XixiDongaHailinYangbXiangzhenZhuaShouxunJiaShow moreAdd to MendeleyShareCite
https://doi.org/10.1016/j.jallcom.2018.09.260Get rights and content
Abstract
A high strength (Yield strength ≥ 320 MPa) and high ductility (Tensile elongation ≥ 10%) die–cast aluminium alloy was first developed. The AlSiCuMgMn alloy processed by high pressure die casting can provide the high yield strength of 321 MPa, the high ultimate tensile strength of 425 MPa and the high ductility of 11.3%, after solution treated at 510 °C for 30 min and aged at 170 °C for 12 h. The alloy demonstrated 150% increase in ductility over the reported most advanced die–cast aluminium alloy, also comparable tensile properties to the 6000 series wrought aluminium alloys but with much lower manufacturing cost. The as–cast microstructure of the alloy mainly contained the primary α1–Al phase solidified in the shot sleeve, the secondary α2–Al phase solidified in the die, the Al–Si eutectic phase and the intermetallic phases Q–Al5Cu2Mg8Si6 and θ–Al2Cu. The intermetallic phases Q and θ were dissolved into the α–Al matrix during solution. Nanoscale precipitates Q′ and θ′ were precipitated from the α–Al matrix for the strengthening of the alloy through ageing treatment. Multiple effects resulted in the high ductility of the alloy.
고강도(항복강도≥320MPa) 및 고연성(인장신율≥10%) 다이캐스트 알루미늄 합금이 최초로 개발되었습니다. 고압 다이캐스팅으로 가공된 AlSiCuMgMn 합금은 510°C에서 30분 동안 용체화 처리되고 170°에서 시효된 후 321MPa의 높은 항복 강도, 425MPa의 높은 극한 인장 강도 및 11.3%의 높은 연성을 제공할 수 있습니다. 12시간 동안 이 합금은 보고된 가장 진보된 다이캐스트 알루미늄 합금에 비해 연성이 150% 증가했으며, 6000 시리즈 단조 알루미늄 합금과 비슷한 인장 특성을 나타내었지만 제조 비용은 훨씬 낮았습니다.
주조된 합금의 미세 구조는 주로 샷 슬리브에서 응고된 1차 α1-Al 상, 다이에서 응고된 2차 α2-Al 상, Al-Si 공융 상 및 금속간 상 Q-Al5Cu2Mg8Si6 및 θ-Al2Cu를 포함했습니다. 금속간 상 Q 및 θ는 용해 중에 α-Al 매트릭스에 용해되었습니다. 시효 처리를 통해 합금을 강화하기 위해 α-Al 매트릭스에서 나노 크기의 침전물 Q' 및 θ'가 침전되었습니다. 여러 가지 효과로 인해 합금의 높은 연성이 발생했습니다.
Graphical abstract

Introduction
High pressure die casting (HPDC) is a near–net shape manufacturing process in which molten metal is injected into a metal mould at high speed and solidified under high pressure. HPDC has been widely used in producing thin wall aluminium and magnesium alloy components with high dimensional accuracy, high production efficiency, and considerable economic benefit for automotive and other industries [[1], [2], [3], [4], [5]]. However, the turbulent flow and the consequent entrapment of air during die filling is an inherent problem for HPDC, which results in the formation of gas porosity in HPDC castings [[6], [7], [8]]. The presentence of gas porosity decreases the possibility of the further strengthening of HPDC castings through heat treatment due to blistering. Therefore, the application of HPDC is normally limited to low strength as–cast non–structural components not requiring heat treatment for strengthening.
Recent development in manufacturing lightweight components requires the die–cast aluminium alloys to be able to provide higher strength and high ductility. High strength and high ductility (Yield strength ≥ 320 MPa, Elongation ≥ 10%) die–cast aluminium alloys are attractive in industry, because they are comparable with the tensile properties of 6000 series wrought aluminium alloys [[9], [10], [11], [12]], but with much lower manufacturing cost. The problem is that the as–cast tensile properties of the currently available die–cast aluminium alloys are usually low, with a yield strength of 130–170 MPa and an elongation of 3–5% [13]. Explorations were done to develop die–cast aluminium alloys with higher as–cast strength [[14], [15], [16], [17], [18]]. Hu et al. [14] reported a die–cast Al–Mg–Si–Mn alloy with a yield strength of 183 MPa. Zhang et al. [15] developed an Al–5Mg–0.6Mn die–cast alloy with a yield strength of 212 MPa. However, the as–cast yield strength of the currently developed die–cast aluminium alloys is still around the low level of 200 MPa [15,18].
The successful development of the vacuum assisted HPDC has provided the capability of producing castings with much reduced gas porosities, which enables the further strengthening of the as–cast heat treatable die–cast alloys through heat treatment [[19], [20], [21], [22], [23], [24]]. Ji et al. [13,25] developed a high strength Al–10Mg–3.5Zn–3Si die–cast alloy exhibited the yield strength of 320 MPa, the UTS of 420 MPa and the tensile elongation of 4.5% after solution and ageing heat treatment. The tensile elongation of 4.5% was the highest reported ductility in association with a high yield strength of 320 MPa for die–cast aluminium alloys processed by HPDC. Die–cast aluminium alloy with both high yield strength above 320 MPa and high ductility over 10% is still unachievable.
The objective of the present work is to develop a die–cast aluminium alloy to achieve the high yield strength above 320 MPa and the high ductility over 10%. HPDC was applied for the processing of the alloy. The microstructure, mechanical properties and the strengthening mechanism of the alloy under as–cast and heat treatment condition were investigated.
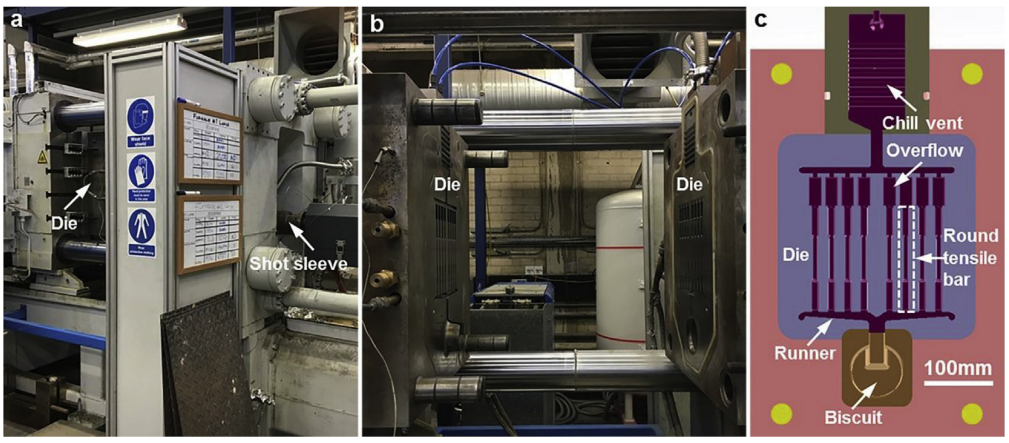
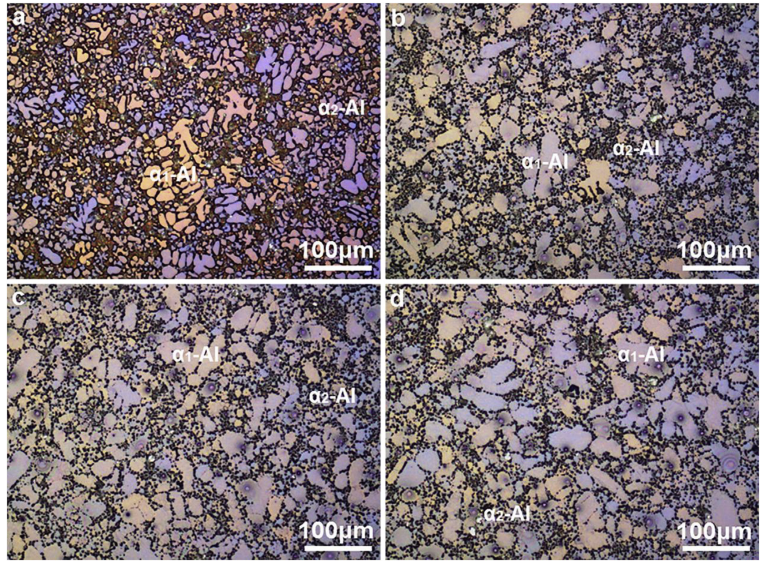
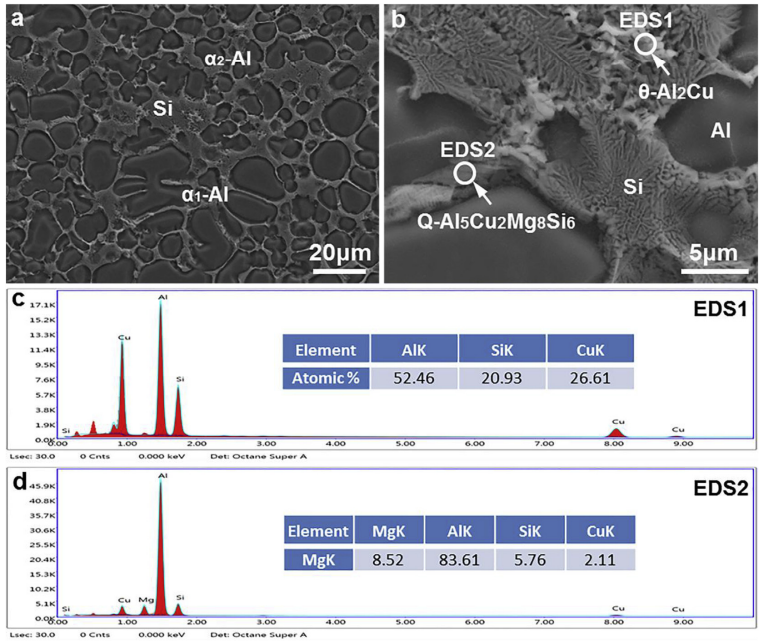
Materials and melt preparation
The AlSiCuMgMn die–cast alloy, with the actual composition of 8.82 wt%Si, 1.71 wt%Cu, 0.40 wt%Mg, 0.50 wt%Mn, 0.18 wt%Fe, 0.13 wt%Ti and balanced Al, was melted in a 15–kg capacity clay–graphite crucible using an electric resistance furnace. During melting, the temperature of the furnace was controlled at 750 °C, and a melt of 10 kg was prepared. The melt was held for one hour to ensure the good homogenisation of the composition, since the melt was prepared based on the addition and melting of
OM microstructure
Fig. 2(a) shows the polarized optical micrograph of the as–cast AlSiCuMgMn alloy processed by HPDC. Two kinds of α–Al phase with different size were found in the as–cast alloy, i.e., the primary α1–Al phase solidified in the shot sleeve and the secondary α2–Al phase solidified in the die cavity. The size of the α2–Al phase is much finer than that of the α1–Al phase, due to the higher cooling rate in the die cavity. Fig. 2(b), (c) and (d) show the polarized optical micrographs of the AlSiCuMgMn
Conclusions
(1)
Die–cast AlSiCuMgMn alloy containing 8.8 wt%Si, 1.7 wt%Cu, 0.4 wt%Mg and 0.5 wt%Mn was developed. The tensile properties of the alloy under as–cast condition are 189 MPa of yield strength, 372 MPa of ultimate tensile strength, and 8.0% of elongation. The tensile properties of the alloy are 211 MPa of yield strength, 391 MPa of ultimate tensile strength, and 20.7% of elongation, after solution treatment.(2)
The AlSiCuMgMn die–cast alloy can provide the high yield strength of 321 MPa, the high
Acknowledgements
Financial support from Innovate UK under project 131817 is gratefully acknowledged.
References (36)
- C.H. Cáceres et al.Casting defects and the tensile properties of an Al–Si–Mg alloyMater. Sci. Eng. A(1996)
- M.K. Surappa et al.Effect of macro–porosity on the strength and ductility of cast Al–7Si–0.3Mg alloyScr. Metall.(1986)
- S.G. Lee et al.Quantitative fractographic analysis of variability in the tensile ductility of high–pressure die–cast AE44 Mg–alloyMater. Sci. Eng. A(2006)
- S.G. Lee et al.Variability in the tensile ductility of high–pressure die–cast AM50 Mg–alloyScr. Mater.(2005)
- A. Biswas et al.Compositional evolution of Q-phase precipitates in an aluminum alloyActa Mater.(2014)
- X.X. Dong et al.High performance gravity cast Al9Si0.45Mg0.4Cu alloy inoculated with AlB2 and TiB2J. Mater. Process. Technol.(2018)
- J.Y. Hwang et al.The effect of Mg on the structure and properties of type 319 aluminum casting alloysActa Mater.(2009)
- Q. Xiao et al.Effect of Cu content on precipitation and age-hardening behavior in Al-Mg-Si-xCu alloysJ. Alloys Compd.(2017)
- X.X. Dong et al.Enhancement of mechanical properties in high silicon gravity cast AlSi9Mg alloy refined by Al3Ti3B master alloyMater. Sci. Eng. A(2017)
- F. Yan et al.Effect of solutionising and ageing on the microstructure and mechanical properties of a high strength die-cast Al–Mg–Zn–Si alloyMater. Chem. Phys.(2015)
View more references
Cited by (56)
- Effect of ageing and thermal exposure on microstructure and mechanical properties of a HPDC Al–Si–Cu–Mg alloy2022, Materials Science and Engineering AShow abstract
- The evolution of microstructure, micromechanical and magnetic properties of FeCoNiSi alloys solidified under high pressure2022, Materials CharacterizationShow abstract
- Understanding of surface segregation of Cu and Zn on nano Si precipitates to the mechanical property improvement of high pressure die casting Al9Si3CuFe alloy2022, Journal of Alloys and CompoundsShow abstract
- Microstructures, mechanical properties and solidification mechanism of a hot tearing sensitive aluminum alloy asymmetric part fabricated by squeeze casting2021, Journal of Alloys and CompoundsShow abstract
- Influence of in-flight particle characteristics and substrate temperature on the formation mechanisms of hypereutectic Al-Si-Cu coatings prepared by supersonic atmospheric plasma spraying2021, Journal of Materials Science and TechnologyShow abstract
- Effect of temperature on the mechanical properties of Al–Si–Cu–Mg–Ni–Ce alloy2021, Materials Science and Engineering AShow abstract