This article introduces the paper "Studies on performance and process improvement of implementing novel vacuum process for new age castings" presented at the Materials Today: Proceedings
1. Overview:
- Title: Studies on performance and process improvement of implementing novel vacuum process for new age castings
- Authors: J. Senthil, M. Prabhahar, C. Thiagarajan, S. Prakash, Ramalingam Lakshmanan
- Publication Year: July 2020
- Publishing Journal/Academic Society: Materials Today: Proceedings
- Keywords: V-process, Casting process, L-type junctions, Foundry practices, Stereo lithography
2. Research Background:
- Social/Academic Context of the Research Topic: The modern nonferrous casting industry is continuously evolving, seeking processes that enhance product aesthetics and reduce manufacturing costs. Sand casting and gravity die casting are widely used, but often suffer from issues like poor surface finish and environmental concerns. Investment casting offers better quality but is economically challenging for broad industrial adoption due to high development and operating costs.
- Limitations of Existing Research: Conventional casting methods like sand casting and die casting have inherent drawbacks, particularly in achieving good surface finish and dimensional accuracy. These methods often require significant post-processing, such as fettling and machining, increasing production time and cost. There was a need for processes that could improve aesthetics and provide value-added features in castings beyond the conventional methods.
- Necessity of the Research: Industries require casting processes that offer improved aesthetics, dimensional accuracy, reduced porosity, minimized machining, and environmental friendliness, all while being economically viable. The V-process (Vacuum process) emerged as a potential solution observed in some foundries to address these needs, offering excellent yield and near net shape finish, thereby reducing machining costs and promoting environmental sustainability.
3. Research Purpose and Research Questions:
- Research Purpose: The research aims to investigate and highlight the performance and process improvements achieved by implementing the V-process for producing new age castings. It focuses on demonstrating how the V-process can overcome the limitations of conventional casting methods and provide a more efficient and effective alternative.
- Key Research Questions:
- How does the V-process address the drawbacks of conventional casting methods like sand casting and die casting in terms of surface finish and dimensional accuracy?
- What are the specific advantages of the V-process in terms of operational cost, surface finish, machining, yield, and reusability of materials compared to traditional methods?
- What are the key steps involved in the V-process implementation, and how do they contribute to the improved casting quality?
- Research Hypotheses: The paper implicitly hypothesizes that the V-process can provide superior casting quality with improved surface finish, dimensional accuracy, and reduced post-processing requirements compared to conventional sand casting and die casting methods, leading to overall process improvement and cost reduction.
4. Research Methodology:
- Research Design: This study appears to be an exploratory and descriptive study based on observations and implementation of the V-process in industrial settings. It involves a review of existing casting processes, an in-depth examination of the V-process, and a comparative analysis of its advantages. It also includes a pilot project implementation in industries.
- Data Collection Method: The information is gathered through:
- Detailed observation of various casting processes.
- Literature review on V-process and its practical implications.
- Expert opinions from foundries currently using the V-process.
- Pilot project implementation and observation in industries.
- Analysis Method: The analysis is primarily qualitative, focusing on describing the V-process, outlining its operational steps, and comparing its features and benefits against conventional casting methods based on industry observations and expert opinions. Quantitative data is presented in tables to compare tolerances and process parameters across different casting methods.
- Research Subjects and Scope: The research focuses on the application of the V-process for non-ferrous castings, specifically within the context of industries seeking improved casting quality and process efficiency. The scope includes examining the process parameters, advantages, and potential applications of the V-process as a modern foundry methodology.
5. Main Research Results:
- Key Research Results: The study highlights that the V-process offers several advantages over conventional methods:
- Improved Surface Finish: V-process achieves a surface finish of "125-150 RMS," which is significantly better than sand casting ("250-500 RMS") and comparable to plaster mold and investment casting.
- Dimensional Accuracy: V-process provides tighter tolerances compared to sand casting and permanent mold casting (See Table 1). For example, for a 3-inch casting, V-process tolerance is "±0.014 in." compared to "±0.030 in." for sand casting.
- Reduced Machining: The near net shape capability of the V-process reduces the need for extensive machining, saving time and material. "Trial conducted at the plant on Housing of weight 6 kg indicated that the aesthetics improvement was seen and a significant machining time of about 30% was saved."
- Higher Yield: V-process can achieve a "Higher yield, from existing 65% to 77%."
- Re-usable Sand: The dry sand used in the V-process is re-usable, reducing material waste and environmental impact.
- Zero Draft: V-process allows for zero degree draft angles, providing design flexibility and reducing material usage. "when comparing with sand casting and die casting the draft requirement in V-process is zero".
- Time Efficiency: The "timing required for the V process is 2 to 4 h which is the least of all the process" compared to some other methods.
- Statistical/Qualitative Analysis Results:
- Table 1 provides a comparison of tolerances and surface finish for V-Process, Sand Cast, Permanent Mold, Plaster Mold, Die Cast, and Investment Cast methods across different casting sizes (3 in., 6 in., 12 in., 24 in.).
- Table 2 compares tolerances and process parameters such as size range, minimum section thickness, draft, surface finish, tooling lead time, and applicable metals for Aluminum Die Casting, Sand Casting, V-Casting, and Investment Casting.
- Table 3 offers a comparative summary of Casting Process Comparisons, detailing typical size range, tolerances, surface finish, minimum draft, minimum section thickness, typical order quantities, and tooling costs for V-PROCESS Castings, Sand Castings, Investment (Lost Wax) Castings, and Die Castings.
- Data Interpretation: The data presented in tables and the observations from industrial implementation consistently indicate that the V-process offers a superior balance of casting quality, dimensional accuracy, surface finish, and cost-effectiveness compared to traditional sand casting and die casting. While investment casting and die casting may offer tighter tolerances in some aspects, the V-process provides a competitive alternative with advantages in specific areas like draft requirements, surface finish compared to sand casting, and cost compared to investment casting.
- Figure Name List:
- Fig. 1. Handle for X-Ray machine made out of V Process.
- Fig. 2. V-process sequence.
- Fig. 3. Step1: Hollow Pattern Carrier.
- Fig. 4. Step2: Heating of Plastic Film.
- Fig. 5. Step 3: Pattern covered with thin sheet.
- Fig. 6. Step 4: Flask Arrangement.
- Fig. 7. Step 5: Dry Sand Filling.
- Fig. 8. Step 6: Application of Vacuum.
- Fig. 9. Step 7: Removal of Flask.
- Fig. 10. Step 8: Cope and Drag Arrangement.
- Fig. 11. Step 9: Pouring of Molten metal.
- Fig. 12. Step 10: Solidification.
- Fig. 13. Final Component.
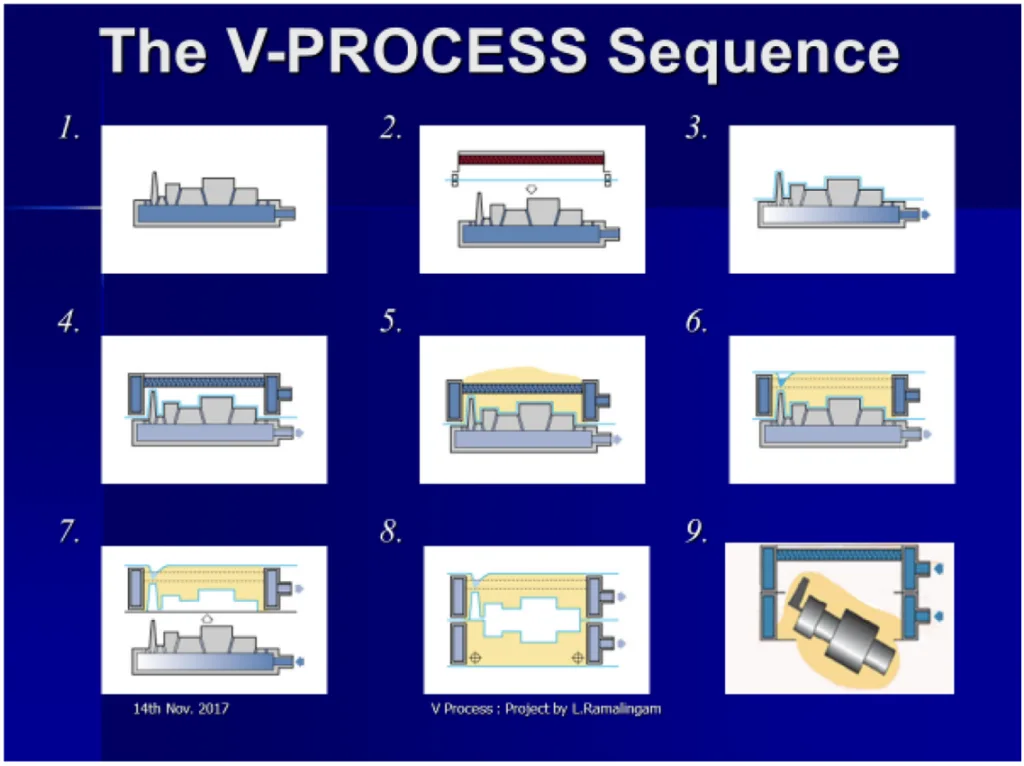
6. Conclusion and Discussion:
- Summary of Main Results: The study concludes that the V-process is a viable and advantageous casting method, particularly for achieving near net shape castings with improved surface finish, dimensional accuracy, and reduced machining requirements. It offers a cleaner, more environmentally friendly process with re-usable sand and potential for higher yield compared to conventional sand casting. The industrial trial demonstrated a significant reduction in machining time and aesthetic improvements.
- Academic Significance of the Research: This paper contributes to the existing body of knowledge by providing a detailed overview of the V-process and empirically highlighting its benefits in a practical industrial context. It underscores the potential of the V-process as a modern foundry methodology capable of addressing the evolving demands of the casting industry for higher quality and efficiency.
- Practical Implications: The findings have significant practical implications for the casting industry, particularly for manufacturers of non-ferrous castings. The V-process offers a pathway to:
- Reduce production costs through minimized machining and material waste.
- Improve casting quality and aesthetics, enhancing product value.
- Enhance environmental sustainability through re-usable sand and reduced waste.
- Achieve tighter tolerances and complex geometries, expanding design possibilities.
- Limitations of the Research: The study is limited by its primarily descriptive and observational nature. While it presents comparative data and industrial trial results, it lacks in-depth quantitative experimental validation across a wider range of casting parameters and alloy types. Further research with rigorous experimental designs would be beneficial to solidify these findings.
7. Future Follow-up Research:
- Directions for Follow-up Research: Future research should focus on:
- Conducting detailed experimental studies to quantify the performance benefits of the V-process across various alloy types, casting sizes, and complexities.
- Optimizing V-process parameters for specific applications and materials to further enhance casting quality and efficiency.
- Investigating the long-term economic and environmental benefits of V-process adoption in industrial settings.
- Exploring the application of V-process for a broader range of casting applications beyond those currently highlighted.
- Areas Requiring Further Exploration: Further exploration is needed in areas such as:
- Detailed cost-benefit analysis of V-process implementation compared to conventional methods.
- Material characterization and performance evaluation of V-process castings under various operating conditions.
- Integration of advanced technologies like simulation and automation into the V-process to further improve its efficiency and control.
8. References:
- [1] D.E. Walsh, Do It Yourself Vacuum Forming for the Hobbyist, Workshop Publishing, Lake Orion, MI, 2002.
- [2] M. Denoual, P. Mognol, B. Lepioufle, Vacuum casting, a new answer for manufacturing biomicrosystems, Proc. Inst. Mech. Eng., Part B: J. Eng. Manuf. 219 (9) (2005) 697-701, https://doi.org/10.1243/095440505X32571.
- [3] C.K. Jin, Chang Hyun Jang, Chung Gil Kang, Vacuum Die Casting Process and Simulation for Manufacturing 0.8 mm-Thick Aluminum Plate with Four Maze Shapes, Metals 5 (2015) 192-205, doi: 10.3390/met5010192.
- [4] Hu Bo, Xiong Shoumei, Masayuki Murakami, Yoshihide Matsumoto, Shingo Ikeda, Study on vacuum die casting process of aluminum alloys, https://www.researchgate.net/publication/287906872.
- [5] Hyung-Yoon Seo, Pan-Ki Seo, Chung-Gil Kang, A study on the S/W application for a riser design process for fabricating axisymmetric large offshore structures by using a sand casting process, Int. J. Naval Architecture Ocean Eng. 11 (2019) 462e473.
- [6] Santosh Reddy Sama, Tony Badamo, Paul Lynch, Guha Manogharan, Novel sprue designs in metal casting via 3D sand-printing, Addit. Manuf. 25 (2019) 563-578.
- [7] Isaac Nelson, Steven E. Naleway, Intrinsic and extrinsic control of freeze casting, J. Mater. Res. Technol. 8 (2) (2019) 2372-2385, https://doi.org/10.1016/j.jmrt.2018.11.011.
- [8] L. Krügera, E. Jentsch, L. Brunke, A. Keßler, G. Wolf, T. Lehnert, N. Schubert, Development of an innovative lightweight piston through process, Scientific Committee of ICAFT/SFU/AutoMetForm 2018, doi: 10.1016/j.promfg.2018.12.061.
- [9] Federica Fiorentinia, Pellegrino Curcio, Enrico Armentani, Carlo Rosso, Paolo Baldissera, Study of two alternative cooling systems of a mould insert used in die casting process of light alloy components, in: AIAS 2019 International conference on stress analysis Structural Integrity procedia 24 (2019) 569-582.
- [10] Markets and markets, January. Metal Casting Market: Global Forecast Until 2025, https://www.Markets and markets.com/Market-Reports/metal-casting-market-23885716.html (accessible on 2018).
9. Copyright:
- This material is J. Senthil, M. Prabhahar, C. Thiagarajan, S. Prakash, Ramalingam Lakshmanan's paper: Based on Studies on performance and process improvement of implementing novel vacuum process for new age castings.
- Paper Source: https://doi.org/10.1016/j.matpr.2020.06.269
This material was summarized based on the above paper, and unauthorized use for commercial purposes is prohibited.
Copyright © 2025 CASTMAN. All rights reserved.