This article introduces the paper ['Simplified models for high pressure die casting simulation'] presented at the ['Procedia Engineering, The Manufacturing Engineering Society International Conference, MESIC 2015']
1. Overview:
- Title: Simplified models for high pressure die casting simulation
- Author: E. Anglada, A. Meléndez, I. Vicario, E. Arratibel, G. Cangas
- Publication Year: 2015
- Publishing Journal/Academic Society: Procedia Engineering, The Manufacturing Engineering Society International Conference, MESIC 2015
- Keywords: finite elements; numerical simulation; heat transfer; HPDC; metal casting
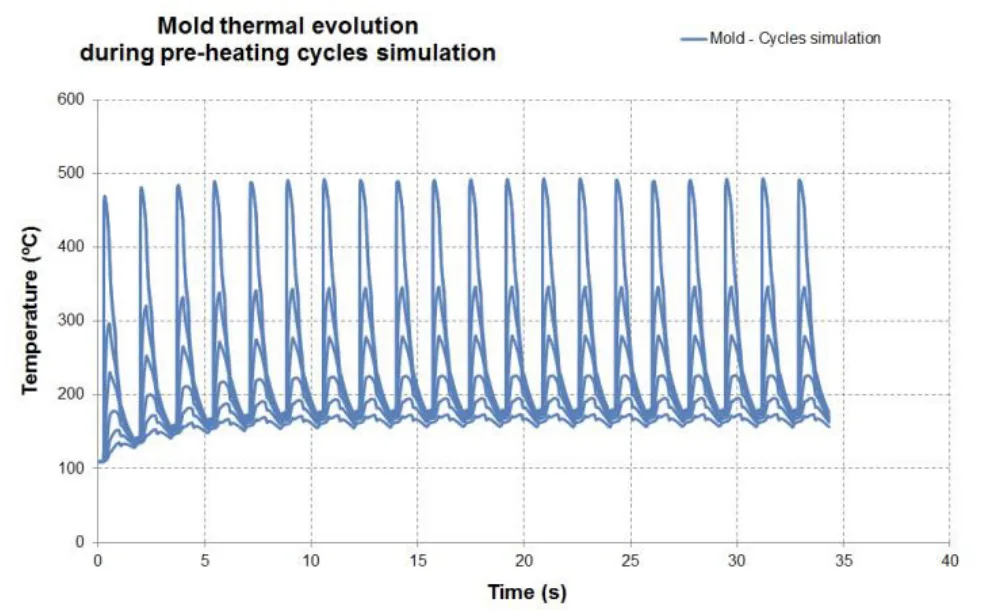
2. Research Background:
Background of the Research Topic:
The numerical simulation of metal casting processes is inherently complex. High Pressure Die Casting (HPDC) simulation presents additional challenges due to the cyclical nature of the industrial process, intricate part geometries, and high alloy injection velocities. These factors collectively contribute to extended calculation times, potentially spanning several days for complex simulations.
Status of Existing Research:
Numerical simulation is a widely adopted tool in the metal casting industry. While detailed models are crucial for accurate process prediction, situations arise where rapid solutions are necessary, even at the cost of some accuracy. This need for speed is particularly relevant during initial offer phases, quick evaluations of design alternatives, and notably, during the iterative adjustment process of simulation models.
Necessity of the Research:
Balancing accuracy and computational efficiency is paramount in HPDC simulation. The iterative nature of simulation model adjustment, which involves repeated simulations to correlate with experimental data, can become prohibitively time-consuming with detailed models. Therefore, exploring and validating simplified models that offer faster computation times without unacceptable loss of accuracy is essential for practical applications, especially in model adjustment workflows.
3. Research Purpose and Research Questions:
Research Purpose:
This research aims to investigate and discuss various methodologies for simplifying HPDC simulation models. The study evaluates the benefits and drawbacks of these simplifications, focusing on the trade-off between computational speed and accuracy in predicting the thermal behavior of the mold and casting.
Key Research:
The core research questions addressed in this paper are:
- How do simplifications related to the inclusion of pre-heating cycles affect the accuracy and calculation time of HPDC simulations?
- What is the impact of using thermal-only analysis versus coupled thermal and flow analysis on simulation results and computational efficiency?
- To what extent can geometrical simplifications, specifically using pseudo-2D models, reduce calculation times, and what is the associated loss of accuracy?
Research Hypotheses:
The central hypothesis is that simplified HPDC simulation models can significantly reduce calculation times while maintaining a reasonable level of accuracy, particularly for predicting thermal behavior. The study explores specific simplification techniques to validate this hypothesis and quantify the trade-offs involved.
4. Research Methodology
Research Design:
The research employs a comparative methodology. The accuracy of simplified models is evaluated by comparing their simulation results against those obtained from a detailed 3D simulation model. This detailed model, serving as the reference, was previously validated against experimental results in prior work.
Data Collection Method:
Data is collected through numerical simulations performed using the commercial finite element software ProCAST. The software is utilized to simulate HPDC processes, incorporating computational fluid dynamics (CFD) coupled with heat transfer analysis. The primary data collected are temperature profiles at specific points within the mold and the cast part during the simulation.
Analysis Method:
The analysis focuses on comparing temperature results and calculation times across different simulation scenarios. These scenarios include:
- Detailed 3D model with and without pre-heating cycles.
- Detailed 3D model using thermal-only analysis versus coupled thermal and flow analysis.
- Pseudo-2D model compared to the detailed 3D model.
The accuracy of simplified models is assessed by quantifying the deviation of their temperature predictions from the detailed 3D model results. Calculation times are directly compared to evaluate the computational efficiency gains achieved through simplification.
Research Subjects and Scope:
The research focuses on the HPDC process using a prototype mold with a simple cylindrical cavity (Ø50 mm and 250 mm length). The injected alloy is AlSi9Cu3, a common aluminum die casting alloy, and the mold material is H13 steel. The simplifications investigated are:
- Pre-heating cycles: Simulating with and without pre-heating cycles to reach thermal stabilization.
- Analysis type: Comparing thermal-only analysis to coupled thermal and flow analysis.
- Geometrical simplification: Utilizing a pseudo-2D model representing a slice of the 3D mold.
5. Main Research Results:
Key Research Results:
- Pre-heating Cycles Simulation: Including pre-heating cycles in the simulation is crucial for accurately estimating the average mold temperature. While omitting pre-heating cycles and estimating an average initial mold temperature is possible, it may introduce inaccuracies, especially if the initial temperature estimation is not precise. The temperature results obtained with and without pre-heating cycles are shown in Fig. 2.
- Thermal and Flow vs. Only Thermal Analysis: Restricting the simulation to thermal-only analysis significantly reduces calculation time. For a single cycle detailed model, the calculation time decreases from 6.9 hours for thermal and flow analysis to 0.3 hours for thermal-only analysis. As shown in Fig. 4, temperature results from thermal-only analysis are comparable to those from thermal and flow analysis, indicating that thermal-only analysis is a viable simplification when the primary interest is thermal behavior, such as in pre-heating cycle simulations.
- Geometrical Simplifications (Pseudo-2D Model): Employing a pseudo-2D model drastically reduces calculation times. For 20 cycles of heat transfer simulation, the calculation time decreases from 425 minutes for the detailed 3D model to 43 minutes for the pseudo-2D model (Table 3). However, as depicted in Fig. 6, the pseudo-2D model exhibits a more pronounced loss of accuracy compared to the other simplification methods.
Data Interpretation:
- Figure 1 illustrates the mold thermal evolution during pre-heating cycles simulation, showing the temperature increase over consecutive cycles until stabilization.
- Figure 2 compares temperature results with and without pre-heating cycles, demonstrating a low loss of accuracy when pre-heating cycles are omitted but with a carefully estimated initial mold temperature.
- Figure 3 shows the impact of varying initial mold temperatures on simulation results, highlighting the sensitivity to accurate initial temperature estimation when pre-heating cycles are not simulated.
- Figure 4 compares temperature results for thermal-only versus thermal and flow analysis, indicating good agreement and the efficiency of thermal-only analysis for thermal behavior prediction.
- Figure 5 depicts the detailed HPDC mold and the section used for the pseudo-2D model, along with the mesh of the pseudo-2D model.
- Figure 6 compares temperature results between the detailed 3D model and the pseudo-2D model after 20 cycles, showing a noticeable deviation in temperature prediction with the pseudo-2D model.
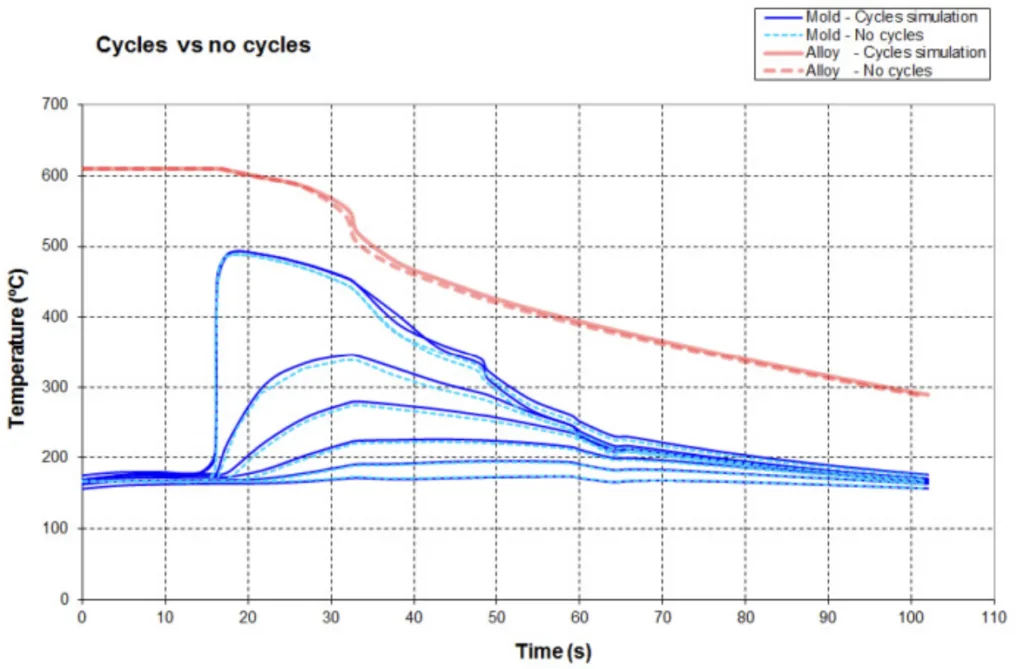
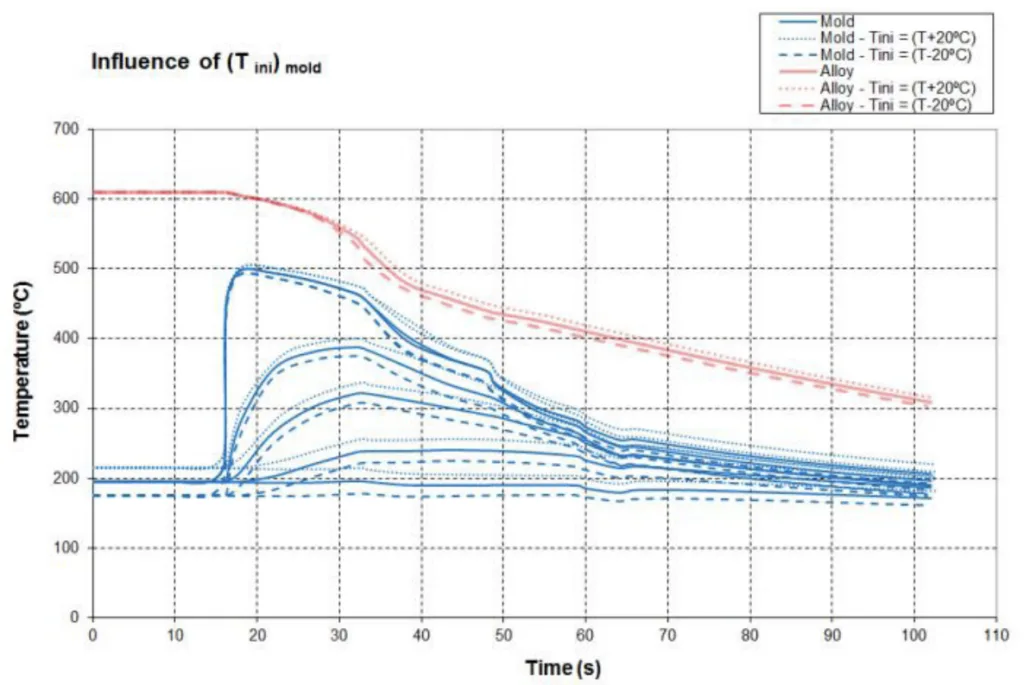
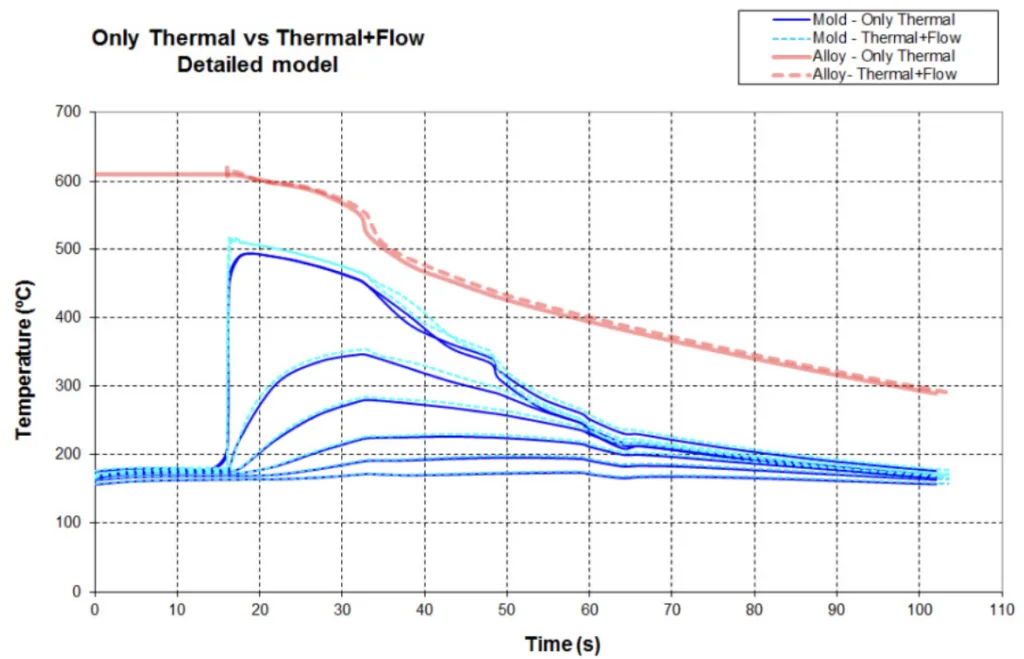
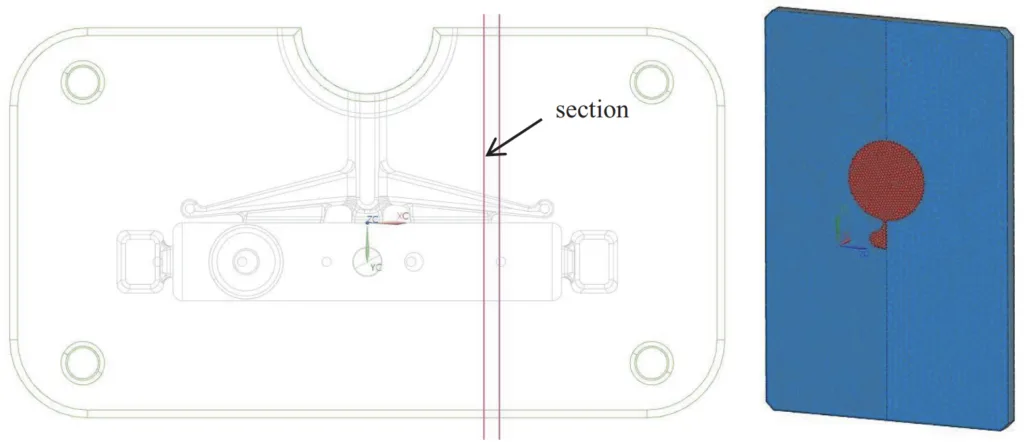
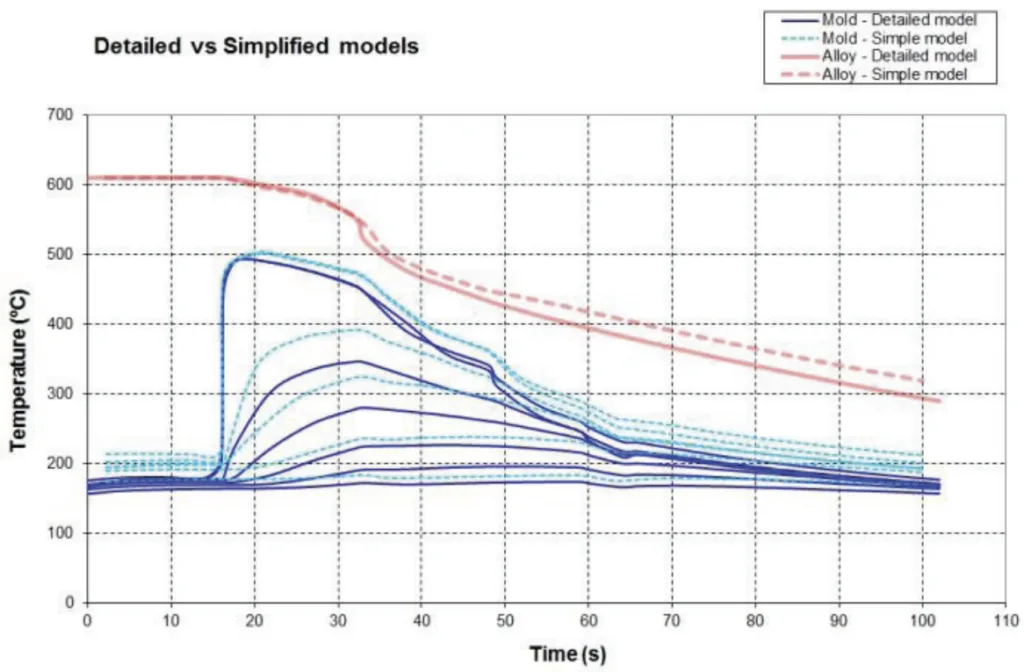
Figure Name List:
- Fig. 1. Mold thermal evolution during pre-heating cycles simulation
- Fig. 2. Temperature results including or not the pre-heating cycles in simulation
- Fig. 3. Temperature results for different initial mold temperatures
- Fig. 4. Detailed model. Temperature results for only thermal vs thermal and flow.
- Fig. 5. Drawing of the HPDC mold and the section selected for the pseudo-2D model (left). Mesh corresponding to the pseudo-2D model (right)
- Fig. 6. Detailed vs pseudo-2D model temperature results (after 20 cycles)
6. Conclusion:
Summary of Main Results:
The study demonstrates that simplified simulation models can effectively reproduce the thermal behavior of the HPDC mold and casting, achieving significant reductions in calculation times. Key findings include: the importance of including pre-heating cycles for accurate average mold temperature estimation; the efficiency of thermal-only analysis for thermal behavior prediction; and the substantial time savings offered by pseudo-2D models, albeit with a greater compromise in accuracy.
Academic Significance of the Research:
This research contributes to the understanding of computational trade-offs in HPDC simulation. It systematically evaluates the impact of different simplification strategies on accuracy and computational cost, providing valuable insights for researchers and engineers working in the field of metal casting simulation.
Practical Implications:
The findings offer practical guidelines for selecting appropriate simplification strategies in HPDC simulation based on specific objectives and constraints. For scenarios prioritizing computational speed, particularly in iterative processes like model adjustment, simplified models offer viable alternatives. The study suggests a pragmatic two-step approach: initially simulating pre-heating cycles using thermal-only analysis to establish mold thermal distribution, followed by a thermal and flow analysis of the injection process using the obtained mold temperature distribution as the initial condition. For cases with stringent time restrictions and acceptable accuracy trade-offs, pseudo-2D models can be considered.
Limitations of the Research
The accuracy loss associated with pseudo-2D models may be unacceptable in applications demanding high precision. Furthermore, the study is based on a relatively simple cylindrical cavity geometry. The applicability and effectiveness of these simplification strategies for more complex industrial part geometries warrant further investigation.
7. Future Follow-up Research:
- Directions for Follow-up Research
Future research should focus on validating these simplification methodologies with more complex part geometries and in real industrial case studies. This will help to further assess the robustness and general applicability of the proposed simplified models. - Areas Requiring Further Exploration
Further exploration is needed to optimize the application of these simplification strategies for specific HPDC applications and accuracy requirements. Investigating adaptive simplification techniques, which dynamically adjust the level of simplification based on the simulation phase or region of interest, could also be a valuable direction.
8. References:
- [1] F. Bonollo, S. Odorizzi, P. Hansen, D.M. Lipinski, M. Schneider, I. Erauskin, I.L. Svensson, M. Wessen, E. Hepp, N. Gramegna. Numerical simulation of Foundry Processes. Padova (Italy): SGE; 2001.
- [2] C. Hirsch. Numerical computation of internal and external flows. Salisbury (UK): John Wiley and Sons; 1997.
- [3] A.J. Chapman. Transmisión del calor. Madrid (Spain): Libreria Editorial Bellisco; 1984.
- [4] M. Schäfer. Computational engineering. Berlin (Germany): Springer; 2006.
- [5] J.A. Dantzig, M. Rappaz. Solidification. Lausanne (Switzerland): CRC Press; 2009.
- [6] E. Anglada, A. Melendez, L. Maestro, I. Dominguez. Adjustment of Numerical Simulation Model to the Investment Casting Process. Procedia Eng. 2013; 63: 75-83. doi:10.1016/j.proeng.2013.08.272.
- [7] E. Anglada, A. Melendez, L. Maestro, I. Dominguez. Finite Element Model Correlation of an Investment Casting Process. Mater. Sci. Forum 2014; 797: 105-110. doi:10.4028/www.scientific.net/MSF.797.105.
- [8] Y. Dong, K. Bu, Y. Dou, D. Zhang. Determination of interfacial heat-transfer coefficient during investment-casting process of single-crystal blades. J. Mater. Process. Technol. 2011; 211: 2123-2131. doi:10.1016/j.jmatprotec.2011.07.012.
- [9] H. Jin, J. Li, D. Pan. Application of inverse method to estimation of boundary conditions during investment casting simulation. Acta Metall. Sin. Engl. 2009; 22: 429-434. doi:10.1016/S1006-7191(08)60119-2.
- [10] J.-M. Drezet, M. Rappaz, G.-U. Grün, M. Gremaud. Determination of thermophysical properties and boundary conditions of direct chill-cast aluminum alloys using inverse methods. Metall. Mater. Trans. A 2000; 31 A: 1627-1634. doi:10.1007/s11661-000-0172-5.
- [11] A. Long, D. Thornhill, C. Armstrong, D. Watson. Determination of the heat transfer coefficient at the metal-die interface for high pressure die cast AlSi9Cu3Fe. Appl. Therm. Eng. 2011; 31: 3996-4006. doi:10.1016/j.applthermaleng.2011.07.052.
- [12] G.-X. Wang, E.F. Mathys. Experimental determination of the interfacial heat transfer during cooling and solidification of molten metal droplets impacting on a metallic substrate: effect of roughness and superheat. Int. J. Heat Mass Transfer. 2002; 45: 4967-4981. doi:10.1016/S0017-9310(02)00199-0.
- [13] E. Anglada, A. Meléndez, I. Vicario, E. Arratibel, I. Aguillo. Adjustment of a high pressure die casting simulation model against experimental data. In: M.A. Rosendo, G. Puig, I. Buj Corral, J. Minguella Canela, editors, The 6th Manufacturing Engineering Society International Conference, MESIC 2015. Procedia Eng. In press.
9. Copyright:
- This material is "E. Anglada et al."'s paper: Based on "Simplified models for high pressure die casting simulation".
- Paper Source: doi:10.1016/j.proeng.2015.12.585
This material was summarized based on the above paper, and unauthorized use for commercial purposes is prohibited.
Copyright © 2025 CASTMAN. All rights reserved.