D. T. Peters
Copper Development Association Inc. Hilton Head Island, SC
J. G. Cowie
Copper Development Association Inc. New York, NY E. F. Brush, Jr.
Copper Development Association Inc. Weston, MA
S. P. Midson
Copper Development Association Inc. Denver, CO
Presented by: North American Die Casitng Association
Abstract
Little use has been made of pressure die casting for the manufacture of copper or copper alloy parts due in large part to poor economics resulting from short die life in casting these high melting metals. A research program initiated in 1997 was driven by the promise of a signifi cant increase in the energy effi ciency of the induction motor by substituting high conductivity copper for aluminum in the rotor “squirrel cage” structure. Use of high temperature materials including tungsten-, molybdenum- and nickel-base alloys was examined in an extensive series of casting trials. The importance of operating dies at elevated temperatures to minimize the cyclic temperature gradient through the die that leads to heat checking and cracking has been demonstrated by both thermal modeling and experimentation. Shot-by-shot inducion melting of the copper charge has been implemented and is described. Performance of motors with die cast copper rotors is compared to that of the aluminum rotor. Preliminary work on the applicability of the hot high temperature die technology combined with semi-solid processing for copper alloy part production is presented.
Korea Abstract
구리 또는 구리 합금 부품의 제조를 위한 고압 다이 캐스팅은 거의 사용되지 않았는데, 그 이유는 이러한 고융점 금속을 주조할 때 다이 수명이 짧기 때문에 대부분 경제성이 좋지 않기 때문입니다.
1997년에 시작된 연구 프로그램은 회전자 "농구" 구조에서 알루미늄을 전도성이 높은 구리로 대체하여 유도 전동기의 에너지 효율을 크게 증가시키겠다는 약속에 의해 주도되었습니다. 텅스텐, 몰리브덴 및 니켈 기반 합금을 포함한 고온 재료의 사용은 광범위한 주조 시험에서 조사되었습니다.
열 검사 및 균열로 이어지는 다이를 통한 주기적인 온도 구배를 최소화하기 위해 고온에서 다이를 작동하는 것의 중요성은 열 모델링과 실험을 통해 입증되었습니다. 구리 전하의 샷별 유도 용융이 구현되어 설명됩니다.
다이캐스트 구리 로터가 있는 모터의 성능은 알루미늄 로터의 성능과 비교됩니다. 구리 합금 부품 생산을 위한 반고체 처리와 결합된 고온 고온 다이 기술의 적용 가능성에 대한 예비 작업이 제시됩니다.
Introduction
The work described in this paper on die casting of copper was driven by the objective of achieving a signifi cant increase in the electrical energy effi ciency of the induction motor by substituting copper for the aluminum in the squirrel cage structure of the motor rotor. This effi ciency increase is due in large part to the reduced I2R losses in the rotor because the electrical conductivity of copper is nearly 60 percent higher than that of aluminum. Motors with copper rotors are expected to show overall loss reductions of 15 percent to 20 percent compared to the aluminum counterpart rotor. Because of the proliferation of motors, a very signifi cant energy savings is possible. The U.S. Department of Energy1 reports that motors above 1/6 Hp use about 60 percent of all electricity generated in the United States and that medium power motors (1 to 125 Hp) use about 60 percent of electricity supplied to all motors. A 1 percent increase in motor electrical energy effi ciency would save 20 billion kW-hrs per year or $1.4 billion in electricity (at 7 cents per kW-hr) and 3.5 million barrels of oil in the U.S. These savings would be multiplied by about a factor of four on a worldwide basis. Although very large motors (>250 Hp) are equipped with copper rotors manufactured by expensive and time consuming fabrication procedures, pressure die casting is the only practical way to produce the huge numbers of integral horsepower motors used in our industrialized society. Figure 1 shows a typical rotor made up of a stack of iron laminations with the end rings of the rotor visible. An aluminum squirrel cage of a similar motor liberated from the rotor by dissolution of the iron in acid is also shown.
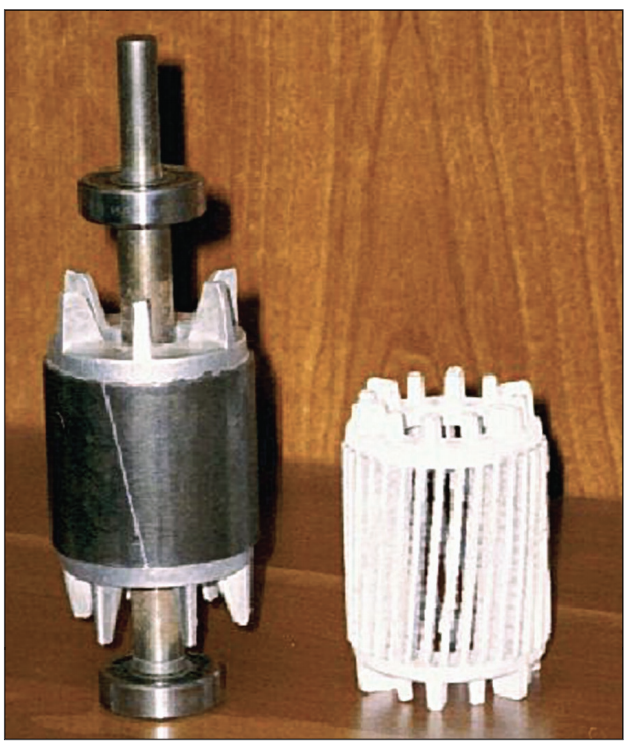
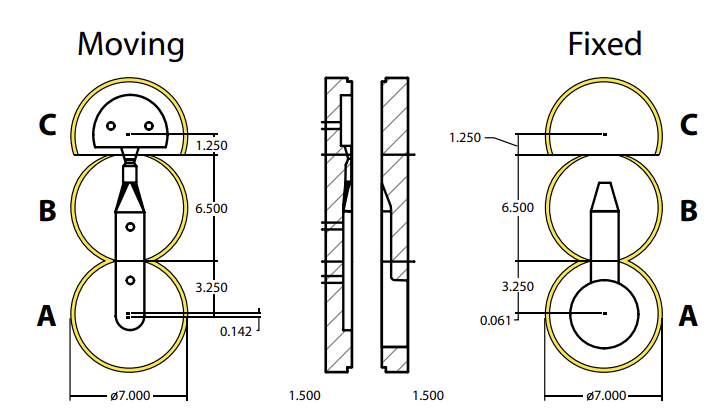
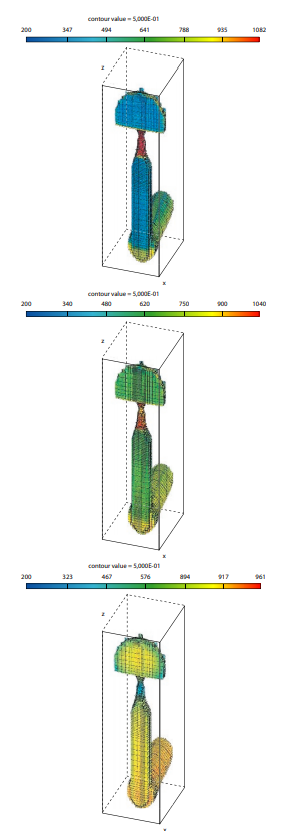
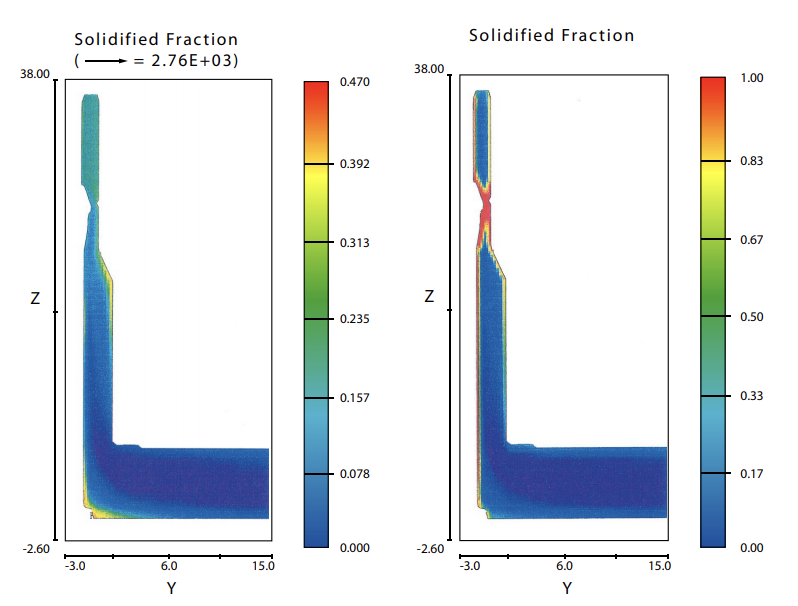
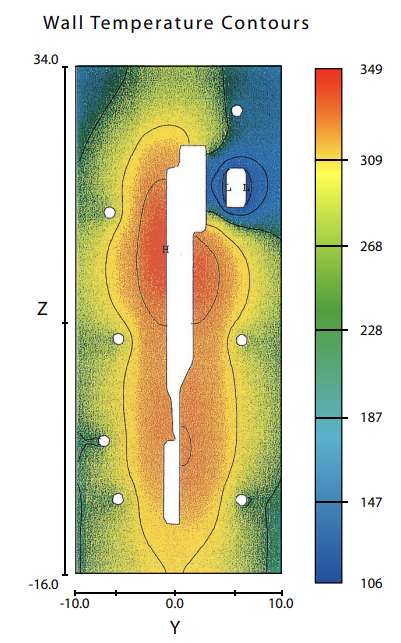
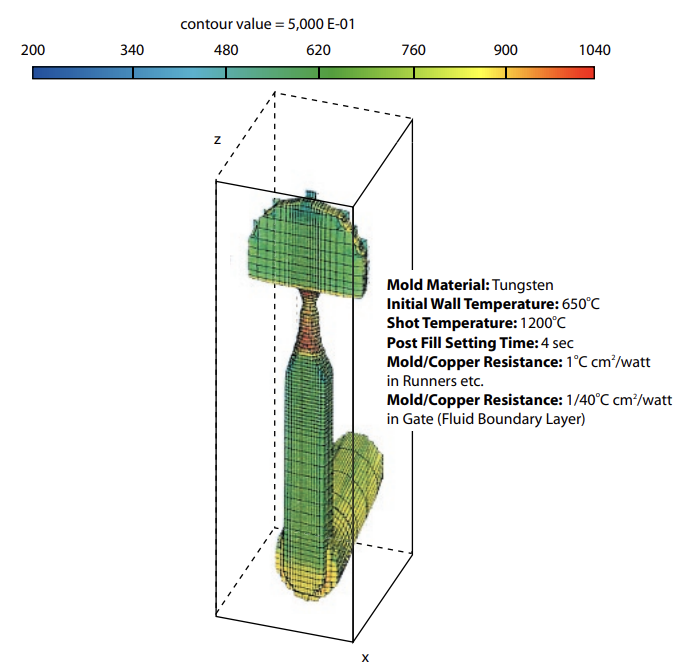
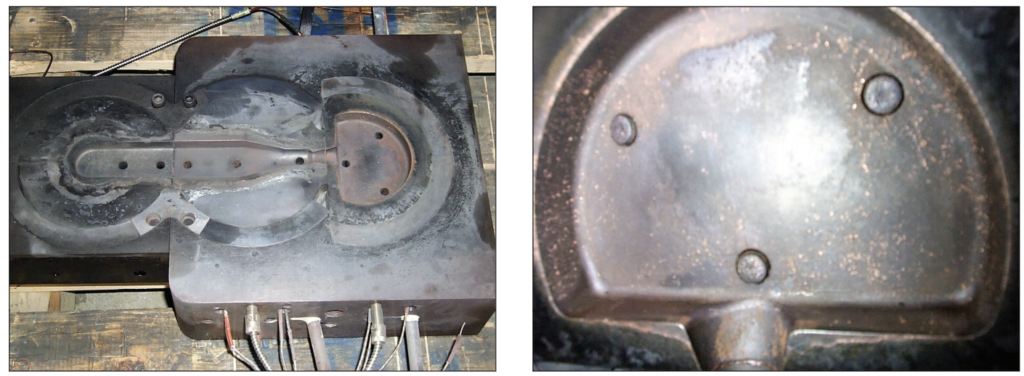
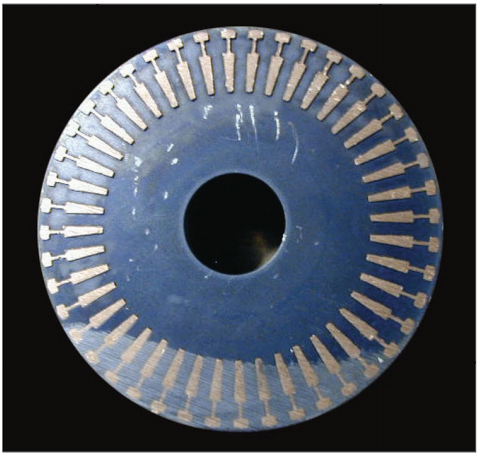
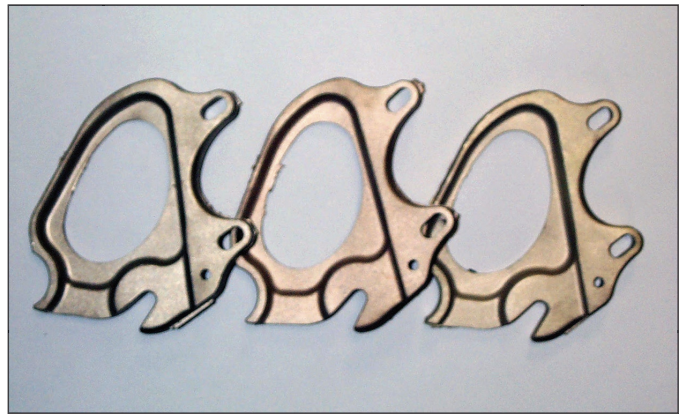
References
1) U.S. Department of Energy (1980), “Classifi cation and Evaluation of Electric Motors and Pumps,” DOE/CS-0147.
2) Benedyk, J.C., Moracz, D.J. and Wallace, J.F. (1970), “Thermal Fatigue Behavior of Die Materials for Aluminum Die Castings.” Trans. of SDCE, Paper No. 111.
3) Herman, E.A., Wallace, J.F. and Machonis, A.A. (1975), Copper Alloy Pressure Die Casting, p. 52, International Copper Research Association, New York, NY
4) Doehler, H.H. (1951), Die Casting, pp. 163-165, McGraw-Hill Book Co., Inc., New York, NY
5) Cowie, John G., Peters, Dale T., Brush, Edwin F. Jr. and Midson, Stephen P. (2001), “Materials and Modifi cations to Die Cast the Copper Conductors of the Induction Motor Rotor,” Die Casting
Engineer Engineer, The North American Die Casting Association, September, , The North American Die Casting Association, September, 38-47.
6) Peters, D. T., Cowie, J. G., Brush, E. F. Jr., and Midson, S. P. (2002), “Advances in Pressure Die Casting Electrical Grade Copper,” Proceedings of the American Foundry Association Casting Congress, Paper 02-002.
7) Rumburger, W.M. (1966), “Investigation of Materials for Use in Copper Alloy Die Casting Dies,” INCRA Project No. 59
8) Peters, D.T., Van Son, D.J., Cowie, J.G. and Brush, E.F., Jr. (2002), “Improved Motor Energy Effi ciency and Performance Through the Die-Cast Copper Rotor,” Proceedings of the International Conference on Electrical Machines 2002, August 25-28, Brugge, Belgium.