This technical brief is based on the academic paper "Possibilities of reducing the degradation of molds for high-pressure of Al alloys" by Ján Hašul and Janette Brezinová, published in INTERNATIONAL SCIENTIFIC JOURNAL "MACHINES. TECHNOLOGIES. MATERIALS" (2022). It is summarized and analyzed for HPDC professionals by the experts at CASTMAN.
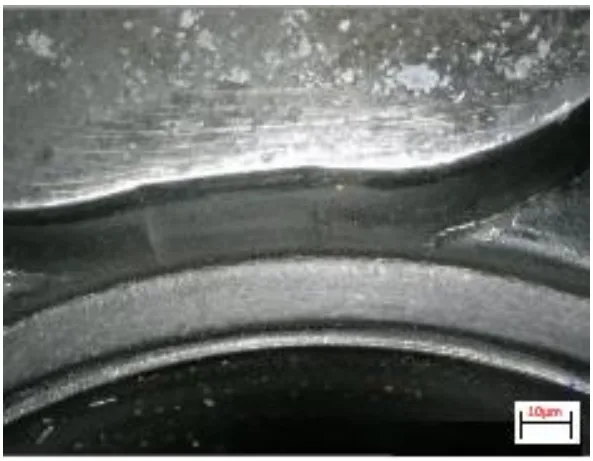
Keywords
- Primary Keyword: PVD Coatings for HPDC Molds
- Secondary Keywords: Aluminum Die Casting, Mold Life Extension, Thermal Fatigue Cracks, nACRo³ Coating, AlXN³ Coating, Mold Surface Treatment, Uddeholm Dievar
Executive Summary
- The Challenge: Molds used in high-pressure aluminum die casting are constantly exposed to severe thermal and mechanical stresses, leading to degradation mechanisms like thermal fatigue, cracking, and erosion, which cause costly production downtime and mold replacement.
- The Method: Researchers analyzed the common failure modes of mold inserts made from H13 tool steel. They then applied and tested two different PVD coatings—a conventional AlXN³ and a nanostructured nACRo³—to evaluate their potential for improving mold durability.
- The Key Breakthrough: The nanostructured nACRo³ PVD coating demonstrated superior performance, significantly increasing surface microhardness by up to 25% (to 810 HV) and showing excellent adhesion. This creates a robust protective barrier against the molten aluminum and the stresses of the casting cycle.
- The Bottom Line: This study confirms that applying advanced PVD coatings, particularly nanostructured variants like nACRo³, is a highly effective, data-driven strategy to combat degradation, extend the operational life of HPDC molds, and improve overall manufacturing efficiency.
The Challenge: Why This Research Matters for HPDC Professionals
In the demanding world of high-pressure die casting (HPDC), the operational lifespan of a mold is a critical economic factor. Molds are subjected to a brutal cycle of high pressure (up to 100 MPa), high temperatures (around 700 °C), and rapid temperature fluctuations. These conditions inevitably lead to primary failure mechanisms that limit a die's life: corrosion, soldering, erosive wear, and, most notably, thermal fatigue.
Thermal fatigue, resulting from the constant heating and cooling of the die surface, causes a network of interconnected cracks to form. These cracks can grow, leading to material loss, dimensional inaccuracies in the cast parts, and eventually, catastrophic mold failure. For decades, engineers have grappled with this problem, as replacing or repairing these complex tools constitutes a significant portion of production costs. This research directly addresses this challenge by investigating a surface treatment solution designed to protect the mold from the very start.
The Approach: Unpacking the Methodology
To find a solution, the researchers took a two-phase approach. First, they analyzed a worn mold insert made of Uddeholm Dievar (a common H13-type hot-work tool steel) to understand the root cause of failure. Using light microscopy, scanning electron microscopy (SEM), and energy-dispersive X-ray spectroscopy (EDX), they examined the cracks that formed in the mold's sharp corners.
Second, they tested a preventative solution. The team applied two different duplex PVD (Physical Vapor Deposition) coatings to the Uddeholm Dievar base material:
- AlXN³: A conventional nano-multilayer coating.
- nACRo³: A next-generation nanocomposite coating composed of AlCrN nanocrystalline grains in an amorphous Si₃N₄ matrix, designed for high-temperature abrasion resistance.
These coated samples were then subjected to rigorous testing to measure their real-world viability, including the Rockwell C indentation test for adhesion and Vickers microhardness tests to quantify the improvement in surface hardness.
The Breakthrough: Key Findings & Data
The study yielded clear, quantitative results demonstrating the effectiveness of PVD coatings.
- Finding 1: Cracking Mechanism Identified: The analysis of the worn mold confirmed that wedge-shaped, branched cracks were the primary mode of failure. These cracks initiated in sharp corners due to cyclic stress and were filled with oxides and release agents from the casting process, which acted as a wedge, propagating the crack with each cycle. This is detailed in Figure 5 and Figure 6 of the paper.
- Finding 2: Excellent Coating Adhesion: Both the AlXN³ and nACRo³ coatings demonstrated "good adhesion" to the steel substrate. In the Rockwell adhesion test (a severe indentation test shown in Figure 7), the coatings achieved a rating of HF 1-2, indicating only minor, isolated radial cracks with no significant peeling or delamination. This proves the coating can withstand significant mechanical stress without flaking off.
- Finding 3: Significant Increase in Surface Hardness: The PVD coatings delivered a substantial boost in surface hardness, a key factor in resisting wear and erosion. Compared to the base material, the AlXN³ coating increased hardness to a maximum of 720 HV. The advanced nACRo³ coating performed even better, reaching a maximum hardness of 810 HV—an increase of approximately 18-25%. The results are clearly visualized in the hardness profile graph in Figure 9.
Practical Implications for Your HPDC Products
Based strictly on the paper's results, these findings have direct, practical implications for manufacturing operations.
- For Process Engineers: The research suggests that proactively applying a nanostructured PVD coating like nACRo³ to new or refurbished molds can create a more durable and resilient surface. This can directly combat the formation of thermal fatigue cracks, potentially extending the intervals between required maintenance and reducing unscheduled downtime.
- For Quality Control: The superior hardness and adhesion of the nACRo³ coating, as shown in Figure 7 and Figure 9, provide a stable and wear-resistant mold surface. This helps maintain the precise geometry of the mold cavity for a longer period, leading to more consistent part quality and dimensional accuracy throughout the mold's extended lifespan.
- For Die Design: This study reinforces a critical design principle. While coatings are a powerful protective layer, the research identified that failure initiates in "zones of sharp transitions" (Figure 5). This implies that the combination of robust PVD coatings with die designs that minimize sharp internal corners is the most effective strategy for maximizing mold life.
Paper Details
Possibilities of reducing the degradation of molds for high-pressure of Al alloys
1. Overview:
- Title: Possibilities of reducing the degradation of molds for high-pressure of Al alloys
- Author: Ján Hašul, Janette Brezinová
- Year of publication: 2022
- Journal/academic society of publication: INTERNATIONAL SCIENTIFIC JOURNAL "MACHINES. TECHNOLOGIES. MATERIALS"
- Keywords: ALUMINUM, DIE CASTING, DEGRADATION, COATINGS, ADHESION, CRACKS
2. Abstract:
The paper focuses on the degradation of molds used for the technology of high-pressure casting of Al and its alloys. The method of high-pressure casting of aluminum products is one of the widely used production methods, which at the same time meets the requirements for precision and productivity in the production of cars and various mechanical parts. In the high-pressure casting process, the molds are exposed to various thermal and mechanical loads, where the molds and their shaped parts are degraded. The paper presents the results of research focused on the use of duplex PVD coatings to increase the life of shaped parts of molds for high-pressure casting of Al and its alloys.
3. Introduction:
The high-pressure die casting process is used to produce parts from aluminum, magnesium, zinc, and copper alloys. The molds endure severe conditions, including high pressure, rapid temperature fluctuations, and erosion from molten metal moving at 20-60 m/s. These conditions lead to failure mechanisms like erosion, corrosion, wear, and thermal fatigue, which limit the die's lifespan. Thermal fatigue, in particular, causes a network of cracks, leading to costly die maintenance and replacement. Surface treatments, such as nitriding and PVD coatings, have been developed to improve thermal fatigue resistance and reduce wear, with studies showing PVD coatings can increase service life by 4 to 17 times.
4. Summary of the study:
Background of the research topic:
Molds for high-pressure die casting of aluminum alloys suffer from degradation due to severe operating conditions. This degradation limits the lifetime of the molds, which is a significant economic and environmental issue.
Status of previous research:
Previous research has identified the primary failure mechanisms (corrosion, soldering, erosion, thermal fatigue) and has explored various surface treatments to mitigate them. Hard PVD coatings based on nitrides and carbides (e.g., TiN, CrN) and duplex treatments have been shown to significantly increase service life.
Purpose of the study:
The study aimed to analyze the degradation mechanisms of mold inserts in detail and to investigate the effectiveness of applying a conventional (AlXN³) and a new-generation nanostructured (nACRo³) PVD coating to improve the quality and lifespan of the mold's functional surfaces.
Core study:
The core of the study involved two parts: 1) A failure analysis of a worn mold insert, identifying the formation and cause of wedge-shaped cracks. 2) A comparative analysis of two PVD coatings (AlXN³ and nACRo³) applied to the mold base material, evaluating their adhesion and microhardness as key performance indicators.
5. Research Methodology
Research Design:
The research was designed as an experimental study. It began with a failure analysis of an existing worn mold part and then moved to a comparative evaluation of two different PVD coatings applied to a standardized base material.
Data Collection and Analysis Methods:
The base material was Uddeholm Dievar tool steel. Failure analysis was conducted using light microscopy and a Jeol JSM 7000F scanning electron microscope (SEM) with an EDX unit. Coating adhesion was evaluated using the Rockwell C indentation test (Mercedes test) according to ISO 18265. Microhardness was measured using a Leco LM 700 tester with a Vickers indenter (HV 0.025) per ISO 6507-1. Tribological properties were assessed with a scratch test on a CSEM-Revertest device.
Research Topics and Scope:
The research focused on molds for high-pressure casting of aluminum alloys, specifically an Al-Si-Cu based alloy. The scope included analyzing crack formation on worn molds and quantifying the improvement in adhesion and microhardness provided by AlXN³ and nACRo³ PVD coatings.
6. Key Results:
Key Results:
The study found that wedge-shaped cracks form in sharp corners of the mold due to cyclic stress. It confirmed that both AlXN³ and nACRo³ PVD coatings have good adhesion to the H13 steel substrate. Crucially, the coatings significantly increased surface microhardness, with the nACRo³ nanocomposite coating showing a higher maximum hardness (810 HV) than the conventional AlXN³ coating (720 HV).
Figure Name List:
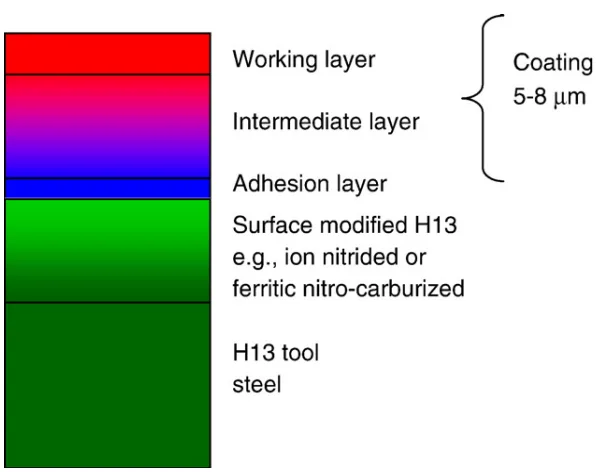

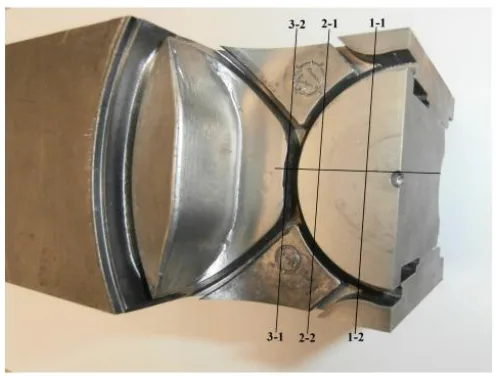
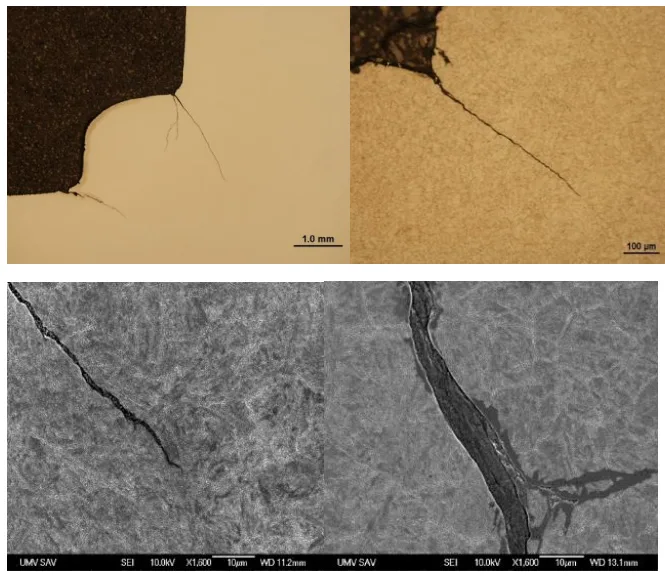
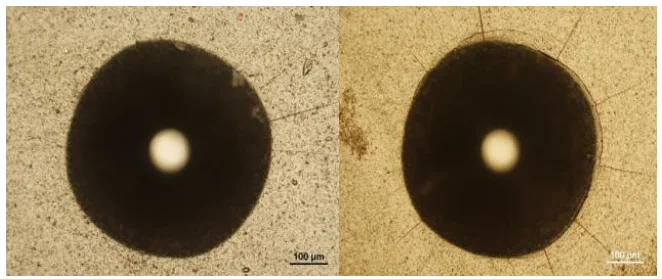
- Fig.1 Degradation of the mold part
- Fig.2 A diagram of an optimized coating architecture for die coatings used in aluminum high pressure die-casting.
- Fig.3 Sampling procedure from the mold part
- Fig.4 Worn solid half of the mold insert (left); appearance of cracks by capillary method (right)
- Fig.5 Cracks in the zones of sharp transitions of the surfaces of shaped parts of the mold (light and electron microscopy)
- Fig.6 Zone of sharp transitions of the surfaces of the shaped parts of the mold
- Fig.7 Indentation impression after Mercedes test; AIXN³ (left), nACRo³ (right)
- Fig.8 Dependence of acoustic emissions (AE) on the coefficient of friction (COF) of coatings
- Fig.9 Graph of measured microhardness values
7. Conclusion:
The paper concludes that PVD nanostructured coatings are an effective method for modifying the functional surfaces of molds for high-pressure aluminum die casting. The degradation mechanism of branched cracks due to elastic deformation was analyzed. The study successfully applied and tested a conventional AlXN3 coating and a new-generation nanostructured nACRo3 coating. Tests confirmed the high quality of the PVD coatings, showing they were compact, intact, and formed a protective barrier, with good adhesion and increased hardness.
8. References:
- D. Abid, A. Ktari, D. Mellouli, N. Gafsi, N. Haddar: Failure analysis of shot-sleeves used in brass high pressure die-casting process, In: Engineering Failure Analysis, 2019, Volume 104, pp. 177-188
- V. Nunes, F.J. Silva, M.F. Andrade, R. Alexandre, A.P.M. Baptista: Increasing the lifespan of high-pressure die cast molds subjected to severe wear, In: Surface & Coatings Technology, 2017, Volume 332, pp. 319-331
- S. H. Kang, J.J. Han, W.T. Hwang, S.M. Lee, H.K. Kim: Failure analysis of die casting pins for an aluminum engine block, In: Engineering Failure Analysis, 2019, Volume 104, pp. 690-703
- D. Mellouli, N. Haddar, A. Koster, H.F. Ayedi: Thermal fatigue failure of brass die - casting dies, In: Engineering Failure Analysis, 2012, Volume 20, pp. 137-146
- J. Wang et.al.: On the failure mechanism for high pressure die casting A390 hypereutectic alloy in low cycle and high cycle fatigue, In: Materials Science & Engineering A, 2018, Volume 723, pp. 48-55
- R. Ding et.al.: Failure analysis of H13 steel die for high pressure die casting Al alloy, In. Engineering Failure Analysis, 2021, Volume 124, pp. 105330
- J. Lin et.al.: Design methodology for optimized die coatings: The case for aluminum pressure die-casting, In: Surface & Coating Technology, 2006, Volume 201, pp. 2930-2941, Elsevier
- K. Bobzin, et. al: Analysis of CrN/AIN/Al2O3 and two industrially used coatings deposited on die castings cores after application in an aluminum die casting machine, In: Surface & Coating Technology, 2016, Volume 308, pp. 374-382, Elsevier
- B. Wang, et.al.: Method to evaluate the adhesion behaviour of aluminum-based alloys on various materials and coatings for lube-free die casting, In: Journal of Materials Processing Technology 2016, Volume 237, pp. 386-393, Elsevier
Expert Q&A: Your Top Questions Answered
Q1: What was the single most critical factor identified in this study for improving mold durability?
A1: The study concluded that modifying the quality of the mold's functional surfaces by applying a high-quality, nanostructured PVD coating like nACRo3 was the most critical factor. This is detailed in the "Conclusions" section, which highlights the coating's ability to form a compact, intact barrier with high hardness and adhesion.
Q2: How does this research compare to traditional methods for addressing mold degradation?
A2: The paper’s Introduction
mentions traditional reactive maintenance like grinding or welding when surface quality is no longer sufficient. In contrast, the PVD coating approach investigated here is a proactive surface treatment designed to prevent degradation from occurring, with the paper noting that PVD coatings can increase service life "several times (4 to 17 times)" compared to uncoated dies.
Q3: Is this finding applicable to all types of alloys, or a specific one?
A3: The research, as described in the Abstract
and Materials and Methods
sections, was specifically conducted for molds used in the high-pressure casting of Al and its alloys, with testing involving an Al-Si-Cu based alloy. The mold material itself was Uddeholm Dievar, a hot-work tool steel. Applicability to other die materials or cast alloys would require further investigation.
Q4: What specific measurement or simulation technique did the researchers use to arrive at this conclusion?
A4: The researchers utilized the Rockwell C indentation test, also known as the Mercedes test, to evaluate coating adhesion and a Vickers microhardness tester (HV 0.025) to quantify the increase in surface hardness. These physical tests, explained in the Materials and Methods
and Adhesion of PVD coatings
sections, provided the quantitative data to support the conclusions.
Q5: According to the paper, what is the main limitation or area for future research?
A5: The paper focuses on the material science and properties of the coatings themselves and does not detail their performance over a long-term production run in a manufacturing facility. The Acknowledgments
section mentions a related project on "laser weld overlaying," suggesting that restorative techniques are another area of focus for future work.
Q6: What is the direct, practical takeaway from this paper for a die casting facility?
A6: The core takeaway is that by applying a nanostructured PVD coating like nACRo³ to mold inserts, it is possible to significantly increase surface hardness and ensure excellent adhesion, which directly combats the primary wear and cracking mechanisms in aluminum die casting. This is a practical strategy for extending mold life and improving production stability, a conclusion strongly supported by the overall results of the paper, "Possibilities of reducing the degradation of molds for high-pressure of Al alloys".
Conclusion & Next Steps
This research provides a valuable roadmap for enhancing mold durability in aluminum HPDC operations. The findings offer a clear, data-driven path toward improving quality and reducing the costly impact of mold degradation. By demonstrating the superior hardness and adhesion of nanostructured PVD coatings, the study highlights a powerful tool for any manufacturer looking to optimize production and gain a competitive edge.
At CASTMAN, we are dedicated to applying the latest industry research to solve our customers' most challenging die casting problems. If the issues discussed in this paper resonate with your operational goals, contact our engineering team to discuss how we can help you implement these advanced principles in your components.
Copyright
- This material is a paper by "Ján Hašul, Janette Brezinová". Based on "Possibilities of reducing the degradation of molds for high-pressure of Al alloys".
- Source of the paper: The paper does not list a specific DOI URL, but it was published in INTERNATIONAL SCIENTIFIC JOURNAL "MACHINES. TECHNOLOGIES. MATERIALS", YEAR XVI, ISSUE 4, P.P. 123-126 (2022).
This material is for informational purposes only. Unauthorized commercial use is prohibited.
Copyright © 2025 CASTMAN. All rights reserved.