This introduction paper is based on the paper "Experimental and Numerical Study of an Automotive Component Produced with Innovative Ceramic Core in High Pressure Die Casting (HPDC)" published by "Metals (MDPI)".
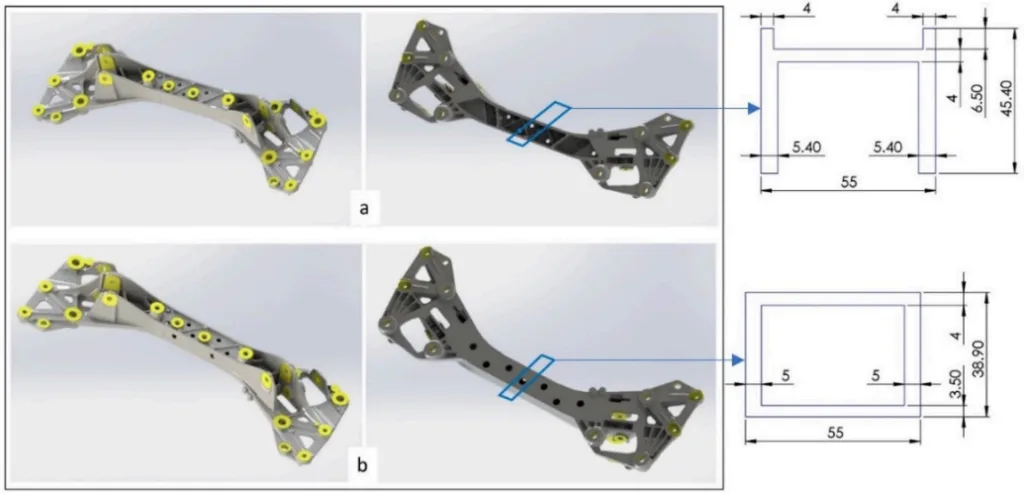
1. Overview:
- Title: Experimental and Numerical Study of an Automotive Component Produced with Innovative Ceramic Core in High Pressure Die Casting (HPDC)
- Author: Giovanna Cornacchia, Daniele Dioni, Michela Faccoli, Claudio Gislon, Luigi Solazzi, Andrea Panvini and Silvia Cecchel
- Year of publication: 2019
- Journal/academic society of publication: Metals (MDPI)
- Keywords: non-ferrous alloys; ceramic core; FEA; HPDC; de-coring; material characterization
2. Abstract:
Weight reduction and material substitution are increasing trends in the automotive industry. High pressure die casting (HPDC) is the conventional casting technology for the high volume production of light alloys; it has recently found wide application in the manufacturing of critical components, such as complex and thin geometry automotive parts. However, the major restriction of this affordable technology is the difficulty to design and realize hollow sections or components with undercuts. An innovative way to further increase the competitiveness of HPDC is to form complex undercut shaped parts through the use of new lost cores that are able endure the high pressures used in HPDC. This paper investigates the use of innovative ceramic lost cores in the production of a passenger car aluminum crossbeam by HPDC. Firstly, process and structural simulations were performed to improve the crossbeam design and check the technology features. The results led to the selection of the process parameters and the production of some prototypes that were finally characterized. These analyses demonstrate the feasibility of the production of hollow components by HPDC using ceramic cores.
3. Introduction:
The automotive industry increasingly requires lightweight components to improve vehicle performance, reduce fuel consumption, and lower emissions. High Pressure Die Casting (HPDC) is a competitive technology for high-volume, low-cost, near-net shape aluminum parts. However, HPDC traditionally struggles to produce complex hollow sections or parts with undercuts, which often require metallic moving cores, limiting design freedom compared to lost cores used in gravity casting. Lost cores compatible with the high pressures and flow speeds of HPDC are needed to overcome this limitation. While research exists on salt cores for HPDC, challenges remain. This paper explores the use of innovative ceramic lost cores, produced via injection molding for complex shapes and good tolerances, which resist high HPDC pressures (over 1000 bar) and do not release gas. The study focuses on the redesign, production, and feasibility demonstration of a passenger car aluminum crossbeam using HPDC with these ceramic cores, aiming to achieve benefits like weight reduction, increased torsional stiffness, and reduced production time compared to conventional methods.
4. Summary of the study:
Background of the research topic:
The automotive sector's drive for weight reduction favors light alloys like aluminum. HPDC is a primary manufacturing method for these alloys due to its high productivity and cost-effectiveness. However, producing complex hollow components, which offer superior stiffness-to-weight ratios, is challenging with standard HPDC due to the difficulty of incorporating undercuts and internal cavities using traditional methods (metallic cores) or the incompatibility of conventional lost cores (e.g., sand, salt) with high injection pressures.
Status of previous research:
Previous research explored various expendable cores (sand, salt, metallic, organic materials) for casting processes. Salt cores have received attention for HPDC applications, with studies investigating their strength and process parameters. Patents exist for using soluble cores in HPDC for components like cylinder blocks. However, achieving the required strength and process reliability remains a challenge. Ceramic cores, produced by injection molding, offer potential advantages like good dimensional tolerance, low surface roughness, and absence of gas release during casting, potentially leading to higher mechanical properties. Decoring methods like leaching and high-pressure water jet exist, but removing resistant cores from complex internal cavities needs consideration.
Purpose of the study:
The primary goal was to investigate and demonstrate the feasibility of producing a complex, hollow automotive component (an aluminum passenger car crossbeam) using HPDC combined with innovative ceramic lost cores. This involved redesigning the component, simulating the process and structural performance, producing prototypes, and characterizing both the cores and the final cast part.
Core study:
The study involved redesigning an existing open-profile aluminum crossbeam (EN AC-43500 alloy) into a closed-box section using a ceramic core (Al2O3 + SiO2 + K2O based). Finite Element Analysis (FEA) was used to compare the structural performance (modal analysis, buckling) of the original and modified designs. Computational Fluid Dynamics (CFD) simulations were performed to analyze the HPDC process (filling, solidification, air entrapment) for both designs, considering the thermal properties of the ceramic core. Experimental work included characterizing the ceramic cores (density, decoring methods, mechanical properties via three-point bending) produced with different sintering temperatures. HPDC prototypes were manufactured using the selected core type. Finally, the cast prototypes were characterized through microstructural analysis (OM, SEM/EDS) and Vickers microhardness testing.
5. Research Methodology
Research Design:
The research employed a combination of numerical simulation and experimental validation. An existing automotive crossbeam design was modified to incorporate a hollow section enabled by a ceramic core. Comparative analyses (numerical and implicit experimental) were performed between the original open-profile design and the new closed-profile (boxed) design. The study followed a sequence: component redesign -> numerical simulation (structural FEA and process CFD) -> ceramic core material selection and characterization -> prototype manufacturing via HPDC -> final component characterization.
Data Collection and Analysis Methods:
- Numerical Simulation:
- Structural Analysis (FEA): Performed using Autodesk Simulation® software with parabolic brick elements. Modal analysis (natural frequencies) under free-free and fixed boundary conditions, and buckling analysis under applied force and moment loads were conducted.
- Process Simulation (CFD): Carried out using CastleBody from PiQ2 software, employing a compressible–incompressible dual phase volume of fluid (VOF) formulation. Simulations analyzed mold filling, solidification, air entrapment, and potential defects, considering the thermal properties of both the aluminum alloy (EN AC-43500) and the ceramic core insert. A hexahedral mesh (~1,000,000 cells) with local refinement was used.
- Experimental Characterization:
- Ceramic Cores: Density measured using a pycnometer with ethanol. Decoring effectiveness tested using chemical leaching (various acids) and high-pressure water jet. Mechanical properties (flexural strength σf, Young's Modulus E) determined by three-point bending tests (Instron 3369) according to UNI EN 843-1 and UNI EN 843-3.
- HPDC Component: Prototypes produced on an IDRA OLS2000 HPDC machine. Microstructure analyzed on transverse sections using optical microscopy (OM - Leica DMI 5000M) and scanning electron microscopy (SEM - LEO EVO 40) with Energy Dispersive Spectroscopy (EDS - Link Analytical eXL). Vickers microhardness (HV0.3) measured across the section using a Micro Duromat 4000 Reichert Jung instrument according to ASTM E92-16 and ASTM E140-02.
Research Topics and Scope:
The research focused on the application of innovative ceramic lost cores in the HPDC process for an automotive structural component (crossbeam). The scope included:
- Geometric redesign of the crossbeam from open to closed profile.
- Comparative structural performance analysis (stiffness, buckling resistance).
- HPDC process feasibility simulation, including fluid flow, heat transfer, solidification, and defect prediction (air entrapment, cold joints, shrinkage).
- Characterization of Al2O3 + SiO2 + K2O based ceramic cores (physical, chemical resistance for decoring, mechanical properties).
- Experimental production of prototypes using EN AC-43500 aluminum alloy.
- Metallurgical characterization of the final cast component, including the interface between the aluminum alloy and the residual ceramic/cermet material.
6. Key Results:
Key Results:
- The redesigned crossbeam with a closed-box section achieved a slight weight reduction compared to the original open profile (3.93 kg vs 3.95 kg).
- FEA simulations demonstrated superior structural performance for the new design: higher natural frequencies (indicating increased stiffness, e.g., first torsional frequency increased by ~54.3% in free-free conditions) and significantly higher buckling load factors under both force and moment loading conditions compared to the original design.
- CFD process simulations confirmed the feasibility of the HPDC process with the ceramic core. Predicted casting quality (air entrapment, solidification pattern, potential defects) was very similar to the traditional HPDC process without a core. Simulation parameters (e.g., filling time ~0.2s, solidification time ~8.4s) were consistent with standard HPDC practice.
- Ceramic core characterization showed density around 1.92-1.98 g/cm³. Chemical leaching tests revealed that only HF solutions etched the ceramic, but these severely damaged the aluminum. High-pressure water jetting was identified as the effective and non-damaging decoring method. Mechanical tests (three-point bending) showed that flexural strength and Young's modulus increased with sintering temperature; the "c-1110 °C" variant was selected for prototypes.
- Approximately 100 hollow crossbeam prototypes were successfully produced using HPDC with the selected ceramic cores and subsequently decored using a water jet. The manufacturing cycle time was ~70 seconds.
- Microstructural analysis of the prototypes revealed the expected structure for EN AC-43500 alloy (α-Al matrix, Al-Si eutectic, intermetallics like α-Al15(Mn,Fe)3Si2). A thin (~100 µm) cermet layer (ceramic-metal mixture) was observed at the interface between the aluminum and the ceramic core in some areas, but it showed good coherence with the aluminum and was not considered detrimental to the application.
- Vickers microhardness measurements across the component section yielded values between 75-90 HV0.3, typical for this alloy and process, indicating that the presence of the core and the thin cermet layer did not negatively impact the overall mechanical properties of the bulk material.
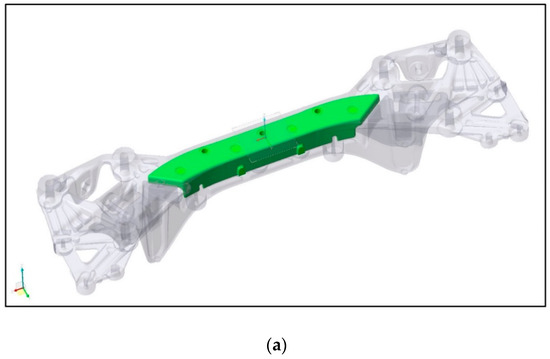
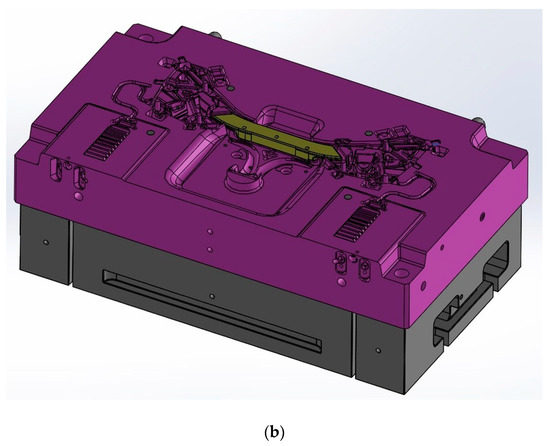
Figure 2. (a) 3D model of the closed profile crossbeam with ceramic core. (b) The geometry and the positioning solutions in the mold cavity adopted for the ceramic core.
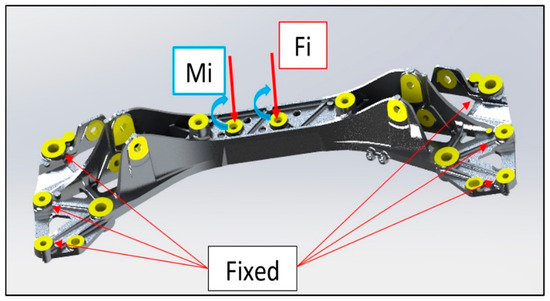
Figure 3. Buckling analysis model: boundary condition and load cases.Table 2. FEM simulation parameters.
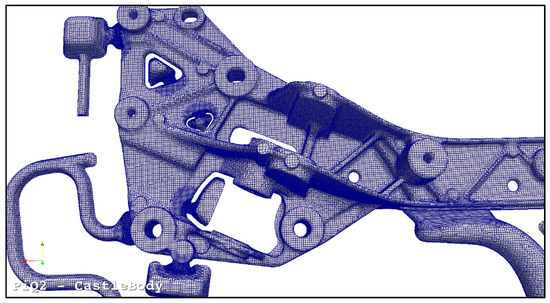
Figure 4. Local mesh refinement.
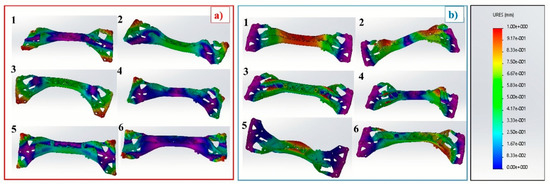
Figure 5. Displacement trend for the first six vibration modes for original geometry: (a) free-free boundary conditions and (b) fixed conditions.
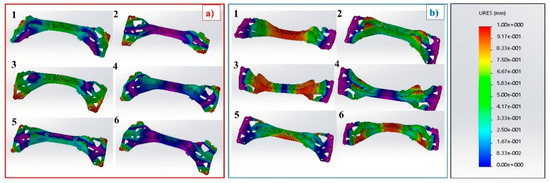
Figure 6. Displacement trend for the first six vibration modes for new geometry: (a) free-free boundary conditions and (b) fixed conditions.
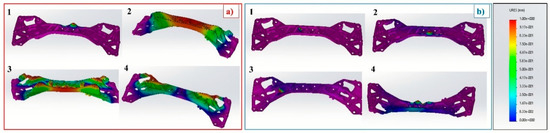
Figure 7. Displacement trend for the first four deformations for original geometry: (a) load case 1 (F); (b) load case 2 (M).
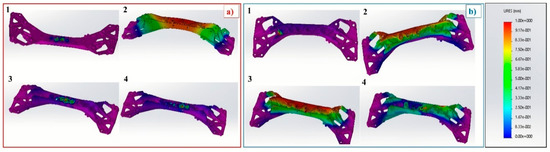
Figure 8. Displacement trend for the first four deformations for new geometry: (a) load case 1 (F); (b) load case 2 (M).
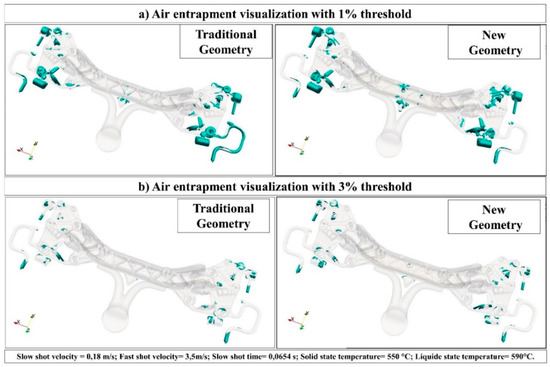
Figure 9. Air entrapment visualization (a) with 1% threshold and (b) with 3% threshold for traditional and new geometry.
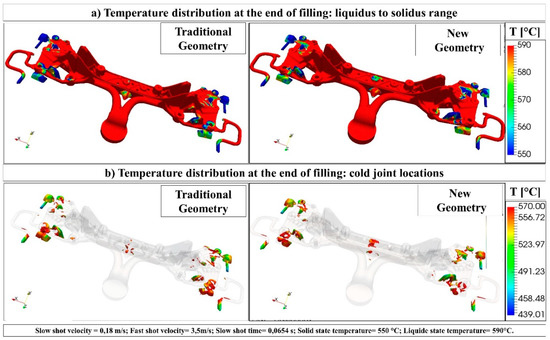
Figure 10. (a) Temperature distribution at the end of filling: liquidus to solidus range; (b) Temperature distribution at the end of filling: cold joint locations.

Figure 11. Results of solidification analysis.Figure 10a,b shows the temperature distribution of the alloy at the end of filling in the range between liquidus and solidus temperatures.
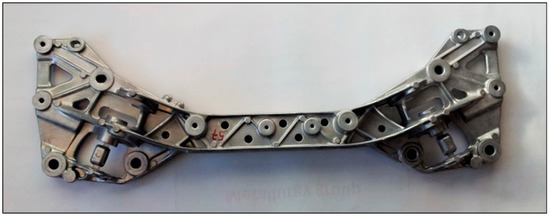
Figure 12. Hollowed aluminum high pressure die casting component.
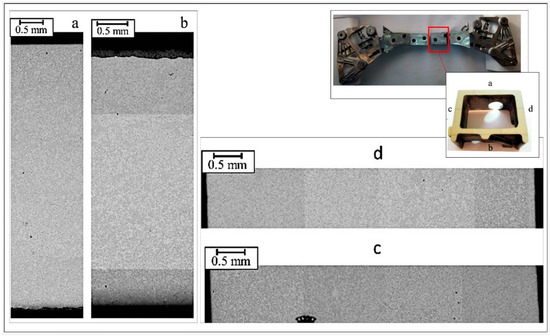
Figure 13. Collage of various micrographs of the transverse sections of the hollowed crossbeam.
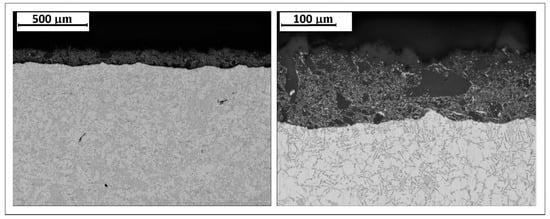
Figure 14. Optical microscope details of the transverse sections of the hollowed crossbeam.
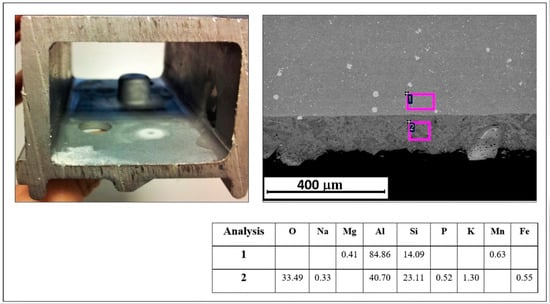
Figure 15. Visual inspection on cermet and SEM image with results of EDS analysis (wt%).
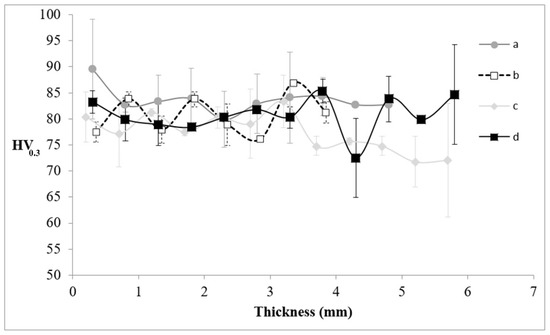
Figure 16. Vickers microhardness HV0.3 variation with respect to the thickness along the transverse section of .
Figure Name List:
- Figure 1. 3D design and schematic sketch of the section profile of (a) original crossbeam (b) modified crossbeam. The dimensions are expressed in (mm).
- Figure 2. (a) 3D model of the closed profile crossbeam with ceramic core. (b) The geometry and the positioning solutions in the mold cavity adopted for the ceramic core.
- Figure 3. Buckling analysis model: boundary condition and load cases.
- Figure 4. Local mesh refinement.
- Figure 5. Displacement trend for the first six vibration modes for original geometry: (a) free-free boundary conditions and (b) fixed conditions.
- Figure 6. Displacement trend for the first six vibration modes for new geometry: (a) free-free boundary conditions and (b) fixed conditions.
- Figure 7. Displacement trend for the first four deformations for original geometry: (a) load case 1 (F); (b) load case 2 (M).
- Figure 8. Displacement trend for the first four deformations for new geometry: (a) load case 1 (F); (b) load case 2 (M).
- Figure 9. Air entrapment visualization (a) with 1% threshold and (b) with 3% threshold for traditional and new geometry.
- Figure 10. (a) Temperature distribution at the end of filling: liquidus to solidus range; (b) Temperature distribution at the end of filling: cold joint locations.
- Figure 11. Results of solidification analysis.
- Figure 12. Hollowed aluminum high pressure die casting component.
- Figure 13. Collage of various micrographs of the transverse sections of the hollowed crossbeam.
- Figure 14. Optical microscope details of the transverse sections of the hollowed crossbeam.
- Figure 15. Visual inspection on cermet and SEM image with results of EDS analysis (wt%).
- Figure 16. Vickers microhardness HV0.3 variation with respect to the thickness along the transverse section of Figure 13.
7. Conclusion:
This study successfully demonstrated the feasibility of producing a lighter and structurally improved safety-relevant automotive component (aluminum crossbeam) using HPDC with innovative ceramic lost cores. The redesigned boxed geometry showed significantly enhanced dynamic behavior (higher natural frequencies) and increased resistance to buckling compared to the original open-profile design. Process simulations confirmed that the HPDC process with ceramic cores can achieve casting quality comparable to traditional methods. Experimental characterization identified suitable ceramic core properties and an effective decoring method (high-pressure water jet). Analysis of the produced prototypes confirmed that the microstructure and hardness were consistent with standard HPDC parts, despite the presence of a thin, non-detrimental cermet layer at the core-metal interface. The results highlight the potential of HPDC with ceramic lost cores for manufacturing complex, hollow, near-net shape components in high volumes, enhancing the competitiveness of HPDC for advanced automotive applications and opening possibilities for further lightweighting and design optimization of hollow structures.
8. References:
- [1] Chindamo, D.; Gadola, M. Reproduction of real-world road profiles on a four-poster rig for indoor vehicle chassis and suspension durability testing. Adv. Mech. Eng. 2017, 9, 1–10. [CrossRef]
- [2] Chiaberge, M. New Trends and Developments in Automotive Industry; InTech: London, UK, 2011; ISBN 978-953-307-999-8. [CrossRef]
- [3] Tempelman, E. Multi-Parametric study of the effect of materials substitution on life cycle energy use and waste generation of passenger car structures. Transp. Res. Part D Transp. Environ. 2011, 16, 479–485. [CrossRef]
- [4] Cecchel, S.; Chindamo, D.; Turrini, E.; Carnevale, C.; Cornacchia, G.; Gadola, M.; Panvini, A.; Volta, M.; Ferrario, D.; Golimbioschi, R. Impact of reduced mass of light commercial vehicles on fuel consumption, CO2 emissions, air quality, and socio-economic costs. Sci. Total Environ. 2018, 613–614, 409–417. [CrossRef] [PubMed]
- [5] Cecchel, S.; Ferrario, D.; Panvini, A.; Cornacchia, G. Lightweight of a cross beam for commercial vehicles: Development, testing and validation. Mater. Des. 2018, 149, 122–134. [CrossRef]
- [6] Cecchel, S.; Ferrario, D. Numerical and experimental analysis of a high pressure die casting Aluminum suspension cross beam for light commercial vehicles. La Metallurgia Italiana 2016, 6, 41–44.
- [7] Morello, L.; Rosti Rossini, L.; Pia, G.; Tonoli, A. The Automotive Body: Volume I: Components Design; Springer: New York, NY, USA, 2001; ISBN 978-94-007-0513-5.
- [8] Cecchel, S.; Cornacchia, G.; Panvini, A. Cradle-to-Gate Impact Assessment of a High-Pressure Die-Casting Safety-Relevant Automotive Component. JOM 2016, 8, 2443–2448. [CrossRef]
- [9] Cecchel, S.; Chindamo, D.; Collotta, M.; Cornacchia, G.; Panvini, A.; Tomasoni, G.; Gadola, M. Lightweighting in light commercial vehicles: Cradle-to-grave life cycle assessment of a safety relevant component. Int. J. Life Cycle Assess. 2018, 23, 1–12. [CrossRef]
- [10] Cecchel, S.; Collotta, M.; Cornacchia, G.; Panvini, A.; Tomasoni, G. A comparative cradle-to gate impact assessment: Primary and secondary aluminum automotive components case. La Metallurgia Italiana 2018, 2, 46–55.
- [11] Cecchel, S.; Cornacchia, G.; Gelfi, M. Corrosion behavior of primary and secondary AlSi High Pressure Die Casting alloys. Mater. Corros. 2017, 68, 961–969. [CrossRef]
- [12] Solazzi, L. Applied research for Weight Reduction of an industrial Trailer. FME Trans. 2012, 40, 57–62.
- [13] Solazzi, L. Wheel rims for industrial vehicles: Comparative and experimental analyses. Int. J. Heavy Veh. Syst. 2011, 18, 214–225. [CrossRef]
- [14] Hirsch, J. Aluminium in Innovative Light-Weight Car Design. Mater. Trans. 2011, 52, 818–824. [CrossRef]
- [15] Chindamo, D.; Lenzo, B.; Gadola, M. On the vehicle sideslip angle estimation: A literature review of methods, models and innovations. Appl. Sci. 2018, 8, 355. [CrossRef]
- [16] Henriksson, F.; Johansen, K. On Material Substitution in Automotive BIWs – From Steel to Aluminum Body Sides. Procedia CIRP 2016, 50, 683–688. [CrossRef]
- [17] Kelkar, A.; Roth, R.; Clark, J. Automobile Bodies: Can Aluminum Be an Economical Alternative To Steel? JOM 2001, 53, 28–32.
- [18] Zhoua, J.; Wana, X.; Lia, Y. Advanced aluminium products and manufacturing technologies applied on vehicles at the EuroCarBody conference. Mater. Proc. 2015, 2, 5015–5022. [CrossRef]
- [19] Fridlyander, I.N.; Sister, V.G.; Grushko, O.E.; Berstenev, V.V.; Sheveleva, L.M.; Ivanova, L.A. Aluminum alloys: Promising materials in the automotive industry. Met. Sci. Heat Treat. 2002, 44, 365–370. [CrossRef]
- [20] Dioni, D.; Cecchel, S.; Cornacchia, G.; Faccoli, M.; Panvini, A. Effects of artificial aging conditions on mechanical properties of gravity cast B356 aluminum alloy. Trans. Nonferrous Met. Soc. China 2015, 25, 1035–1042. [CrossRef]
- [21] Faccoli, M.; Dioni, D.; Cecchel, S.; Cornacchia, G.; Panvini, A. Optimization of heat treatment of gravity cast Sr-modified B356 aluminum alloy. Trans. Nonferrous Met. Soc. China 2017, 27, 1698–1706. [CrossRef]
- [22] Haracopos, B.; Fisher, T.P. The Technology of Gravity Die Casting; Hart Pub. Co.: Oxford, UK, 1968.
- [23] ASM. Metals Handbook, 10th ed.; ASM-Metals Park: Geauga, OH, USA, 1990.
- [24] Campbell, J.; Harding, R.A. Casting Technology; TALAT 2.0 [CD-ROM]; EAA: Bruxelles, Belgium, 2000.
- [25] Schleg, S.; Kamicki, D.P. Guide to casting and moulding processes. Engineered casting solutions. Technical Articles, 2000.
- [26] Brown, J.R. Foseco Non-Ferrous Foundryman’s Handbook; Elsevier: Oxford, UK, 1999; ISBN 9780080531878.
- [27] Street, A.C. The Diecasting Book, 2nd ed.; Portcullis Press: London, UK, 1990.
- [28] Nagendra Parashar, S.; Mittal, R.K. Elements of Manufacturing Processes; PHI learning Pvt. Ltd.: New Delhi, India, 2006.
- [29] Vinarcik, E.J. High Integrity Die Casting Processes; John Wiley & Sons: Hoboken, NJ, USA, 2002; ISBN 978-0-471-20131-1.
- [30] Andresen, W. Die Cast Engineering: A Hydraulic, Thermal, and Mechanical Process; CRC Press: Boca Raton, FL, USA, 2004.
- [31] Jelínek, P.; Adámková, E.; Mikšovský, F.; Beňo, J. Advances in technology of soluble cores for die castings. Arch. Foundry Eng. 2015, 15, 29–34. [CrossRef]
- [32] Pierri, D. Lost Core: New Perspectives in Die Casting. Available online: https://www.buhlergroup.com/northamerica/en/industry-solutions/die-casting/latest-news/details-7797.htm?title= (accessed on 9 February 2019).
- [33] Czerwinski, F.; Birsan, G.; Benkel, F.; Kasprzak, W.; Walker, M.J.; Smith, J.; Trinowski, D.; Musalem, I. Developing strong core technology for high pressure die casting. Automot. Mater. 2017, 8, 1–11.
- [34] Rupp, S.; Heppes, F. La rivoluzione nella pressofusione. Tecnico-Industria Fusoria 2017, 4, 72–76.
- [35] Donahue, R.J.; Degler, M.T. Congruent Melting Salt Alloys for Use as Salt Cores in High Pressure Die Casting. U.S Patent US9527131B1, 25 August 2014.
- [36] Radadiya, V.A.; Dave, K.G.; Patel, K.R. Design and analysis of salt core for a casting of alluminium alloys. Int. J. Adv. Eng. Res. Dev. 2015, 2, 344–348.
- [37] Jelinek, P.; Miksovsky, F.; Beoo, J.; Adamkova, E. Development of foundry cores based on inorganic salts. MTAEC9 2013, 47, 689–693.
- [38] Jelínek, P.; Adámková, E. Lost cores for high-pressure die casting. Arch. Foundry Eng. 2014, 14, 101–104. [CrossRef]
- [39] Yaokawa, J.; Miura, D.; Anzai, K.; Yamada, Y.; Yoshii, H. Strength of salt core composed of alkali carbonate and alkali chloride mixtures made by casting technique. Mater. Trans. 2007, 8, 1034–1041. [CrossRef]
- [40] Yaokawa, J.; Koichi, A.; Yamada, Y.; Yoshii, H. Strength of salt core for die casting. In Proceedings of the International Conference CastExpo ’05 NADCA, St. Louis, MO, USA, 16–19 April 2005; NADCA: St. Louis, MO, USA, 2005.
- [41] Fuchs, B.; Eibisch, H.; Körner, C. Core viability simulation for salt core technology in high-pressure die casting. Int. J. Metalcast. 2013, 7, 39–45. [CrossRef]
- [42] Fuchs, B.; Körner, C. Mesh resolution consideration for the viability prediction of lost salt cores in the high pressure die casting process. Prog. Comput. Fluid Dyn. 2014, 14, 24–30. [CrossRef]
- [43] Mizukusa, Y. Casting Apparatus and Casting Method for Producing Cylinder Block. U.S. Patent 5,690,159, 27 August 1996.
- [44] Ackerman, A.D.; Aula, H.A. Method of Making a Cast Aluminum Based Engine Block. U.S. Patent 4,446,906, 8 May 1984.
- [45] Brown, W.N.; Robinson, P.M. Soluble Metal Casting Cores Comprising a Water Soluble Salt and a Synthetic Resin. U.S. Patent 364,549, 22 July 1969.
- [46] Gibbons, W.A. Core or Filler of Fusible Material for Hollow Vulcanizable Articles. U.S. Patent 1,523,519, 20 January 1925.
- [47] Foreman, R.W. Mixture and Method for Preparing Casting Cores and Cores Prepared Thereby. U.S. Patent 4,840,219, 20 June 1989.
- [48] Sakoda, T. Water Soluble Core for Pressure Die Casting and Process for Making the Same. U.S. Patent 3,963,818, 15 June 1976.
- [49] Molina, R.; Moschini, R. Production of hollow components in high pressure die casting through the use of ceramic lost cores. In Proceedings of the International Conference High Tech Die Casting 2012, Vicenza, Italy, 9–10 April 2012.
- [50] Moschini, R.; Calzolaro, A.L. Method for Manufacturing Monolithic Hollow Bodies by Means of a Casting or Injection Moulding Process. Patent International Publication No WO 2011/061593 A1, 26 May 2011.
- [51] Solazzi, L. Innovative Bolted junction with high ductility for circular tubular element. J. Constr. Steel Res. 2015, 112, 175–182. [CrossRef]
- [52] Mats, G.; Larson, F.B. The Finite Element Method: Theory, Implementation and Applications; Springer: Berlin, Germany, 2010; ISBN 978-3-642-33286-9.
- [53] Dimitrios, G. Pavlou Essentials of Finite Element Method for Mechanical and Industrial Engineers; Elsevier: Amsterdam, The Netherlands, 2015; ISBN 978-0-12-802386-0.
- [54] Panvini, A.; Molin, D.; Gislon, C. Dual phase simulation for high pressure die casting: Overview and validation of its capabilities. In Proceedings of the HTDC Conference 2016, AIM, Venice, Italy, 22–23 June 2016.
- [55] Panvini, A.; Gislon, C. Air entrapment prediction in diecasting through dual phase simulation. In Proceedings of the Die Casting Congress Tabletop 2013, Louisville, KY, USA, 16–18 September 2013.
- [56] Miller, A. PQ2 and Gating Manual; NADCA: Arlington Heights, IL, USA, 2016.
- [57] UNI EN 843-1:2007. Advanced Technical Ceramics—Mechanical Properties of Monolithic Ceramics at Room Temperature—Part 1: Determination of Flexural Strength; NSAI: Dublin, Ireland, 2007.
- [58] UNI EN 843-2:2007. Advanced Technical Ceramics—Mechanical Properties of Monolithic Ceramics at Room Temperature—Part 2: Determination of Young’s Modulus, Shear Modulus and Poisson’s Ratio; NSAI: Dublin, Ireland, 2007.
- [59] Smith, J.H. An Introduction to Modern Vehicle Design; Elsevier: Oxford, UK, 2002; ISBN 07506 5044 3.
- [60] Pacejka, H.B. Tyre and Vehicle Dynamics, 2nd ed.; Butterworth-Heinemann: Oxford, UK, 2006; ISBN 0-7506-6918-7.
- [61] Franke, R.; Dragulin, D.; Zovi, A.; Casarotto, F. Progress in ductile aluminium high pressure die casting alloys for the automotive industry. La Metallurgia Italiana 2007, 5, 21–26.
- [62] Tinklepaugh, J.R.; James, R. Cermets; Reinhold Publishing Corporation: New York, NY, USA, 1960; ASIN B0007E6FO4.
- [63] Hanaor, D.A.H.; Hu, L.; Kan, W.H.; Proust, G.; Foley, M.; Karaman, I.; Radovic, M. Compressive performance and crack propagation in Al alloy/Ti2AlC composites. Mater. Sci. Eng. 2016, 72, 247–256. [CrossRef]
- [64] Bhattacharya, A.K.; Petrovic, J.J. Ductile phase toughening and R-curve behaviour in a B4C-AI cermet. J. Mater. Sci. 1992, 27, 2205–2210. [CrossRef]
9. Copyright:
- This material is a paper by "Giovanna Cornacchia, Daniele Dioni, Michela Faccoli, Claudio Gislon, Luigi Solazzi, Andrea Panvini and Silvia Cecchel". Based on "Experimental and Numerical Study of an Automotive Component Produced with Innovative Ceramic Core in High Pressure Die Casting (HPDC)".
- Source of the paper: https://doi.org/10.3390/met9020217
This material is summarized based on the above paper, and unauthorized use for commercial purposes is prohibited.
Copyright © 2025 CASTMAN. All rights reserved.