This introduction paper is based on the paper "Stereometry specification of anodization surface of casting aluminium alloys" published by "Journal of Achievements in Materials and Manufacturing Engineering".
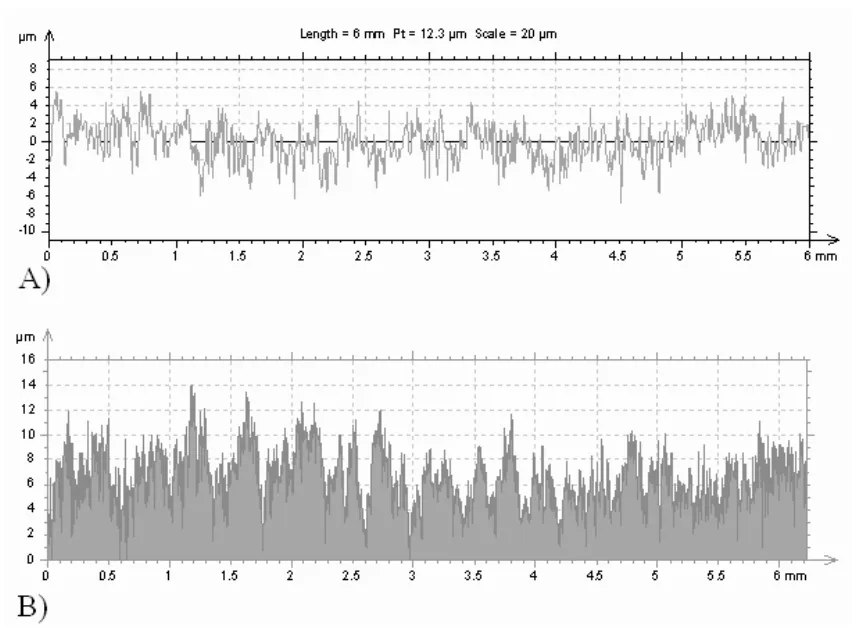
1. Overview:
- Title: Stereometry specification of anodization surface of casting aluminium alloys
- Author: J. Konieczny, K. Labisz, J. Wieczorek, L. A. Dobrzański
- Year of publication: 2008
- Journal/academic society of publication: Journal of Achievements in Materials and Manufacturing Engineering
- Keywords: Mechanical properties; Metallography; Computational material science; Surface treatment
2. Abstract:
Purpose: The aim of the work is presents the influence of casting method and anodic treatment parameters on properties of an anodic layer formed on aluminum casting alloys.
Design/methodology/approach: Investigations were carried out on the laser profile measurement gauge MicroProf from company FRT on two casting aluminum alloys which both were founding by pressure die casting and gravity casting.
Findings: The researches included analyze of the influence of chemical composition, geometry and roughness of anodic layer obtained on aluminum casts.
Research limitations/implications: Contributes to research on anodic layer for aluminum casting alloys.
Practical implications: Conducted investigations lay out the areas of later researches, especially in the direction of the possible, next optimization anodization process of aluminum casting alloys, e.g. in the range of raising resistance on corrosion.
Originality/value: The range of possible applications increases for example as materials on working building constructions, elements in electronics and construction parts in air and motorization industry in the aggressive environment.
3. Introduction:
It the continuous growth of use of alloys aluminum in different branches the wide comprehended industry as well as development of technology of production of aluminum and its alloys and composites with aluminum matrix was observed in last years in many scientific centres on all world [1-5]. The anodic layers have a protective - decorative function applying on the aluminum electronic elements, articles of home farm, part of instruments, the gardens - pieces of furniture, the touristic equipment and sport, the motor accessories and elements of aluminum woodwork. The oxides layers are produced on aluminum foil designed on electrode in condenser too. Hard anodic layers can be applied in air and motor industry.
Anodic oxide layers which are connected fixedly with the aluminum substrate are resistant on corrosion. The corrosion resistance can be reduced by the pores and pits in layer or the presence of harmful alloy-forming elements and admixtures, particularly the copper or by impurities. The intermetallic phase of copper with aluminum dissolve during anodizing, which causes lowering the hardness and thickness of coats, and the enlargement the porosity.
The gain in thickness of the anodic layer in relation to the thickness of the formed oxide film amounts about to 0.001 µm per 1V. A porous and conducting layer forms from the basic layer, which is dissolved by electrolyte. The basic layer is simultaneously restored by formation of aluminium oxide that proceeds with the same speed as it transforms into the surface layer. In this way the basic layer maintains its thickness at almost constant voltage.
During the forming process the aluminum oxide occurring the small increase of mass element as well as his volume. The layer of oxides is fixedly with substrate very strongly. Dissolving of oxides layer is possible only in basic solutions or acid about larger pH than 8.8 relatively lower than 4.0 [13-15].
4. Summary of the study:
Background of the research topic:
The use of aluminum alloys is continuously growing in various industries, alongside advancements in the production technology of aluminum, its alloys, and composites with an aluminum matrix [1-5]. Anodic layers are applied to aluminum for protective and decorative purposes across a wide range of applications, including electronic elements, household items, automotive accessories, and in the air and motor industry.
Status of previous research:
Anodic oxide layers are known for their corrosion resistance when fixed to an aluminum substrate. However, this resistance can be compromised by pores, pits, or harmful alloy-forming elements like copper, which can dissolve during anodizing, reducing hardness and thickness and increasing porosity. The formation and properties of these layers, including their thickness gain (approx. 0.001 µm per 1V) and dissolution characteristics, have been studied [12, 13-15].
Purpose of the study:
The goal of the work is to investigate the properties of anodic layer made on casting aluminum alloys in anodizing process and evaluation of influence of electrolyte and casting method on obtained anodic layer. (Source: "Stereometry specification of anodization surface of casting aluminium alloys", Section 1. Introduction)
Core study:
The core of the study involved investigating two casting aluminum alloys, EN AC-AlSi12(b) and EN AC-AlSi9Cu3(Fe), produced by both pressure die casting and gravity (sand) casting. The research focused on analyzing the influence of the casting method and subsequent anodic treatment on the surface geometry and roughness of the anodic layer formed on these alloys. The study examined samples in their initial (as-cast) state and after applying an oxide layer by a galvanic method, using specific anodizing parameters.
5. Research Methodology
Research Design:
Investigations were carried out on EN AC-AlSi12(b) and EN AC-AlSi9Cu3(Fe) alloys, cast using high pressure and sand casting methods. The chemical compositions are detailed in Table 1. Samples were divided into two groups: starting material (directly after casting) and material with an oxide layer applied by a galvanic method. Four types of elements were anodized: EN AC-AlSi12(b) high pressure cast alloy, EN AC-AlSi12(b) sand cast alloy, EN AC-AlSi9Cu3(Fe) high pressure cast alloy, and EN AC-AlSi9Cu3(Fe) sand cast alloy. Anodizing was performed in H2SO4 (295-315 g/l) at -4 to 2°C, with a pulsating current (2 A/dm² for 0.25 s, 1 A/dm² for 0.1 s) and an aluminum ion concentration of 6-9 g/l, as specified in Table 2.
Data Collection and Analysis Methods:
The analysis of surface geometry was based on data acquired with measurement of selected fragments of casts, executed on laser profile measurement gauge MicroProf of the FRT company. This involved comparing two- and three-dimensional surface figures and roughness distributions.
Research Topics and Scope:
The research focused on the stereometry specification of anodized surfaces of casting aluminum alloys. The scope included analyzing the influence of the alloy's chemical composition, the casting method (pressure vs. gravity), and the presence of an anodic layer on the resulting surface geometry, topography, and roughness.
6. Key Results:
Key Results:
The study found that the casting method applied (pressure or gravitational cast) is the primary factor determining the surface shape geometry of the aluminum alloys. The chemical composition of the investigated samples did not show an influence on surface forming. The application of an anodic layer reproduces the primary geometry of the surface that was shaped during the casting process. The anodic layer does not affect the geometry profile of the surface; its configuration keeps characteristic features even after applying the layer. Furthermore, the anodic layer has no influence on the roughness value of the surface. For instance, the maximum roughness for high-pressure cast materials was around 15 µm, while for sand cast materials it was 60 to 70 µm, and these values remained consistent regardless of anodization. Similarly, features like pick distribution and preferred orientation were not changed by the presence of the anodic layer. An "acclivity" of circa 5 µm was observed on the EN AC-AlSi9Cu3(Fe) high pressure cast alloy surface, potentially due to cast form damage or impurities.
Figure Name List:
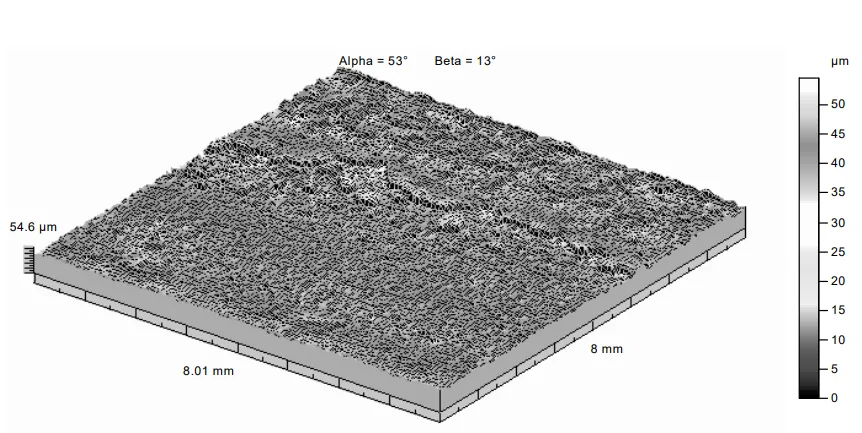
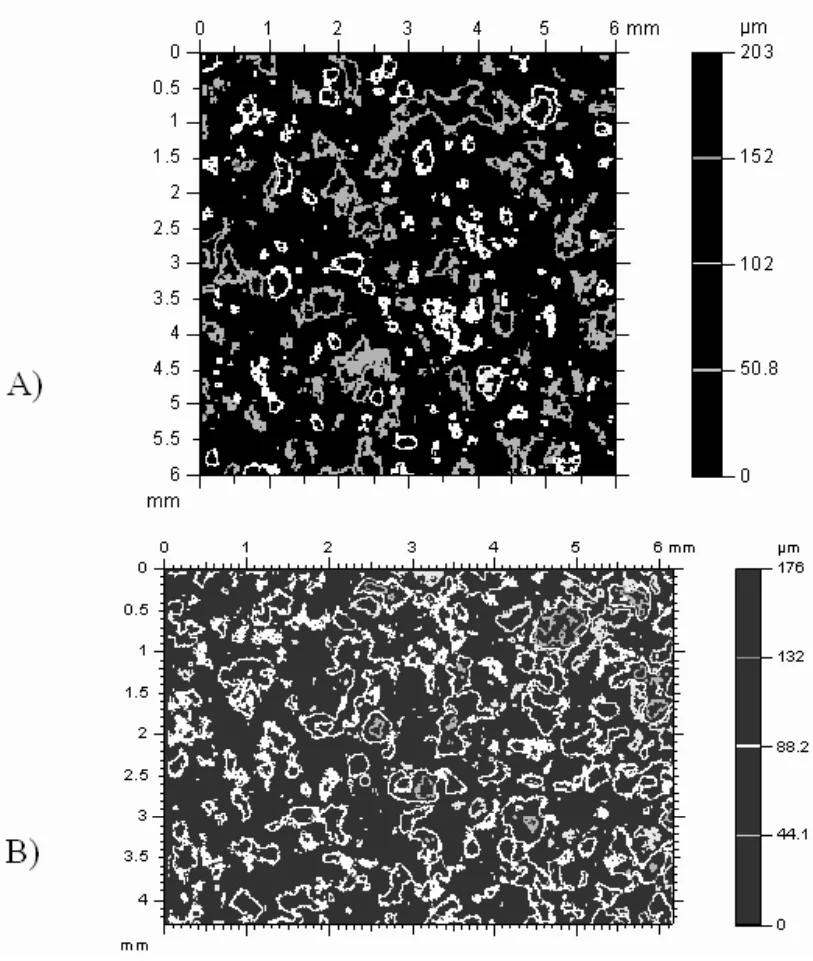
- Fig. 1. The geometrical shape of fragment of studied surface, topography of 3D surface, sand cast alloys; A) EN AC-AlSi12(b), B) EN AC-AlSi9Cu3(Fe)
- Fig. 2. Profiles 2D cut out from studied surface in plane N - S, EN AC-AlSi12(b) high pressure cast alloy; A) before anodization, B) after anodization
- Fig. 3. Three-dimensional topography of surface sample of EN AC-AlSi9Cu3(Fe) high pressure cast alloy
- Fig. 4. The distribution of tops on surface of sample from EN AC-AlSi9Cu3(Fe) sand cast alloy A) before anodization, B) after anodization.
- Fig. 5. The texture of surface (the schedule of characteristic directions) from EN AC-AlSi9Cu3(Fe) sand cast alloy A) before anodization, B) after anodization
7. Conclusion:
The analysis results of geometry investigations of anodic layer surface proved the technology of casting for studied group of materials determining the quality of surface, its geometrical features. Similar results were obtained in.
The applying an oxide layer reproduces the primary geometry of surface, shaped in casting process. The only attendance of applied kind of coat has not influence on characteristic features of surface.
8. References:
- T. Haga, H. Sakaguchi, H. Inui, H. Watari, S. Kumai, Aluminum alloy semisolid strip casting using an unequal diameter twin roll caster, Journal of Achievements in Materials and Manufacturing Engineering 14 (2006) 157-162.
- J. Myalski, J. Wieczorek, A. Dolata-Grosz, Tribological properties of heterophase composites with an aluminum matrix, Journal of Achievements in Materials and Manufacturing Engineering 15 (2006) 53-55.
- M.H. Robert, D. Delbin, Production of cellular A2011 alloy from semi-solid state, Journal of Achievements in Materials and Manufacturing Engineering 17 (2006) 137-140.
- M. Wierzbińska, J. Sieniawski, Effect of morphology of eutectic silicon crystals on mechanical properties and cleavage fracture toughness of AlSi5Cul alloy, Journal of Achievements in Materials and Manufacturing Engineering 14 (2006) 31-36.
- M. Kciuk, The structure, mechanical properties and corrosion resistance of aluminum AlMg1Si1 alloy, Journal of Achievements in Materials and Manufacturing Engineering 16 (2006) 51-56.
- A.W. Brace, The Technology of Anodizing Aluminium, third ed, Interall Srl, Modena, Italy, 2000.
- K.P. Han, J.L. Fang, Decorative-protective coatings on aluminium, Surface and Coathings Technology 88 (1996) 178-182.
- H. Konno, K. Utaka, R. Furuichi, Two step of anodizing process of aluminium as a means of improving the chemical and physical properties of oxide films, Corrosion Science 38/12 (1996) 2247-2256.
- M. Maejima, K. Saruwatari, M. Takaya, Friction behaviour of anodic oxide film on aluminum impregnated with molybdenum sulfide compounds, Surface and Coatings Technology 132 (2000) 105-110.
- I. Vrublevsky, V. Parkoun, V. Sokol, J. Schreckenbach, Study of chemical dissolution of the barrier oxide layer of porous alumina films formed in oxalic acid using a re-anodizing technique, Applied Surface Science 236 (2004) 270–277.
- J. Konieczny, L.A. Dobrzański, K. Labisz, J. Duszczyk, The influence of cast method and anodizing parameters on structure and layer thickness of aluminum alloys, Journal of Materials Processing Technology 157-158 (2004) 718-723.
- L.E. Fratila-Apachitei, J. Duszczyk, L. Katgerman, AlSi(Cu) anodic oxide layers formed in H2SO4 at low temperature using different current waveforms, Surface and Coatings Technology 165 (2003) 232-240.
- L.E. Tichelaar, F.D. Thompson, G.E. Terryn, H. Skeldon, J. Duszczyk, A transmission electron microscopy study of hard anodic oxide layers on AlSi(Cu) alloys, Electrochim. Acta 49 (2004) 3169.
- I. Vrublevsky, V. Parkoun, J. Schreckenbach, G. Marx, Effect of the current density on the volume expansion of the deposited thin films of aluminum during porous oxide formation, Applied Surface Science 220 (2003) 51.
- I. Vrublevsky, V. Parkoun, V. Sokol, J. Schreckenbach, G. Marx, The study of the volume expansion of aluminum during porous oxide formation at galvanostatic regime, Applied Surface Science 222 (2004) 21-25.
- L.E. Fratila-Apachitei, J. Duszczyk, L. Katgerman, Voltage transients and morphology of AlSi(Cu) anodic oxide layers formed in H2SO4 at low temperature, Surface and Coatings Technology 157 (2002) 80-94.
9. Copyright:
- This material is a paper by "J. Konieczny, K. Labisz, J. Wieczorek, L. A. Dobrzański". Based on "Stereometry specification of anodization surface of casting aluminium alloys".
- Source of the paper: www.journalamme.org
This material is summarized based on the above paper, and unauthorized use for commercial purposes is prohibited.
Copyright © 2025 CASTMAN. All rights reserved.
Paper Summarize:
Key questions and answers about the research:
This study investigates the influence of casting method (pressure die and gravity casting) and anodic treatment parameters on the properties, particularly surface geometry, of anodic layers formed on EN AC-AlSi12(b) and EN AC-AlSi9Cu3(Fe) aluminum casting alloys. The research found that the casting method primarily determines the surface geometry, and the application of an anodic layer reproduces this primary surface shape without significantly altering its geometric profile or roughness. These findings are important for optimizing the anodization process for aluminum casting alloys used in various industrial applications.
Q1. What was the main aim of this research?
A1. The main aim was to present the influence of casting method and anodic treatment parameters on the properties of an anodic layer formed on aluminum casting alloys. (Source: "Stereometry specification of anodization surface of casting aluminium alloys", Abstract: Purpose)
Q2. Which aluminum alloys and casting methods were investigated?
A2. The investigations were carried out on EN AC-AlSi12(b) and EN AC-AlSi9Cu3(Fe) aluminum alloys, both produced by pressure die casting and gravity (sand) casting. (Source: "Stereometry specification of anodization surface of casting aluminium alloys", Abstract: Design/methodology/approach; Section 2. Material and methods)
Q3. How does the casting method affect the surface geometry of the aluminum alloys?
A3. The surface shape geometry is clearly dependent on the casting method applied. (Source: "Stereometry specification of anodization surface of casting aluminium alloys", Section 3. Results and discussion)
Q4. Does the application of an anodic layer change the original surface geometry of the cast aluminum?
A4. No, the applying of an anodic layer does not affect the geometry profile of the surface; it is a representation of the substrate surface shape and reproduces the primary geometry shaped in the casting process. (Source: "Stereometry specification of anodization surface of casting aluminium alloys", Section 3. Results and discussion; Section 4. Conclusions)
Q5. What was the effect of the anodic layer on the surface roughness of the cast alloys?
A5. The anodic layer hasn't any influence on the roughness value of the surface. For example, for high-pressure casts, the maximum roughness was 15 µm, and for sand casts, it was 60 to 70 µm, both before and after anodization. (Source: "Stereometry specification of anodization surface of casting aluminium alloys", Section 3. Results and discussion)
Q6. What are the practical implications of these findings?
A6. The conducted investigations lay out areas for further research, especially towards optimizing the anodization process for aluminum casting alloys to improve properties like corrosion resistance, which is valuable for applications in construction, electronics, and the automotive industry. (Source: "Stereometry specification of anodization surface of casting aluminium alloys", Abstract: Practical implications)