This paper summary is based on the article "Development of Salt Core Use as an Alternative in Aluminum Alloy Castings" published in the Celal Bayar University Journal of Science.
1. Overview:
- Title: Development of Salt Core Use as an Alternative in Aluminum Alloy Castings
- Author: Tülay Hançerlioğlu
- Publication Year: 2022
- Publishing Journal/Academic Society: Celal Bayar University Journal of Science
- Keywords: Core gas, sand core, salt core
2. Research Background:
- Social/Academic Context of the Research Topic: The automotive industry demands increasingly complex geometries in casting parts. While steel cores are sometimes insufficient for intricate designs and casting quality, sand cores are commonly employed for parts with complex structures and internal cavities. However, sand cores present challenges. Salt core technology has emerged as a potential alternative since the late 20th century, particularly in gravity and low-pressure die casting.
- Limitations of Existing Research: Traditional sand core methods, utilizing resin binders in cold-box or hot-box processes, can lead to core gas generation during casting. Furthermore, sand core removal often involves mechanical impact and vibration, which are energy-intensive and generate noise and dust, posing environmental and health concerns. Existing research acknowledges the strength of salt cores and their positive environmental impact in high-pressure casting, but further investigation into their practical application and detailed performance in specific casting scenarios is warranted.
- Necessity of the Research: This research addresses the need to explore and validate the use of salt cores as a viable substitute for sand cores in aluminum alloy castings. The study focuses on the potential benefits of salt cores, including improved mechanical properties, easier and cleaner removal, reduced waste, and a more environmentally friendly casting process.
3. Research Purpose and Research Questions:
- Research Purpose: The primary purpose of this research is to investigate the development and application of salt cores as an alternative to conventional sand cores in the production of aluminum alloy castings.
- Key Research Questions: While not explicitly stated as questions, the research implicitly seeks to answer:
- Can salt cores effectively replace sand cores in producing complex geometry aluminum alloy castings?
- What are the advantages of salt cores over sand cores in terms of core gas reduction, removal efficiency, surface quality of the casting, and environmental impact?
- What are the critical process parameters and challenges associated with salt core production and casting, and how can they be optimized?
- Research Hypotheses: The underlying hypothesis is that salt cores offer significant advantages over sand cores in aluminum alloy casting, specifically by reducing core gas defects, enabling easier and residue-free core removal using water dissolution, and minimizing environmental impact.
4. Research Methodology:
- Research Design: This study employs an experimental research design, focusing on a case study using a pump body part casting.
- Data Collection Method:
- Casting Trials: Experiments were conducted using a gravity mold tilting casting method with salt cores to produce pump body parts.
- Salt Core Production: Salt cores were manufactured using an injection molding method with molten salt (NaCl).
- Dimensional Measurement: Laser scanning with Faro Edge Scan Arm HD and comparison with a 3D data model were used to assess the dimensional accuracy and shrinkage of the salt cores.
- Surface Roughness Measurement: Surface roughness of castings produced with both salt and sand cores was measured and compared.
- Visual Inspection and Cross-Section Analysis: Cast parts were visually inspected for defects, and cross-sections were analyzed after polishing to examine internal quality and core removal effectiveness.
- Analysis Method: The research involved a comparative analysis of salt core casting against traditional sand core casting. Qualitative assessments were made through visual inspection, while quantitative data was obtained from dimensional and surface roughness measurements. The study focused on evaluating the feasibility, advantages, and challenges of using salt cores in a practical casting scenario.
- Research Subjects and Scope: The research focused on the production of a pump body part made from aluminum alloy. The salt core material used was NaCl. The trials were conducted within an industrial setting at Nemak İzmir Döküm San.A.Ş., utilizing their facilities and expertise.
5. Main Research Results:
- Key Research Results:
- Core Gas Reduction: The use of salt cores eliminated core gas issues observed with sand cores, where resin burning caused gas and blocked air filters in the mold. No resin stack or air filter blockage was observed after salt core casting.
- Efficient Core Removal: Salt cores were easily and completely removed by dissolving them in water in a short time, leaving no residue in the cast part. The salt could potentially be recycled from the water.
- Improved Surface Quality: Surface roughness measurements showed that castings produced with salt cores exhibited a smoother surface finish compared to those made with sand cores.
- Salt Core Casting Roughness: Rz = 17.86 µm, Ra = 2.51 μm, Rmax = 34.63 µm (Figure 8).
- Sand Core (60 AFS) Casting Roughness: Rz = 60.9 µm, Ra = 11.4 µm, Rmax = 86.2 µm (Figure 8.1).
- Critical Process Parameters: Shrinkage control and cooling during salt core production were identified as critical parameters. Temperature changes significantly affected surface quality, scale, and core strength. Optimized cooling channels and parameters were necessary to prevent cracks and ensure homogeneous solidification.
- Statistical/Qualitative Analysis Results: Quantitative roughness measurements confirmed the qualitative observation of smoother surfaces with salt cores. Visual inspection of cast parts revealed successful core removal and no significant defects related to core gas or residue.
- Data Interpretation: The results indicate that salt cores offer significant advantages in terms of reduced core gas defects, simplified and cleaner core removal, and improved casting surface finish compared to sand cores for the tested aluminum alloy pump body part. However, precise control over cooling and shrinkage is essential for successful salt core production.
- Figure Name List:
- Figure 1. Sectional view of the pump body.
- Figure 2.1. Injection mold movable side manufactured for salt core.
- Figure 2.2. Injection mold fixed side manufactured for salt core.
- Figure 3. Salt core injection molding.
- Figure 4. Salt core laser scanning compared with 3D data model.
- Figure 5. Salt core exterior surface crack.
- Figure 6. Salt core inner diameter surface crack visible with eye control.
- Figure 7. Mold inner diameter core insertion.
- Figure 8. Roughness value measure from the casting part with a salt core.
- Figure 8.1. Roughness value measure from the casting part with a 60 AFS sand core.
- Figure 9. Inside view of salt core.
- Figure 10.1. Salt core produced in low temperature and short time.
- Figure 10.2. Salt core produced in high temperature and long time.
- Figure 11.1. Tilt casting machine.
- Figure 11.2. Tilt casting ladle.
- Figure 11.3. The tilt casting machine rotates 180 degrees.
- Figure 12. The casting part with salt core that comes out of the casting mold.
- Figure 13. The salt that starts to dissolve, the core and the cast part.
- Figure 14. Casting part cross section.
- Figure 15. Polished cast part cross-section.
- Figure 16. Cast part zoomed images.
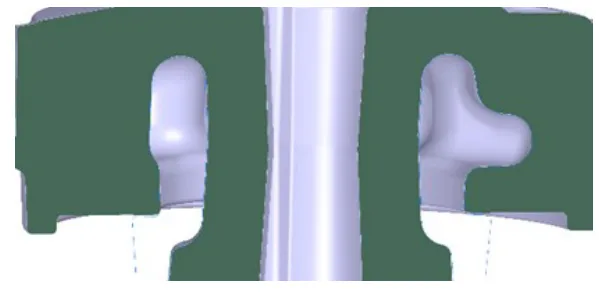
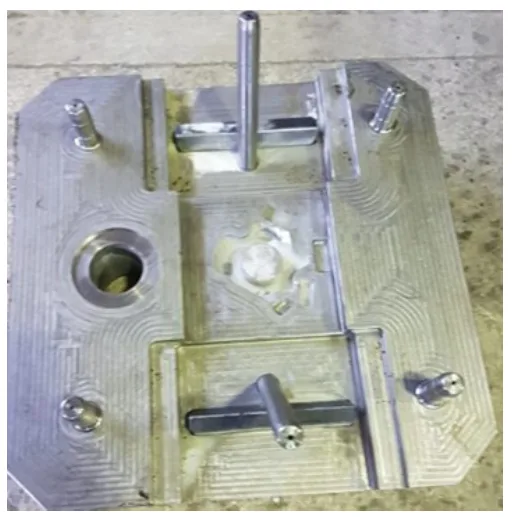
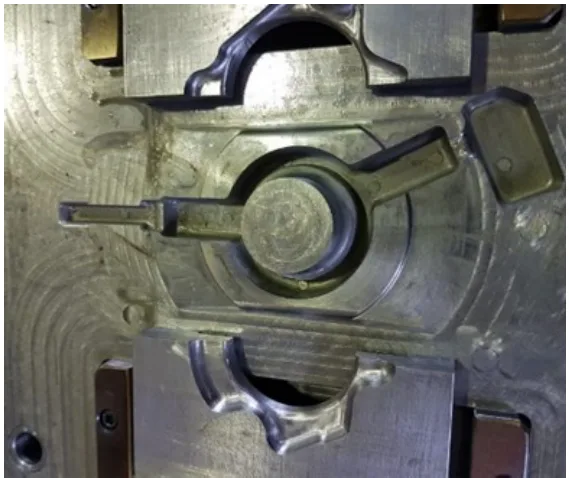
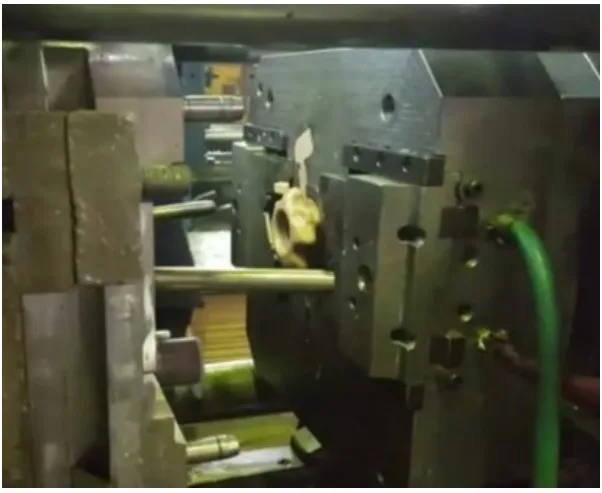
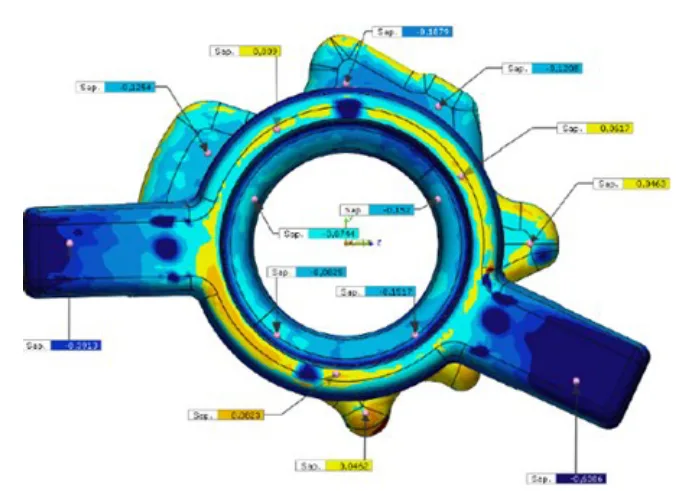
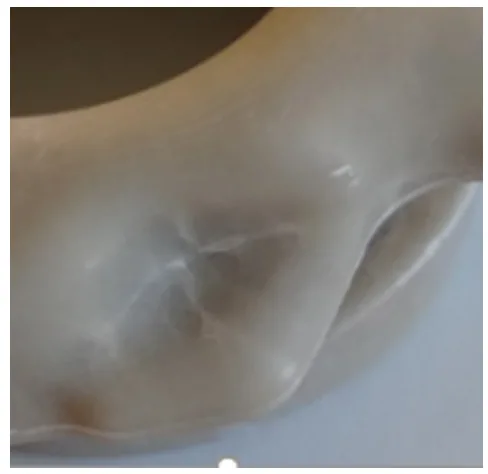
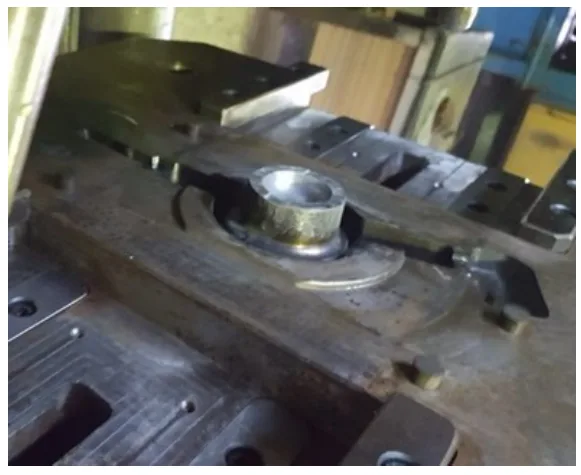
6. Conclusion and Discussion:
- Summary of Main Results: This study demonstrates that salt core casting is a promising alternative to sand core casting for producing complex aluminum alloy parts. It effectively addresses core gas issues, simplifies core removal through water dissolution without residue, enhances casting surface finish, and offers environmental benefits by eliminating dust and noise associated with mechanical core removal.
- Academic Significance of the Research: This research provides valuable practical evidence supporting the viability of salt core technology in an industrial setting. It contributes to the growing body of knowledge on advanced casting techniques and environmentally conscious manufacturing processes.
- Practical Implications: The findings suggest that industries utilizing aluminum alloy casting, particularly for complex parts, can benefit from adopting salt core technology. This can lead to improved casting quality, reduced defect rates, streamlined post-casting processes, and a more sustainable manufacturing footprint. The water-based core removal process offers energy savings and eliminates noise pollution compared to traditional mechanical methods.
- Limitations of the Research: The study is limited to a single pump body part design and specific gravity tilt casting conditions. Further research is needed to assess the general applicability of salt core technology across various aluminum alloys, part geometries, and casting methods (e.g., high-pressure die casting). The challenges related to shrinkage control and cooling optimization in salt core production require further investigation and refinement.
7. Future Follow-up Research:
- Directions for Follow-up Research:
- Mechanical and Thermal Properties: Further experimental studies should focus on comprehensively evaluating the mechanical and thermal properties of salt cores and directly comparing them to sand cores.
- Process Optimization: In-depth research is needed to optimize cooling systems and cooling parameters for salt core production to achieve homogeneous solidification and minimize cracking.
- Cost Reduction: Exploring cost-effective strategies, including the recycling of dissolved salt and identifying local alternative salt suppliers, is crucial for industrial adoption.
- Areas Requiring Further Exploration:
- Long-term Stability: Investigating the long-term stability and performance of salt cores, particularly in humid environments, is important for practical applications.
- Broader Application Range: Expanding the application scope of salt cores to various casting methods, such as high and low-pressure die casting, and different aluminum alloys and part complexities, will broaden the technology's impact.
8. References:
- [1]. Brůna, M., Sládek, A. & Kucharčík, L. (2012). Formation of porosity in Al-Si alloys. Archives of Foundry Engineering. 12(1), 5-8. DOI: 10.2478/v10266-012-0001-5.
- [2]. Lichý, P., Bednářová, V. & Elbel, T. (2012). Casting routes for porous metals production. Archives of Foundry Engineering. 12(1), 71-74. DOI: 10.2478/v10266-012-0014-0.
- [3]. Dańko, J., Dańko, R. (2009). Theoretical and technological aspects of the production processes of foundry cores blown In 50. Konferencji i Krystalizacja Metali (pp. 71-86). Katowice - Gliwice, Poland: Polska ademia Nauk, Komisja Odlewnictwa. ISBN: 978-83-929266-0-3. (in Polish).
- [4]. Fuchs, B., Eibisch, H. & Körner, C. (2013). Core viability simulation for salt core technology in high pressure die casting. International Journal of Metalcasting. 7(3), 39-45. ISSN: 1939-5981
- [5]. Stingl, P., & Shiller, G. (2009). Gichte und rückstandfreie Entkernung - Salzkerne für den Aluminiumguss. Giesserei-Erfahrungsaustausch. 6, 4-8.
- [6]. Adámková, E., Jelínek, P., & Študentová, S. (2013). Application of cooking salts in manufacture of water soluble cores for high pressure die. Materials and technology. 61(11-12), 689-693. ISSN: 1580-2949, 1580-3414.
- [7]. P. Jelínek, E. Adámková "Lost Cores for High-Pressure Die Casting" Department of Metallurgy and Foundry Engineering, VŠB-Technical University of Ostrava DOI:10.2478/afe-2014-0045.
- [8]. P. Jelínek, E. Adámková, F. Mikšovský, J. Beňo Advance in Technology of Soluble Cores for Die Castings, Department of Metallurgy and Foundry, VŠB - Technical University of Ostrava ISSN (1897-3310) Volume 15 Issue 2/2015 29-34.
- [9]. Eliska Adámková, Petr Jelínek, Jaroslav Beòo Frantiek Mik{ovský, Water-Soluble Cores-Verifying Development Trends, V[B-Technical University of Ostrava, Faculty of Metallurgy and Materials Engineering, Department of Metallurgy and Foundry, ISSN 1580-2949 MTAEC9,49(1)61(2015).
- [10]. Mr. Vijaykumar A. Radadiya, Dr. Komal G. Dave, Mr. Kalpeshkumar R. Patel, Design and Analysis of Salt Core for a Casting of Alüminium Alloys Core casting, International Journal Of Advance Engineering and Research Development, Volume 2, Issue 3-2015.
- [11]. Jun Yaoka wa, Daisuke Miura, Koichi Anzail, Youji Ya mada and Hiroshi Yoshii, "Strength of Salt Core Composed of Alkali Carbonate and Alkali Chloride Mixtu res Made by Casting" Journal of Technique Mate rials Transactions, Vol. 48, No. 5 (2007) pp. 1034 to 1041, Japan Foundry Engineering Society.
- [12]. Petr Jelinek, Frantisek Miksovsky, Jaroslav Beoo, Eliska Adamkova, " Development of Foundry Cores Based On Inorganic Salts" MTAEC9, 47(6)689(2013), ISSN 1580-2949.
- [13]. Bühler AG: Lost Core An Industrial Process Path for High-Quality Salt Cores. https://www.foundry-planet.com (Date of access: 25.06.2021).
9. Copyright:
This material is Tülay Hançerlioğlu's paper: Based on Development of Salt Core Use as an Alternative in Aluminum Alloy Castings.
Paper Source: https://doi.org/10.18466/cbayarfbe.1033177
This material was summarized based on the above paper, and unauthorized use for commercial purposes is prohibited.
Copyright © 2025 CASTMAN. All rights reserve