This article introduces the paper ['Layout Design and Die Casting Using CAE Simulation for Household Appliances'] published by ['MDPI'].
1. Overview:
- Title: Layout Design and Die Casting Using CAE Simulation for Household Appliances
- Author: Hong-Kyu Kwon
- Publication Year: 2021
- Publishing Journal/Academic Society: Applied Sciences (MDPI)
- Keywords: gate system; high pressure die casting; CAE simulation; flow analysis; cooking grill
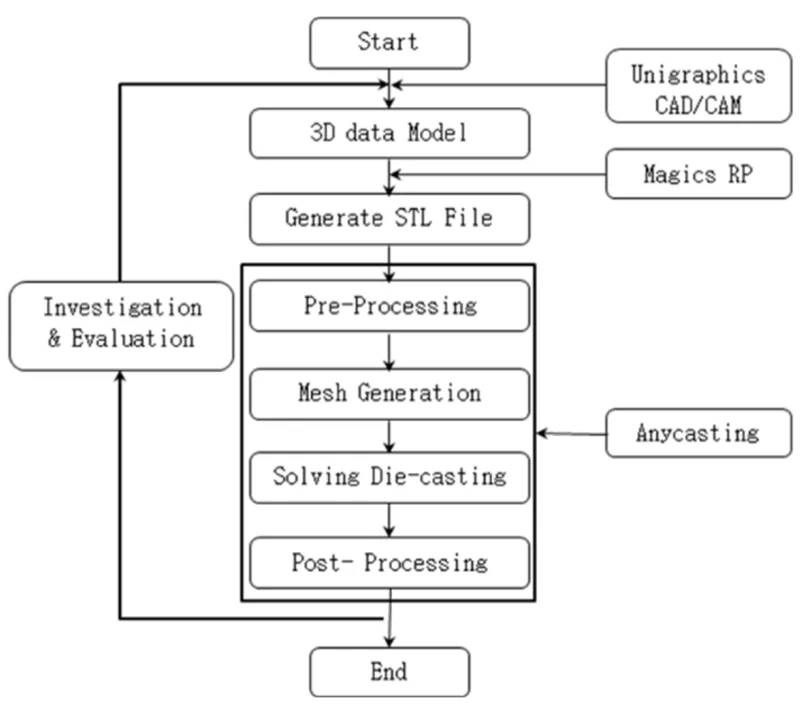
2. Abstracts or Introduction
The study investigates the application of Computer-Aided Engineering (CAE) technology in High-Pressure Die Casting (HPDC) for household appliances, specifically cooking grills. The research addresses the increasing demand for aluminum alloy components in various industries and the necessity for efficient casting layout designs to reduce production costs and enhance product quality. Traditional casting layout design, heavily reliant on expert experience, is becoming insufficient in the face of rapid technological advancements and economic pressures. CAE technology is presented as a solution to predict casting defects and optimize mold design through filling and solidification analysis, thereby minimizing trial and error in mold development and fabrication. The research aims to establish a sound casting layout for household appliance molds using CAE simulation to ensure product quality and reduce production costs.
3. Research Background:
Background of the Research Topic:
The development and industrialization of science and technology have led to increased utilization of aluminum alloys. Driven by resource conservation, energy efficiency, and environmental concerns, aluminum products are increasingly replacing cast iron components in the foundry industry, particularly in High-Pressure Die Casting (HPDC). HPDC is recognized as an economical mass production technology for complex parts, crucial in consumer goods, automotive, and electronics industries demanding high quality, low cost, and short delivery times. However, HPDC necessitates advanced mold-making techniques due to the high melt temperatures, mold surface pressures, and product complexity.
Status of Existing Research:
Existing research acknowledges the critical role of casting layout design and gating systems in HPDC, traditionally dependent on mold designers' experience. The application of CAE technology is rapidly growing to address the limitations of experience-based design. Prior studies have demonstrated the effectiveness of CAE in various casting process analyses, including solidification simulation for thin-walled housings [10], filling and solidification analysis for fuel cell bipolar plates [11], optimization of automobile gear housings [13], and LPDC parameter optimization for thin-walled components [14]. Furthermore, research has explored semi-automated gating system design using computer-aided parametric design [15]. These studies highlight the trend towards utilizing CAE simulation to enhance casting process design and defect prediction.
Necessity of the Research:
The traditional trial-and-error approach in casting layout design and mold making is time-consuming and costly. The advancement of CAE technology offers a significant opportunity to reduce this reliance on empirical methods. There is a need for methodologies that can quickly and accurately predict filling and solidification processes in die casting to establish robust and cost-effective production methods. Specifically, for household appliances like cooking grills, optimizing the casting layout through CAE simulation can ensure product quality by minimizing defects such as air porosities and shrinkage, while simultaneously reducing production costs and time associated with mold development and fabrication.
4. Research Purpose and Research Questions:
Research Purpose:
The primary purpose of this research is to utilize CAE simulation technology to predict filling and solidification processes in die casting for household appliances (cooking grills). This aims to establish sound casting methods that minimize production costs and ensure product quality. The study seeks to analyze mold filling and solidification processes to develop a defect control method and determine the optimal casting method for die-casting mold design and fabrication.
Key Research:
The key research focuses on applying CAE simulation software (AnyCasting) to analyze three different casting layouts for a cooking grill made of ADC 12 alloy. The research investigates the impact of gating system design on melt flow and solidification patterns to minimize internal air porosities and shrinkage defects, thereby ensuring casting quality and stability.
Research Hypotheses:
The research hypothesizes that by employing CAE simulation and systematically modifying the gating system design, specifically by transitioning from a multi in-gate system (Case 1) to a ring gate system (Case 2 and 3) and further refining the biscuit design (Case 3), it is possible to achieve a more balanced melt flow, reduce air porosity isolation, minimize backflow and eddy phenomena, and optimize solidification to reduce shrinkage defects in the die-cast cooking grill. The study anticipates that Case 3, with its refined gating and biscuit design, will demonstrate superior casting performance compared to Case 1 and Case 2, leading to an optimal casting layout.
5. Research Methodology
Research Design:
This research employs a simulation-based experimental design using CAE software (AnyCasting) to analyze and compare the performance of three different casting layouts for a household appliance (cooking grill). The study focuses on numerical analysis of melt flow and solidification processes under controlled conditions defined by material properties, process parameters, and mold design variations.
Data Collection Method:
Data is collected through CAE simulations performed using AnyCasting software. The simulation process involves pre-processing of 3D CAD models, mesh generation, solving die-casting process equations, and post-processing to visualize and analyze the results. The software utilizes a hybrid numerical analysis method combining the PM (Porous Media) method and the Cut-Cell method. The simulation outputs include visual representations of melt flow patterns at different filling stages and solidification progression, as well as predicted locations of air porosity and shrinkage defects.
Analysis Method:
The analysis method involves a comparative assessment of the simulation results for the three casting layouts. Flow analysis results are evaluated based on melt flow uniformity, presence of misruns or cold shuts, air porosity isolation, and backflow phenomena. Solidification analysis results are assessed based on the location and extent of predicted shrinkage defects. Qualitative and visual analysis of the simulation outputs, particularly Figures 3-11, are used to compare the performance of each casting layout and identify the optimal design.
Research Subjects and Scope:
The research subject is the die casting process for a household appliance cooking grill made of ADC12 aluminum alloy. The scope of the study is limited to numerical simulation analysis of three specific casting layout designs (Case 1, Case 2, and Case 3) using AnyCasting software. The material properties, process parameters (injection speed, temperatures), and mold material (SKD61) are defined based on typical HPDC conditions. The analysis focuses on filling and solidification stages, aiming to optimize the gating system and overall casting layout for defect minimization and quality enhancement.
6. Main Research Results:
Key Research Results:
- Flow Analysis:
- Case 1 (eight in-gates): Demonstrated imbalanced flow and potential air porosity isolation (Figure 4).
- Case 2 (ring gate): Improved flow balance compared to Case 1, but showed vortex formation in biscuits (sprues) and backflow phenomena (Figure 6).
- Case 3 (modified ring gate with round biscuit feature): Exhibited the most uniform melt flow, minimized backflow and eddy phenomena, and reduced air porosity (Figure 8, Figure 11).
- Solidification Analysis:
- Solidification analysis for Case 3 indicated potential shrinkage defects in thick areas (Figure 9, Figure 10).
- The modular method in AnyCasting was used to identify shrinkage defect areas.
- The study suggests controlling mold temperature and implementing detailed cooling designs to mitigate shrinkage porosity.
Analysis of presented data:
- Figure 3: Shows melt filling process for all three cases (Case 1, 2, 3) at different percentages (25%, 45%, 60%, 80%, 93%, 96%). Cases 2 and 3 exhibit more uniform filling compared to Case 1.
- Figure 4: Highlights imbalanced flow and expected isolated air porosity areas in Case 1 at 93% and 96% filling stages.
- Figure 5: Compares 96% filling behavior of Case 1 and Case 2, showing improved flow balance and reduced isolated areas in Case 2 due to gating system redesign.
- Figure 6: Illustrates vortex formation in biscuits for Case 2 at 45% and 60% filling stages, indicating potential backflow issues.
- Figure 7: Depicts the gate system design differences between Case 2 and Case 3, emphasizing the round feature added to the biscuit in Case 3 to minimize backflow.
- Figure 8: Shows improved melt flow for Case 3 at 45% and 60% filling stages, demonstrating minimized vortex and backflow due to design modifications.
- Figure 9: Presents solidification simulation results for Case 3 at different solidification percentages (5%, 15%, 30%, 40%, 50%, 65%), indicating solidification isolated areas.
- Figure 10: Details the expected shrinkage defect area for Case 3 at 65% solidification, using AnyCasting's modular method.
- Figure 11: Displays final casting layout simulation results for Case 3 (Fixed and Moving sides) at different filling percentages (30%, 45%, 75%, 85%, 95%), showing minimized vortex flow and potential microporosity.
Figure Name List:
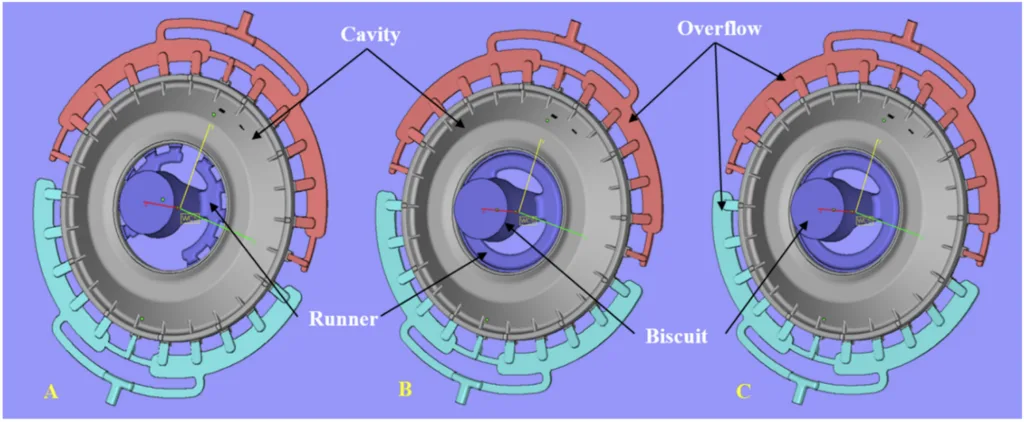
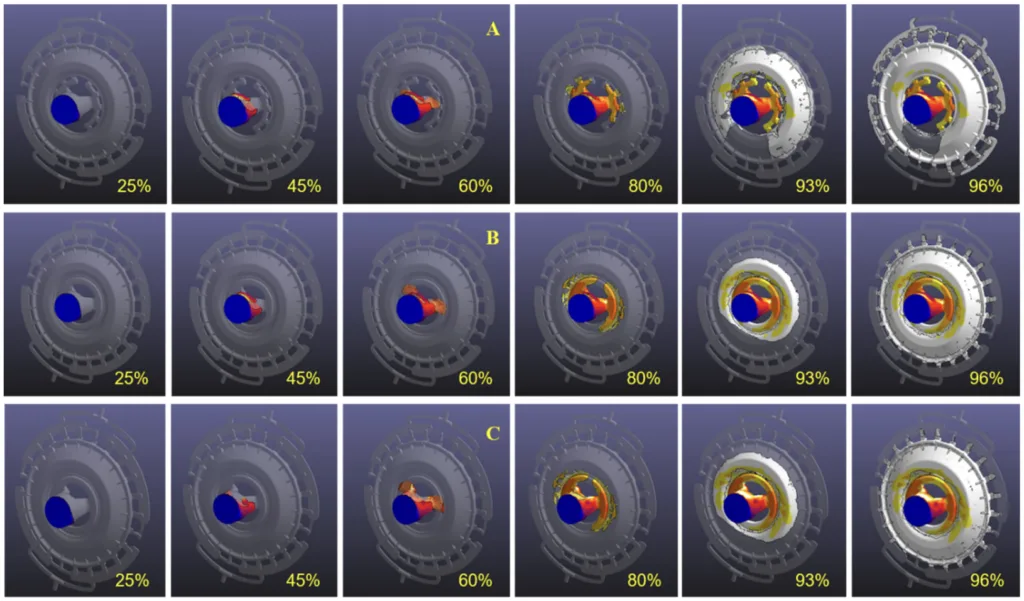
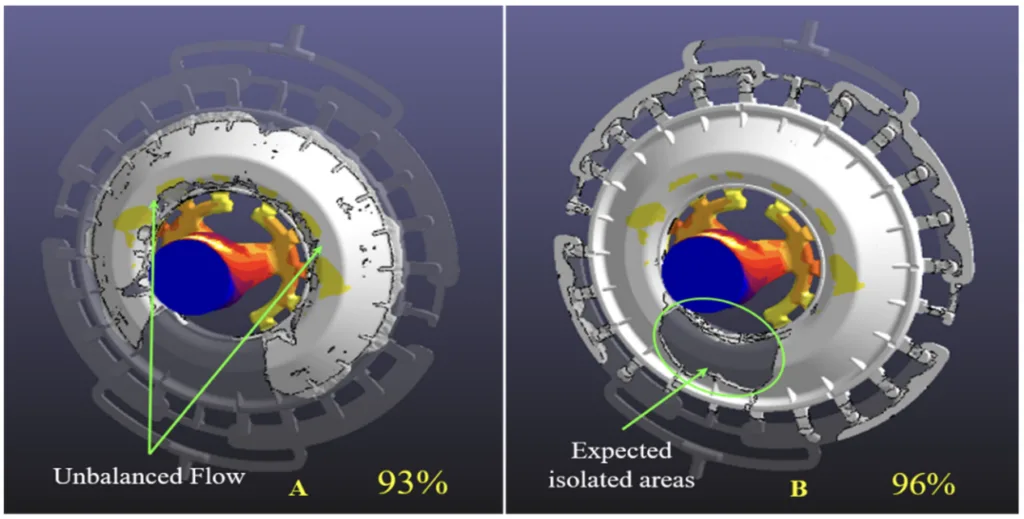
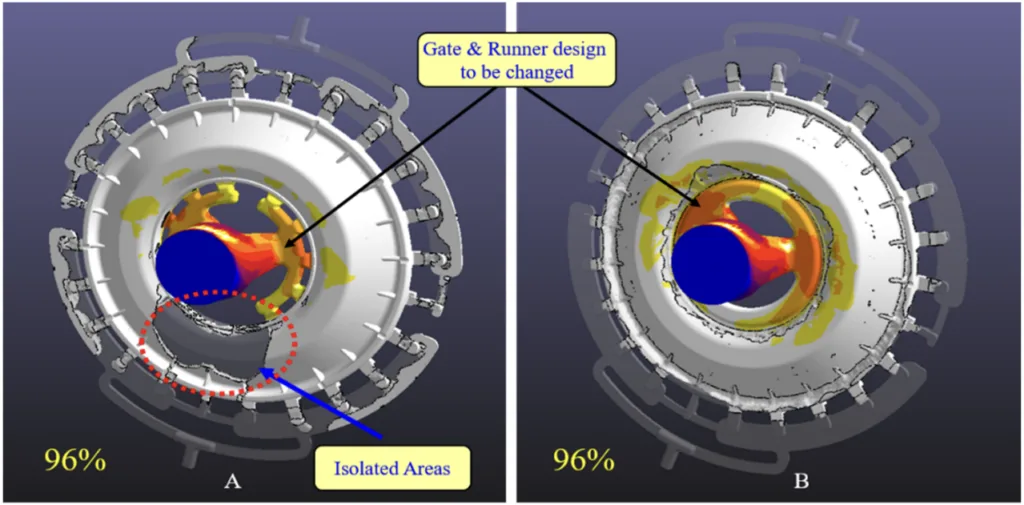
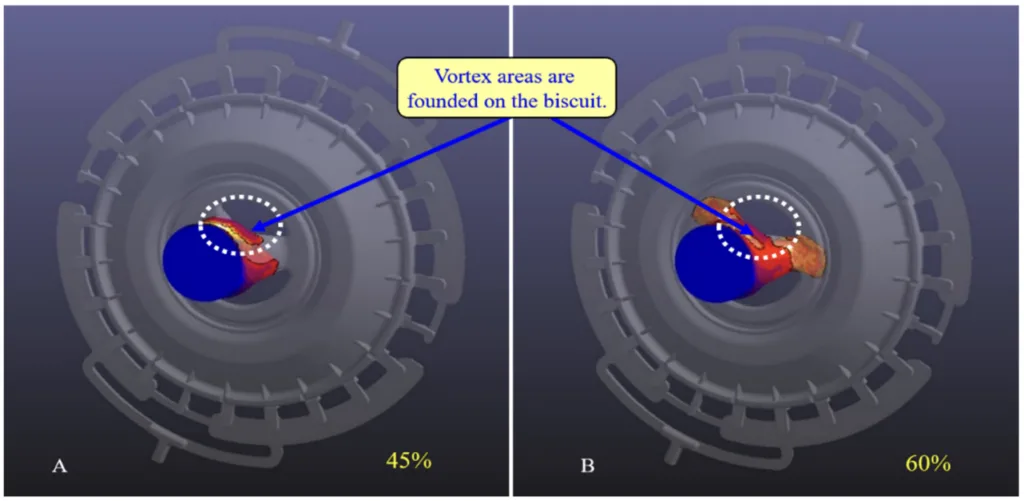
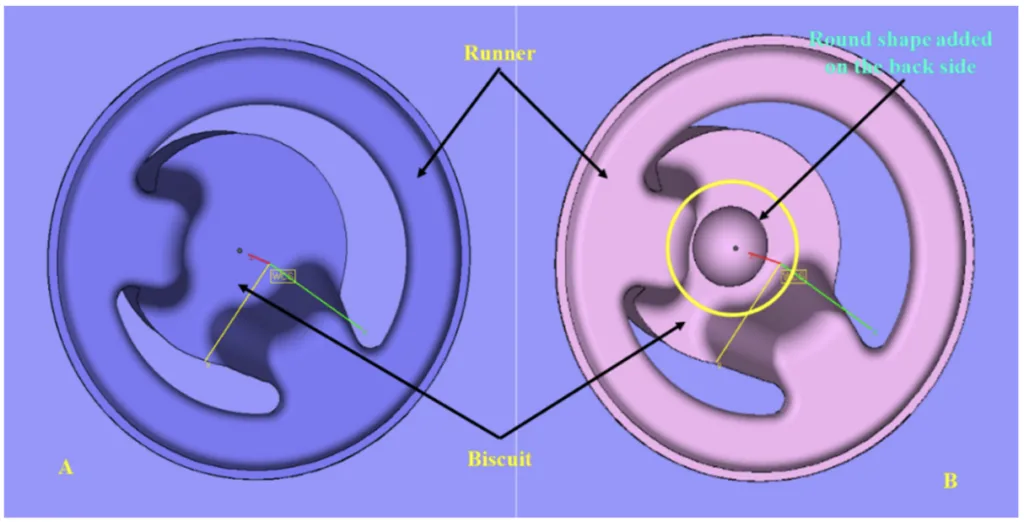
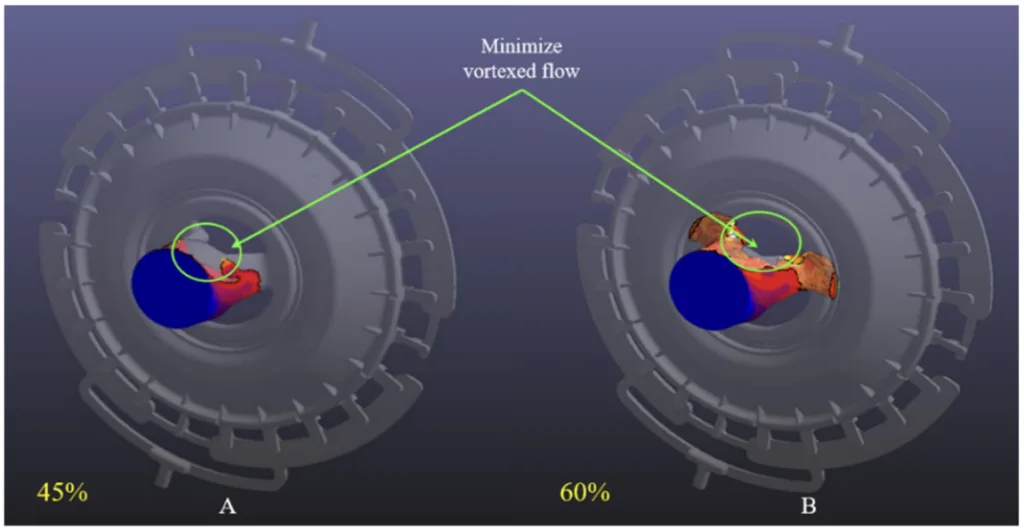
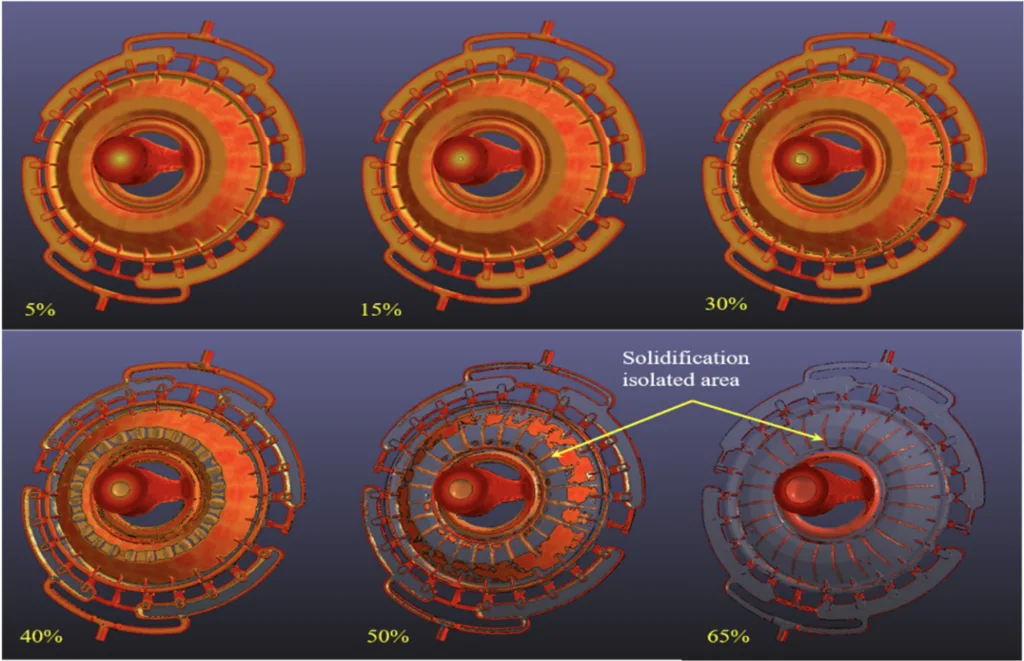
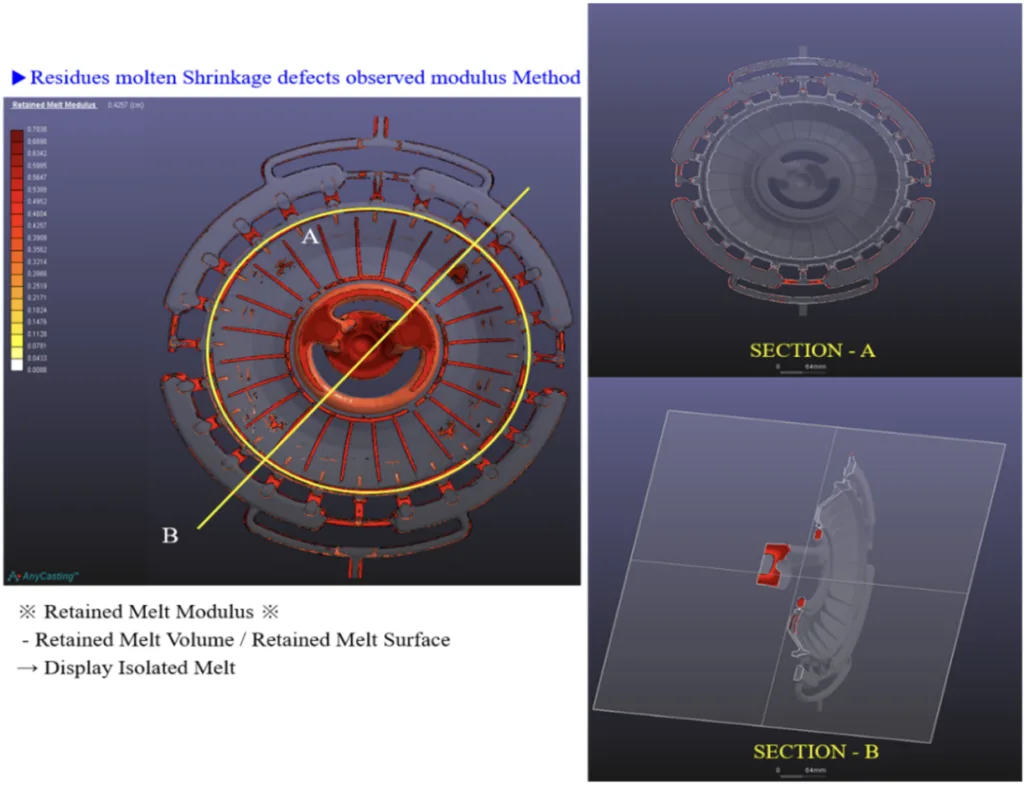
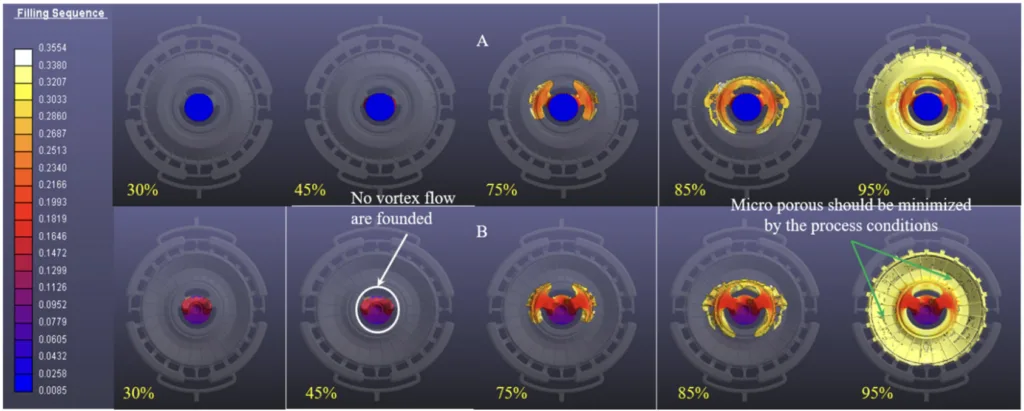
- Figure 1. Flow Chart of CAE simulation.
- Figure 2. Casting model of cooking grill: (A) Case 1; (B) Case 2; (C) Case 3.
- Figure 3. Simulation results of the melt filling process: (A) Case 1; (B) Case 2; (C) Case 3.
- Figure 4. Simulation results of the melt flow for Case 1: (A) 93% filling; (B) 96% filling.
- Figure 5. Simulation results of the melt flow: (A) 96% filling of case 1; (B) 96% filling of case 2.
- Figure 6. Simulation results of the melt flow for case 2: (A) 45% filling; (B) 60% filling.
- Figure 7. Gate system: (A) case 2; (B) case 3.
- Figure 8. Simulation results of the melt flow for Case 3: (A) 45% filling; (B) 60% filling.
- Figure 9. Simulation results of the solidification for case 3.
- Figure 10. Expected shrinkage defect area for Case 3 at 65% solidification.
- Figure 11. Simulation results with the final casting layout: (A) Fixed side; (B) Moving side.
7. Conclusion:
Summary of Key Findings:
The study concludes that CAE simulation is effective in optimizing casting layouts for HPDC processes. Flow analysis identified and resolved issues of imbalanced flow, air porosity, and backflow through iterative design modifications of the gating system. Case 3, featuring a ring gate and a modified biscuit design, demonstrated the most uniform melt flow and minimized backflow and air porosity compared to Case 1 and Case 2. Solidification analysis for Case 3 revealed potential shrinkage defects in thick sections, highlighting the need for optimized cooling strategies.
Academic Significance of the Study:
This research demonstrates the practical application of CAE simulation in die casting layout design, validating its capability to predict and mitigate potential casting defects. It contributes to the body of knowledge by showcasing a systematic approach to optimize gating systems for complex geometries using numerical analysis, moving away from purely experience-based design methods. The study reinforces the importance of integrating flow and solidification simulations in the design phase to achieve high-quality die-cast components.
Practical Implications:
The findings offer practical guidelines for die casting engineers in designing gating systems for household appliances and similar components. Utilizing CAE simulation tools like AnyCasting can significantly reduce the trial-and-error process in mold development, leading to faster design cycles and reduced production costs. The optimized casting layout (Case 3) provides a template for similar cooking grill designs, and the identified need for refined cooling strategies emphasizes the importance of comprehensive thermal management in die casting mold design.
Limitations of the Study and Areas for Future Research:
The study is limited to numerical simulation and does not include experimental validation of the simulation results. Future research should focus on conducting physical experiments to validate the predicted casting performance of Case 3 and to further refine the casting process parameters. Further investigation into optimized cooling channel designs and their integration with the casting layout is recommended to address the identified shrinkage defect areas and to achieve more uniform solidification. Additionally, exploring the impact of process parameter variations on casting quality using CAE simulation would be a valuable extension of this research.
8. References:
- [1] Hu, B.; Tong, K.; Niu, X.; Pinwill, I. Design and optimisation of runner and gating systems for the die casting of thin-walled magnesium telecommunication parts through numerical simulation. J. Mater. Process. Technol. 2000, 105, 128-133. [CrossRef]
- [2] Park, J.-Y.; Kim, E.-S.; Park, Y.-H.; Park, I.-M. Optimization of Casting design for automobile transmission gear housing by 3D filling and solidification simulation in local squeeze diecasting process. Korean J. Mater. Res. 2006, 16, 668-675. [CrossRef]
- [3] Kim, E.; Park, J.; Jeon, E.; Park, I. Current state and technology trend of domestic diecasting industry for automotive parts. J. Korea Foundry Soc. 2007, 27, 13–19.
- [4] Jeong, B.-G.; Kwon, H.-K. A case study on developing automotive part (housing) by filling and solidification analysis. J. Soc. Korea Ind. Syst. Eng. 2015, 38, 44-51. [CrossRef]
- [5] Cho, G.-S.; Choe, K.-H. Study on the rationalization of aluminium casting alloys for automobiles components. J. Korea Foundry Soc. 2011, 31, 319-325. [CrossRef]
- [6] Jeong, W.; Yoon, H.; Hong, S.; Park, I. Optimal gating system design of escalator step die casting part by using Taguchi method. J. Korea Foundry Soc. 2000, 20, 97-103.
- [7] Fu, M.; Yong, M. Simulation-enabled casting product defect prediction in die casting process. Int. J. Prod. Res. 2009, 47, 5203-5216. [CrossRef]
- [8] Jeon, E.; Park, J.; Park, I. Application trend of aluminum castings in automotive component. J. Korea Foundry Soc. 2007, 27, 20-23.
- [9] Lee, D.; Kang, C.; Lee, S. Prediction defect of automotive components by filling and solidification analysis. J. Korea Foundry Soc. 2000, 20, 159-166.
- [10] Kim, Y.; Choi, S.; Cho, J.; Jeong, C.; Kang, C. Optimization of thin-walled aluminum die casting design by solidification simulation. J. Korea Foundry Soc. 2008, 28, 190–194.
- [11] Jin, C.-K.; Kang, C.-G. Fabrication process of aluminum bipolar plate for fuel cell using vacuum die casting. J. Korea Foundry Soc. 2011, 31, 71-78. [CrossRef]
- [12] Gramegna, N.; Della Corte, E.; Poles, S. Manufacturing process simulation for product design chain optimization. Mater. Manuf. Process. 2011, 26, 527-533. [CrossRef]
- [13] Park, J.; Kim, E.; Park, I. Die casting process design of automobile gear housing by metal flow and solidification simulation. J. Korea Foundry Soc. 2004, 24, 347-355.
- [14] Zhang, L.; Li, L.; Zhu, B. Simulation study on the LPDC process for thin-walled aluminum alloy casting. Mater. Manuf. Process. 2009, 24, 1349-1353. [CrossRef]
- [15] Wu, S.; Fuh, J.; Lee, K. Semi-automated parametric design of gating systems for die-casting die. Comput. Ind. Eng. 2007, 53, 222-232. [CrossRef]
- [16] AnyCasting. User Manual Version 6.5; AnyCasting Software: Seoul, Korea, 2019; pp. 55-62.
- [17] Kwon, H.; Kwon, H. Computer aided engineering (CAE) simulation for the design optimization of gate system on high pressure die casting (HPDC) process. Robot. Comput. Integr. Manuf. 2019, 55, 147–153. [CrossRef]
- [18] Kim, T.G.; Choi, J.K.; Hong, J.P.; Lee, Z.H. Reduction of computing time through FDM using implicit method and latent heat treatment in solidification analysis. J. Korea Foundry Soc. 1993, 13, 323-332.
- [19] Xun, S.; Junqing, W.; Hwang, H.Y.; Choi, J.K. Numerical simulation of mold filling process of castings by using of predictor-two step Corrector-VOF. J. Korea Foundry Soc. 2002, 22, 299-303.
- [20] Lee, Y.C.; Choi, J.K.; Hong, C.P. Development of an Integrated Simulation System and its Application to Casting Design. J. Korea Foundry Soc. 1997, 17, 552–559.
- [21] Kwon, H.Y.; Yoon, T.H.; Lee, B.J. Computer simulation on the High-Pressure Die Casting (HDPC) process by filling and solidification analysis. Int. J. Appl. Eng. Res. 2015, 10, 142–145. [CrossRef]
- [22] Jin, C.-K.; Jang, C.-H.; Kang, C.-G. Vacuum die casting mold design of fuel cell bipolar plate using die filling simulation and experimental verification. J. Korea Foundry Soc. 2012, 32, 65–74. [CrossRef]
- [23] Hosseini, S.M.; Utlu, Z. Design optimization of clutch housing mold by fluid flow and solidification simulation. J. Mech. Sci. Technol. 2016, 30, 2731-2742. [CrossRef]
9. Copyright:
- This material is "Hong-Kyu Kwon"'s paper: Based on "Layout Design and Die Casting Using CAE Simulation for Household Appliances".
- Paper Source: https://doi.org/10.3390/app112110128
This material was summarized based on the above paper, and unauthorized use for commercial purposes is prohibited.
Copyright © 2025 CASTMAN. All rights reserved.