This article introduces the paper ['The Impact of Giga-Castings on Car Manufacturing and Aluminum Content'] presented at the ['Light Metal Age']
1. Overview:
- Title: The Impact of Giga-Castings on Car Manufacturing and Aluminum Content
- Author: Alicia Hartlieb and Martin Hartlieb
- Publication Year: 2023
- Publishing Journal/Academic Society: Light Metal Age (June 2023 issue, Editor's Note)
- Keywords: giga-castings, mega-castings, car manufacturing, aluminum content, automotive, castings, sheet metal, extrusions, BEVs, BIW, rheocasting, sustainability
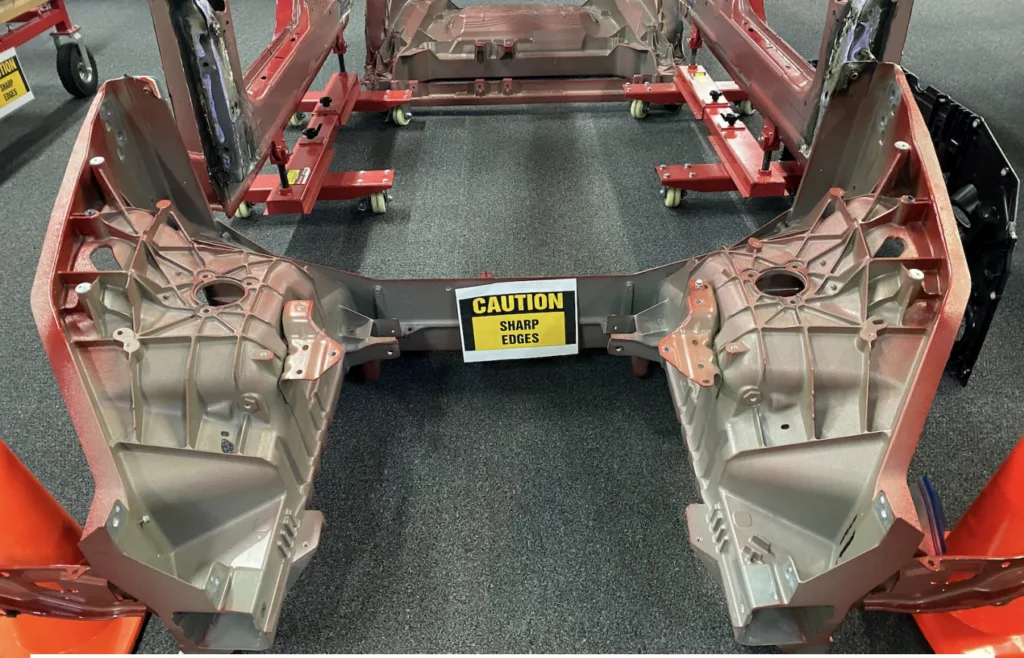
2. Abstracts
Numerous studies, especially from Ducker-Carlisle, have shown that aluminum usage in light vehicles has been growing for decades, having surpassed 500 lbs (227 kg) per light vehicle in North America and 396 lbs (180 kg) per vehicle in Europe. Until now, castings have been the predominant product form, but in recent years and even more so in coming years, sheet and extrusion applications are showing the greatest growth rates. The main driver for aluminum use has always been lightweighting.
The accelerating electrification of vehicles has only continued aluminum's growth trend, while also changing the product mix. Historically, castings have been the predominant product form and have mainly been used in the powertrain of internal combustion engine (ICE) vehicles (primarily using secondary A380 or 319 alloys), while hybrid vehicles usually contain smaller engines and battery electric vehicles (BEVs) do not use ICEs. Now, the aluminum growth has been shifting to the car body and chassis, and for electric vehicles also to the battery trays and electric drive components. Today, these components are mostly made from sheet and extruded products with only some castings, which are often structural and, therefore, made with more sophisticated processes and cleaner aluminum alloys (either primary or secondary from clean scrap).
Currently, a higher aluminum content, especially assemblies of sheet metal and extrusions, means higher costs. Additionally, if primary aluminum is used, it also means a higher carbon footprint. OEMs and their suppliers have therefore been working on lowering both the material and processing costs of their components, while improving production quality and enhancing sustainability, i.e., increasing recycling content in all types of aluminum parts.¹
In the last few years, a new trend is starting to catch on. Initiated by Tesla, the trend involves utilizing giga-castings (also referred to by some OEMs as "mega-castings"). These large cast structural components are able to integrate many different parts into a single ultra-large casting. This could not only impact the way cars are manufactured and the utilization of aluminum in general, but also affect the content of different product forms (castings, sheet, and extrusions) in light vehicles. In other words, it could spur new growth for castings and potentially slow down the growth of sheet and extrusions.
3. Research Background:
Background of the Research Topic:
Aluminum usage in light vehicles has been increasing for decades, driven by lightweighting. Historically, castings were the predominant aluminum product form, mainly used in powertrain of internal combustion engine (ICE) vehicles. However, with the accelerating electrification of vehicles, aluminum application is shifting towards car body and chassis, battery trays, and electric drive components, predominantly using sheet and extrusions. Higher aluminum content, especially with sheet metal and extrusions, increases costs and carbon footprint, prompting OEMs to seek cost reduction, quality improvement, and enhanced sustainability through increased recycling content.
Status of Existing Research:
Studies from Ducker-Carlisle have indicated the growing trend of aluminum usage in light vehicles, surpassing 500 lbs (227 kg) per light vehicle in North America and 396 lbs (180 kg) per vehicle in Europe. These studies highlight the historical predominance of castings, but also the recent growth in sheet and extrusion applications.
Necessity of the Research:
A new trend of utilizing giga-castings (or mega-castings), initiated by Tesla, is emerging. These large cast structural components can integrate numerous parts into a single casting, potentially revolutionizing car manufacturing, aluminum utilization, and the product form mix in light vehicles. Understanding the impact of giga-castings on car manufacturing and aluminum content is crucial for the automotive industry.
4. Research Purpose and Research Questions:
Research Purpose:
The paper aims to analyze the impact of giga-castings on car manufacturing processes and aluminum content within vehicles. It explores the potential of giga-castings to transform traditional car body design and manufacturing, and assesses the benefits and challenges associated with this technology.
Key Research:
The key research questions addressed in this paper are:
- How do giga-castings revolutionize traditional car body (unibody) design and streamline manufacturing?
- What are the benefits of using giga-castings in car manufacturing, such as component reduction, weight reduction, and simplified assembly?
- What are the downsides and challenges associated with giga-castings, including repairability, tolerance control, and casting quality?
- How do giga-castings impact the utilization of different aluminum product forms (castings, sheet, extrusions) and steel sheet metal stampings in vehicles?
- What is the potential of rheocasting as a solution to address some of the challenges in producing giga-castings?
Research Hypotheses:
Not explicitly stated in the paper. However, implicitly, the paper explores the hypothesis that giga-castings represent a significant shift in automotive manufacturing with both considerable advantages and new challenges compared to traditional methods using sheet metal assemblies and smaller castings.
5. Research Methodology
Research Design:
This paper employs a descriptive and analytical approach, based on industry observation and analysis of emerging trends in automotive manufacturing, particularly the adoption of giga-castings. It is presented as an industry overview rather than a strictly academic research paper.
Data Collection Method:
The analysis is based on industry reports, case studies of OEMs like Tesla, Volvo, and Polestar, and general knowledge of automotive manufacturing and die casting technologies. Specific sources are cited as references throughout the text.
Analysis Method:
The paper uses a qualitative analysis method, discussing the benefits, downsides, and challenges of giga-castings based on current industry practices and expert opinions. It compares giga-casting technology to traditional methods and explores the potential impacts on material usage and manufacturing processes.
Research Subjects and Scope:
The scope of the paper is focused on the application of giga-castings in the automotive industry, specifically for car body structures (BIW), chassis components, and battery trays in light vehicles, including both Battery Electric Vehicles (BEVs) and vehicles with Internal Combustion Engines (ICE).
6. Main Research Results:
Key Research Results:
- Revolutionizing Car Manufacturing: Tesla's use of two giga-castings in Model Y replaced 171 parts, eliminated 1,600 welds, and removed 300 robots, significantly reducing capital investment and floorspace.
- Benefits of Giga-Castings:
- Component Reduction: Integrates numerous stamped sheet components and smaller castings into one large casting.
- Weight Reduction: Reduces overall vehicle weight, especially beneficial for BEVs to increase range and efficiency.
- Simplified Assembly: Simplifies vehicle bill of material, making manufacturing and assembly easier and quicker.
- Reduced Capital Investment: Greenfield facilities designed for giga-casting benefit from reduced assembly space and time.
- Supply Chain Logistics: Shortened assembly line and reduced welding.
- Downsides and Challenges of Giga-Castings:
- Repairability: Damage to a giga-casting necessitates replacement of the entire casting, which is cost-prohibitive.
- Tolerance Control: Maintaining tight tolerances during manufacturing is challenging due to varying wall thicknesses and cooling rates, leading to distortions. Complex straightening systems are required.
- Casting Quality: Achieving defect-free large structural castings is extremely challenging, leading to potentially high scrap rates.
- Die Challenges: Dies for giga-castings are huge, expensive, and have limited die life compared to stamping dies.
- Impact on Material Usage:
- Giga-castings may slightly impact aluminum sheet content growth but will convert some steel sheet to aluminum castings.
- Extrusions are less affected, especially for components like crash boxes. Battery trays might see some replacement of extrusions with giga-castings.
- Overall, giga-castings are expected to increase total aluminum content in vehicles, taking share from steel sheet stampings.
- Rheocasting as a Solution: Rheocasting (semi-solid casting) is considered a potential solution to address giga-casting challenges, offering benefits like improved part complexity, increased flow length, extended die life, reduced machine size requirements, and enhanced alloy and sustainability options.
Data Interpretation:
Giga-castings represent a paradigm shift in automotive body structure manufacturing. While offering significant advantages in terms of manufacturing efficiency and vehicle performance, they also introduce new challenges related to production, quality control, and repair. The industry is actively exploring solutions like rheocasting to mitigate these challenges and fully realize the potential of giga-casting technology. The impact on material usage suggests a potential increase in overall aluminum content in vehicles, with a shift from sheet and steel to castings in certain structural applications.
Figure Name List:
- Figure 1. A Tesla Model Y giga-casting. (Source: S. Munro.)
- Figure 2. A giga-casting being processed in an automatic straightening system. (Source: Laubinger & Rickmann.)

7. Conclusion:
Summary of Key Findings:
Giga-castings are revolutionizing car body designs and manufacturing in the automotive industry. They are primarily used for front and rear underbody and battery trays, replacing aluminum and steel sheet metal, smaller castings, and extrusions. Giga-castings offer benefits like component reduction, weight reduction, and simplified assembly, but also pose challenges in repairability, tolerance control, and casting quality. Rheocasting is being explored as a potential solution to overcome some of these challenges and enhance sustainability through increased recycled content. The overall impact of giga-castings is positive for aluminum growth in vehicles, with a likely shift in material usage patterns.
Academic Significance of the Study:
This paper provides a timely overview and analysis of the emerging trend of giga-castings in the automotive industry. It highlights the technological advancements and challenges associated with this manufacturing innovation, contributing to the understanding of evolving automotive manufacturing techniques and their impact on material selection and vehicle design.
Practical Implications:
For automotive OEMs, giga-castings offer a pathway to streamline manufacturing, reduce costs, and improve vehicle performance, particularly for electric vehicles. However, it necessitates significant capital investment in new equipment and expertise in large-scale casting processes. Suppliers need to adapt to the demands of giga-casting production, addressing challenges in die manufacturing, casting quality, and post-processing. The shift towards giga-castings also has implications for the aluminum industry, potentially increasing demand for specific alloys and recycled aluminum content.
Limitations of the Study and Areas for Future Research:
This paper is based on an overview of current industry trends and lacks in-depth quantitative data or technical analysis. Future research could focus on:
- Detailed technical studies on the metallurgy and processing of giga-cast alloys.
- Quantitative analysis of cost savings and performance improvements achieved through giga-casting.
- Investigation of advanced process control and quality assurance methods for giga-casting production.
- Comparative life cycle assessments of vehicles manufactured with giga-castings versus traditional methods.
- Further exploration of rheocasting and other advanced casting techniques for giga-casting applications.
8. References:
- Hart, C., A. Afseth, and B. Zuidema, "Aluminum Value in Battery Electric Vehicles,” The Aluminum Association, 2022.
- Abraham, A.K., "Automotive Materials in an Evolving Landscape,” Ducker Carlisle, January 24, 2023.
- Loots, W., "Tesla Giga Casting,” Driven, January 1, 2023.
- Schuh, G., G. Bergweiler, L. Dworog, and F. Fiedler, "Die Karosserie aus dem Aluminium-Druckguss / Opportunities and Risks of Mega-Casting in Automotive Production – The Aluminum Die-Casted Body in White,” Düsseldorf: VDI Fachmedien, September 2022, www.researchgate.net/publication/363880399.
- Wärmefjord, K., J. Hansen, and R. Söderberg, "Challenges in Geometry Assurance of Megacasting in the Automotive Industry,” ASME, Journal Computing and Information Science in Engineering, Vol. 23, No. 6, December 2023, https://doi.org/10.1115/1.4062269.
- "Giga Presses – the giant die casts that are reshaping car manufacturing,” Reuters/Automotive News Europe, February 10, 2023.
- Volk, W., "Gigacasting ist geeignet, den Karosseriebau neu zu denken,” Automobil-Produktion, February 3, 2022.
- Carney, D., "Volvo Joins Tesla in the Giga Press Club," Design News, Mar 14, 2022.
- Bergeron, S., M. Hartlieb, P. Jansson, and J.-C. Tawil, “Rheocasting Structural Components," Die Casting Engineer, May 2023, pp. 24-30.
9. Copyright:
- This material is "Alicia Hartlieb and Martin Hartlieb"'s paper: Based on "The Impact of Giga-Castings on Car Manufacturing and Aluminum Content".
- Paper Source: [No DOI URL provided in the text, please use the article link if available or indicate 'N/A']
This material was summarized based on the above paper, and unauthorized use for commercial purposes is prohibited.
Copyright © 2025 CASTMAN. All rights reserved.