This technical summary is based on the academic paper "Aluminium Based Brazing Fillers for High Temperature Electronic Packaging Applications" published by Ashutosh Sharma and Jae-Pil Jung in J. Microelectron. Packag. Soc. (2015). It was analyzed and summarized for HPDC experts by CASTMAN experts with the help of LLM AI such as Gemini, ChatGPT, and Grok.
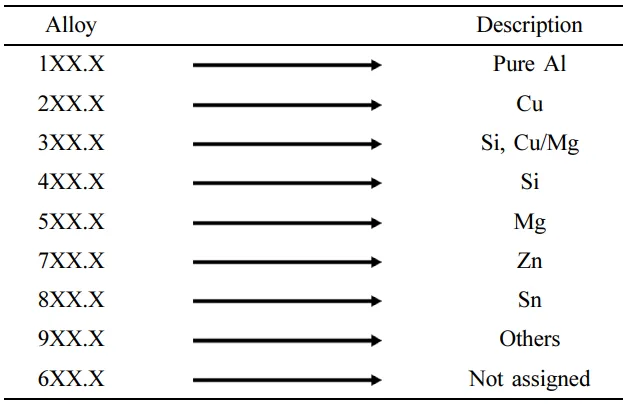
Keywords
- Primary Keyword: Aluminium brazing fillers
- Secondary Keywords: Alloying elements in aluminum, High temperature electronic packaging, Al-Cu alloys, Al-Si alloys, Guinier-Preston (GP) zones, Grain refinement in aluminum, Precipitation hardening
Executive Summary
- The Challenge: Selecting the right aluminium-based brazing filler for high-temperature electronic applications, such as in aerospace, is critical. These applications demand high joint strength and reliability, but poor strength from casting and shrinkage defects remains a significant challenge.
- The Method: This paper provides a comprehensive review of how various alloying elements (e.g., Cu, Si, Mg, Ni, Ti, B) and advanced additives modify the microstructure and final properties of aluminium-based alloys and fillers.
- The Key Breakthrough: The research clarifies the specific role of each major alloying element, providing a roadmap for material selection. Copper (Cu) is identified as crucial for aerospace applications due to its precipitation hardening effects, while Silicon (Si) is ideal for automotive parts requiring high castability.
- The Bottom Line: The final performance, strength, and durability of a brazed aluminium component are not accidental; they are the direct result of a strategic selection of alloying elements tailored to the specific demands of the end-use application.
The Challenge: Why This Research Matters for HPDC Professionals
For decades, aluminium alloys have been a cornerstone in automotive and aerospace engineering due to their high specific strength, excellent thermal conductivity, and corrosion resistance [Ref. 1, 2]. In applications ranging from aircraft electronics enclosures to automotive heat exchangers, joining individual components via brazing is a common manufacturing step. However, the final integrity and performance of the brazed joint depend almost entirely on the composition of the filler metal used.
Engineers constantly face the challenge of achieving specific, reliable properties. For instance, in aerospace applications, the formation of specific precipitates like GP zones is essential for hardening the alloy. Conversely, in other contexts, certain intermetallic compounds (IMCs) like CuAl₂ can be detrimental to joint strength [Ref. 6, 7]. The selection of an improper alloy composition can lead to undesirable outcomes, such as poor strength from casting defects, which is unacceptable in critical applications. This paper addresses this core challenge by reviewing how the deliberate addition of specific elements can be used to engineer the exact properties required for high-performance applications.
The Approach: Unpacking the Methodology
The researchers conducted a comprehensive review of existing scientific literature to consolidate the understanding of how different alloying elements impact aluminium-based fillers. The study methodically examines the role of:
- Major Alloying Elements: The effects of key elements like Copper (Cu), Silicon (Si), and Magnesium (Mg).
- Minor Alloying and Modifying Elements: The influence of Nickel (Ni), Manganese (Mn), Titanium (Ti), and Boron (B).
- Advanced Additives: The potential of newer materials, including rare earth elements and nano-ceramic oxides, to further refine microstructure and enhance properties.
The paper categorizes aluminium alloys according to the standard Aluminium Association (AAA) nomenclature for both cast and wrought alloys (Table 1 and Table 2) and reviews the fundamental mechanisms of strengthening, such as heat treatment and age hardening (Table 3). This systematic approach provides a clear and organized foundation for understanding the science of alloy design.
The Breakthrough: Key Findings & Data
The review distills a vast amount of research into clear, actionable findings on how individual elements control the final properties of aluminium alloys.
- Finding 1: Copper (Cu) for High Strength: The addition of copper is the primary method for strengthening aluminium alloys for aerospace applications. Through a process of heat treatment and aging, copper atoms form clusters known as Guinier-Preston (GP) zones, which evolve into strengthening precipitates (θ" and θ' phases). This transformation, shown in Figure 1, significantly hardens the material. However, prolonged aging can lead to poor strength, making precise process control essential [Ref. 12].
- Finding 2: Silicon (Si) for Superior Castability: Silicon is the most critical element for aluminium alloy castings, especially in the automotive industry. It provides excellent fluidity and low shrinkage, enabling the production of complex components. Silicon precipitates as a hard phase, which also improves abrasion resistance, though it can negatively impact machinability [Ref. 1-3].
- Finding 3: Magnesium (Mg) for Additional Strengthening: Similar to copper, magnesium enhances strength through precipitation hardening. In Al-Mg alloys, aging leads to the formation of the β-phase (Mg₅Al₈), which strengthens the matrix, as shown in the sequence in Figure 2.
- Finding 4: Nickel (Ni) for High-Temperature Stability: In Al-Cu based alloys, adding nickel leads to the formation of Cu-Ni aluminides. These intermetallic compounds are stable at elevated temperatures and do not dissolve during heat treatment. This "locks up" a portion of the copper, preventing overaging and thereby increasing the alloy's strength and stability at high temperatures [Ref. 14, 15].
- Finding 5: Titanium (Ti) and Boron (B) for Grain Refinement: Ti and B are powerful grain refiners. Titanium, at levels around 0.015%, effectively refines the grain structure of Al-Si alloys. The effect is even more pronounced when Ti is coupled with Boron, as TiB₂ particles act as potent nuclei for grain formation, which provides additional strength [Ref. 17, 18].
- Finding 6: Manganese (Mn) for Improved Strength and Ductility: Manganese interacts with aluminium to form Al₆Mn dispersoids. These particles are incoherent with the matrix and effectively hinder dislocation motion, which increases both yield strength and ultimate tensile strength without a significant loss of ductility [Ref. 19-22].
Practical Implications for HPDC Products
- For Process Engineers: The findings on Al-Cu systems (Section 3.1) underscore the criticality of precise thermal management. To achieve maximum strength for high-performance aerospace components, aging temperature and time must be tightly controlled to develop optimal GP zones while avoiding the overaging that degrades hardness, as detailed in Figure 1.
- For Quality Control: The direct correlation between precipitate phases (e.g., θ'' in Al-Cu alloys) and mechanical strength provides a powerful QC metric. Microstructural analysis can be used to validate that the heat treatment process has successfully achieved the desired strengthening phases.
- For Die Design and Alloy Selection: This review acts as a practical guide for material selection. For high-strength aerospace parts, an Al-Cu base is optimal. For complex, thin-walled automotive castings requiring high fluidity to prevent misruns, an Al-Si alloy is superior. For components exposed to high operating temperatures, the addition of Nickel (Section 3.4) to an Al-Cu alloy should be strongly considered to ensure long-term thermal stability.
Paper Details
Aluminium Based Brazing Fillers for High Temperature Electronic Packaging Applications
1. Overview:
- Title: Aluminium Based Brazing Fillers for High Temperature Electronic Packaging Applications
- Author: Ashutosh Sharma and Jae-Pil Jung
- Year of publication: 2015
- Journal/academic society of publication: J. Microelectron. Packag. Soc., 22(4), 1-5 (2015)
- Keywords: Aluminium alloys, brazing, strength, electronics, porosity
2. Abstract:
In high temperature aircraft electronics, aluminium based brazing filler is the prime choice today. Aluminium and its alloys have compatible properties like weight minimization, thermal conductivity, heat dissipation, high temperature precipitation hardening etc. suitable for the aerospace industry. However, the selection of brazing filler for high temperature electronics requires high temperature joint strength properties which is crucial for the aerospace. Thus the selection of proper brazing alloy material, the composition and brazing method play an important role in deciding the final reliability of aircraft electronic components. The composition of these aluminium alloys dependent on the addition of the various elements in the aluminium matrix. The complex shapes of aluminium structures like enclosures, heat dissipaters, chassis for electronic circuitry, in avionics are designed from numerous individual components and joined thereafter. In various aircraft applications, the poor strength caused by the casting and shrinkage defects is undesirable. In this report the effect of various additional elements on Al based alloys and brazing fillers have been discussed.
3. Introduction:
Aluminium based fillers are playing a great role not only in automotive but also aerospace applications. The various attracting properties obtained from the aluminium alloys are high specific strength, available in plenty, highly oxidation and corrosion resistant, high thermal and electrical conductivities. Aluminium alloys are a clean source free from unwanted health hazard and toxicity in brazing technology, and economically very cheap. A high specific strength accounts for the weight reduction drastically as compared to steel, which is beneficial to improve the fuel efficiency and reduces carbon emissions. The various parts of the aircraft or automotive requires joining by braze welding or simply brazing.
4. Summary of the study:
Background of the research topic:
The paper establishes that aluminium alloys are critical for high-temperature applications like aerospace electronics due to their favorable properties. However, achieving reliable, high-strength joints through brazing is a significant engineering challenge. The final properties of the brazed component depend heavily on the chemical composition of the filler alloy.
Status of previous research:
Previous research has extensively studied Al-Cu alloys for aerospace and Al-Si alloys for automotive applications. Work has been done on refining intermetallic compounds (IMCs) and modifying silicon structures to improve mechanical properties. The roles of various alloying elements, modifiers, and even nano-ceramic oxides have been investigated to control the final microstructure and performance of brazed joints.
Purpose of the study:
The purpose of this report is to review and discuss the effect of various additional elements on Al based alloys and brazing fillers. The goal is to provide a consolidated understanding of how different alloying elements should be selected to tailor the alloy's properties for specific brazing applications.
Core study:
The core of the study is a systematic review of the influence of key alloying elements on the microstructure and properties of aluminium. It details the mechanisms by which elements like Cu, Si, Mg, Ni, Ti, B, and Mn contribute to strength, castability, high-temperature stability, and grain structure.
5. Research Methodology
Research Design:
The study is designed as a comprehensive literature review. It synthesizes findings from numerous published academic papers and handbooks on aluminium metallurgy.
Data Collection and Analysis Methods:
The authors collected and analyzed data from existing research to explain the fundamental principles of alloy design. This includes phase transformation sequences, precipitation mechanisms, and the empirical effects of adding specific elements.
Research Topics and Scope:
The scope covers the classification of aluminium alloys (cast, wrought, heat-treatable), the conditions for age hardening, and a detailed analysis of the effects of alloying additions, including: Aluminium-Copper, Aluminium-Silicon, Aluminium-Magnesium, Aluminium-Nickel, Aluminium-Titanium/Boron, Aluminium-Manganese, Rare Earth elements, and Nano-additives.
6. Key Results:
Key Results:
- Copper (Cu): Induces precipitation hardening through the formation of GP zones, leading to high strength suitable for aerospace applications.
- Silicon (Si): Provides excellent castability, high fluidity, and low shrinkage, making it ideal for complex automotive castings.
- Magnesium (Mg): Increases strength by forming Mg₅Al₈ precipitates during aging.
- Nickel (Ni): Enhances high-temperature strength in Al-Cu alloys by forming stable Cu-Ni aluminides that resist overaging.
- Titanium (Ti) & Boron (B): Act as potent grain refiners, improving mechanical properties.
- Manganese (Mn): Improves yield and ultimate tensile strength by forming Al₆Mn dispersoids.
- Rare Earths & Nano-additives: Show potential for refining grain size, IMCs, and Si morphology.
Figure Name List:
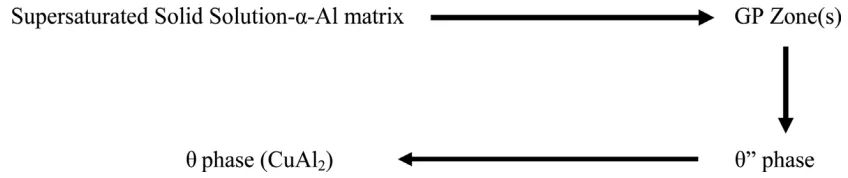
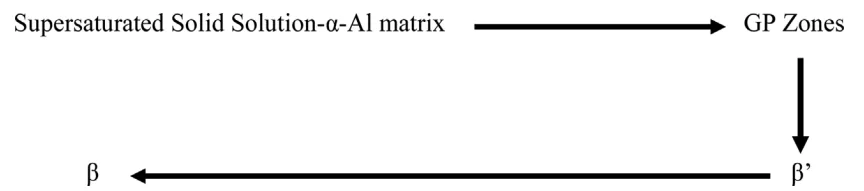
- Fig. 1. Transformation sequence of GP zones in Al-Cu alloys.1,10-12)
- Fig. 2. Precipitation sequence in Al-Mg alloy.13)
7. Conclusion:
Alloying elements provide the improved microstructure of aluminium and decides the final properties of the alloy. Microstructural modifications are usually brought about by the precipitates causing an enhancement of the strength and durability at high temperatures. The addition of copper triggers the formation of GP zones from the supersaturated solid solution during aging after heat treatment suitable for aerospace. Silicon provides mostly fluidity and castability and suitable for automotive applications. Magnesium too forms precipitates and increase strengthening of the alloy. Ti and B improves the grain refinement and hence provide additional strengthening. Nickel, though expensive used in minute concentration produces aluminides with copper and aluminium for high temperature stability. Addition of Mn improves the yield strength and ultimate tensile strength, though a reduction in ductility is also observed. Recently, various reports have shown a beneficial effect of the addition of rare earth elements and nano ceramic oxides to refine the grain size as well as the various IMC and Si morphology. It can be suggested from this review that an alloying of the aluminium alloys affects the various properties, therefore the selection of alloying element should be exercised depending on its role and suitability for the particular brazing application.
8. References:
- [1] I. J. Polmear, Light alloys: From Traditional Alloys to Nanocrystals, 4th Ed., pp. 16-26, Elsevier, Butterworth Heinemann (2006).
- [2] B. Altshuller, Aluminum Brazing Handbook, 4th Ed., pp. 24-32, The Aluminum Association, Inc., Washington D.C. (1990).
- [3] A. H. Musfirah and A. G. Jaharah, "Magnesium and Aluminum Alloys in Automotive Industry", J. Appl. Sci. Res., 8, 4865 (2012).
- [4] F. Stadler, H. Antrekowitsch, W. Fragner, H. Kaufmann and P. J. Uggowitzer, "Effect of Main Alloying Elements on Strength of Al-Si Foundry Alloys at Elevated Temperatures", Int. J. Cast Metal. Res., 25, 215 (2012).
- [5] C. J. Hang, C. Q. Wang, M. Mayer, Y. H. Tian, Y. Zhou and H. H. Wang, "Growth Behavior of Cu/Al Intermetallic Compounds and Cracks in Copper Ball Bonds During Isothermal Aging", Microelectron. Reliab., 48, 416 (2008).
- [6] W. F. Smith, Principles of Materials Science and Engineering, 3rd Ed., pp. 1-892, McGraw-Hill, Inc. (1996).
- [7] M. H. Larsen, J. C. Walmsley, O. Lunder, R. H. Mathiesen and K. Nisancioglu, “Intergranular Corrosion of Copper-Containing AA6xxx AlMgSi Aluminium Alloys", J. Electrochem. Soc., 155(11), C550 (2008).
- [8] K. Thulukkanam, Heat Exchanger Design Handbook, 2nd Ed., pp. 996-1002, CRC Press, Florida USA (2013).
- [9-28] Additional references are listed in the original paper and are available upon request.
Expert Q&A: Your Top Questions Answered
Q1: My application is in aerospace and requires high strength at elevated temperatures. Which alloying elements should I focus on?
A1: The paper strongly suggests a focus on Copper (Cu) and Nickel (Ni). Copper creates strength through precipitation hardening via GP zones (Figure 1). Nickel is crucial for high-temperature stability, as it forms stable Cu-Ni aluminides that prevent the alloy from weakening due to overaging at service temperatures (Section 3.1, 3.4).
Q2: We manufacture complex, thin-walled automotive components. What's the most critical element for ensuring our castings fill completely?
A2: According to the paper, Silicon (Si) is the most important element for this purpose. It provides excellent castability, high fluidity, and low shrinkage, which are all essential for successfully producing sound, complex castings with thin sections (Section 3.2).
Q3: We are observing inconsistent mechanical properties and large grains in our castings. How can we improve this?
A3: The research points to Titanium (Ti) and Boron (B) as effective grain refiners. The paper notes that adding a small amount of Ti (around 0.015%) can significantly refine the grain structure. The combination of Ti and B, which forms TiB₂, is even more potent for achieving a fine, uniform grain structure and more consistent properties (Section 3.5, Ref. [17], [18]).
Q4: What is the main mechanism that gives heat-treatable aluminum alloys their strength?
A4: The primary mechanism is precipitation hardening (or age hardening). This process involves a solution heat treatment and quench to create a supersaturated solid solution. Subsequent aging allows for the formation of fine, coherent precipitates—like GP zones in Al-Cu alloys (Figure 1) or the β-phase in Al-Mg alloys (Figure 2)—that impede dislocation movement and dramatically increase strength (Section 2.5, 3.1, 3.3).
Q5: Are there any downsides to adding certain alloying elements that I should be aware of?
A5: Yes, the selection of an alloying element always involves trade-offs. For example, while Silicon improves castability, the paper notes it can decrease machinability. Excessive addition of Titanium (e.g., up to 0.15%) can be deleterious, causing grain coarsening and porosity. The paper also mentions that adding Zinc (Zn) to Al-Mg alloys has been found to increase the corrosion rate (Section 3.2, 3.5, 3.3, Ref. [13], [17]).
Conclusion & Next Steps
This research provides a valuable roadmap for enhancing the performance of aluminium components through strategic alloy design. The findings offer a clear, science-based path toward improving strength, castability, and high-temperature durability by making informed choices about alloying elements.
At CASTMAN, we are dedicated to applying the latest industry research to solve our customers' most challenging die casting problems. If the issues discussed in this paper resonate with your operational goals, contact our engineering team to discuss how we can help you implement these advanced principles in your components.
Copyright
- This material is a paper by "Ashutosh Sharma and Jae-Pil Jung". Based on "Aluminium Based Brazing Fillers for High Temperature Electronic Packaging Applications".
- Source of the paper: http://dx.doi.org/10.6117/kmeps.2015.22.4.001
This material is for informational purposes only. Unauthorized commercial use is prohibited. Copyright © 2025 CASTMAN. All rights reserved.