The content of this introduction paper is based on the article 'Copper in the Rotor for Lighter, Longer Lasting Motors' published by ASNE.

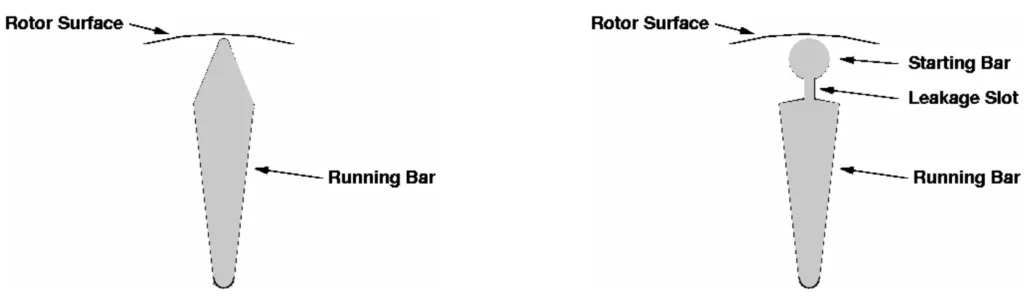
1. Overview:
- Title: Copper in the Rotor for Lighter, Longer Lasting Motors
- Author: C. Stark, J. G. Cowie, D. T. Peters, and E. F. Brush, Jr.
- Year of publication: 2005
- Journal/academic society of publication: ASNE SAN DIEGO SECTION, FLEET MAINTENANCE SYMPOSIUM 2005
- Keywords: (The paper does not explicitly list keywords, but based on the content, relevant keywords would include: copper rotor, die casting, motor efficiency, motor weight, die life, nickel-base alloy, thermal fatigue, heat checking)
2. Abstract:
This paper reviews the advantages of substituting die-cast copper for aluminum in the motor rotor. This advance in motor technology has been long sought by the motor industry but short die life due to the high melting point of copper frustrated attempts to manufacture by pressure die casting. The nickel-base alloy hot die technology developed to solve the manufacturing problem is briefly reviewed. Development work done prior to the present program and commercial motors derived from that work have focused on the increased electrical energy efficiency achievable by using copper with its higher electrical conductivity in the rotor. Performance characteristics of example industrial motors are presented. Modification of the conductor bar shape to control in-rush current and starting torque to accommodate copper in the rotor will be discussed. Modeling by motor manufacturers has shown that by using copper in the rotor, a lighter motor than an aluminum rotor motor at the same efficiency can be built. An example of weight savings calculated for a 15 Hp (11 kW) motor is presented. Data presented here show that motors with copper rotors run cooler. Industry experience shows that cooler operation translates to reduced maintenance costs, improved reliability and longer motor life.
3. Summary of the study:
Background of the research topic:
The Defense community needs lighter weight, lower cost, environmentally friendly, and more reliable materials. The Copper-Based Casting Technology (C-BCT) program aims to develop copper-based alloy applications for lighter, more efficient components in defense systems, specifically focusing on die-cast copper rotors for electric motors.
Status of previous research:
Previous research had identified the benefits of copper rotors (higher efficiency, lower operating temperatures), but manufacturing was hindered by short die life due to copper's high melting point. Prior work focused primarily on efficiency gains.
Purpose of the study:
The study aims to design, build, and test die-cast copper rotor motors with improved electrical energy efficiency or a substantial weight advantage compared to aluminum counterparts. It also addresses the die life problem.
Core study:
The core study involves two phases: (1) addressing die life issues in pressure die casting of copper by investigating high-temperature die materials and optimal operating conditions, and (2) evaluating the performance of motors with die-cast copper rotors compared to aluminum rotor motors.
4. Research Methodology
Research Design:
The research involved a combination of materials science investigation (die materials), thermal modeling, and experimental testing (dynamometer testing of motors).
Data Collection and Analysis Methods:
- Die Material Study: Survey of candidate high-temperature die materials, 3-D thermal modeling of die thermal profiles, and experimental testing of die materials with molten copper.
- Motor Performance Testing: Dynamometer efficiency tests (IEEE Specification 112, Test Method B, and IEC 34-2 test method) were conducted on motors with die-cast copper rotors and compared to aluminum rotor motors. Loss segregation analysis was performed.
Research Topics and Scope:
The research covered die materials for copper die casting, die heating technology, motor performance testing (efficiency, torque, temperature rise, slip, power factor), and motor design optimization for copper rotors. The scope included 60 Hz and 400 Hz motors.
5. Key Results:
Key Results:
- Die Material: Nickel-base alloys (INCONEL alloys 617, 625, and Haynes alloy 230) operated at elevated temperatures (600-650°C) showed promise for extended die life in copper die casting. A practical die heating and insulation design was developed.
- Motor Performance (15 Hp motor): Copper rotors showed a 40% reduction in rotor resistance losses (I²R), a 14% reduction in total losses, a 1.2 percentage point increase in efficiency, and a nearly 5°C reduction in temperature rise.
- Motor Performance(SEW Eurodrive): Copper rotors motors have higher efficiency while maintaining the outer motor dimensions standard for aluminum.
- Motor Weight and Cost: Modeling showed that copper rotor motors could be built lighter (18-20%) and less expensively (14-18%) than aluminum rotor motors at the same efficiency, when frame size reduction was possible.
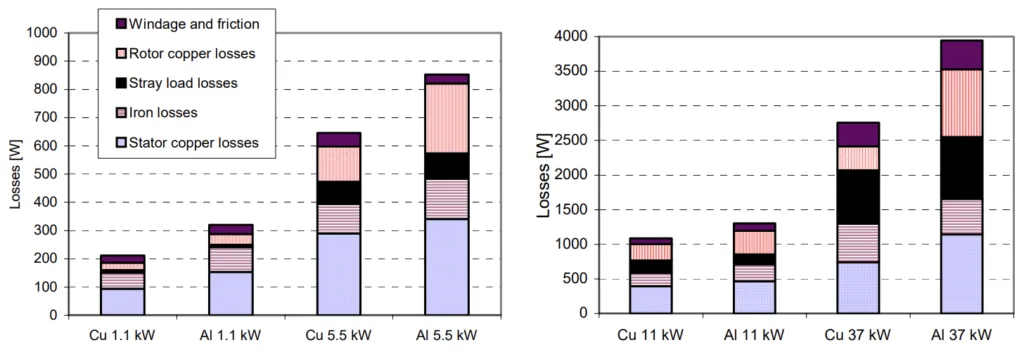
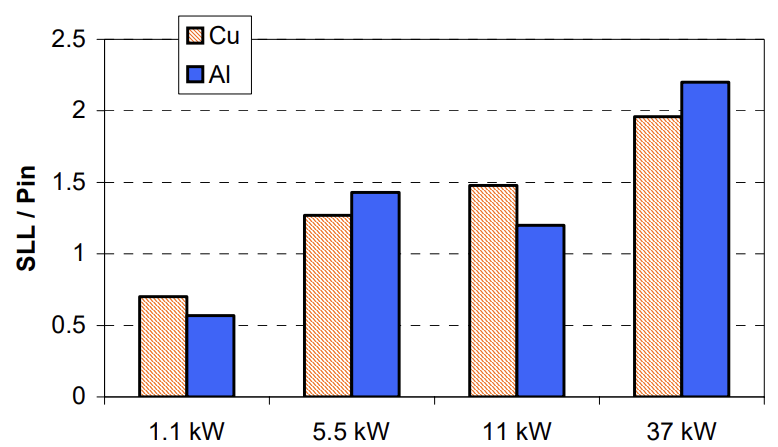
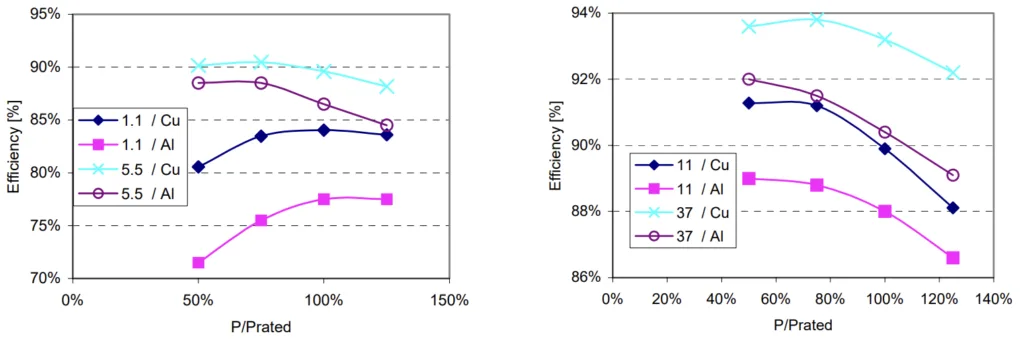
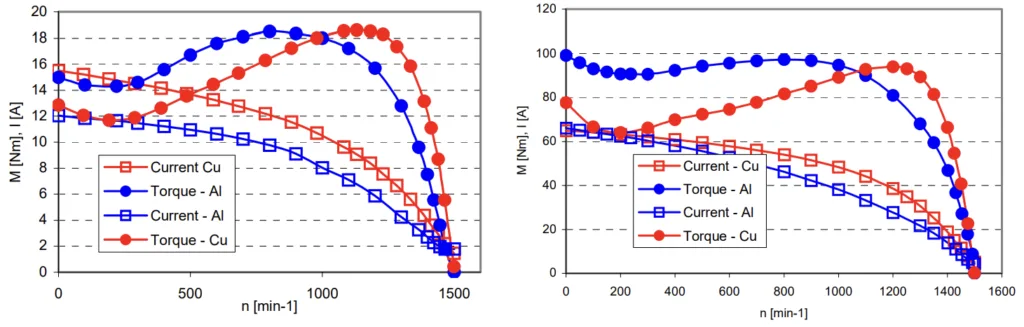
Standard efficiency Al motor (blue); Cu high effficiency motor (red).
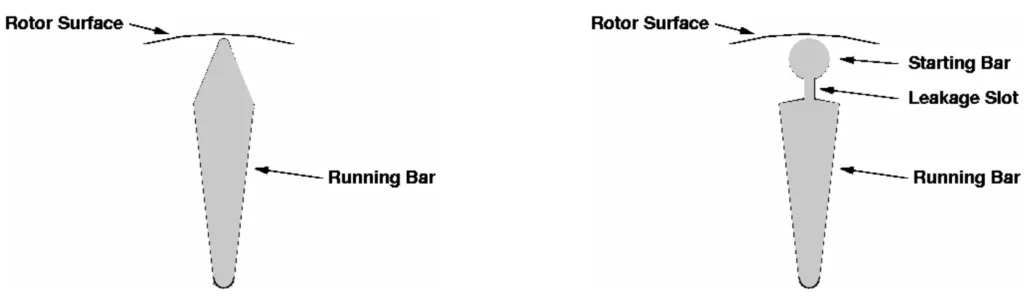
Figure Name List:
- Figure 1. Schematic illustration of the placement of electric resistance heaters and insulation in the die material testing and now being adopted commercially by motor manufacturers.
- Figure 2. Loss distributions at 60 Hz for the four SEW motors, copper rotor versions compared to the aluminum rotor lower efficiency standard line.
- Figure 3. Stray load losses per unit input power for the four SEW motors sizes.
- Figure 4. Efficiency dependence on out put power at 60 Hz.
- Figure 5. Torque-speed and current-speed curves for1.1 kW motors (left) and 5.5 kW motors (right). Standard efficiency Al motor (blue); Cu high effficiency motor (red).
- Figure 6. Aluminum conductor bar left and copper bar right.
6. Conclusion:
Summary of Key Results:
Die-cast copper rotors significantly improve motor efficiency and reduce operating temperature, leading to potential increases in motor life. A heated nickel-base alloy die system significantly improves die life. Copper rotor motors can be lighter and less expensive than comparable aluminum rotor motors.
Limitations of the Study:
The 15 Hp motor tests used laminations designed for aluminum, not optimized for copper. Torque was reduced in the 15 Hp motor tests, requiring further design adjustments. Long-term die life in production runs needs further validation.
7. Future Follow-up Research:
Directions for Follow-up Research:
- Further optimization of rotor slot design for copper to improve torque characteristics.
- Long-term production runs to validate die life.
- Investigation of the application of copper rotors in a wider range of motor sizes and types.
Areas for Further Exploration:
- Quantifying the precise increase in motor life due to reduced operating temperatures.
- Exploring the potential for further weight and cost reductions through optimized motor design.
8. References:
- Brush, E.F., jr., D.T. Peters, J.G. Cowie, M. Doppelbauer, and R. Kimmich, “Recent Advances in Development of the Die-cast Copper Rotor Motor,” Proceedings of the International Conference on Electric Machines, Crakow, Poland, 2004.
- Cowie, J.G., D.T. Peters and D.T. Brender, “Die-cast Copper rotors for Improved Motor Performance," IEEE Pulp and Paper Conference. Charleston, SC, 2003.
- Kirtley, J.L., Jr., “Designing Squirrel Cage Rotor Slots with High Conductivity,” Proceedings of the International Conference on Electric Machines, Crakow, Poland, 2004.
- Peters, D.T, J.G. Cowie, E.F. Brush, Jr. and S.P. Midson, “Advances in Pressure Die Casting of Electrical Grade Copper," Amer. Foundry Society Congress Paper No. 02-002, Kansas City, Mo., 2002.
- Peters, D.T., J.G. Cowie, E.F. Brush, Jr. and S.P. Midson, "Use of High Temperature Die Materials and Hot Dies for High Pressure Die Casting Pure Copper and Copper Alloys," Trans. of the North Amer. Die Casting Assoc. Die Casting Congress, Rosemont, II. 2002.
9. Copyright:
- This material is a paper by "C. Stark, J. G. Cowie, D. T. Peters, and E. F. Brush, Jr.". Based on "Copper in the Rotor for Lighter, Longer Lasting Motors".
- Source of the paper: [The provided text does not contain a DOI URL]
This material is summarized based on the above paper, and unauthorized use for commercial purposes is prohibited.
Copyright © 2025 CASTMAN. All rights reserved.