This introduction paper is based on the paper "Double-Sided Surface Structures with Undercuts on Cold-Rolled Steel Sheets for Interlocking in Hybrid Components" published by "MDPI".
![Figure 1. Scheme of the rolling process for surface structures (as proposed by Senge et al. [15]); view
in the normal direction (ND) and transverse direction (TD)](https://castman.co.kr/wp-content/uploads/image-1904-1024x219.webp)
1. Overview:
- Title: Double-Sided Surface Structures with Undercuts on Cold-Rolled Steel Sheets for Interlocking in Hybrid Components
- Author: Aron Ringel, Sindokht Shayan and David Bailly
- Year of publication: 2024
- Journal/academic society of publication: Machines
- Keywords: interlocking; multi-material components; structured cold rolling; FE-modelling
2. Abstract:
Weight reduction strategies are essential for the transportation sector to reduce greenhouse gas emissions or extend the range of electric vehicles. In the field of lightweight assembly strategies, multi-material design offers great potential. Joining materials typically used in the automotive sector, such as aluminum and steel, brings challenges as conventional processes such as fusion welding are unsuitable. Therefore, new technologies can extend the design options. In previous studies, a mechanical interlocking between cold-rolled surface structures with undercuts on a steel sheet and die-cast aluminum was presented. This method has now been extended to double-sided structures for more complex applications with a joint on both sheet surfaces. Numerical simulations and validation experiments were performed to investigate the manufacturing of the double-sided structures. Furthermore, the influence of the alignment of the upper and lower structures in relation to each other on the resulting structural geometry and the rolling forces were analyzed. More advantageous geometric parameters, e.g., 24% larger undercuts, and approx. 24.1% lower forming forces at 20% height reduction were observed for a shifted alignment. However, significantly higher wear of the structured rollers occurred in the corresponding experiments.
3. Introduction:
Lightweight structures are imperative in the transportation sector to meet demands for reduced greenhouse gas emissions and increased electric vehicle range, while maintaining part properties like stiffness and collision safety [1, 2]. Multi-material design, particularly combining low-density aluminum with high-strength steel, presents an attractive solution [3]. However, joining these dissimilar materials poses challenges, as conventional techniques like welding can lead to brittle intermetallic phases (IMPs) [4]. Joining by forming processes, including mechanical joining methods like riveting or clinching, and hybrid molding or casting processes, offer alternatives [5, 6, 7, 8]. Hybrid casting, specifically, allows for complex part geometries and mass production, potentially achieving metallurgical bonding [9] or mechanical interlocking [7]. Mechanical interlocking typically involves surface structuring followed by assembly. A promising method for structuring large steel sheet surfaces involves a multi-pass cold rolling process to create channel structures with undercuts, which are subsequently filled by, for example, die-cast aluminum [15, 16]. This process, previously studied for single-sided structures achieving joint strengths up to 45 MPa [16], involves an initial structural rolling pass followed by a flattening pass to form the undercuts (Figure 1). This study extends the concept to double-sided structures required for more complex components, such as a demonstrator part based on a roof cross beam section (Figure 2), investigating the manufacturing process for structures on both sides of the steel sheet insert.
4. Summary of the study:
Background of the research topic:
The development of lightweight multi-material components, particularly combining steel and aluminum, is crucial for the automotive industry. Effective joining methods that avoid the formation of brittle intermetallic phases common in fusion welding are required. Mechanical interlocking via surface structuring prior to hybrid casting (e.g., High-Pressure Die Casting - HPDC) is a viable alternative.
Status of previous research:
Previous research established a multi-pass cold rolling process (structural rolling followed by flattening) to create single-sided surface structures with undercuts on steel sheets for mechanical interlocking with die-cast aluminum [15]. Studies investigated the process parameters, resulting geometry (undercuts Wf-uc, inner notches Wf-no), joint strength (up to 45 MPa) [16], FE-modelling of the process [17], and the influence of subsequent bending [20]. A demonstrator part requiring double-sided structures was conceptualized, and its compound strength focusing on casting parameters was analyzed [21]. However, the forming process analysis remained limited to single-sided structures.
Purpose of the study:
The primary aim was to understand the material flow and structural formation during the manufacturing of double-sided surface structures using the established cold rolling and flattening technique. Specifically, the study sought to investigate how simultaneous imprinting from both sides affects channel and undercut formation, comparing two distinct alignments: a "mirrored" alignment and a "shifted" alignment (Figure 3). The goal was to use this understanding to optimize the process regarding undercut width and resulting joint strength.
Core study:
The study extended the cold rolling and flattening method to create double-sided structures on DC04 steel sheets. Two configurations were investigated: a mirrored alignment (ribs opposite ribs, channels opposite channels) and a shifted alignment (ribs opposite channels). Finite Element (FE) simulations (using Abaqus) were developed and validated through physical rolling experiments. The research analyzed the influence of the alignment on the resulting structural geometry (channel depth ∆hs, undercut width Wf-uc, inner notch length Wf-no) and the required rolling forces during both the structural rolling and flattening passes.
5. Research Methodology
Research Design:
The study employed a comparative research design, investigating two different alignments (mirrored and shifted) for double-sided surface structures. The methodology combined numerical simulation (2D FE-modelling) with experimental validation (structural cold-rolling experiments).
Data Collection and Analysis Methods:
- FE-Simulation: 2D FE models were developed in Abaqus 2017, based on previous single-sided models [17], assuming plane strain conditions. The model simulated structural rolling using rigid rollers (punches) and subsequent flattening, incorporating Arbitrary Lagrangian-Eulerian (ALE) meshing and mapping of field variables (stresses, strains) between passes [23]. A friction coefficient µ = 0.07 was used [22]. Convergence studies were performed for mesh size and friction sensitivity. Geometric features (∆hf, Wf-uc, Wf-no) were evaluated using Python scripts. Rolling forces from the 2D simulation were transformed for comparison with experiments using Equation (6).
- Experimental Validation: Rolling was performed on a Dreistern P3.160 roll-forming machine using DC04 steel sheets (ho = 2.0 mm). Profiled rollers (92.5 mm radius) created the initial structure, and flat rollers (93.0 mm radius) performed the flattening pass at 5.8 m/min. Lateral guide rails were used. Rolling forces were measured using load cells. Cross-sections were prepared via water jet cutting, polished, and etched with 3% Nital. Geometry was measured using a Keyence VHX-7000 digital microscope. Height reductions (ɛh,1, ɛh,2) and average geometric features (Wf-uc, Wf-no) were calculated using Equations (1, 3, 4, 5).
Research Topics and Scope:
The research focused on the manufacturing process of double-sided undercut structures on cold-rolled DC04 steel sheets via structured cold rolling and flattening. The scope included:
- Investigating the feasibility of creating double-sided structures.
- Comparing the "mirrored" versus "shifted" alignment of upper and lower structures.
- Analyzing material flow using FE simulation (PEEQ) and experimental cross-sections.
- Quantifying the resulting geometry (channel depth, undercut width, inner notch length) as a function of process parameters (height reduction).
- Measuring and simulating the rolling forces for both alignments and process steps.
- Validating simulation results with experimental data.
6. Key Results:
Key Results:
- Material Flow: FE simulations (Figure 6) and etched experimental cross-sections (Figure 7) indicated different material flow patterns for the two alignments. The mirrored alignment suggested lateral and vertical flow from the channel into the ribs, while the shifted alignment showed evidence of shearing at the intersection between channels and ribs.
- Structural Rolling: Experimental channel depth formation for double-sided structures showed better agreement with simulations compared to previous single-sided studies [17] (Figure 8). A total channel depth (∆hs = ∆hs,up + ∆hs,low) of 1.0 mm was achieved at approximately 27% height reduction (ɛh,1) for the mirrored alignment and 26% for the shifted alignment (Table 1). Experimentally, the mirrored alignment required significantly higher rolling forces (approx. 24.1% higher at 20% ɛh,1) compared to the shifted alignment (Figure 10a), potentially due to the different material flow mechanisms.
- Flattening: Good agreement was found between simulated and experimental undercut widths (Wf-uc) (Figure 9a). The shifted alignment consistently produced larger undercuts (experimental maximum ~84 µm vs. ~68 µm for mirrored). Inner notch (Wf-no) development was predicted similarly for both alignments in simulations, but experiments showed larger inner notches for the shifted alignment (Figure 9b). Experimental flattening forces were constant (~48 kN) and higher than simulations, likely due to wider experimental rollers contacting undeformed material; no significant difference in force was observed between alignments experimentally (Figure 10b).
- Roller Wear: Significant wear, particularly shearing of roller rib edges, was observed on the experimental rollers, especially for the shifted alignment when rolling plate material (attributed to preloading and elastic roll gap changes).
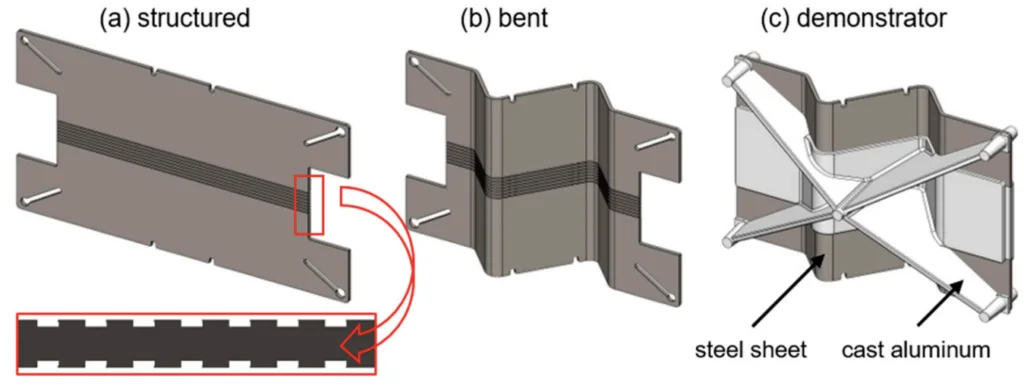
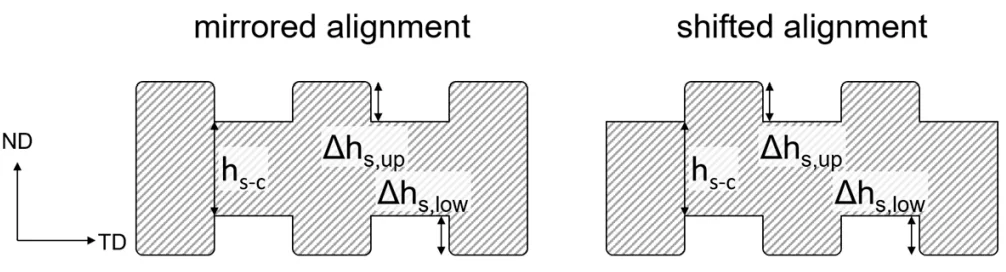
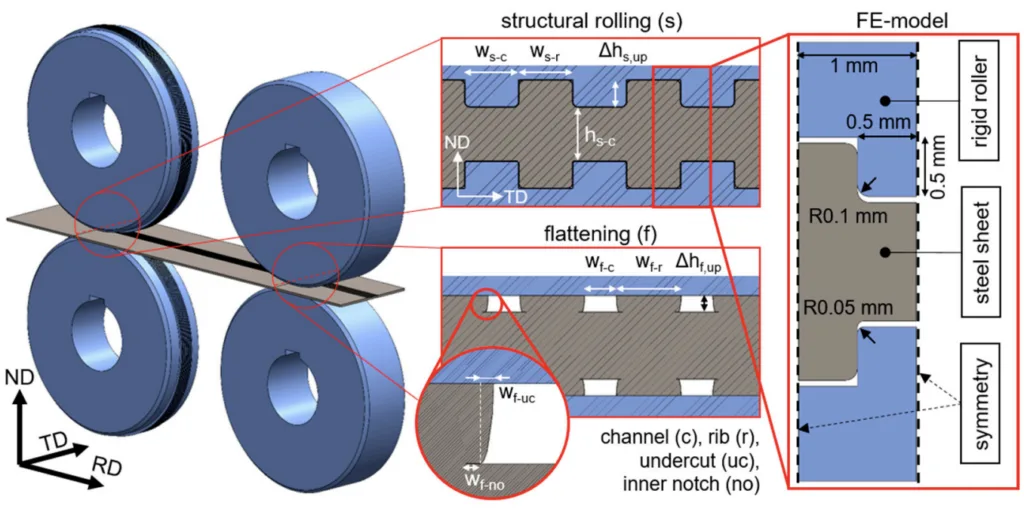
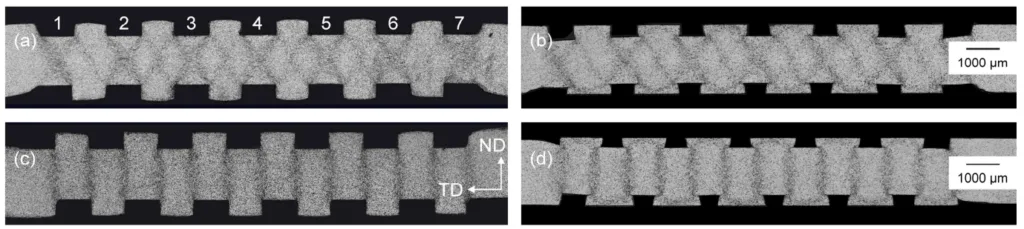
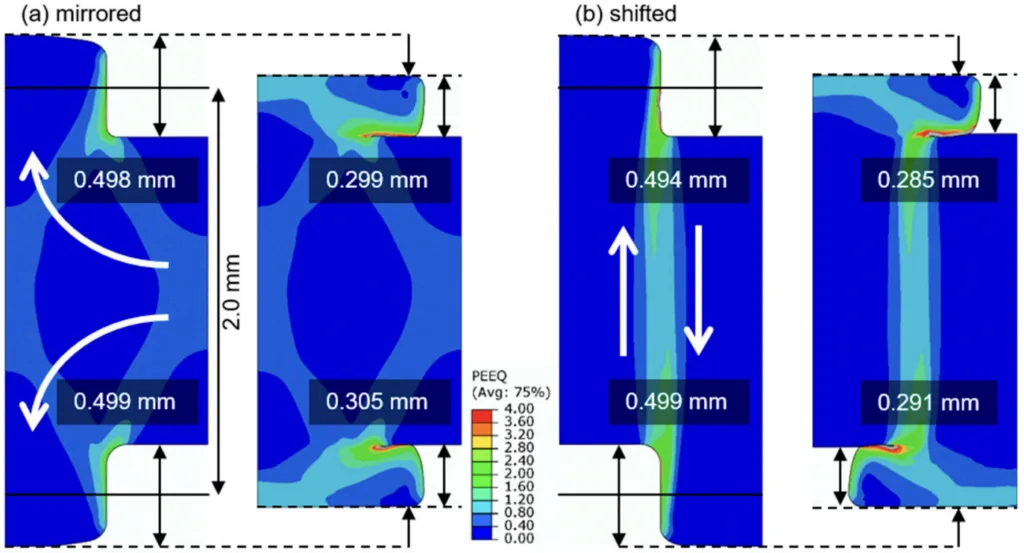
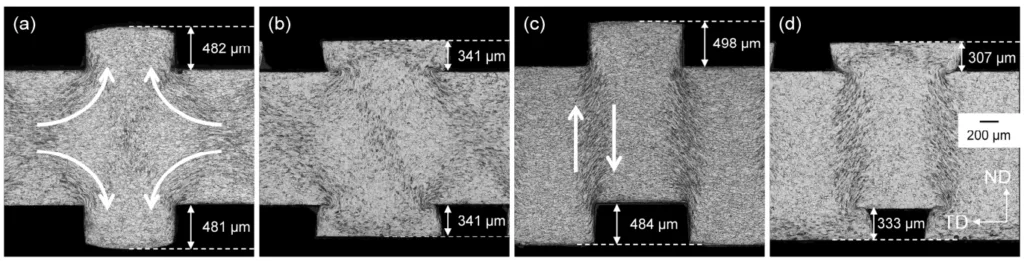
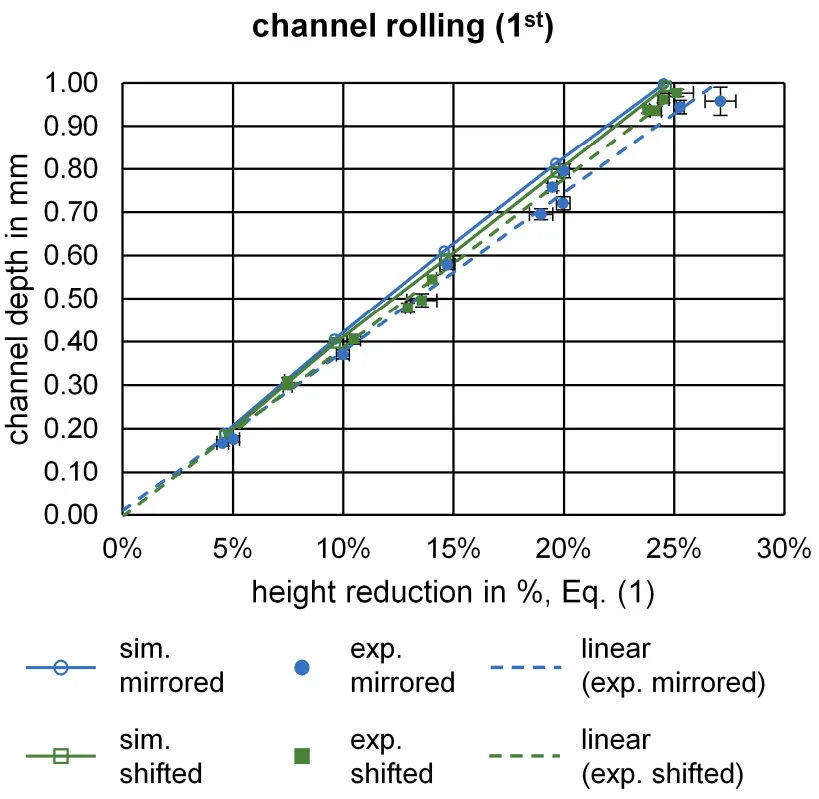
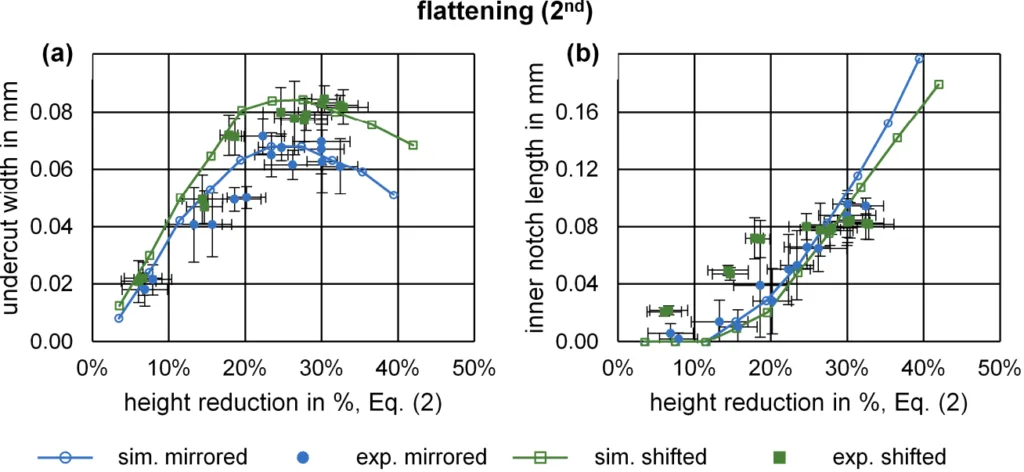
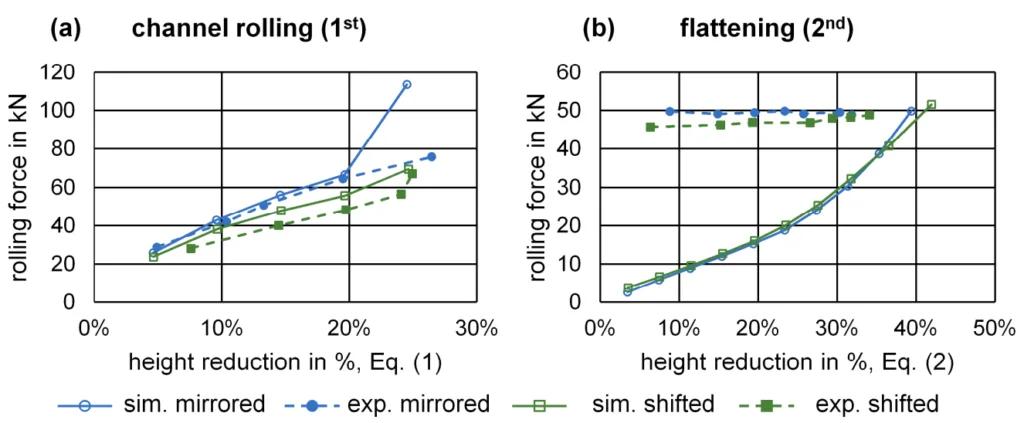
Figure Name List:
- Figure 1. Scheme of the rolling process for surface structures (as proposed by Senge et al. [15]); view in the normal direction (ND) and transverse direction (TD).
- Figure 2. Examples of surface structures on steel sheets after (a) rolling and cutting, (b) bending, and (c) casting of the demonstrator part.
- Figure 3. Investigated alignments of the double-sided surface structure.
- Figure 4. 3D scheme of the rolling process and 2D simplification in the FE simulation.
- Figure 5. Cross-section preparations of (a) structural rolling, mirrored, (b) flattening, mirrored, (c) structural rolling, shifted, (d) flattening, shifted.
- Figure 6. Exemplary material flow in FE simulations by equivalent plastic strain (PEEQ) after structural rolling and flattening.
- Figure 7. Close-up cross-section measurement examples of (a) structural rolling, mirrored, (b) flattening, mirrored, (c) structural rolling, shifted, (d) flattening, shifted.
- Figure 8. Channel depth after structural rolling for simulations vs. experiments of both alignments.
- Figure 9. (a) Undercut width and (b) inner notch length after flattening for simulations vs. experiments of both alignments.
- Figure 10. Max. rolling forces for (a) channel rolling and (b) flattening for simulations vs. experiments of both alignments.
7. Conclusion:
This study successfully simulated and experimentally validated a double-sided structural rolling process for creating undercut features on steel sheets. Good agreement between simulation and experiment was achieved for the resulting geometry, particularly undercut width during flattening. The experiments revealed less ideal channel formation at the sheet edges compared to the middle channels. The mirrored alignment exhibited higher rolling forces during structural rolling compared to the shifted alignment. Conversely, the shifted alignment yielded larger undercuts (potentially beneficial for joint strength) but also showed a tendency for larger inner notches experimentally and caused significant roller wear in the experimental setup using plate material. The choice between alignments involves trade-offs: the shifted alignment offers larger undercuts and lower structural rolling forces but potentially increases wear and inner notch formation. Future work will involve analyzing the influence of kinetics and guide rails on structural homogeneity and testing the compound strength of the shifted alignment structures in combination with HPDC aluminum.
8. References:
- [1] Kim, H.C.; Wallington, T.J. Life-cycle energy and greenhouse gas emission benefits of lightweighting in automobiles: Review and harmonization. Environ. Sci. Technol. 2013, 47, 6089–6097. [CrossRef] [PubMed]
- [2] Cecchel, S. Materials and Technologies for Lightweighting of Structural Parts for Automotive Applications: A Review. SAE Int. J. Mater. Manf. 2021, 14, 81–97. [CrossRef]
- [3] Mori, K.; Abe, Y. A review on mechanical joining of aluminium and high strength steel sheets by plastic deformation. Int. J. Lightweight Mater. Manuf. 2018, 1, 1–11. [CrossRef]
- [4] Meschut, G.; Janzen, V.; Olfermann, T. Innovative and Highly Productive Joining Technologies for Multi-Material Lightweight Car Body Structures. J. Mater. Eng. Perform. 2014, 23, 1515–1523. [CrossRef]
- [5] Mori, K.; Bay, N.; Fratini, L.; Micari, F.; Tekkaya, A.E. Joining by plastic deformation. CIRP Ann. Manuf. Technol. 2013, 62, 673–694. [CrossRef]
- [6] Salamati, M.; Soltanpour, M.; Fazli, A.; Zajkani, A. Processing and tooling considerations in joining by forming technologies; part A—Mechanical joining. Int. J. Adv. Manuf. Technol. 2019, 101, 261–315. [CrossRef]
- [7] Feistauer, E.E.; dos Santos, J.F.; Amancio-Filho, S.T. A review on direct assembly of through-the-thickness reinforced metal-polymer composite hybrid structures. Polym. Eng. Sci. 2019, 59, 661–674. [CrossRef]
- [8] Noguchi, T.; Asano, K.; Hiratsuka, S.; Miyahara, H. Trends of composite casting technology and joining technology for castings in Japan. Int. J. Cast Met. Res. 2008, 21, 219–225. [CrossRef]
- [9] Fang, X.; Gundlach, J.; Schipperges, J.-J.; Jiang, X. On the Steel–Aluminum Hybrid Casting by Sand Casting. J. Mater. Eng. Perform. 2018, 27, 6415–6425. [CrossRef]
- [10] Ma, Y.; Zhang, G.; Cao, S.; Huo, Z.; Han, J.; Ma, S.; Huang, Z. A Review of Advances in Fabrication Methods and Assistive Technologies of Micro-Structured Surfaces. Processes 2023, 11, 1337. [CrossRef]
- [11] Müller, S.; Brand, M.; Dröder, K.; Meiners, D. Increasing the Structural Integrity of Hybrid Plastics-Metal Parts by an Innovative Mechanical Interlocking Effect. Mater. Sci. Forum 2015, 825–826, 417–424. [CrossRef]
- [12] Buxton, A.L.; Ferhati, A.; Glen, R.J.; Dance, B.G.I.; Mullen, D.; Karayiiannis, T. EB Surface Engineering for High Performance Heat Exchangers. In Proceedings of the First International Electron Beam Welding Conference, Chicago, Illinois, USA, 17–18 November 2009.
- [13] Ucsnik, S.; Gradinger, R.; Becirovic, A.; Waldhör, A. Enhanced Performance of Steel-Aluminium Cast Nodes through Cold Metal Transfer. Mater. Sci. Forum 2013, 765, 736–740. [CrossRef]
- [14] Abe, H.; Chung, J.C.; Mori, T.; Hosoi, A.; Jespersen, K.M.; Kawada, H. The effect of nanospike structures on direct bonding strength properties between aluminum and carbon fiber reinforced thermoplastics. Compos. Part B Eng. 2019, 172, 26–32. [CrossRef]
- [15] Senge, S.; Brachmann, J.; Hirt, G.; Bührig-Polaczek, A. Interlocking Multi-Material Components made of Structured Steel Sheets and High-Pressure Die Cast Aluminium. In Proceedings of the 20th International ESAFORM Conference on Material Forming, Dublin, Ireland, 26–28 April 2017; p. 190007.
- [16] Senge, S.; Brachmann, J.; Hirt, G.; Bührig-Polaczek, A. Evaluation of interlocking bond strength between structured 1.0338 steel sheets and high pressure die cast AlMg5Si2. In Proceedings of the 21st International ESAFORM Conference on Material Forming, Palermo, Italy, 23–25 April 2018; p. 40019.
- [17] Ringel, A.; Lohmar, J. Optimization of the Surface Geometry in Structured Cold Rolling for Interlocking of Formed and Die-Cast Metal Components. Defect Diffus. Forum 2022, 414, 89–94. [CrossRef]
- [18] Jakumeit, J.; Behnken, H.; Laqua, R.; Eiken, J.; Brachmann, J. Multi-scale simulation of hybrid light metal structures produced by high pressure die casting. IOP Conf. Ser. Mater. Sci. Eng. 2020, 861, 12035. [CrossRef]
- [19] Joop, D. Präzisionsbestimmende Faktoren bei der Herstellung blechverstärkter Hybridstrukturen im Druckguss: Grenzflächenanalyse und Verzugsoptimierung. Doctoral Thesis, Gießerei-Institut, RWTH Aachen University, Aachen, Germany, 2018.
- [20] Ringel, A.; Hirt, G. Bending behavior of structured steel sheets with undercuts for interlocking with Al die-cast metal. Int. J. Mater. Form. 2024, 17, 2. [CrossRef]
- [21] Bruckmeier, L.; Ringel, A.; Vroomen, U.; Bailly, D.; Bührig-Polaczek, A. Influence of High-Pressure Die Casting Process Parameters on the Compound Strength of Hybrid Components with Undercut Sheet Metal. Metals 2023, 13, 1717. [CrossRef]
- [22] Tieu, A.; Liu, Y. Friction variation in the cold-rolling process. Tribol. Int. 2004, 37, 177–183. [CrossRef]
- [23] Clausmeyer, T.; Schowtjak, A.; Wang, S.; Gitschel, R.; Hering, O.; Pavliuchenko, P.; Lohmar, J.; Ostwald, R.; Hirt, G.; Tekkaya, A.E. Prediction of Ductile Damage in the Process Chain of Caliber Rolling and Forward Rod Extrusion. Procedia Manuf. 2020, 47, 649–655. [CrossRef]
9. Copyright:
- This material is a paper by "Aron Ringel, Sindokht Shayan and David Bailly". Based on "Double-Sided Surface Structures with Undercuts on Cold-Rolled Steel Sheets for Interlocking in Hybrid Components".
- Source of the paper: https://doi.org/10.3390/machines12080562
This material is summarized based on the above paper, and unauthorized use for commercial purposes is prohibited.
Copyright © 2025 CASTMAN. All rights reserved.