This article introduces the paper "Study on the Influence of Injection Velocity on the Evolution of Hole Defects in Die-Cast Aluminum Alloy" presented at the MDPI
1. Overview:
- Title: Study on the Influence of Injection Velocity on the Evolution of Hole Defects in Die-Cast Aluminum Alloy
- Author: Hanxue Cao, Qiang Zhang, Weikai Zhu, Sheng Cui, Qin Yang, Zhibai Wang and Bin Jiang
- Publication Year: 2024
- Publishing Journal/Academic Society: Materials (MDPI)
- Keywords: aluminum alloy die-casting; visualization; injection rate; hole defects
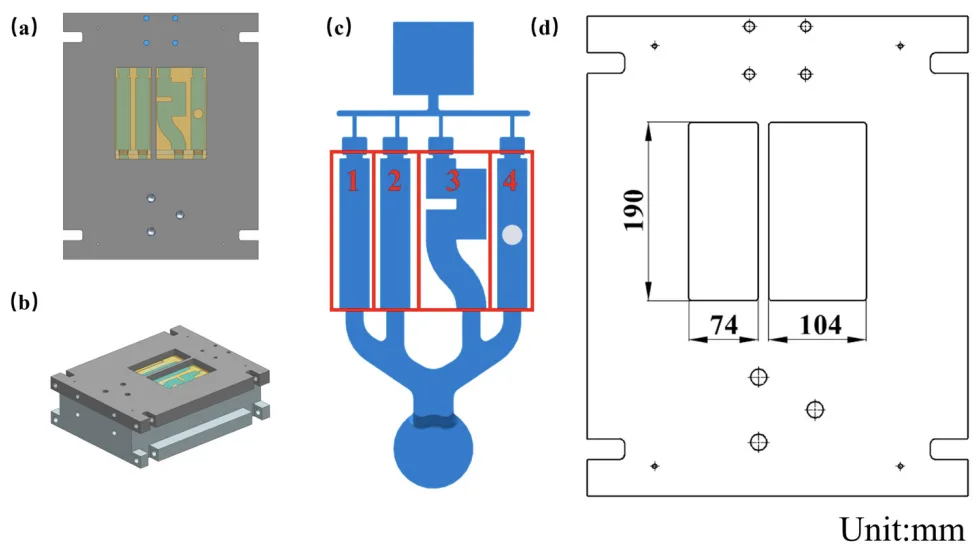
2. Research Background:
- Social/Academic Context of the Research Topic: Aluminum alloy die casting is a rapidly developing technology widely used across industries due to its efficiency and dimensional accuracy. However, porosity defects, commonly known as hole defects, are a significant challenge in die casting, negatively impacting the mechanical and processing properties of components. Understanding and mitigating these defects is crucial for improving the quality and reliability of die-cast products.
- Limitations of Existing Research: While previous studies have explored the influence of process parameters and mold structure on porosity, there is a lack of direct observation and characterization of molten metal flow behavior within the mold cavity during high-pressure die casting. Existing methods like water simulation and numerical simulation have limitations in accurately representing the complex dynamics of liquid metal flow and defect formation.
- Necessity of the Research: To effectively reduce or eliminate hole defects, a deeper understanding of gas behavior during the die casting process is essential. This research addresses the need for a method to directly observe and analyze the influence of injection velocity on alloy flow patterns and gas-induced defects in real-time during the die casting process of aluminum alloys, specifically ADC12, a commonly used alloy.
3. Research Purpose and Research Questions:
- Research Purpose: The primary purpose of this research is to investigate the influence of different injection velocities on the formation and evolution of hole defects in die-cast aluminum alloy by directly visualizing the filling process.
- Key Research Questions:
- How does varying injection velocity affect the flow pattern of molten aluminum alloy during die casting?
- What is the relationship between injection velocity and the formation and evolution of gas-induced hole defects?
- What mechanisms contribute to the formation of hole defects at different injection velocities?
- Research Hypotheses: The research hypothesizes that increasing injection velocity will alter the molten metal flow pattern, leading to increased air entrapment and consequently, a higher degree of porosity and larger hole defects in die-cast aluminum alloy components.
4. Research Methodology
- Research Design: This study employs an innovative dynamic visualization experiment using a specially designed die with a glass window mounted on a horizontal cold chamber die-casting machine (DCC630M). This setup allows for direct observation of the aluminum alloy filling process.
- Data Collection Method: A high-speed camera (1000 frames per second, 1024 × 1024 resolution) recorded the molten metal flow during die casting at different injection velocities (1.0 m/s and 1.5 m/s). Cast samples were produced and porosity was quantified using the static water method and a density balance (MH-110E).
- Analysis Method: The recorded videos were analyzed to characterize the dynamic evolution of flow patterns and defect formation. Image-Pro Plus software was used to measure and analyze hole defects in cross-sections of the cast samples. Numerical simulations using Anycasting software were conducted to compare with experimental observations.
- Research Subjects and Scope: The research focuses on ADC12 aluminum alloy die casting. The study investigates the influence of two different injection velocities (1.0 m/s and 1.5 m/s) on hole defect formation in a mold with four common cavity structures: countersunk hole, stepped boss, bow, and through-the-hole structures. Samples were taken from four locations (S1, S2, S3, S4) within these cavity structures for porosity analysis.
5. Main Research Results:
- Key Research Results:
- Increasing the injection speed from 1.0 m/s to 1.5 m/s resulted in an increase in average porosity from 7.49% to 9.57%. This indicates a significant increase in both the number and size of pores with higher injection velocity.
- Visualization and simulation showed that at 1.5 m/s injection velocity, the flow front exhibited more significant fracturing and splashing compared to 1.0 m/s.
- The degree of broken splash at the flow front was more severe at higher injection speeds, attributed to the wall-attached jet effect.
- Increased injection velocity led to a decrease in the microgroup volume formed by liquid breakage, resulting in increased air entrapment and cavity defects.
- Statistical/Qualitative Analysis Results: Quantitative porosity measurements confirmed a statistically significant increase in porosity with higher injection velocity. Qualitative analysis of the visualization videos revealed distinct flow patterns and increased turbulence and splashing at the higher injection speed.
- Data Interpretation: The increased porosity at higher injection velocities is attributed to the intensified wall-attached jet effect and flow front fracturing. This phenomenon makes it difficult for subsequent liquid metal to fuse with the initial flow, trapping air and leading to cavity defects.
- Figure Name List:
- Figure 5. Flow characteristics at different velocities of injection
- Figure 6. Simulation results of filling flow at different speeds
- Figure 7. Cross-sectional morphology of specimens with an inner gate thickness of 3.0 mm and an injection velocity of 1.0 m/s.
- Figure 8. Cross-sectional morphology of specimens with an inner gate thickness of 3.0 mm and an injection velocity of 1.5 m/s.
- Figure 9. Porosity at different injection velocities at a 3.0 mm inner gate.
- Figure 10. Flow pattern of liquid metal at S2 position at injection velocity of 1.0 m/s.
- Figure 11. Flow pattern of liquid metal at S2 position at injection velocity of 1.5 m/s.
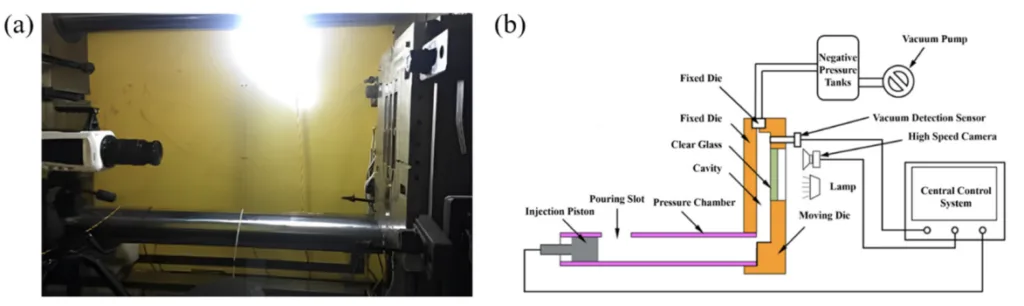
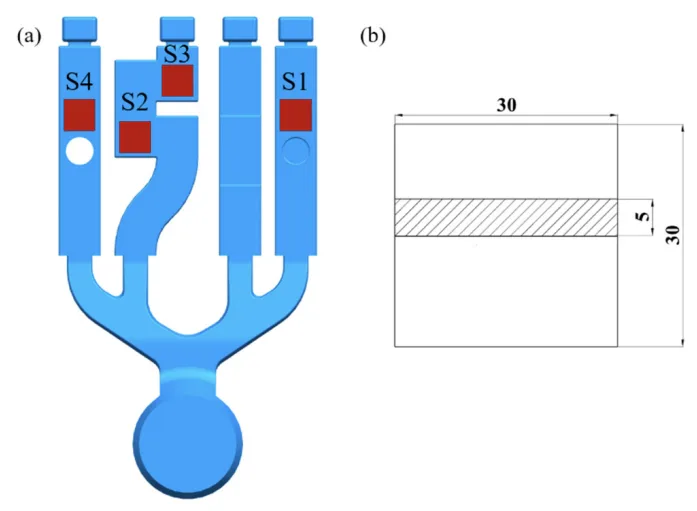
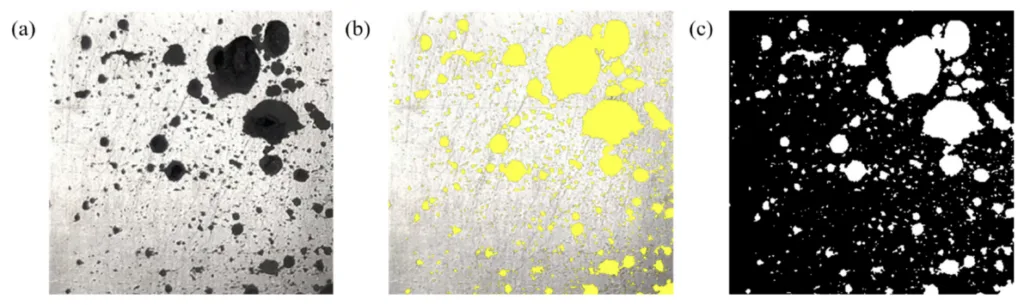
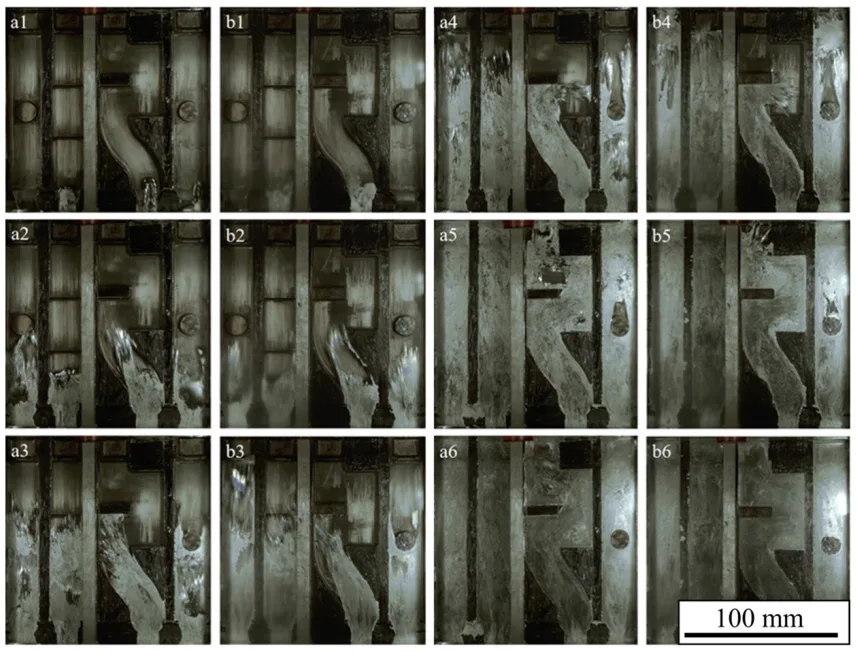
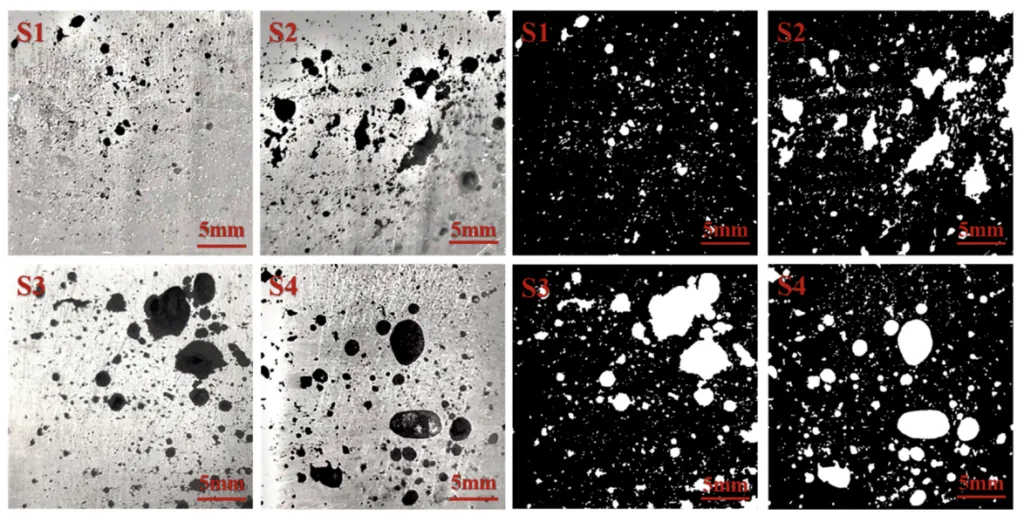
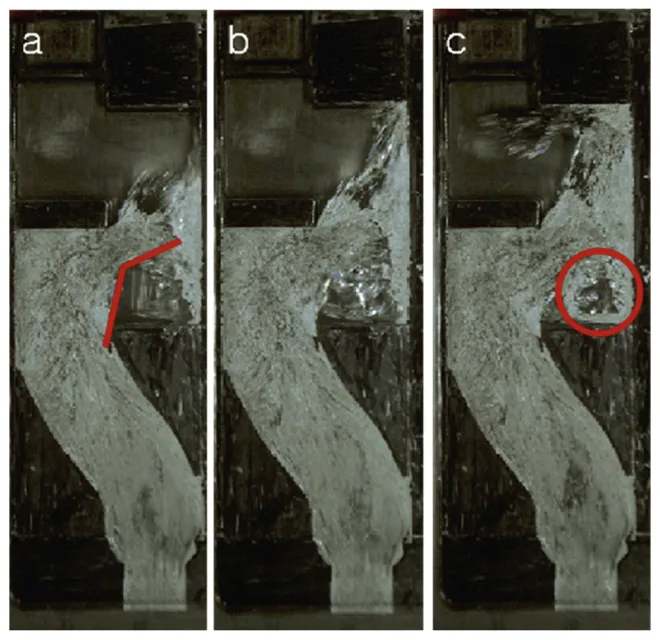
6. Conclusion and Discussion:
- Summary of Main Results: This study demonstrated that increasing injection velocity in aluminum alloy die casting leads to a significant increase in porosity and hole defects. This is primarily due to intensified flow front fracturing, wall-attached jet effects, and increased air entrapment caused by higher injection speeds.
- Academic Significance of the Research: The innovative dynamic visualization method provides a valuable tool for directly observing and understanding molten metal flow behavior and defect formation in die casting. The findings contribute to a deeper understanding of the mechanisms behind gas-induced defects and the influence of injection velocity.
- Practical Implications: The research suggests practical measures for mold design to minimize porosity, including:
- Avoiding large flat surfaces to redirect flow and reduce wall jet effect.
- Adding small protrusions or depressions on large flat surfaces to disrupt stable flow and promote metal integration.
- Incorporating flow guiding plates or tubes to control fluid direction for uniform flow.
- Designing streamlined or curved mold shapes to minimize fluid stagnation and uneven flow.
- Limitations of the Research: This study primarily focused on the influence of injection velocity. The paper acknowledges that factors like temperature distribution also play a significant role in flow and pore formation, which were not the primary focus of this research.
7. Future Follow-up Research:
- Directions for Follow-up Research: Future research should explore the impact of temperature distribution on molten metal flow and pore formation in die casting.
- Areas Requiring Further Exploration: Further investigation is needed to optimize numerical simulation boundary conditions and develop more realistic physical models to enhance the accuracy of simulations in predicting flow behavior and defect formation, potentially incorporating temperature effects.
8. References:
- [1] Wang, G.G.; Weiler, J.P. Recent developments in high-pressure die-cast magnesium alloys for automotive and future applications. J. Magnes. Alloys 2023, 11, 78–87.
- [2] Yang, Y.-T.; Qiu, Z.-Y.; Zheng, Z.; Pu, L.-X.; Chen, D.-D.; Zheng, J.; Zhang, R.-J.; Zhang, B.; Huang, S.-Y. Al-enabled properties distribution prediction for high-pressure die casting Al-Si alloy. Adv. Manuf. 2024, 12, 591-602.
- [3] Cleary, P.; Ha, J.; Alguine, V.; Nguyen, T. Flow modelling in casting processes. Appl. Math. Model. 2002, 26, 171-190.
- [4] Kang, H.J.; Yoon, P.H.; Lee, G.H.; Park, J.Y.; Jung, B.J.; Lee, J.Y.; Lee, C.U.; Kim, E.S.; Choi, Y.S. Evaluation of the gas porosity and mechanical properties of vacuum assisted pore-free die-cast Al-Si-Cu alloy. Vacuum 2021, 184, 109917.
- [5] Hu, Q.; Guo, W.; Xiao, P.; Zhao, H. Effects of Fast Shot Speed and Wall Thickness on the Microstructures and Mechanical Properties of the High Pressure Die-casting 6061-SiC Composites. Metall. Mater. Trans. B-Process Metall. Mater. Process. Sci. 2021, 52, 2283–2293.
- [6] Ma, Y.-H.; Yu, W.-B.; Zhou, Y.-Q.; Xiong, S.-M. Influence of different high pressure die casting processes on 3D porosity distribution of Mg-3.0Nd-0.3Zn-0.6Zr alloy. China Foundry 2021, 18, 521–528.
- [7] Majerník, J.; Gašpár, S.; Husár, J.; Paško, J.; Kolínský, J. Research and Evaluation of the Influence of the Construction of the Gate and the Influence of the Piston Velocity on the Distribution of Gases into the Volume of the Casting. Materals 2021, 14, 2264.
- [8] Ibrahim, M.D.; Mohamad, M.R.; Roslan, L.; Sunami, Y.; Lam, S.S. High Pressure Die Casting Porosity Defect Analysis and Experimental Validation for Power Steering Columns and DVVTs. In Lecture Notes in Mechanical Engineering; Springer: Singapore, 2018; pp. 187–196.
- [9] Gautam, S.K.; Roy, H.; Lohar, A.K.; Samanta, S.K. Studies on Mold Filling Behavior of Al-10.5Si-1.7Cu Al Alloy during Rheo Pressure Die Casting System. Int. J. Met. 2023, 17, 2868–2877.
- [10] Haghniaz, F.; Delbergue, D.; Côté, R.; Demers, V. Mold filling behaviour of LPIM feedstocks using numerical simulations and real-scale injections. Powder Metall. 2023, 66, 436-449.
- [11] Hu, M.Y.; Cai, J.J.; Li, N.; Yu, H.L.; Zhang, Y.; Sun, B.; Sun, W.L. Flow Modeling in High-Pressure Die-Casting Processes Using SPH Model. Int. J. Met. 2018, 12, 97-105.
- [12] Ren, M.; Gu, J.; Li, Z.; Ruan, S.; Shen, C. Simulation of Polymer Melt Injection Molding Filling Flow Based on an Improved SPH Method with Modified Low-Dissipation Riemann Solver. Macromol. Theory Simul. 2022, 31, 2100029.
- [13] Niu, X.F.; Zhao, J.Y.; Wang, B.J. Application of smooth particle hydrodynamics (SPH) method in gravity casting shrinkage cavity prediction. Comput. Part. Mech. 2019, 6, 803–810.
- [14] Zarbini Seydani, M.; Krimi, A.; Bedel, M.; Khelladi, S.; El Mansori, M. A 2D filling and solidification benchmark test: Validating smoothed particle hydrodynamics (SPH) simulations for sand gravity casting. Int. J. Adv. Manuf. Technol. 2023, 128, 801–821.
- [15] Saeedipour, M.; Schneiderbauer, S.; Pirker, S.; Bozorgi, S. A Numerical and Experimental Study of Flow Behavior in High Pressure Die Casting. In Magnesium Technology, Proceedings of the 2014—TMS 2014 143rd Annual Meeting and Exhibition, San Diego, CA, USA, 16–20 February 2014; Springer: Berlin/Heidelberg, Germany, 2014.
- [16] Kulasegaram, S.; Bonet, J.; Lewis, R.W.; Profit, M. High pressure die casting simulation using a Lagrangian particle method. Commun. Numer. Methods Eng. 2003, 19, 679-687.
- [17] Homayonifar, P.; Babaei, R.; Attar, E.; Shahinfar, S.; Davami, P. Numerical modeling of splashing and air entrapment in high-pressure die casting. Int. J. Adv. Manuf. Technol. 2008, 39, 219-228.
- [18] Bi, C.; Xiong, S. Development of a Full PLIC-VOF Method for Mold Filling Simulation of High Pressure Die Casting Process. In Proceedings of the 8th Pacific Rim International Congress on Advanced Materials and Processing, Waikoloa, HI, USA, 4–9 August 2013; Marquis, F., Ed.; Springer International Publishing: Cham, Switzerland, 2016; pp. 2867–2874.
- [19] Sakuragi, T. Mould filling simulation with consideration of surface tension and its application to a practical casting problem. Cast Metals 2013, 18, 202-208.
- [20] Niida, A.; Maeda, Y. Observation of Air Entrapment during Mold Filling of Die Casting Using Water Model Experiment for Mold Filling Simulation. Mater. Trans. 2020, 61, 1364-1368.
- [21] Liu, J.; Zhou, P.; Zuo, X.; Wu, D.; Wu, D. Optimization of the Liquid Steel Flow Behavior in the Tundish through Water Model Experiment, Numerical Simulation and Industrial Trial. Metals 2022, 12, 1480.
- [22] Lin, S.P.; Reitz, R.D. Drop and spray formation from a liquid jet. Annu. Rev. Fluid Mech. 1998, 30, 85–105.
9. Copyright:
This material is Hanxue Cao et al.'s paper: Based on Study on the Influence of Injection Velocity on the Evolution of Hole Defects in Die-Cast Aluminum Alloy.
Paper Source: https://doi.org/10.3390/ma17204990
This material was summarized based on the above paper, and unauthorized use for commercial purposes is prohibited.
Copyright © 2025 CASTMAN. All rights reserved.