This article introduces the paper "The DIRECTOOL Software – Tool Design on Facet Geometries with Decision Support" presented at the INTERNATIONAL CONFERENCE ON ENGINEERING DESIGN
1. Overview:
Title: THE DIRECTOOL SOFTWARE – TOOL DESIGN ON FACET GEOMETRIES WITH DECISION SUPPORT
Author: Dieter H. Müller, Claus Aumund-Kopp, Robert Weitzel, Axel Selk
Publication Year: 2003
Publishing Journal/Academic Society: INTERNATIONAL CONFERENCE ON ENGINEERING DESIGN (ICED 03 STOCKHOLM, AUGUST 19-21, 2003-02-11)
Keywords: Solid modelling, tool design, decision support, case based reasoning
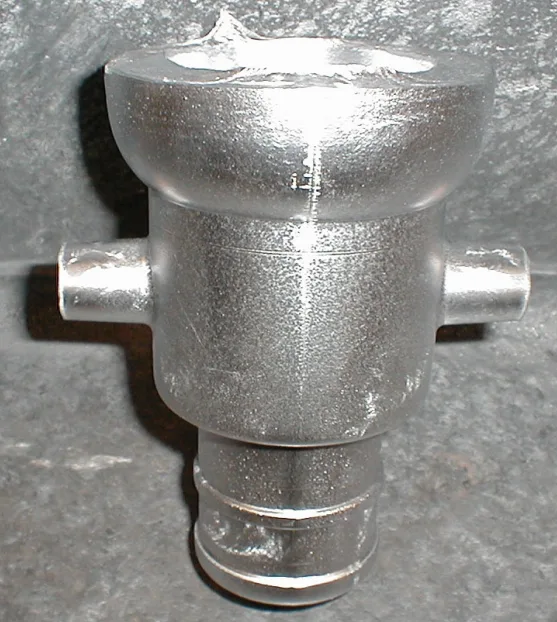
2. Research Background:
Social/Academic Context of the Research Topic:
The manufacture of dies and moulds is a significant part of the European economy. Small and medium-sized foundries need to maintain competitiveness in design and data management. Industrial practice in tooling design predominantly uses surface models within specialized CAD systems.
Limitations of Existing Research:
Current 3D CAD systems present several limitations:
- Data Exchange Issues: Inaccuracies occur during data format and interface transfer between customer and tool maker due to different CAD systems and the complexity of surface models. Model geometry is often transferred incompletely or with errors.
- Cost and Complexity: 3D CAD systems are expensive and overloaded with geometric design functionality, with companies using only a fraction of their capabilities.
- Lack of Process and Material Integration: CAD systems primarily focus on geometry manipulation, neglecting process and material data and knowledge crucial for tool design.
- Limited Comprehensive Tooling Coverage: Tool making companies require comprehensive solutions covering all tooling-related aspects beyond just geometry.
Necessity of the Research:
There is a need for a robust, easy-to-use, and comprehensive software system for tool design that overcomes the limitations of existing CAD systems, especially for small and medium-sized foundries in the metal casting industry. This system should address data exchange problems, reduce costs, integrate process and material considerations, and provide decision support for tool designers.
3. Research Purpose and Research Questions:
Research Purpose:
The paper describes the development and validation of a robust, easy-in-use and comprehensive software system for tool design, named DIRECTOOL. This software aims to improve tool design by using triangulated facet data (STL format) instead of complex mathematical surface descriptions and by incorporating decision support components. The focus is on metal casting applications.
Key Research Questions:
The paper implicitly addresses the following research questions:
- How can triangulated facet data (STL) be effectively used for solid modelling in tool design to overcome the limitations of surface models in CAD systems?
- How can decision support components be integrated into a tool design software to assist tool designers in making informed decisions related to process, material, and reference designs?
- How can Case Based Reasoning (CBR) be applied to retrieve and adapt existing tool designs to support new design tasks in metal casting?
- How can a software system be developed to provide a comprehensive tool design solution, including geometric description, decision protocols, and efficient data management?
Research Hypotheses:
The research operates under the hypothesis that:
- Using triangulated facet data (STL) for tool design offers advantages over surface models in terms of data exchange robustness, error repair, and development of flexible design tools.
- Integrating decision support, particularly Case Based Reasoning, into tool design software can significantly improve the efficiency and quality of the design process by providing reference solutions and guiding design decisions based on process and material considerations.
4. Research Methodology
Research Design:
The research follows a development and validation approach. It involves the development of the DIRECTOOL software system and its validation through a case study. The development is based on addressing the identified limitations of existing CAD systems and incorporating features like facet geometry modelling, decision support, and CBR.
Data Collection Method:
The paper does not explicitly detail traditional data collection. However, the research is informed by:
- Analysis of Industry Needs: Understanding the problems faced by tool making companies, particularly small and medium-sized foundries, regarding CAD system limitations and tooling design challenges.
- Analysis of Existing Tool Designs: Analyzing a large variety of tool designs for sand casting and gravity die casting to identify relevant tooling characteristics and develop a reference model for CBR.
- Software Development and Implementation: Building the DIRECTOOL software incorporating the proposed features and functionalities.
- Case Study Validation: Testing the developed software with a real-world tool design task (female coupling for fire fighting equipment) to demonstrate its functionality and benefits.
Analysis Method:
- Case Based Reasoning (CBR): Applied to determine and retrieve best-match solutions from a database of previously solved tool designs. Similarity assessment is based on characteristic attributes of castings (geometry and material), using defined formulae (equations (1), (2), (3)) for similarity computation.
- Software Validation: Demonstrating the functionality of DIRECTOOL through a case study, showing its ability to guide the design process, provide reference solutions, generate design protocols, and handle facet geometry data efficiently.
Research Subjects and Scope:
- Research Subjects: The research focuses on tool designers in the metal casting industry, particularly those involved in sand casting and gravity die casting.
- Research Scope: The scope is limited to the development of a software system for tool design, specifically for metal casting applications. The DIRECTOOL software is designed for gravity die casting and sand casting patterns. The case study focuses on gravity die casting.
5. Main Research Results:
Key Research Results:
- Development of DIRECTOOL Software: A robust, easy-to-use, and comprehensive software system for tool design based on triangulated facet geometries (STL) has been developed.
- Facet Geometry Modelling: The software effectively utilizes STL format, enabling automatic detection of split lines and undercuts, and derivation of mould halves. This approach simplifies geometry handling and improves data exchange.
- Decision Support Integration: DIRECTOOL incorporates decision support components, including Case Based Reasoning, to assist tool designers in process and material considerations.
- Case Based Reasoning for Reference Solutions: CBR is successfully implemented to retrieve similar, previously solved tool designs, providing valuable reference solutions for new design tasks.
- VFX File Format: A new file format (VFX) was developed for efficient storage and handling of faceted geometries, achieving high compression ratios and fast read/write speeds, crucial for large and detailed models.
- Automated Mould Derivation: The software automates mould derivation processes, including split line determination and undercut detection.
- 10-Stage Design Process for Gravity Die Casting: A structured 10-stage design process for gravity die casting is integrated into the software, guiding the designer through all necessary steps (Figure 2).
- Design Protocol Generation: DIRECTOOL generates a protocol of all design decisions, providing comprehensive documentation beyond just the CAD geometry.
Statistical/Qualitative Analysis Results:
- VFX File Compression: Figure 3 demonstrates the compression capabilities of the VFX file format compared to STL. For Part 3 (1,172,878 triangles), VFX file size is significantly smaller than STL file size, showcasing efficient data compression.
- CBR Similarity Formulae: Equations (1), (2), and (3) are presented as the formulae used to calculate the degree of similarity between castings for CBR.
Data Interpretation:
- Benefits of Facet Data: Using facet data (STL) simplifies geometric representation, facilitates data exchange, and enables automation in mould derivation processes.
- Effectiveness of CBR: Case Based Reasoning proves to be a valuable approach for providing decision support in tool design by leveraging past design experiences and offering relevant reference solutions.
- Value of Design Protocol: Generating a design protocol enhances the comprehensiveness of tool design documentation, aiding in communication, reference, and potential failure analysis.
Figure Name List:
- Figure 1 Characteristic attributes for the casting case description
- Figure 2 Gravity die design: Schematic sequence of design decisions
- Figure 3 Compression capabilities of the new VFX file format compared to the existing STL standard
- Figure 4 Mould derivation: Split line and detection of undercuts
- Figure 5 New casting: Female coupling from Al-Si7Mg
- Figure 6 Interface of the design support component
- Figure 7 Summary of the case study
- Figure 8 A casting of the presented case study from Al-Si7Mg
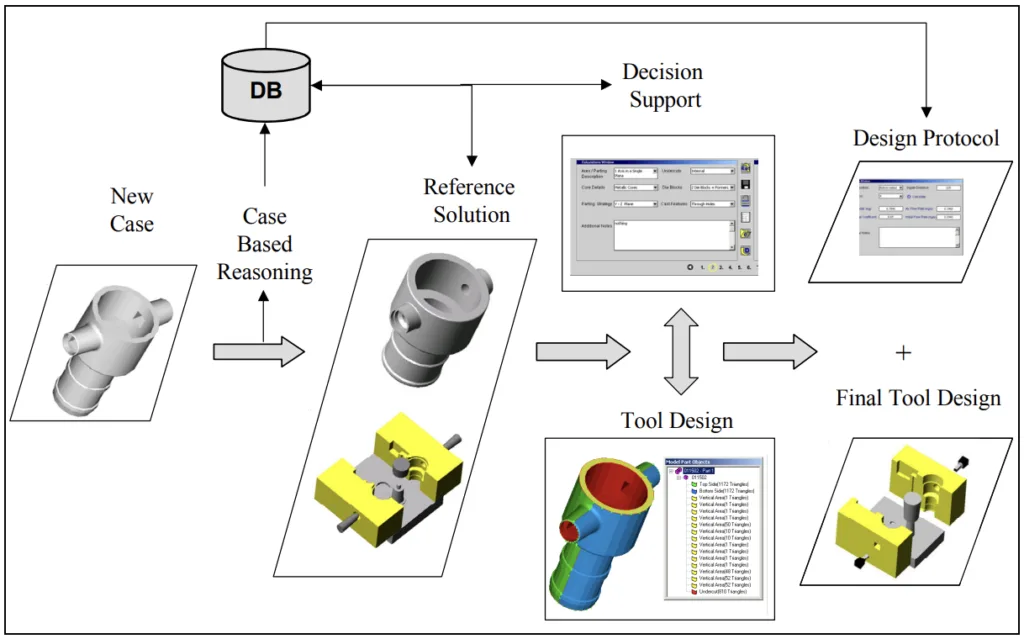
6. Conclusion and Discussion:
Summary of Main Results:
The DIRECTOOL project successfully developed a tool design system that operates on triangulated facet geometries, enabling automatic split line and undercut detection and mould half derivation. It integrates decision support for material and process considerations through Case Based Reasoning, allowing designers to retrieve and adapt solutions from previous designs. The system uses a 10-stage framework for gravity die design and generates a comprehensive design protocol.
Academic Significance of the Research:
This research demonstrates the effectiveness of using facet geometry and Case Based Reasoning in tool design software. It contributes to the field by providing a novel approach to overcome limitations of traditional CAD systems in tool design, particularly by integrating decision support and simplifying geometry handling.
Practical Implications:
- Improved Efficiency: DIRECTOOL offers a more efficient tool design process through automation, decision support, and reference solutions.
- Enhanced Data Exchange: Using STL format improves data exchange robustness and reduces errors.
- Comprehensive Documentation: The generated design protocol provides valuable documentation for communication, reference, and failure analysis.
- Cost Reduction: By addressing limitations of expensive and complex CAD systems, DIRECTOOL can potentially reduce costs for tool making companies, especially SMEs.
- Knowledge Retention and Reuse: CBR facilitates the reuse of past design knowledge, improving consistency and quality.
Limitations of the Research:
The paper does not explicitly discuss limitations. However, potential limitations could include:
- Scope: The system's validation is primarily focused on gravity die casting and sand casting patterns. Further validation might be needed for other casting processes or tooling types.
- Database Dependency: The effectiveness of CBR relies on the quality and comprehensiveness of the case database. Initial implementation might require building a sufficiently large and representative database.
7. Future Follow-up Research:
Directions for Follow-up Research:
The paper does not explicitly detail future research directions. However, based on the presented work, potential follow-up research areas include:
- Expanding CBR Database: Developing a larger and more diverse database of case studies to enhance the effectiveness of the Case Based Reasoning component.
- Integration of More Advanced Simulation Tools: Integrating mould flow simulation and other advanced analysis tools directly within the DIRECTOOL environment.
- Extending to Other Casting Processes: Adapting and extending the DIRECTOOL system to support a wider range of casting processes beyond gravity die casting and sand casting.
- Further Validation and Industrial Application: Conducting more extensive validation in industrial settings to assess the system's performance and impact in real-world tool design scenarios.
- Usability and User Interface Enhancements: Continuously improving the user interface and usability of the DIRECTOOL software based on user feedback.
Areas Requiring Further Exploration:
- Refinement of Similarity Metrics: Further exploring and refining the similarity metrics used in CBR to improve the accuracy and relevance of retrieved reference solutions.
- Automated Adaptation of Reference Solutions: Investigating methods for automating the adaptation of retrieved reference solutions to new design requirements, further reducing manual design effort.
8. References:
[1] VDMA: “Statistik zur Situation des europäischen Werkzeug- und Formenbaus im globalen Umfeld“, Branchenstudie im Auftrag des VDMA, 2000
[2] Aamodt, A.; Plaza, E.: “Case-Based Reasoning: Foundational Issues, Methodological Variations and System Approaches”, AI Communications, Vol.7 No 1, 1994, pp.39-59.
[3] Leake, D.; Birnbaum, L.; Hammond, K.; Cameron, M.; Hao, Y.: “Integrating diverse information resources in a case-based design environment”, Engineering Applications of Artificial Intelligence, 12 (1999), pp. 705-716.
[4] Liao, T.W.; Zhang, Z.M.; Mount, C.R.: “A Case-Based Reasoning System for Identifying Failure Mechanisms”, Engineering Applications of Artificial Intelligence, 13 (2000), pp. 199-213.
9. Copyright:
*This material is Dieter H. Müller, Claus Aumund-Kopp, Robert Weitzel, Axel Selk's paper: Based on THE DIRECTOOL SOFTWARE – TOOL DESIGN ON FACET GEOMETRIES WITH DECISION SUPPORT.
*Paper Source: [No DOI URL provided in the paper, using contact URL: http://www.biba.uni-bremen.de]
This material was summarized based on the above paper, and unauthorized use for commercial purposes is prohibited.
Copyright © 2025 CASTMAN. All rights reserved.