This introductory paper is the research content of the paper "Final Report on Refining Technologies of Aluminum" published by Government of Canada.
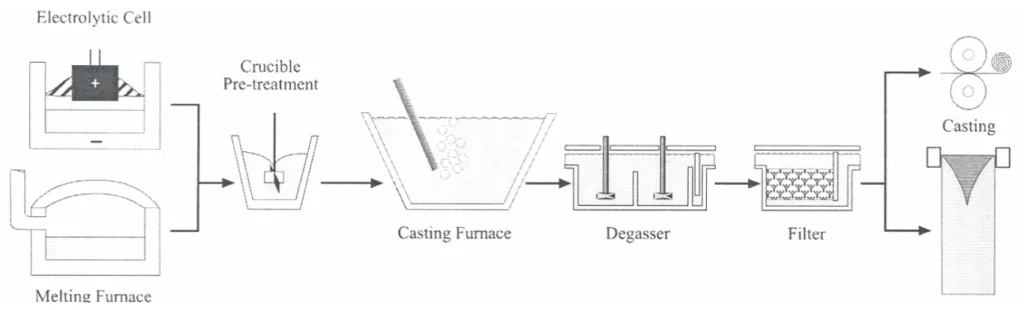
1. Overview:
- Title: Final Report on Refining Technologies of Aluminum
- Author: S. Bell B. Davis, A. Javaid and E. Essadiqi
- Publication Year: 2003
- Publishing Journal/Academic Society: Government of Canada. Report No. 2003-21(CF).
- Keywords: Aluminum, Refining, Fluxing, Floatation, Filtration, Alkali Metals, Inclusions, Degassing, Rotary Gas Injection, Rotary Flux Injection, Ceramic Foam Filters, Deep Bed Filters.
2. Abstracts / Introduction
Aluminum refining is crucial for meeting the stringent quality demands of industries like automotive. The report details the three primary refining processes: fluxing, floatation, and filtration. These processes are carried out sequentially in the pre-treatment crucible/casting furnace, degasser, and filtration unit. Impurities like alkali metals, non-metallic inclusions, and dissolved hydrogen significantly degrade aluminum's properties. The report focuses on techniques to reduce these impurities.
3. Research Background:
Background of the Research Topic:
The increasing use of aluminum, particularly in the automotive industry, demands higher purity levels. Impurities such as alkali metals (sodium, calcium, lithium), non-metallic inclusions, and dissolved hydrogen compromise the mechanical properties of aluminum alloys.
Status of Existing Research:
Historically, refining involved salt-based fluxes (aluminum chloride) and mechanical puddling. Alcan's Treatment of Aluminum in Crucible (TAC) process improved this with a specialized rotor and aluminum fluoride salt. Gas fluxing using chlorine, introduced via lances, was also developed. Rotary Gas Injection (RGI) further improved efficiency.
Necessity of the Research:
Existing methods had limitations: puddling was inefficient, lance fluxing had poor stirring and high chlorine emissions, and early solid flux methods couldn't meet commercial cleanliness standards. Stricter environmental regulations also demanded reduced chlorine use.
4. Research Purpose and Research Questions:
Research Purpose:
To summarize and evaluate the existing and emerging technologies for refining molten aluminum, focusing on their effectiveness in removing various impurities and their environmental impact.
Key Research:
To describe of below key research.
- Review and comparing fluxing methods (salt-based, lance, RGI, RFI).
- Examining the floatation process in degassing.
- Evaluating filtration techniques and filter types.
5. Research Methodology
Research Design:
Literature review and analysis of existing refining technologies.
Data Collection Method:
Review of published papers, patents, and technical reports.
Analysis Method:
Qualitative comparison and synthesis of information on different refining methods.
Research Subjects and Scope:
The scope includes pre-treatment, degassing, and filtration processes used in aluminum cast houses, focusing on impurity removal and process efficiency.
6. Main Research Results:
Key Research Results:
- Fluxing:
- Salt-Based: TAC process uses AlF3 and a rotor for efficient alkali and oxide removal in a pre-treatment crucible. RFI uses reactive salts (MgCl2 or AlF3) and a rotor, offering reduced chlorine emissions and high efficiency.
- Lance Fluxing: Uses chlorine gas, but is less efficient than RGI due to large bubble size and poor stirring.
- Rotary Gas Injection (RGI): Uses a high-shear gas disperser, significantly improving alkali removal rates and reducing chlorine consumption.
- Rotary Flux Injection(RFI): The effectiveness of MgCl2 in removing alkali species was determined by Celik et al.
- Floatation (Degassing): Uses a mixture of argon and chlorine to remove hydrogen. The Alcan Compact Degasser (ACD) reduces metal retention issues.
- Filtration: Ceramic foam filters (CFF) and deep bed filters are common. CFFs are suitable for small-scale, multi-alloy operations, while deep bed filters are more efficient but suited for large-scale, single-alloy use.
Analysis of presented data:
- Table 1: Shows typical impurity levels in primary and secondary aluminum.
- Fig. 1: Illustrates the sequence of molten aluminum processing steps.
- Fig. 2: Compares the calcium removal rate of different fluxing methods, highlighting RGI's superior performance.
- Fig. 3: Hydrogen removal to gas bubbles in a degasser.
- Fig. 4: Schematic representation of a multi-rotor compact degassing unit.
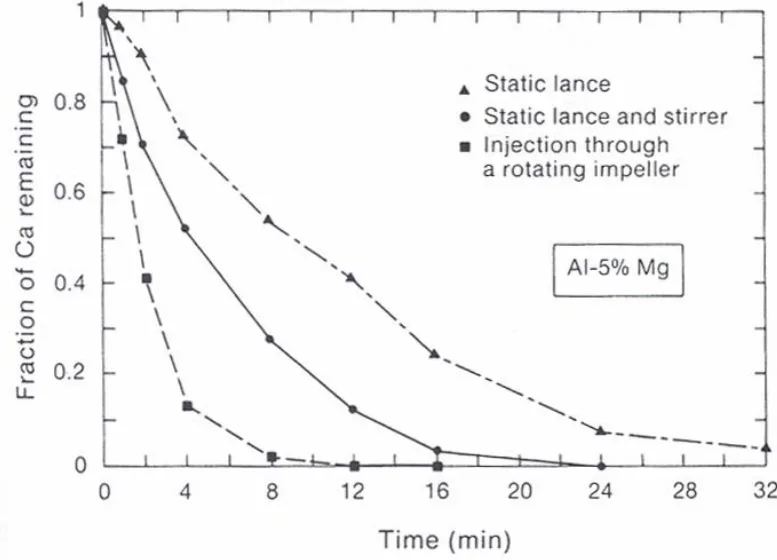
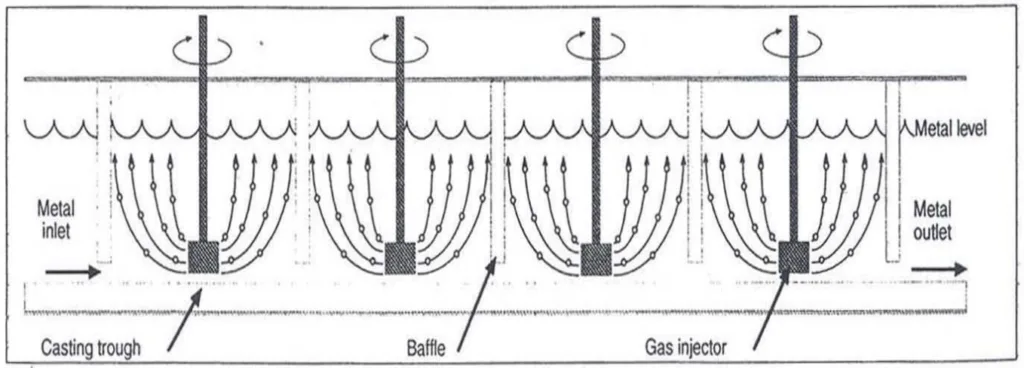
Figure Name List:
- Fig. 1 - Sequence of molten aluminum processing steps.
- Fig. 2 - Removal rate of calcium using various fluxing processes.
- Fig. 3 - Hydrogen removal to gas bubbles in a degasser.
- Fig. 4 - Schematic representation of a multi-rotor compact degassing unit.
7. Conclusion:
Summary of Key Findings:
- RFI is the most efficient and environmentally friendly solid-flux method.
- RGI is the most effective gas-flux technique, reducing chlorine use compared to lance fluxing.
- Degassing requires chlorine for optimal hydrogen removal, but magnesium chloride formation is a concern in Al-Mg alloys.
- CFFs and deep-bed filters are the main filtration methods, each with advantages and disadvantages depending on the application.
Academic Significance of the Study:
Provides a comprehensive overview of aluminum refining technologies, consolidating information from various sources.
Practical Implications:
Highlights the benefits of RFI and RGI for improved efficiency and reduced environmental impact. Informs choices about filtration methods based on operational needs.
Limitations of the Study and Areas for Future Research:
- The study is based on a literature review up to 2003; newer technologies may exist.
- Limited information was available on some specific processes (e.g., chlorine-free degassing).
- Future research should focus on chlorine-free degassing methods and optimizing filtration for specific impurity profiles. The need for research into depth filtration mechanisms is emphasized.
8. References:
- [1] Gesing and R. Wolanski, “Recycling Light Metals from End-of-Life Vehicles,” JOM, (2001), pp. 21-23.
- [2] P. Waite, “A Technical Perspective on Molten Aluminum Processing,” Light Metals, (2002), pp. 842.
- [3] G. Dube, and V. Newberry, “TAC-A Novel Process for the Removal of Lithium and other Alkalis in Primary Aluminum,” Light Metals, (1990), pp. 991-1003.
- [4] Rasch, E. Myrbostad, and K. Hafas, “Refining of Potroom Metal Using the Hydro RAM Crucible Fluxing Process,” Light Metals, (1998), pp. 851-854.
- [5] F. Achard and C. Leroy, “Pre-treatment in Potlines Crucibles: The Mixal Process,” Light Metals, (1990), pp. 765-768.
- [6] J. Edwards, F. Frary, and Z. Jeffries, “The Aluminum Industry – Aluminum Products and their Fabrication,” Chemical Engineering Series, (1930), pp. 284.
- [7] W. Hyatt, British Patent 8 801, (1901).
- [8] Tullis, “Cindal-A New Aluminum Alloy,” The Metal Industry, (1928), 31, pp. 487.
- [9] Celik and D. Doutre, “Theoretical and Experimental Investigation of Furnace Chlorine Fluxing,' Light Metals, (1988), pp. 793-800.
- [10] M. Nilmani, “Aluminum Melt Gas Fluxing by Helical Plug Lance, Aluminum Melt Treatment and Casting – Theory and Practice,” Proceedings of the Second Australian Asian Pacific Course and Conference on Aluminum Melt Treatment and Casting, (1991), pp. 6:1-6:10.
- [11] J. Guttery, “A Two Year User's Experience with Porous Plugs Fluxing in a Modern Casting Facility”, Light Metals, (1993), pp. 899-905.
- [12] J. Guttery and W. Evans, “A New Generation of Fluxing in Aluminum Melting and Holding Furnaces", Light Metals, (1994), pp. 921-927.
- [13] J. Bilodeau, C. Lakroni, and Y. Kacaefe, “Modeling of Rotary Injection Process for Molten Aluminum Processing,” Light Metals, (1995), pp. 1189-1195.
- [14] DeYoung, “Salt Fluxes for Alkali and Alkaline Earth Element Removal from Molten Aluminum," Aluminum Cast House Technology, Proceedings of the 7th Australian Asian Pacific Conference, (2001), pp. 99-113.
- [15] Beland, C. Dupuis, and G. Riverin, “Rotary Flux Injection: Chlorine-Free Technique for Furnace Preparation,” Light Metals, (1998), pp. 843-847.
- [16] P. Flisakoski, et al., “Improvements in Cast Shop Processing using Pyrotek's HD-2000 and PHD-50 Rotary Injector System,” Light Metals, (2001), pp. 1041-1047.
- [17] B. Gariepy et al., “Aluminum Ladle Metallurgy (ALM): A New Process for More Efficient Alloy Preparation,” Light Metals, (1988), pp. 452-462.
- [18] P. Waite, “Improved Metallurgical Understanding of the Alcan Compact Degasser After Two Years of Industrial Implementation in Aluminum Casting Plants,” Light Metals, (1998), pp. 791-796.
- [19] J. Buehler and R. Frank, “Startup and Evaluation of the First Snif Sheer System at Kaiser Aluminum, Trentwood Works," Presented at the 122nd TMS Annual Meeting, Denver Colorado, Feb. 24, (1993).
- [20] P. Waite and R. Thiffault, ‘The Alcan Compact Degasser: A Trough-Based Aluminum Treatment Process part 1: Metallurgical Principles and Performance,” Light Metals, (1996), pp. 1001-1005.
- [21] P. Waite, “Improved Metallurgical Understanding of the Alcan Compact Degasser After Two Years of Industrial Implementation in Aluminum Casting Plants,” Light Metals, (1998), pp. 791-796.
- [22] C. English, “The Cast House Trough Reactor A New Concept for Degassing Reactor Design,” Light Metals, (1998), pp. 811-815.
- [23] L. Aubrey et al., “New Product Developments for Aluminum Cast Houses,” Aluminum Cast House Technology, Proceedings of the 7th Australian Asian Pacific Conference, (2001), pp. 23-43.
- [24] Eckert et al., “Molten Salt Coalescence in Molten Aluminum,” US Patent 5122184, (1992).
- [25] Proffitt, "Magnesium and Magnesium Alloys,” Metals Handbook, 9, [2], (1989), pp. 801-802.
9. Copyright:
- This material is S. Bell B. Davis, A. Javaid and E. Essadiqi's paper: Based on "Final Report on Refining Technologies of Aluminum".
- Paper Source: The paper itself does not provide a DOI URL.
This material was created to introduce the above paper, and unauthorized use for commercial purposes is prohibited.
Copyright © 2025 CASTMAN. All rights reserved.