich D, Trabesinger S, Novak ´ P. Rechargeable Batteries:
Grasping for the Limits of Chemistry. J Electrochem Soc 2015;162:A2468–75.
https://doi.org/10.1149/2.0081514jes.
[51] Patry G, Romagny A, Martinet S, Froelich D. Cost modeling of lithium-ion battery
cells for automotive applications. Energy Sci Eng 2015;3:71–82. https://doi.org/
10.1002/ese3.47.
[52] Safoutin M, McDonald J, Ellies B. Predicting the Future Manufacturing Cost of
Batteries for Plug-In Vehicles for the U.S. Environmental Protection Agency (EPA)
2017–2025 Light-Duty Greenhouse Gas Standards. World Electr Veh J 2018;9:42..
https://doi.org/10.3390/wevj9030042.
[53] Mechler GC. Manufacturing and Cost Analysis for Aluminum and Copper Die Cast
Induction Motors for GM’s Powertrain and R&D Divisions. 2010.
[54] Ford’s Crown Jewel, the F-150, Has a Big Problem - Bloomberg n.d. https://www.
bloomberg.com/news/articles/2016-06-16/ford-s-crown-jewel-the-f-150-has-abig-problem-after-overhaul (accessed February 28, 2020).
[55] WorldSteel. STEEL IN AUTOMOTIVE | worldsteel. WorldSteel Assoc 2019. https://
www.worldsteel.org/steel-by-topic/steel-markets/automotive.html (accessed
February 28, 2020).
[56] Neubauer J, Wood E. The impact of range anxiety and home, workplace, and public
charging infrastructure on simulated battery electric vehicle lifetime utility.
J Power Sources 2014;257:12–20. https://doi.org/10.1016/j.
jpowsour.2014.01.075.
[57] Connecting Electric Vehicles to the Grid for Greater Infrastructure Resilience |
News | NREL n.d. https://www.nrel.gov/news/program/2017/connectingelectric-vehicles-to-the-grid-for-greater-infrastructure-resilience.html (accessed
February 28, 2020).
[58] Esteban M, Portugal-Pereira J. Post-disaster resilience of a 100% renewable energy
system in Japan. Energy 2014;68:756–64. https://doi.org/10.1016/j.
energy.2014.02.045.
[59] Motavalli J. In a Blackout. Nissan: Mitsubishi and Toyota E.V’.s Could Function as
Generators; 2011.
[60] Shi R, Li S, Zhang P, Lee KY. Integration of Renewable Energy Sources and Electric
Vehicles in V2G Network with Adjustable Robust Optimization. Renew Energy
2020;153:1067–80. https://doi.org/10.1016/j.renene.2020.02.027.