This article introduces the paper "A Review of Recent Trends in High Efficiency Induction Motor Drives".
1. Overview:
- Title: A Review of Recent Trends in High Efficiency Induction Motor Drives
- Author: Mohamed Ahmed Azab
- Publication Year: 2025
- Journal/Conference: Preprints.org
- Keywords: electric drives; ED; AC drives; IM; induction motor; electric vehicles; EV; efficiency; energy saving; energy efficiency; power electronics; wide bandgap semiconductors; electric motors; field oriented control; direct torque control; model predictive control; industrial automation; regenerative braking; SDG; sustainable development goals; UN; united nations
2. Research Background:
Induction Motor (IM) drives are a crucial technology in modern industry, powering various applications including material handling, food and beverage processing, and electric transportation systems like EVs and e-trucks. Recently, there's a growing focus on high-efficiency IM drive systems to reduce energy and fuel consumption, aligning with global sustainability initiatives.
This paper reviews recent trends and advancements in high-efficiency IM drives from 2017 to 2024. Existing research primarily focuses on the development of high-efficiency motors, the utilization of efficient Wide Band Gap (WBG) semiconductor devices in inverter topologies, and common control strategies for achieving high-performance drives.
However, a significant limitation of previous studies is the lack of a comprehensive comparison of control techniques adopted in industrial IM drive products from various manufacturers. Furthermore, in-depth discussions on regenerative braking methods and energy-saving algorithms contributing to efficiency improvements are often insufficient.
This research aims to address these gaps and provide a more comprehensive understanding of high-efficiency IM drive technology.
3. Research Objectives and Questions:
- Research Objective: This study comprehensively reviews and analyzes recent trends and advancements in high-efficiency induction motor drives from 2017 to 2024. This includes examining advancements in high-efficiency motor design, the utilization of WBG semiconductor devices in power electronic converters, commonly used control strategies for high-performance drives, and the adoption of energy-saving algorithms and regenerative braking techniques. The study also identifies key industrial IM drive manufacturers and their respective control techniques, comparing their pros and cons.
- Key Research Questions:
- What are the recent trends in the design and manufacturing of high-efficiency induction motors?
- How is the utilization of WBG semiconductor devices in high-efficiency power electronic converters progressing?
- What are the state-of-the-art control strategies used to achieve high-performance IM drives? What are the advantages and disadvantages of each strategy?
- Who are the key industrial IM drive manufacturers, and what control techniques are adopted in their products?
- What are the recent trends in regenerative braking methods and energy-saving algorithms that contribute to improved energy efficiency?
- Research Hypothesis: The integrated application of high-efficiency induction motors, WBG semiconductor devices, advanced control strategies, and regenerative braking techniques will significantly enhance the overall energy efficiency of IM drive systems.
4. Research Methodology:
- Research Design: This study is based on a comprehensive literature review of high-efficiency IM drives from 2017 to 2024. A systematic approach was employed to identify relevant publications.
- Data Collection Methods: Data were collected from a wide range of sources including journal articles, conference proceedings, technical reports, and patents. Keywords such as "high-efficiency induction motor," "wide bandgap semiconductor," "power electronics," "control techniques," "regenerative braking," and "energy saving" were used in literature searches.
- Analysis Methods: Both quantitative and qualitative analyses were performed. Quantitative analysis involved examining publication trends of high-efficiency IM drive-related research, the emergence timeline of key technologies, and the rate of technological advancements. Qualitative analysis involved a detailed review of the content, methodologies, and results of individual studies to identify key technological trends, assess the advantages and disadvantages of different techniques, and project future development directions. The performance and characteristics of various control techniques (FOC, DTC, MPC) were comparatively analyzed.
- Study Population and Scope: The study population consists of publications on high-efficiency IM drives published from 2017 to 2024. The scope encompasses high-efficiency IM design, WBG power semiconductor utilization, advanced control techniques, regenerative braking methods, and energy-saving algorithms.
5. Main Research Findings:
Advancements in high-efficiency IM drive systems are driven by developments in high-efficiency motor design, WBG power semiconductors, and advanced control techniques. High-efficiency IMs feature design improvements such as longer core length, thinner core laminations, high-grade core materials, wider stator slots with optimized shapes, thicker stator windings, and lower rotor bar resistance. WBG devices (SiC and GaN) offer superior characteristics compared to conventional silicon-based devices, including wider band gaps, higher voltage withstand capability, higher switching frequencies, and lower power losses. Key control techniques investigated include Field Oriented Control (FOC), Direct Torque Control (DTC), and Model Predictive Control (MPC), each with its own advantages and limitations. Regenerative braking and energy-saving algorithms also play a crucial role in enhancing overall energy efficiency.
- Key Findings: The combination of high-efficiency IMs, WBG power semiconductors, advanced control techniques (FOC, DTC, MPC), and regenerative braking strategies significantly improves the overall efficiency of IM drive systems.
- Quantitative/Qualitative Analysis Results: Analysis of numerous research papers confirmed that the adoption of WBG power semiconductors and advanced control techniques substantially contributes to enhancing the efficiency of IM drive systems. A comparative analysis of different control techniques highlighted their respective strengths and weaknesses.
- Data Interpretation: Literature analysis revealed the advancement trends in high-efficiency IM drive technology and provided insights into future technological developments.
- Figure Name List:
- Figure 1. The Estimated Global Market Size of Electrical Drives,
- Figure 2. The Estimated Global Market Size of AC Drives,
- Figure 3. Block Diagram of a Typical Electric Drive System,
- Figure 4. Cross Section of Stator of 3-F Induction Motor,
- Figure 5. Rotor of a Squirrel Cage 3-F Induction Motor,
- Figure 6. Simplified Energy Diagram and Band Gap Energy of Si, WBG, and Insulators,
- Figure 7. Phasor diagram of stator current components with FOC,
- Figure 8. Block Diagram of the Basic Scheme of FOC of IM Drives,
- Figure 9. Block Diagram of Conventional DTC System of IM Drive,
- Figure 10. Stator Flux Vector Lies in Sector 1,
- Figure 11. Control of Motor Stator Flux and Torque In Sector 1,
- Figure 12. Effects of Inverter Discrete Voltage Vectors On Stator Flux & Torque In Sector 1,
- Figure 13. Trajectory of stator flux vector under DTC with conventional two-level VSI,
- Figure 14. Block Diagram of FCS-MPC System of IM Drive
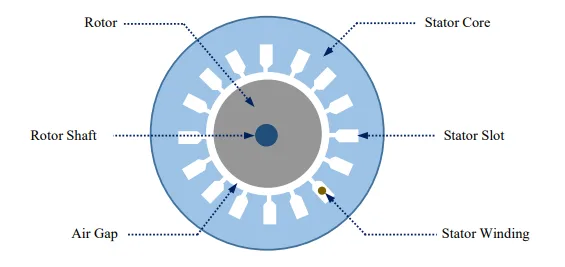
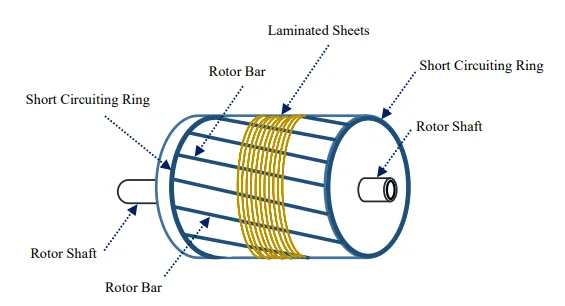
6. Conclusions and Discussion:
This research provides a comprehensive analysis of recent trends and technological advancements in high-efficiency induction motor drives. The advancements in high-efficiency IM design, WBG power semiconductors, and sophisticated control techniques (FOC, DTC, and MPC) have significantly contributed to improved energy efficiency. Regenerative braking plays a crucial role in further enhancing energy savings. The findings offer valuable insights for industrial applications, particularly emphasizing the strategic adoption of WBG power semiconductors and advanced control algorithms to accelerate the development and commercialization of high-efficiency IM drives.
- Summary of Main Findings: The integrated use of high-efficiency IMs, WBG power semiconductors, and advanced control techniques (FOC, DTC, and MPC) significantly enhances the efficiency of IM drive systems. Regenerative braking contributes substantially to energy savings.
- Academic Significance: This study systematically organizes and analyzes the latest technological trends in high-efficiency IM drives, providing a valuable resource for future research and development in this field.
- Practical Implications: Industrial stakeholders should adopt strategies focusing on the integration of high-efficiency IMs, WBG power semiconductors, and advanced control techniques to maximize energy efficiency. The effective implementation of regenerative braking is also crucial.
- Limitations of the Study: This study is a literature review and does not include experimental validation of IM drive performance. Furthermore, a deeper analysis of the manufacturing costs and reliability of WBG power semiconductors is needed.
7. Future Research Directions:
- Future Research Directions: Future research should focus on experimental validation of the findings through real-world performance testing of IM drive systems under various operating conditions. Further research is needed on cost-effectiveness and reliability analysis of WBG power semiconductors. Research should also explore the development and optimization of high-efficiency IM drive systems for specific applications and operating environments.
- Areas Requiring Further Investigation: Future studies should investigate the performance of high-efficiency IM drives under various environmental conditions (temperature, humidity, vibration, etc.), perform a more comprehensive comparison and optimization of different control algorithms, and conduct long-term reliability tests on WBG power semiconductor devices.
8. References:
This paper cites 291 references, covering various aspects of high-efficiency IM drives, including high-efficiency motor design, WBG power semiconductors, advanced control techniques, regenerative braking, and energy-saving algorithms.
References
- Electric Drives Market Analysis Report: https://www.mordorintelligence.com/industry reports/electric‐drives‐market.
- Global AC Drives Industry Research Report, Growth Trends and Competitive Analysis 2022‐2028.
https://www.360researchreports.com/global‐ac‐drives‐industry‐21727719, September 2022. - UN‐SDGs report 2024: https://unstats.un.org/sdgs/files/report/2024/SG‐SDG‐Progress‐Report‐2024‐
advanced‐unedited‐version.pdf - UN‐SDGs report 2023: https://unstats.un.org/sdgs/report/2023/The‐Sustainable‐Development‐Goals‐Report‐2023.pdf.
Zhao, J.; Xi, X.; Na, Q.; Wang, S.; Kadry, S.N.; Kumar, P.M. The technological innovation of hybrid and
plug‐in electric vehicles for environment carbon pollution control. Environ. Impact Assess. Rev. 2021, 86, 106506. - Fuinhas, J.A.; Koengkan, M.; Leitão, N.C.; Nwani, C.; Uzuner, G.; Dehdar, F.; Relva, S.; Peyerl, D. Effect of
Battery Electric Vehicles on Greenhouse Gas Emissions in 29 European Union Countries. Sustainability 2021, 13, 13611. https://doi.org/10.3390/su132413611. - Azab, M. Low‐Cost DTC Drive Using Four‐Switch Inverter for Low Power Ranges. Vehicles 2024, 6, 895‐ https://doi.org/10.3390/vehicles6020043.
- Parv, A.L.; Daicu, R.; Dragoi, M.V.; Rusu, M.; Oancea, G. , “ A Method to Design Assembling Lines for
Super Premium Efficiency Motors. Processes 2023, 11, 215. https://doi.org/10.3390/pr11010215 - M. Dems and K. Komeza, “Designing an Energy‐Saving Induction Motor Operating in a Wide Frequency Range,” in IEEE Transactions on Industrial Electronics, vol. 69, no. 5, pp. 4387‐4397, May 2022, doi:10.1109/TIE.2021.3082057.
- Zibo Chen, Alex Q. Huang, “Extreme high efficiency enabled by silicon carbide (SiC) power devices,”
Materials Science in Semiconductor Processing, Volume 172, 2024, 108052,
https://doi.org/10.1016/j.mssp.2023.108052. - Y. Xu et al., “Impact of High Switching Speed and High Switching Frequency of Wide‐Bandgap Motor
Drives on Electric Machines,” in IEEE Access, vol. 9, pp. 82866‐82880, 2021, doi:
10.1109/ACCESS.2021.3086680. - Takahashi, I., Noguchi, T.: “A new quick‐response and high‐efficiency control strategy of an induction
motor”, IEEE Trans. Indus. App., 1986, 22, (5), pp. 820–827. - G. Mirzaeva and Y. Mo, “Model Predictive Control for Industrial Drive Applications,” in IEEE Transactions on Industry Applications, vol. 59, no. 6, pp. 7897‐7907, Nov.‐Dec. 2023, doi: 10.1109/TIA.2023.3299887.
- I. Karatzaferis, E. C. Tatakis and N. Papanikolaou, “Investigation of Energy Savings on Industrial Motor
Drives Using Bidirectional Converters,” in IEEE Access, vol. 5, pp. 17952‐17961, 2017, doi:
10.1109/ACCESS.2017.2748621. - Fethi Farhani, Abderrahmen Zaafouri, Abdelkader Chaari, Real time induction motor efficiency
optimization, Journal of the Franklin Institute, Volume 354, Issue 8, 2017, Pages 3289‐3304,
https://doi.org/10.1016/j.jfranklin.2017.02.012. - https://www.ti.com/lit/pdf/sprabq0.
- https://www.typhoon‐hil.com/solutions/power‐electronics/electric‐motor‐drives/
- [18]Wu, Z., Xie, B., Li, Z., Mitsuoka, M., Inoue, E., Okayasu, T., & Hirai, Y. (2019). DSPACE based Hardware in the loop Testing Platform for Powertrain Management Unit of Electric Tractor. Journal of the Faculty of Agriculture, Kyushu University, 64(2), 309‐317. https://doi.org/10.5109/2340993
- H. ‐J. Kim and C. ‐S. Lee, “Shape Parameters Design forImproving Energy Efficiency of IPM Traction Motor for EV,” in IEEE Transactions on Vehicular Technology, vol. 70, no. 7, pp. 6662‐6673, July 2021, doi:10.1109/TVT.2021.3089576.
- Shyi‐Min Lu, “A review of high‐efficiency motors: Specification, policy, and technology,” Renewable and Sustainable Energy Reviews, Vol.59, Pages 1‐12, 2016, https://doi.org/10.1016/j.rser.2015.12.360.
- M. D. Nardo, A. Marfoli, M. Degano and C. Gerada, “Rotor Slot Design of Squirrel Cage Induction Motors With Improved Rated Efficiency and Starting Capability,” in IEEE Transactions on Industry Applications, vol.58, no. 3, pp. 3383‐3393, May‐June 2022, doi: 10.1109/TIA.2022.3147156.
- A. Marfoli, M. D. Nardo, M. Degano, C. Gerada and W. Chen, “Rotor Design Optimization of Squirrel Cage Induction Motor—Part I: Problem Statement,” in IEEE Transactions on Energy Conversion, vol. 36, no. 2, pp. 1271‐1279, June 2021, doi: 10.1109/TEC.2020.3019934.
- J. Zhang et al., “Optimization and Experimental Validation of Amorphous Alloy High‐Speed
Asynchronous Motor for Simultaneous Reduction on Core and Copper Losses,” in IEEE Access, vol. 11, pp. 101112‐101122, 2023, doi: 10.1109/ACCESS.2023.3312992. - M. Popescu, L. Di Leonardo, G. Fabri, G. Volpe, N. Riviere and M. Villani, “Design of Induction Motors
With Flat Wires and Copper Rotor for E‐Vehicles Traction System,” in IEEE Transactions on Industry
Applications, vol. 59, no. 3, pp. 3889‐3900, May‐June 2023, doi: 10.1109/TIA.2023.3256391.
J. Mei, C. H. T. Lee and J. L. Kirtley, “Design of Axial Flux Induction Motor With Reduced Back Iron for
Electric Vehicles,” in IEEE Transactions on Vehicular Technology, vol. 69, no. 1, pp. 293‐301, Jan. 2020, doi:10.1109/TVT.2019.2954084. - T. ‐V. Tran, E. Nègre, K. Mikati, P. Pellerey and B. Assaad, “Optimal Design of TEFC Induction Machine
and Experimental Prototype Testing for City Battery Electric Vehicle,” in IEEE Transactions on Industry
Applications, vol. 56, no. 1, pp. 635‐643, Jan.‐Feb. 2020, doi: 10.1109/TIA.2019.2943447. - C. P. Ion and I. Peter, “Manufacturing of induction motors with Super Premium Efficiency,” 2022
International Conference and Exposition on Electrical And Power Engineering (EPE), Iasi, Romania, 2022, pp. 047‐050, doi: 10.1109/EPE56121.2022.9959834. - M. ‐S. Kim, J. ‐H. Park, K. ‐S. Lee, S. ‐H. Lee and J. ‐Y. Choi, “Performance Characteristics of the Rotor
Conductor of an IE4 Class Induction Motor With Varying Al‐Cu Ratio,” in IEEE Transactions on Magnetics, vol. 58, no. 8, pp. 1‐6, Aug. 2022, Art no. 8203406, doi: 10.1109/TMAG.2022.3153335. - T. Gundogdu and S. Suli, “Role of End‐Ring Configuration in Shaping IE4 Induction Motor Performance,” in CES Transactions on Electrical Machines and Systems, vol. 8, no. 3, pp. 245‐254, September 2024, doi:10.30941/CESTEMS.2024.00014.
- M. Aishwarya, R.M. Brisilla, Design of Energy‐Efficient Induction motor using ANSYS software, Results in Engineering, Volume 16, 2022, https://doi.org/10.1016/j.rineng.2022.100616.
- L. Alberti and D. Troncon, “Design of Electric Motors and Power Drive Systems According to Efficiency
Standards,” in IEEE Transactions on Industrial Electronics, vol. 68, no. 10, pp. 9287‐9296, Oct. 2021, doi:10.1109/TIE.2020.3020028. - Marfoli, A.; DiNardo, M.; Degano, M.; Gerada, C.; Jara, W. Squirrel Cage Induction Motor: A Design‐Based Comparison between Aluminium and Copper Cages. IEEE Open J. Ind. Appl. 2021, 2, 110–120.
- A. Cavagnino, S. Vaschetto, L. Ferraris, Z. Gmyrek, E. B. Agamloh and G. Bramerdorfer, “Striving for the
Highest Efficiency Class With Minimal Impact for Induction Motor Manufacturers,” in IEEE Transactions on Industry Applications, vol. 56, no. 1, pp. 194‐204, Jan.‐Feb. 2020, doi: 10.1109/TIA.2019.2949262. - Usha, S.; Subramani, C.; Raman, A.; Bhaduri, M.; Doss, M.A.N.; Puri, R. Efficiency Improvement of
Induction Motor Through Altered Design. Int. J. Recent Technol. Eng. 2019, 8, 3429–3435. - K. Khan, S. Shukla and B. Sing, “Design and Development of High Efficiency Induction Motor for PV Array Fed Water Pumping,” 2018 IEEE International Conference on Power Electronics, Drives and Energy Systems
(PEDES), Chennai, India, 2018, pp. 1‐6, doi: 10.1109/PEDES.2018.8707578. - I. Tig, M. Imeryuz, M. Akcomak and A. Polat, “Design of High Efficient 1.1 kW 8 Pole Induction Motor for Industrial Application,” 2023 14th International Conference on Electrical and Electronics Engineering (ELECO),
Bursa, Turkiye, 2023, pp. 1‐5, doi: 10.1109/ELECO60389.2023.10416050 - Asgharpour‐Alamdari, Hossein, Yousef Alinejad‐Beromi, and Hamid Yaghobi. “Improvement of induction motor operation using a new winding scheme for reduction of the magnetomotive force distortion.” IET Electric Power Applications 12.3 (2018): 323‐331.
- H. M. Kim, K. W. Lee, D. G. Kim, J. H. Park and G. S. Park, “Design of Cryogenic Induction Motor
Submerged in Liquefied Natural Gas,” in IEEE Transactions on Magnetics, vol. 54, no. 3, pp. 1‐4, March 2018, Art no. 8201204, doi: 10.1109/TMAG.2017.2751099. - C. Verucchi et al., “Efficiency optimization in small induction motors using magnetic slot wedges”, Electric Power Systems Research, vol. 152, pp. 1‐8, 2017.
- L. Shao, A. E. H. Karci, D. Tavernini, A. Sorniotti and M. Cheng, “Design Approaches and Control Strategies for Energy‐Efficient Electric Machines for Electric Vehicles—A Review,” in IEEE Access, vol. 8, pp. 116900‐116913, 2020, doi: 10.1109/ACCESS.2020.2993235.
- Dems, M.; Komeza, K.; Szulakowski, J.; Kubiak, W. Increase the Efficiency of an Induction Motor Feed from Inverter for Low Frequencies by Combining Design and Control Improvements. Energies 2022, 15, 530. https://doi.org/10.3390/en15020530
- U. Sharma and B. Singh, “Design and Development of Energy Efficient Single Phase Induction Motor For Ceiling Fan Using Taguchi’s Orthogonal Arrays,” in IEEE Transactions on Industry Applications, vol. 57, no. 4, pp. 3562‐3572, July‐Aug. 2021, doi: 10.1109/TIA.2021.3072020.
N. Zhao and N. Schofield, “An Induction Machine Design With Parameter Optimization for a 120‐kW
Electric Vehicle,” in IEEE Transactions on Transportation Electrification, vol. 6, no. 2, pp. 592‐601, June 2020,
doi: 10.1109/TTE.2020.2993456. - A. M. Silva, F. J. T. E. Ferreira, M. V. Cistelecan and C. H. Antunes, “Multiobjective Design Optimization of Generalized Multilayer Multiphase AC Winding,” in IEEE Transactions on Energy Conversion, vol. 34, no. 4, pp. 2158‐2167, Dec. 2019, doi: 10.1109/TEC.2019.2935009.
- M. Aishwarya and R. M. Brisilla, “Design and Fault Diagnosis of Induction Motor Using ML‐Based
Algorithms for EV Application,” in IEEE Access, vol. 11, pp. 34186‐34197, 2023, doi:
10.1109/ACCESS.2023.3263588. - W. Xu, X. Xiao, G. Du, D. Hu and J. Zou, “Comprehensive Efficiency Optimization of Linear Induction
Motors for Urban Transit,” in IEEE Transactions on Vehicular Technology, vol. 69, no. 1, pp. 131‐139, Jan. 2020,
doi: 10.1109/TVT.2019.2953956. - Farshid Mahmouditabar, Nick J. Baker, Design Optimization of Induction Motors with Different Stator Slot Rotor Bar Combinations Considering Drive Cycle, Energies, 10.3390/en17010154, 17, 1, (154), (2023).
- A. Lei, C.‐X. Song, Y.‐L. Lei and Y. Fu, “Design optimization of vehicle asynchronous motors based on
fractional harmonic response analysis”, Mech. Sci., vol. 12, no. 1, pp. 689‐700, Jul. 2021. - Bortoni, Edson C., et al. “Evaluation of manufacturers strategies to obtain high‐efficient induction motors.” Sustainable Energy Technologies and Assessments 31 (2019): 221‐227
- M. A. Kabir, M. Z. M. Jaffar, Z. Wan and I. Husain, “Design, Optimization, and Experimental Evaluation of Multilayer AC Winding for Induction Machine,” in IEEE Transactions on Industry Applications, vol. 55, no. 4, pp. 3630‐3639, July‐Aug. 2019, doi: 10.1109/TIA.2019.2910775.
- Bianchini, C.; Vogni, M.; Torreggiani, A.; Nuzzo, S.; Barater, D.; Franceschini, G. Slot Design Optimization for Copper Losses Reduction in Electric Machines for High Speed Applications. Appl. Sci. 2020, 10, 7425.
https://doi.org/10.3390/app10217425. - M.J. Akhtar, R.K. Behera, “Optimal design of stator and rotor slot of induction motor for electric vehicle applications.” IET Electr. Syst. Transp. 2019;9 pp.35‐43.
- S. Mallik et al., “Efficiency and Cost Optimized Design of an Induction Motor Using Genetic Algorithm,” in IEEE Transactions on Industrial Electronics, vol. 64, no. 12, pp. 9854‐9863, Dec. 2017, doi:10.1109/TIE.2017.2703687.
- Min‐Seok Kim, Chang‐Eob Kim, “Multi‐Objective Optimum Design of Premium High Efficiency Induction Motor Using Parameter Learning,”The Transactions of the Korean Institute of Electrical Engineers KIEE Vol. 70, No. 7, p.991‐998, June 2021.http://doi.org/10.5370/KIEE.2021.70.7.991.
- I. Laouar and A. Boukadoum, “Design Optimization of a Three‐Phase Squirrel‐Cage Induction Motor by Algorithm Harmony Search,” 2022 IEEE International Conference on Electrical Sciences and Technologies in Maghreb (CISTEM), Tunis, Tunisia, 2022, pp. 1‐6, doi: 10.1109/CISTEM55808.2022.10044025.
- R. Srimathi, P. Ponmurugan, A. Iqbal, K. K. V, M. Lakshmanan and E. S. Nadin, “A More Efficient Induction Machine based on Hill Climbing Local Search Optimization,” 2022 International Virtual Conference on Power Engineering Computing and Control: Developments in Electric Vehicles and Energy Sector for Sustainable Future (PECCON), Chennai, India, 2022, pp. 1‐6, doi: 10.1109/PECCON55017.2022.9851011.
- Bian, Y., Yang, Z., Sun, X. et al. Speed Sensorless Control of a Bearingless Induction Motor Based on
Modified Robust Kalman Filter. J. Electr. Eng. Technol. 19, 1179–1190 (2024). https://doi.org/10.1007/s42835‐023‐01649‐y. - Su, Y., Yang, Z., Sun, X., & Shen, Z. (2024). Direct torque control of bearingless induction motor based on super‐twisting sliding mode control. Journal of Control and Decision, 1–11.
https://doi.org/10.1080/23307706.2024.2403487. - X. Ye, X. Tang, K. Xing, H. Wang, J. Yao and T. Zhang, “Repetitive Control for Vibration Suppression of
Bearingless Induction Motor,” in IEEE Access, vol. 12, pp. 60532‐60540, 2024, doi:
10.1109/ACCESS.2024.3391292. - Su, Y., Yang, Z., Sun, X. et al. Backstepping control of a bearingless induction motor based on a linear
extended state observer. Electr Eng 105, 4569–4579 (2023). https://doi.org/10.1007/s00202‐023‐01958‐5.
Z. Yang, J. Jia, X. Sun and T. Xu, “A Fuzzy‐ELADRC Method for a Bearingless Induction Motor,” in IEEE
Transactions on Power Electronics, vol. 37, no. 10, pp. 11803‐11813, Oct. 2022, doi: 10.1109/TPEL.2022.3177204. - J. Chen, Y. Fujii, M. W. Johnson, A. Farhan and E. L. Severson, “Optimal Design of the Bearingless Induction Motor,” in IEEE Transactions on Industry Applications, vol. 57, no. 2, pp. 1375‐1388, March‐April 2021, doi:
10.1109/TIA.2020.3044970. - J. Chen and E. L. Severson, “Design and Modeling of the Bearingless Induction Motor,” 2019 IEEE
International Electric Machines & Drives Conference (IEMDC), San Diego, CA, USA, 2019, pp. 343‐350, doi:10.1109/IEMDC.2019.8785270. - A. Sinervo and A. Arkkio, “Rotor Radial Position Control and its Effect on the Total Efficiency of a
Bearingless Induction Motor With a Cage Rotor,” in IEEE Transactions on Magnetics, vol. 50, no. 4, pp. 1‐9, April 2014, Art no. 8200909, doi: 10.1109/TMAG.2013.2291224. - J. Chen, J. Zhu and E. L. Severson, “Review of Bearingless Motor Technology for Significant Power
Applications,” in IEEE Transactions on Industry Applications, vol. 56, no. 2, pp. 1377‐1388, March‐April 2020, doi: 10.1109/TIA.2019.2963381. - E. L. Severson, R. Nilssen, T. Undeland and N. Mohan, “Design of Dual Purpose No‐Voltage Combined Windings for Bearingless Motors,” in IEEE Transactions on Industry Applications, vol. 53, no. 5, pp. 4368‐4379, Sept.‐Oct. 2017, doi: 10.1109/TIA.2017.2706653.
- J. Chen, M. W. Johnson, A. Farhan, Z. Wang, Y. Fujii and E. L. Severson, “Reduced Axial Length Pole‐
Specific Rotor for Bearingless Induction Machines,” in IEEE Transactions on Energy Conversion, vol. 37, no. 4, pp. 2285‐2297, Dec. 2022, doi: 10.1109/TEC.2022.3172017. - Z. Yang, Q. Ding, X. Sun and C. Lu, “Design and Analysis of a Three‐Speed Wound Bearingless Induction Motor,” in IEEE Transactions on Industrial Electronics, vol. 69, no. 12, pp. 12529‐12539, Dec. 2022, doi:10.1109/TIE.2021.3128900.
- Fang, W., Yang, Z., Sun, X. et al. Speed Sensorless Control of Bearingless Induction Motors Based on
Adaptive Flux Observer. J. Electr. Eng. Technol. 17, 1803–1813 (2022). https://doi.org/10.1007/s42835‐022‐01012‐7. - Carvalho Souza, F.E.; Silva, W.; Ortiz Salazar, A.; Paiva, J.; Moura, D.; Villarreal, E.R.L. A Novel Driving
Scheme for Three‐Phase Bearingless Induction Machine with Split Winding. Energies 2021, 14, 4930.
https://doi.org/10.3390/en14164930. - Ye, X., & Yang, Z. (2019). Development of bearingless induction motors and key technologies. IEEE Access, 121055–121066. https://doi.org/10.1109/ACCESS.2019.2937118.
- J. Lu, Z. Yang, X. Sun, C. Bao and X. Chen, “Direct Levitation Force Control for a Bearingless Induction
Motor Based on Model Prediction,” in IEEE Access, vol. 7, pp. 65368‐65378, 2019, doi:
10.1109/ACCESS.2019.2917331. - J. Chen and E. L. Severson, “Optimal Design of the Bearingless Induction Motor for Industrial
Applications,” 2019 IEEE Energy Conversion Congress and Exposition (ECCE), Baltimore, MD, USA, 2019, pp. 5265‐5272, doi: 10.1109/ECCE.2019.8912543. - Nunes, E.A.D.F.; Salazar, A.O.; Villarreal, E.R.L.; Souza, F.E.C.; Dos Santos Júnior, L.P.; Lopes, J.S.B.; Luque, J.C.C. Proposal of a fuzzy controller for radial position in a bearingless induction motor. IEEE Access 2019, 7, 114808–114816.
- Asama, J.; Oi, T.; Oiwa, T.; Chiba, A. Simple Driving Method for a 2‐DOF Controlled Bearingless Motor
Using One Three‐Phase Inverter. IEEE Trans. Ind. Appl. 2018, 54, 4365–4376. - Yang, Zebin, Chen, Lin, Sun, Xiaodong, Sun, Weiming, Zhang, Dan, A Bearingless Induction Motor Direct Torque Control and Suspension Force Control Based on Sliding Mode Variable Structure, Mathematical Problems in Engineering, 2017, 2409179, 11 pages, 2017. https://doi.org/10.1155/2017/2409179
- P. ‐W. Han, U. ‐J. Seo, S. Paul and J. Chang, “Computationally Efficient Stator AC Winding Loss Analysis Model for Traction Motors Used in High‐Speed Railway Electric Multiple Unit,” in IEEE Access, vol. 10, pp. 28725‐28738, 2022, doi: 10.1109/ACCESS.2022.3158647.
- J. M. Tabora et al., “Assessing Energy Efficiency and Power Quality Impacts Due to High‐Efficiency Motors Operating Under Nonideal Energy Supply,” in IEEE Access, vol. 9, pp. 121871‐121882, 2021, doi:10.1109/ACCESS.2021.3109622.
Julio R. Gómez, et. Al., “Assessment criteria of the feasibility of replacement standard efficiency electric motors with high‐efficiency motors,” Energy, Volume 239, Part A, 121877, 2022,
https://doi.org/10.1016/j.energy.2021.121877. - Yang, Z., Sun, C., Sun, X., & Sun, Y. , An improved dynamic model for bearingless induction motor
considering rotor eccentricity and load change. IEEE Transactions on Industrial Electronics, 69, 3439–3448.
https://doi.org/10.1109/TIE.2021.3071712. - J. Mei, Y. Zuo, C. H. T. Lee and J. L. Kirtley, “Modeling and Optimizing Method for Axial Flux Induction
Motor of Electric Vehicles,” in IEEE Transactions on Vehicular Technology, vol. 69, no. 11, pp. 12822‐12831, Nov. 2020, doi: 10.1109/TVT.2020.3030280. - M. Z. Ali, M. N. S. K. Shabbir, X. Liang, Y. Zhang and T. Hu, “Machine learning‐based fault diagnosis for single‐ and multi‐faults in induction motors using measured stator currents and vibration signals”, IEEE Trans. Ind. Appl., vol. 55, no. 3, pp. 2378‐2391, May 2019.
- Wang, K.; Huai, R.; Yu, Z.; Zhang, X.; Li, F.; Zhang, L. Comparison Study of Induction Motor Models
Considering Iron Loss for Electric Drives. Energies 2019, 12, 503. https://doi.org/10.3390/en12030503. - Liu, Y.; Bazzi, A.M. A General Analytical Three‐Phase Induction Machine Core Loss Model in the Arbitrary Reference Frame. IEEE Trans. Ind. Appl. 2017, 53, 4210–4220.
- Konda, Y.R.; Ponnaganti, V.K.; Reddy, P.V.S.; Singh, R.R.; Mercorelli, P.; Gundabattini, E.; Solomon, D.G.
Thermal Analysis and Cooling Strategies of High‐Efficiency Three‐Phase Squirrel‐Cage Induction
Motors—A Review. Computation 2024, 12, 6. https://doi.org/10.3390/computation12010006. - Madhavan, S.; P B, R.D.; Gundabattini, E.; Mystkowski, A. Thermal Analysis and Heat Management
Strategies for an Induction Motor, a Review. Energies 2022, 15, 8127. https://doi.org/10.3390/en15218127. - B. Assaad, K. Mikati, T. V. Tran and E. Negre, “Experimental Study of Oil Cooled Induction Motor for
Hybrid and Electric Vehicles,” 2018 XIII International Conference on Electrical Machines (ICEM),
Alexandroupoli, Greece, 2018, pp. 1195‐1200, doi: 10.1109/ICELMACH.2018.8507058. - Gundabattini, E.; Kuppan, R.; Solomon, D.G.; Kalam, A.; Kothari, D.; Abu Bakar, R. A review on methods
of finding losses and cooling methods to increase the efficiency of electric machines. Ain Shams Eng. J. 2021, 12, 497–505. - Cabral, P.; Adouni, A. Induction Motor Thermal Analysis Based on Lumped Parameter Thermal Network.
KnE Eng. 2020, 5, 451–464. - S. Zhong, C. Tschida and D. Bednarowski, “Thermal Analysis of Water‐Cooled Totally Enclosed Non‐
Ventilated Induction Motor,” SoutheastCon 2024, Atlanta, GA, USA, 2024, pp. 793‐798, doi:
10.1109/SoutheastCon52093.2024.10500195. - Madhavan, S., Devdatta P B, R., Konda, Y.R. et al. Thermal management analyses of induction motor
through the combination of air‐cooling and an integrated water‐cooling system. Sci Rep 13, 10125 (2023).
https://doi.org/10.1038/s41598‐023‐36989‐2. - L. F. D. Bucho, J. F. P. Fernandes, M. Biasion, S. Vaschetto and A. Cavagnino, “Experimental Assessment of Cryogenic Cooling Impact on Induction Motors,” in IEEE Transactions on Energy Conversion, vol. 37, no.
4, pp. 2629‐2636, Dec. 2022, doi: 10.1109/TEC.2022.3183939. - Deriszadeh, A.; de Monte, F. On heat transfer performance of cooling systems using nanofluid for electric motor applications. Entropy 2020, 22, 99.
- Abdullah, A.T.; Ali, A.M. Thermal analysis of a three‐phase induction motor based on motor‐CAD, flux2D, and Matlab. Indones. J. Electr. Eng. Comput. Sci. 2019, 15, 48–55.
- Adouni, A.; Marques Cardoso, A.J. Thermal analysis of low‐power three‐phase induction motors operating under voltage unbalance and inter‐turn short circuit faults. Machines 2020, 9, 2.
- M. Appadurai, E. Fantin Irudaya Raj, K. Venkadeshwaran, Finite element design and thermal analysis of an induction motor used for a hydraulic pumping system, Materials Today: Proceedings, Vol.45, Part 7, 2021, Pages 7100‐7106, https://doi.org/10.1016/j.matpr.2021.01.944.
- Putra, N.; Ariantara, B. Electric motor thermal management system using L‐shaped flat heat pipes. Appl. Therm. Eng. 2017, 126, 1156–1163.
- Ahmed, F.; Kar, N.C. Analysis of End‐Winding Thermal Effects in an Enclosed Fan‐Cooled Induction Motor with a Die‐Cast Copper Rotor. IEEE Trans. Ind. Appl. 2017, 53, 3098–3109.
M. Towhidi, F. Ahmed, A. Mollaeian and N. C. Kar, “Thermal Modelling of an Induction Motor with Liquid Cooling Optimization for Different EV Drive Cycles,” 2020 10th International Electric Drives Production Conference (EDPC), Ludwigsburg, Germany, 2020, pp. 1‐6, doi: 10.1109/EDPC51184.2020.9718577. - M. ‐S. Kim, J. ‐H. Park, K. ‐S. Lee, S. ‐H. Lee and J. ‐Y. Choi, “Optimum Design of Cooling Fan considering Experimental Method for Three‐Phase Induction Motor,” 2020 23rd International Conference on Electrical Machines and Systems (ICEMS), Hamamatsu, Japan, 2020, pp. 1220‐1224, doi:10.23919/ICEMS50442.2020.9290852.
- Boglietti, A., Nategh, S., Carpaneto, E., Boscaglia, L., & Scema, C. An optimization method for cooling
system design of traction motors. In 2019 IEEE International Electric Machines and Drives Conference (IEMDC) 1210–1215, 2019. - Satrústegui, M. et al. Design criteria for water cooled systems of induction machines. Appl. Therm. Eng. 5(114), 1018–1028, 2017.
- https://library.e.abb.com/public/e35d57ce4df3160285257d6d00720f51/9AKK106369_SuperE_101_web.pdf
- https://www.lafertaust.com.au/wp‐content/uploads/2019/02/Lafert‐Catalogue‐AC‐motors‐2018.pdf
- https://static.weg.net/medias/downloadcenter/hae/hdc/US100‐Standard‐Catalog‐Super‐Premium‐and‐Explosion‐Proof‐Sections.pdf
- https://www.leadgomotor.com/ye3%EF%BC%88ie3%EF%BC%89series‐premium‐efficiency‐three‐phase‐asynchronous‐motor/
- https://apsrewinds.com.au/wpcontent/uploads/specs_attach/Catalogue%20Toshiba%20LVM%20Premium% 20Efficiency%20A4%201209.pdf
- P. Ning, X. Hui, D. Li, Y. Kang, J. Yang and C. Liu, “Review of Thermal Design of SiC Power Module for
Motor Drive in Electrical Vehicle Application,” in CES Transactions on Electrical Machines and Systems, vol.
8, no. 3, pp. 332‐346, September 2024, doi: 10.30941/CESTEMS.2024.00041. - C. Liu et al., “Hybrid SiC‐Si DC–AC Topology: SHEPWM Si‐IGBT Master Unit Handling High Power
Integrated With Partial‐Power SiC‐MOSFET Slave Unit Improving Performance,” in IEEE Transactions on Power Electronics, vol. 37, no. 3, pp. 3085‐3098, March 2022, doi: 10.1109/TPEL.2021.3114322. - S. Baek, Y. Cho, B. ‐G. Cho and C. Hong, “Performance Comparison Between Two‐Level and Three‐Level SiC‐Based VFD Applications With Output Filters,” in IEEE Transactions on Industry Applications, vol. 55, no. 5, pp. 4770‐4779, Sept.‐Oct. 2019, doi: 10.1109/TIA.2019.2920360.
- A. K. Morya et al., “Wide Bandgap Devices in AC Electric Drives: Opportunities and Challenges,” in IEEE Transactions on Transportation Electrification, vol. 5, no. 1, pp. 3‐20, March 2019, doi:
10.1109/TTE.2019.2892807. - A. Schroedermeier and D. C. Ludois, “Integration of Inductors, Capacitors, and Damping Into Bus Bars for Silicon Carbide Inverter dv/dt Filters,” in IEEE Transactions on Industry Applications, vol. 55, no. 5, pp. 5045‐5054, Sept.‐Oct. 2019, doi: 10.1109/TIA.2019.2920596.
- Loncarski, J.; Monopoli, V.G.; Leuzzi, R.; Ristic, L.; Cupertino, F. Analytical and Simulation Fair
Comparison of Three Level Si IGBT Based NPC Topologies and Two Level SiC MOSFET Based Topology for High Speed Drives. Energies 2019, 12, 4571. https://doi.org/10.3390/en12234571 - Haruki Taniguchi, et. Al., Analysis of Energy‐Saving Effect for Applying a SiC Switching Device to
Inverters for Railway Vehicles Drives, IEEJ Journal of Industry Applications, 2024, Volume 13, Issue 1,
Pages 105‐112, https://doi.org/10.1541/ieejjia.22008551. - D. Cittanti, E. Vico and I. R. Bojoi, “New FOM‐Based Performance Evaluation of 600/650 V SiC and GaN Semiconductors for Next‐Generation EV Drives,” in IEEE Access, vol. 10, pp. 51693‐51707, 2022, doi:10.1109/ACCESS.2022.3174777.
- M. T. Fard, M. Abarzadeh, K. A. Noghani, J. He and K. Al‐Haddad, “Si/SiC hybrid 5‐level active NPC
inverter for electric aircraft propulsion drive applications,” in Chinese Journal of Electrical Engineering, vol.
6, no. 4, pp. 63‐76, Dec. 2020, doi: 10.23919/CJEE.2020.000031. - Naoto Fujishima, Technical Trends of SiC Power Semiconductor Devices and Their Applications in Power Electronics, IEEJ Journal of Industry Applications, 2024, vol. 13, no. 4, p. 372‐378.
https://doi.org/10.1541/ieejjia.23005497.
Yao, W.; Lu, J.; Taghizadeh, F.; Bai, F.; Seagar, A. Integration of SiC Devices and High‐Frequency
Transformer for High‐Power Renewable Energy Applications. Energies 2023, 16, 1538.
https://doi.org/10.3390/en16031538. - Q. Li, X. Zhang, C. Yuan, J. Ma and D. Jiang, “Variable Switching Frequency DPWM for ZVS in AC Motor Drive Fed by Two Paralleled SiC Inverters With Coupled Inductors,” in IEEE Transactions on Power Electronics, vol. 39, no. 1, pp. 1308‐1318, Jan. 2024, doi: 10.1109/TPEL.2023.3324194.
- Kelsey Horowitz, Samantha Reese, and Timothy Remo, “Research Highlight In “Manufacturing: SiC Power Electronics for Variable Frequency Motor Drives”, Research Highlight in Manufaturing Analysis, National Renewable Energy Laboratory, NREL/BR‐6A20‐68103, 2017. https://www.nrel.gov/docs/fy17osti/68103.pdf
- W. Zhou, M. Diab, X. Yuan and C. Wei, “Mitigation of Motor Overvoltage in SiC‐Based Drives Using Soft‐Switching Voltage Slew‐Rate (dv/dt) Profiling,” in IEEE Transactions on Power Electronics, vol. 37, no. 8, pp. 9612‐9628, Aug. 2022, doi: 10.1109/TPEL.2022.3157395.
- S. Sundeep, J. Wang, A. Griffo and F. Alvarez‐Gonzalez, “Antiresonance Phenomenon and Peak Voltage Stress Within PWM Inverter Fed Stator Winding,” in IEEE Transactions on Industrial Electronics, vol. 68, no. 12, pp. 11826‐11836, Dec. 2021, doi: 10.1109/TIE.2020.3048286.
- Y. Li et al., “500 kW Forced Air‐Cooled Silicon Carbide (SiC) Three‐Phase DC/AC Converter With a Power Density of 1.246 MW/m3 and Efficiency >98.5%,” in IEEE Transactions on Industry Applications, vol. 57, no.
5, pp. 5013‐5027, Sept.‐Oct. 2021, doi: 10.1109/TIA.2021.3087546. - Atsuo Kawamura, Yukinori Tsuruta, Hidemine Obara, Over 99.7% Efficiency at 100kW DC‐DC Power
Conversion using a 3.3kV SiC Device and Discussion on Device dv/dt Estimation, IEEJ Journal of Industry Applications, 2024, Volume 13, Issue 4, Pages 426‐436, https://doi.org/10.1541/ieejjia.23013265. - D. Woldegiorgis, M. M. Hossain, Z. Saadatizadeh, Y. Wei and H. A. Mantooth, “Hybrid Si/SiC Switches:
A Review of Control Objectives, Gate Driving Approaches and Packaging Solutions,” in IEEE Journal of Emerging and Selected Topics in Power Electronics, vol. 11, no. 2, pp. 1737‐1753, April 2023, doi:
10.1109/JESTPE.2022.3219377. - B. J. Baliga, “Silicon Carbide Power Devices: Progress and Future Outlook,” IEEE Journal of Emerging and Selected Topics in Power Electronics, vol. 11, no. 3, pp. 2400–2411, Jun. 2023.
- B. Y. Zhang, S. Wang, and Y. W. Lai et al., “Modeling and Prediction of Low‐frequency Radiated EMI for a SiC Motor Drive System,” IEEE Transactions on Industrial Electronics, vol. 71, no. 9, pp. 10210–10220, Sept. 2023.
- B. T. DeBoi, A. N. Lemmon, B. McPherson and B. Passmore, “Improved Methodology for Parasitic Analysis of High‐Performance Silicon Carbide Power Modules,” in IEEE Transactions on Power Electronics, vol. 37, no. 10, pp. 12415‐12425, Oct. 2022, doi: 10.1109/TPEL.2022.3176981.
- Zhang, L.; Yuan, X.;Wu, X.; Shi, C.; Zhang, J.; Zhang, Y. Performance Evaluation of High‐Power SiC
MOSFET Modules in Comparison to Si IGBT Modules. IEEE Trans. Power Electron. 2019, 34, 1181–1196. - X. Li et al., “A SiC Power MOSFET Loss Model Suitable for High‐Frequency Applications,” in IEEE
Transactions on Industrial Electronics, vol. 64, no. 10, pp. 8268‐8276, Oct. 2017. - Stefanik, J.; Zygmanowski, M. Power Loss Analysis of Advanced‐Neutral‐Point‐Clamped Converter with SiC MOSFETs and Si IGBTs. In Proceedings of the 2021 IEEE 19th International Power Electronics and Motion Control Conference (PEMC), Gliwice, Poland, 25–29 April 2021; pp. 161–166.
- A. Abdelrahman, Z. Erdem, Y. Attia and M. Youssef, “Performance of Wide Band Gap Devices in Electric Vehicles Converters: A Case Study Evaluation”, 2018 20th European Conference on Power Electronics and Applications (EPE’18 ECCE Europe), pp. 1‐9, 2018.
- S. Yu, J. Wang, X. Zhang, Y. Liu, N. Jiang and W. Wang, “The potential impact of using traction inverters with SiC MOSFETs for electric buses”, IEEE Access, vol. 9, pp. 51561‐51572, 2021.
- Nisch, A.; Heller, M.; Wondrak, W.; Bucher, A.; Hasenohr, C.; Kefer, K.; Lunz, B.; Pawellek, A.; Smit, A.;
Gärtner, M.; et al. Simulation and Measurement‐Based Analysis of Efficiency Improvement of SiC
MOSFETs in a Series‐Production Ready 300 KW / 400 V Automotive Traction Inverter. In Proceedings of the 2020 22nd European Conference on Power Electronics and Applications (EPE’20 ECCE Europe), Lyon, France, 7–11 September 2020; pp. 1–10.
Ding, X.; Du, M.; Duan, C.; Guo, H.; Xiong, R.; Xu, J.; Cheng, J.; Luk, P.C.K. Analytical and Experimental
Evaluation of SiC‐Inverter Nonlinearities for Traction Drives Used in Electric Vehicles. IEEE Trans. Veh.
Technol. 2018, 67, 146–159. - S. Halder, K. Bhuvir, S. Bhattacharjee, J. Nakka, A. Panda and M. Ghosh, “Performance Analysis of WBG Inverter Fed Electric Traction Drive System for EV Application,” 2023 IEEE IAS Global Conference on Renewable Energy and Hydrogen Technologies (GlobConHT), Male, Maldives, 2023, pp. 1‐6, doi:
10.1109/GlobConHT56829.2023.10087485. - S. Amirpour, T. Thiringer and D. Hagstedt, “Energy Loss Analysis in a SiC/IGBT Propulsion Inverter over Drive Cycles Considering Blanking time MOSFET’s Reverse Conduction and the Effect of Thermal Feedback”, 2020 IEEE Energy Conversion Congress and Exposition (ECCE), pp. 1505‐1511, 2020.
- L. Li et al., “Overview of Finite‐Element Analysis in Simulation of SiC Power Device Packaging,” 2021 18th China International Forum on Solid State Lighting & 2021 7th International Forum on Wide Bandgap Semiconductors (SSLChina: IFWS), Shenzhen, China, 2021, pp. 53‐57, doi:
10.1109/SSLChinaIFWS54608.2021.9675174. - L. Li, P. Ning, X. Wen, Y. Bian and D. Zhang, “Gate Drive Design for a Hybrid Si IGBT/SiC MOSFET
Module,” 2018 1st Workshop on Wide Bandgap Power Devices and Applications in Asia (WiPDA Asia), Xi’an,
China, 2018, pp. 34‐41, doi: 10.1109/WiPDAAsia.2018.8734665. - M. S. Diab and X. Yuan, “A Quasi‐Three‐Level PWM Scheme to Combat Motor Overvoltage in SiC‐Based Single‐Phase Drives,” in IEEE Transactions on Power Electronics, vol. 35, no. 12, pp. 12639‐12645, Dec. 2020,
doi: 10.1109/TPEL.2020.2994289. - Z. Chen and A. Q. Huang, “High Performance SiC Power Module Based on Repackaging of Discrete SiC Devices,” in IEEE Transactions on Power Electronics, vol. 38, no. 8, pp. 9306‐9310, Aug. 2023.
- Y. Zhang, C. Chen,Y. Xie, T. Liu,Y. Kang, and H. Peng, ``A high efficiency dynamic inverter dead‐time
adjustment method based on an improved GaN HEMTs switching model,’’ IEEE Trans. Power Electron., vol. 37, no. 3, pp. 2667_2683, Mar. 2022. - H. V. Nguyen, et. Al., “A novel SiC‐based multifunctional onboard battery charger for plug‐in electric
vehicles”, IEEE Trans. Power Electron., vol. 36, no. 5, pp. 5635‐5646, May 2021. - R. Ruffo, P. Guglielmi, and E. Armando, “Inverter Side RL Filter Precise Design for Motor Overvoltage
Mitigation in SiC‐Based Drives,” IEEE Trans. Ind. Electron., vol. 67, no. 2, pp. 863–873, Feb. 2020. - C. M. DiMarino, et. Al., “10‐kV SiC MOSFET Power Module With Reduced Common‐Mode Noise and
Electric Field,” in IEEE Transactions on Power Electronics, vol. 35, no. 6, pp. 6050‐6060, June 2020. - X. Li et al., “Achieving Zero Switching Loss in Silicon Carbide MOSFET,” in IEEE Transactions on Power
Electronics, vol. 34, no. 12, pp. 12193‐12199, Dec. 2019. - I. Laird, X. B. Yuan, and J. Scoltock et al., “A Design Optimization Tool for Maximizing the Power Density of 3‐phase DC–AC Converters Using Silicon Carbide (SiC) Devices,” IEEE Transactions on PowerElectronics,
vol. 33, no. 4, pp. 2913–2932, Apr. 2018. - Castellazzi, A.; Gurpinar, E.; Wang, Z.; Suliman Hussein, A.; Garcia Fernandez, P. Impact of Wide‐
Bandgap Technology on Renewable Energy and Smart‐Grid Power Conversion Applications Including
Storage. Energies 2019, 12, 4462. https://doi.org/10.3390/en12234462. - Zaman, H.; et. Al., Suppression of Switching Crosstalk and Voltage Oscillations in a SiC MOSFET Based Half‐Bridge Converter. Energies 2018, 11, 3111.
- Z. Chen, C. Chen, Q. Huang and A. Q. Huang, “Design of High Power Converter with Single Low Ron
Discrete SiC Device,” 2022 IEEE 9th Workshop on Wide Bandgap Power Devices & Applications (WiPDA),
Redondo Beach, CA, USA, 2022, pp. 209‐214. - Kumar, A.; et. Al., Current Source Gate Driver for SiC MOSFETs in Power Electronics Applications. In
Proceedings of the 2022 International Symposium on Power Electronics, Electrical Drives, Automation and Motion (SPEEDAM), Sorrento, Italy, 22–24 June 2022; pp. 523–527. - E. Velander et al., “An Ultra Low Loss Inductorless dv/dt Filter Concept for Medium‐Power Voltage Source Motor Drive Converters With SiC Devices,” IEEE Trans. Power Electron., vol. 33, no. 7, pp. 6072–6081, Jul. 2018. J. He et al., “Multi‐Domain Design Optimization of dv/dt Filter for SiC‐Based Three‐Phase Inverters in High‐Frequency Motor‐Drive Applications,” IEEE Trans. Ind. Appl., vol. 55, no. 5, pp. 5214‐5222, Sept.‐Oct. 2019.
- J. W. Kolar, et. Al., “Application ofWBGpower devices in future 3‐F variable speed drive inverter systems how to handle a double‐edged sword,’’ in IEDM Tech. Dig., Dec. 2020, pp. 27.7.1_27.7.4.
- Z. Liu, B. Li, F. C. Lee and Q. Li, “High‐Efficiency High‐Density Critical Mode Rectifier/Inverter for WBG‐Device‐Based On‐Board Charger”, IEEE Transactions on Industrial Electronics, vol. 64, no. 11, pp. 9114‐9123, Nov. 2017.
- M. Sun, Y. Zhang, X. Gao and T. Palacios, “High‐Performance GaN Vertical Fin Power Transistors on Bulk GaN Substrates”, IEEE Electron Device Letters, vol. 38, pp. 509‐512, 2017.
- Hussein, A.; Castellazzi, A. Variable Frequency Control and Filter Design for Optimum Energy Extraction from a SiC Wind Inverter. In Proceedings of the International Power Electronics Conference (IPEC‐Niigata 2018–ECCE Asia), Niigata, Japan, 20–24 May 2018.
- H. Kogure, K. Ishikawa, Y. Kohno, T. Sakai and T. Ishigaki, “Development of low loss inverter system
adopted lower harmonic losses technology and ultra compact inverters adopted high power density sic module”, Proc. 20th Eur. Conf. Power Electron. Appl., pp. P.1‐P.7, 2018. - R. Amorim Torres, H. Dai, W. Lee, B. Sarlioglu and T. Jahns, “Current‐Source Inverter Integrated Motor
Drives Using Dual‐Gate Four‐Quadrant Wide‐Bandgap Power Switches,” in IEEE Transactions on Industry Applications, vol. 57, no. 5, pp. 5183‐5198, Sept.‐Oct. 2021, doi: 10.1109/TIA.2021.3096179. - F. Stella, S. Savio, E. Vico, R. Bojoi and E. Armando, “Cost Effective 3D Printed Heatsink for Fast
Prototyping of WBG Power Converters,” 2024 IEEE Applied Power Electronics Conference and Exposition (APEC), Long Beach, CA, USA, 2024, pp. 2562‐2567, doi: 10.1109/APEC48139.2024.10509035 - A. Osman, G. Moreno, and S. Myers et al., “Automotive Silicon Carbide Power Module Cooling with a
Novel Modular Manifold and Embedded Heat Sink,” Journal of Electronic Packaging, vol. 146, no. 2, pp. 021007, Jun. 2024 - J. Zachariae, M. Tiesler, and R. Singh et al., “Silicon Carbide Based Traction Inverter Cooling in Electric
Vehicle Using Heat Pipes,” Thermal Science and Engineering Progress, vol. 46, no. 1, pp. 102155 Dec. 2023. - R. A. Torres, H. Dai, W. Lee, K. Saviers, T. M. Jahns and B. Sarlioglu, “Investigation of Cooling Techniques and Enclosure Types for Integrated Motor Drives,” 2022 IEEE Energy Conversion Congress and Exposition (ECCE), Detroit, MI, USA, 2022, pp. 01‐08, doi: 10.1109/ECCE50734.2022.9947618.
- R. A. Torres, H. Dai, T. M. Jahns, B. Sarlioglu and W. Lee, “Thermal Analysis of Housing‐Cooled Integrated Motor Drives,” 2021 IEEE Transportation Electrification Conference & Expo (ITEC), Chicago, IL, USA, 2021,
pp. 1‐6, doi: 10.1109/ITEC51675.2021.9490174 - Mademlis, G.; Orbay, R.; Liu, Y.; Sharma, N.; Arvidsson, R.; Thiringer, T. Multidisciplinary Cooling Design Tool for Electric Vehicle SiC Inverters Utilizing Transient 3D‐CFD Computations. eTransportation 2021, 7, 100092.
- Abramushkina, E.; Zhaksylyk, A.; Geury, T.; El Baghdadi, M.; Hegazy, O. A Thorough Review of Cooling
Concepts and Thermal Management Techniques for Automotive WBG Inverters: Topology, Technology and Integration Level. Energies 2021, 14, 4981. https://doi.org/10.3390/en14164981. - Zeng, Z.; Zhang, X.; Blaabjerg, F.; Chen, H.; Sun, T. Stepwise Design Methodology and Heterogeneous
Integration Routine of Air‐Cooled SiC Inverter for Electric Vehicle. IEEE Trans. Power Electron. 2020, 35, 3973–3988. - M. Alizadeh, R. Rodriguez, and J. Bauman et al., “Optimal Design of Integrated Heat Pipe Air‐cooled
System Using TLBO algorithm for SiC MOSFET Converters,” IEEE Open Journal of Power Electronics, vol. 1, pp. 103–112, Apr. 2020. - T. Wu, Z. Q. Wang, and B. Ozpineci et al., “Automated Heatsink Optimization for Air‐cooled Power
Semiconductor Modules,” IEEE Tran. on Power Electronics, vol. 34, no. 6, pp. 5027–5031, Jun. 2019. - A. Michalak, M. S. Zaman, and O. Tayyara et al., “A Thermal Management Design Methodology for
Advanced Power Electronics Utilizing Genetic Optimization and Additive Manufacturing Techniques,” in Proc. of 2020 19th IEEE Intersociety Conference on Thermal and Thermomechanical Phenomena in Electronic Systems (ITherm), Orlando, FL, USA, Jul. 2020, pp. 547–557.
E. Gurpinar, R. Sahu and B. Ozpineci, “Heat Sink Design for WBG Power Modules Based on Fourier Series and Evolutionary Multi‐Objective Multi‐Physics Optimization,” in IEEE Open Journal of Power Electronics, vol. 2, pp. 559‐569, 2021, doi: 10.1109/OJPEL.2021.3119518. - R. Yao et al., “A Double‐Sided Cooling Approach of Discrete SiC MOSFET Device Based on Press‐Pack
Package,” in IEEE Open Journal of Power Electronics, vol. 5, pp. 1629‐1640, 2024, doi:
10.1109/OJPEL.2024.3479293. - R. Chen and F. F. Wang, “SiC and GaN Devices With Cryogenic Cooling,” in IEEE Open Journal of Power Electronics, vol. 2, pp. 315‐326, 2021, doi: 10.1109/OJPEL.2021.3075061.
- D. G. Pahinkar, L. Boteler, and D. Ibitayo et al., “Liquid‐cooled Aluminum Silicon Carbide Heat Sinks for Reliable Power Electronics Packages,” Journal of Electronic Packaging, vol. 141, no. 4, pp. 041001, Dec. 2019.
- Tang, G.; Wai, L.C.; Boon Lim, S.; Lau, B.L.; Kazunori, Y.; Zhang, X.W. Thermal Analysis, Characterization
and Material Selection for SiC Device Based Intelligent Power Module (IPM). In Proceedings of the 2020 IEEE 70th Electronic Components and Technology Conference (ECTC), Orlando, FL, USA, 3–30 June 2020; pp. 2078–2085. - Mademlis, G.; Orbay, R.; Liu, Y.; Sharma, N. Designing Thermally Uniform Heatsink with Rectangular Pins for High‐Power Automotive SiC Inverters. In Proceedings of the IECON 2020 The 46th Annual Conference of the IEEE Industrial Electronics Society, Singapore, 18–21 October 2020; pp. 1317–1322.
- Becker, N.; Bulovic, S.; Bittner, R.; Herzer, R. Thermal Simulation for Power Density Optimization of SiC‐MOSFET Automotive Inverter. In Proceedings of the CIPS 2020; 11th International Conference on
Integrated Power Electronics Systems, Berlin, Germany, 24–26 March 2020; pp. 1–6. - Catalano, A.P.; Scognamillo, C.; Castellazzi, A.; d’Alessandro, V. Optimum Thermal Design of High‐
Voltage Double‐Sided Cooled Multi‐Chip SiC Power Modules. In Proceedings of the 2019 25th
International Workshop on Thermal Investigations of ICs and Systems (THERMINIC), Lecco, Italy, 25–27 September 2019; pp. 1–4. - McPherson, B.; McGee, B.; Simco, D.; Olejniczak, K.; Passmore, B. Direct Liquid Cooling of High
Performance Silicon Carbide (SiC) Power Modules. In Proceedings of the 2017 IEEE Int. Workshop On
Integrated Power Packaging (IWIPP), Delft, The Netherlands, 5–7 April 2017; pp. 1–5. - S. Acharya, A. Anurag, S. Bhattacharya and D. Pellicone, “Performance Evaluation of a Loop
Thermosyphon‐Based Heatsink for High‐Power SiC‐Based Converter Applications,” in IEEE Transactions on Components, Packaging and Manufacturing Technology, vol. 10, no. 1, pp. 99‐110, Jan. 2020, doi:10.1109/TCPMT.2019.2923332. - W. Lee, R. A. Torres, H. Dai, T. M. Jahns and B. Sarlioglu, “Integration and Cooling Strategies for WBG‐
based Current‐Source Inverters‐Based Motor Drives,” 2021 IEEE Energy Conversion Congress and Exposition
(ECCE), Vancouver, BC, Canada, 2021, pp. 5225‐5232, doi: 10.1109/ECCE47101.2021.9595747. - S. ‐G. Han, W. ‐H. Lee, D. ‐Y. Hwang, S. ‐M. Park, J. ‐H. Choi and D. ‐M. Joo, “Thermal Design and
Development of a Inverter Considering the Switch Characteristics of Wide Band Gap Power
semiconductor,” 2021 24th International Conference on Electrical Machines and Systems (ICEMS), Gyeongju,
Korea, Republic of, 2021, pp. 2138‐2144, doi: 10.23919/ICEMS52562.2021.9634211. - A. I. Emon, Mustafeez‐ul‐Hassan, A. B. Mirza, J. Kaplun, S. S. Vala and F. Luo, “A Review of High‐Speed
GaN Power Modules: State of the Art, Challenges, and Solutions,” in IEEE Journal of Emerging and Selected
Topics in Power Electronics, vol. 11, no. 3, pp. 2707‐2729, June 2023, doi: 10.1109/JESTPE.2022.3232265. - Singh, S., Chaudhary, T. & Khanna, G. Recent Advancements in Wide Band Semiconductors (SiC and GaN) Technology for Future Devices. Silicon 14, 5793–5800 (2022). https://doi.org/10.1007/s12633‐021‐01362‐3.
- Kumar, A.; Moradpour, M.; Losito, M.; Franke, W.‐T.; Ramasamy, S.; Baccoli, R.; Gatto, G. Wide Band Gap Devices and Their Application in Power Electronics. Energies 2022, 15, 9172.
https://doi.org/10.3390/en15239172. - S. M. S. H. Rafin, R. Ahmed and O. A. Mohammed, “Wide Band Gap Semiconductor Devices for Power
Electronic Converters,” 2023 Fourth International Symposium on 3D Power Electronics Integration and Manufacturing (3D‐PEIM), Miami, FL, USA, 2023, pp. 1‐8, doi: 10.1109/3D‐PEIM55914.2023.10052586.
Y. Bérubé, A. Ghazanfari, H. F. Blanchette, C. Perreault and K. Zaghib, “Recent Advances in Wide Bandgap Devices for Automotive Industry,” IECON 2020 The 46th Annual Conference of the IEEE Industrial Electronics
Society, Singapore, 2020, pp. 2557‐2564, doi: 10.1109/IECON43393.2020.9254478. - Setera, B.; Christou, A. Challenges of Overcoming Defects in Wide Bandgap Semiconductor Power
Electronics. Electronics 2022, 11, 10. https://doi.org/10.3390/electronics11010010 - Wang, Y.; Ding, Y.; Yin, Y. Reliability of Wide Band Gap Power Electronic Semiconductor and Packaging:A Review. Energies 2022, 15, 6670. https://doi.org/10.3390/en15186670
- G. Iannaccone, C. Sbrana, I. Morelli and S. Strangio, “Power Electronics Based on Wide‐Bandgap
Semiconductors: Opportunities and Challenges,” in IEEE Access, vol. 9, pp. 139446‐139456, 2021, doi:
10.1109/ACCESS.2021.3118897. - Lee, H.; Smet, V.; Tummala, R. A Review of SiC Power Module Packaging Technologies: Challenges,
Advances, and Emerging Issues. IEEE J. Emerg. Sel. Top. Power Electron. 2020, 8, 239–255. - Chen, J.; Du, X.; Luo, Q.; Zhang, X.; Sun, P.; Zhou, L. A Review of Switching Oscillations of Wide Bandgap
Semiconductor Devices. IEEE Trans. Power Electron. 2020, 35, 13182–13199. - S. J. Bader et al., “Prospects for Wide Bandgap and Ultrawide Bandgap CMOS Devices,” in IEEE
Transactions on Electron Devices, vol. 67, no. 10, pp. 4010‐4020, Oct. 2020, doi: 10.1109/TED.2020.3010471. - J. A. Ferreira and P. Wilson, “The Impact of ITRW: How Can WBG Power Semiconductors Break
Through?,” in IEEE Open Journal of Power Electronics, vol. 2, pp. 327‐335, 2021, doi:
10.1109/OJPEL.2021.3071876. - I. C. Kizilyalli, Y. A. Xu, E. Carlson, J. Manser and D. W. Cunningham, “Current and future directions in
power electronic devices and circuits based on wide band‐gap semiconductors,” 2017 IEEE 5th Workshop on Wide Bandgap Power Devices and Applications (WiPDA), Albuquerque, NM, USA, 2017, pp. 417‐417, doi:
10.1109/WiPDA.2017.8170583. - [196] Yuan, X.; Laird, I.; Walder, S. Opportunities, Challenges, and Potential Solutions in the Application
of Fast‐Switching SiC Power Devices and Converters. IEEE Trans. Power Electron. 2021, 36, 3925–3945. - Matallana, A.; Ibarra, E.; López, I.; Andreu, J.; Garate, J.I.; Jordà, X.; Rebollo, J. Power Module Electronics in HEV/EV Applications: New Trends in Wide‐Bandgap Semiconductor Technologies and Design Aspects.
Renew. Sustain. Energy Rev. 2019, 113, 109264. - Investigation and Review of Challenges in a High‐Temperature 30‐KVA Three‐Phase Inverter Using SiC MOSFETs. IEEE Trans. Ind. Appl. 2018, 54, 2483–2491.
- I. C. Kizilyalli, E. P. Carlson and D. W. Cunningham, “Barriers to the Adoption of Wide‐Bandgap
Semiconductors for Power Electronics,” 2018 IEEE International Electron Devices Meeting (IEDM), San
Francisco, CA, USA, 2018, pp. 19.6.1‐19.6.4, doi: 10.1109/IEDM.2018.8614501. - X. Yuan, “Application of silicon carbide (SiC) power devices: Opportunities, challenges and potential
solutions,” IECON 2017—43rd Annual Conference of the IEEE Industrial Electronics Society, Beijing, China, 2017, pp. 893‐900, doi: 10.1109/IECON.2017.8216154. - Z. Zhang, Y. Hu, X. Chen, G. W. Jewell and H. Li, “A Review on Conductive Common‐Mode EMI
Suppression Methods in Inverter Fed Motor Drives,” in IEEE Access, vol. 9, pp. 18345‐18360, 2021, doi:10.1109/ACCESS.2021.3054514 - P. Weiss, C. Bauer, R. Jung and K. Berberich, “Double Side Cooled Modules Enable Future Generation of SiC‐Traction‐Inverters,” PCIM Europe digital days 2021; International Exhibition and Conference for Power Electronics, Intelligent Motion, Renewable Energy and Energy Management, Online, 2021, pp. 1‐6
- E. A. Jones, F. F. Wang and D. Costinett, “Review of commercial GaN power devices and GaN‐based
converter design challenges”, IEEE J. Emerg. Sel. Topics Power Electron., vol. 4, no. 3, pp. 707‐719, Sep. 2016. - https://us.metoree.com/categories/sic‐mosfet/
- Blaschke, F. The principle of field‐orientation as applied to the new transvector closed‐loop system for rotating‐field machines. Siemens Rev. 1972, 34, 217–220.
- Carbone, L.; Cosso, S.; Kumar, K.; Marchesoni, M.; Passalacqua, M.; Vaccaro, L. Induction Motor Field‐
Oriented Sensorless Control with Filter and Long Cable. Energies 2022, 15, 1484.
https://doi.org/10.3390/en15041484.
J. R. Domínguez, I. Dueñas and S. Ortega‐Cisneros, “Discrete‐Time Modeling and Control Based on Field Orientation for Induction Motors,” in IEEE Transactions on Power Electronics, vol. 35, no. 8, pp. 8779‐8793, Aug. 2020, doi: 10.1109/TPEL.2020.2965632. - M. J. Akhtar and R. K. Behera, “Space Vector Modulation for Distributed Inverter‐Fed Induction Motor
Drive for Electric Vehicle Application,” in IEEE Journal of Emerging and Selected Topics in Power Electronics,
vol. 9, no. 1, pp. 379‐389, Feb. 2021, doi: 10.1109/JESTPE.2020.2968942. - G. ‐J. Jo and J. ‐W. Choi, “Gopinath Model‐Based Voltage Model Flux Observer Design for Field‐Oriented Control of Induction Motor,” in IEEE Transactions on Power Electronics, vol. 34, no. 5, pp. 4581‐4592, May 2019, doi: 10.1109/TPEL.2018.2864322.
- I. M. Mehedi, N. Saad, M. A. Magzoub, U. M. Al‐Saggaf and A. H. Milyani, “Simulation Analysis and
Experimental Evaluation of Improved Field‐Oriented Controlled Induction Motors Incorporating
Intelligent Controllers,” in IEEE Access, vol. 10, pp. 18380‐18394, 2022, doi: 10.1109/ACCESS.2022.3150360. - M. J. Cheerangal, A. K. Jain and A. Das, “Multiple Fault Tolerant Control Strategy for Rotor Field Oriented Induction Motor Drive Fed From CHB Converter With Redundant Cells,” in IEEE Transactions on Power Electronics, vol. 38, no. 1, pp. 852‐861, Jan. 2023, doi: 10.1109/TPEL.2022.3202313.
- H. Abbasi, M. Ghanbari, R. Ebrahimi and M. Jannati, “IRFOC of Induction Motor Drives Under Open‐
Phase Fault Using Balanced and Unbalanced Transformation Matrices,” in IEEE Transactions on Industrial Electronics, vol. 68, no. 10, pp. 9160‐9173, Oct. 2021, doi: 10.1109/TIE.2020.3026278. - A. Devanshu, M. Singh and N. Kumar, “An Improved Nonlinear Flux Observer Based Sensorless FOC IM Drive With Adaptive Predictive Current Control,” in IEEE Transactions on Power Electronics, vol. 35, no. 1, pp. 652‐666, Jan. 2020, doi: 10.1109/TPEL.2019.2912265.
- M. Shabandokht‐Zarami, M. Ghanbari, E. Alibeiki and M. Jannati, “A Modified FOC Strategy With Optimal Rotor Flux for FTC of Star‐Connected TPIMDs Against Single‐Phase Open Fault,” in IEEE Canadian Journal of Electrical and Computer Engineering, vol. 44, no. 1, pp. 83‐93, winter 2021, doi:
10.1109/ICJECE.2020.3027606. - I. G. Prieto, M. J. Duran, P. Garcia‐Entrambasaguas and M. Bermudez, “Field‐Oriented Control of
Multiphase Drives With Passive Fault Tolerance,” in IEEE Transactions on Industrial Electronics, vol. 67, no. 9, pp. 7228‐7238, Sept. 2020, doi: 10.1109/TIE.2019.2944056. - https://www.st.com/en/applications/industrial‐motor‐control/3‐phase‐field‐oriented‐control‐foc.
- Białoń, T.; Niestrój, R.; Michalak, J.; Pasko, M. Induction Motor PI Observer with Reduced‐Order
Integrating Unit. Energies 2021, 14, 4906. https://doi.org/10.3390/en14164906 - Wang, F.; Zhang, Z.; Mei, X.; Rodríguez, J.; Kennel, R. Advanced Control Strategies of Induction Machine:
Field Oriented Control, Direct Torque Control and Model Predictive Control. Energies 2018, 11, 120. - Fnaiech, M.A.; Guzinski, J.; Trabelsi, M.; Kouzou, A.; Benbouzid, M.; Luksza, K. MRAS‐Based Switching
Linear Feedback Strategy for Sensorless Speed Control of Induction Motor Drives. Energies 2021, 14, 3083.
https://doi.org/10.3390/en14113083 - Pal, A.; Das, S.; Chattopadhyay, A. An improved rotor flux space vector based MRAS for field‐oriented
control of induction motor drives. IEEE Trans. Power Electron. 2018, 33, 5131–5141. - Dehghan‐Azad, E.; Gadoue, S.; Atkinson, D.; Slater, H.; Barrass, P.; Blaabjerg, F. Sensorless control of im based on stator‐voltage mras for limp‐home ev applications. IEEE Trans. Power Electron. 2018, 33, 1911–S. Khadar, H. Abu‐Rub and A. Kouzou, “Sensorless Field‐Oriented Control for Open‐End Winding Five‐Phase Induction Motor With Parameters Estimation,” in IEEE Open Journal of the Industrial Electronics Society, vol. 2, pp. 266‐279, 2021, doi: 10.1109/OJIES.2021.3072232.
- E. Hamdi, T. Ramzi, I. Atif and M. F. Mohamed, “Real time implementation of indirect rotor flux oriented control of a five‐phase induction motor with novel rotor resistance adaption using sliding mode observer”, J. Franklin Inst., vol. 355, pp. 2112‐2141, 2018.
- K. K. Prabhakar, C. Upendra Reddy, P. Kumar and A. K. Singh, “A New Reference Flux Linkage Selection Technique for Efficiency Improvement of Direct Torque Controlled IM Drive,” in IEEE Journal of Emerging and Selected Topics in Power Electronics, vol. 8, no. 4, pp. 3751‐3762, Dec. 2020, doi:
10.1109/JESTPE.2020.2979235.
S. Savarapu, M. Qutubuddin and Y. Narri, “Modified Brain Emotional Controller‐Based Ripple
Minimization for SVM‐DTC of Sensorless Induction Motor Drive,” in IEEE Access, vol. 10, pp. 40872‐40887,2022, doi: 10.1109/ACCESS.2022.3165651. - I. M. Alsofyani, Y. Bak and K. ‐B. Lee, “Fast Torque Control and Minimized Sector‐Flux Droop for Constant Frequency Torque Controller Based DTC of Induction Machines,” in IEEE Transactions on Power Electronics, vol. 34, no. 12, pp. 12141‐12153, Dec. 2019, doi: 10.1109/TPEL.2019.2908631.
- I. M. Alsofyani, N. R. N. Idris and K. ‐B. Lee, “Dynamic Hysteresis Torque Band for Improving the
Performance of Lookup‐Table‐Based DTC of Induction Machines,” in IEEE Transactions on Power
Electronics, vol. 33, no. 9, pp. 7959‐7970, Sept. 2018, doi: 10.1109/TPEL.2017.2773129. - M. H. Holakooie, M. Ojaghi and A. Taheri, “Direct Torque Control of Six‐Phase Induction Motor With a
Novel MRAS‐Based Stator Resistance Estimator,” in IEEE Transactions on Industrial Electronics, vol. 65,no. 10, pp. 7685‐7696, Oct. 2018, doi: 10.1109/TIE.2018.2807410. - R. H. Kumar, et. Al., “Review of recent advancements of direct torque control in induction motor drives—a decade of progress”, IET Power Electronics, Vol. 11, No. 1, pp. 1‐15, 2018
- N. El Ouanjli et al., “Modern improvement techniques of direct torque control for induction motor drives—a review,” in Protection and Control of Modern Power Systems, vol. 4, no. 2, pp. 1‐12, April 2019, doi:10.1186/s41601‐019‐0125‐5.
- Peter, A. K., Mathew, J., & Gopakumar, K. (2023). A simplified DTC‐SVPWM scheme for induction motor drives using a single PI controller. IEEE Transactions on Power Electronics, 38(open in a new window)(1(open in a new window)), 750–761. https://doi.org/10.1109/TPEL.2022.3197362.
- Benevieri, A.; Maragliano, G.; Marchesoni, M.; Passalacqua, M.; Vaccaro, L. Induction Motor Direct Torque Control with Synchronous PWM. Energies 2021, 14, 5025.
- P. Naganathan and S. Srinivas, “MTPA Associated DTC Methodologies for Enhanced Performance and
Energy Savings in Electric Vehicle Mobility With Induction Motor Drive,” in IEEE Transactions on
Transportation Electrification, vol. 8, no. 2, pp. 1853‐1862, June 2022, doi: 10.1109/TTE.2021.3130178. - Pimkumwong, N.; Wang, M.S. Full‐order observer for direct torque control of induction motor based on constant V/F control technique. ISA Trans. 2018, 73, 189–200.
- Ammar, A., Bourek, A. & Benakcha, A. Robust SVM‐direct torque control of induction motor based on sliding mode controller and sliding mode observer. Front. Energy 14, 836–849 (2020).
https://doi.org/10.1007/s11708‐017‐0444‐z - E. Hamdi, T. Ramzi, I. Atif and M. F. Mohamed, “Adaptive direct torque control using Luenberger‐sliding mode observer for online stator resistance estimation for five‐phase induction motor drives”, Elect. Eng.,
vol. 100, pp. 1639‐1649, 2018. - A. Abdelkarim, K. Aissa, M. Brahim, A. Tarek and A. Younes, “Feedback linearization based sensorless
direct torque control using stator flux MRAS‐sliding mode observer for induction motor drive”, ISA Trans., vol. 98, pp. 382‐392, Mar. 2020. - V. S. Reddy Chagam and S. Devabhaktuni, “Enhanced Low‐Speed Characteristics With Constant Switching Torque‐Controller‐Based DTC Technique of Five‐Phase Induction Motor Drive With FOPI Control,” in IEEE Transactions on Industrial Electronics, vol. 70, no. 11, pp. 10789‐10799, Nov. 2023, doi:10.1109/TIE.2022.3227275.
- X. Wu, W. Huang, X. Lin, W. Jiang, Y. Zhao and S. Zhu, “Direct Torque Control for Induction Motors Based on Minimum Voltage Vector Error,” in IEEE Transactions on Industrial Electronics, vol. 68, no. 5, pp. 3794‐3804, May 2021, doi: 10.1109/TIE.2020.2987283.
- Tiitinen, P.; Surandra, M. The next generation motor control method, DTC direct torque control. In
Proceedings of the International Conference on Power Electronics, Drives and Energy Systems for
Industrial Growth, New Delhi, India, 8–11 January 1996;Volume 1, pp. 37–43. - [241] B. Çavuş and M. Aktaş, “MPC‐Based Flux Weakening Control for Induction Motor Drive With DTC for Electric Vehicles,” in IEEE Transactions on Power Electronics, vol. 38, no. 4, pp. 4430‐4439, April 2023, doi: 10.1109/TPEL.2022.3230547.
J. Rodriguez et al., “Latest Advances of Model Predictive Control in Electrical Drives—Part I: Basic
Concepts and Advanced Strategies,” in IEEE Transactions on Power Electronics, vol. 37, no. 4, pp. 3927‐3942, April 2022, doi: 10.1109/TPEL.2021.3121532. - M. H. Arshad, M. A. Abido, A. Salem and A. H. Elsayed, “Weighting Factors Optimization of Model
Predictive Torque Control of Induction Motor Using NSGA‐II With TOPSIS Decision Making,” in IEEE
Access, vol. 7, pp. 177595‐177606, 2019, doi: 10.1109/ACCESS.2019.2958415. - [244] Aziz, A.G.M.A.; Rez, H.; Diab, A.A.Z. Robust Sensorless Model‐Predictive Torque Flux Control for
High‐Performance Induction Motor Drives. Mathematics 2021, 9, 403. - I. Gonzalez‐Prieto, M. Duran, J. Aciego, C. Martin and F. Barrero, “Model predictive control of six‐phase induction motor drives using virtual voltage vectors”, IEEE Trans. Ind. Electron., vol. 65, no. 1, pp. 27‐37, Jan. 2018.
- Y. Zhou and G. Chen, “Predictive DTC Strategy With Fault‐Tolerant Function for Six‐Phase and Three‐
Phase PMSM Series‐Connected Drive System,” in IEEE Transactions on Industrial Electronics, vol. 65, no. 11, pp. 9101‐9112, Nov. 2018, doi: 10.1109/TIE.2017.2786236. - M. Chebaani, M. Ebeed, W. S. E. Abdellatif, Z. M. S. Elbarbary and N. A. Nouraldin, “Design and
Implementation of an Improved Finite‐State Predictive Direct Torque Control for Induction Motor With New Weighting Factor Elimination,” in IEEE Access, vol. 11, pp. 58169‐58187, 2023, doi:
10.1109/ACCESS.2023.3283983. - A. Yang and Z. Lu, “Multiscalar Model‐Based Predictive Torque Control Without Weighting Factors and Current Sensors for Induction Motor Drives,” in IEEE Journal of Emerging and Selected Topics in Power Electronics, vol. 10, no. 5, pp. 5785‐5797, Oct. 2022, doi: 10.1109/JESTPE.2022.3181802.
- T. Wang, Y. Wang, Z. Zhang, Z. Li, C. Hu, and F. Wang, “Comparison and analysis of predictive control of induction motor without weighting factors,” Energy Reports, vol. 9, no. 2, pp. 558–568, Apr. 2023, doi:10.1016/j.egyr.2023.03.046.
- Wróbel, K.; Serkies, P.; Szabat, K. Model Predictive Base Direct Speed Control of Induction Motor Drive—Continuous and Finite Set Approaches. Energies 2020, 13, 1193. https://doi.org/10.3390/en13051193.
- Novak, M.; Xie, H.T.; Dragicevic, T.; Wang, F.X.; Rodríguez, J.; Blaabjerg, F. Optimal Cost Function
Parameter Design in Predictive Torque Control (PTC) Using Artificial Neural Networks (ANN). IEEE Trans. Ind. Electron. 2021, 68, 7309–7319. - Muddineni, V.P.; Bonala, A.K.; Sandepudi, S.R. Grey Relational Analysis‐Based Objective Function
Optimization for Predictive Torque Control of Induction Machine. IEEE Trans. Ind. Appl. 2021, 57, 835–844. - Y. Zhang, Z. Yin, W. Li, J. Liu and Y. Zhang, “Adaptive Sliding‐Mode‐Based Speed Control in Finite Control Set Model Predictive Torque Control for Induction Motors,” in IEEE Transactions on Power Electronics, vol. 36, no. 7, pp. 8076‐8087, July 2021, doi: 10.1109/TPEL.2020.3042181.
- Norambuena, M.; Rodríguez, J.; Zhang, Z.B.; Wang, F.X.; Garcia, C.; Kennel, R. A Very Simple Strategy for High‐Quality Performance of AC Machines Using Model Predictive Control. IEEE Trans. Power Electron. 2019, 34, 794–800.
- Mamdouh, M.; Abido, M.A. Efficient Predictive Torque Control for Induction Motor Drive. IEEE Trans. Ind. Electron. 2019, 66, 6757–6767
- Geyer, T. Algebraic tuning guidelines for model predictive torque and flux control. IEEE Trans. Ind. Appl. 2018, 51, 4464–4475.
- Mohamed Azab, Comparative Study of BLDC Motor Drive with Different Approaches: FCS‐Model
Predictive Control and Hysteresis Current Control, World Electric. Vehicle. Journal, MDPI. 2022, vol. 13, no. 7: 112, pp. 1‐22. MDPI, June 2022. https://doi.org/10.3390/wevj13070112. - X. Wang, H. Zhang, S. Sun, Y. Gao and B. Jin, “Energy Recovery and Utilization Efficiency Improvement for Motor‐Driven System Using Dynamic Energy Distribution Method,” in IEEE Transactions on Vehicular Technology, vol. 71, no. 10, pp. 10327‐10336, Oct. 2022, doi: 10.1109/TVT.2022.3187051.
- Y. Zhang, W. Yuan, R. Fu and C. Wang, “Design of an Energy‐Saving Driving Strategy for Electric Buses,” in IEEE Access, vol. 7, pp. 157693‐157706, 2019, doi: 10.1109/ACCESS.2019.2950390.
Y. Zhang, Y. Zhang, Z. Ai, Y. L. Murphey and J. Zhang, “Energy Optimal Control of Motor Drive System
for Extending Ranges of Electric Vehicles,” in IEEE Transactions on Industrial Electronics, vol. 68, no. 2, pp. 1728‐1738, Feb. 2021, doi: 10.1109/TIE.2019.2947841. - S. Wang, Q. Zhang, G. Kang, X. Fan, S. Zhang and J. Bao, “An Optimization Method for Improving
Efficiency of Electric Propulsion System of Electric Seaplane,” in IEEE Access, vol. 11, pp. 31052‐31061, 2023, doi: 10.1109/ACCESS.2023.3249293. - M. N. Almani, G. A. Hussain and A. A. Zaher, “An Improved Technique for Energy‐Efficient Starting and Operating Control of Single Phase Induction Motors,” in IEEE Access, vol. 9, pp. 12446‐12462, 2021, doi:10.1109/ACCESS.2021.3050920.
- V. R. Babu, T. Maity and G. Ramesh, “Speed Control and Optimum Efficiency of Induction Motor Driven Ventilation Fan in Mines,” 2019 IEEE International Conference on Electrical, Computer and Communication Technologies (ICECCT), Coimbatore, India, 2019, pp. 1‐4, doi: 10.1109/ICECCT.2019.8869355
- Golsorkhi, M.S.; Binandeh, H.; Savaghebi, M. Online Efficiency Optimization and Speed Sensorless Control of Single‐Phase Induction Motors. Appl. Sci. 2021, 11, 8863. https://doi.org/10.3390/app11198863
- S. Nassiri, M. Labbadi, C. Chatri and M. Cherkaoui, “Optimal Efficiency Controller Design of Pumping
Systems,” 2024 American Control Conference (ACC), Toronto, ON, Canada, 2024, pp. 4493‐4498, doi:
10.23919/ACC60939.2024.10645052. - Shukla, N. K., Srivastava, R., & Mirjalili, S. (2022). A hybrid dragonfly algorithm for efficiency optimization of induction motors. Sensors, 22, 2594. https://doi.org/10.3390/s22072594
- Z. Ma and D. Sun, “Energy Recovery Strategy Based on Ideal Braking Force Distribution for Regenerative Braking System of a Four‐Wheel Drive Electric Vehicle,” in IEEE Access, vol. 8, pp. 136234‐136242, 2020, doi:10.1109/ACCESS.2020.3011563.
- Q. Xu, F. Wang, X. Zhang and S. Cui, “Research on the Efficiency Optimization Control of the Regenerative Braking System of Hybrid Electrical Vehicle Based on Electrical Variable Transmission,” in IEEE Access, vol.7, pp. 116823‐116834, 2019, doi: 10.1109/ACCESS.2019.2936370.
- S. Dabral, S. Basak and C. Chakraborty, “Regenerative Braking Efficiency Enhancement Using Pole‐
Changing Induction Motor,” in IEEE Transactions on Transportation Electrification, vol. 10, no. 3, pp. 7580‐7590, Sept. 2024, doi: 10.1109/TTE.2023.3331448. - [270] N. B. b. Ahamad, C. ‐L. Su, X. Zhaoxia, J. C. Vasquez, J. M. Guerrero and C. ‐H. Liao, “Energy
Harvesting From Harbor Cranes With Flywheel Energy Storage Systems,” in IEEE Transactions on Industry Applications, vol. 55, no. 4, pp. 3354‐3364, July‐Aug. 2019, doi: 10.1109/TIA.2019.2910495. - [271] M. Becker, M. Stender and O. Wallscheid, “Nonlinear Efficiency‐Optimal Model Predictive Torque Control of Induction Machines,” in IEEE Journal of Emerging and Selected Topics in Power Electronics, vol. 12, no. 5, pp. 4740‐4753, Oct. 2024, doi: 10.1109/JESTPE.2024.3437739.
- https://new.abb.com/drives/dtc
- https://www.danfoss.com/en/about‐danfoss/our‐businesses/drives/
- https://www.deltaww.com/en‐US/products/AC‐Motor‐Drives/ALL/
- https://www.eaton.com/us/en‐us/products/controls‐drives‐automation‐sensors/variable‐frequency‐
drives.html - https://www.emotron.com/products/variable‐frequency‐drives‐vdf/
- https://www.fujielectric.com/products/drives_inverters/ac_drives_lv/index.html
- https://hitachiacdrive.com/
- https://www.inomaxtechnology.com/product‐category/motion‐control/variable‐frequency‐ drives/
- https://www.invertekdrives.com/
- https://emea.mitsubishielectric.com/fa/products/drv/inv
- https://acim.nidec.com/en/drives/control‐techniques/Products
- https://industrial.omron.eu/en/products/variable‐speed‐drives
- https://www.rockwellautomation.com/en‐gb/products/hardware/allen‐bradley/vfd.html
- https://www.se.com/us/en/product‐category/2900‐variable‐speed‐drives/
- https://www.siemens.com/us/en/products/drives/sinamics‐electric‐drives.html
- https://www.toshiba.com/tic/motors‐drives
https://www.weg.net/catalog/weg/US/en/Drives/Variable‐Speed‐Drives/c/GLOBAL_WDC_DRV_IF - https://www.yaskawa.com/products/drives/industrial‐ac‐drives
- https://literature.rockwellautomation.com/idc/groups/literature/documents/td/750‐td100_‐en‐p.pdf
- https://literature.rockwellautomation.com/idc/groups/literature/documents/wp/drives‐wp002_‐en‐p.pdf
Disclaimer/Publisher’s Note: The statements, opinions and data contained in all publications are solely those of the individual author(s) and contributor(s) and not of MDPI and/or the editor(s). MDPI and/or the editor(s) disclaim responsibility for any injury to people or property resulting from any ideas, methods, instructions or products referred to in the content.
Copyright and Source Material:
This summary is based on the paper "A Review of Recent Trends in High Efficiency Induction Motor Drives" by Mohamed Ahmed Azab.
Paper Source: doi: 10.20944/preprints202412.1530.v2
This summary is for informational purposes only and should not be used for commercial purposes without permission from the author.
Copyright © 2025 CASTMAN. All rights reserved.