Sathishkumar Kaliyavarathan, Sivakumaran T.S.
ISSN: 0305-6120
Article publication date: 6 April 2020
Issue publication date: 7 October 2020
Abstract
Purpose
The purpose of this paper is to study the development of novel multiphase induction motor (MPIM) with copper die cast rotor in the drive system of electric propulsion vehicles (EPV). It is estimated that the manufacturers are concerned about high torque,Efficiency, motor life, energy conservation and high thermal tolerance. To ensure maximum torque and efficiency with multiphase winding and copper die cast technology to increasing high thermal tolerance, life, energy conversations. On other hand, it is very important of EPV application.
Design/methodology/approach
The focus of the investigation is threefold: the modified method carried out on MPIM both stator and rotor can overcome the current scenario problem facing by electric vehicles manufacture and developed perfect suitable electric motor for EPV applications. The design and simulation carried out finite element method (FEM) that was more accurate calculations. Finally developed prototype model of MPIM with copper die cast are discussed with conventional three phase Die casting Induction motor.
Findings
The paper confirmed the multiphase copper die-cast rotor induction motor (MDCrIM) is providing better performance than conventional motor. Proposed motor can bring additional advantage like heat tolerances, long life and energy conversations.
Originality/value
The experiments confirmed the MDCIM suitable for EPV Applications. The modified MDCIM of both stator and rotor are giving better result and good performance compared to conventional method.
Keywords
- Multiphase copper die-cast induction motor
- Electric propulsion vehicles
- Copper dies cast technology
- Finite element analysis
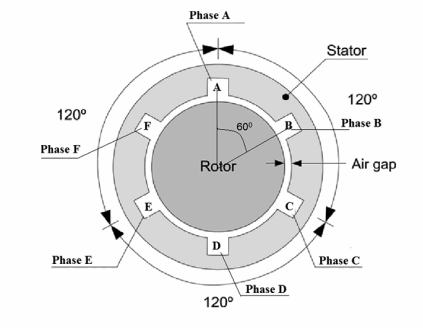
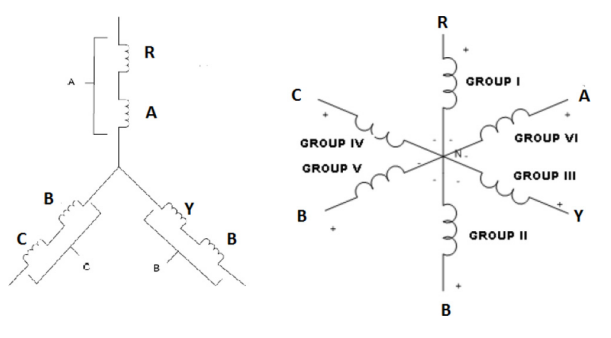
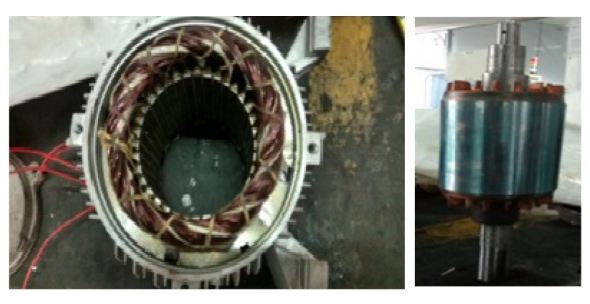
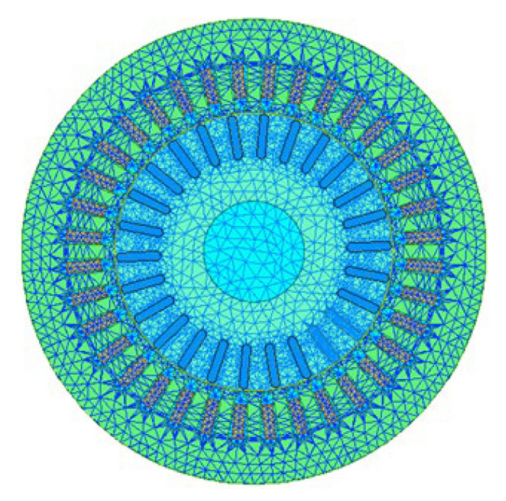
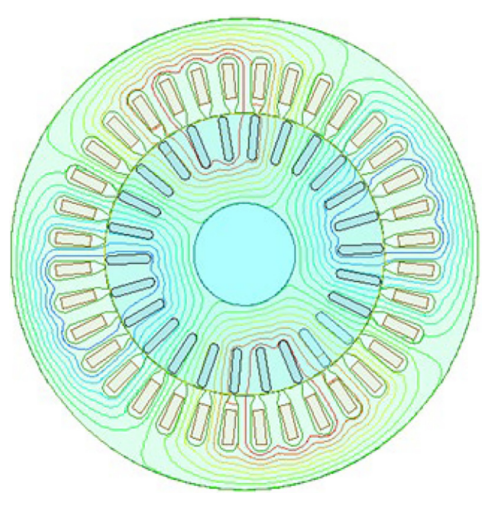
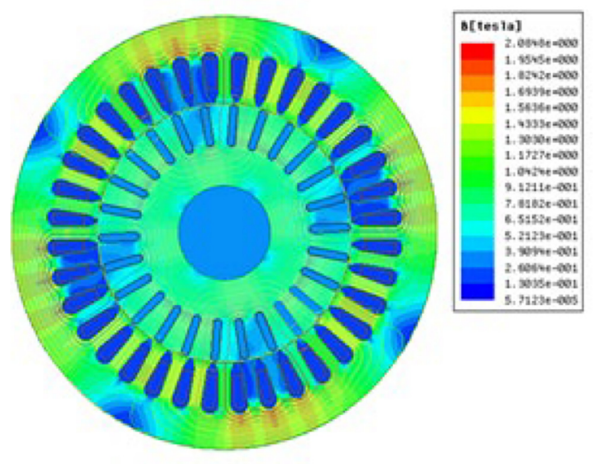
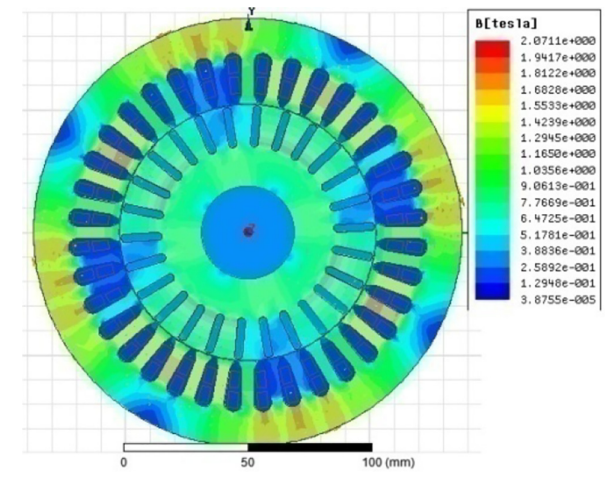
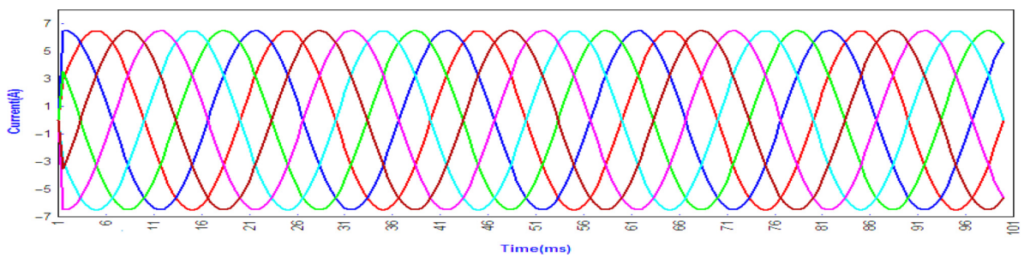
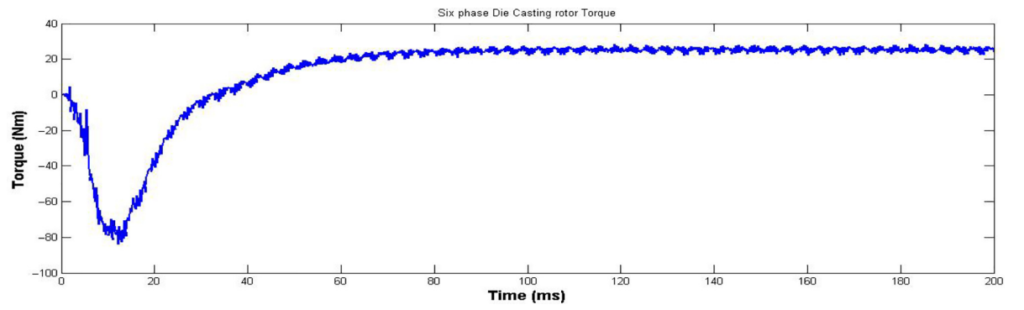
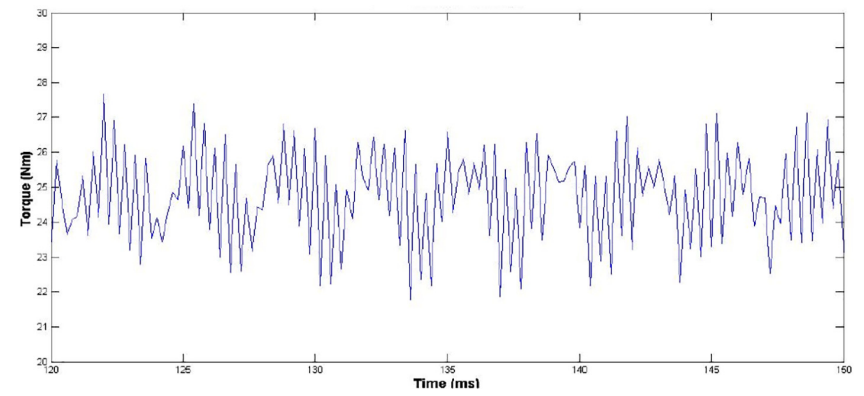

References
Alcala, I., Claudio, A. and Guerrero, G.V. (2005), “Analysis of propulsion systems in electric vehicles”, 2nd International Conference on Electrical and Electronics Engineering.
Chan, C.C. (2002), “The state of the art of electric and hybrid vehicles”, Proceedings of the IEEE, Vol. 90 No. 2, pp. 247-275.
Chan, C.C. and Wong, Y.S. (2004), “The state of the art of electric vehicles technology”, 4th International Power Electronics and Motion Control Conference, IPEMC,
Cortes, F., Barrero, F., Toral, S., Prieto, J. and Guevara, J. (2009), “Multi–sensorintegration in the vehicular system using the IEEE1451 std.: a case study”, 12th International
IEEE Conference on Intelligent Transportation Systems, ITSC.
Levi, E., Jones, M., Vukosavic, S.N. and Toliyat, H.A. (2006), “Steady state modelling of series-connected five-phase and six-phase two-motor drives”, CD-ROM paper no. IAS11p1,
Proceedings IEEE Industry Applications Society Annual Meeting IAS, Tampa, FL, p. 147.
Levi, E., Bojoi, R., Profumo, F., Toliyat, H.A. and Williamson, S. (2007), “Multiphase induction motor drives – a technology status reviewIET electric power applications”,
Vol. 1 No. 4, pp. 489-516.
Singh, G.K. (2002), “Multi-phase induction machine drive research – a survey”, Electric Power Systems Research, Vol. 61 No. 2, pp. 139-147.
Suhel, S.M. and Maurya, R. (2017), “Modelling, design and analysis of multi-phase induction motor”, International Journal of Power and Energy Conversion (IJPEC), Vol. 8 No. 2.
Ward, E.E. and HäRer, H. (1969), “Preliminary investigation of an invertor-fed 5-phase induction motor”, Proceedings of the Institution of Electrical Engineers, Vol. 116 No. 6, pp. 980-984.
Further reading
Bangura, J.F. (1999), “A time-stepping coupled finite elementstate space modeling for on-line diagnosis of squirrel-cage induction motor faults”, Ph.D. dissertation, Marquette University, Milwaukee, WI,
Bangura, J.F. and Demerdash, N.A. (1999a), “Simulation of inverter-fed induction motor drives with pulse-width modulation by a time-stepping coupled finite element-flux linkage-based state space model”, IEEE Transactions on Energy Conversion, Vol. 14 No. 3, pp. 518-525.
Bangura, J.F. and Demerdash, N.A. (1999b), “Diagnosis and characterization of effects of broken rotor bars and connectors in squirrel-cage induction motors by a timestepping coupled finiteelement- state space modeling approach”, IEEE Transactions on Energy Conversion, Vol. 14
No. 4, pp. 1167-1175.
Bangura, J.F. and Demerdash, N.A.O. (2000), “Effects of broken bars/end-ring connectors and airgap eccentricities on Ohmic and core losses of induction motors in ASDs using a
coupled finite element-state space method”, IEEE Transactions on Energy Conversion, Vol. 15 No. 1, pp. 40-47.
Benatmane, M., McCoy, T., Dalton, T. and Cooper, T.L. (1998), “Electric power generation and propulsion motor development for US navy surface ships”, Proceeding All Electric Ship: Developing Benefits for Maritime Applications Conference, London, pp. 89-94.
Demerdash, N.A. and Bangura, J.F. (1997), “A time-stepping coupled finite element-state space modeling for analysis and performance quality assessment of induction motors in
adjustable speed drives applications”, Presented at the Naval Symposium on Electric Machines, Newport, RI,
Edelson, J.S., Cox, I.W. and Magdych, J.S. ` (2005), “The chorus meshcon solution for starter-generator”, Proceedings IEEE Int. Electric Machines and Drives Conference IEMDC,
San Antonio, TX, pp. 1720-1724.
Fuchsloch, J.F., Finley, W.R. and Walter, R.W. (2008), “The next generation motor-designing a new approach to improve the energy efficiency of NEMA premium MotorsIEEE
industry applications magazine”.
Jones, M., Levi, E. and Iqbal, A. (2020), “Vector control of a five-phase series-connected two-motor drive using synchronous current controllers”, Electric Power Components
and Systems, Vol. 4, pp. 411-430.
Jones, M., Levi, E. and Vukosavic, S.N. (2006b), “Independent control of two five-phase induction machines connected in parallel to a single inverter supply”, Proceedings
IEEE Industrial Electronics Society Annual Meeting IECON,
Paris, p. 1257-1262.
Jones, M., Levi, E. and Vukosavic, S.N. (2006a), “A parallelconnected vector-controlled five-phase two-motor drive”, CD-ROM paper no. PMA2-19, Proceedings International
Conference on Electrical Machines ICEM.
Leicht, A. and Makowski, K. (2019), “Influence of shape and material of rotor bars on performance characteristics of single-phase self-excited induction generators”, COMPEL –
The International Journal for Computation and Mathematics in Electrical and Electronic Engineering, Vol. 38 No. 4, pp. 1235-1244, available at: https://doi.org/10.1108/
COMPEL-10-2018-0430
Levi, E., Jones, M., Vukosavic, S.N. and Toliyat, H.A. “A fivephase two-machine vector controlled induction motor drive supplied from a single inverter”, EPE Journal, Vol. 3, pp. 38-48.
Mahopatra, K.G. (2002), “A novel scheme for six phase induction motor with open end windings”, 28th Annual Conference of IEEE Industrial Electronics Society, 5th – 8th
November.
Parasiliti, F. and Villani, M. (2003), “Design of high efficiency induction motors with die-casting copper rotors”, in Parasiliti, F. and Bertoldi, P. (Eds), Energy Efficiency in Motor Driven Systems, Springer, pp. 144-151, ISBN 3-540-00666-4.
Samir, H., Omar, T. and Rachid, I. (May 2008), “A generalized two axes model of a squirrel-cage induction motor for rotor fault diagnosis”, Serbian Journal of Electrical Engineering, Vol. 5 No. 1, pp. 155-170.
Shen, J., Wang, K., Shi, D., Wang, C. and Jin, M. (2014), “Optimal design of low-cost IPM AC motor”, COMPEL – The International Journal for Computation and Mathematics in
Electrical and Electronic Engineering, Vol. 33 No. 5, pp. 1587-1598, available at: https://doi.org/10.1108/ COMPEL-09-2013-0292
Vasic, V., Marcˇetic, D., Vukosavic, S. and Oros, D. (2010), “Prediction of local instabilities in open-loop induction motor drives”, COMPEL – The International Journal for Computation and Mathematics in Electrical and Electronic Engineering, Vol. 29 No. 3, pp. 865-884